隨著工業化發展步伐的加快,腐蝕成為了工程技術領域的焦點。防腐蝕關系到煉油設備使用壽命、保證正常生產、減少污染、改善操作環境的重要工作,是一項重大課題。對于常減壓蒸餾裝置,企業應根據不同的腐蝕類型,采用多種防護技術措施,確保設備長周期安全運行。
據報道,目前煉油行業出現的大量事故中,腐蝕及泄露因素占70% ~ 90%。腐蝕不僅影響裝置運行效率,還可能造成重大事故,甚至危害生命和環境。因此,防腐蝕工作是關系到煉油裝置使用壽命、保證正常生產、減少污染、改善操作環境的重要工作,是一項重大課題。對于絕大多數煉廠來說,常減壓蒸餾裝置是必不可少的加工裝置,也是受腐蝕影響的第一道關口,科學的腐蝕分析及合理的防腐蝕對策,有助于企業實現裝置長周期安全運行。
一 常減壓蒸餾裝置主要腐蝕類型
1原油的主要成分
原油的主要成分是各種烷烴、環烷烴和芳香烴,它們并不腐蝕金屬設備。但是原油中的雜質,如無機鹽、硫化物、有機酸等,在加工過程中轉換為腐蝕性介質,對裝置和設備造成腐蝕威脅。
2腐蝕介質分類
據《煉油廠設備》分析,石油加工過程中的腐蝕性介質主要分為原油中的腐蝕性介質和石油加工過程中引入的介質兩類,見表1。
表1 腐蝕介質分類表
3 煉油廠常見腐蝕類型
煉油廠常見的腐蝕類型有三種: 硫腐蝕、環烷酸腐蝕和與氫有關的腐蝕,見表2 。
表2 煉油廠常見腐蝕類型
常減壓蒸餾裝置在高酸原料油加工過程中存在嚴重的高溫環烷酸腐蝕,同時,由于電脫鹽的難度增加以及氮含量較高,也存在較嚴重的低溫部位腐蝕。常見的腐蝕包括低溫濕硫化氫腐蝕、高溫硫化物腐蝕、環烷酸腐蝕、氯化物腐蝕、應力腐蝕破裂和其他腐蝕六種類型,見表3。
表3 常減壓裝置常見腐蝕類型
二 常減壓蒸餾裝置主要腐蝕類型原因分析
在煉油廠中,曾發生多起塔頂HCL-H2 S-H2O 腐蝕穿孔,減壓塔塔壁高溫環烷酸腐蝕,減壓塔填料高溫環烷酸腐蝕,藥劑注入口的露點腐蝕,減壓塔減壓轉油線高溫環烷酸腐蝕,含硫污水換熱器應力腐蝕開裂等情況,對安全生產造成重大威脅。科學的確定裝置腐蝕重點部位,采取切實有效的防腐蝕策略,才能確保裝置安全、平穩、長周期運行,實現裝置本質安全。
常減壓裝置重點腐蝕部位主要分布在常減壓爐( 爐管內、外壁) ,常減壓塔及塔頂管道,常減壓轉油線,冷凝冷卻系統管道及側線部位等( 見圖1 所示,黃色部分主要為氯化物和硫磺物影響區,紅色部分主要為高溫硫腐蝕影響區) 。主要腐蝕原因分析如下。
圖1 常減壓蒸餾裝置主要腐蝕部位圖
1 硫化物腐蝕
常減壓蒸餾裝置硫化物腐蝕常見原因主要為硫化物腐蝕。即原油中含有一定量的氯化物,經過脫鹽后仍存在微量鎂鹽、鈣鹽甚至鈉鹽,在有液相水的環境下生成鹽酸,造成腐蝕。硫化物腐蝕受硫化物濃度,介質溫度、流速和流態,特殊工況,pH值,材料硬度及合金成分等影響。硫化物腐蝕介質有酸性水、富胺液、貧胺液、硫化氫等。硫化物腐蝕常見為低溫濕硫化氫腐蝕和高溫硫化物腐蝕兩種類型。就常減壓蒸餾裝置而言,低溫硫化物腐蝕主要為初餾塔、常壓塔和減壓塔塔頂管道,冷凝冷卻系統管道,塔頂分液罐罐頂和罐底管道等部位。高溫硫化物腐蝕主要分布于常減壓爐進出口管道,常減壓塔底管道,含硫油品、油氣管道等部位。
2 環烷酸腐蝕
環烷酸腐蝕主要受原油酸值、溫度和流速的影響。在一定的溫度條件下,酸值越高,腐蝕越嚴重。見20#鋼所受環烷酸腐蝕與溫度關系圖2。
圖2 20#鋼所受環烷酸腐蝕與溫度關系圖
由圖2 可見,溫度在270 ~ 280℃之間腐蝕性最強; 350℃左右時,氣相濃度增加,腐蝕又加劇; 400℃左右時,環烷酸基本全部氣化,對設備的高溫部位不在產生腐蝕。環烷酸腐蝕部位常發生在加熱爐進出口管道,常減壓塔塔底及部分側線部位等,具體為常壓蒸餾部分的常壓爐爐管、常壓塔進料管、常一線、常一中、常二線、常二中、常二線進入汽提塔的進料管、常三線進入汽提塔進料管線、汽提塔兩個抽出線;減壓蒸餾部分的減壓爐管、減壓進料段、減二線、減二中、減三線、減三中、減三進入汽提塔的進料段、汽提塔進料段及彎頭、閥們、大小頭等易沖刷的部位。
3 氯化物腐蝕
氯化物主要為氯化鈉、氯化鎂和氯化鈣組成,在生產過程中受熱水解,生成氯化氫等腐蝕性物質,對金屬產生點腐蝕、應力腐蝕及縫隙腐蝕等。氯化物腐蝕的影響因素有濃度、溫度、pH 值、氧含量等。氯化物腐蝕主要發生在電脫鹽部分,常壓塔塔頂管道中。
4 金屬應力腐蝕
金屬應力腐蝕主要受敏感的金屬材料、特定的介質環境、設備運行時間和處于拉應力狀態四種因素影響,導致金屬管道產生破裂想象。
三 長減壓蒸餾裝置防腐蝕措施
由于常減壓蒸餾裝置腐蝕成因復雜,破壞形式多樣。因此,企業應樹立全面腐蝕控制理念,從設計、制造、貯運安裝、操作運行、維修五個方面和教育、科研、管理、經濟評價四個環節對各種腐蝕進行全面控制。結合常減壓蒸餾裝置具體特點,企業應根據不同的腐蝕類型,采用多種防護技術措施。
1優化防腐設計,做好原料控制
通過梳理腐蝕物質流程,進行合理的防腐設計,優化生產工藝流程,減輕或防止腐蝕。如在裝置設計時高溫易腐蝕部位采用大管徑,降低流速; 新建、更換的管道或設備內壁焊縫磨平,防止產生渦流。采取集中加工方式,進廠原料分貯分煉,均勻混合,減少分散加工對生產和設備的影響; 嚴控裝置進料,確保酸值不超過設備設防標準; 嚴控裝置進料混合比例,保持原料性質相對穩定; 根據不同原油的性質改變操作條件,掐好油頭,及時調整操作。
2 加強工藝防腐,“一脫四注”管理
對于常三線、減二線、減三線抽出線及其換熱部位的高溫環烷酸、硫腐蝕的控制措施,應加強前段工藝控制。原料進入常壓、減壓加熱爐之前,加注高溫緩蝕劑。塔器高溫腐蝕嚴重區域的側線管線上,加注緩蝕劑,控制減二線蠟油中Fe2+ ≤5 ×10-6 ,減緩腐蝕速率。采用有機胺中和劑,控制常減壓塔塔頂系統的HCl 腐蝕。塔頂揮發線注緩蝕劑,對注入點以后一系列設備進行防護。通過緩蝕劑等隔絕金屬與環烷酸等腐蝕物的接觸或反應,生成不具腐蝕性的油溶性產物,達到抑制環烷酸腐蝕,保護設備的目的。
選擇合適的電脫鹽技術,把好原油脫鹽環節。一級電脫鹽深度較小,可使原油中的鹽含量降低60% ~ 90%,大部分在80%左右。二級脫鹽基本適用于各種原油,脫鹽后的含鹽量可以控制在3.0mg /L 以下。控制好原料油電脫鹽環節的電脫鹽溫度、電場強度、注水量、混合強度及電場內停留時間等因素,充分脫除鹽類、重金屬等物質,防止低溫腐蝕和后續加工過
程中的催化劑中毒。完善注氨、注水、注緩蝕劑設施,同時采取原油注堿措施,滿足均勻、多點、可調節功能,使塔頂至冷凝冷卻完成的整個低溫系統處于堿性緩蝕環境; 健全脫后含鹽、塔頂Fe2+、Cl- 和pH 值的分析監測控制管理系統。有資料顯示,“一脫四注”后,空冷器進口腐蝕率、冷凝水鐵損失等均得到良好改善。為優化調整操作和對緩蝕劑的使用效果提供準確、完整、可靠的數據支持; 篩選合適的緩蝕劑,在多點、均勻分散條件下注入,保證緩蝕劑濃度穩定,根據Fe2+ 含量調整注入量,防止保護膜反復破壞修補,影響使用效果。“一脫四注”防腐措施可以充分抑制腐蝕介質的發生和作用,達到防腐蝕效果。
3合理選材
在控制金屬腐蝕方面,首先是做到合理選材。耐環烷酸腐蝕的主要材料是0Cr18Ni10Ti 類、316L 和317L。設備及管道選材時要考慮設備的用途、工藝過程及其結構設計特點。根據介質的溫度、流速、流態,選擇經濟合理的耐蝕材料; 根據側線硫含量、側線溫度等綜合考慮選材。高溫腐蝕環境應選擇耐蝕材料,要結合腐蝕情況選擇有效高溫緩蝕劑。冷凝冷卻系統選材以碳鋼為主; 高溫管道選材以1Cr5Mo,00Cr19Ni10 和00Cr17Ni14 Mo2 為主; 高溫泵過流部位用316L; 換熱器系統采用碳鋼材質; 常壓爐管采用5Cr- 1 /2Mo 材質,減壓爐管采用9Cr-1Mo 鋼; 轉油線采用5Cr-1 /2Mo 鋼等。
4 借助信息化工具,建立防腐蝕管理系統
一套完整的防腐蝕管理系統,可為企業提供從腐蝕預測到腐蝕檢測、分析、材料選擇、腐蝕速率評價等一整套完整的解決方案。腐蝕監控部位依據腐蝕流程選擇,結合溫度和壓力的影響來確定監測部位。通過腐蝕監測,能夠合理確定設備檢修周期,明確設備腐蝕狀態,有效杜絕因腐蝕造成的重大事故。
免責聲明:本網站所轉載的文字、圖片與視頻資料版權歸原創作者所有,如果涉及侵權,請第一時間聯系本網刪除。
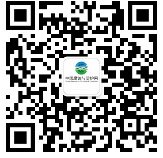
官方微信
《中國腐蝕與防護網電子期刊》征訂啟事
- 投稿聯系:編輯部
- 電話:010-62316606-806
- 郵箱:fsfhzy666@163.com
- 中國腐蝕與防護網官方QQ群:140808414