摘要
采用可控的化學氧化法制備出功能化石墨烯,最終實現石墨烯與三乙烯四胺的接枝反應。結果表明:石墨烯經化學修飾后其片層結構更平滑舒展。添加改性石墨烯的涂層在致密性、附著力等方面的性能明顯提高。化學改性通過提高石墨烯的分散性及其與環氧樹脂基料的相容性,減少涂層的內部缺陷,涂層結構更加致密,有效阻擋了腐蝕介質的擴散。同時,與環氧樹脂形成緊密結合的化學結合界面,延緩了交變壓力對該界面的破壞作用,從而延長涂層在交變壓力條件下的使役壽命。
關鍵詞: 改性石墨烯 ; 有機涂層 ; 壓力交變 ; 失效機制
深海資源的開發利用對深海設備腐蝕防護的需求與日俱增。作為金屬材料的主要防護手段[1],有機防腐涂層在深海服役時面臨嚴重的快速失效問題,影響深海設備的穩定性及安全性[2]。因此,針對復雜苛刻的深海環境研發新型防護涂料是亟待解決的難題。
傳統的重防腐涂層在深海高壓力、壓力交變條件作用下,腐蝕性介質會快速向涂層內部滲透,到達涂層/金屬界面后導致涂層附著力快速喪失,涂層從金屬表面快速剝離;涂層中的無機屏蔽填料與有機樹脂相容性差,導致填料/樹脂界面成為涂層體系的薄弱環節,在壓力作用下容易發生開裂,涂層致密性破壞從而引發提前失效[3,4,5,6,7]。可見,新型防護涂料應具有耐壓及屏蔽性能優異的特點,以實現深海環境下長效服役的目的。
石墨烯自被發現以來,在各個領域的應用研究都受到了廣泛關注[8,9]。石墨烯具有sp2雜化的C—C鍵,其理論本征強度比任何材料都要強,單片層的石墨烯擁有最大的比表面積,這些性質預計會在有機涂層應用中展現出優異的屏蔽和力學性能,理論上是作為涂層填料最理想的候選材料[10]。然而,由于石墨烯化學性質穩定,惰性的表面不親水親油,與有機樹脂的相容性較差。較高的表面能導致其片層極易發生團聚,這些都使得石墨烯在實際應用時不僅不會增強涂層的機械性能與防護性能,反而會導致性能下降[11]。
為了解決上述問題,通常選擇對石墨烯氧化物表面進行修飾。由于氧化石墨烯表面具有羥基 (—OH)、羧基 (—COOH)、環氧基 (—O—)、羰基 (C=O) 等活性官能團,可實現對其分散性及與有機樹脂相容性的改善。Mo等[12]采用硅烷偶聯劑對氧化石墨烯進行改性,硅烷分子水解生成活性的Si—OH,與氧化石墨烯邊緣的活性基團,如羥基、羧基、環氧樹脂等發生化學反應。硅烷分子上的官能團,如氨基、環氧樹脂等,可為后續的偶聯修飾提供活性位點,既提高了石墨烯的分散性,又增強了石墨烯與樹脂的相容性。與羧基反應后成功將氨基接枝到氧化石墨烯表面,實現了填料分散性的提升。Yu等[13]通過將氧化石墨烯與Al2O3顆粒進行雜化,從而提高了環氧涂層的防護性能。Chang等[14]采用原位聚合法制備了聚苯胺/四氨基苯甲酸改性石墨烯,使涂層具有更好的阻水、阻氧性能和耐金屬腐蝕性能。
然而,氧化石墨烯的制備過程通常會引入晶格缺陷,使其力學性能及阻隔性能遠低于理論值。為使石墨烯從惰性材料變為有反應功能的活化材料,同時基本保持石墨烯的原始結構,降低生成缺陷的程度,本研究采用氨水作為還原劑調整反應體系的氧化能力,使過硫酸銨的自由基與石墨烯反應并在其片層上產生環氧官能團,接著采用多乙烯多胺與石墨烯上的環氧官能團反應,制備出具有活性且較低缺陷的改性石墨烯。針對深海交變壓力環境下改性石墨烯涂層的防護性能及失效機制進行了分析,為涂層設計及研發提供一定的理論依據。
1 實驗方法
實驗采用可控的化學氧化法制備改性石墨烯填料。將0.1 g石墨烯分散至100 g水與50 g乙醇的混合溶液中,并將2 g氨水逐漸加入到上述溶液,混合并加熱攪拌。待溫度穩定后向混合物中加入2 g過硫酸銨以開始氧化反應,隨后每小時加入1 g過硫酸銨,3次后取出樣品。將獲得的懸浮液采用去離子水反復洗滌并高速離心,當pH值約為7、電導率<100 μs/cm即時停止洗滌,干燥后獲得穩定的功能化石墨烯粉末。
取0.1 g功能化石墨烯加入100 mL去離子水與10 g三乙烯四胺并攪拌均勻,超聲5 h制備改性石墨烯。提純、超聲潤洗后滿足pH值約為7、電導率<100 μs/cm即得到改性石墨烯樣品。
有機涂層成膜物質選用現役防腐涂料中常用的E-44雙酚A型環氧樹脂,其固化劑為低分子TY-650聚酰胺,溶劑為二甲苯,三者質量配比為1∶0.8∶0.4。改性及未改性的石墨烯粉末作為填料各自加入成膜物質并制成涂層 (分別稱作G-coating和MG-coating),其質量占比為0.1%。涂料配好后在25 ℃的環境中靜置0.5 h,待充分熟化后進行涂裝。
自由膜樣品用于稱重測量及拉伸實驗。將涂料刷涂至硅膠板表面,經40 ℃固化4 h后進行裁剪。拉伸樣品按照GB/T 528-92標準的尺寸進行裁剪。裁剪完成后,將自由膜繼續在60 ℃固化20 h,而后取出在室溫下 (25 ℃,RH30%) 固化24 h,以確保溶劑完全揮發。涂層/金屬樣品則是將涂料刷涂至Q235鋼試樣表面,經40 ℃固化4 h,60 ℃固化20 h后,再在室溫下 (25 ℃,RH30%) 固化1 d。固化后干態涂層厚度的平均值為 (200±10) ?m。
交變壓力實驗均在深海模擬裝置[7]中進行,交變壓力加速條件設置為:常壓0.1 MPa與高靜水壓6 MPa循環加載,以24 h為一個交變周期。前半個周期 (12 h) 在高靜水壓6 MPa下浸泡,后半個周期 (12 h) 在常壓下浸泡,浸泡至少10個周期共240 h。實驗溫度通過恒溫控溫槽控制在 (25±1) ℃,溶解氧含量保持在空氣飽和值 (約8 mg/L)。
實驗通過重量法計算涂層的吸水率。將浸泡前自由膜的重量記為m0,在不同浸泡時間t條件下的重量稱重并記為mt,則涂層的吸水率Qt按如下公式進行計算:
Qt=mt?m0m0×100% (1)
每組測量3個平行樣品,最終結果為其算術平均值。附著力測試按照ASTM D4541-02進行。用快固AB膠黏劑將不同浸泡時間條件下的涂層樣品表面與拉伸鋁錠 (直徑20 mm) 粘結起來,待粘結劑完全固化后,將涂層從基體上拉開時所需的臨界附著強度,即為涂層與金屬的附著力。每組實驗選取5個平行樣,最終結果為其平均值。涂層的強韌性測試按照ISO 37-2005進行,將浸泡后的拉伸試樣采用萬能拉伸試驗機在室溫下進行測試,加載速率為2 mm/min。為保證數據的重現性,每組實驗采用6個平行樣品。涂層微觀形貌采用掃描電子顯微鏡 (SEM,ZEISS SUPRA 55) 進行直接觀測。
電化學阻抗譜采用AutoLab PGSTAT302型電化學工作站進行測量,測量在開路電位下進行,測試頻率范圍為105~10-2 Hz,正弦擾動信號為20 mV。交變壓力下三電極體系中的工作電極為涂層/金屬電極,參比電極為固態高壓參比電極 (ESCE=-0.157 V),輔助電極為鉑電極。阻抗數據經計算機采集后,用ZSimpWin軟件進行擬合。
2 結果與討論
2.1 改性石墨烯的表征
為了分析對石墨烯功能化的效果,將過硫酸銨氧化的石墨烯進行紅外光譜 (FTIR) 測試,其結果如圖1所示。其中1220 cm-1波數處的振動特征應屬于環氧特征峰,在1140 cm-1波數處的振動峰應屬于環氧C—O—C的振動吸收峰。這些結果表明環氧官能團已經接枝到石墨烯的表面上,可實現與氨基的進一步反應。
圖1 功能化后石墨烯的紅外光譜圖
為了對比改性前后石墨烯的分散性,進行了未改性及改性石墨烯的沉降實驗,結果如圖2所示??梢钥闯?,初始時兩種石墨烯分散液都呈現均一、黑色不透明的狀態。本征態的石墨烯在8 h后全部沉淀,這是由于石墨烯本身沒有官能團,與有機溶劑的結合力較差從而分散性不佳。而通過改性處理后,石墨烯在靜置48 h后仍然可以在極性溶劑中保持良好的分散性,主要是由于氨基實現了與石墨烯表面官能團的接枝。
圖2 不同時間條件下改性和未改性石墨烯粉末在有機溶劑中的分散穩定性
通過對兩種狀態下的石墨烯進行SEM觀察,進一步分析本征態石墨烯的改性效果。從圖3可以看出,本征態石墨烯片層堆疊較多,其延展性與分散性較差,而改性石墨烯的片層堆疊數較少,石墨烯片層之間的分散的更為徹底,片層延展性更好,說明采用本方法進行的石墨烯改性可以減少片層團聚,使其分散的更加均勻。
圖3 改性及未改性石墨烯粉末的SEM像
2.2 交變壓力條件下石墨烯涂層的性能測試
水、氧氣等腐蝕性介質在到達金屬基體前會逐漸向有機涂層內部滲透,涂層的高聚物網絡結構與形態上的多孔性決定了吸水過程是不可避免的,而有機涂層中填料/基料樹脂界面的致密性是涂層耐滲透能力的關鍵[15]。通過測試未改性石墨烯環氧涂層與改性石墨烯環氧涂層的吸水隨浸泡時間的質量變化,計算涂層的吸水動力學,得到兩種涂層吸水率與浸泡時間關系的對比曲線,研究石墨烯的化學改性對涂層致密性的影響以及有機涂層中的水傳輸過程。從圖4中可以看出,兩種涂層在整個浸泡周期內吸水率的變化大致可以分為兩個階段:吸收階段和飽和階段,在吸收階段過程中,石墨烯涂層和改性石墨烯涂層的吸水率在浸泡初期明顯增加,此時水會快速滲透到涂層的孔隙中。浸泡48 h后,未改性石墨烯和改性石墨烯涂層吸水率分別為2.23%和1.99%。另外,相同浸泡時間下改性石墨烯涂層的吸水率要小于未改性石墨烯涂層,在浸泡后期兩種涂層吸水率均出現平臺,即均達到飽和狀態。浸泡周期480 h后,未改性石墨烯和改性石墨烯涂層吸水率分別為3.63%和2.71%,可見,采用三乙烯四胺改性的石墨烯不僅能延緩涂層飽和吸水時間而且明顯降低了涂層的吸水量。
圖4 交變壓力條件下未改性石墨烯和改性石墨烯涂層的吸水動力學曲線
由于涂層/金屬界面基體腐蝕、起泡等界面反應的發生,涂層濕態附著力將會顯著下降。因而涂層的濕態附著力是評價涂層防護性能的關鍵參數之一。改性與未改性石墨烯有機涂層的濕態附著力隨浸泡時間變化曲線如圖5所示。兩種涂層的干態附著力較高,為10.88 MPa。當浸泡時間為24 h時,改性石墨烯涂層和未改性涂層的濕態附著力分別下降至6.94和3.74 MPa。此時通過對涂層表面宏觀形貌的觀察,未有肉眼可見的腐蝕點,表明在形成宏觀腐蝕產物之前,附著力即發生明顯下降。隨著浸泡時間的延長,兩種涂層的濕態附著力均呈下降趨勢,表明涂層附著力都在逐漸喪失。當浸泡20個周期后,涂層的濕態附著力分別下降到1.99和1.32 MPa,此時涂層已不能很好地附在基體上。以上分析可以得出,交變壓力會導致涂層附著力的快速下降喪失,而改性石墨烯能夠延緩附著力下降的速度。
圖5 不同壓力條件下石墨烯有機涂層的濕態附著力隨浸泡時間的變化
2.3 涂層的失效歷程分析
涂層失效歷程的研究是全面準確分析涂層失效機制的基礎。電化學阻抗譜 (EIS) 是目前最成熟的涂層失效電化學評價手段之一,通過等效電路擬合可分別得到涂層電容、微孔電阻等與涂層破壞過程有關的信息。圖6和7分別為實驗所測的未改性和改性石墨烯涂層Nyquist圖。未改性涂層在最初的96 h內,只有一個容抗弧特征。從96 h到約120 h,阻抗曲線隨著浸泡時間的變化而變化,且阻抗弧的半徑隨著浸泡時間的增加而逐漸減小。隨后阻抗譜出現擴散特征。涂層在整個浸泡時期 (240 h) 內顯示了經歷了3個階段。另一方面,改性石墨烯涂層初始階段的阻抗數據也呈現單容抗弧,在120 h后阻抗譜圖呈現兩容抗弧特征。半徑隨著浸泡時間增加而減少,整個浸泡時期分為兩個階段。
圖7 改性石墨烯有機涂層在交變壓力下浸泡不同時間的Nyquist圖
圖6 未改性石墨烯有機涂層在交變壓力下浸泡不同時間的Nyquist圖
通過對兩種有機涂層EIS結果的擬合,可以確定表征涂層防護性能的涂層孔隙電阻Rc隨浸泡時間變化的曲線 (如圖8所示)。對于改性涂層和未改性涂層,240 h實驗周期內Rc值分別從1.25×1010 Ω·cm2降低到9.02×108 Ω·cm2和約9.92×109 Ω·cm2降低到6.73×107 Ω·cm2。兩種涂層的防護作用皆因吸水逐漸惡化,而交變壓力的“推-拉”作用導致涂層防護性能的快速下降。根據以上分析可以發現,改性石墨烯涂層能通過延緩水在涂層內部的傳輸而顯著地降低交變壓力帶來的破壞作用。
圖8 兩種有機涂層的涂層電阻Rc隨浸泡時間的變化
從交變壓力條件下兩種涂層的性能變化以及失效歷程分析中可知,有機涂層中的石墨烯經改性而與環氧樹脂化學結合后,涂層的防護性能有了顯著的提升。如圖9a所示,未改性石墨烯涂層添加了具有較高表面能的本征態石墨烯顆粒,為降低表面自由能,石墨烯粒子會相互聚集以減少表面積,發生團聚現象。石墨烯填料加入有機涂層體系中,在界面處就會產生一定的缺陷,難以形成結合較好的界面。涂層服役時,水等腐蝕介質在交變壓力作用下,快速滲透到涂層內部,同時涂層孔隙以及缺陷會進一步擴展,增大水的擴散速率,在填料/樹脂結合較差的位置還會出現一些相對寬松的擴散通道,使水較快地到達金屬界面。水分子在該界面存積,涂層的屏障作用減弱。涂層結構破壞達到一定程度后導致提前失效。改性的石墨烯涂層 (圖9b) 中石墨烯片層的分散性較好,填料與有機樹脂之間的結合更加緊密,因此產生的缺陷較少。在交變壓力的推拉作用下,相容性較好的界面能夠更好地延緩水的滲透及傳輸過程,結合力較好的界面不易被破壞,因此涂層的防護性能得到了改善,使用壽命大大延長。通過以上分析可以得出,顏填料的化學改性可以減少涂層內部的缺陷,使涂層的防護性能提高,并且可以在涂層服役的過程中有效地減緩腐蝕介質的傳輸滲透過程。
圖9 交變壓力下兩種涂層失效過程示意圖
3 結論
(1) 采用過硫酸銨和氨水制備出的改性石墨烯可實現石墨烯與三乙烯四胺的接枝反應。添加改性石墨烯的涂層在致密性、附著力等方面的性能明顯提高。
(2) 石墨烯經化學修飾后其片層結構更平滑舒展。化學改性提高了石墨烯的分散性及其與環氧樹脂基料的相容性,減少了涂層的內部缺陷,涂層結構更加致密,有效阻擋了腐蝕介質的擴散。
(3) 三乙烯四胺改性將氨基接枝到石墨烯表面,與環氧樹脂形成緊密結合的化學結合界面,延緩了交變壓力對該界面的破壞作用,從而延長涂層在交變壓力環境下的使役壽命。
免責聲明:本網站所轉載的文字、圖片與視頻資料版權歸原創作者所有,如果涉及侵權,請第一時間聯系本網刪除。
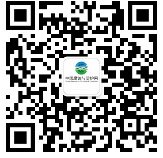
官方微信
《中國腐蝕與防護網電子期刊》征訂啟事
- 投稿聯系:編輯部
- 電話:010-62316606-806
- 郵箱:fsfhzy666@163.com
- 中國腐蝕與防護網官方QQ群:140808414