鋰的添加不僅降低了鎂合金的密度,而且提高了其在室溫下的可成形性。這些優勢滿足了航空業的嚴格要求,從而引起了對鎂鋰合金的高度重視。Mg-Li二元合金的晶體結構取決于Li的添加濃度。然而,低強度和差的耐腐蝕性成為其廣泛應用的兩個障礙。為了使Mg-Li合金達到中等強度,添加了Al,Zn和稀土(RE)元素以形成各種類型的沉淀物。除了合金化之外,微結構細化也是提高雙相Mg-Li合金性能的另一種有效方法,即兩相分布(相細化)是提高雙相鎂鋰合金力學性能的有效方法。疊軋和高壓扭轉等劇烈塑性變形方法可以細化兩相組織,但是由于成本和試樣尺寸限制而難以實現工業化。雖然陸續出現了一些新方法,但是都存在一些不足之處,比較難以控兩相的分布及尺寸等。
來自重慶理工大學和重慶大學的研究人員首次在室溫雙相鎂鋰合金中發現應變誘導相變(SIP)現象。研究表明:高密度應變誘導相變細化了相結構,并在不犧牲延展性的情況下極大地提高了材料的強度,可達到抗拉258MPa。相關論文以題為“Strengthening a dual-phase Mg–Li alloy by strain-induced phase transformation at room temperature”于4月1日發表在Scripta Materialia。
論文鏈接:https://www.sciencedirect.com/science/article/pii/S1359646220300026
研究人員對擠壓Mg-9.5Li-1Zn合金設計了兩類總壓下率71%的軋制方案,即在室溫沿軋向軋制16道次的單方向軋制(SDR),第二種是多方向軋制16道次(MDR),每道次之間旋轉45°(見圖1 )。在多方向軋制中,大大增強了應變誘導相變,并相互交叉將基體分成多個單元。多方向軋制不僅改變了應變誘導相變的密度,而且還改變了其形態。與單方向軋制樣品中的應變誘導相變相比,多方向軋制產生的相變由于數量大且分布交錯,有效地打破了β-Li相的連續性,β-Li相的強化可以大大提高整個樣品的機械性能。單方向軋制后試樣屈服強度由85MPa幾乎翻了一倍成160MPa,多方向軋制則獲得了約227MPa的屈服強度和258MPa的抗拉強度,而伸長率仍處于中等水平。

圖1SDR樣品的微觀結構在TD平面上軋制(a)10%;(b)30%;(c)50%;(d)SDR示意圖;(e)70%;(f)ND平面上軋制;(g)MDR示意圖;(h)TD;(i)ND

圖2(a)初始,SDR和MDR樣品沿RD,TD和45°延伸的流動曲線;(b)Mg-Li合金的力學性能
在傅立葉逆變換圖中,α-Mg相的不同滑動面中的位錯突出。與該應變誘導相變中的棱形滑移相比,錐面滑移很容易被激活。該結果與冷軋時初始α-Mg的變形行為相關,表明應變誘導相變的變形行為與大尺寸的α-Mg相類似。

圖3 (a)SEM;(b)亮場;(c)在SIP上具有SAED模式的HADDF-STEM圖像;(d)SAED模式的相界上的HR-TEM;(e,f)在(d)中綠色和黃色矩形;(g,h)SIP階段內部的位錯結構
分析織構發現Schmid Factor有明顯區別。軋制方向的變化可能會使得在多方向軋制中不同滑移面上的位錯有更多相互作用機會。隨著滑移的進行,位錯相互作用大大增強。隨著滑移平面較大的扭折,應變誘導相變的有利位置將大大增多。

圖4(a)沿RD,TD和45°軋制的β-Li的Schmid Factor;(b)沿三個方向軋制的Schmid Factor列表
總的來說,劇烈塑性變形的應變誘導部分BCC結構的β-Li相在室溫下轉變為HCP α-Mg相。不同滑移系統的激活對應變誘導相的形態和分布有重要影響。多方向軋制大大增強了雙相Mg-Li合金中的應變誘導相變行為。β相中由應變引起的相互纏繞的相結構大大細化了相結構,并提高了雙相Mg-Li合金的力學性能。
免責聲明:本網站所轉載的文字、圖片與視頻資料版權歸原創作者所有,如果涉及侵權,請第一時間聯系本網刪除。
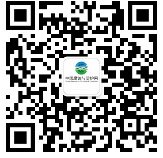
官方微信
《中國腐蝕與防護網電子期刊》征訂啟事
- 投稿聯系:編輯部
- 電話:010-62316606-806
- 郵箱:fsfhzy666@163.com
- 中國腐蝕與防護網官方QQ群:140808414