先進航空發動機朝著高推質比、高可靠性、長壽命和經濟可承受性的方向發展,苛刻且相互矛盾的指標要求航空發動機關重件構型復雜、輕質高效。傳統的“減材”制造技術面臨生產周期長、成品率低、制造成本高等挑戰,成為制約先進航空發動機研發的瓶頸。變革性的“近凈成形”增材制造技術,因具有一體化成形、無需模具、制造成本低等優點,最早被美國聯合技術研究中心(UTRC)嘗試用于渦輪葉盤一體化制造,隨后通用電氣(GE)、羅爾斯-羅伊斯(RR)等航空發動機企業也開始應用增材制造技術加工或修復零部件。例如,GE公司在GE9X、Leap 系列航空發動機中已成功應用增材制造技術成形了燃油噴嘴、傳感器外殼、熱交換器、渦輪葉片等10 余種結構。Safran、MTU等發動機公司增材制造了燃油噴嘴、燃燒室機匣等結構,提升了生產效率。中國航發湖南動力機械研究所采用增材制造技術加工了微型渦噴發動機,將近百個零件集成制造為10個,包括增材制造成形的壓氣機/渦輪的整體葉盤結構,并成功通過某型渦噴發動機試車。
圖1 拓撲優化后增材制造航空發動機泄壓門鉸鏈
增材制造技術給航空發動機復雜結構的加工提供了新的途徑,但在能量源“逐點掃描熔化-逐線掃描搭接-逐層凝固堆積”的過程中,粉末/絲材局部熔化形成熔池,熔池內殘留未完全恢復的“匙孔”,導致增材制造結構內部存在廣布缺陷;且受限于加工可達性,復雜結構(如渦輪葉片)內部空腔等關鍵部位殘留粉末等表面缺陷。另外,增材制造結構不同部位處的晶體形貌、內部/表面缺陷等具有顯著差異,導致結構強度、疲勞壽命與結構特征密切相關且表現出大的分散性。為此,美國聯邦航空管理局(FAA) 、歐洲航空安全局(EASA)分別于2018 年、2021 年發布的《粉末床熔融增材制造成形渦輪發動機零件及修復指南》建議稿、《增材制造認證備忘錄》等適航認證文件中指出,需發展適用于航空發動機增材制造結構的強度及壽命評價方法。
圖2 基于點陣結構的空心風扇葉片設計
目前航空發動機增材制造結構在無損檢測技術與初始缺陷表征、強度預測方法、壽命評估方法及創新結構一體化設計方面的研究進展,得到主要結論如下:
1)渦流、超聲等技術可以檢測增材制造簡單結構近表面及內部缺陷,借助這些方法,實現增材制造結構初始缺陷形貌的量化表征,進而建立缺陷空間取向與增材制造方向的關聯規律。
2)基于CT 檢測的原位試驗方法,揭示了單軸拉伸、循環拉伸等典型載荷下缺陷演化機理,發展了用于預測拉伸極限、延伸率等性能的塑性損傷模型,實現了增材制造發動機離心葉輪破裂轉速的準確預測。
3) 發展了以初始缺陷等效參量為輸入的增材制造材料級壽命模型,實現了增材制造標準試樣、缺口試樣的高循環疲勞、低循環疲勞壽命預測。
4)考慮增材制造工藝約束、強度、多物理場服役環境等因素,發展了航空發動機增材制造結構一體化設計方法,并開展了齒輪箱殼體、離心葉輪、整體葉盤等創新構型的設計與試驗驗證。
為了進一步推動航空發動機增材制造結構的實際應用,仍需開展以下幾個方面的研究:
1) 在試驗數據方面,國內外學者針對增材制造材料的拉伸、高循環及低循環疲勞等開展了試驗研究,但仍處于零散、樣本量少的狀態。需針對航空發動機選用的材料開展系統且深入的試驗研究,擴大數據樣本,表征材料力學特性及分散性。同時,渦輪葉盤等熱端結構長期工作在復雜、嚴苛的載荷環境中,現有研究仍無法滿足增材制造熱端結構設計的需求,仍需針對復雜失效模式開展蠕變、蠕變-疲勞等試驗研究。
2) 航空發動機空心氣冷渦輪葉片、雙輻板渦輪盤等結構具有復雜內腔與幾何不連續特征。采用增材制造工藝成形后,結構局部呈現大應力梯度-缺陷-表面粗糙度多因素耦合特征。如何實現復雜結構的缺陷-表面粗糙度表征,闡明多因素耦合下的失效機理,并建立相應的強度、壽命評估方法仍是當前應用的難點。
免責聲明:本網站所轉載的文字、圖片與視頻資料版權歸原創作者所有,如果涉及侵權,請第一時間聯系本網刪除。
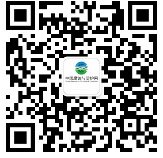
官方微信
《腐蝕與防護網電子期刊》征訂啟事
- 投稿聯系:編輯部
- 電話:010-62316606
- 郵箱:fsfhzy666@163.com
- 腐蝕與防護網官方QQ群:140808414