導(dǎo)語:本研究采用淬火工藝制備了無析出的低碳超高強(qiáng)度鋼,并設(shè)計(jì)了多尺度富銅和 NiAl 的共析出強(qiáng)化,分別通過淬火-回火 (QT) 和淬火-分配-回火 (QPT) 工藝提高疲勞性能。淬火鋼的微觀組織顯示出板條馬氏體 (LM) 和顆粒貝氏體 (GB) 的典型混合微觀結(jié)構(gòu)。在 550 °C 下老化 1 h 后,高密度 (1.945 × ) 的 B2-NiAl 和 B2 核心-9R 殼納米顆粒均勻共沉淀,使屈服強(qiáng)度和高周疲勞強(qiáng)度分別從 965 MPa 和 384.6 MPa 大幅提高到 1548 MPa 和 510.7 MPa。疲勞性能的顯著改善歸因于大量小尺寸納米顆粒的移動(dòng),這些納米顆粒阻礙了位錯(cuò)的運(yùn)動(dòng)以形成高密度位錯(cuò)纏結(jié) (HDDT) 和細(xì)胞結(jié)構(gòu),從而降低了晶界的應(yīng)力集中。此外,幾何相分析 (GPA) 揭示了小尺寸多組分沉淀物周圍存在微應(yīng)變,不太可能引起微裂紋萌生,從而提高了疲勞性能。QPT 處理后,共沉淀的納米顆粒表現(xiàn)出多尺度分布,數(shù)密度顯著降低,為 1.005 × 1023m-3,并鑒定出典型的大尺寸FCC-Cu顆粒,削弱了析出強(qiáng)化,導(dǎo)致屈服強(qiáng)度和疲勞強(qiáng)度分別達(dá)到1396 MPa和424.5 MPa。此外,由于位錯(cuò)和旁路納米顆粒的運(yùn)動(dòng),GNDs 明顯積累在反向奧氏體 (RA) 和基體之間的界面處,這增加了界面處微裂紋萌生的趨勢。此外,在 FCC-Cu 顆粒界面處積累的高應(yīng)變增加了疲勞損傷的風(fēng)險(xiǎn),限制了疲勞性能的改善。
由于強(qiáng)度(屈服強(qiáng)度>1.2 GPa)、延展性(伸長率>10%)和可焊性的出色結(jié)合,添加銅的低碳超高強(qiáng)度鋼(LCUHSS)有望成為建筑機(jī)械(如大噸位起重機(jī))領(lǐng)域的下一代理想工程材料(Beladi等人,2017;Fan等人,2022;Jiao等人,2015;Kapoor等人,2016;Khan等人,2012;Kong等人,2021;Li等人,2020;Xu等人,2020)。此外,LCUHSS擠壓的無縫鋼管用于大噸位起重機(jī)的臂架結(jié)構(gòu),滿足了減輕自重、提高結(jié)構(gòu)承載能力和安全性的迫切需要。LCUHSS的超高強(qiáng)度源于控制阻礙位錯(cuò)運(yùn)動(dòng)的內(nèi)部障礙物的形成,包括晶粒細(xì)化(Chu等人,2024;Wang等人,2023a;Wang等,2023b)、形成高密度位錯(cuò)纏結(jié)(Pan等人,2023)和沉淀強(qiáng)度。
在過去的幾十年里,為了追求抗疲勞性的顯著提高,人們系統(tǒng)地研究了各種改性的沉淀強(qiáng)化部件,包括納米碳化物的誘導(dǎo)沉淀和B2-NiAl強(qiáng)化相等(Feng等人,2021;Ghosh等人,2021,Mai等人,2023,Tian等人,2021)。Ghosh等人報(bào)告稱,通過多軸鍛造(MAF)加工形成納米碳化物強(qiáng)化的超細(xì)晶粒,低碳微合金鋼的疲勞強(qiáng)度從270 MPa提高到355 MPa(Ghosh等人,2021)。Mai等人報(bào)告稱,Nb(C,N)沉淀物被引入低碳渦輪機(jī)轉(zhuǎn)子鋼的馬氏體基體中,有效地阻礙了位錯(cuò)線的運(yùn)動(dòng),提高了疲勞極限(Mai等人,2023)。先前的研究表明,富銅和NiAl納米粒子的共沉淀強(qiáng)化顯著提高了鋼的強(qiáng)度,但其對疲勞性能的協(xié)同作用尚不清楚(Jiao等人,2015;Yang等人,2023b)。此外,為了大大提高沖擊韌性并獲得優(yōu)異的強(qiáng)韌性組合,通過淬火-分配-回火(QPT)工藝將大量小尺寸的反奧氏體和富銅和NiAl的多尺度納米粒子同時(shí)引入LCUHSS中(Li等人,2018;Yang等人,2024)。然而,一系列熱處理過程伴隨著逆奧氏體的復(fù)雜微觀結(jié)構(gòu)轉(zhuǎn)變和納米粒子的自然結(jié)構(gòu)、尺寸參數(shù),導(dǎo)致疲勞性能與微觀結(jié)構(gòu)演變之間的內(nèi)在關(guān)系不明確。事實(shí)上,富銅和NiAl納米粒子對LCUHSS疲勞壽命的影響尚未得到系統(tǒng)報(bào)道,相關(guān)的疲勞失效機(jī)制仍知之甚少。
傳統(tǒng)的疲勞損傷機(jī)制表明,高強(qiáng)度金屬材料持久滑移帶中不可逆局部疲勞損傷的累積會(huì)引發(fā)疲勞斷裂(Li等人,2011)。通常,位錯(cuò)很容易在無沉淀的LCUHSS的晶界、夾雜物和偏析區(qū)等局部缺陷位置嚴(yán)重堆積,導(dǎo)致疲勞損傷的局部堆積(Mai等人,2023)。然而,沉淀硬化鋼中的納米顆粒強(qiáng)烈地釘扎了位錯(cuò),導(dǎo)致位錯(cuò)堆積和局部疲勞損傷累積的機(jī)制更加復(fù)雜(Ghosh等人,2021;Mai等人,2023)。沉淀硬化鋼的疲勞失效機(jī)理包括兩個(gè)代表性理論。一是高密度小尺寸納米粒子均勻分散在基體上,有效阻礙位錯(cuò)運(yùn)動(dòng),從而大大減輕位錯(cuò)積累和疲勞損傷引起的局部應(yīng)力集中(Feng等人,2021;Mai等人,2023)。另一項(xiàng)研究表明,沉淀的第二相顆粒降低了微觀結(jié)構(gòu)的穩(wěn)定性,并可能成為循環(huán)加載過程中裂紋萌生的來源,導(dǎo)致局部損傷(Hossein-Nedjad等人,2008;Tian等人,2021;Wang等人,2017a)。在過硬化的基體中,位錯(cuò)在第二相顆粒處積聚引起的局部應(yīng)力集中超過了顆粒的臨界斷裂強(qiáng)度,微裂紋往往在斷裂的第二相顆粒上開始(Wang等人,2017a)。在軟基體中,在循環(huán)加載過程中,通過分離或脫粘,在軟基體和硬相顆粒之間的界面上很容易形成微裂紋,最終導(dǎo)致斷裂失效(Hossein-Nedjad等人,2008;Liu等人,2023)。此外,研究表明,較硬的第二相顆粒周圍的應(yīng)力容易集中在顆粒的頂部和底部,從而導(dǎo)致脫粘和開裂,而對于較軟的顆粒,應(yīng)力很容易集中在中間,從而導(dǎo)致顆粒的直接斷裂(Fincato等人,2020)。兩種疲勞失效機(jī)制的觸發(fā)取決于基體強(qiáng)度、沉淀物-基體界面特性和納米顆粒臨界斷裂強(qiáng)度的競爭效應(yīng)。在LCUHSS中,高密度的小尺寸納米粒子阻礙了位錯(cuò)的運(yùn)動(dòng)和積累,大大提高了材料的疲勞性能。然而,大尺寸納米粒子的釘扎效應(yīng)較弱,位錯(cuò)容易在界面(包括晶界和沉淀界面)移動(dòng)和積累,從而引起局部應(yīng)力集中,從而引發(fā)微裂紋,顯著降低循環(huán)應(yīng)力下的疲勞性能。富銅和NiAl納米粒子的自然結(jié)構(gòu)和尺寸在不同的熱處理工藝后經(jīng)歷了復(fù)雜的轉(zhuǎn)變,這極大地影響了LCUHSS的疲勞斷裂機(jī)制。事實(shí)上,多組分納米粒子與LCUHSS疲勞性能之間的內(nèi)在關(guān)系尚未建立。有必要闡明富銅和NiAl納米粒子與位錯(cuò)的相互作用及其對疲勞斷裂機(jī)制的影響,這對LCUHSS的應(yīng)用至關(guān)重要。
在這項(xiàng)研究中,我們設(shè)計(jì)了一種通過多尺度富銅和NiAl納米粒子共沉淀增強(qiáng)的LCUHSS無縫管,并闡明了納米粒子對LCUHSS疲勞行為的影響機(jī)制,旨在探索提高結(jié)構(gòu)材料疲勞強(qiáng)度的新方法。采用掃描電鏡(SEM)、X射線衍射(XRD)、電子背散射衍射(EBSD)和高分辨率透射電鏡(HRTEM)對實(shí)驗(yàn)鋼的微觀結(jié)構(gòu)進(jìn)行了表征,并研究了鋼的高周疲勞(HCF)性能。研究結(jié)果有望為優(yōu)化高強(qiáng)度鋼的抗疲勞性能提供基礎(chǔ)和思路,并有助于為抗疲勞設(shè)計(jì)創(chuàng)造更多可能性。
相關(guān)研究以“Enhancing fatigue life of low-carbon ultra-high strength steel by inducing multi-component precipitates”發(fā)表在International Journal of Plasticity上
鏈接:https://www.sciencedirect.com/science/article/abs/pii/S0749641925000464
表1
設(shè)計(jì)LCUHSS的化學(xué)成分(重量%)。
圖1
實(shí)驗(yàn)鋼的軋制
(a)和熱處理工藝(b)示意圖。(c) 拉伸、疲勞和金相試樣的取樣位置,(d)和(e)分別是拉伸和疲勞試樣的尺寸,(f)是應(yīng)力比R=0.1、穩(wěn)定頻率為75 Hz的三角波形,以及夾緊疲勞試樣。
圖2顯示了不同熱處理?xiàng)l件下設(shè)計(jì)的實(shí)驗(yàn)鋼的微觀結(jié)構(gòu)和相組成。所有實(shí)驗(yàn)鋼均表現(xiàn)出板條馬氏體(LM)和粒狀貝氏體(GB)的典型特征。在淬火鋼中,圖2a1顯示了約88.3%的LM和約11.7%的GB的混合微觀結(jié)構(gòu),LM具有清晰的板條邊界,GB具有塊狀貝氏體鐵素體基體。在圖2a2中,大量高密度位錯(cuò)纏結(jié)(HDDT)分散在寬度為200-600nm的LM鐵氧體板條內(nèi),并顯示出LM鐵素體的明顯板條界面。在550℃下時(shí)效60分鐘后,QT550鋼的微觀結(jié)構(gòu)表現(xiàn)出回火板條馬氏體(TM)的典型特征,如圖2b1和2b2所示。值得注意的是,TM的板條界面模糊,位錯(cuò)纏結(jié)明顯減弱,這與時(shí)效過程中位錯(cuò)和亞晶粒邊界的湮滅有關(guān)(Zou等人,2021)。通過XRD分析了實(shí)驗(yàn)鋼的相組成,圖2d顯示了不同熱處理?xiàng)l件下的XRD光譜。淬火鋼和QT550鋼顯示出典型的、
和
衍射峰,表明這兩種實(shí)驗(yàn)鋼都是BCC相。在QPT650鋼中,發(fā)現(xiàn)了明顯的奧氏體衍射峰
、
和
,根據(jù)改進(jìn)的Miller方法計(jì)算出奧氏體的體積分?jǐn)?shù)為~7.0%(Miller,1964;Yang等人,2023a)。圖2e和2f分別顯示了基于MWH方法的不同熱處理?xiàng)l件下實(shí)驗(yàn)鋼的ΔK與K
的擬合線斜率和位錯(cuò)密度((Peˇsiˇcka等人,2003;Yang等人,2023b)。結(jié)果表明,淬火鋼的位錯(cuò)密度最大,達(dá)到1.38×
,斜率最高,這與圖2a2中的TEM形貌一致。時(shí)效和分割處理后,位錯(cuò)密度顯著下降至5.44×
和2.39×
,分別對應(yīng)QT550鋼和QPT650鋼。
圖2
不同熱處理狀態(tài)下實(shí)驗(yàn)鋼的初始顯微組織。
(a1)SEM和(a2)TEM圖像顯示了淬火鋼中具有高密度位錯(cuò)纏結(jié)的LM和GB的典型形態(tài)。(b1)和(b2)顯示了QT550鋼中回火LM、GB和纏結(jié)位錯(cuò)的形態(tài)。(c1)和(c2)顯示了QPT650鋼中典型的回火LM、GB、SM和RA。(d) 是不同熱處理?xiàng)l件下RA的X射線衍射圖和體積分?jǐn)?shù)。(e)(f)分別是ΔK與K和位錯(cuò)密度的對應(yīng)擬合線。
圖3
分別在(a)淬火鋼、(b)QT550鋼和QPT650鋼中的(a1-c1)逆極圖(IPF)圖、(a2-c2)核平均錯(cuò)向(KAM)圖。
圖4
QT550鋼(a-d)和QPT650鋼(ei)中多組分沉淀物的TEM暗場顯微照片(a和e)和尺寸分布(b和f)以及相應(yīng)納米粒子的化學(xué)成分(c、d、g和h)和HRTEM形態(tài)特征(c1-d4和g1-i2)。
表2 QT550鋼和QPT650鋼中納米粒子的平均半徑和數(shù)密度。
圖5顯示了實(shí)驗(yàn)鋼在不同熱處理狀態(tài)下的單軸拉伸性能。對于淬火鋼,平均屈服強(qiáng)度(YS)達(dá)到965 MPa,極限抗拉強(qiáng)度(UTS)為1216 MPa,斷裂伸長率為16.9%。在550℃下老化60分鐘后,由于納米沉淀強(qiáng)化的增強(qiáng),應(yīng)力-應(yīng)變曲線顯著增加。平均YS顯著增加到1491 MPa,UTS增加到1548MPa,斷裂伸長率降低到11.2%。QPT650鋼的平均YS略降至1374 MPa,UTS達(dá)到1396 MPa,斷裂伸長率為14.0%,這是由于納米粒子粗化和數(shù)量密度降低削弱了沉淀強(qiáng)化。
圖5
(a) 不同熱處理狀態(tài)下實(shí)驗(yàn)鋼的工程應(yīng)力-應(yīng)變曲線和(b)平均屈服強(qiáng)度和抗拉強(qiáng)度
圖6
不同熱處理狀態(tài)下實(shí)驗(yàn)鋼的HCF性能。
(a) S-N曲線,以及(b)疲勞強(qiáng)度和極限抗拉強(qiáng)度之間的關(guān)系,(c)疲勞強(qiáng)度系數(shù)σf'與疲勞強(qiáng)度指數(shù)b的關(guān)系,以及(d)疲勞比與抗拉強(qiáng)度的關(guān)系,并與文獻(xiàn)中的先進(jìn)高強(qiáng)度鋼進(jìn)行比較。虛線是疲勞強(qiáng)度的等值線,并標(biāo)記了相應(yīng)的值。
表3不同熱處理狀態(tài)的實(shí)驗(yàn)鋼的詳細(xì)HCF參數(shù)
圖7顯示了實(shí)驗(yàn)鋼在低Nf(高應(yīng)力幅)和高Nf(低應(yīng)力幅”)條件下的疲勞斷裂形態(tài)特征。結(jié)果表明,所有試樣中的主要疲勞裂紋都是從表面開始并擴(kuò)展到試樣內(nèi)部的,因此所有試樣的疲勞源都位于試樣表面。疲勞斷裂面被劃分為四個(gè)區(qū)域:疲勞源區(qū)(FSZ)、穩(wěn)定裂紋擴(kuò)展區(qū)(SCPZ)、快速裂紋傳播區(qū)(RCPZ)和瞬時(shí)斷裂區(qū)(IFZ)
圖7
通過SEM分別觀察了(a和d)淬火鋼、(b和e)QT鋼和(c和f)QPT鋼在(a-c)高Nf和(d-e)低Nf下的HCF斷口形貌。使用CLSM觀察了穩(wěn)定裂紋擴(kuò)展區(qū)中的相應(yīng)3D光學(xué)輪廓儀(a4-f4)。
圖8
GND分別繪制了低(a1-c1)和高(a2-c2)應(yīng)力振幅條件下疲勞裂紋源附近的GND分布圖,以及(a)淬火鋼、(b)QT550鋼和(c)QPT650鋼的相應(yīng)GND分布值(a3-c3)。
為了進(jìn)一步闡明位錯(cuò)亞結(jié)構(gòu)對疲勞性能的影響,位錯(cuò)增殖、位錯(cuò)胞和高密度位錯(cuò)纏結(jié)(HDDT)如圖9所示。
圖9
分別對(a)淬火鋼、(b)QT550鋼和(c)QPT650鋼在低應(yīng)力幅和高應(yīng)力幅條件下典型位錯(cuò)結(jié)構(gòu)(a1-c1,a3-c3)的演變以及相應(yīng)的局部位錯(cuò)特征(a2-c2,a4-c4)的放大圖。
圖10顯示,QT550鋼中剪切強(qiáng)化占主導(dǎo)地位,總沉淀強(qiáng)化為585.3 MPa,剪切強(qiáng)化和奧羅萬強(qiáng)化的貢獻(xiàn)分別為528.6 MPa和251.2 MPa。對于QPT650鋼,Orowan強(qiáng)化的貢獻(xiàn)大大增加到366.0 MPa,而由于369.8 MPa的低剪切強(qiáng)化,總沉淀強(qiáng)化降低到520.3 MPa。
圖10
多種強(qiáng)化機(jī)制對實(shí)驗(yàn)鋼的強(qiáng)化貢獻(xiàn)。
圖11
(a-c)QT550鋼和(d-f)QPT650鋼在(a和d)低應(yīng)力幅和(b和e)高應(yīng)力幅條件下位錯(cuò)沉淀相互作用的TEM形貌。(c) 是位錯(cuò)線剪切的小型B2-NiAl納米顆粒的HRTEM形態(tài),(c1-c2)通過GPA分析顯示了B2-NiA1納米顆粒周圍的和
應(yīng)變分布,(c3)是沿指定線的相應(yīng)應(yīng)變分布。(f) 是短棒狀FCC Cu顆粒與位錯(cuò)相互作用的HRTEM形態(tài),(f1-f2)顯示了FCC Cu顆粒周圍的
和
應(yīng)變分布,(f3)是相應(yīng)的應(yīng)變分布。
圖12
淬火鋼、QT550鋼和QPT650鋼在低應(yīng)力幅水平下的HCF斷裂機(jī)理示意圖。
在這項(xiàng)研究中,通過B2-NiAl和富銅多組分納米粒子的共沉淀強(qiáng)化結(jié)合熱處理,開發(fā)了具有高疲勞性能的LCUHSS無縫管。系統(tǒng)研究了循環(huán)應(yīng)力下微觀結(jié)構(gòu)、拉伸性能和疲勞性能的演變以及疲勞斷裂機(jī)制。主要結(jié)論如下:
(1) 設(shè)計(jì)的LCUHSS在淬火狀態(tài)下表現(xiàn)出LM和GB的典型混合微觀結(jié)構(gòu),位錯(cuò)密度高達(dá)1.38×。在550℃下時(shí)效1小時(shí)后,微觀結(jié)構(gòu)保持了LM和GB的特征,小尺寸B2 NiAl和B2核-9R殼納米粒子共沉淀在LM基體上的位錯(cuò)密度。在QPT650鋼中,觀察到典型的RA和SM,位錯(cuò)密度較低,為2.39×
。
(2) 淬火鋼的屈服強(qiáng)度為965MPa,疲勞強(qiáng)度為384.5MPa。在550℃下老化60分鐘后,屈服強(qiáng)度顯著提高到1548 MPa,最大疲勞強(qiáng)度達(dá)到510.7 MPa,這歸因于剪切強(qiáng)化的顯著增強(qiáng)~528.6 MPa。QPT650鋼的屈服強(qiáng)度略降至1396MPa,疲勞強(qiáng)度為424.5MPa。
(3) 在高應(yīng)力振幅條件下(循環(huán)次數(shù)~),三種不同熱處理狀態(tài)下的試樣均顯示出明顯的晶間斷裂。大量位錯(cuò)通過平面滑移在LM的包邊界處積累,形成HDDT,這是導(dǎo)致疲勞裂紋沿晶斷裂的主要因素。
(4) 在低應(yīng)力振幅條件下(循環(huán)次數(shù)~),QT550鋼的初始位錯(cuò)密度較低,大量的小尺寸納米粒子釘扎位錯(cuò)有效地阻礙了位錯(cuò)運(yùn)動(dòng)形成HDDT,大大提高了實(shí)驗(yàn)鋼的損傷容限和抗疲勞裂紋萌生能力,導(dǎo)致完全穿晶斷裂。然而,在QPT650鋼中,納米顆粒的明顯粗化削弱了剪切強(qiáng)化,GND移動(dòng)并積聚在RA和LM板條之間的界面以及大尺寸FCC Cu顆粒的界面上,導(dǎo)致應(yīng)變集中和穿晶和晶間混合斷裂,從而顯著降低疲勞性能。
免責(zé)聲明:本網(wǎng)站所轉(zhuǎn)載的文字、圖片與視頻資料版權(quán)歸原創(chuàng)作者所有,如果涉及侵權(quán),請第一時(shí)間聯(lián)系本網(wǎng)刪除。
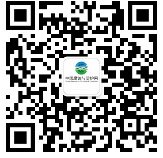
官方微信
《腐蝕與防護(hù)網(wǎng)電子期刊》征訂啟事
- 投稿聯(lián)系:編輯部
- 電話:010-62316606
- 郵箱:fsfhzy666@163.com
- 腐蝕與防護(hù)網(wǎng)官方QQ群:140808414