引言
聚合物驅作為油田三次采油的主要方式,由于增油效果顯著,該技術在國內陸地油田應用廣泛。渤海油田早在2003年,就開展了單井聚合物驅實驗,并取得了良好的開發效果。到目前為止,渤海油田已在遼東作業公司下轄的綏中36-1油田等油田開展了大規模聚合物驅油現場試驗。注水注聚井油管腐蝕、井內污垢積聚以及聚合物垢卡等問題日益突出,導致注采量下降,嚴重影響油田的正常生產和經濟效益。
目前,渤海油田的井下管柱腐蝕問題極為突出,這對油田開采造成了極大影響,根據腐蝕機理的不同,造成井下管柱腐蝕的原因也各不相同。要想針對性地實施防腐措施,首要問題就是明確腐蝕的原因,因此本文通過對入井液分析、氯離子腐蝕預測、SRB含量分析、天然氣成分分析、采出液腐蝕評價、腐蝕產物分析等,對井下管柱腐蝕穿孔原因進行分析,為后續防腐提供理論依據。
采出液腐蝕分析
渤海某油田在2013—2017年修井期間共發現14井次注聚受益井腐蝕穿孔,其中分離器腐蝕斷裂7井次。例如,該油田A13井2015年9月份換管柱作業中也發現油管腐蝕嚴重,電泵分離器上有直徑為1 cm的腐蝕穿孔,2018年1月,再次發現油管腐蝕穿孔現象。
圖1 A13井Y接頭以下泵頭以上雙公短節穿孔
圖2 A17井第116、117根油管連接處(深度為1136.41m)
A17井起井時發現,井下油管有腐蝕穿孔現象,油管穿孔部位主要為外大內小,邊緣尖銳,腐蝕產物輕微附著,呈現點蝕形貌,孔周圍的管壁壁厚由外向內逐漸減薄,這說明穿孔是由外向內逐漸腐蝕形成的。孔洞呈馬蹄形,邊緣尖銳,可推測腐蝕過程中不斷有介質沖刷。A13井外壁大量腐蝕坑,局部減薄達60%以上,內部未見腐蝕坑,腐蝕均勻。
井流體對管材腐蝕分析
陽離子腐蝕:含鉀離子、鈉離子和鈣離子的水都會對N80鋼產生腐蝕,平均腐蝕速率分別為0.087 mm/a,0.081 mm/a,0.11 mm/a。在同一離子濃度下,腐蝕性最強的是鈣離子。
陰離子腐蝕:N80鋼在含氯離子水中,腐蝕速率為0.09 mm/a;而在含相同濃度碳酸氫根離子的水中,腐蝕速率為0.04 mm/a,氯離子的腐蝕大于碳酸氫根離子的腐蝕。水質分析顯示水型為氯化鈣型,氯離子在4 284~4 339 mg/L之間,管柱可能存在嚴重的氯腐蝕。
氯離子腐蝕預測
采用Labor指數法對氯離子腐蝕進行預測。當LI值大于0.5時,容易發生以Cl-為主的電化學腐蝕。
采出液腐蝕評價
發現一批井油管出現腐蝕,初步懷疑該井采出液可能對管柱存在一定腐蝕。實驗通過測定N80掛片在A17井采出水中的腐蝕速率,研究該井采出水的自身腐蝕性。
實驗參考《SY/T 5405-1996 酸化用緩蝕劑性能試驗方法及評價指標》中《3. 常壓靜態腐蝕速率、緩蝕率測定方法及評價指標》,將N80掛片置于A17井采出水中,在65 ℃恒溫烘箱中放置72 h,通過測定老化前后掛片的質量,研究采出水對掛片的腐蝕情況。
圖3 腐蝕后掛片清洗前后照片
分析結果表明,該井采出水對N80掛片平均腐蝕速率為0.09675 mm/a,參考《SY/T-5329-2012碎屑巖油藏注水水質指標及分析方法》中對注水腐蝕速率要求≤0.076 mm/a。從圖3也可以明顯看出腐蝕后的掛片表面已經存在銹斑,表明該井采出水的腐蝕速率偏高,該井井下管柱腐蝕和該井采出水自身腐蝕速率偏高有一定關系。此次評價中發現的部分點蝕,可能來自于氯離子腐蝕。
水樣SRB細菌含量分析
如果井液中含有硫酸鹽還原菌SRB,當開采生成的新環境有利于細菌生長時,這些菌種就會大量繁殖產生硫化氫,進而腐蝕管柱,因此需對水樣硫酸鹽還原菌SRB含量進行檢測。水樣硫酸鹽還原菌SRB含量檢測參考SY/T 5329-2012 碎屑巖油藏注水水質指標及分析方法,連續監測水樣硫酸鹽還原菌SRB含量,恒溫箱培養溫度59 ℃,培養時間為7 d,結果顯示:未觀察到SRB細菌。
圖4 水樣硫酸鹽還原菌SRB含量檢測
天然氣成分分析
取該井伴生氣,使用《天然氣的組成分析氣相色譜法》GB/T 13610-2003檢測氣體成分。通過天然氣分析結果顯示,上述井可能存在二氧化碳腐蝕。結合井底壓力,計算A13井與A17井CO2分壓均大于0.07 MPa,參考《QHS 14015-2012海上油氣井油管和套管防腐設計指南》,采用N80普通碳鋼油管生產,有腐蝕風險。
腐蝕樣分析
外壁腐蝕樣品分析
外壁為塊狀腐蝕產物,采用德國蔡司Zeiss EVO MA15掃描電鏡進行垢樣形態及元素含量分析。通過掃描電鏡(SEM)判斷垢樣形態,對不同形態樣品進行分類(圖5)。
通常與X射線能譜儀(EDS)配合使用對材料微區成分元素種類與含量進行分析。EDS分析結果顯示,外壁腐蝕產物主要為FeCO3,Fe2O3和Fe3O4,為二氧化碳腐蝕產物及鐵的氧化物。部分腐蝕樣品含氯元素,表明存在Cl-局部腐蝕現象。
圖5 腐蝕垢樣掃描電鏡圖
內壁腐蝕樣品分析
內壁腐蝕較均勻,腐蝕產物為粉末狀細小顆粒, XRD元素分析結果表明,內壁腐蝕產物主要由C、O、Fe、Si、Cl等元素組成,Cl元素含量0.4%,說明無論管柱是否穿孔,管壁內外Cl-都在局部腐蝕過程中扮演著重要角色。根據檢索PDF卡片庫可知垢樣中結晶主體存在FeCO3(卡片號為29-0696)和Fe2(OH)2CO3(卡片號為33-0650)。
檢測結果表明,管柱內外壁腐蝕產物不同,腐蝕產物形態不同,可能原因是兩者的腐蝕機理不同。內部發生電化學腐蝕,所以為均勻腐蝕,外壁發生縫隙腐蝕,所以腐蝕坑以及穿孔現場明顯。
井下管柱腐蝕原因分析
通過以上實驗及腐蝕產物成分分析, 得出該油田井管柱腐蝕原因如下:▼▼▼
電化學腐蝕。電化學腐蝕是指金屬管體和外部環境介質發生電化學反應。在反應過程中,有分離的陰極區和陽極區,電子由陰極區流向陽極區。金屬表面分布著許多雜質, 當它與鹽水(電解質溶液)接觸時,這個表面必然有許多微小的陰極和陽極同時存在,金屬表面形成許多微小的原電池,稱為微電池。井筒不同部位的含鹽量不同,使井筒各段的電極電位不同, 可以把井下油套管看成是一個宏觀電池腐蝕。電化學腐蝕中以Cl- 影響較大, 其次是Ca2+、Mg2+含量的影響。因此,參考水質分析,含氯,礦化度高是油管腐蝕穿孔的原因之一;
二氧化碳腐蝕。單井天然氣、掃描電鏡SEM、能譜分析EDS與X射線多晶衍射XRD分析,得出腐蝕產物主要為二氧化碳腐蝕產物及鐵的氧化物,鐵的氧化物可能是在空氣中暴露后生成的。因此,油管腐蝕主要是由于二氧化碳腐蝕造成的;
聚合物腐蝕。目前發現失效油管所在大多為注聚受益井,井液的 pH=7.5~7.8,為弱堿性,當注聚中有游離態氧存在時,油管內、外壁金屬易發生吸氧腐蝕。同時聚合物的滲入會加速腐蝕產物的剝離,使得管壁減薄。
通過上述分析,總結得出如下結論:▼▼▼
井下無SRB細菌,無硫化氫氣體,腐蝕因素可排除細菌及硫化氫腐蝕;
地層水氯離子,鈣離子含量較高,是發生腐蝕的重要因素;
腐蝕主要來自地層水,地層水腐蝕速率為0.09675 mm/a,腐蝕速率較高;
井下管柱腐蝕產物主要為二氧化碳腐蝕產物及鐵的氧化物,腐蝕原因為主要為二氧化碳腐蝕;
建議停用注聚受益井對應的注入井,并檢測套管氣,聚合物含氧量,分析氧腐蝕來源,以及二氧化碳含量的變化,并提高油管耐腐蝕等級,使用耐腐蝕材料,減緩油管腐蝕。
免責聲明:本網站所轉載的文字、圖片與視頻資料版權歸原創作者所有,如果涉及侵權,請第一時間聯系本網刪除。
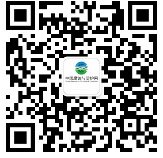
官方微信
《中國腐蝕與防護網電子期刊》征訂啟事
- 投稿聯系:編輯部
- 電話:010-62316606-806
- 郵箱:fsfhzy666@163.com
- 中國腐蝕與防護網官方QQ群:140808414