摘要
微生物腐蝕是造成管線材料破壞和失效并導致巨大經濟損失的一個重要原因,發展具有耐微生物腐蝕性能的新型管線鋼是從材料自身角度降低發生微生物腐蝕傾向的新途徑,具有重要的科學意義和應用價值。在傳統的管線鋼化學成分基礎上,通過適量的Cu合金化,在服役環境中發生的微量銅離子的持續釋放會殺死細菌并抑制細菌生物膜形成,從而起到耐微生物腐蝕作用,這是提高管線鋼耐微生物腐蝕性能的主要創新思想。本文通過總結當前管線鋼的微生物腐蝕及其研究現狀,提出了一種從材料角度防治微生物腐蝕的新方法。介紹了新型含Cu管線鋼在合金設計、組織結構、力學性能、抗氫致開裂性能和耐微生物腐蝕性能方面的研究進展,重點介紹了含Cu管線鋼在實驗室條件下的耐微生物腐蝕性能研究結果,最后展望了新型含Cu管線鋼的未來發展趨勢。
關鍵詞: 管線鋼 ; Cu合金化 ; 顯微組織 ; 力學性能 ; 微生物腐蝕 ; 氫致開裂
微生物腐蝕(microbiologically influenced corrosion,MIC)是指附著在材料表面生物膜中微生物的生命活動導致或促進材料腐蝕破壞的一種現象[1]。它是一種電化學過程,在能量、碳源、電子供體、電子受體和水的聯合作用下完成[2]。微生物腐蝕能在土壤、淡水、海水和油田等多種環境下發生[3],如石油開采、儲存和輸運系統,船舶系統,污水處理管道,飲用水管道,發電廠冷卻水循環系統,機車燃油儲存罐等都有不同程度的微生物腐蝕發生。微生物腐蝕以局部腐蝕(如點蝕)為主,腐蝕的發生、發展在時間和空間上具有不可預見性,由此引起的安全、環境和經濟損失等問題越來越突出。據統計,全球因微生物腐蝕造成的損失約占總腐蝕的20%[4]。油井管75%的腐蝕和地埋管線50%的故障都來自微生物腐蝕[5]。據相關調查,美國81%的嚴重腐蝕與微生物相關,埋地金屬腐蝕至少有50%是由于微生物腐蝕的參與,油井管77%以上的腐蝕與微生物有關[6]。2002年,美國一項腐蝕損失調查表明,腐蝕損失占其國內生產總值的3.1%,其中微生物腐蝕約占所有金屬和建筑材料腐蝕破壞的20%,每年因微生物腐蝕引起的損失約為30~50億美元[7]。我國每年因微生物腐蝕造成的損失高達500億元[7]。微生物腐蝕造成的經濟損失巨大,而且防治困難。以往,人們總是用非生物的腐蝕機制來解釋觀察到的腐蝕現象,而微生物對腐蝕的影響往往被忽略,但實質上大多數的腐蝕都是微生物參與下的電化學過程[1]。隨著檢測手段的日益發展,微生物在腐蝕過程中的作用越來越受到重視。近年來,金屬材料尤其是鋼鐵材料的微生物腐蝕已引起了國內外學者的廣泛關注,成為一個重要的研究課題[3,8]。
微生物對材料的腐蝕和分解是一個復雜的科學問題,長期以來由于缺乏對微生物腐蝕機理的深入認識,人們甚至認為微生物腐蝕是腐蝕領域中的一個“謎”[9]。目前,已公認的導致發生微生物腐蝕的主要因素是生物膜,即微生物附著于材料表面并形成生物膜,是材料腐蝕過程中的重要步驟[10,11]。生物膜是由一種或多種微生物組成,并由其自身產生的胞外多聚物(主要為多糖)包圍而形成的復雜混合膜物質,它可以通過多種方式影響腐蝕的發生[1]。生物電化學研究[12,13,14,15,16,17]表明,附著在金屬表面的生物膜內的細菌,可通過直接電子轉移(細胞膜上的電子轉運蛋白)或間接電子轉移(自身分泌的生物小分子電子轉移載體)從金屬獲得電子,從而導致金屬微生物腐蝕的發生。如果生物膜被抑制或破壞,微生物腐蝕發生的機率將會大大減小。因此,控制微生物腐蝕的有效途徑之一就是控制生物膜在材料表面的形成和生長。
然而,目前應用于管線微生物腐蝕的控制措施并不多,且有較大局限性,最常用的防治微生物腐蝕的方法包括殺菌劑和抗菌涂層[18,19],但上述手段尚難以有效緩解微生物腐蝕所造成的危害。殺菌劑可直接殺死環境介質中的微生物。但殺菌劑的大量使用會增加環境的負擔,破壞生態環境,長期使用易誘導產生耐藥菌,使其有效性喪失。而且多數殺菌劑對游離微生物較為有效,但對生物膜的滲透和剝離能力不足,很難殺死附著在材料表面生物膜中的微生物。抗菌涂層是在材料表面涂覆對微生物有毒的物質以防止生物膜附著,從而延緩材料微生物腐蝕的方法。目前應用最為廣泛的是以Cu2O為主要成分的防污劑,多用于海洋船舶材料的防污涂覆,而其它微生物污染嚴重的防污涂料已經被國際海事公約明確禁止使用[20]。從國內外對管線微生物腐蝕防治措施來看,目前還沒有完全解決材料的微生物腐蝕問題,控制微生物腐蝕的措施仍然是長期使用殺菌劑和抗菌涂層。由于環保要求和不完全有效等原因,殺菌劑和污染嚴重的抗菌涂層的使用會受到越來越嚴格的限制,而發展新型耐微生物腐蝕材料是一種更有效的選擇。
銅離子具有強烈的抗菌作用。人們認識和利用銅離子殺菌的歷史非常悠久,為此人們已開發出多種類型的含Cu抗菌材料和涂層[21,22]。自2003年以來,中國科學院金屬研究所對含Cu抗菌不銹鋼的系統研究,使人們對不銹鋼中加入適量Cu元素所具有的抗菌性能和微量銅離子釋放起到抑制細菌生物膜形成的作用形成了共識[23,24,25,26,27,28]。鑒于此,中國科學院金屬研究所的研究團隊將含Cu抗菌不銹鋼的設計思想拓展到低合金高強度管線鋼中,針對微生物腐蝕導致的管線失效問題,提出設計和開發具有耐微生物腐蝕特性的含Cu管線鋼新材料[29,30]。本文首先綜述管線鋼的微生物腐蝕及其研究現狀,然后介紹新型含Cu管線鋼在合金設計、組織結構、力學性能、抗氫致開裂(HIC)性能和耐微生物腐蝕性能方面的研究進展,以增進鋼鐵企業對新型含Cu耐微生物腐蝕管線鋼的認識和了解,為我國鋼鐵材料的創新發展提供一條新的途徑。
1 管線鋼的微生物腐蝕及其研究現狀
我國自21世紀初“西氣東輸”一線工程啟動,截止到2015年底,長輸油氣管道總里程已達12×104 km,預計到“十三五”末將超過16×104 km[31]。這些縱橫交錯的管道一旦發生腐蝕失效,極易造成經濟損失、生態環境破壞和人員傷亡。近年來,國內外報道了大量微生物腐蝕導致的管線失效案例,微生物腐蝕已經成為石油、天然氣和水處理等工業領域中非常棘手的難題。微生物腐蝕會造成石油管道的泄漏和注射井的堵塞,從而導致石油在生產、運輸過程中存在潛在安全風險[32]。
微生物腐蝕導致的管線失效案例最早是1934年由von Wolzogen Kuhr等人發現的[2]。此后,研究人員針對細菌對管線鋼腐蝕的影響展開了大量研究。2000年,Li等[33]報道了韓國石油天然氣公司1條X65級長輸管道因微生物腐蝕導致全面停工勘察。現場調查發現,在失效管線表面覆蓋著一層易于剝離的黑色沉淀物,滴加鹽酸后散發出“臭雞蛋”氣味,表明腐蝕產物為硫化物。隨后,研究人員從腐蝕產物分析、腐蝕坑的形貌特點和土壤中高的細菌數量以及可利用的能源和C源,證實埋地管線剝離涂層下發生了硫酸鹽還原菌(SRB)和產酸菌(APB)的腐蝕。類似的案例同樣發生在德國,Enning和Garrelfs[34]報道了1條埋在沼澤地下的輸氣管道發生了剝離涂層下的SRB腐蝕,致使剝離涂層下管道外壁出現多處毗鄰的坑狀腐蝕,造成管壁的大幅減薄,給管道運輸帶來極大的安全隱患。2004年,伊朗北部的1條X52級埋地管道由于山體滑坡導致管線發生應力腐蝕開裂。分析原因發現,裂紋起裂處存在大量SRB導致的點蝕坑,這是SRB誘導管線失效的一個典型案例[35]。2006年,美國阿拉斯加隸屬于英國石油公司(BP)的Prudhoe Bay油田中1條長度為863 km原油管道發生泄漏,這是該油田30多年開發歷史中最大的一次泄漏事故[36]。這條線路擔負著運輸全美國每年用油量的20%,Prudhoe Bay油田突然停止原油供應,造成環境的嚴重污染和國際油價的大幅度提高。事后,經過權威部門調查研究,微生物腐蝕被認為是造成這次事故的主要原因。Bhat等[37]在2011年報道了微生物腐蝕導致直徑為20.32 cm、壁厚6.4 mm的X46級石油和產出水運輸管道在服役8個月后失效,導致大量石油泄漏,造成附近農田的大面積污染。同樣在2011年,Al-Jaroudi等[38]報道了1條直徑686 mm、長25.5 km、材質為C1018鋼的原油埋地管道在服役3 a后有8處因SRB導致的穿孔泄漏。在中國,劉黎[39]報道了1條X52級輸油管道因微生物腐蝕發生爆管泄露事件。在這之前,該條管道沿線起伏管段曾多次發生內腐蝕穿孔泄漏事故。對事故的最終調查認為,該管段起伏較大,原油流量較低,難以將微量游離積水帶走而聚積在低洼處,致使SRB得以生存和大量繁殖,導致局部腐蝕失效。2014年,牛濤等[40]報道了1條X60級輸氣管線鋼管在埋地1 a后,7.1 mm厚的管身出現腐蝕孔漏氣現象,通過現場調研及取樣分析,明確了蝕孔產生的原因為SRB造成的微生物腐蝕。2016年,Xiao等[41]報道了1條X52級從中國甘肅運往寧夏的原油管道因遭受SRB和氧腐蝕共同作用導致管線早期失效。除此之外,Jack等[42]在聚氯乙烯和聚烯烴涂層下觀察到了管線鋼的微生物腐蝕。Pikas[43]調查了美國德克薩斯州和新澤西州的4段管道失效原因,結果表明,瀝青/煤焦油瓷漆涂層下的管線鋼發生了微生物腐蝕。加拿大橫加公司調查表明,每6起管道外部腐蝕失效事故中,大約有3起是由于微生物腐蝕引起的[44]。
對于管線鋼的微生物腐蝕研究,不僅對現場腐蝕失效案例進行了大量分析,而且在實驗室也進行了廣泛的研究工作。Chen等[45]研究發現,SRB的存在會降低X70管線鋼的開路電位,而且相比無菌條件,含有SRB條件下的腐蝕電流密度會變大。同時還發現在沒有SRB存在情況下,施加-775 mV (vs SCE)陰極電位保護可以完全避免X70管線鋼剝離涂層下的縫隙腐蝕,然而SRB的存在使其陰極保護失去作用。Alabbas等[46]同樣研究了有無SRB參與的情況下X80管線鋼的腐蝕行為,認為在含有SRB條件下X80管線鋼的腐蝕速率是不含SRB條件下的6倍之多,可見,SRB對管線鋼腐蝕影響的嚴重性。Wu等[47]先后研究了X80管線鋼在有無應力加載、陰極保護電位大小的情況下,SRB對X80管線鋼應力腐蝕開裂敏感性的影響,結果表明,SRB誘導的點蝕是管線鋼應力腐蝕開裂的直接原因;SRB的生理活動和外加陰極電位共同提高了管線鋼應力腐蝕敏感性,而這種敏感性的提高隨著外加電位的降低而有所減弱。Sun等[48]分別在中性土壤浸出液和酸性土壤浸出液環境下研究了有無SRB對管線鋼的腐蝕影響,結果顯示,實驗初期SRB的生理活動減緩了腐蝕速率,實驗后期SRB又加速了腐蝕速率。Kuang等[49]研究了SRB的生長過程對碳鋼的腐蝕影響,結果表明,碳鋼的腐蝕速率在SRB的繁殖階段最大,而且與SRB的代謝產物積聚息息相關。
以上可以看出,管線鋼的微生物腐蝕研究多集中在有無微生物參與或者微生物的生理活動對腐蝕的影響等方面,而對于材料本身的冶金因素對微生物腐蝕的影響并不多見。1972年,Mara和Williams研究了不同C含量碳鋼在SRB作用下的腐蝕行為,結果表明,隨著鋼中C含量的增加,微生物腐蝕速率增加,但相關原因并沒有闡明;另一項研究結果表明,大腸桿菌(Escherichia coli)的參與加速了不同C含量Fe-C合金的腐蝕,但其腐蝕速率與C含量并沒有直接關系[50]。在上述2項工作基礎上,Javed等[50]認為微生物腐蝕速率與細菌在鋼表面附著的數量有很大關系,為此對不同強度級別和不同組織形態的低碳鋼中細菌的初始附著數量進行了原位統計,結果顯示,在與細菌共培養的1 h內,隨著鋼中C含量的增加,珠光體含量增加,鋼的強度相應增高,Escherichia coli在其表面的附著數量減少。另外,Sreekumari等[51]以及Javed等[52]還發現,碳鋼的晶粒尺寸越小,其附著的細菌數量越多,表明微生物腐蝕速率隨晶粒尺寸減小而變大。
此外,關于生物膜的形態對管線鋼腐蝕性能的影響、土壤環境對管線鋼微生物腐蝕的影響、交流電和微生物共同作用對管線鋼腐蝕的影響、管線的微生物腐蝕監測與防治等方面做了大量研究工作[53,54,55]。然而,這些研究結果均沒有從材料自身上解決管線鋼遭受微生物腐蝕的威脅。因此,發展具有耐微生物腐蝕性能的新型管線鋼材料為管線的微生物腐蝕的防治提供了一個新途徑。
2 新型含Cu管線鋼的合金設計
新型含Cu管線鋼的合金設計思想如圖1所示。鋼中的關鍵合金化元素是Cu,是保證新型管線鋼提高強度和抗氫致開裂性能(提供有益的氫陷阱),同時還兼具耐微生物腐蝕性能的必要條件。在Fe-Cu二元相圖中,Cu在奧氏體相中的溶解度較大,而在鐵素體相中的溶解度較小,并隨著溫度的下降,溶解度急劇降低,室溫時Cu幾乎不溶于α-Fe。因而軋制后緩慢冷卻或經時效處理后,Cu會以第二相的形式析出,從而對鋼起到強化作用。Cu的加入不僅能夠促進管線鋼表面保護膜的形成,減少H原子對鋼基體的“入侵”,而且在時效過程中析出的納米尺度富Cu相還可以起到有益的氫陷阱作用,大幅減少鋼中H的有害作用。對于耐微生物腐蝕性能,當Cu含量較低時,基體中析出的富Cu相不足,耐微生物腐蝕作用較小;當Cu含量相對過高時,會對沖擊韌性及熱加工性能產生不利影響。因此綜合考慮,Cu的設計含量為1.0%~2.0% (質量分數,下同),以保證在軋制后的時效處理或緩冷過程中,納米尺寸富Cu相在基體中均勻彌散析出,從而可起到多重有益作用。此外,采用降低C含量、低S、低P的設計原則,可降低鋼中形成夾雜物帶來的不利影響,使管線鋼具有較高的韌性和耐蝕性能。通過加入適量Nb和Mo,可以有效細化晶粒尺寸,提高鋼的強韌性。加入適量Ni,可在改善韌性的同時,減小Cu在鋼中的熱脆傾向。現有商用管線鋼中的Mn含量較高,通過適當降低Mn含量,增加Cu含量,一方面可以抵消Mn含量降低導致的強度損失,另一方面還可以改善抗氫致開裂性能[56]。
圖1 新型含Cu管線鋼的化學成分設計思路
按照上述成分設計思想,本研究團隊設計了一種新型含Cu耐微生物腐蝕管線鋼[29,30]。對不同級別含Cu管線鋼經過反復成分優化,最終獲得具有優異強韌性能和耐微生物腐蝕性能配合的最佳Cu含量范圍:X80級管線鋼為1.0%~1.2%,X65級管線鋼為1.3%~1.5%。表1列出了2種不同強度級別的含Cu管線鋼和對照商用鋼的化學成分分析結果。為了制定合理的控軋控冷工藝,從而獲得理想的組織,研究了新型管線鋼的相變規律[57,58]。根據相變規律研究結果,制定出熱機械控制軋制和控制冷卻工藝[59]。
表1 新型含Cu管線鋼和傳統商用管線鋼的化學成分分析結果 (mass fraction / %)
3 新型含Cu管線鋼的組織與力學性能研究
3.1 含Cu管線鋼時效處理后的組織形貌
組織結構是影響金屬材料性能的內在基礎,在給定成分下,管線鋼的控軋控冷工藝決定了組織結構的形成。圖2[60]為X80級含Cu管線鋼顯微組織的OM像和組織中析出的納米尺寸富Cu相。X80級含Cu管線鋼具有典型的針狀鐵素體組織,這種組織中含有大量的亞結構、高的位錯密度、無規則分布的非等軸鐵素體等特征,從而賦予管線鋼更高的強韌性匹配[61]。控軋控冷后,經過時效處理(500 ℃、1 h)的含Cu管線鋼的基體中析出了納米尺寸富Cu相[60],這種納米尺寸富Cu相為提升管線鋼的強度和抗氫致開裂性能以及具備耐微生物腐蝕性能奠定了基礎。
圖2 X80級含Cu管線鋼顯微組織的OM像和組織中析出的納米尺寸富Cu相[60]
與X80級管線鋼相比,低強度級別的X65含Cu管線鋼組織結構為多邊形鐵素體(圖3a)。這種組織可以在較慢冷速下獲得,不僅可以達到相應的強韌性能,而且在慢冷過程中還可以同時析出富Cu相,起到補充時效處理的作用。圖3b是X65含Cu管線鋼經慢冷及時效處理(550 ℃、2 h)后析出的納米尺寸富Cu相。可見,析出相密度明顯高于X80級含Cu管線鋼(圖2b[60])。不可否認,X65含Cu鋼中具有較高的Cu含量(表1),而且慢冷過程中進行的非等溫時效也起了重要作用。
圖3 X65級含Cu管線鋼顯微組織的OM像和組織中析出的納米尺寸富Cu相
3.2 含Cu管線鋼的力學性能
實現含Cu管線鋼具有“結構/功能”一體化的前提是保證新型鋼達到相應力學性能的要求。圖4[60]為X80含Cu管線鋼與對應的商用管線鋼的力學性能比較。控軋控冷并時效處理的X80含Cu管線鋼不僅屈服強度提高近30 MPa,而且其沖擊韌性(120 J vs 116 J)與商用管線鋼相當[60]。對于X65管線鋼,雖然軋制狀態的強度不及對照鋼,但經過慢冷及時效處理的X65-Cu管線鋼的強度大幅提高,而且沖擊韌性仍然高于對照鋼,表現出優異的強韌性(圖5)。以上力學性能結果為含Cu管線鋼實現“結構/功能”一體化奠定了前提基礎。
圖4 X80-Cu (1.0Cu as-aged)和X80管線鋼的拉伸應力-應變曲線和沖擊斷裂形貌[60]
圖5 X65-Cu和X65管線鋼的力學性能
4 新型含Cu管線鋼的耐微生物腐蝕性能研究
4.1 X65含Cu管線鋼耐SRB腐蝕性能
對化學成分和力學性能優化后的含Cu管線鋼進行了耐微生物腐蝕性能研究。圖6為在API-RP38培養基中培養14 d后,SRB在X65管線鋼表面的活/死情況。商用X65管線鋼(圖6a)表面上只有活的細菌附著(圖中綠色點),而經軋制和慢冷后的X65-Cu管線鋼(圖6b)表面出現了部分黃色點和紅色點,表明富Cu相在鋼中未充分析出的情況下,還沒有顯示出強烈的抑制生物膜形成的作用,只表現為殺死(紅色點)或損傷(黃色點)部分細菌。經過等溫時效(550 ℃、2 h)處理后,含Cu管線鋼表面綠色點(活細菌)的數量急劇減少,同時出現紅色點(死細菌),表現為優異的抑制細菌生物膜形成的作用(圖6c)。
圖6 在API-RP38培養基中培養14 d后硫酸鹽還原菌(SRB)在X65含Cu管線鋼表面活/死染色形貌的CLSM像
圖7為X65管線鋼在接種SRB的土壤浸出液中培養65 d后去除表面細菌生物膜和腐蝕產物后的腐蝕形貌。可以看出,商用管線鋼(圖7a)和軋態未經時效的含Cu管線鋼(圖7b)表面上不僅出現了“密”而“深”的點蝕坑,而且表面砂紙研磨的痕跡已經模糊,表明鋼的表面同時發生了均勻腐蝕和點蝕。而經過時效處理后的含Cu管線鋼(圖7c)表面上的研磨痕跡依然清晰,而且點蝕坑“疏”而“淺”。實驗結果與細菌在鋼表面形成的生物膜結果一致,表明細菌生物膜對微生物腐蝕有重要影響。同時也說明并非所有狀態的含Cu管線鋼都具有良好的耐微生物腐蝕特性,要想具有良好的耐微生物腐蝕性能,不僅要添加適量的Cu元素,還必須進行合適的時效處理,使鋼中的過飽和Cu能充分析出,這是含Cu耐微生物腐蝕管線鋼的關鍵技術之一。
圖7 X65含Cu管線鋼在API-RP38培養基中培養65 d后表面點蝕形貌的SEM像
微生物腐蝕的特點是以局部腐蝕(點蝕)為主,為了評價微生物導致的鋼表面點蝕程度,利用激光掃描共聚焦顯微鏡(CLSM)統計了以上3種狀態X65級管線鋼的4個平行樣品點蝕坑的直徑和深度,每個平行樣品隨機選取30個點蝕坑進行測量,最終選取每個平行樣品中點蝕坑深度最深的5個點繪入圖8中。結果發現,商用X65管線鋼的點蝕坑深度分布在10~35 μm內,坑直徑在30~80 μm內;未經時效的含Cu管線鋼的點蝕坑深度在7~15 μm內,坑直徑在6~33 μm內;經時效處理的含Cu管線鋼的點蝕坑深度在2~8 μm內,坑直徑在4~31 μm內。由此可見,商用X65管線鋼的點蝕坑深度和點蝕坑直徑均遠大于含Cu管線鋼,而經過時效處理后的含Cu管線鋼的耐點蝕程度優于未經時效處理的含Cu管線鋼。由此表明,鋼中析出的納米尺寸富Cu相對其耐微生物腐蝕性能起到了關鍵作用[62]。
圖8 X65含Cu管線鋼在API-RP38培養基中培養65 d后的點蝕坑數據統計
4.2 X80含Cu管線鋼耐SRB腐蝕性能
圖9[63]為更高強度級別的X80管線鋼在接菌SRB的土壤浸出液中浸泡20 d后鋼表面點蝕形貌的SEM像。在X80-Cu鋼和X80鋼表面上均可明顯觀察到砂紙研磨痕跡,表明2種鋼都沒有發生均勻腐蝕。X80-Cu鋼表面出現輕微的點蝕坑,而且分布不均勻。而X80鋼表面則出現了大量的點蝕坑,坑與坑之間幾近相連。而且可觀察到X80鋼的點蝕坑深度明顯大于X80-Cu鋼。
圖9 X80-Cu鋼和X80鋼在含有SRB的土壤浸出液中浸泡20 d后表面腐蝕形貌的SEM像[63]
分別對2種鋼進行了點蝕坑形貌三維立體重構和點蝕密度統計。選取2種鋼表面上30個較深的點蝕坑進行CLSM測量,并統計最大和平均點蝕深度。由SRB造成點蝕坑的直徑尺寸分布、密度、最大點蝕坑深度及平均點蝕深度測量結果見圖10和表2。從點蝕坑直徑分布圖可知,X80管線鋼表面上的點蝕坑直徑分布在5~35 μm范圍內,直徑為15 μm左右的點蝕坑數量最多。而X80-Cu管線鋼表面的點蝕坑直徑較小,最大點蝕坑直徑僅在10 μm左右。從點蝕坑密度數據來看,二者明顯不同。X80管線鋼表面的點蝕坑密度高達508 mm-2,腐蝕嚴重。而X80-Cu管線鋼的點蝕坑密度僅為68 mm-2,腐蝕程度較輕。最大點蝕坑深度的三維形貌如圖11[63]所示。X80-Cu管線鋼表面的最大點蝕坑深度為1.9 μm,直徑為10.5 μm (圖11a[63]);而X80管線鋼表面的最大點蝕坑深達23.6 μm,直徑達到318.2 μm (圖11b[63])。SRB環境下X80管線鋼形成的點蝕坑深度和直徑均遠大于X80-Cu管線鋼,顯示后者具有優異的耐SRB腐蝕性能。
圖10 X80-Cu和X80鋼在含有SRB的土壤浸出液中浸泡20 d后表面上的點蝕坑直徑分布
表2 X80-Cu和X80鋼在含有SRB的土壤浸出液中浸泡20 d后的點蝕坑數據統計
圖11 X80-Cu和X80鋼在含有SRB的土壤浸出液中浸泡20 d后的點蝕坑三維形貌[63]
4.3 X80含Cu管線鋼耐銅綠假單胞菌(P. aeruginosa)腐蝕性能
P. aeruginosa是一種需氧菌,在自然界中分布廣泛,是土壤、海洋等環境中存在的最常見的細菌[64]。為了驗證含Cu管線鋼耐微生物腐蝕性能的廣譜性,對X80-Cu管線鋼和對比X80管線鋼在含P. aeruginosa的2216E介質中進行了腐蝕實驗研究。圖12[60]比較了X80-Cu和X80管線鋼在接菌P. aeruginosa的2216E培養基中經過1、3和5 d浸泡后的生物膜厚度。從圖中可以看到,5 d內2種鋼表面上的生物膜厚度逐漸增加,說明細菌在前5 d處于快速繁殖期。
圖12 X80-Cu (A1.0Cu)和X80鋼在銅綠假單胞菌(P. aeruginosa)菌液中經過1、3和5 d浸泡后的生物膜厚度[60]
圖12[60]表明,經過3和5 d浸泡后的X80-Cu鋼表面的生物膜平均厚度要略低于X80鋼,這可以從圖13[60]觀察到的細菌活性情況來解釋這一現象。與P. aeruginosa菌液共培養1 d后,2種鋼表面上只有活的細菌附著(圖13a和b[60]中綠色圓點);浸泡3 d后,X80-Cu鋼表面出現了大量死細菌(圖13c[60]中紅色圓點),而且死細菌多出現在下層,即接近鋼的表面,而X80鋼表面上仍然為活細菌附著(圖13d[60]中綠色圓點)。由此可以推斷,經過3 d的浸泡,X80-Cu鋼表面可有效殺滅部分細菌。隨著浸泡時間延長到5 d,雖然生物膜厚度有所增加,但X80-Cu鋼表面的死細菌數量也在增加(圖13e[60]),而X80鋼表面附著的細菌仍然活性較強,而且細菌分布更加致密(圖13f[60])。
圖13 X80-Cu和X80鋼在P. aeruginosa菌液中經過1、3和5 d浸泡后活/死細菌的CLSM像[60]
圖14[60]為2種管線鋼在接種P. aeruginosa的2216E培養基中浸泡14 d后去除生物膜和腐蝕產物后的表面點蝕形貌。由圖可見,X80-Cu鋼和X80鋼表面仍然可觀察到砂紙研磨的痕跡,2種鋼并沒有發生均勻腐蝕,這與上述SRB腐蝕的形貌一致,微生物導致了鋼表面發生點蝕,但并未造成均勻腐蝕。從2種鋼表面的點蝕數量、形貌和分布來看,生物膜中細菌被殺死的X80-Cu鋼表面只出現輕微的點蝕坑,數量較少,而且分布疏松;X80鋼表面卻出現大量嚴重而且致密的點蝕坑。以上結果表明,含Cu管線鋼同樣可有效殺滅P. aeruginosa,表現為附著在含Cu管線鋼表面上的活細菌數量減少,生物膜較薄,點蝕坑深度疏而淺。
圖14 X80-Cu和X80鋼在接種P. aeruginosa菌液中浸泡14 d后表面點蝕坑形貌的SEM像[60]
以上對2種不同強度級別含Cu管線鋼和對照鋼在不同介質、不同菌種、不同時間條件下進行的微生物腐蝕實驗研究結果,證實了含Cu管線鋼具有強烈、穩定和廣譜的耐微生物腐蝕性能。結合含Cu管線鋼優異的力學性能,實現了含Cu管線鋼的“結構/功能”一體化的目標。
4.4 含Cu管線鋼耐微生物腐蝕機制探討
圖15[60]為時效態X80-Cu鋼和商用X80鋼在NS4溶液中浸泡60 d后的腐蝕截面圖和EDS分析結果。X80-Cu鋼表面未見明顯腐蝕產物/生物膜層,表明腐蝕產物/生物膜層很薄。界面與基體元素線掃描分析發現,出現了S和Cu元素峰,S峰的出現是發生SRB腐蝕的典型特征。S峰寬度在1 μm左右,相對應的位置處同時出現Cu元素峰,而且隨著深入基體內部,Cu含量有所下降(圖15a[60])。可見,X80-Cu鋼的表面出現了Cu的富集。相比而言,X80鋼截面形貌可發現明顯的腐蝕產物/生物膜層(圖15b[60])。而且,SRB生理活動導致的S含量和峰寬均高于X80-Cu鋼,S峰寬度約為4 μm,表明X80鋼的生物膜厚度較厚。由于X80鋼中含有少量的Cu (0.20%),在界面和基體處同樣也出現了Cu元素峰,但其分布較均勻,而且含量很低。可以推測,當X80-Cu鋼與含SRB的腐蝕介質接觸時,鋼中的富Cu相與基體會形成微腐蝕,從而發生Cu的離子化。然而,銅離子如何與細菌相互作用尚不明確。O'Gorman和Humphreys[65]認為,Cu的抗菌作用主要歸因于它能夠通過得失單個電子的方式改變銅離子的氧化形態(Cu+?Cu2+(Cu(I)?Cu(II))),其中Cu可以充當催化劑從而產生活性氧(ROS),如羥基自由基和超氧離子,這些活性氧可以導致細菌關鍵生理結構的蛋白、核酸或脂類的氧化性損傷,從而起到殺滅細菌的作用[66]。另一觀點認為,銅離子與其它如Zn、Fe、Ni離子等金屬離子相比,占據細菌蛋白上的重要結合位置更具有競爭力,從而使其蛋白喪失其功能[67]。銅離子自身還可能通過損壞支鏈氨基酸所必需的細胞質酶中的Fe-S集群來達到使蛋白失去活性的目的[68]。由此可見,鋼中Cu具有抗菌作用是一個多因子交互影響的結果,并不存在一個普適的抗菌機制。綜合實驗結果和以上觀點可以得出,含Cu管線鋼中起到主要抗菌作用的仍是納米富Cu相中釋放出的銅離子。當含Cu管線鋼表面在接觸服役環境時會發生輕微腐蝕,而后裸露出的富Cu相釋放出的銅離子通過得失單個電子的方式改變銅離子的氧化形態,這個過程中將會產生ROS,這些ROS通過接觸細菌的蛋白、核酸或脂類造成其氧化性損傷,使其喪失活性。同時,自由的銅離子還可通過凝固細菌蛋白質來滅殺細菌。這2方面最終的結果均使細菌喪失活性,達到減輕微生物腐蝕的目的(圖16[60])。
圖15 時效態X80-Cu鋼和X80鋼在NS4溶液中浸泡60 d后的腐蝕截面圖和EDS分析結果[60]
圖16 含Cu管線鋼耐微生物腐蝕機制示意圖[60]
然而,值得提出的是,鋼中的Cu與SRB相互作用有其特殊性。Liu等[69]研究了316L-Cu不銹鋼的耐SRB腐蝕性能,結果表明,SRB在代謝過程中會產生H2S,H2S與Cu反應將降低鋼中Cu的耐SRB性能。本文作者認為SRB弱化鋼中Cu的抗菌作用的確存在,但由于SRB產生的H2S數量較少,與釋放更多的銅離子相比,只能消耗部分Cu的作用。由于耐腐蝕性不同,與含Cu不銹鋼相比,含Cu管線鋼在服役環境中會釋放更多的銅離子,這樣在中和SRB產生的H2S的同時仍會有足夠的銅離子殺死細菌,這可能是含Cu管線鋼與含Cu不銹鋼的耐SRB腐蝕性能存在差異的可能原因。
5 含Cu耐微生物腐蝕管線鋼的抗氫致開裂性能
在傳統管線鋼的合金設計中,Cu本身就是管線鋼中常見的合金元素之一。而且,Cu具有提高抗HIC性能的作用[70,71]。這種作用的機制是Cu可以促進在鋼的表面形成一層CuS及FeS1-X保護膜,減少H對鋼基體的侵入,減少了H的吸收,從而減輕了HIC的發生[70]。然而,傳統管線鋼中加入的少量Cu對進入鋼中的H所起到的作用有限。由于管線鋼的HIC本質是H進入鋼中的重新分布,因此如何使進入鋼中的H盡可能地均勻分布,而不造成H的局部富集是提高管線鋼抗HIC性能的關鍵。基于此,提出了含Cu管線鋼可同時提高其抗HIC性能的思路,如圖17所示。在新型含Cu耐微生物腐蝕管線鋼中,均勻彌散析出的細小富Cu相可為H的分布提供眾多有利位置,利用富Cu相充當有益氫陷阱的作用。通過納米尺寸富Cu相捕獲H原子,使進入鋼中的H原子均勻彌散分布,從而避免在局部區域產生高的H富集而在微觀區域發生氫脆,從而提高了管線鋼的抗HIC性能。
圖17 含Cu管線鋼提高抗氫致開裂(HIC)性能的機制
文獻[72]和[73]證實了這個思路的可行性。分別在傳統X80管線鋼的成分基礎上添加1.0%Cu (X80Cu)、1.5%Cu和2.0%Cu后,可使管線鋼的強度分別達到X80、X100和X120級別。參照NACE TM 0284標準進行了HIC性能實驗,研究結果表明,傳統X80管線鋼的抗HIC性能不佳,氫致裂紋主要沿著馬氏體/奧氏體(M/A)島與基體界面擴展;而不同Cu含量的新型管線鋼表現出優異的抗HIC性能,HIC實驗后無裂紋出現。這一研究結果不僅拓寬了新型耐微生物腐蝕含Cu管線鋼的應用領域,也為發展兼具高強度和優異抗HIC性能的鋼鐵新材料提供了一條新思路。
6 結語與展望
隨著微生物腐蝕導致的管線失效案例的增加,微生物對油氣管道造成的腐蝕問題已引起高度重視。發達國家的管線鋪設較早,出現的微生物腐蝕問題頻繁、嚴重。我國西氣東輸管線的鋪設至今已有近20 a,管線外部涂層已進入老化降解期。可以預測,我國管線的微生物腐蝕問題在不久的將來會日益突出。然而,我國對管線微生物腐蝕問題還沒有給予足夠的關注,尤其是從材料自身角度考慮微生物腐蝕的防治還未引起足夠的重視,因此,對耐微生物腐蝕管線材料的前瞻性研究具有重要的戰略意義。
新型耐微生物腐蝕含Cu管線鋼是針對微生物腐蝕導致的管線失效問題,從材料設計角度提出發展的一種結構/功能一體化鋼鐵新材料。圍繞含Cu管線鋼中最佳Cu含量的控制與性能優化、Cu的存在形式與耐微生物腐蝕行為及相關機制等一系列科學問題的系統研究,實現了X65和X80級耐微生物腐蝕含Cu管線鋼的實驗室研究開發。然而,要推動其發展和未來應用,仍面臨著一系列科學問題和技術挑戰:
(1) Cu在管線鋼中的存在形式與其耐微生物腐蝕性能的優劣密切相關。納米尺寸富Cu相比固溶于基體中的Cu具有更佳的耐微生物腐蝕性能。因此,管線鋼中富Cu析出相的形貌、尺寸、數量密度、與基體的位向關系等對其耐微生物腐蝕性能的影響需要深入研究。
(2) 含Cu管線鋼在熱機械控制軋制(TMCP)過程中可能存在發生“銅脆”的風險,含Cu管線鋼的連鑄連軋過程要嚴格控制,科學合理地制定TMCP工藝參數是耐微生物腐蝕含Cu管線鋼實現工業化生產的重要基礎。
(3) 管線鋼的應用還需考慮其焊接性能,Cu加入管線鋼中勢必會對焊接性能產生一定的影響,因此對耐微生物腐蝕含Cu管線鋼的焊接性及影響因素等仍需展開研究。
對以上這些問題的系統和深入研究,對于優化耐微生物腐蝕含Cu管線鋼的綜合性能和推動其發展及應用具有重要的理論指導意義。
免責聲明:本網站所轉載的文字、圖片與視頻資料版權歸原創作者所有,如果涉及侵權,請第一時間聯系本網刪除。
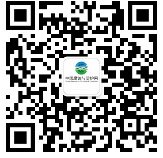
官方微信
《中國腐蝕與防護網電子期刊》征訂啟事
- 投稿聯系:編輯部
- 電話:010-62316606-806
- 郵箱:fsfhzy666@163.com
- 中國腐蝕與防護網官方QQ群:140808414