高強(qiáng)度材料常因缺乏加工硬化而受到損害,使其易出現(xiàn)開(kāi)裂和災(zāi)難性失效。具體來(lái)說(shuō),通過(guò)添加一種或多種元素的合金化方法可以提高純金屬和合金的強(qiáng)度,但往往會(huì)不可避免地降低塑性和韌性。由于元素在晶界( GBs )的偏析,合金化有時(shí)會(huì)面臨晶間脆化問(wèn)題 。例如,錫青銅合金(添加了2~20 wt.%的Sn以及其他元素如Zn、Pb、Ni、Al )已被廣泛研究,以獲得比純銅更高的強(qiáng)度。但是由于脆性富錫δ偏析相沿晶界處填充,會(huì)誘發(fā)災(zāi)難性的沿晶斷裂,導(dǎo)致錫青銅合金表現(xiàn)出有限的加工硬化穩(wěn)定性,因此其塑性變形能力較低 。
最近一種具有吸引力的方法是利用納米析出相來(lái)顯著強(qiáng)化金屬而不損失甚至提高塑性。其優(yōu)異的強(qiáng)度源于共格或半共格的 納米析出相,這些析出相呈均勻分布,產(chǎn)生大量的共格應(yīng)變。同時(shí),具有較小晶格失配的共格或半共格納米析出相-基體界面有助于減少位錯(cuò)的塞積,從而緩解了加載時(shí)界面處的應(yīng)力集中,降低了界面開(kāi)裂的傾向,有利于保持良好的塑性。盡管如此,在多元合金(一類具有廣闊應(yīng)用潛力的高強(qiáng)度低塑性材料)中在保持強(qiáng)度提高的前提下實(shí)現(xiàn)顯著的塑性提升仍然具有挑戰(zhàn)性。
在這里,北京科技大學(xué)王自東教授、陳凱旋副教授等人報(bào)告了一種“晶內(nèi)超細(xì)納米析出”策略,在塑性差的錫青銅合金(即Cu-12Sn-1.5Ni合金)中實(shí)現(xiàn)了一種非常穩(wěn)定的應(yīng)變硬化響應(yīng),顯著提高了塑性,并且伴隨著強(qiáng)度的提升。具體來(lái)說(shuō),原始鑄態(tài)Cu-12Sn-1.5Ni合金的抗拉強(qiáng)度 σu 為327.36±11.55 MPa,屈服強(qiáng)度σy為182.58±1.39 MPa,大約是粗晶純銅的3倍(63±3 MPa ), 但伴隨著較差的均勻延伸率εu為6.70±1.49%,約為純銅(32±2% )的1/8。通過(guò)添加微量的Fe元素(<0.1 wt.%),我們?cè)?/span>Cu-12Sn-1.5 Ni合金晶粒內(nèi)部實(shí)現(xiàn)了高數(shù)量密度的超細(xì)Fe納米析出相(ultra-nano Fe precipitation,簡(jiǎn)寫(xiě)為un-Fe)的均勻彌散分布,并且這些納米Fe析出相具有極小的晶格錯(cuò)配度。細(xì)小彌散分布的晶內(nèi)納米Fe相不僅緩解了晶間斷裂,還通過(guò)納米Fe相-位錯(cuò)相互作用激活了穩(wěn)定的應(yīng)變硬化機(jī)制,從而形成超高塑性(εu約為20%)和強(qiáng)度提高(σu約為400 MPa,σy約為200 MPa)的獨(dú)特組合。晶內(nèi)超細(xì)納米析出是一種很有前景的方法,未來(lái)可以廣泛用于制造高塑韌性和高強(qiáng)度的合金。
圖1a、b、d、e、g、h的OM顯微組織表征表明,Cu-12Sn-1.5Ni-xFe (x=0, 0.08, 0.83 wt. %)鑄態(tài)合金均具有粗大的樹(shù)枝狀枝晶組織,并且枝晶之間存在δ相。OM表征表明,與Cu-12Sn-1.5Ni合金(dgrain=97.0±16.8 μm,Aδ=11.20±1.26)相比,Cu-12Sn-1.5Ni-0.08Fe合金的晶粒尺寸(dgrain)和δ相的面積分?jǐn)?shù)(Aδ)略有降低(dgrain=95.6±15.5 μm,Aδ=10.12±1.79%)。而在Cu-12Sn-1.5Ni-0.83Fe合金中,可以觀察到晶粒尺寸dgrain明顯降低至80.7±13.3 μm,同時(shí)Aδ為10.25±1.66%,與Cu-12Sn1.5Ni-0.08Fe合金相近。晶粒尺寸的減小與先前報(bào)道的Fe摻雜在銅 [24]和銅合金[13,14,,]中誘導(dǎo)晶粒的細(xì)化的結(jié)果一致,這是由于原位形成的Fe納米析出相的異質(zhì)形核作用 [13,14]。
圖1f中的TEM圖顯示,Cu-12Sn-1.5Ni-0.08Fe合金中析出了高數(shù)量密度的(1.3×1023 m−3,見(jiàn)表1)超細(xì)點(diǎn)狀Fe納米析出相(直徑為5.0 ± 2.7 nm,見(jiàn)圖1k),且分布高度均勻。相比之下,圖1i可以看到,在Cu-12Sn-1.5Ni-0.83Fe合金中,分散良好的點(diǎn)狀(直徑為5.7 ± 1.7 nm,圖1l)和球狀(直徑為35.4 ± 7.6 nm,圖1m)的Fe納米析出相的數(shù)量密度較低(0.1×1023 m−3,表1)。后者合金中的Fe納米析出相的尺寸分布更寬(圖1k-m),且體積分?jǐn)?shù)更高(表1)。通過(guò)STEM-EDS對(duì)點(diǎn)狀和球狀Fe納米析出相的富鐵成分進(jìn)行了驗(yàn)證(圖1j)。關(guān)于析出相特征的詳細(xì)評(píng)估可參見(jiàn)補(bǔ)充數(shù)據(jù)的第1節(jié)。由于在Cu-12Sn-1.5Ni-(0.08, 0.83)Fe合金中,點(diǎn)狀Fe納米析出相的尺寸極小,因此將點(diǎn)狀的Fe超細(xì)納米析出相被稱為超細(xì)納米Fe(un-Fe)。而在Cu-12Sn-1.5Ni-0.83Fe合金中尺寸分布更寬的球狀Fe納米析出相(15-55 nm,圖1i,l和m)被稱為納米Fe(n-Fe)。納米顆粒誘導(dǎo)的晶粒細(xì)化只有在顆粒具有高效能(良好的晶體學(xué)匹配關(guān)系且尺寸適當(dāng))、足夠的數(shù)量密度、合適的尺寸和足夠?qū)挼某叽绶植紩r(shí)才會(huì)發(fā)生[32,33]。在這種情況下,不同于Cu-12Sn-1.5Ni-0.83Fe合金中具有良好組合un-Fe和n-Fe的明顯晶粒細(xì)化效果(圖1g),單獨(dú)具有超細(xì)尺寸且尺寸分布范圍較窄的un-Fe對(duì)銅熔體的異質(zhì)成核能力和效率較低,因此對(duì)銅晶粒細(xì)化效果很弱(圖1d)
采用HRTEM對(duì)un-Fe和n-Fe顆粒進(jìn)行表征(圖2)。從<112>Cu帶軸拍攝的圖像(圖2a)的快速傅里葉變換(FFT)圖譜顯示,un-Fe顆粒和銅基體均為面心立方(FCC)結(jié)構(gòu),二者呈cube-on-cube的取向關(guān)系(OR)。圖2a表明,un-Fe/Cu界面清晰且完全共格,理論晶格錯(cuò)配度δ值極低,僅為0.0069,un-Fe顆粒周圍沒(méi)有明顯的晶格畸變。需要注意,0.0069的δ值是通過(guò)理論計(jì)算得出的,計(jì)算公式為δ=2(aCu-aFe)/(aCu+aFe) ,其中aCu和aFe分別是純Cu和γ-Fe的晶格參數(shù) (aCu=0.3615, aFe=0.359 [,])。原則上,un-Fe顆粒和銅基體之間的晶格錯(cuò)配度受到其他合金元素(如Sn和Ni)的影響。顆粒主要由Fe組成,而基體主要由Cu組成,因此此處的晶格失配僅考慮純Cu和純Fe。此外,以真實(shí)原子尺度分辨率在圖2b中15個(gè)平面層進(jìn)行測(cè)量計(jì)算得到了un-Fe顆粒和Cu基體的(111)面的晶面間距d(111),其平均值分別為0.1976 nm和0.1959 nm。因此實(shí)驗(yàn)計(jì)算(111)γ-Fe 和(111)Cu 晶面之間的d值錯(cuò)配度為0.008nm。這種低的晶格錯(cuò)配度降低了析出相的形核勢(shì)壘,從而使具有高數(shù)量密度和超細(xì)尺寸的un-Fe析出相得以形成和穩(wěn)定。結(jié)合FFT濾波圖像(圖2b)和晶格條紋的強(qiáng)度變化(圖2c),可以在HAADF-STEM下確定單個(gè)顆粒的尺寸。HAADF成像的襯度來(lái)源于低原子序數(shù),因此,暗柱應(yīng)該由Fe原子的分區(qū)引起。
圖3.鑄態(tài)Cu-12Sn-1.5Ni-(0,0.08,0.83wt.%)Fe合金的力學(xué)性能。(a)無(wú)Fe、un-Fe增強(qiáng)和un-Fe+n-Fe共增強(qiáng)銅合金(分別為0、0.08、0.83wt.%Fe) 的工程應(yīng)力-應(yīng)變曲線;(b) 實(shí)驗(yàn)測(cè)得的三種Cu合金的應(yīng)變硬化率Θ=dσ/dε(其中σ和ε分別為真應(yīng)力和真應(yīng)變);(c)應(yīng)變硬化指數(shù)(n=d(lnσ)/d(ln?))隨真應(yīng)變的變化。(d)拉伸性能和硬度柱狀圖(HV0.3),其中誤差棒代表標(biāo)準(zhǔn)差,表示每種狀態(tài)下進(jìn)行的多次測(cè)試的離散程度;(e) un-Fe增強(qiáng)銅合金與其他鑄造錫青銅合金的抗拉強(qiáng)度與總伸長(zhǎng)率(?total)的比較[14,48-56] ,表明un-Fe增強(qiáng)超出了傳統(tǒng)的塑性與強(qiáng)度關(guān)系范圍;(f) 分別采用分子動(dòng)力學(xué)模擬得到的嵌有球狀FCC Fe粒子(直徑分別為15.880 nm、12.410 nm、6.896 nm和3.998 nm)的30.3×30.3×30.3 nm³ Cu-Fe體系下沿[001]方向的工程應(yīng)力-應(yīng)變曲線(詳見(jiàn)附加數(shù)據(jù)中的圖S3,第4節(jié)),表明較小的顆粒產(chǎn)生更大的抗拉強(qiáng)度和塑性。
根據(jù)Hall-Petch關(guān)系[,],在Cu-12Sn-1.5Ni-(0.08, 0.83 wt. %) Fe合金中,晶粒細(xì)化有限,平均晶粒尺寸減小了1.4 μm和16.3 μm,對(duì)屈服強(qiáng)度σy的貢獻(xiàn)很小,分別為0.1 MPa和1.3 MPa,因此Fe增強(qiáng)銅合金屈服強(qiáng)度的提高主要?dú)w因于納米析出強(qiáng)化。在該材料中,un-Fe和n-Fe在Cu基體內(nèi)提供了更強(qiáng)的相界面,需要更高的應(yīng)力才能使位錯(cuò)切過(guò)或繞過(guò)。我們結(jié)合位錯(cuò)-顆粒相互作用的TEM表征研究了Fe增強(qiáng)銅合金的強(qiáng)化機(jī)制。圖4為預(yù)先經(jīng)過(guò)0.5%變形處理的Cu-12Sn-1.5Ni-(0.08, 0.83)Fe合金中位錯(cuò)與Fe納米析出相相互作用的BF-TEM圖像。位錯(cuò)在n-Fe/Cu界面上堆積(圖4a中的I區(qū)域)或者弓出(圖4a中的II區(qū)域)。顯然,n-Fe顆粒沒(méi)有被滑移位錯(cuò)剪切。相反,位錯(cuò)被un-Fe/Cu界面釘扎,歸因于位錯(cuò)與un-Fe顆粒之間的相互作用,un-Fe似乎被位錯(cuò)剪切(圖4b中黃色箭頭標(biāo)注)。因此,由un-Fe和n-Fe顆粒引起的位錯(cuò)釘扎促進(jìn)了位錯(cuò)相互作用而提高強(qiáng)度 []。
研究表明,顆粒剪切和Orowan環(huán)機(jī)制[26,,]描述了納米析出強(qiáng)化的屈服強(qiáng)度。因此,我們通過(guò)使用模量強(qiáng)化(?σModulus)和共格強(qiáng)化(?σCoherency)模型[46],估算了完全共格的un-Fe對(duì)Cu-12Sn-1.5Ni-0.08Fe合金的σy貢獻(xiàn)分別為約38 MPa和約46 MPa,接近實(shí)驗(yàn)結(jié)果的25.99 MPa。同樣在Cu-12Sn-1.5Ni-0.83Fe合金中,un-Fe (?σModulus模量強(qiáng)化約13 MPa,?σCoherency共格強(qiáng)化約16 MPa) 和半共格的n-Fe (~123 MPa,通過(guò)Orowan環(huán)模型估計(jì)) ,二者對(duì)σy的總強(qiáng)化貢獻(xiàn)約為~136/~139 MPa,基本上與實(shí)際σy增量58.60 MPa一致。關(guān)于強(qiáng)化響應(yīng)的估計(jì)細(xì)節(jié)請(qǐng)參閱補(bǔ)充資料的第2部分。需要注意的是,由于強(qiáng)化模型中使用的參數(shù)(表S2,補(bǔ)充資料)以及納米析出相的統(tǒng)計(jì)結(jié)果(表1)不可避免的存在偏差,因此估算的強(qiáng)化貢獻(xiàn)不能與實(shí)驗(yàn)值完全一致。
免責(zé)聲明:本網(wǎng)站所轉(zhuǎn)載的文字、圖片與視頻資料版權(quán)歸原創(chuàng)作者所有,如果涉及侵權(quán),請(qǐng)第一時(shí)間聯(lián)系本網(wǎng)刪除。
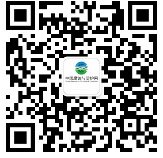
官方微信
《腐蝕與防護(hù)網(wǎng)電子期刊》征訂啟事
- 投稿聯(lián)系:編輯部
- 電話:010-62316606
- 郵箱:fsfhzy666@163.com
- 腐蝕與防護(hù)網(wǎng)官方QQ群:140808414