先進單晶高溫合金中難熔元素(Re、W、Mo和Ta)含量的增加引起了偏析加劇、共晶含量增多、元素擴散困難等一系列問題[1-3], 導致合金固溶處理的溫度升高、時間延長, 成本顯著提高。第三代單晶合金CMSX-10的標準固溶處理制度分為10級, 最高固溶溫度達到1365℃, 共耗時45 h[4]。為了降低成本, 嘗試對合金的固溶處理制度進行優化[4, 5], 但效果并不理想。傳統的分級固溶處理制度為經驗式方法, 雖然能夠提高初熔溫度以使合金達到均勻化, 但并不注重固溶處理過程中合金組織的變化。Hegde等[6]研究發現, 在γ‘相溶解溫度以下固溶時合金中共晶的體積分數增加, 共晶的穩定性提高; 在γ’相溶解溫度以上長時間等溫固溶時共晶中合金元素發生反常的上坡擴散, 引起初熔的產生[6]。在研究CMSX-4合金的固溶處理時, Reed等也預測了共晶區域上坡擴散的發生[7]。由此可見, 在分級固溶處理過程中合金組織的變化尚有不確定性, 直接影響固溶處理制度的優化。本文研究第三代單晶高溫合金DD33在分級固溶處理過程中組織的演變。
1 實驗方法
實驗用合金為第三代鎳基單晶高溫合金DD33, 其難熔元素的總含量(質量分數)(W+Mo+Re+Ta)為19.5%, C、B的含量分別為0.04%和0.003%。
先用真空感應爐熔煉母合金, 然后采用以錫為冷卻介質的液態金屬冷卻(LMC)定向凝固技術制備[001]取向的單晶試棒, 凝固過程中的抽拉速率為8 mm/min。在直徑為16 mm的單晶試棒上垂直于定向凝固方向切取10 mm厚的試樣, 進行分級固溶處理實驗。固溶處理的溫度區間為1240-1340℃, 具體的固溶處理工藝如圖1所示。固溶處理時, 將各溫度段所需的樣品一起放入箱式熱處理爐中加熱, 每個溫度段結束后迅速從爐中取出一個試樣在空氣中冷卻, 其它樣品繼續升溫。
圖1 合金的固溶處理工藝
使用Axiovert200MAT光學顯微鏡(OM)和S-3400N掃描電子顯微鏡(SEM)觀察合金鑄態和固溶處理不同階段的組織。常規腐蝕所用的試劑為4 gCuSO+10 mlHCl+20 mlHO,觀察碳化物演變所用的深腐蝕試劑為70%HCl+30%HO。用定量金相法測量合金中碳化物的體積分數,每個溫度段采用10張200倍的掃描背散射照片進行統計。用電子探針(EPMA)測量固溶處理過程中共晶冠處粗大γ‘相的成分, 束斑直徑為1 μm, 每個試樣測3點取平均值。
2 結果與討論
2.1 鑄態組織
如圖2a所示, 合金鑄態為典型的枝晶組織, 枝晶間存在白亮的(γ+γ’)共晶。定量金相統計結果表明, 合金的一次枝晶間距約為140 μm, 共晶含量約為9.5%。圖2b為枝晶間(γ+γ‘)共晶的形貌, 可以看出, 共晶為典型的葵花狀, 共晶芯由細小的γ和γ’兩相組成, 共晶冠為粗大的γ‘相。在枝晶干和枝晶間析出了兩種不同尺寸和形貌的γ’相, 如圖2c和d所示。枝晶干γ‘相尺寸較小, 呈立方狀; 枝晶間γ’相尺寸較大, 呈蝴蝶形。草書體狀碳化物分布于枝晶間(圖2e)。從能譜(EDS)分析的結果(圖2f)可以推斷, 這些碳化物為主要含Ta和Ti的MC型碳化物。
圖2 鑄態合金的枝晶組織及析出相
2.2 固溶處理過程中的組織演變
圖3給出了合金在1240℃/2 h和1260℃/2 h固溶后的顯微組織。如圖3a中箭頭所示, 合金中最先固溶的區域為共晶前沿及碳化物周圍, 在這些區域中出現了γ’相貧化區。隨著溫度的提高, 枝晶干γ‘相也開始逐漸溶解(圖3b)。對比圖3c和d的放大照片可見, 枝晶干γ’相的溶解與長大并存; 同時, 其它區域的γ‘相也長大了: 二次枝晶臂及枝晶間的γ’相相互連接, 形成近似筏化的形態; (γ+γ‘)共晶芯發生粗化, 共晶冠的大塊γ’相相互合并形成一個整體。
圖3 合金在1240℃/2 h和1260℃/2 h固溶后的顯微組織
圖4給出了合金在1280~1340℃各溫度段固溶后的顯微組織。由圖4a可見, 在1280℃/2 h固溶后枝晶干γ‘相已經完全溶解, 二次枝晶臂上的γ’相也部分溶解。對比圖4a、b和c可見, 隨著固溶溫度的升高枝晶間γ‘相并沒有顯著溶解, 反而在1310℃時明顯長大, 共晶γ’相也有粗化的趨勢。枝晶間γ‘相完全溶解的溫度為1320℃, 此時共晶也開始溶解(圖4d)。當溫度達到1330℃時共晶基本消除, 只有少量的殘余共晶存在(圖4e)。進一步提高溫度到1340℃, 合金中出現初熔, 初熔形貌如圖4f所示。
圖4 合金在1280~1340℃各溫度段固溶后的顯微組織
在分級固溶處理過程中, MC碳化物也發生了變化。圖5給出了固溶處理過程中MC碳化物形貌的演變, 可以看出, 溫度低于1280℃時MC碳化物還保持草書體狀(圖5b); 溫度達到1280℃后草書體狀碳化物逐漸破碎, 變得圓滑(圖5c); 到1310℃時, 碳化物已經變為顆粒狀(圖5d)。EDS分析結果表明, 碳化物的成分并沒有發生明顯的變化, 說明碳化物的類型沒有改變, 只是發生了溶解。圖6為固溶處理過程中MC碳化物體積分數的變化曲線, 如圖所示, MC碳化物的含量隨固溶溫度的升高逐漸降低, 到1310℃時, 已由鑄態的0.55%降低到0.36%。
圖5 固溶處理過程中MC碳化物形貌的變化
圖6 分級固溶處理不同階段MC碳化物體積分數的變化曲線
從γ’相的溶解過程可見, 在合金中不同區域γ‘相的溶解溫度不同, 這是凝固偏析導致的成分差異造成的。在凝固過程中枝晶干的單相g 固溶體率先形成, Al、Ta等γ’相形成元素向枝晶間液相富集, 當剩余液相的溶質濃度達到共晶點時生成(g +γ‘)共晶[8]。合金的這種凝固特點導致Al、Ta含量從枝晶干到枝晶間逐步升高。研究表明, Ta能夠提高γ’相的高溫穩定性, 使其溶解溫度更高[9]。因此, 合金中γ‘相的溶解溫度由低到高依次為: 枝晶干γ’、枝晶間γ‘、共晶γ’。在低于1320℃時枝晶間γ‘相尚未達到溶解溫度, 不發生溶解。但是為了降低界面能γ’相會長大, 其長大方式極可能為Ostwald熟化。同時, 在MC碳化物在界面能的作用下發生溶解[10], 并向枝晶間的基體中釋放出大量的Ta原子。Ta為γ‘相形成元素, 能促進γ’相的長大。隨著溫度的提高Ta元素的擴散變得更加容易, γ‘相的長大速率增加。因此, 在1310℃恒溫時枝晶間γ’相發生明顯長大。同樣, 共晶γ‘相在這期間也發生粗化, 這與Hegde[6]的實驗結果一致。
2.3 共晶’成分的變化
圖7給出了共晶冠處粗大γ‘相中各合金元素含量(原子分數)隨固溶溫度的變化曲線。從圖7可見, 隨著固溶溫度的提高Al、Ta等γ’相形成元素的含量先升高后降低, 峰值溫度為1310℃, 且Al含量的變化幅度更加顯著; Co、Cr、Mo等元素的含量則先降低, 后逐漸趨于平穩; W的含量在1280℃前先緩慢升高, 之后又逐漸降低; Re的含量最低, 幾乎沒有變化。
圖7 共晶γ’相中各合金元素含量隨溫度的變化曲線
隨著固溶處理的進行, 合金中的微觀偏析通常逐漸減輕。但是, 在本實驗中共晶γ’相中的偏析卻出現了反常的加劇。根據文獻[6,7]的觀點, 這一現象可能是上坡擴散引起的。以錫為冷卻介質的LMC定向凝固技術, 其溫度梯度達到70-100 K/cm[11], 合金的凝固速率可近似用抽拉速率表示。在拉速為8 mm/min的定向凝固過程中, 共晶的凝固無法在平衡條件下進行。由于凝固速率高, 共晶固液界面前沿的溶質還來不及充分擴散就已經凝固, 使共晶中g 和γ‘兩相的成分偏離平衡狀態。在固溶處理過程中未達到共晶溶解溫度以前, 共晶γ’相的成分會自發地進行調整以降低系統的自由能。此時, 共晶γ‘相中過飽和的Cr、Co、Mo、W等元素向外發生上坡擴散, 從而導致Al、Ta含量的提高。由于Cr、Co、Mo的擴散系數相對較高, 其含量在溫度較低時就開始降低; 而W的擴散系數較低, 其含量在1280℃以后才開始降低。此外, 共晶的粗化也可能導致共晶γ’相中成分偏析的加劇。在粗化過程中, 為了使共晶γ‘相的成分向所在溫度下的平衡成分轉變, 元素發生有選擇地擴散, Al、Ta擴散到γ’相表面參與粗化, 從而提高了共晶γ‘相中Al、Ta的含量。
γ’相的溶解過程實質上是溶質原子的擴散過程, 而共晶γ‘相中Al、Ta含量的升高以及γ’相的長大會減慢這一過程。因此, 在確保不發生初熔的前提下應盡量縮短在共晶γ‘相溶解溫度以下的固溶時間, 降低上坡擴散和γ’相長大的影響, 以提高固溶處理的效率, 降低固溶處理的成本。
3 結論
1. DD33合金鑄態的析出相由枝晶干和枝晶間γ‘相、(g +γ’)共晶以及MC碳化物組成。在分級固溶處理過程中, 枝晶干γ‘相在1280℃/2 h固溶后完全溶解; 枝晶間γ’相在1310℃固溶時明顯長大, 而在1320℃/2 h固溶后完全溶解; (g +γ‘)共晶在高于1320℃時才顯著溶解。
2. MC碳化物在固溶處理過程中發生溶解, 由草書體狀向顆粒狀轉變。隨著固溶溫度的提高共晶γ’相中合金元素的偏析加劇, Al、Ta的含量逐漸提高而Cr、Co等元素的含量降低, 這可能是上坡擴散引起的。
2013年11月12日收到初稿; 2014年2月14日收到修改稿。
免責聲明:本網站所轉載的文字、圖片與視頻資料版權歸原創作者所有,如果涉及侵權,請第一時間聯系本網刪除。
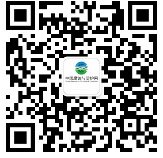
官方微信
《中國腐蝕與防護網電子期刊》征訂啟事
- 投稿聯系:編輯部
- 電話:010-62313558-806
- 郵箱:fsfhzy666@163.com
- 中國腐蝕與防護網官方QQ群:140808414