導讀
隨著國內煉油企業加工高硫原油比例的增加以及油品質量控制標準的提升,煉油企業面臨的污染物排放壓力越來越大。尤其是各裝置在停工檢修過程中,受原料及加工方案的影響,裝置產生大量的氣體、油品和污水,如果處理不當,大量油氣排放至大氣,造成環境污染。因此,如何實現綠色停工檢修是當前大型煉油企業亟待解決的問題。
以國內某大型煉廠為例,該廠項目以“常減壓-渣油加氫-催化裂化-加氫裂化-延遲焦化”為加工工藝路線,設計加工科威特高硫原油。針對首次綠色停工檢修過程存在的難點,制定專項風險控制實施方案,做到油氣全部密閉環保處理,保證了停工檢修過程環保達標,實現“氣不上天,油不落地”,為同類大型煉油企業提供了技術借鑒。
技術難點分析
01 硫磺回收裝置二氧化硫排放超標
380kt/a硫磺回收裝置是煉油項目的配套項目,采用兩級克勞斯(Claus)轉化+無在線爐尾氣還原吸收(SSR)工藝,由四個系列的制硫單元和兩個系列尾氣處理單元組成。硫磺回收裝置在停工吹硫過程中,不論采用傳統的瓦斯吹硫,還是采用新興的酸性氣完全燃燒吹硫,煙氣中二氧化硫濃度均嚴重超標,同時燃料氣吹硫易析炭污染催化劑。酸性氣完全燃燒吹硫易導致反應器床層嚴重超溫,造成催化劑失活。保證吹硫期間煙氣達標排放,同時保證系統吹硫效果,是此次硫磺回收裝置停工檢修過程主要難點之一。
02 新時期環保要求
隨著煉油企業大型化、集約化,裝置間相互關聯度增加。煉油裝置停工吹掃會夾帶大量含硫、含氨的廢氣、污水和污油,污染環境。為符合環保標準,停工檢修過程的“密閉吹掃”面臨更大的挑戰,尤其是塔器,經過多年運行,即使停工過程將存油退干凈,其器壁及內構件上仍會附著少量存油及硫化物,傳統的煮塔是采用底部給蒸汽,頂部放空。雖然器壁及內構件上的殘油被吹掃蒸汽攜帶至大氣,但現場排放會產生大量有味道的油氣,導致大氣污染。
03 系統高溫重污油管線密閉吹掃
煉油企業加工原油日益重質化、劣質化,裝置停工檢修難度增加,尤其是重油裝置,如常減壓、渣油加氫、延遲焦化以及加氫裂化裝置,停工吹掃難度大、蒸汽耗量大,而且污染物不易處理。對于重油系統管線,常規做法是在吹掃前通過從罐區引入柴油或是返回自產柴油進行置換,當重油管線出裝置處出現柴油后,改為裝置閉路循環,但在最后重油管線吹掃過程中,大量攜帶油氣的蒸汽進入罐區,高溫重污油系統面臨負荷過大和罐區出現異味等問題。另外,系統高溫重污油管線是全廠所有含重油裝置退油和吹掃的后路,使用頻繁,任務重,管理難度大。
04 硫化亞鐵自燃風險
油品中的硫對管壁發生腐蝕,生成硫化亞鐵。在設備停工檢修階段,若不采取有效預防措施,硫化亞鐵與空氣中的氧氣會迅速發生氧化反應,釋放出大量熱量,并形成連鎖反應,使溫度迅速上升,引發自燃,進而引起火災和爆炸等事故。傳統的預防硫化亞鐵自燃的措施主要有:隔離法、清洗法以及鈍化法等。該煉油廠設計原料為科威特原油,硫質量分數高達2.75%。生產過程中,加氫反應產物富含硫化氫,硫化氫和裝置塔容器及管線接觸后易反應生成硫化亞鐵,消除塔容器硫化亞鐵是綠色停工檢修難點之一。
05 胺液系統回收儲存難度大
全廠胺液系統按富液來源分為非加氫型、加氫型及硫磺尾氣胺液系統等3個系統,并對應其配套的溶劑再生系統。正常運行期間,全廠胺液系統總量約4000t,而溶劑再生系統貧液儲罐的有效罐容僅3000t,還要考慮停工期間胺液系統將產生大量的高濃度沖洗液必須進行回收、儲罐儲存胺液時的安全高度要求、硫磺尾氣的胺液不能與其他兩個系統的胺液互混互用等因素,因此在當前胺液濃度下,溶劑再生系統現有的罐容不能滿足停工檢修期間胺液儲存要求。
解決措施及效果
1 硫磺回收裝置“熱氮吹硫”
借鑒同類裝置成功應用經驗,硫磺回收裝置停工期間采用“熱氮吹硫”方案:以氮氣為主吹硫,將系統的硫磺攜帶至液硫池和加氫反應器,同時配以合適的風量使反應器床層及系統管線積存的FeS自燃,吹掃過程氣按正常流程,經尾氣系統加氫反應并胺液吸收后,凈化尾氣經焚燒爐焚燒達標排放。
參照類似規模硫磺回收裝置吹硫期間的氮氣量及實際吹硫效果,停工檢修前,保留原有氮氣線流程,同步實施“自硫磺回收裝置制硫單元管廊氮氣總管新接管線至各列制硫爐前蒸汽線”的技改措施。在熱氮吹硫過程中,所需氮氣量按傳統“燃料氣當量燃燒吹硫”產生的過程氣量折算,少量燃料氣當量燃燒用于維持系統吹硫溫度。
全廠停工期間加工低硫原油,同時四列硫磺回收裝置錯開停工,輔以“熱氮吹硫”流程,裝置停工吹硫過程中,煙氣中二氧化硫質量濃度平均在260mg/m3,低于排放新標準400mg/m3,避免了大量高濃度酸性氣長時間排放,保護了環境。
2 “密閉煮塔”
裝置停工處理過程中,先進行系統水洗,再用蒸汽吹掃貫通,減少蒸汽吹掃過程產生的油氣量。
如上圖所示,煮塔時,各系統放空全部關閉,在設備和管線底部接蒸汽,吹掃蒸汽經塔頂空冷器和水冷器冷卻后進入分液罐,分離出來的水排入污水系統,油進入污油回收系統,不凝氣排入低壓瓦斯管網。
各裝置吹掃結束前對排放氣體進行檢測,檢測項目包括烴、H2S等主要污染物含量,檢測結果經生產人員、技術人員及HSE人員三方共同確認后方能停止吹掃,對外排放泄壓。吹掃期間全廠設置200多處監測點,隨時監控廠區大氣狀況,保證吹掃過程不擾民。停工吹掃期間下風向廠界監測點分析結果見下表。
3 延遲焦化裝置放空系統增設接收全廠吹掃
污油線此次停工過程實施“放空系統增設接收全廠吹掃污油線”技改技措項目,即:延遲焦化裝置放空系統增設接收全廠吹掃污油線及退油線,使延遲焦化裝置放空塔系統滿足接收全廠吹掃重污油并冷卻條件,同時將各冷卻物料送至相應的罐區或下游裝置。
系統高溫重污油管線增加至延遲焦化裝置放空塔入口管線,停工期間各裝置吹掃污油自柴油以下組分進行切割,直接吹掃至放空塔內,經過放空系統冷卻,分別將塔頂冷凝的污水送至硫磺酸性水汽提裝置,燃料氣和其他不凝氣氣體送至低壓火炬系統,塔底冷卻的重污油送至低溫重污油罐,實現吹掃介質全密閉排放。
停工吹掃期間,延遲焦化裝置放空系統回收吹掃污油約1000t,接收吹掃蒸汽約2000t,燃料氣氣體約30dam3,成功避免了重污油吹掃至儲罐內冒罐及設備損壞等風險,將全廠異味氣體排放降至最低,實現了吹掃介質全密閉排放。
4 鈍化清洗
全廠煉油裝置高硫部位(涉及200多臺設備)全部進行鈍化清洗,鈍化清洗劑均為弱堿性螯合劑,確認沒有產生硫化氫風險;同時全廠塔頂增上了淋水線作為預防措施。
為確保鈍化清洗效果,又要降低成本費用,需反復確認清洗部位、清洗介質,實現化學清洗一裝置一方案,并盡量做到循環利用,發揮化學清洗的有效作用。另外,為防止FeS發生自燃,潛在FeS自燃裝置均編制防FeS自燃預案。
本次停工檢修過程中催化裂化、延遲焦化、加氫裂化和渣油加氫等裝置重油系統采用柴油清洗,常減壓裝置采用化學清洗方式。從停工后設備打開情況來看,分餾塔內構件清潔干凈,換熱器清潔易抽芯,同時設備沒有發生較大FeS自燃現象,表明設備清洗、鈍化效果良好。
5 胺液提濃
為解決停工檢修期間的胺液儲存問題,保證全廠停工檢修按計劃進行,停工前將各系統的胺液送至溶劑再生單元提高胺液濃度。
提濃的胺液送至貧胺液罐,沖洗水送至酸性水罐。為保證停工檢修期間胺液與沖洗液分類儲存,提前完成溶劑再生單元貧液罐(4×1000m3)清罐,用于儲存胺液;完成一列汽提單元原料水罐(5000m3)清罐,用于儲存沖洗水。
停工期間,根據原制定的退胺方案及沖洗方法,嚴格控制沖洗水量;按照停工統籌安排,同一胺液系統內不同脫硫裝置間的停工退胺及沖洗時間盡量同步或間隔應盡可能短,同時退胺及沖洗過程上下游裝置加強聯系溝通,按照操作步驟和時間要求嚴格執行。通過上述系列措施,最終順利完成全廠胺液系統的轉移儲存及正常停工。
免責聲明:本網站所轉載的文字、圖片與視頻資料版權歸原創作者所有,如果涉及侵權,請第一時間聯系本網刪除。
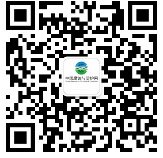
官方微信
《中國腐蝕與防護網電子期刊》征訂啟事
- 投稿聯系:編輯部
- 電話:010-62316606-806
- 郵箱:fsfhzy666@163.com
- 中國腐蝕與防護網官方QQ群:140808414