石墨材料具有優異的耐高溫性、熱膨脹系數小、導電導熱性、抗熱震性等特性,因此在冶金、化工、航空航天及核工業中得到廣泛應用。然而,石墨材料在高于 400 ℃開始發生氧化,這大大降低了石墨材料的使用性能。因此,解決石墨材料高溫氧化問題是其作為高溫結構材料的關鍵。抗氧化涂層技術是提高石墨高溫抗氧化的有效方法之一。
碳化硅抗氧化性能較好且與碳材料具有較好的物理和化學相容性,是高溫下保護石墨材料的一種有效涂層[3]。目前制備碳化硅涂層的方法主要有:包埋法[4]、化學氣相沉積(CVD)[5]、化學氣相反應[6]、等離子噴涂[7]、浸涂法[8]等。
這些方法制備的碳化硅涂層都可以有效地防止石墨材料的氧化,但是仍然存在一些問題,如:工藝復雜、成本高、抗熱震性能差、涂層不致密等。此外,由于 SiC 涂層與石墨基體間熱膨脹系數不匹配會導致高溫過程中容易產生裂紋,這便提供了氧氣進入石墨基體的通道[9,10],從而導致石墨基體的氧化。為了改善 SiC 涂層與石墨基體之間熱膨脹系數不匹配的問題,應該制備具有C/SiC 過渡結構的致密 SiC 涂層,這對于改善其抗氧化及抗熱震性能具有重要的實際應用價值。
本實驗以 SiC、Si 和酚醛樹脂為主要原料,通過浸涂和氣相滲硅兩步法在石墨表面制備厚度可控的SiC 抗氧化涂層。利用 XRD、SEM 研究涂層的相組成與形貌,并分析碳化硅涂層的形成機制及涂層的抗氧化、抗熱震性能。
實 驗
實驗選用高強石墨為基體,其密度為 1.75 g/cm3,試樣尺寸為 10 mm×10 mm×5 mm,試樣表面用砂紙研磨并去除棱角,然后用去離子水和乙醇超聲清洗、并放入 120 ℃烘箱中干燥 2 h 后備用。涂層原料主要為 SiC(純度為 99%,d50=0.5 ?m),金屬硅塊(純度為 99.4%,粒度為 5~10 mm),并采用實驗室自制的酚醛樹脂溶液(殘碳率為 50%,質量分數)為碳源及粘結劑。
將 SiC 微粉、酚醛樹脂和無水乙醇按照一定的比例混合后,經超聲分散、磁力攪拌形成均勻的料漿。采用浸漬的方式在石墨試樣表面形成均勻的預涂層,待其干燥后,置于 100~150 ℃烘箱中固化 1~3 h。固化后的樣品放入在氮氣保護的管式爐中于 900 ℃進行裂解 60 min,升溫速率 5 ℃/min。裂解后的試樣放入石墨坩堝中,坩堝底部放入足量的硅塊,然后在真空狀態下 1650 ℃保溫 30 min 進行氣相滲硅,使硅蒸氣與碳反應生成 SiC 涂層。
恒溫抗氧化性能測試在 1200 ℃的箱式電阻爐中進行,每隔 2 h 將樣品從高溫爐中取出并置于 25 ℃中冷卻,用電子天平(感量 0.1 mg)稱量氧化前后的質量,根據其質量變化來表征涂層的抗氧化性能。試樣質量變化率(ΔM)與質量關系如下:
ΔM=(m2–m1)/m1×100% (1)
式中,m1、m2 分別代表涂層樣品氧化前后的質量。
抗熱震實驗在電阻爐中進行,將爐溫快速升至1000 ℃。然后放入樣品,待溫度穩定后保溫 15 min,快速取出試樣,降至室溫后稱量質量變化,以此循環實驗。按照式(1) 計算試樣熱震前后的質量變化率。利用 X'Pert Pro MRD 射線衍射儀和 JSM-7001 型掃描電子顯微鏡測試物相組成及微觀形貌。
結果與討論
預涂層的微觀結構
由圖可知,預涂層表面較為平整且與石墨基體結合較好。如圖 1a 所示預涂層表面存在一些微孔以及微裂紋,這是由酚醛樹脂高溫下裂解體積收縮所產生的,但是這些微觀缺陷會有助于氣相硅的浸滲過程。預涂層厚度均勻(圖 1b),厚度約為 100 ?m,且主要為 SiC 顆粒,熱解碳分散在 SiC 周圍。
可以看出,經過氣相滲硅后的涂層十分致密,表面無裂紋與孔洞出現。涂層由不同粒徑的六方 SiC 及立方 SiC 組成,其中六方碳化硅是作為原料引入的,立方碳化硅為反應生成的(圖 2a、2b)。
由圖 2a 可以看出,六方 SiC 粒徑約為30 ?m,和原料中的SiC顆粒相比尺寸增大了數十倍,這是由于高溫下液相硅的存在促使了 SiC 晶粒的長大。顆粒尺寸較大的原料 SiC 與反應生成的尺寸較小的 SiC顆粒緊密相連,晶界處可見有部分硅殘留(圖 2a)。
從涂層的截面組織形貌(圖 2c、2d)可看出,涂層的厚度約為 150 ?m,厚度均勻且與基體結合良好。圖 2d 中線中間的區域為 C/SiC 混合的過渡區域,沿著涂層厚度方向至石墨基體,硅元素逐漸減少,碳含量逐漸增加,形成了良好的 C/SiC 過渡結構。
這是由于在高溫下氣態硅浸滲預涂層時會與酚醛樹脂熱解所產生的碳反應生成碳化硅,同時會有一部分硅蒸氣進入到石墨基體并與之反應,生成的 SiC 過渡層附著于石墨基體,這一過渡層可增加石墨基體與涂層之間的結合力。
氧化前涂層主要由 α-SiC,β-SiC 和 Si 組成,其中硅(圖 2a)是由于氣相滲硅過程中殘留的。氧化后涂層主要由 SiC及氧化生成的 SiO2 組成,在 1200 ℃空氣條件下 SiC以及殘余 Si 會與空氣中的氧氣反應生成 SiO2。反應式如下:
Si(s)+O2(g)→SiO2(s) (2)
SiC(s)+O2(g)→SiO2+CO(g) (3)
涂層的抗氧化及抗熱震性能
由圖可知,未經涂層處理的試樣,1 h 之后試樣質量變化率達到–100%,說明試樣已被完全氧化,而具有碳化硅涂層的試樣,經過 16 h 氧化后,樣品增重量約為每小時 2.18 mg/cm2,說明涂層有效的保護了石墨基體。SiC 涂層的存在有效防止了氧氣對石墨的侵蝕,提高了石墨在有氧環境下的使用壽命。
由圖可知,碳化硅涂層在 1200 ℃氧化 16 h 后表面無裂紋與孔洞,氧化后形成了致密的表面。SiC 和 Si 的摩爾體積(12.47、12.02 cm3/mol)遠小于 SiO2的摩爾體積(27.43 cm3/mol),因此,涂層中 SiC 和 Si 的氧化體積膨脹約120%,使表面變得致密[11]。高倍數下(圖 5b)可以看出,大顆粒碳化硅形成了氧化層外殼,而細顆粒的碳化硅氧化后表面變得更加圓滑。在氧化過程中,涂層表面的殘余硅首先被氧化成 SiO2,隨后碳化硅也發生了不同程度的氧化。圖 5c 為局部元素掃描分析,表面元素主要由 C、Si,O 組成。這與前邊的 XRD 分析結果一致,氧化后的涂層主要由 SiC 和 SiO2 組成。
由圖可知,試樣在熱震過程中質量變化率隨熱震次數的增加呈現先增大后減小的規律。這是由于在熱震試驗初期,涂層中 SiC 和殘留 Si 的氧化使試樣的質量增加,C/SiC 過渡層以及殘余 Si 的存在減緩了石墨基體與涂層之間的熱膨脹系數不匹配所產生的應力,減少了微裂紋的產生,同時,在高溫下 SiC 和 Si 的氧化產物能愈合熱震過程中產生的微裂紋[12],因此涂層保護了基體石墨的氧化;隨著熱震次數的增加,由于涂層中產生的微裂紋不能夠自愈合而且逐漸擴大,為氧氣進入并氧化石墨基體提供了通道,因此試樣的質量變化率逐漸降低,循環熱震15 次后試樣質量變化率為–0.17%。
結 論
采用浸涂和氣相硅浸滲法成功在石墨表面制備了 SiC 抗氧化涂層,涂層致密無裂紋,主要由粒徑不同的 α-SiC,β-SiC 及少量殘余硅組成。
涂層可有效防止石墨材料在高溫條件下的氧化,1200 ℃空氣條件下氧化 16 h 后試樣每小時增重量約為 2.18 mg/cm2,提高了石墨在有氧環境下的使用壽命。
涂層具有良好的抗熱震性能,經 1000~25 ℃循環熱震 15 次后試樣質量變化率僅為–0.17%。
免責聲明:本網站所轉載的文字、圖片與視頻資料版權歸原創作者所有,如果涉及侵權,請第一時間聯系本網刪除。
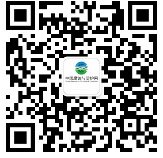
官方微信
《中國腐蝕與防護網電子期刊》征訂啟事
- 投稿聯系:編輯部
- 電話:010-62313558-806
- 郵箱:fsfhzy666@163.com
- 中國腐蝕與防護網官方QQ群:140808414