金屬絲電弧定向能量沉積(DED)-通常稱為金屬絲電弧增材制造(WAAM)是一種新興的制造技術,它將傳統電弧焊接的概念轉變為自動化制造方法,并能夠設計和加工具有三維幾何形狀的大型部件。雖然許多不同的焊接技術,如氣體金屬極電弧焊(GMAW)和等離子弧焊(PAW),原則上可以實現自動化,但由于鎢電極和基底之間的穩定電弧,將鎢極氣體保護焊(GTAW)轉換為WAAM工藝,可以減少飛濺,實現金屬轉移。在加工過程中,焊槍的計算機輔助移動允許以1–10 kg/h的速度逐層沉積焊道,從而實現替代添加劑制造(AM)方法無法實現的生產能力和能力。盡管傳統GTAW的基本原理適用于WAAM工藝,但與該AM技術相關的重復熱循環導致的熱傳遞梯度導致凝固特性和微觀結構演變,與使用傳統焊接工藝處理的材料明顯不同。傳統多道焊的工藝可以被描述為與使用WAAM技術處理材料類似,然而,WAAM中沒有基材導致制造過程中的熱傳遞主要通過先前沉積的層和基底發生。多線進給系統的引入為WAAM材料的設計和加工提供了獨特的機會。控制單個金屬絲的進給速率的能力不僅能夠使用市售的標準金屬絲對具有廣泛化學成分的材料進行原位合金化,而且能夠處理在整個材料中表現出漸變或圖案狀成分變化的成分梯度材料(CGM)。兩種設計策略都可用于加工具有特定位置化學性質和微觀結構和機械性能的獨特組合的材料。然而,CGM需要在局部和宏觀長度尺度上進行表征,特別是在強度和抗斷裂性方面,這是用于結構應用的關鍵特性。雖然通過激光金屬沉積(LMD)和激光粉末床融合(LPBF)等其他AM技術制造CGM是可行的,但WAAM工藝具有較高的沉積速率等優點,并能夠在單層內改變成分。
高強度與重量比、優異的耐腐蝕性和良好的焊接性等性能組合使許多鋁合金成為汽車、航空航天和國防工業中的主要材料。此外,這些行業通常需要從AM技術的設計自由中受益的三維幾何結構。盡管近年來已經使用WAAM成功地加工了各種系列的鋁合金,例如Al-Cu(2xxx系列)、Al-Si(4xxx系列),在凝固過程中,鋁氧化物的容易形成以及合金元素與污染物(例如碳氫化合物或水分)的相互作用使得制造無氣孔、雜質和裂紋的部件具有挑戰性。此外,由于電弧產生的高溫,熔池表面的峰值溫度可能超過沸點,因此蒸汽壓力可能高于大氣壓,從而增加了處理鋁合金的復雜性。例如,4xxx系列的合金——它們在全球80%以上的鋁制品中使用——可能存在縮孔(由不同元素和相的熱膨脹系數不同導致)和凝固裂紋形式的缺陷。然而,Langelandsvik等人最近的工作表明,WAAM AlSi12可加工至<1%的孔隙率,這與傳統的加工工藝(如砂和鋼模鑄造)相當。重要的是,與鑄造材料相比,由于WAAM Al-Si合金加工過程中的高冷卻速率而形成的精細微觀結構通常會導致優異的機械性能。雖然強度傾向于各向同性,但與正交(水平)試樣相比,平行(垂直)于構建方向測試的試樣的延性通常降低約20-35%。在含有較少Si的Al合金中,這種差異明顯較小,這表明除了工藝參數外,用于加工的Si的量可能影響各向異性。雖然多線原位合金化成功地用于處理AlSi7Mg和AlSi12饋線(使用雙線冷金屬轉移(CMT)系統)并制造化學均勻的AlSi10Mg合金,但據作者所知,它尚未用于制造CGM。
在此,新南威爾士大學Bernd Gludovatz團隊首次使用雙進料GTAW系統加工WAAM梯度Al-Si合金,從而證明了利用這種添加劑制造技術加工大型Al-Si組件的可行性,并對其成分進行了特定位置的修改。我們使用市售的饋線,可以處理位于Al-Si相圖亞共晶區域內的材料。迄今為止,尚未研究變形和破壞特征,特別是Si濃度對WAAM加工材料微觀結構形成和機械性能的影響。因此,我們沿著材料的構建高度表征了微觀和介觀結構特征,并評估了在兩個正交方向(平行于構建方向和垂直于構建方向)上,強度和抗斷裂性方面的機械性能如何隨著Si濃度的變化而變化。我們的研究結果表明,增加Si濃度會影響強度和延性,但對成分梯度Al-Si合金的斷裂抗力影響有限。此外,與延性相比,WAAM生產的CGM的斷裂韌性相對各向同性,并且始終高于鑄造材料。這使得WAAM處理的Al-Si合金能夠用于需要特定位置機械性能的各種應用。相關成果以題“Strength and fracture resistance of in-situ alloyed compositionally-graded Al-Si processed by dual-wire arc directed energy deposition”發表在增材制造頂刊Additive Manufacturing上。
鏈接:https://www.sciencedirect.com/science/article/abs/pii/S2214860422006807
圖1.(a)雙饋電線GTAW系統;(b)最終的Al-Si梯度材料;(c)使用WAAM的成分分級鋁硅合金制造示意圖(紅色虛線表示焊槍的擺動);(d)拉伸和C(T)樣品相對于構建方向的取向參考。
圖2.(a)WAAM Al-Si材料的介觀結構的3D視圖;(b)熔池邊界附近的SE-SEM圖像;顯示Si顆粒(c)來自熔池區域和(d)在熔池邊界內的放大SE-SEM圖像;(e)BSE-SEM圖像顯示元素對比度;(f–g)(e)插圖所示掃描區域的EDS元素映射。
圖3.沿構建方向從光學發射光譜獲得的化學分析,理論化學濃度用虛線表示;Si濃度讀數在距離襯底約12毫米(±0.0215 wt%)處的小誤差使該位置的誤差條無法與符號區分開來。插圖(a–c)顯示了相應區域的微觀結構和孔隙率(黃色圓圈)。圖中所示的相對密度是用阿基米德原理測量的。(d) 顯示了在ZY平面中獲得的光學顯微照片,并且(e)顯示了沿著構建方向的相應硬度圖。
圖4.取自(a1–4)頂部、(b1–4)中部和(c1–4)底部區域的Al和Si的OM、EBSD和EDS圖。(紅色和綠色分別表示Al和Si)。
圖5.從(a)底部、(b)中部和(c)頂部區域水平(X)和垂直(Z)測試的樣品的拉伸應力-應變曲線。還顯示了:在(d)水平和(e)垂直方向上測試時三個區域的比較;從(f)底部、(g)中部和(h)頂部區域垂直測試樣品的斷裂表面;以及(i)來自從頂部區域測試的樣品的OM圖像,顯示了在垂直測試樣品中主要沿著熔池邊界發生的失效。
圖6.(a)從現場拉伸試驗中獲得的代表性應力-應變曲線,該試驗對取自建筑頂部區域的水平樣品進行了中間階躍加載。(b)與整體應變相比,α-Al和共晶Al-Si區域在兩個不同位置的局部應變。在加載的(c,d)之前和最后階段(e,f)拍攝的頸縮區域的光學顯微結構圖像。
圖7.Al-Si梯度結構材料不同區域的裂紋擴展阻力曲線(R曲線)。關于(a)頂部、(b)中部和(c)底部區域的C(T)樣本的不同取向的R曲線比較。關于不同Si濃度的R曲線比較(d),裂紋生長垂直于構建方向。(g)不同區域的組合平均R曲線。(h)KJIc值相對于Si濃度。(i)試樣位置和裂紋擴展方向示意圖。
圖8.(a)顯示從疲勞預裂紋區到過載失效區斷裂特征變化的顯微圖。(b,c)過載斷裂表面的放大SE-SEM圖像。
圖9.沿B、M和T區域的(a–c)熔池邊界和(d–f)熔池內部共晶Si的尺寸比較。
圖10.(a)原位拉伸試驗最后階段獲得的顯示頸縮區域塑性變形的光學顯微結構圖像。(b,c)顯示滑移帶和裂紋萌生的高分辨率SE-SEM圖像。黃色箭頭表示沿兩相界面的裂紋。(d)KAM圖顯示了α-Al和共晶Al-Si邊界附近的位錯停滯。(e)變形機制示意圖。
圖11.(a)SE-SEM圖像顯示了裂紋尖端之前的微裂紋形成。紅色虛線表示裂紋尖端的輪廓,黃色箭頭表示微裂紋。(b,c)OM圖像顯示了來自T區域的ZX樣品的裂紋路徑分析。
雙絲電弧增材制造(WAAM)用于Al-Si的原位合金化,其化學成分沿構建高度梯度分布。研究了改變Si濃度對微觀和細觀結構以及硬度、拉伸應力應變響應和裂紋擴展阻力曲線(R曲線)行為方面的力學性能的影響。根據此研究的結果,可以得出以下結論:
1.使用具有AlSi5和AlSi12導線的雙WAAM系統,得到具有以下梯度化學成分的Al-Si合金∼ 6.5–9.5 % Si濃度。整個構建方向上的化學分析表明,所獲得的組合物與理論濃度分布計算非常一致,從而確認原料的適當混合和工藝的可行性。
2.微觀和細觀結構分析表明,α-Al枝晶和共晶Al-Si的體積分數受Si濃度的控制,Si含量的增加導致形成更寬的枝晶結構,共晶相的體積分數更大。
3.兩個正交方向的拉伸應力應變測試顯示強度隨Si濃度增加而增加,而無論Si濃度如何,與水平測試方向相比,沿構建方向測試的樣品顯示出較低的破壞應變。強度和延性的各向異性隨著Si濃度的增加而增加。
4.原位拉伸試驗表明,塑性變形時,由于α-Al枝晶和共晶Al-Si的局部應變變形能力不匹配,沿α-Al樹枝晶和共晶體Al-Si的界面以微裂紋的形式開始破壞。
5.斷裂韌性結果在48–51 MPa√m范圍內,并且對Si濃度和測試取向的影響很小。這與Si顆粒在其界面處的脫粘引起的裂紋萌生以及主要控制裂紋擴展的相應微裂紋有關。
免責聲明:本網站所轉載的文字、圖片與視頻資料版權歸原創作者所有,如果涉及侵權,請第一時間聯系本網刪除。
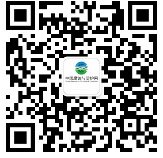
官方微信
《腐蝕與防護網電子期刊》征訂啟事
- 投稿聯系:編輯部
- 電話:010-62316606-806
- 郵箱:fsfhzy666@163.com
- 腐蝕與防護網官方QQ群:140808414