摘要
針對添加稀土Sc的新型高強7000系鋁合金中析出相的特征,發展了相應的陽極氧化工藝,并通過封孔后處理進一步提高膜層的致密性。結果表明,在7000系稀土鋁合金表面存在的含Sc析出相作為微陰極,加速其周圍Al基體的溶解,影響成膜均勻性。通過調整氧化溶液組成及電參數,在鋁合金表面獲得了均勻的陽極氧化膜。同時對比了氟鋯酸鹽、鈰鹽及沸水3種封孔工藝對陽極氧化膜耐蝕性的影響,結果顯示沸水封孔后的陽極氧化膜呈銀白色,膜層均勻致密,無缺陷和微裂紋存在,耐蝕性最佳,該膜層鹽霧測試336 h未發生腐蝕,可以滿足實際工業應用的要求。
關鍵詞: 稀土鋁合金 ; 析出相 ; 陽極氧化 ; 封孔處理 ; 耐蝕性
鋁合金具有質量輕、力學性能良好、易于加工等眾多優點,應用十分廣泛[1]。其中7000系鋁合金屬于Al-Zn系超硬鋁合金,主要用作飛機結構件和其他高強度抗腐蝕結構件[2,3]。隨著航空航天領域對鋁合金部件性能要求逐漸提高,人們嘗試對7000系鋁合金進行改性,其中添加稀土元素日益受到重視。稀土元素化學活性比堿金屬低,但比其他金屬要更活潑,所以具有很強的脫氫除氧功能,也是改善材料綜合性能的“一味良劑”。但稀土元素可與多種金屬及非金屬發生化學反應生成金屬間化合物,這些金屬間化合物會與Al基體形成腐蝕微電偶對,導致微電偶腐蝕的發生,降低鋁合金的耐蝕性,在實際使用過程中表面防護是必不可少的。
目前,陽極氧化是應用最廣泛的鋁合金防護技術。它是利用電解作用使鋁合金表面形成耐蝕性良好,且與基體結合力極佳的氧化膜。膜層一般由多孔狀的外層和致密的阻擋層組成[4]。常見的陽極氧化工藝包括鉻酸陽極氧化、硫酸陽極氧化、草酸陽極氧化和混合酸陽極氧化等[5,6,7]。其中硫酸陽極氧化工藝環保、操作簡單、成本低、膜層透明度高、耐蝕性優異,是7000系鋁合金表面處理最常用的技術。但對于稀土7000系鋁合金,由于含稀土析出相的微電偶腐蝕加速作用,采用現有的硫酸氧化工藝得到的膜層質量下降,無法滿足實際應用中耐蝕性的要求。因此,發展適宜的陽極氧化工藝尤顯重要。本文針對添加稀土Sc的新型高強7000系鋁合金中析出相的特征,在硫酸陽極氧化的基礎上添加適宜的添加劑,并對陽極氧化工藝進行優化,獲得了耐蝕性優異的陽極氧化膜。
1 實驗方法
本研究所使用的實驗材料為含稀土Sc的7000系鋁合金,具體化學成分 (質量分數,%) 為:Zn 9,Mg 2,Cu 1.1,Sc 0.25, Zr 0.3,Al余量。樣品尺寸為80 mm×50 mm×4 mm,由20 mm厚軋制板材經線切割制備。樣品表面平行于軋制面,為T74態 (固溶處理,之后時效)。
用砂紙逐級將樣品打磨至2000#,無水乙醇清洗,干燥后用于陽極氧化實驗。為了觀察合金的金相組織,將基體繼續打磨至5000#,拋光后進行刻蝕。腐蝕介質選用Kellor試劑,具體成分為95 mL H2O,2.5 mL HNO3,1.5 mL HCl,1.0 mL HF。刻蝕時間為120 s。
陽極氧化的工藝流程為:化學預處理 (堿蝕:30~50 g·L-1 NaOH,溫度40~50 ℃,時間5~20 s;除灰:20%~35% HNO3,室溫,20~30 s)→陽極氧化 (H2SO4 35~65 g·L-1,添加劑 4~16 g·L-1,電壓 12~24 V,溫度22.5~37.5 ℃,時間10~40 min)→封孔 (3種封孔方法:(a) 沸水封孔30 min;(b) 氟鋯酸鉀溶液25 ℃封孔10 min;(c) 硝酸鈰溶液30 ℃封孔30 min)→吹干,每步后水洗。使用WS30H25直流電源進行陽極氧化處理,鋁合金樣品作為陽極,鉛板作為陰極,使用恒溫水浴槽保持實驗所需的溫度。
電化學測試采用三電極體系:待測樣品為工作電極,Pt片為輔助電極,飽和甘汞電極 (SCE) 為參比電極。采用PARSTAT 4000電化學綜合測試系統進行極化曲線和電化學阻抗測量,測量前初始延遲300 s。動電位極化曲線的掃描速率是1.0 mV/s,掃描范圍從低于自腐蝕電位0.25 V至陽極電流密度急劇增大,所得到的極化曲線采用Cview軟件中的Tafel模式進行擬合。電化學阻抗測量使用的激勵信號為幅值10 mV的正弦波,頻率范圍105~10-2 Hz。阻抗譜采用ZSimpWin軟件進行擬合。電化學測試所使用的腐蝕介質為3.5% (質量分數) NaCl溶液,測試樣品工作面積為1 cm2。為了確保實驗結果的重現性,相同條件樣品至少測試3次。
陽極氧化后的樣品耐鹽霧腐蝕性能根據GJB150.11A-2009進行測試,5% (質量分數) NaCl溶液,pH值為7,24 h噴霧和24 h干燥兩種狀態交替進行,噴霧階段溫度為35 ℃,鹽霧沉積量為2 mL/(80 cm2·h),干燥階段為室溫 (20±5) ℃,相對濕度 (45±5)%。
樣品表面及截面形貌采用XL20 FEG ESEM環境掃描電鏡 (SEM) 進行觀察,采用SEM配置的能譜儀 (EDS) 進行化學成分分析。
2 結果與討論
2.1 Al基體微觀結構
拋光但未進行腐刻的鋁合金基體背散射表面形貌如圖1a所示。基體表面平整、光滑,零星分散的白色顆粒為析出相,析出相分布并不均勻,有些區域比較密集,有些區域比較稀少,這應該與合金變形加工過程導致析出相分布不均有關。由析出相的放大圖可以清晰地觀察到析出相的形貌,這些析出相尺寸大小不一,從幾微米至十幾微米,形狀也不同。
圖1 7000系稀土鋁合金SEM背散射微觀形貌
鋁合金基體拋光并腐刻后的背散射表面形貌如圖1b所示。合金的晶界清晰可見,晶粒形狀并不規則,除了大尺寸的析出相之外,晶界上還彌散分布著較多小尺度的析出相。EDS分析結果表明,大尺寸和小尺寸析出相的化學元素組成基本相同,除了Al (57.18%,質量分數) 和Zn(5.55%) 外,Zr及Sc含量較高,分別為22.76%和14.51%。結合文獻中TEM檢測及相圖分析結果可知[8,9],該第二相應為含少量Zn的Al3(Sc,Zr) 混合相。這表明稀土元素Sc在鋁合金中固溶度較低,與其他合金元素有較強的結合力,會形成金屬間化合物,以析出相的形式偏聚在晶界或彌散分布在晶內。這些析出相由Al和合金化元素組成,與Al基體的電位不同,后續的預處理及陽極氧化過程在水溶液中進行,析出相與Al基體間將會形成腐蝕微電池,影響成膜過程。除了含稀土析出相外,合金中還可能含有少量小尺寸的η相 (MgZn2)、θ相 (AlCu2)、S相 (Al2CuMg) 和T相 (Al-Zn-Mg-Cu) 等[10]。與Al3(Sc,Zr) 相比,這些相尺寸較小且數量較少,微電偶效應弱很多,后續對陽極氧化的影響不做重點考察。
2.2 化學預處理
通常,鋁合金陽極氧化前都有預處理過程,用來去除材料表面殘留的氧化皮、污物等,為陽極氧化提供良好的表面狀態。鋁合金在熱的NaOH堿蝕溶液中會發生非常劇烈的化學反應,鋁材表面迅速均勻溶解,化學反應式如下[11]:
Al表面自然氧化膜的溶解:
Al2O3+2NaOH→2NaAlO2+H2O(1)
Al基體的溶解反應:
2Al+2NaOH+2H2O→2NaAlO2+3H2↑(2)
NaAlO2發生水解反應:
2NaAlO2+4H2O→2Al(OH)3+2NaOH (3)
含Sc的7000系鋁合金堿蝕后的表面形貌如圖2所示。與未經處理的Al基體相比 (圖1a),表面增加許多腐蝕凹坑,這些腐蝕凹坑主要分布在大尺寸析出相周圍。這是由于合金元素的添加使Al基體表面微觀結構不均,不同組織間存在電位差[12,13]。Al3(Sc,Zr) 析出相的電位比α-Al基體的更正,在堿洗過程中作為微陰極,表面發生O的還原反應[14]:
O2+2H2O+4e?→4OH?(4)
圖2 7000系鋁合金堿蝕后表面形貌
其周圍的α-Al基體則作為微陽極,被加速溶解,導致析出相周圍形成腐蝕坑:
Al+4OH?→Al(OH)?4+3e?(5)
此外,圖2中有些腐蝕坑周圍并未觀察到析出相存在,可能是析出相周圍的Al基體腐蝕嚴重,導致析出相脫落,也可能是一些陽極相η(MgZn2) 溶解脫落所致。
經過堿蝕的樣品,一方面由于NaAlO2的水解反應會在表面殘留疏松的Al(OH)3沉積物,另一方面Al基體中未溶解的析出相會脫落附著在樣品表面,形成灰褐色的產物層。通過硝酸清洗可以去除灰褐色的產物,但對基體微觀結構沒有明顯影響。
2.3 陽極氧化工藝的影響
經預處理后的鋁合金進行陽極氧化處理,影響氧化膜質量的主要因素包括H2SO4濃度、添加劑濃度、氧化電壓、氧化時間及氧化溫度。根據不同處理條件獲得的膜層阻抗值的差異,對比分析了工藝參數對膜層耐蝕性的影響。
由圖3a可知,H2SO4濃度在35~65 g·L-1范圍內,陽極氧化膜阻抗值隨著H2SO4濃度的增加而先增大后減小,在H2SO4濃度為45 g·L-1時,陽極氧化膜的阻抗值最高。鋁合金在H2SO4溶液中的陽極氧化過程包括以下反應:
圖3 各工藝參數對陽極氧化膜阻抗值的影響
成膜反應:2Al+3H2O→Al2O3+6H++6e? (6)
膜溶解反應:Al2O3+6H+→Al3++3H2O (7)
陰極上發生H2O的分解析氫反應:
2H2O+2e?→H2+2OH?(8)
在H2SO4溶液中的氧化過程,實際上不只是Al氧化物的形成和溶解反應,陰離子SO42-也會參與反應過程,最終生成含SO42-的陽極氧化膜,成分為Al2O3·Al(OH)x(SO4)y。
在SO42-參與的情況下,陽極反應如下[11],即開始是Al的溶解:
2Al+6H+→2Al3++3H2↑?(9)
然后,SO42-參與氧化物的形成,成為陽極氧化膜的成分之一:
2Al3++2H2O+3SO2?4→Al2O3+3H2SO4(10)
Al3++xH2O+ySO2?4→Al(OH)x(SO4)y+xH+(11)
隨著H2SO4濃度的增加,電解液中的H+含量增加,從而加快了Al3+在溶液中的遷移速率,促進了氧化膜的生成,陽極氧化膜的耐蝕性增強。但隨著H2SO4濃度的進一步增加,電解液的酸性增強,加劇了膜的溶解反應,使陽極氧化無法正常進行,導致成膜質量下降,因此在H2SO4濃度為45 g·L-1時,膜層的耐蝕性最佳。
前面預處理過程已表明,鋁合金中的Al3(Sc,Zr)析出相作為微陰極,在其表面發生還原反應,無論是析氫反應還是氧還原反應,都會導致其周圍pH值升高。根據反應式 (9) 可知,只有在酸性條件下,析出相及其周圍的鋁合金才會溶解參與成膜過程。為了使7000系稀土鋁合金表面獲得均勻的膜層,在H2SO4溶液中復合了添加劑,能夠起到平衡電解液酸堿度的作用,控制氧化反應和溶解反應速率,獲得均勻的陽極氧化膜。由圖3b可知,在添加劑濃度為8 g·L-1時,膜層的阻抗值最高。
氧化電壓是影響膜層質量的另一重要因素,由圖3c可知,隨著陽極氧化電壓的增大,膜層阻抗值有先增大后減小的趨勢,在電壓為20 V時存在峰值。這主要是因為當電壓逐漸增大時,通過樣品表面的電量也逐漸增加,氧化膜生成的速度加快,生成的氧化膜愈發致密并逐漸增厚,使陽極氧化膜的耐蝕性增強,但隨著電壓的進一步增加,陽極氧化電流迅速增大,樣品表面電解液迅速升溫,最后造成膜層的“燒蝕”。
氧化時間對膜層阻抗值的影響如圖3d所示。隨著氧化時間的延長,陽極氧化膜阻抗值先增大后減小,在20 min時存在峰值。這是因為在反應剛開始時氧化膜的生成速率大于溶解速率,在一定時間范圍內,隨著氧化時間的增加,氧化膜逐漸變厚,耐蝕性增強;但隨著氧化時間的繼續增加,膜層擊穿困難,導致膜中微孔尺寸增大,致密性下降,耐蝕性變差。
圖3e為陽極氧化膜阻抗值隨電解液溫度的變化趨勢,在溫度為22.5 ℃時膜層阻抗值最大,隨著溫度的上升,膜層阻抗值下降。這是因為當電解液溫度較高時,膜層冷卻緩慢,導致膜中微孔數量增多,尺寸變大,致密性下降。
當然,各因素之間也存在一定交互作用。例如,氧化電壓過高時會導致樣品表面電解液溫度迅速攀升,兩者共同影響成膜過程。在實際生產中綜合考慮了各因素的影響規律,確定了最佳的陽極氧化工藝,即:H2SO4濃度45 g·L-1,添加劑濃度8 g·L-1、氧化電壓20 V、氧化時間20 min、氧化溫度22.5 ℃。在最佳成膜工藝下獲得的膜層對鋁合金的保護性采用浸泡和阻抗譜進行了測試。由圖4鋁合金陽極氧化前后在3.5%NaCl溶液中的阻抗譜對比可知,Al基體的阻抗值約為500 Ω·cm2,且低頻端阻抗值有下降趨勢,這表明鋁合金基體在NaCl溶液中已經有局部腐蝕萌生[15]。陽極氧化后的鋁合金阻抗值大于105 Ω·cm2,比Al基體的阻抗值高兩個數量級以上,且低頻端阻抗值一直呈上升趨勢,沒有局部腐蝕萌生,這表明陽極氧化膜可以為Al基體提供良好的保護。
圖4 7000系鋁合金陽極氧化前后在3.5%NaCl溶液中的阻抗譜對比
鋁合金基體及陽極氧化膜在NaCl溶液中的宏觀腐蝕形貌如圖5所示。打磨后未經任何處理的Al基體在浸泡前表面光亮,有金屬光澤存在 (圖5a)。在NaCl溶液中浸泡20 h后 (圖5b),基體表面已經完全變黑,發生明顯的腐蝕。陽極氧化后的鋁合金表面金屬光澤不復存在,在NaCl溶液中浸泡20 h后 (圖5c),表面狀態沒有發生變化,并未出現黑點等腐蝕現象,表明陽極氧化膜可以有效改善鋁合金的耐蝕性。
圖5 鋁合金基體表面形貌及鋁合金基體和陽極氧化膜在3.5%NaCl溶液中浸泡20 h的表面形貌
2.4 封孔工藝
從反應式 (6) 和 (7) 可以看出,氧化過程同時發生Al2O3膜的形成和溶解兩個反應。在通電的瞬間,Al基體表面會迅速生成較為致密的Al2O3層,即阻擋層。隨后,電解液中的酸開始溶解阻擋層,并在這層膜周圍產生電流聚積,導致氧化膜局部過熱,加速溶解,使阻擋層與電解液的界面開始生成小孔,最終形成了多孔的陽極氧化膜。為了提高膜層的致密性,陽極氧化后需要進行封孔處理。圖6對比了沸水封孔、氟鋯酸鹽封孔及鈰鹽封孔后陽極氧化膜在NaCl溶液中的阻抗譜。由圖可知,經沸水封孔后的膜層阻抗值最大,約5.7×106 Ω·cm2,明顯大于氟鋯酸鹽封孔 (7.4×105 Ω·cm2) 和鈰鹽封孔 (2×105 Ω·cm2) 后膜層的阻抗值。與圖4中未封孔膜層阻抗值 (1×105 Ω·cm2) 相比,3種封孔處理都使膜層的阻抗值有所提高,但沸水封孔使阻抗值提高的最多,這也表明鋁合金陽極氧化膜經沸水封孔后耐蝕性能更佳。
圖6 經3種封孔方法處理后的鋁合金陽極氧化膜在3.5%NaCl溶液中的阻抗譜對比
將3種封孔處理后的陽極氧化膜的阻抗譜采用如圖7所示的等效電路圖進行擬合。圖譜包括兩個時間常數,對應著兩個容抗弧信息,即高頻容抗對應外層多孔膜,低頻容抗對應內層阻擋層[16]。等效電路中,Rs代表溶液的電阻,Rp和Qp分別為多孔層的電阻和電容,描述高頻容抗特征。Rb和Qb分別為阻擋層的電阻和電容,描述低頻容抗特征。考慮到樣品表面微觀結構的不均勻性,使用恒相位角元件Q代替純電容C進行電路擬合。阻抗譜擬合后得到的等效電路參數列于表1,其中np和nb分別為Qp和Qb的彌散指數。從表中擬合結果可知,鋁合金陽極氧化膜經沸水封孔處理后,內部阻擋層的Rb達到了8190 kΩ·cm2,遠大于經氟鋯酸鹽和鈰鹽封孔處理后的Rb值。同時,外層多孔層的Rp也是沸水封孔樣品最高。這表明沸水封孔處理對陽極氧化膜內層阻擋層和外層多孔層的致密性都有明顯的改善。這是因為沸水封孔時,熱水能很快滲透到微孔中,水中的OH-與微孔中向外擴散的Al3+相遇,形成水合氧化鋁沉淀。這種水合氧化鋁是不完全結晶的假勃姆體Al2O3·3H2O。通過進一步溶解-沉淀反應,固態沉淀不斷增多,從孔壁和孔底阻擋層處開始發展,阻塞整個微孔。在封孔進行中,假勃姆體會發生再結晶,生成勃姆體型的水合氧化鋁Al2O3·H2O,勃姆體比原陽極氧化膜的分子體積大30%,使膜中大部分微孔被填充封閉,腐蝕液的運輸通道被阻斷,氧化膜的阻抗增加,耐蝕性增強[17]。
圖7 阻抗譜的等效電路圖
表1 阻抗譜的擬合結果
2.5 最優陽極氧化膜的微觀結構及耐蝕性表征
沸水封孔后陽極氧化膜的表面和截面形貌如圖8所示。鋁合金基體在表面處理前使用砂紙打磨到2000#,因此表面存在大量劃痕,盡管預處理會將Al基體表面溶解掉一層,使劃痕變淺,但仍然無法完全避免。在后續的氧化過程中,膜層在Al基體表面原位生長,且膜層較薄,不能將劃痕完全覆蓋,因此從膜層的低倍形貌中 (圖8a) 清晰可見樣品表面殘留的劃痕。無劃痕的區域膜層比較均勻,不能分辨出析出相的位置,這表明析出相周圍形成了均勻致密的陽極氧化膜。從高倍形貌照片可以清晰觀察到陽極氧化膜的狀態,膜層很均勻致密,由條狀顆粒堆積而成,條狀顆粒間也存在微小的縫隙,但這些縫隙并非貫穿的,縫隙底部依然有膜層存在,可以有效阻擋腐蝕介質的入侵。陽極氧化膜的截面形貌如圖8b所示。膜層十分致密,并未見微裂紋、微孔等缺陷,且與Al基體結合良好,厚度大約4 μm。膜層的EDS結果主要包含O,Al,S和Zn,這也證明SO4-參與了氧化成膜過程。
圖8 沸水封孔后鋁合金陽極氧化膜的表面和截面形貌
鋁合金基體、未封孔的陽極氧化膜及沸水封孔后陽極氧化膜耐蝕性采用極化曲線進行了比較,結果如圖9所示。極化曲線的擬合結果如表2所示。由極化陽極分支可見,鋁合金基體發生明顯的溶解反應,溶解速率遠高于陽極氧化處理后的樣品。同時,鋁合金基體陰極發生的氧還原反應速率也是最快的。在Al基體表面覆蓋未封孔的陽極氧化膜后,自腐蝕電位正移160 mV,自腐蝕電流密度降低近兩個數量級,陽極的溶解反應和陰極的氧還原反應速率都大幅降低。在陽極氧化膜封孔處理后,自腐蝕電位繼續正移100 mV,自腐蝕電流密度再降低約兩個數量級,而且陽極曲線存在明顯的鈍化趨勢。由極化曲線對比結果可見,鋁合金表面覆蓋陽極氧化膜后,陽極溶解反應和陰極還原反應都得到了抑制,尤其沸水封孔后膜層的防護效果大幅改善。
圖9 鋁合金基體、未封孔及沸水封孔陽極氧化膜在3.5% NaCl溶液中的極化曲線對比
表2 極化曲線的擬合結果
鋁合金陽極氧化膜及其經沸水封孔、再經鹽霧腐蝕336 h后的宏觀形貌如圖10所示。陽極氧化后樣品與鋁合金基體 (圖5a) 相比表面狀態差別不大,仍然保持銀白色狀態,但金屬光澤消失,表面隱約可見膜層存在。沸水封孔后的樣品與封孔前表面狀態沒有任何差別。封孔樣品鹽霧測試336 h后,表面顏色稍微變白,沒有出現任何腐蝕點。綜上所述,經過沸水封孔的陽極氧化膜可以為7000系稀土鋁合金提供極佳的保護,滿足工業應用中的耐蝕性要求。
圖10 陽極氧化膜及其經沸水封孔、再經鹽霧腐蝕336 h后的宏觀形貌
3 結論
(1) 添加0.25% (質量分數) Sc的7000系稀土鋁合金中的Sc會與其它合金元素結合,形成陰極析出相,彌散分布在鋁合金基體中,影響氧化成膜過程。
(2) 確定了最佳的7000系稀土鋁合金陽極氧化工藝,即:H2SO4濃度45 g·L-1、添加劑濃度8 g·L-1、氧化電壓20 V、氧化時間20 min、氧化溫度22.5 ℃,可獲得耐蝕性良好的氧化膜。
(3) 沸水封孔后的陽極氧化膜與基體結合力良好,均勻致密,與Al基體相比自腐蝕電流密度降低約4個數量級,鹽霧測試336 h未發生腐蝕,可以為7000系稀土鋁合金提供良好的防護。
免責聲明:本網站所轉載的文字、圖片與視頻資料版權歸原創作者所有,如果涉及侵權,請第一時間聯系本網刪除。
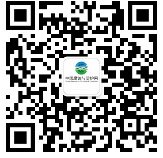
官方微信
《中國腐蝕與防護網電子期刊》征訂啟事
- 投稿聯系:編輯部
- 電話:010-62316606-806
- 郵箱:fsfhzy666@163.com
- 中國腐蝕與防護網官方QQ群:140808414