近年來,隨著我國石油工業的快速發展,海底油氣管道內壁的腐蝕問題受到了廣泛的關注。當油氣管道與外部環境存在較大的溫差時,水蒸氣會在溫度較低的管道頂部凝結,導致嚴重的頂部腐蝕(TLC)。1959年在法國LACQ酸性氣田第一次發現了頂部腐蝕問題,之后在加拿大、印尼、美國等國家也相繼發生了嚴重的頂部腐蝕案例。頂部腐蝕的出現會嚴重影響管道的安全性能。
物理法與電化學法是兩種研究腐蝕問題的常用分析手段。頂部腐蝕的腐蝕環境是體積微小的冷凝液滴,液滴出現的位置具有一定的隨機性,難以布置有效的對電極與參比電極來構造三電極體系,因此用常規的電化學方法研究頂部腐蝕是無效的,國內外學者大多采用物理法來研究頂部腐蝕。
有研究發現影響頂部腐蝕的主要因素有CO2分壓、溫度、氣體流速、水冷凝率以及CH3COOH含量等。也有研究人員通過布置在掛片下方的溫度傳感器測液滴的滴落周期,提出液滴在試片表面的滯留時間(DRT)對頂部腐蝕有重要的影響。但是,由于失重法無法對頂部腐蝕進行連續性監測,為了得到更為詳細的腐蝕發展狀態,需頻繁取出試片稱量,該方法操作復雜且會帶來一定的誤差。此外,冷凝液滴分布的隨機性決定了頂部腐蝕是一種局部腐蝕現象,通過失重法得到的是平均腐蝕速率,無法得到準確的局部腐蝕信息。因此,設計一種新的頂部腐蝕監測方法是十分必要的。
新型傳感器的設計加工
新型傳感器為3×3陣列電極傳感器,由9個試片按3×3陣列排列,如圖1所示。其中,8個試片為X65管線鋼,1個試片為304不銹鋼,試片尺寸均為10mm×10mm×2mm,工作面的表面積為1cm2,背面焊接銅導線。304不銹鋼試片居中(標注為0號試片),X65管線鋼試片環繞其四周(標注為1~8號試片),相鄰試片的間距為1mm。
(a) 正視圖
(b) 橫剖面圖
圖1 傳感器試片布置和尺寸示意圖
除工作面外,其余面用環氧樹脂密封。傳感器總厚度為4mm,以保證傳感器具有良好的傳熱性能。封裝完成后,用400號至1200號水磨砂紙逐級打磨工作面,并依次用無水乙醇和去離子水沖洗后烘干。在打磨過程中要確保工作面平整,防止表面傾斜影響冷凝液滴的形成。工作表面封裝完成后,將傳感器放置于干燥箱中備用。
頂部腐蝕試驗裝置
圖2 頂部腐蝕試驗裝置示意
如圖2所示,通過泵機向冷卻水箱中循環注入溫度為10℃的冷卻水,使裝置頂部環境保持恒定低溫。將傳感器緊貼于冷卻水箱下表面,確保冷卻水可以起到良好的冷卻作用。試驗溶液為去離子水,裝置內部與空氣連通。將試驗裝置的玻璃容器部分置于水浴恒溫箱中,水浴溫度維持在70℃,使裝置底部保持恒定的高溫。由此,傳感器下表面與氣體環境之間形成溫度梯度,冷凝液滴會在傳感器下表面形成。腐蝕性氣體溶解在冷凝液滴中,形成頂部腐蝕環境。為了觀察液滴的形成和試片的腐蝕過程,在傳感器下方安裝了數碼攝像頭,進行觀察記錄。
頂部腐蝕試驗方法
采用CST508多通道腐蝕監測儀測量工作電極之間的電偶電流以及它們相對于參比電極的耦合電位。其中,1~8號試片為工作電極,0號試片為參比電極。
當傳感器置于空氣中時,各個試片之間沒有電解質連通,無法測得其電偶電流與耦合電位。而在頂部腐蝕環境中,試片工作面與氣體環境的溫差使水蒸氣在試片表面冷凝,形成冷凝液滴。試驗中未引入揮發性介質,因此試片表面的冷凝水同樣為去離子水。當空氣中的O2與CO2等可溶性氣體溶于冷凝水中時,形成腐蝕環境。
由于液滴的附著位置具有隨機性,為了方便討論,假定一種液滴的附著情況,如圖3所示。圖中1?2?4?0號試片被同一滴液滴覆蓋。液滴長時間附著于試片表面,液滴內部溶入Fe2+?H+?CO32-?HCO3- ?OH-等離子,形成電解質環境。此時,1?2?4?0號試片被液滴導通,可以測量出1?2?4號試片之間的電偶電流,以及它們相對于0號試片的耦合電位;1?2?4號試片之間測得的電流數據具有對應關系,理論上同一時刻其電流和為0。同理,3?5號試片與6?7號試片之間同樣存在電偶電流,且分別具有對應關系。由于腐蝕過程的不確定性,被不同液滴覆蓋的區域(如1?3?5號試片)所對應的電流數據之間不存在對應關系。由此,通過電偶電流數據,可以推斷出液滴分布位置。當液滴自試片表面滴落時,試片表面狀態會發生劇烈改變,導致試片之間的電偶電流發生突變。因此,可以通過電流數據的變化得出液滴滯留時間。
圖3 一種假定的試驗情況示意圖
綜上,理論上新型傳感器可以有效監測頂部腐蝕液滴覆蓋區域的具體位置以及液滴滯留時間等關鍵信息,彌補了傳統傳感器的不足。
試驗過程中,耦合電位與電偶電流的測量時間間隔為3s,試驗共進行2天。試驗結束后,將試片取出,用酸洗液清除表面腐蝕產物,隨后用去離子水沖洗干凈,置于光學顯微鏡下觀察其腐蝕表面形貌。
頂部腐蝕試驗結果
01 宏觀形貌
(a) 2min (b) 5min
(c) 15min (d) 30min
(e) 1h (f) 3h
(g) 12h (h) 48h
圖4 頂部腐蝕不同時間后試片表面的宏觀形貌
在試驗開始階段,水蒸氣在試片表面大量形核,生成微小的液滴,如圖4a,b所示。隨著時間的推移,水蒸氣的凝結量不斷增加,小液滴不斷生長,逐漸與相鄰的液滴融合,形成近乎于覆蓋所有試片的薄液膜,如圖4c~e所示。在這一過程中,X65管線鋼試片開始出現點蝕,點蝕坑出現的位置與液滴的形核、聚集過程有關。隨后,液膜下的腐蝕逐漸加劇,X65管線鋼試片的表面不再光亮,而作為參比電極的304不銹鋼試片在這種環境中沒有發生腐蝕,表面依舊光潔。
隨著水蒸氣的進一步冷凝,液膜厚度逐漸增加,由于重力以及表面張力作用,冷凝水聚集形成較大的冷凝液滴。試驗中,液滴主要形成在8號試片表面,同時覆蓋了部分5?7號試片,其余X65管線鋼試片表面沒有液滴,如圖4(f)所示。此時,304不銹鋼試片與X65管線鋼試片表面的冷凝水不再連通。此后,液滴位置不會發生改變,液滴覆蓋區域下的試片腐蝕加劇,而其他試片表面的腐蝕無明顯變化。
液滴的形成、滴落與液滴在試片表面的吸附力有關,計算公式為:Fσ = πr2(2σ/r)(Fσ為水在試片表面的吸附力;r為液滴半徑;σ為表面張力)。
水表面張力大小與其在試片表面的接觸角有關,而接觸角受試片表面粗糙度的影響。試驗初期和中期,X65管線鋼試片與304不銹鋼試片表面粗糙度相同,冷凝過程相仿,試片表面間液膜連通。隨著時間的推移,X65管線鋼試片表面逐漸形成腐蝕產物,而304不銹鋼試片表面保持光潔。此時,兩種試片的表面粗糙度發生改變,水分子在兩種試片表面的吸附力隨之改變,冷凝過程也相應產生差異,液膜不再相連。圖4d~f中液膜的變化過程很好證實了這一現象。
試驗結束后,取出試片,清除其表面殘留冷凝水,其表面腐蝕產物形貌如圖5所示,可見試片表面的腐蝕產物呈棕黃色,為鐵的氧化物及氫氧化物的混合物。
圖5 頂部腐蝕試驗結束后試片表面腐蝕產物的形貌
根據液滴的分布情況,可將8個X65試片分成3類。第一類為完全沒有液滴覆蓋的試片,包括1?2?3?4?6號試片;第二類為部分被液滴覆蓋的試片,包括5?7號試片;第三類為完全被液滴覆蓋的試片,為8號試片。
從上述3類試片中分別選取2?5?8號試片,置于100倍光學顯微鏡下觀察,其腐蝕表面形貌如圖6a所示。結果表明:1號試片表面除點蝕坑外,其余部分仍可見金屬光澤,腐蝕產物較少;5號試片上半部分表面狀況與1號試片的相仿,然而在其下部有液滴附著的區域,腐蝕產物顯著增多,幾乎無金屬光澤;8號試片表面的腐蝕產物較厚,近乎覆蓋整個試片表面,有明顯的黑色與褐色腐蝕產物,分別是鐵的二價與三價氧化物。
(a) 試驗結束未清除腐蝕產物
(b) 試驗結束清除腐蝕產物
(c) 試驗時間為60min時
圖6 不同狀態2,5,8號試片的表面腐蝕形貌(100×)
將上述三個試片用酸洗液清除表面腐蝕產物后,置于100倍光學顯微鏡下觀察,得到試片的表面形貌如圖6b所示,可見2號試片與5號試片的上半區域,即沒有液滴覆蓋的區域,點蝕坑極其微小,可清晰地觀察到試片表面的打磨痕跡,表明該區域腐蝕速率較小;而8號試片與5號試片的下半部分,即被液滴覆蓋的區域,存在面積與深度均較大的點蝕坑,且8號試片表面已無法觀測到打磨痕跡,表明該區域腐蝕速率較大。選取試驗時間為60min時2?5?8號試片的影像,觀察試片的腐蝕情況,如圖6c所示。通過對比發現,在試驗中期3個試片表面的蝕坑數量、位置與試驗結束后幾乎沒有變化。由此說明頂部腐蝕過程中點蝕坑出現只與初始時小液滴的形核、聚集過程有關,但當試片表面形成大液滴,并不斷重復穩定的生長和滴落過程,點蝕只會在已有的蝕坑處發展,不會形成新的蝕坑。
02 電偶電流與耦合電位數據
圖7 試驗測得8個X65管線鋼試片的耦合電位隨時間變化曲線
試驗初期(試驗開始至60min)
如圖7所示,耦合電位表現為幅值較大的正弦信號。試驗初期,X65管線鋼試片表面布滿微小的冷凝液滴,作為工作電極的8個X65管線鋼試片與作為參比電極的304不銹鋼試片之間沒有介質連通,不構成閉合回路。因此,此時無法測得耦合電位,圖中正弦信號其實是儀器固有的隨機信號。
在試驗初期與中期的過渡階段
工作試片開始出現明顯的點蝕坑,試片表面的小液滴不斷生長融合形成不均勻的液膜,將工作試片與參比試片連通。因此,理論上可以測得8個工作試片的耦合電位。然而這一過程為液膜生成的初始過程,其厚度較薄,溶液電阻較大,導致測量誤差較大。此時,耦合電位雖然仍表現為正弦信號,但與試驗初期的正弦信號比,其均值和幅值均有所改變。耦合電位逐漸降低表明工作試片腐蝕不斷加劇,此外電位的幅值變化可以反映出連接工作試片與參比試片的液膜厚度變化。
試驗中期(試驗進行至1~3h)
試片表面液膜厚度增加,導電性有所提升。此時,電位減小,得到的耦合電位較為準確。
試驗后期(試驗進行至3h后)
電位波動幅值又開始逐漸增大,直至回到試驗的初始狀態。這一階段工作試片表面的液膜逐漸轉變為大液滴,溶液覆蓋區的面積減小。由于工作試片表面存在銹層,參比試片表面的液滴冷凝過程與工作試片表面的不再相似,二者之間不再有介質連通,因而無法測得耦合電位。電位波動幅值的逐漸增大可能代表連通二者的液膜面積逐漸減小。
圖8 8個X65工作試片之間的電偶電流密度隨時間變化曲線
試驗初期(試驗開始至60min)
如圖8所示,8個工作試片相互獨立,電偶電流均為0。
在試驗初期與中期的過渡階段
電偶電流會在相鄰的兩個試片之間產生小幅波動,如3號與5號試片,表明兩個試片之間有小液滴融合。
試驗中期(試驗進行至1~3h)
8個工作試片的電偶電流密度均有顯著增大。此時,液膜覆蓋整個傳感器表面,8個工作試片彼此連通,電偶電流密度的大小反映了試片表面液膜狀態及腐蝕情況。這一階段電偶電流密度大小劇烈波動,但在后半段電偶電流密度的變化開始呈現出一定的周期性。
試驗后期(試驗進行至3h后)
除5、7、8號試片外,其余試片的電偶電流密度減小為0,說明只有5、7、8號試片被液滴附著而連通。5號與7號試片電偶電流密度較小,為陰極電流,試片腐蝕緩慢;8號試片電偶電流密度較大,表現為陽極,試片腐蝕較為嚴重。同一時刻下,3個試片的電偶電流密度和為0,與理論分析相符。分析電偶電流密度數據得到的結果與宏觀觀測結果完全一致。
圖9 8號試片電偶電流密度隨時間變化曲線
試驗后期,電偶電流密度存在著明顯的周期性特征。將8號試片的電偶電流密度局部放大,得到如圖9所示的電偶電流密度曲線,可見電偶電流密度存在周期性規律,即電流密度大小先迅速減小隨后快速恢復,這一過程出現的周期為210s左右。通過觀察攝影機的錄像,發現此周期與液滴滴落周期相符,這反映了液滴周期性滴落對電流密度的影響。由此,可以準確得到影響頂部腐蝕問題的液滴滯留時間這一關鍵參數。
結論
1 新型傳感器可以有效地監測到頂部腐蝕問題中液滴的具體位置,得到液滴在試片表面的滯留時間(DRT)。
2 液滴的冷凝過程受腐蝕產物的影響。試驗后期304不銹鋼與X65管線鋼試片表面液滴的冷凝過程完全不同。
3 頂部腐蝕點蝕坑的形成與初始條件下液滴的形核和聚集過程有關。
免責聲明:本網站所轉載的文字、圖片與視頻資料版權歸原創作者所有,如果涉及侵權,請第一時間聯系本網刪除。
相關文章
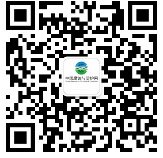
官方微信
《中國腐蝕與防護網電子期刊》征訂啟事
- 投稿聯系:編輯部
- 電話:010-62316606-806
- 郵箱:fsfhzy666@163.com
- 中國腐蝕與防護網官方QQ群:140808414
點擊排行
PPT新聞
“海洋金屬”——鈦合金在艦船的
點擊數:7130
腐蝕與“海上絲綢之路”
點擊數:5741