【激光表面改性技術(shù)】新疆大學(xué)孫文磊教授等:激光熔覆CoCrFeNiTi高熵合金工藝優(yōu)化及預(yù)測(cè)模型研究
2024-09-05 11:55:56
作者:王宇迪,喬紅超,韓冰,張旖諾,梁金盛,王順山,陳燕,趙吉賓 來(lái)源:表面云社區(qū)
分享至:
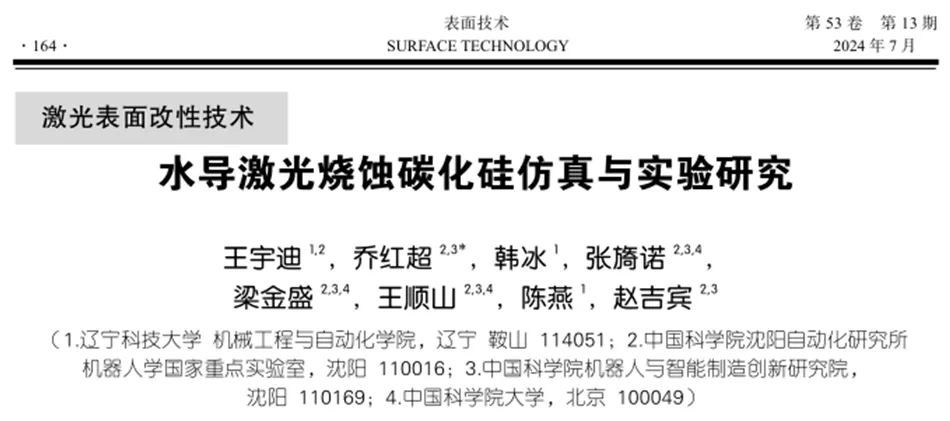
水導(dǎo)激光作為一門(mén)新興加工技術(shù),具有較低的熱效應(yīng)及較高的精度,逐漸廣泛應(yīng)用于各種硬脆性材料的加工。由于水導(dǎo)激光的燒蝕機(jī)理較復(fù)雜,因此材料的燒蝕行為也存在差異。中國(guó)科學(xué)院沈陽(yáng)自動(dòng)化研究所喬紅超研究員團(tuán)隊(duì)為了更加深入地研究水導(dǎo)激光作用下SiC材料的燒蝕行為,建立了SiC水導(dǎo)激光加工燒蝕溫度場(chǎng)數(shù)值模型,著重探究了SiC材料加工時(shí)溫度場(chǎng)的變化。由于水射流強(qiáng)制換熱作用對(duì)加工的影響較大,故將水射流貼壁射流流場(chǎng)換熱進(jìn)行細(xì)分和計(jì)算,使得水射流換熱作用與實(shí)際加工更接近。SiC到達(dá)熔點(diǎn)氣化,結(jié)合Clausius-Clapeyron方程通過(guò)氣化帶走熱通量反求出蝕孔的形貌,從而較準(zhǔn)確地分析激光燒蝕過(guò)程,以及SiC材料加工時(shí)溫度場(chǎng)的變化規(guī)律。目前,水導(dǎo)激光燒蝕機(jī)理研究還未形成較完善的體系,本研究主要將飛秒激光燒蝕閾值思想融入水導(dǎo)激光燒蝕機(jī)理中,并結(jié)合燒蝕實(shí)驗(yàn)探究水導(dǎo)激光作用下SiC的燒蝕閾值,并對(duì)SiC材料的燒蝕形貌進(jìn)行分析和研究,揭示SiC材料的水導(dǎo)激光加工去除行為。采用自主研發(fā)的水導(dǎo)激光加工系統(tǒng)實(shí)驗(yàn)裝置進(jìn)行加工,如圖1所示。該系統(tǒng)主要由激光器、水凈化系統(tǒng)、耦合裝置、三維工作平臺(tái)、CCD相機(jī)、計(jì)算機(jī)等組成,采用532 nm的Nd:Yag固體激光器,其峰值激光功率為100 W,輸出頻率為50 kHz,脈沖寬度為100 ns。為了減少水對(duì)激光能量的吸收,將實(shí)驗(yàn)用水過(guò)濾、去離子和除氣,調(diào)節(jié)高壓水泵,使得水壓穩(wěn)定在30 MPa。激光束被聚焦在直徑70 μm的水噴嘴中,并與水射流進(jìn)行耦合,形成水束光纖,激光能量通過(guò)水射流被引導(dǎo)至工件,完成加工。
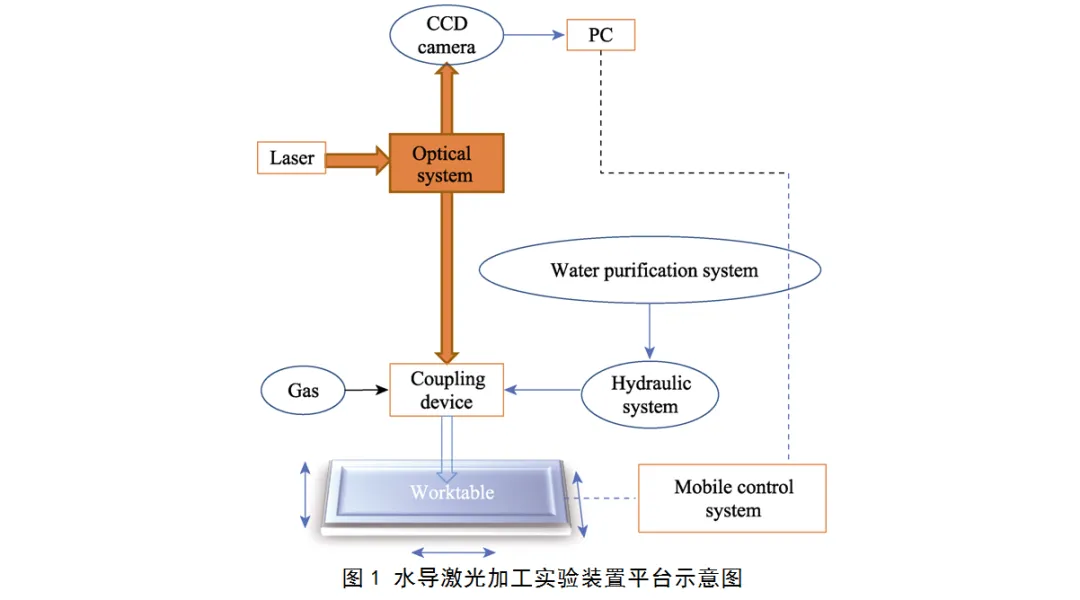
通過(guò)水導(dǎo)激光系統(tǒng)實(shí)測(cè)的激光能量在水束截面中的能量分布如圖2a所示。當(dāng)水射流到達(dá)工件表面后,激光能量密度在加工區(qū)域表面均勻連續(xù)分布,該能量分布近似為頂帽分布。頂帽函數(shù)f(r)的圖像函數(shù)如圖2c所示。對(duì)比高斯分布激光,水導(dǎo)激光蝕孔徑深度更淺、更寬,如圖2b所示。為了使燒蝕區(qū)域過(guò)渡平滑,將均勻分布高密度能量與周?chē)兔芏饶芰窟^(guò)渡區(qū)域進(jìn)行了平滑處理。
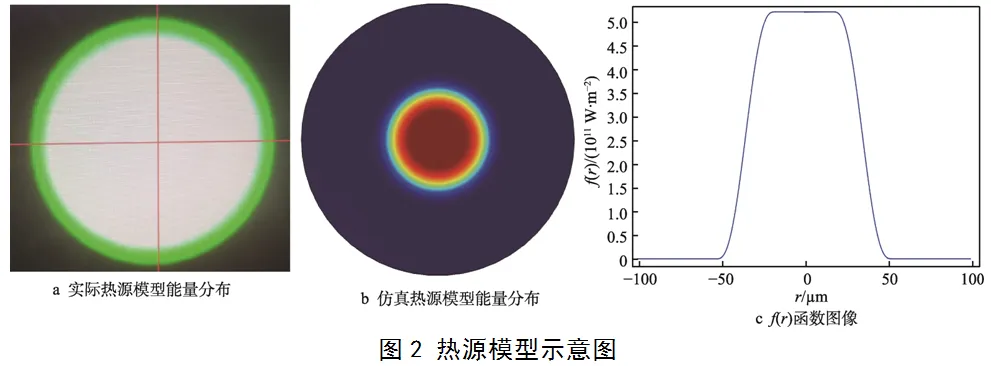
為了簡(jiǎn)化仿真計(jì)算,采用定點(diǎn)燒蝕方式對(duì)水導(dǎo)激光加工SiC的溫度場(chǎng)進(jìn)行仿真數(shù)值模擬,燒蝕區(qū)域內(nèi)最高溫度隨時(shí)間的變化趨勢(shì)仿真情況如圖3a所示。在加熱階段初期,溫度迅速上升,隨著加熱的進(jìn)行,最高溫度逐漸趨于平穩(wěn)。這是由于材料表面能量向基體內(nèi)部能量擴(kuò)散,抑制了表面溫度的上升速率,使得材料在去除階段的表面溫度基本保持恒定;在快速冷卻階段,加工區(qū)域在水射流強(qiáng)制對(duì)流換熱、材料內(nèi)部熱傳遞及空氣對(duì)流的共同作用下迅速冷卻。隨著冷卻時(shí)間的延長(zhǎng),靶材表面的溫度及溫度梯度減小,抑制了材料內(nèi)部熱擴(kuò)散量和表面對(duì)流熱損失,故材料仍然存在熱量殘余,脈沖強(qiáng)度的重復(fù)導(dǎo)致表面殘余溫度持續(xù)上升,溫度的增加量隨著脈沖不斷疊加逐漸減小。
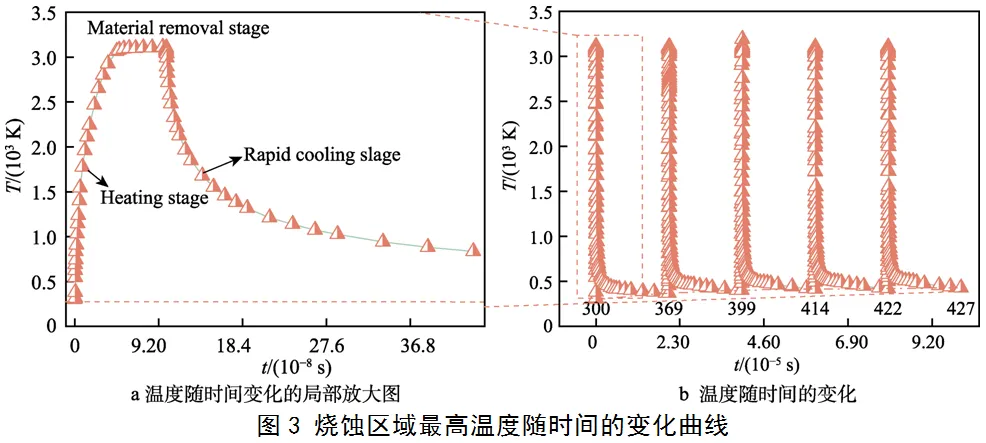
在功率10 W、不同脈沖數(shù)的作用下,SiC燒蝕形貌如圖4所示,隨著脈沖的疊加,SiC燒蝕直徑與熱擴(kuò)散區(qū)域基本不發(fā)生變化,燒蝕深度逐漸增加。可見(jiàn),在保證激光其他參數(shù)不變的條件下,保持激光功率不變時(shí),SiC多脈沖水導(dǎo)激光燒蝕直徑基本恒定。在激光功率與脈沖數(shù)的共同作用下,SiC燒蝕寬度和燒蝕深度的變化趨勢(shì)如圖5a所示。在激光–水射流復(fù)合加工過(guò)程中,隨著激光功率密度的增加,所形成的等離子體的密度會(huì)不斷增加,熱阻塞效應(yīng)會(huì)加劇,相應(yīng)材料所吸收的激光能量會(huì)減弱。在激光–水射流復(fù)合加工過(guò)程中,隨著激光功率密度的增加,所形成的等離子體的密度會(huì)不斷增加,熱阻塞效應(yīng)會(huì)加劇,相應(yīng)材料所吸收的激光能量會(huì)減弱。
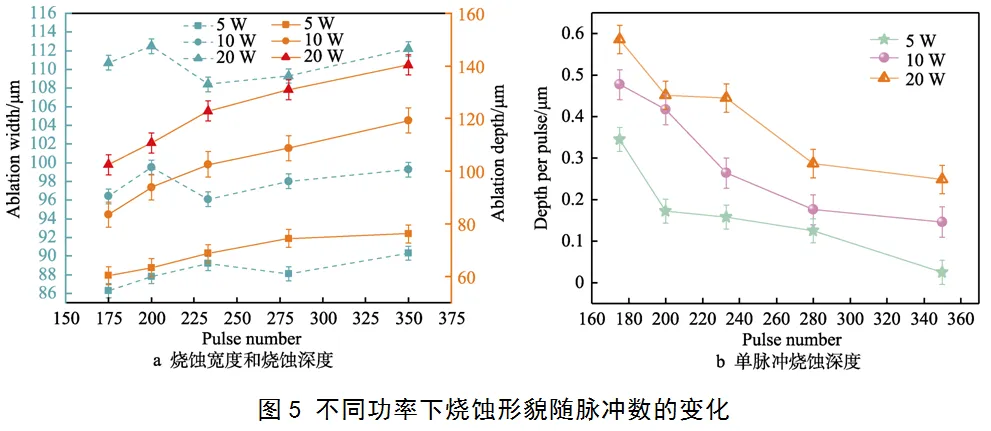
在不同功率下的二維形貌及切口輪廓截面形狀如圖6所示。由于激光能量在水射流中心近似為高斯頂帽分布,射流中心能量密度較大,材料更易被燒蝕,而其外側(cè)附近能量較弱,加上水射流局部換熱較強(qiáng),較難達(dá)到材料的燒蝕條件,使得截面輪廓整體呈倒梯形,且隨著激光功率的增加,溝槽深寬比逐漸增大。SiC燒蝕邊緣與未加工邊緣過(guò)渡平滑,與常見(jiàn)激光加工不同,加工邊緣不會(huì)產(chǎn)生較厚的重鑄層,燒蝕區(qū)域形成的軟化物質(zhì)基本被水射流沖刷而剝離,不會(huì)富集在材料表面,使得燒蝕區(qū)域基本無(wú)明顯熱影響區(qū)。在加工完成后,會(huì)在側(cè)壁表面形成帶狀條紋,該條紋垂直于進(jìn)給方向。這主要因水射流接觸熔池底部后沿著平行于側(cè)壁的方向噴射,將熔融物沿底部向溝槽上方?jīng)_刷,燒蝕區(qū)域底部無(wú)明顯重鑄物堆積,較為平整。由于存在水射流冷卻和沖刷作用,因此水導(dǎo)激光在加工硬脆性材料時(shí)具有相對(duì)較好的優(yōu)勢(shì),基本可以實(shí)現(xiàn)對(duì)硬脆性材料無(wú)裂紋及無(wú)熱影響加工。
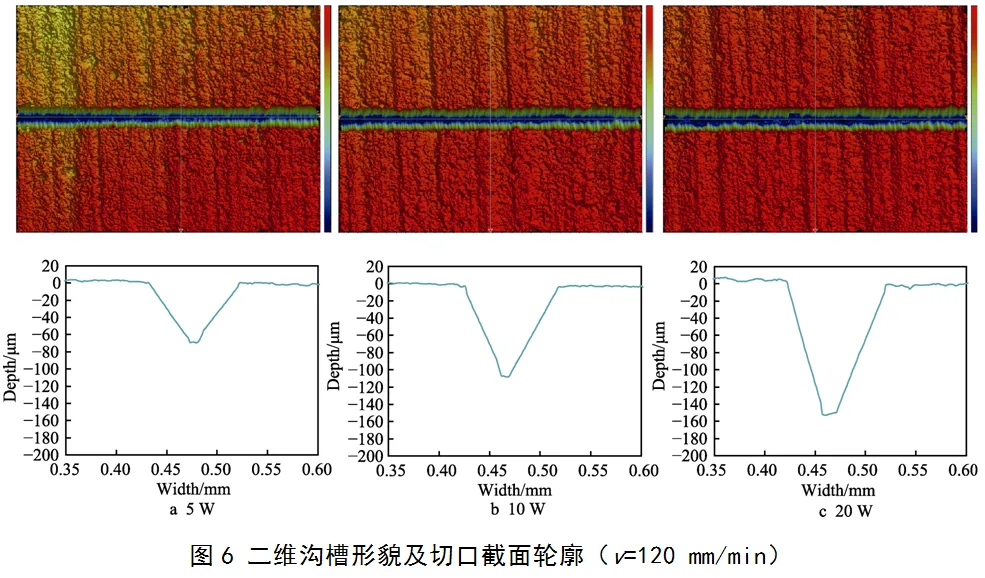
通過(guò)對(duì)SiC水導(dǎo)激光進(jìn)行仿真模擬與燒蝕實(shí)驗(yàn)研究,在水導(dǎo)激光加工SiC過(guò)程中,水射流不僅存在較強(qiáng)的換熱能力,減少了多脈沖燒蝕帶來(lái)的熱累積效應(yīng),而且大幅度降低了SiC脈沖期間材料的內(nèi)部余熱,加工材料內(nèi)部殘余溫度飽和速度較快。通過(guò)計(jì)算燒蝕功率閾值可知,對(duì)于SiC材料,其燒蝕功率閾值基本恒定。燒蝕區(qū)域面積會(huì)隨著激光功率的增加逐漸從激光輻照區(qū)域中心向外擴(kuò)散,燒蝕寬度隨激光功率增加得較為明顯。由于水射流對(duì)激光輻照區(qū)域的外換熱能力較強(qiáng),因而擴(kuò)散區(qū)域的長(zhǎng)度不會(huì)太長(zhǎng),使得燒蝕寬度基本不受脈沖數(shù)的影響,并確定激光功率與燒蝕寬度存在定量關(guān)系。SiC這類(lèi)硬脆性材料在高溫下的斷裂強(qiáng)度較低,水射流沖刷作用更易將燒蝕區(qū)域熔融物質(zhì)及軟化物質(zhì)快速?gòu)陌胁闹袆冸x,防止重凝物質(zhì)附著在加工區(qū)域底部及表面,使得燒蝕區(qū)域邊緣與未加工邊緣過(guò)渡較為平滑,底部基本無(wú)熔融物堆積。隨著燒蝕深度的增加,水射流狀態(tài)容易受到溝槽內(nèi)壁形貌的影響,使得激光無(wú)法直接作用于物體表面,大量能量會(huì)被水層吸收,相應(yīng)地增大激光燒蝕功率能夠有效提高水導(dǎo)激光燒蝕能力,更易實(shí)現(xiàn)對(duì)SiC較大深寬比溝槽的加工。由于無(wú)法準(zhǔn)確觀(guān)測(cè)水導(dǎo)激光燒蝕SiC材料的具體過(guò)程,故后續(xù)需要通過(guò)實(shí)驗(yàn)與檢測(cè)手段進(jìn)一步完善SiC水導(dǎo)激光燒蝕機(jī)理。
該文章發(fā)表在《表面技術(shù)》第53卷第13期
引文格式:
王宇迪, 喬紅超, 韓冰, 等. 水導(dǎo)激光燒蝕碳化硅仿真與實(shí)驗(yàn)研究[J]. 表面技術(shù), 2024, 53(13): 164-174.
WANG Yudi, QIAO Hongchao, HAN Bing, et al. Simulation and Experimental Study of Water Jet-guided Laser Ablation Silicon Carbide[J]. Surface Technology, 2024, 53(13): 164-174.
DOI:10.16490/j.cnki.issn.1001-3660.2024.13.016
免責(zé)聲明:本網(wǎng)站所轉(zhuǎn)載的文字、圖片與視頻資料版權(quán)歸原創(chuàng)作者所有,如果涉及侵權(quán),請(qǐng)第一時(shí)間聯(lián)系本網(wǎng)刪除。