熱障涂層涂覆于航空發動機和燃氣輪機高溫部件表面,具有防止高溫腐蝕、延長熱端部件使用壽命、提高發動機功率和減少燃油消耗等優點[1]。通常典型的熱障涂層包括表面陶瓷層(TC: top coat)和金屬粘結層(BC: bond coat)。在服役過程中,粘結層會發生氧化,在粘結層和陶瓷層界面形成厚度為1~10 μm的熱生長氧化物(TGO: thermally grown oxide)[2-4]。TGO的形成是一個體積膨脹過程,界面會限制這種體積變化,因而在TGO內部會隨之產生應力[5,6]。而且,陶瓷層與金屬基底的熱膨脹系數相差較大,在熱循環過程中會在熱載荷的作用下產生較大的熱應力,從而在界面缺陷處引起應力集中,促進裂紋的萌生與擴展[7,8]。此外,服役溫度超過1250℃,陶瓷層會發生嚴重燒結,導致其熱導率和彈性模量升高,隔熱性能下降; 同時在冷卻過程中,陶瓷層會發生相變,由平衡四方相(t)轉變為單斜相(m),并伴隨3%~5%體積膨脹[9,10]。這些都促使裂紋萌生和擴展,造成涂層剝落失效。
服役過程中,渦輪葉片不僅受到較大的交變載荷,而且在葉片表面和內部分別受到高溫高壓燃氣的沖擊和冷卻氣體的作用,這樣渦輪葉片就遭受載荷和溫度同時變化帶來的熱機械疲勞損傷[11-13]。此外,為了增強發動機冷卻效果,提高發動機效率,先進的航空發動機和燃氣輪機熱端渦輪葉片多為薄壁多孔結構[14]。涂覆熱障涂層后,在內部冷卻氣體作用下,空心薄壁樣品經歷的溫度梯度要遠大于實心樣品,此類涂覆熱障涂層的空心樣品的熱機械疲勞行為稱為熱梯度機械疲勞行為(Thermal gradient mechanical fatigue,簡稱為TGMF)。近年來,人們對高溫合金基體的熱機械疲勞行為已有所研究,發現試樣尺寸、應變幅、溫度范圍及上下限溫度、相位角、升溫速率、高溫保載時間和環境等都會影響其熱機械疲勞行為[15-20]。對于涂覆熱障涂層的空心構件,冷卻過程中內側金屬基體比外側金屬收縮嚴重,從而產生一徑向應力[21,22]。Zhou等[23]通過理論分析發現若空心樣品的曲率半徑不同,溫度梯度的差異不僅會改變熱應力的大小,還會改變熱應力的性質。隨曲率半徑的增大,陶瓷層/粘結層界面由壓縮切向應力轉變為拉伸切向應力,從而影響裂紋萌生及擴展行為。而Ta等[24]發現溫度梯度的存在促進了粘結層中的Al元素向金屬基體擴散,即加速粘結層中的Al貧化,從而降低熱障涂層壽命。此外,實驗過程中,采用的常規感應加熱設備只會對內部金屬層加熱,使得內部金屬層溫度高于外部陶瓷層溫度,這不符合熱障涂層構件實際工作狀態下的溫度分布。實際發動機啟動階段溫度從520℃升到1090℃只需要幾秒鐘的時間,而且降溫也相當迅速,這些都對涂覆熱障涂層的熱梯度機械疲勞試驗設備提出了更高的要求,同時也制約了這方面的研究。由于熱梯度機械疲勞是試驗室中最接近渦輪葉片服役狀態的模擬試驗,因而這方面的研究對于理解涂覆熱障涂層的葉片損傷機理具有重要意義。
本文以MGA1400定向柱晶高溫合金為基體,采用超音速火焰噴涂工藝沉積粘結層、大氣等離子噴涂工藝沉積陶瓷層,采用改進的熱機械疲勞試驗設備,研究涂覆熱障涂層的空心樣品的熱梯度機械疲勞行為以及應變幅、預氧化及高溫保載時間對性能的影響。
1 實驗方法
本文以一種鎳基定向柱晶高溫合金MGA1400為基體,其具體成分(質量分數)如表1所示。將熱處理后的棒材加工成標距段直徑6 mm、長度25 mm、壁厚1.5 mm的空心熱梯度機械疲勞試樣(圖1a),并對試樣進行機械拋光以消除機加工帶來的表面缺陷。噴涂前,對樣品進行噴砂處理,經丙酮和去離子水超聲清洗待用。
試驗中在樣品標距段及圓弧連接段噴涂熱障涂層(圖1b)。采用的粘結層及陶瓷層材料均為北京廊橋表面技術公司生產,牌號分別為LF213和LF441。粘結層主要成分為CoNiCrAlY,粉末粒度為15~45 μm,采用超音速火焰噴涂(HVOF,設備型號: Praxair TAFA JP5000)沉積粘結層。陶瓷層化學組成為ZrO2+8%Y2O3,粉末粒度為15~200 μm,采用大氣等離子噴涂(APS,設備型號: METCO 7M)方法制備陶瓷層。粘結層及陶瓷層具體噴涂工藝參數如表2所示。
熱梯度機械疲勞試驗是在計算機輔助控制的MTS810液壓伺服疲勞試驗機上進行的(圖2a)。為了更好地模擬燃氣輪機葉片實際工作狀態的溫度梯度,試驗中采用聚光燈加熱爐加熱,使得表面陶瓷層溫度高于心部金屬層溫度[21]。冷卻方式為壓縮冷卻空氣吹向試樣心部,并配合水冷液壓夾頭通過熱傳導降溫。應變控制通過軸向高溫陶瓷引伸計來實現,熱電偶布置如圖2b所示。試驗過程中采用反相位(OP,最高機械應變對應最低溫度)波形,機械應變幅大小分別為-0.45%、 -0.30%,試驗溫度范圍為300~1000℃,如表3、圖3所示。其中,樣品1經歷300~1000℃,機械應變幅大小為-0.45%的熱機械疲勞加載。為了研究高溫保載的影響,在樣品1基礎上,樣品2在最高溫度保載5 min。為了研究TGO層對熱障涂層界面性能的影響,樣品3在樣品2的基礎上,在試驗前經過1000℃預氧化100 h來獲得與制備態不同的TGO層厚度,比較預氧化和制備態的熱障涂層的熱梯度機械疲勞性能。此外,將樣品3的機械應變幅降低至-0.30%,以研究應變幅對其熱梯度機械疲勞壽命的影響,并命名為樣品4。試驗中觀察到樣品表面熱障涂層發生開裂時,測試終止。每種實驗條件下,熱梯度機械疲勞壽命取三個樣品試驗結果的平均值。試驗后觀察熱障涂層形貌,以確定試樣疲勞裂紋的萌生和擴展機制。
圖1 TGMF試樣示意圖(a)及涂覆熱障涂層的試樣(b)
圖2 熱梯度機械疲勞試驗機(a)及熱電偶及應變計連接方式(b)
圖3 熱梯度機械疲勞試驗加載曲線
2 實驗結果
2.1 制備態熱障涂層的組織形貌
制備的熱障涂層SEM形貌觀察,如圖4所示。由圖4a的斷面形貌照片可以看出,熱障涂層的厚度比較均勻,其中粘結層厚度大約為60~100 μm,陶瓷層厚度大約為250~350 μm,兩者之間存在一層厚度約5 μm的TGO。將高溫合金基體/粘結層界面放大,可以看出界面處結合良好,未發現明顯的孔洞或裂紋(圖4b)。粘結層內部組織致密,無明顯孔洞,組織中分布著一些河流狀條紋,這是噴涂過程中處于半熔狀態的粒子,在與金屬基體或底面涂層高速碰撞后形成的噴涂粒子的界面(圖4c),偶爾發現球形“未熔”粘結層顆粒存在(圖4d)。此外,粘結層/陶瓷層界面清晰,結合緊密無氣孔(圖4d)。而陶瓷層存在較明顯的空洞和氣孔及微裂紋(圖4e)。
圖4 制備態熱障涂層的組織形貌: (a)整體形貌, (b)基體/粘結層界面, (c)粘結層形貌, (d)粘結層/陶瓷層界面, (e)陶瓷層形貌
2.2 熱梯度機械疲勞壽命
空心高溫合金樣品上涂覆的熱障涂層在熱梯度機械疲勞載荷下經過一定循環后發生開裂及剝落。不同條件下樣品的熱梯度機械疲勞壽命如圖5所示。可以看出,高溫保載時間、預氧化及機械應變幅對熱障涂層壽命具有重要影響。未經預氧化處理,加載過程中沒有高溫保載階段的樣品1壽命最長。在樣品1基礎上施加高溫保載會嚴重降低樣品的熱障涂層壽命(樣品2)。在樣品2基礎上,熱梯度機械疲勞試驗前在1000℃預氧化100 h時樣品表面熱障涂層的壽命最短(樣品3)。將樣品3的應變幅由Δε=-0.45%降低至Δε=-0.30%(樣品4),樣品熱障涂層壽命有了大幅度提高,經過692循環后涂層才發生開裂剝落。
圖5 熱障涂層材料體系的熱梯度機械疲勞壽命
2.3 循環應力響應
圖6是熱障涂層材料體系第一周和穩態(N=0.5Nf) 時典型滯后回線的比較。可以看出所有樣品均表現為拉伸平均應力,這是因為熱機械疲勞試驗過程中溫度不斷變化,材料的彈性模量也隨溫度發生變化,反相位試驗條件下低溫時最大拉伸應力的絕對值高于高溫時最大壓縮應力的絕對值,因此產生拉伸平均應力。樣品1穩態的滯后回線較第一周發生了明顯的向上偏移,相比而言,樣品2,3,4滯后回線偏移現象不明顯。另外,所有樣品在第一循環時已經發生了塑性變形。樣品1塑性應變范圍(滯后回線所截橫軸的寬度)最小,為0.07%左右,而試驗過程中施加高溫保載后,樣品的塑性應變范圍幾乎相同,都在0.2%左右(樣品2~4)。
圖6 熱梯度機械疲勞試驗第一周和穩態滯后回線的比較
2.4 服役后的涂層組織觀察
熱梯度機械疲勞試驗后對四組樣品的組織進行了觀察,發現試驗后四組樣品的組織很相似,以應變幅為-0.30%的樣品4為例,如圖7所示。可以觀察到粘結層與金屬基體形成整體,陶瓷層與粘結層界面已出現較大的分層,在陶瓷層內也出現了很多貫穿裂紋,而且樣品內腔高溫合金基體已發生明顯氧化 (圖7a,b)。分層裂紋主要在TGO層偏下的粘結層中擴展,在擴展過程中與陶瓷層中的貫穿裂紋連接時,會導致陶瓷層開裂甚至剝落(圖7c)。觀察樣品內腔氧化層與基體界面,發現在界面已生成微裂紋并向基體擴展(圖7d)。
圖7 熱梯度機械疲勞試驗后樣品4的橫截面形貌
3 討論
由于熱障涂層具有隔熱效果,陶瓷層與金屬基體間存在溫度差。當表面陶瓷層保持在1000℃時,測得靠近陶瓷層的金屬基體的溫度為900℃左右,即陶瓷層與金屬基體的溫差可達100℃。由于TGO層很薄(只有幾個微米),所以忽略TGO層內的溫度梯度,將其視為均勻的900℃。由于粘結層及基體都是金屬材料,可以忽略其熱導率差異,根據溫度隨厚度的線性變化(粘結層厚100 μm,基體厚1500 μm),可得粘結層/基體界面溫度為897℃,基體內側溫度為850℃。假設熱障涂層中每層材料和基體承受同樣的外加機械應變,同時不考慮涂層界面結合力的影響。在熱機械疲勞過程中,試樣受到了外加的機械載荷,同時由于每層材料熱膨脹系數及彈性模量的不同,試樣還承受由溫度變化帶來的熱失配載荷。
Chen等[25]及Wright等[26]指出,試樣壽命的長短和涂層是否剝落,與試樣實際承受的應力密切相關,而熱障涂層所受的徑向應力往往被認為是決定涂層開裂和剝落的主要因素。由于本文試驗進行到涂層剝落為止,所以著重考慮熱障涂層所受的徑向應力。總的徑向應力 Δσtotal 為外加機械應力 Δσmech 與熱不匹配應力 Δσth 之和:
式中,υ為泊松比; E為彈性模量; Δεmech 為試驗中的機械應變幅。徑向機械應變應為軸向機械應變的分量,即軸向應變乘以泊松比。
Chen等[25]及Wright等[26]定量計算出試樣承受的應力,討論了相位、應變幅與壽命關系和涂層失效機制。但是他們的模型存在以下兩個缺點: (1)將涂層視為一個整體,而未考慮涂層的結構。由于涂層中陶瓷層、TGO層及粘結層的性能存在很大差異,所以將其視為一個整體會存在很大誤差; (2)只考慮了涂層與基體熱膨脹系數的差異,而忽略了各層材料彈性模量的差異,而熱不匹配應力的產生不僅與連接材料的熱膨脹系數差異有關,而且與二者的彈性模量差也相關。
當熱膨脹系數、彈性模量各不同的兩層異種材料連接在一起時,溫度變化過程中產生的熱失配應力[27]為
式中, αi 、 αj 分別為材料i、j的熱膨脹系數; Ei、Ej分別為材料i、j的彈性模量; ΔT 為溫度差。
因此,為了更準確地理解熱障涂層材料體系的熱機械疲勞損傷過程,詳細計算了粘結層、TGO層及陶瓷層受到的總徑向應力,分別為:
由于陶瓷層、TGO層、粘結層及金屬基體四層的熱膨脹系數不同,且滿足 αBase > αBC > αTC > αTGO ,在升溫及降溫過程中每層受到的應力不同。在反相位加載過程中,升溫時,在粘結層/基體金屬界面,金屬基體受壓縮熱不匹配應力,粘結層受拉伸熱不匹配應力; 在粘結層/TGO界面,粘結層受壓縮熱不匹配應力,TGO層受拉伸熱不匹配應力; 在TGO/陶瓷層界面,陶瓷層受壓縮熱不匹配應力,TGO層受拉伸熱不匹配應力。在降溫過程中,情況正好相反。
根據文獻中各層材料的熱膨脹系數、彈性模量和泊松比參數[28,29],得到每層受到的徑向應力如表4所示。可以看出TGO層所受徑向應力最大,TGO層破裂而萌生裂紋,裂紋沿應力較大的粘結層/TGO層擴展而形成分層裂紋,分層裂紋與陶瓷層內的貫穿裂紋連接導致大面積的陶瓷層剝落,從而導致TBC層失效。
材料的疲勞壽命預測是工程應用比較關心的問題,很多研究都提出了相關模型。其中,對于低周疲勞,最經典的模型是Manson-Coffin壽命預測模型[30]。Manson-Coffin方程是等溫低周疲勞壽命計算的基礎模型之一,它實現了低周疲勞壽命從定性研究發展到定量研究的突破。其表達式如下所示:
式中, Δεt , Nf 為總應變范圍與相應地破壞壽命; b,c, σ'f , ε'f 為待定常數。
由于Manson-Coffin壽命預測模型中既考慮了彈性變形,又考慮了塑性變形。而本文熱梯度機械疲勞試驗中熱障涂層剝落時試驗終止,此時金屬基體尚未發生明顯的塑性變形。此外,Manson-Coffin模型中未考慮氧化對壽命的影響,而試驗過程中,粘結層氧化生成的TGO層及其破碎是熱障涂層失效的一個重要因素。
Chan等[31]考慮到粘結層的氧化,陶瓷層的燒結,涂層厚度,基體的曲率等因素的影響,指出等溫氧化及循環氧化過程中熱障涂層的壽命滿足:
式中, ΔσTBC 為熱障涂層所受的應力幅; σ*TBC(t) 為疲勞強度系數; δ 為TGO厚度; δ* 為引起熱障涂層開裂的臨界TGO厚度; b,c為待定常數。
由于 σ*TBC(t) 、 δ 均與氧化時間有關,可將公式(7)右邊簡化為一個氧化時間的函數,修正為以下模式:
式中,f(t)是關于氧化時間的一個函數,在本文中,f(t)考慮了預氧化及試驗中高溫保載時間對氧化的影響。
將數據進行擬合,得到涂覆熱障涂層構件的熱梯度機械疲勞失效壽命滿足關系式(9)
4 結論
(1) 在相同相角度下,隨著應變幅的增加,涂覆TBC的空心高溫合金樣品的熱梯度機械疲勞壽命降低。隨著預氧化及高溫保載時間的增長,樣品的氧化損傷逐漸增大,熱梯度機械疲勞壽命也不斷降低。
(2) 粘結層氧化形成TGO層,TGO層破裂而萌生裂紋,裂紋沿粘結層/TGO層界面擴展而形成成分層裂紋,分層裂紋與陶瓷層內的貫穿裂紋連接導致大面積的陶瓷層剝落,從而導致TBC層失效。
(3) 考慮到涂層內最大應力及氧化損傷,建立了一個帶熱障涂層構件的熱機械疲勞壽命預測模型:
免責聲明:本網站所轉載的文字、圖片與視頻資料版權歸原創作者所有,如果涉及侵權,請第一時間聯系本網刪除。
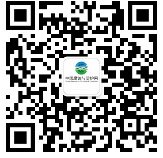
官方微信
《中國腐蝕與防護網電子期刊》征訂啟事
- 投稿聯系:編輯部
- 電話:010-62313558-806
- 郵箱:fsfhzy666@163.com
- 中國腐蝕與防護網官方QQ群:140808414