一、鋁合金復合材料
鋁合金復合材料的優勢所在
在汽車輕量化中強調運用鋁合金復合材料,與其自身特點有很大關系。具體而言,鋁合金復合材料是一種生命力強大的材料,不僅密度低、尺寸穩定、強度較高,而且耐磨性好、抗斷抗疲勞,還具有良好的塑性與模量等諸多優點。其中鍛造鋁合金材料優勢更為突出,即表面光、潔熱鍛不氧化,加工余量小、無缺陷,強大的剛度可與合金鋼相媲美等,經高強度熱處理后的鋁鍛件在汽車輕量化中的運用越來越廣泛。
如豐田公司曾在發動機活塞制備中使用鋁合金復合材料,較之鑄鐵活塞不僅質量減輕了5%-10%,還提高了4倍左右的導熱性。雖然如此,但在我國汽車輕量化發展中,鋁合金復合材料尚未得到有效推廣,畢竟鋁材成本較高,既需要大量的研發費用和維修成本,在深沖、彈性模量等部分力學性能方面還有待改善,致使其使用效果和應用范圍難以達到預期效果。
鋁合金復合材料在汽車輕量化中的運用
1、 在車身中的運用
在汽車質量中車身質量約占30% ,而且70%左右的油耗是用于承載車身質量的,可見將鋁合金復合材料運用至汽車車身制造中十分必要,或者說勢在必行。
如早在90年代初世界第一輛全鋁車身框架轎車-奧迪A8第1代便誕生了,奧迪公司通過采用ASF車身結構,其以鋁板元件為架構支撐,且基于所承擔的任務采用不同形狀和橫截面積的元件,在保證低質量基礎上獲得最佳功能,具體可從車身構造中的A、B、C柱內部發現,不僅減輕了40%左右的質量,使得油耗和排放得以大幅降低,而且抗扭轉剛度的提高可在一定程度上改變碰撞后的吸能路徑,有助于最大限度的保護乘員,故整車的安全性能得到了明顯改善。發展至今,奧迪A8整車質量和輕量化結構系數分別達到了250kg和1.5,可以說是汽車輕量化的一大重要成果。
再如Ford·P2000基于沖壓焊接制造的鋁制車身骨架,結合使用現有鋼板加工工藝,使得自車身質量低至135.6kg,整車質量和百公里油耗分別減少了32.8%和22.8%,由此可知,鋁合金復合材料在汽車車身輕量化中的合理運用發揮了良好的節能降耗效果,值得進一步研究和推廣。
2 、在發動機中的運用
發動機在汽車質量中的比例約為20-30%,顯然運用鋁合金復合材料意義重大。目前最常見的是缸體缸蓋、活塞、曲軸箱、油底殼以及連桿等部位,在此就活塞和缸體缸蓋作重點分析。隨著汽車制造工藝和性能要求的不斷提高,越來越多的發動車活塞采用了鑄鋁合金材料,這是因為作往復運動的活塞需要借助減重降低慣性,達到降低曲軸配重提高工作效率的目的,且要求具有小的熱膨脹系數和良好的導熱性,并在350℃環境下能夠發揮良好的力學性能,而鑄鋁合金不僅能夠滿足上述要求,而且輕質密度低,有助于減少發動機噪音和振以及油耗,故得以應用于活塞及連桿中。再者發動機缸體缸蓋在導熱性、抗腐蝕性等方面對材料的要求極高,故運用性能優良的鋁合金復合材料也是必然的,當下很多國外汽車公司紛紛制備了全鋁型缸體缸蓋。
如日產VQ、凌志IMZ-FEV6等型號的發動機油底殼采用的便是鑄造鋁合金復合材料,但從樣本機看,與傳統材料相比其質量降低了20%左右。
3、 在底盤中的運用
其實在汽車輕量化實踐過程中,底板系統不僅容易實現,而且潛力較大。對于懸掛系統來說,鋁合金復合材料是替代鋼鐵的首選材料。
如福特公司經使用鋁合金制動盤取代原鑄鐵盤,雖然成本有所增加,可是降低了2/3的質量,并提高了2倍的使用壽命;Neod Lite 車底盤在運用鋁合金零部件后,使得轉向機殼、萬向節、下控制臂、轉向軸以及后制動轂等質量均有所降低,顯然符合輕量化要求;此外克爾維特與凱迪拉克等車輛經采用鋁合金復合材料制備的零部件也取得了良好的效果。
4、 在車輪中的運用
對于汽車車輪質量而言,輪轂質量占到了70%的比例,試驗表明,如果每減輕1kg的輪轂質量,在同樣耗費1L汽油的情況下汽車行使距離可增加800m,或者說在節約1L油量的情況下,則有2.5kg的碳無法得到排放,所以輪轂輕量化既便于普及,也有著較高的鋁化率和節能環保功效。同時運用鋁合金復合材料的輪轂還可發揮良好的減震、抗腐蝕、散熱作用,且經久耐用、容易制造,對于改善汽車安全性和舒適性意義重大。預計在日后的發展中,鋁合金輪轂在我國的需求量會飛速增長,故有著廣闊的發展空間。
二、碳纖維復合材料
碳纖維(carbon fiber,簡稱CF),是一種含碳量在90%以上的高強度、高模量纖維的新型纖維材料。是由片狀石墨微晶等有機纖維沿纖維軸向方向堆砌而成,經碳化及石墨化處理而得到的微晶石墨材料。碳纖維“外柔內剛”,比重只有鋼的四分之一,但強度卻高于鋼鐵,并且具有耐腐蝕、高模量的特性。
碳纖維的優點
1.碳纖維復合材料的比強度和比模量高,是最理想的輕質高強車體材料。
2.碳纖維復合材料遇到碰撞時,不是通過塑性形變來吸收能量,而是變成無數細小的碎片,因而能夠吸收大量的碰撞的能量,大約是鋼結構的4倍,具有和高的安全性。
3.碳纖維復合材料容易成型,即容易成型出符合動力學原理以美觀需求、光滑表面的外形,因此可以省去復雜繁瑣的車身涂裝加工的程序,降低一定成本。
4.碳纖維復合材料成型時,可以將不同的材料一體成型,更加有利于汽車在制造時的模塊化和整體化。
5.碳纖維復合材料在酸溶液中、堿溶液中、以及有機溶液中均不溶解,化學性質穩定,因此耐腐蝕性能好、壽命長,幾乎不需要維修,維修成本也很低。
6.碳纖維復合材料強度高,模量高,并沒有蠕變,可以用于制造傳動軸結構。蘭博基尼投資打造的LP700-4車身,擁有極高的強度和剛度,安全性也很高。
F1賽車的剎車盤和剎車片也采用了碳纖維復合材料,這使得F1賽車的剎車盤無論是在性能上還是在價格上,都遠遠高于普通民用車的剎車盤。
但是,碳纖維也存在著自己的局限性
1.操作費時,批量生產少,設計及工藝的開發難度高。
2.材料成本也很高,全碳纖維車身和底盤的LFA售價高于30萬英鎊,這幾乎是一輛法拉利458和一輛路虎攬勝的價格。
3.它是脆性材料,損壞后基本無法修復,而且碳纖維的高強度只限于軸向,它的徑向強度是比較脆弱的,(因此往往利用其耐拉質輕的優勢而避免去做承受側面沖擊的部分)。
4.碳纖維與其他材料的連接也是個問題,若使用傳統的螺栓連接,連接周圍很容易產生裂紋。
5.相對于鋁合金而言,碳纖維無法做到回收利用。
汽車的防撞梁作為汽車保險杠的主要部件,是低速碰撞中最重要的承載和吸能部件,可以保護乘客和周圍的部件。碳纖維復合材料密度小,比強度高,比模量大,碰撞吸能好。根據相關要求建立了碰撞模型后,對鋼制防撞梁和碳纖維復合材料防撞梁進行測試,進行碰撞仿真,分析兩種材料的吸能情況,結果表明:碳纖維的比吸能是鋼制的3.7倍,減重達到了71.4%。吸能特性和輕量化效果提升顯著。
如:2020款雪佛蘭克爾維特黃貂魚設計并制造了汽車行業第一款彎曲的多空心拉擠碳纖維防撞梁,它為黃貂魚的后方及擴展軀干提供了強有力的保護,同時它的輕量化特性也大大提高了黃貂魚的操控性以及節油性能。
人們對于碳纖維的運用在車身上也很多。相對于之前提到的碳纖維的缺點而言,寶馬i系列將它在車身上的運用方法和技術,成功地回避了和解決了一些問題寶馬i系列的車身結構大面積采用碳纖維材料,在制造端萊比錫工廠新建的車身制造車間將碳纖維強化塑料復合組件拼合起來,這樣就制造出Life模塊的基本結構。
由于BMW i3 Life模塊的碳纖維強化塑料結構幾何融合性高,其車身部件的數量只相當于普通鋼制車身的三分之一,整個基本架構由大約150個碳纖維強化塑料組件組成,這也為售后維修提供了便利性。并且,該車身使用最先進的粘合技術并且實現了100%的自動化,避免了傳統的螺栓連接而導致的產生裂紋的問題。而且,為了解決維修難的問題,采用這種車身連接工藝,將各個部件在不接觸的情況下拼合為相互之間形成精確設定的粘合縫,以便在粘合工藝完成后達到最佳的車身剛性。在維修受損部位時,維修工人只需將其中一塊小面積部件進行更換,并采用粘合技術進行再次銜接,這樣帶來的優勢不僅可以恢復到之前的車身強度,成本上也得到了大幅降低。
三、片狀模塑料
片狀模塑料(SMC)可根據部件需要調整力學及耐腐蝕高溫性能,適用于部分車身、承力結構件和耐高溫腐蝕零件。SMC質量輕、強度高、易加工成型,可分為通用型、結構型和功能型三類,可替代車身的部分鋼鋁部件,是汽車輕量化的主流方向之一。該種材料的商業化應用目前主要集中在車體后尾門,其他的應用多為試驗階段。
如雷諾汽車的后尾門相比原鋼制后尾門減重10%,且注塑、組裝工藝簡單,生產成本大為降低。
四、樹脂基復合材料
樹脂基復合材料不僅可使零部件降低多達 40%的質量,而且還可以使生產成本降低 40%左右。目前,玻璃纖維增強樹脂復合材料和碳纖維增強樹脂復合材料在汽車上已經獲得成功的應用,已大量應用于汽車內飾件和外飾件。
玻璃纖維增強樹脂復合材料(GFRP)耐腐蝕、絕緣性好,特別是有良好的可塑性,對模具要求較低,對制造車身大型覆蓋件的模具加工工藝較簡易,生產周期短,成本較低。在轎車和客車上,采用玻璃纖維增強樹脂復合材料制造的轎車車身覆蓋件、客車前后圍覆蓋件和貨車駕駛室等零部件。
碳纖維增強樹脂基復合材料(CFRP)具有輕質高強、高斷裂韌性、耐腐蝕、可設計性強、易成型、減振阻尼性能好等一系列優點,既能夠滿足部件剛強度、輕量化的設計要求,在車輛安全性上也具有明顯優勢,因而是很有前途的汽車用輕量化材料,不過,目前存在成本高、成型周期長等缺點。
注:SMC 、GMT 、FRP 和LFT 分別為聚酯片狀模塑料、玻璃纖維增強樹脂,纖維增強復合材料和長纖維增強熱塑性材料。
目前在汽車車身上已普遍應用的有用玻璃纖維增強不飽和聚酯片狀模塑料(SMC)制造的車身空氣導流板、前翼子板和前擋泥板延伸部件、大燈罩、發動機罩、裝飾條、尾板等,用傳遞模塑工藝技術(RTM)制造的車身板件加強筋等。
五、纖維增強熱塑性塑料
按照塑料中纖維的長度,可分為短纖維增強熱塑性塑料(纖維長度一般為0.2至0.4 mm),長纖維增強熱塑性塑料(纖維長度一般為10 mm以上)和連續纖維增強熱塑性塑料。
LFT與其他材料相比
1、LFT與短玻纖增強塑料比較
和傳統的短玻纖增強塑料相比,具備特殊的螺桿、模頭及切割器設計和浸潤劑配方的LFT技術可以得到12mm以上的料粒片材,纖維長度和料粒長度相當,讓玻璃纖維在最終制品中擁有更長的玻璃纖維長度。一般的短纖維增強,在經過螺桿、注射口、模腔內流動這三個過程后,纖維的長度下降的非常厲害,最終制品中的纖維平均長度已經不到1mm,因此對制品的力學性能的幫助非常有限,而LFT技術,不論是模壓還是注射成型,最終測試制品內的玻璃纖維平均長度仍然不低于4mm,因此大大提高了制品的機械性能。和短纖增強的結構件相比,抗沖擊、抗蠕變性更好,抗熱性能也更優異。
2、LFT與金屬比較
和金屬材料相比,LFT材料有非常低的密度和非常高的比強度,制品加工方法較靈活,材料回收率高,相比材料的成本較低,部件的功能性和整體性很高,LFT的部件加工設備如擠出機、注射劑或壓機、打孔安裝設備、模具,相比昂貴的金屬沖擊設備和模具來說,其成本是很低的,尤其事在生產批量不大的車型,LFT更體現出優異的經濟性。因此,與鋼制結構件相比,LFT使產品重量減輕了很多,并擁有部件合并性能,這樣可以降低成本。
3、LFT與GMT相比較
LFT片材是繼GMT(玻璃纖維氈增強熱塑性塑料)片材后的新一代的熱塑性復合材料,它是以長玻璃纖維為增強材料,以聚丙烯(PP)、PA、PET等為基體材料復合而成。
LFT片材與CMT片材相比較,其突出的優點是:
1、片材在壓制過程中流動性較好。
2、片材價格較低。
3、材料的性能基本上與GMT相同。
若客戶對材料的抗沖擊性能要求較高時,本公司將會提供高抗沖擊性能型號的LFT片材以供需要。
4、LFT與SMC相比較
LFT片材的產品制造工藝與熱固性復合材料玻璃鋼中的SMC(片狀模壓料)十分類似。同樣是用片材在模具中壓制而成。LFT是硬片材加熱變軟后在模具中冷壓,而SMC是在冷態軟片材放入模具后熱壓成型。
LFT片材與SMC片材相比,其技術性能具有如下優點:
1、 無毒、無味,可改善工作環境。
2、 質輕,密度只有1~1.2g/cm3。
3、 邊角料及廢品可循環使用,最大限度減少浪費。
4、 強度比SMC高,抗沖擊韌性尤為突出。
5、 耐腐蝕、電性能更優良。
6、 產品壓制速度比SMC快數倍,生產效率大幅提高。
長纖維增強熱塑性材料(LFT)一直在汽車工業中用在半結構應用領域。它們的主要優點是誘人的成本/性能比和相對較低的密度。歐洲ELV(end of life vehicle)立法推動了這種材料的發展,該立法促進了再循環,因而也促進了熱塑性材料對熱固性材料的取代。
在汽車行業中,LFT主要被用于制作結構和半結構部件,如前端模塊、保險杠大梁、儀表盤骨架、電池托架、備用輪胎倉、座椅骨架、腳踏板及整體底板等。長纖維增強聚丙烯被用于轎車的發動機罩、儀表板骨架、蓄電池托架、座椅骨架、轎車前端模塊、保險杠、行李架、備胎盤、擋泥板、風扇葉片、發動機底盤、車頂棚襯架等;長纖維增強的PA,被進一步擴展到引擎蓋內,因為LFT-PA不僅硬度高、重量低,而且高玻纖含量使其熱膨脹系數幾乎與金屬相同,能承受引擎帶來的高溫。
如:
2003年,Mazda 6安裝了全球第一款長纖維聚丙烯的前端模塊,整個前端模塊重量在3.5公斤,從而開始了長玻纖在前端模塊的正式應用。據統計數據推算,預計在未來5年(2019~2024),全球塑料前端模塊增長率為6%,現階段前端模塊材料集中在金屬(市場占有量 40%),尼龍6+30%GF與金屬復合或尼龍6+60%GF(市場占有量 25%),聚丙烯復合材料LGF30、LGF40,含少量D-LFT、GMT(市場占有量 35%),其中長玻纖前端模塊經過10多年的發展,已經得到越來越多的OEM 認可,包括中國的汽車制造商如吉利、長城、廣汽、上汽等主機廠,都已經開始批量使用長玻纖產品,替代傳統的金屬和尼龍前端模塊。
作為發動機周邊的零部件,一般選擇具有耐熱老化的 30%-40%的長纖維增強聚丙烯材料。
儀表板骨架應用
儀表板骨架上需要安裝各種儀表,要求高剛度和尺寸穩定性,同時需要安裝副安全氣囊,滿足安全氣囊在低溫-35℃和高溫80℃的爆破要求,所以也屬于安全部件,要求較高的抗沖擊韌性和耐高低溫性能。隨著生活水平的提高,對內飾要求的要求也更加高檔,軟質儀表板的使用也是越來越多,儀表板骨架材料也從最先的PP-EPDM-TD30、TD20、PC/ABS和SMA+GF材料到現在改用玻璃纖維增強聚丙烯材料。長玻纖材料的一個特點是低溫沖擊強度比常溫沖擊強度更高,所以該材料的使用,提高儀表表骨架的氣囊安全保護性能,同時,將儀表板骨架從3mm減薄到2.2mm,從而實現了該零部件的輕量化。
為了進一步提高材料性能,降低重量,改善尺寸穩定性和翹曲缺點,寶馬公司引入了結構化學發泡(SGI)工藝。該工藝的特點是將長玻纖塑料和化學發泡劑混合后進入料斗,高速注塑進入模腔,然后再利用模芯后退工藝(Core-Back 工藝),給出發泡空間,進而獲得較大發泡倍率,得到更高倍率的發泡結構件,根據模芯后退的程度來控制發泡倍率。在2017Mini、 Countryman微型跨界多功能車 (CUV) 的儀表板骨架上,就使用了該工藝,其減重效果達到15%。
除了寶馬公司的SGI化學發泡工藝,業界也采用Mucell物理發泡與長玻纖結合的成型工藝,以獲得減重與降低翹曲的儀表板骨架,但在早期的開發中,Mucell的發泡劑分散機構,很容易導致玻璃纖維的折斷,不能保證最終制品中玻璃纖維長度,所以在使用Mucell工藝時,需要和注塑機企業討論其工藝的實用性。
長玻纖在儀表板骨架的開發目前在國內的OEM使用還不多,除了結構較為復雜,厚度較薄、翹曲仿真難度較大之外,還因為前面提到副氣囊的安全技術、整體產品的翹曲變形等問題,目前國外普遍采用有機纖維作為氣囊保護裝置,可以采用類似嵌件注塑的工藝一次成型。而國內還是以采用TPO彈性體為主的安全氣囊支架技術,該技術需要先成型TPO安全氣囊支架,然后利用焊接或者卡扣安裝到儀表板骨架上面,再通過表面火焰處理后進行聚氨酯PU發泡等。
后尾門
后尾門目前普遍使用還是以金屬結構為主,國外的日產、寶馬等主機廠,已經逐步采用長玻纖的全塑后尾門技術,全塑后尾門一般包括外板和內板兩部分,外板主要采用可噴涂的滑石粉填充聚丙烯材料,保證零部件的外觀,而內板主要起增強作用,多采用玻璃鋼 SMC 或者 30%~40% 長玻纖增強聚丙烯材料,兩個板之間,采用膠粘等技術,保證后尾門的結構性與外觀性要求。
零部件企業方面,日立化成在這塊開發比較全面,其產品包括日產Infiniti EX、Infiniti FX、Murano等車型,在國產的日產英菲尼迪、Infiniti、 QX50和奇駿Rogue都已經使用了全塑后尾門產品。同時彼歐、麥格納、佛吉亞等企業,在全塑后尾門都擁有自己的專利技術,上圖是全塑后尾門爆炸示意圖,通過長碳纖維、局部單向帶材增強等技術,可以獲得更大規模的減重效果。
六、玻璃纖維增強樹脂
玻璃纖維氈增強熱塑性復合材料(Glass Mat Reinforced Thermorplastic,簡稱GMT)是指以熱塑性樹脂為基體,以玻璃纖維氈為增強骨架的新穎、節能、輕質的復合材料,是目前國際上極為活躍的復合材料開發品種,被視為世紀新材料之一。
GMT一般可以生產出片材半成品,然后直接加工成所需形狀的產品。GMT具備復雜的設計功能,以及出色的抗沖擊性,同時易于組裝和再加工,并因其強度和輕巧性而倍受贊譽,使其成為替代鋼并減少質量的理想結構部件。
圖 輕質高強的GMT材料
GMT材料的優點
比強度高:GMT的強度和手糊聚酯玻璃鋼制品相似,其密度為1.01-1.19g/cm,比熱固性玻璃鋼(1.8-2.0g/cm)小,因此,它具有更高的比強度。
輕量化、節能 :用GMT材料做的汽車門自重可從26Kg降到15Kg,并可減少背部厚度,使汽車空間增大,能耗僅為鋼制品的60-80%,鋁制品的35-50%。
與熱固性SMC(片狀模塑料)相比,GMT材料具有 成型周期短、沖擊性能好,可再生利用和儲存周期長等 優點。
沖擊性能:GMT吸收沖擊的能力比SMC高2.5-3倍,在沖擊力作用下,SMC、鋼和鋁均出現凹痕或裂紋,而GMT卻安然無恙。
高剛性:GMT里含有GF織物、即使有10mph的沖擊碰撞,仍能保持形狀。
GMT材料在汽車領域的應用
GMT片材比強度高、可制得輕質部件,同時設計自由度高、碰撞能量吸收性強、加工性能好,從上個世紀90年代開始在國外被廣泛應用于汽車工業中。而隨著燃油經濟性,可回收性和易加工性的要求不斷提高,汽車行業用GMT材料市場也將繼續穩步增長。
目前,GMT材料在汽車工業中的應用廣泛,主要有座椅骨架、保險杠、儀表板、發動機罩、電池托架、腳踏板、前端、地板、護板、后牽門、車頂棚、行李托架、遮陽板、備用輪胎架等部件。
如:
1. 座椅骨架
福特汽車公司2015 Ford 跑車上的第二排座椅靠背壓縮成型設計由一級供應商/加工商Continental Structural Plastics公司采用Hanwha L&C的45%單向玻纖增強的玻璃纖維氈熱塑性復合材料(GMT)和Century Tool & Gage的模具,模壓成型,成功地滿足了極具挑戰性的保持行李負載條件下的歐洲安全法規ECE。
該部件需要進行100多次FEA迭代才能完成,從早期的鋼結構設計中省去了五個零件,并且在更薄的結構中每輛車可節省3.1千克,也更易于安裝。
圖 福特汽車公司2015 Ford Mustang跑車的第二排座椅靠背 來源:SPE&福特汽車
2. 車尾防撞梁
現代全新2015款全車尾的防撞梁為GMT采用的就是材料,相比鋼材材質產品重量更輕,緩沖性能更好,在減輕車重、降低油耗的同時,保證了安全性能。
圖 汽車之家
3. 前端模塊
奔馳在其豪華雙門轎跑車中選擇Quadrant Plastic Composites GMTex?織物增強熱塑性復合材料作為前端模塊元件。
圖 梅賽德斯S級雙門跑車前端模塊 圖源:PressReleaseFinder
4. 車身下護板
由Quadrant Plastic Composites用高性能GMTex?制造的車身下罩保護應用于梅賽德斯越野特別版。
圖 車身護板 來源:PressReleaseFinder
5. 尾門骨架
GMT尾門結構除了可以實現功能集成和減輕重量的通常優勢外,GMT的可成型性也實現了鋼或鋁不可能實現的產品形式,應用于日產Murano、Infiniti FX 45等車型。
圖 GMT材料的尾門骨架 來源:PressReleaseFinder
6. 儀表板框架
GMT制造儀表板框架的新概念已在福特集團的幾種型號上使用:沃爾沃S40和V50,馬自達3和福特C-Max。這些復合材料能夠實現廣泛的功能集成,特別是通過將車輛橫梁以薄鋼管的形式包含在模制件中,并且與傳統方法相比,重量大大減輕,而無需增加成本。
圖 GMT制造儀表板框架 來源:PressReleaseFinder
加工工藝
手糊成型工藝和技術
簡單地說,手糊成型工藝(Hand Lay-up Molding)是手工作業把玻璃纖維織物和樹脂交替地鋪層在已被覆好脫模劑和膠衣的模具上,然后用壓輥滾壓壓實脫泡,最后在常溫下固化成型為汽車復合材料制品,如圖1所示。盡管在現代汽車復合材料成型新工藝不斷涌現的情況下,手糊成型工藝顯得比較原始,但是,該工藝卻具有其獨特的不可替代性,仍然為世界各國汽車復合材料行業特別是中國汽車復合材料行業所廣泛采用。
圖1 手糊成型工藝示意圖
圖2所示為手糊成型工藝流程。從該工藝流程可以看出,手糊成型工藝具有以下優點:不需要復雜的設備和模具,投資低;生產技術容易掌握,且產品不受尺寸形狀的限制,適合小批量和大型制件的生產;可與其他材料如金屬、木材及塑料泡沫等同時復合制成一體。這些優點使得手糊成型工藝至今仍然作為汽車復合材料的一種主要成型工藝而被用于小批量地加工各種汽車復合材料制品,如客車和重型卡車的前/后圍面板、高頂、導流罩、引擎罩蓋、保險杠、擋泥板以及休閑車、農用車的車身等。此外該工藝還被用于新車開發,如制造概念車和新車樣件試制。
圖2 手糊成型工藝流程
手糊成型工藝的缺點是生產效率低,生產周期長,工作環境差,因此對于大批量車型的產品不太適合。此外,由于這種工藝與操作人員的技能水平和制作環境條件有很大的關系,受此影響,在我國,由手糊成型工藝生產的汽車零部件的質量往往不夠穩定,從而影響了汽車復合材料的聲譽。
需要說明的是,手糊成型工藝并不是劣質汽車復合材料零部件的代名詞。只要嚴格按照手糊成型工藝的流程和工藝規范,準確掌握手糊工藝的技術要領,同樣能夠制作出一流水平的汽車復合材料制品。實際上,國外很多昂貴和精致的高檔跑車以及在展會上熠熠生輝的很多概念車均出自于手糊成型工藝之手。圖3所示的Chevrolet Corvette跑車,其車身即為用手糊成型工藝生產出來的。
圖3 用手糊成型工藝生產的跑車車身
噴射成型工藝和技術
圖4所示為噴射成型工藝(Spray Up Molding)示意圖。該工藝是將混有引發劑和促進劑的兩種聚酯分別從噴槍兩側噴出,同時將切斷的玻纖無捻粗紗由噴槍中心噴出,使其與樹脂在空間均勻混合后沉積到模具上。當沉積到一定厚度時,用壓輥滾壓使纖維浸透樹脂,排除氣泡,在經常溫固化后成型為汽車復合材料制品。噴射成型工藝是在手糊成型工藝的基礎上發展起來的。由于該工藝是借助于機械的手工操作工藝,因此也被稱為“半機械手糊成型工藝” 。圖5所示為該工藝的工藝流程。
圖4 噴射成型工藝示意圖
圖5 噴射成型工藝流程
與手糊成型工藝相比,噴射成型工藝的效率提高了2~4倍甚至更高。其優點是:由于使用無捻粗紗代替了手糊工藝的玻璃纖維織物,因而材料成本更低;成型過程中無接縫,這使得制品的整體性和層間剪切強度更好;可自由調節產品的壁厚、纖維與樹脂的比例以及纖維的長度,因而滿足了汽車零部件的不同機械強度要求。由于噴射成型工藝具有效率高、成本低及產品尺寸形狀不受限制的優點,因此該工藝在國外汽車復合材料行業中,有逐步取代傳統的手糊成型工藝的趨勢,例如,客車和重型卡車的很多前/后圍面板、側面護板、高頂及導流罩等都已由噴射成型工藝制作。
噴射成型工藝的缺點是:產品的均勻度在很大程度上取決于操作人員的操作熟練程度;由于噴射成型的樹脂含量高且增強玻纖短,因而制品強度較低;陰模成型比陽模成型難度大,小型制品比大型制品生產難度大;生產現場工作環境惡劣,環境污染程度一般均大于其他的工藝方法;初期投資比手糊成型工藝大。盡管如此,近年來,噴射成型工藝的缺點正在得到極大的改善。在國外,已采用機械手編程來替代人工噴射,從而大大提高了產品質量的穩定性,原材料的損耗也被明顯降低。同時,通過對生產現場采取全封閉的管理措施以及進行空氣排放處理,使得環境污染問題得到明顯改善。圖6所示為采用噴射成型工藝生產的KENWORTH重卡高頂。
圖6 采用噴射成型工藝生產的重卡高頂
纏繞成型工藝和技術
纏繞成型工藝(Filament Winding)是在控制纖維張力和預定線型的條件下,將浸過樹脂膠液的連續纖維(或布帶、預浸紗)按照一定的規律連續地纏繞到相應于制品內腔尺寸的芯模或內襯上,然后在室溫或加熱條件下使之固化、脫模,獲得一定形狀的汽車復合材料制品,如圖7所示。根據纖維纏繞成型時樹脂基體的物理化學狀態不同,分為干法纏繞、濕法纏繞和半干法纏繞三種。其中,濕法纏繞的應用最為普遍。濕法纏繞工藝顧名思義是將連續玻璃纖維粗紗或玻璃布帶浸漬樹脂膠后,直接纏繞到芯?;騼纫r上而成型并經固化的成型方法。而干法纏繞一般僅用于高性能、高精度的尖端技術領域中。
圖7 纖維纏繞成型工藝示意圖
纖維纏繞成型工藝的優點是:能夠按產品的受力狀況設計纏繞規律,以充分發揮纖維的強度;比強度高。一般來講,纖維纏繞壓力容器與同體積、同壓力的鋼質容器相比,重量可減輕40%~60%;可靠性高。纖維纏繞制品易實現機械化和自動化生產,工藝條件確定后,纏出來的產品質量穩定、精確;生產效率高。采用機械化或自動化生產,只需少數操作工人,纏繞速度快(240m/min);成本低。在同一產品上,可合理配選若干種材料(包括樹脂、纖維和內襯),使其再復合以達到最佳的技術經濟效果?,F在用纖維纏繞成型工藝生產的CNG/LPG高壓氣瓶、傳動軸和板狀彈簧等已廣泛應用于大客車、轎車和卡車上。纖維纏繞成型工藝的缺點是:纏繞成型適應性小,不能纏任意結構形式的制品,特別是具有凹形表面的制品。這是因為纏繞時,纖維不能緊貼在芯模表面,而是處于架空狀態;纏繞成型需要有纏繞機、芯模、固化加熱爐、脫模機及熟練的技術工人,不僅投資大,而且技術要求高,因此只有大批量生產時才能獲得較大的經濟技術效益。圖8所示為采用纖維纏繞成型工藝生產的CNG乘用車用高壓氣瓶。
圖8 采用纖維纏繞成型工藝生產的CNG車用氣瓶
樹脂傳遞模塑成型工藝和技術
樹脂傳遞模塑成型工藝(Resin Transfer Moulding)簡稱RTM。該技術始于1950年代,是從濕法鋪層手糊成型工藝和注塑成型工藝中衍生出來的一種新的閉模成型工藝。該工藝一般是在模具的型腔中預先放置玻璃纖維增強材料(包括螺栓、螺帽或聚氨酯泡沫塑料等嵌件),閉模鎖緊后,將配好的樹脂膠液在一定的溫度和壓力下,從設置于適當位置的注入孔處注入模腔,浸透玻纖增強材料,然后一起固化,最后啟模、脫模,得到兩面光滑的汽車復合材料制品。圖9所示為RTM工藝示意圖。
圖9 樹脂傳遞模塑成型工藝示意圖
圖10所示為RTM的工藝流程。由于是一種閉模成型工藝,因此RTM的優點是:無需膠衣涂層即可使構件獲得雙面光滑的表面;在成型過程中散發的揮發性物質很少,有利于工人的健康和環境保護;模具制造與材料選擇的機動性強,不需要龐大、復雜的成型設備就可以制造出復雜的、有極好制品表面的大型構件;根據設計需求,增強材料可以按任意方向鋪放或局部增強,因而容易實現按制品受力狀況鋪放增強材料的目的。成型效率高、投資少以及易實現自動化生產的特點,使RTM工藝日益為汽車復合材料行業所重視,并逐步成為取代手糊成型、噴射成型的主導成型工藝之一。
圖10 RTM工藝流程
目前,RTM工藝在汽車制造業中的應用已非常廣泛,如乘用車的車頂、后廂蓋、側門框和備胎倉,以及卡車的整體駕駛室、擋泥板和儲物箱門等都有用RTM工藝生產的。圖11所示是用RTM工藝生產的ASTON MARTIN跑車的車身側圍板。
圖11 用RTM工藝生產的車身側圍板
當然,RTM工藝也存在一些不足,如:雙面模具的加工費用較高;預成型坯加工生產設備的投資大;對原材料(樹脂和玻纖材料)和模具質量的要求高,以及對模具中的設置與工藝要求嚴格等。目前,對RTM成型工藝的研究和推廣不斷取得新的進展,主要研究方向集中在:微機控制注射機組、增強材料預成型技術、低成本模具、快速樹脂固化體系及工藝穩定性和適應性等方面,涌現出了一系列改良的RTM成型工藝,如 Lite-RTM、VARTM、VIP和TERTM等。
模壓成型工藝和技術
模壓成型工藝(Compression Molding)是復合材料生產中最古老而又富有無限活力的一種成型方法。它是將一定量的預混料或預浸料加入金屬對模內,經加熱、加壓固化而成型的一種方法,如圖12所示。模壓料的品種有很多,可以是預浸物料、預混物料,也可以是坯料。當前常用的模壓料品種有:熱固性復合材料,包括SMC、BMC和TMC等;熱塑性復合材料,包括GMT、D-LFT和G-LFT等。
圖12 模壓成型工藝示意圖
在提到模壓成型工藝技術時,我們特別要提到汽車復合材料工業廣泛應用的熱固性復合材料SMC和熱塑性復合材料GMT模壓成型工藝。
SMC主要采用金屬對模的模壓成型工藝,其壓制工藝過程相對比較簡單,主要包括片狀模塑料的制備和成模兩部分。由于SMC的組成比較復雜,每種組分的種類、質量、性能及其配比等對SMC的生產工藝、成型工藝及最終制品的性能、價格等都有很大的影響,因此,對組分、用量和配比等進行合理的選擇,對于制造優良的汽車SMC零部件具有十分重要的意義。圖13所示為SMC模壓成型工藝流程。
圖13 SMC模壓成型工藝流程
GMT片材的成型通常有兩種:一是連續玻璃纖維氈或針刺氈與熱塑性塑料層合而成,另一種則是隨機分布的中長纖維與粉末熱塑性樹脂制成的片材。前者適合于沖壓模壓成型,其制品的形狀一般比較簡單。后者的流動性較好,適合于流動模壓成型,適于成型形狀較為復雜的汽車零部件。與金屬材料相比,GMT的密度約為鋼材的1/6~1/7,具有耐腐蝕以及隔熱、隔音和絕緣性好的優點,可一次加工成型復雜的制品;與SMC片狀模塑料相比,GMT具有極長的貯存期,制品的成型周期是SMC的1/3~1/4,并且沖擊韌性好,可回收利用?;谝陨咸攸c,GMT在汽車工業中的應用范圍不斷擴大,應用量不斷增加,正越來越多地代替金屬和熱固性復合材料。
與SMC相似,GMT也是采用金屬對模的模壓成型工藝,所不同的是SMC的固化成型是化學反應,而GMT的冷卻成型是物理變化,成型所要求的工藝參數和對壓機、模具的技術要求是不相同的。GMT成型工藝的特點是:片材必須先預熱(加熱至220~230℃),成型壓力高(10~25Mpa),成型溫度低(35~50℃),成型周期短(30~60s)。GMT模壓成型工藝流程如圖14所示。
圖14 GMT模壓成型工藝流程
總之,模壓成型工藝的主要優點是:生產效率高,便于實現專業化和自動化大批量生產;產品尺寸精度高,重復性好;表面光潔,無需二次修飾;能一次成型結構復雜的制品;由于可批量生產,因此價格相對低廉。這些優點使得模壓成型工藝特別適合汽車工業要求批量大、精度高及互換性好的生產特點,是目前汽車復合材料工業中最為普遍采用的成型工藝,尤其是乘用車上的復合材料零部件80%均由模壓成型工藝制成,如引擎蓋、車門、后廂蓋、后舉門、車頂、前端框架、儀表臺骨架、車門中間承載板、座椅骨架和底部護板等。
模壓成型工藝的不足之處在于模具制造復雜,投資較大,加上受壓機限制,使其更適合于生產中、大批量的汽車復合材料制品(熱固性汽車復合材料制品在100000件/年以內,熱塑性汽車復合材料制品在1000000件/年以內)。隨著金屬加工技術、壓機制造水平及合成樹脂工藝性能的不斷改進和提高,壓機噸位和臺面尺寸不斷增大,模壓料的成型溫度和壓力也相對降低,使得模壓成型制品的尺寸逐步向大型化發展,目前已能生產的大型汽車部件如模壓重卡高頂、MPV車頂、皮卡車廂、重卡駕駛室側圍板等。圖15所示即為模壓成型工藝生產的2001福特Explorer Sport Trac SMC皮卡車廂。
圖15 SMC模壓成型工藝生產的皮卡車廂
LFT-D成型工藝技術
LFT-D成型工藝(Long-Fiber Reinforce Thermoplastic Direct)是繼GMT和LFT-G之后又一種新的長纖維增強熱塑性復合材料工藝技術,是長纖維增強熱塑性復合材料在線直接生產制品的一種工藝技術,它區別于GMT和LFT-G的關鍵因素是半成品步驟被省去了,而在材料的選擇上更加靈活,是近年來在汽車復合材料行業中最受關注和市場成長最快的一種嶄新的成型工藝技術。在LFT-D技術中,不僅纖維的含量和纖維的長度可以直接調節到最終部件的要求,其基體聚合物也可以直接調節到最終部件的要求。通過使用不同的添加劑可以改變和影響制品的機械和特殊應用特性,如熱穩定性、著色性、紫外穩定性和纖維與基體的粘結特性等,這也意味著每一種特殊應用都可以通過LFT-D獲得其獨特的材料配方。
LFT-D的典型工藝流程是,將聚合物基體顆粒(主要是PP)和添加劑輸送到重力混合計量單元中,根據部件的機械性能要求進行材料的混配。經混配好的原料再被送入雙螺桿擠出機中進行塑化,熔融的混合物通過一個薄膜模頭形成類似瀑布的聚合物薄膜,該聚合物薄膜直接被送入到雙螺桿混煉擠塑機的開口處。此時,玻璃纖維粗紗通過特別設計的粗紗架,在經過預熱、分散等程序后被引入到聚合物薄膜的頂端與薄膜匯合一同進入到雙螺桿擠塑機中,由螺桿切割粗紗,并把它們柔和地混合到預熔的聚合物當中,然后直接送入壓制模具中成型或者推壓進注射模具成型,如圖16所示。
圖16 LFT-D成型工藝示意圖
LFT-D成型工藝的優點主要有兩個:一是成本低。由于是直接一步法生產,因此由LFT-D生產的大型結構部件比兩步法生產的GMT或LFT-G壓制部件的成本低20%~50%;二是制品的綜合性能優異。LFT-D壓制成型制品的抗沖擊性能比GMT稍低一些,但由于比LFT-G成型后的纖維長很多,因此其抗沖擊性能明顯比LFT-G高得多。另外,大量的研究表明,LFT-D注塑的生產效率比采用標準LFT-G粒料的生產效率高,因為LFT-D低的塑化要求改善了纖維被剪斷的可能性。對于成型周期超過1min的部件,用LFT-D注塑設備在30s內就能完成。LFT-D成型工藝的缺點主要是制品廠需要加大對LFT-D成型工藝以及材料、配方等的研究投入。圖17所示為采用 LFT-D生產的2003 大眾 Golf V前端框架。
圖17 用LFT-D成型工藝生產的前端框架
免責聲明:本網站所轉載的文字、圖片與視頻資料版權歸原創作者所有,如果涉及侵權,請第一時間聯系本網刪除。
相關文章
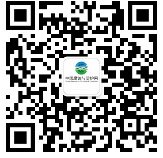
官方微信
《中國腐蝕與防護網電子期刊》征訂啟事
- 投稿聯系:編輯部
- 電話:010-62316606-806
- 郵箱:fsfhzy666@163.com
- 中國腐蝕與防護網官方QQ群:140808414
點擊排行
PPT新聞
“海洋金屬”——鈦合金在艦船的
點擊數:7685
腐蝕與“海上絲綢之路”
點擊數:6157