激光沖擊成形(laser shock forming, LSF)集材料改性強化和成形于一體, 是一種新興的冷成形技術[1-5]。在強激光束輻照表面產生的沖擊波不僅改變材料結構, 而且提高材料的強度、硬度、耐應力腐蝕性能和抗疲勞斷裂性能。采用激光沖擊強化(laser shock processing, LSP)鋁合金[6]、不銹鋼[7]和鈦合金[8]等材料, 研究得比較多。Ye等[9]在激光沖擊強化的NiTi合金中觀察到非晶組織, 經強化和熱處理后得到了納米晶組織。張永康等[10-12]對AM50和AZ31鎂合金激光沖擊強化進行了實驗研究, 發現激光沖擊區表層產生大量位錯與孿晶, 晶粒明顯細化, 表面產生殘余壓應力, 表面顯微硬度比基體約提高58%, 抗應力腐蝕和耐疲勞性能均得到提高。關于激光輻照材料表面波紋現象, Demchuk[13]在激光輻照的無定型硅表面熔化區觀察到表面樹枝狀結構, 袁永華等[14]在脈沖激光輻照的硅材料損傷區附近發現平行等間距波紋。張永康等[15]在AZ91鎂合金的激光沖擊區得到表面周期性波紋現象, 并研究和分析了激光能量的影響。利用激光超高應變率和超高能量產生強烈的應變強化效應, 在2A02航空鋁合金板表面局部可獲得納米晶[16]。本文對AZ31鎂合金薄板進行激光沖擊冷成形實驗, 在此基礎上研究和分析激光沖擊成形過程中沖擊區產生的微觀結構和殘余應力, 并探討波紋現象和周期性波紋結構。
1 實驗方法
實驗用交叉軋制AZ31鎂合金薄板的厚度為0.5 mm, 其晶粒大小和分布如圖1所示。激光沖擊成形試驗用Nd-YAG激光器的最大輸出脈沖能量為12.5 J、頻率為10 Hz、 波長為1.06 μm。在激光沖擊成形過程中, AZ31鎂合金試樣連同模具夾持在工作臺上, 用流動的水為約束層, 選用厚度為100 μm的美國3M公司專用鋁箔作為吸收層。圖2為激光沖擊成形實驗裝置示意圖。圖3給出了不同激光沖擊參數下鎂合金薄板LSF試樣, 沖擊參數: 光斑直徑為3 mm, 激光能量分別為6、 9和12 J, 激光沖擊次數為1-5次, 其中能量為9 J和4次沖擊時LSF最大成形深度達到3.5 mm, LSF試樣將作為本實驗分析和測試用樣品。
圖1 AZ31鎂合金薄板的組織
圖2 激光沖擊成形試驗裝置示意圖
圖3 AZ31鎂合金薄板激光沖擊成形試樣
用X-350A型X射線應力分析儀對LSF后鎂合金沖擊凹面進行殘余應力測定。用LEICA DM2500M型正置透反射光學顯微鏡和JEOL JSEM-7001F熱場發射高分辨率電鏡對鎂合金原始薄板和LSF沖擊面樣品進行微觀結構觀察和研究。薄膜樣品的制備先從沖擊區取樣, 用手工研磨減薄沖擊凸面(背面), 最后用離子減薄凸面, 以便觀察沖擊凹面(沖擊面)形貌。
2 結果與討論
2.1 波紋結構
圖4給出了AZ31鎂合金薄板經不同激光能量和連續4次沖擊LSF后沖擊區域凹面的波紋結構TEM像。從圖4可見, 經研磨和離子減薄后LSF沖擊區凹面表層保留著紋理清晰的周期性波紋結構, 且波紋線性較好, 近似相互平行的直線, 波紋間距隨著激光能量不同而不同, 屬于納米級。激光能量為6 J時波紋間距分布不均勻, 最大間距約為120 nm(圖4a); 隨著激光能量增加至9 J波紋間距分布比較均勻, 波紋間距變小, 其平均大小為50 nm(圖4b); 與9 J激光能量相比, 激光能量為12 J時的波紋間距分布更均勻, 但間距大小變化不明顯(圖4c), 其波紋衍射的同心環狀花樣顯示其納米特征(圖4d)。這表明, LSF后鎂合金成形試樣凹面出現波紋現象, 在其表層均清晰可見波紋。這種波紋將影響激光沖擊表面質量和粗糙度, 而且激光能量對沖擊表面波紋間距和分布有明顯的影響。
圖4 不同能量激光LSF后沖擊區鎂合金波紋分布TEM像
2.2 微觀結構
以激光能量為9 J和連續4次沖擊后LSF試樣作為研究對象, 研究和探討LSF過程中鎂合金顯微結構變化規律。
圖5給出了LSF后AZ31鎂合金沖擊橫斷面的顯微組織。由圖5可見, 經多次激光沖擊后在沖擊區域鎂合金薄板厚度變薄, 光斑中心減薄最大, 且觀察到沖擊凹坑, 沖擊區內組織均勻一致, 如同原始組織(圖1)由細小等軸晶組成。沖擊試樣經高能高速多次沖擊發生塑性變形和沖擊強化, 在沖擊區域表層形成大量位錯和孿晶, 但是在金相顯微鏡下無法觀察到LSF后鎂合金的微觀結構變化趨勢。
圖5 激光能量為9 J和連續4次沖擊區域的橫斷面組織
圖6給出了LSF后沖擊區表層的鎂合金顯微結構的TEM像。除圖4中LSF過程中形成的表層納米波紋結構外, 還觀察到條狀孿晶(圖6a)、不規則形變孿晶和位錯(圖6b); 從圖6c可清楚地觀察到表層波紋表面形成的位錯結構; 在表層還可觀察到析出相(黑色短棒, 圖6d)。對激光沖擊凹面再進行深度離子減薄, 可清楚地觀察到因高應變速率激光沖擊所形成的高密度位錯、亞晶(圖6e)以及納米晶(圖6f)。
圖6 LSF沖擊區域鎂合金組織結構TEM像和電子衍射花樣
圖7給出了原始薄板AZ31鎂合金TEM像。對比圖1和圖7可見, 未經激光沖擊原始薄板的鎂合金由細小等軸晶粒組成, 含有大量孿晶和不同類型位錯, 如形變孿晶(圖7a)、層狀位錯(圖7b)、網狀位錯(圖7c), 還觀察到圖6中相同的析出相(圖7d)。
圖7 原始鎂合金板料組織TEM像
以上結果表明, 激光沖擊成形后鎂合金組織結構發生了明顯變化: 晶粒細化、高密度位錯和不規則孿晶。晶粒細化不僅與激光的脈沖能量有關, 還與沖擊次數有關。在表面晶粒細化的同時, 產生高密度孿晶, 隨著沖擊次數增加塑性變形相應增加, 位錯滑移并大量增殖, 位錯之間相互纏結形成位錯胞, 當達到一定沖擊次數后將形成納米晶。
2.3 殘余應力
圖8給出了激光能量為9 J和連續4次LSF后AZ31鎂合金沖擊凹面的殘余應力分布和模擬結果。圖8a表明, 激光沖擊表面的最大殘余壓應力值出現在成形頂點或其附近, 隨著與中心點距離的增加殘余壓應力值逐漸減小, 隨著沖擊次數的增加表面產生的殘余壓應力也越大。單次沖擊時凹面的最大殘余壓應力達到-50 MPa, 而連續沖擊2次和3次時凹面的殘余壓應力達到-150 — -160 MPa, 其中連續2次LSF凹面的殘余壓應力分布不符合釹玻璃激光器能量的高斯分布特征, 沿沖擊中心區呈W型分布, 最高值出現在中心兩側。其原因是, 在光斑周邊產生的沖擊表面波沿徑向中心傳播, 并在光斑中心聚合, 產生一個巨大的脈沖。這個脈沖可抵消光斑中心點附近的部分殘余應力, 導致光斑中心的殘余壓應力偏小[17]。
圖8 不同次數激光沖擊表面的殘余應力分布和模擬結果
圖8b-d中的LSF模擬結果表明, 在相同條件下激光沖擊凹面的最大殘余壓應力隨著沖擊次數的增加而增加, 即單次沖擊時凹面的最大殘余壓應力達到-60.1 MPa, 連續沖擊2次和3次時凹面的最大殘余壓應力分別為-144.8 MPa和-159.3 MPa, 與實際激光沖擊凹面最大殘余壓應力相符合。實驗測得的殘余應力分布與模擬結果有一定差別, 可能是模擬時沖擊波模型的簡化和凹面殘余應力測試誤差等因素導致的。
2.4 討論
當脈沖激光透過約束層照射在附有吸收層的靶材表面, 吸收層汽化并電離, 形成了等離子體。部分等離子體吸收激光能量后膨脹、爆炸, 產生沖擊波并作用于靶材表面。
張永康等[15]用表面三維形貌儀測量LSP處理后AZ91鎂合金沖擊區域的表面形貌, 對形成的周期性波紋結構和形成機理進行了研究。在激光與靶材材料相互作用過程中, 激光、材料和等離子體之間存在極其復雜的多種能量耦合機制, 吸收層形成的等離子體產生的沖擊波對沖擊材料表面形貌的影響, 對波紋的形成有重要作用。在本文的實驗中, 從不同脈沖激光能量LSF后AZ31鎂合金的沖擊區取樣。為了觀察沖擊凹面的表面形貌, 對沖擊凸面進行研磨和離子減薄, 在高分辨率透射電鏡下觀察到凹面的波紋現象和周期性波紋結構。這種波紋特征與張永康作者在實驗中得到的結果一致, AZ31鎂合金沖擊凹面產生的波紋現象及其形成機理同樣可用AZ91鎂合金表面周期性波紋機理[15]解釋。
Ye等[9]通過激光沖擊對NiTi合金表面進行強化處理, 在沖擊區發現了納米晶和形變孿晶, 所形成的納米晶衍射花樣與圖4d和圖6a中衍射花樣基本相同, 即鎂合金LSF后可能形成納米晶。張靜文等[16]認為表面納米晶是激光沖擊超高應變率和超高能量作用下的非平衡缺陷如位錯和空位及其相互作用等對原始晶粒分化的結果。在超高能量超短時間激光的作用下并在超高應變率條件下不可能完成傳統形核理論關于晶體形核和長大所需要的擴散轉移過程, 只能通過瞬時由自組織分化在原位形成微小的晶粒以抗衡沖擊能量。沖擊波作用下在材料中先形成位錯, 再通過滑移進行塑性變形。而沖擊波在晶界上的反射和折射作用在多方向上作用于晶粒, 因此位錯從復雜的滑移、集聚和湮滅后形成新的晶界, 從而形成較小的亞晶和納米晶[18]。
3 結論
1. AZ31鎂合金薄板經6-12 J激光能量和連續多次沖擊后, 在LSF沖擊區域凹面出現紋理清晰的周期性波紋結構, 波紋近似相互平行, 波紋間距屬于納米級。
2. LSF沖擊區域表層的晶粒得到細化成亞晶和納米晶, 形成高密度位錯及各種形狀孿晶。最大殘余壓應力值位于激光沖擊區頂點或附近, 或呈W型分布, 最高值出現在中心兩側。
免責聲明:本網站所轉載的文字、圖片與視頻資料版權歸原創作者所有,如果涉及侵權,請第一時間聯系本網刪除。
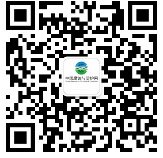
官方微信
《中國腐蝕與防護網電子期刊》征訂啟事
- 投稿聯系:編輯部
- 電話:010-62313558-806
- 郵箱:fsfhzy666@163.com
- 中國腐蝕與防護網官方QQ群:140808414