摘要:
利用定向電沉積技術在316L不銹鋼表面設計制備了一種超疏水微納鎳鍍層,通過對電沉積參數的優化,獲得最佳電沉積工藝參數:初次電沉積電流密度5 Adm-2,電沉積時間為480 s,結晶調節劑濃度為1.5 mol/L;二次電沉積條件為10 Adm-2,60 s。借助SEM、XRD、電化學測試技術、接觸角測試對涂層進行表征,結果表明制備的316L不銹鋼表面鎳鍍層陣列微納結構具有典型的花瓣狀分級結構和較好的超疏水性能,鎳鍍層陣列微納結構由具有 (110) 擇優取向晶面的針錐陣列結構組成,隨著二次電沉積電流密度的增大,鎳鍍層陣列微納結構的生長經歷從針錐向花瓣結構轉變。
關鍵詞: 定向電沉積 ; 超疏水 ; 鎳鍍層 ; 微納分級結構
在金屬材料表面制備超疏水涂層是一種有效的綠色防腐方法。超疏水表面是指水接觸角大于150°并且滾動角小于5°的表面。通常超疏水表面存在微米結構和納米結構相結合的二級結構,且粗糙的表面經低表面能物質修飾。這種具有超疏水結構的金屬表面在浸入腐蝕介質時,材料疏水性使得表面形成一層空氣層,借助空氣層可以有效防止腐蝕現象的發生。目前,國內外學者已經開發出在多種金屬表面制備超疏水涂層的方法,包括自組裝法、刻蝕法、溶膠-凝膠法、化學氣相沉積法、電化學沉積法、電化學陽極氧化法以及機械加工法等[1,2,3,4,5]。
目前,利用直接電沉積方法在316L不銹鋼基體表面制備超疏水涂層的報道較少。盡管有少數學者在不銹鋼、純銅和鎂合金表面進行了直接電沉積微納結構的嘗試,但是所制備的微納結構中較少能夠實現一維微米結構陣列垂直于基體定向規則排列,而且二維納米精細結構較少[6,7],導致超疏水性能差且不穩定。直接電沉積法在金屬材料表面制備微納結構是基于傳統電沉積理論所提出的一種新思路,通過調節電沉積條件,控制晶體生長方向,使之按一定規律排列,最終在金屬材料表面形成微納結構[8,9,10,11,12]。直接電沉積法制備微納結構具有無需模板、工藝簡單、成本低廉等諸多優點,引起許多學者的興趣,但是目前相關報道還較少。利用陰極電沉積方法構建微納結構,主要通過調節電解液組分和優化電沉積參數 (如電沉積電流密度和電沉積時間) 來實現。因此很有必要對直接電沉積方法在316L不銹鋼表面制備超疏水表面微納結構進行深層次的工藝和機理探索,獲得穩定可控的表面超疏水微納結構,并研究其疏水性質。
本文利用循環伏安測試、原子力顯微鏡 (AFM)、激光共聚焦顯微鏡和掃描電鏡 (SEM) 等表面分析手段研究并提出電沉積生長微納結構的機理,利用接觸角測試儀測試材料表面親水性并結合界面潤濕理論提出電沉積微納結構的超疏水性能實現機理。
1 實驗方法
1.1 實驗材料
實驗用材料316L不銹鋼的化學成分 (質量分數,%) 為:C≤0.030,Mn≤2.00,P≤0.035,S≤0.03,Si≤1.00,Cr 16.0~18.0,Ni 12.0~15.0,Mo 2.0~3.0,Fe余量。
1.2 電沉積工藝及配方
電沉積前處理以316L不銹鋼為基體材料。在電沉積前試樣依次采用800#,1000#和2000#水磨砂紙打磨表面,打磨完畢后分別用丙酮和乙醇超聲清洗20 min;接下來采用熱除油液 (30 g/L NaOH,7.5 g/L OP-10,40 g/L Na2CO3,20 g/L Na3PO4) 在80 ℃條件下除油20 min;然后采用10% (質量分數) 的鹽酸溶液浸泡活化2 min;最后用蒸餾水和乙醇清洗,吹干待用。經前處理后,將316L不銹鋼基體材料在60 ℃條件下浸沒于pH值為4.0的電沉積液 (NiCl2·6H2O 1 mol/L,H3BO3 0.5 mol/L,鹽酸乙二胺0.5~2.5 mol/L) 中,以316L不銹鋼為陰極,Pt片為陽極,采用恒壓直流電源進行電沉積。初次電沉積電流密度為1~11 A·dm-2,電沉積時間為480~1440 s。初次電沉積完畢后,以沉積樣品為陰極,進行二次電沉積,調節二次沉積電流密度為10 A·dm-2,電沉積時間為60~120 s。施鍍結束后,將樣品水洗后吹干,在恒溫恒濕條件下 (溫度25 ℃,濕度40%) 儲存14 d后取出待用。
1.3 表面形貌觀察與相組成分析
樣品的微觀表面形貌采用ZEISS SUPRA55型SEM進行觀察,樣品表面成分采用SEM自帶的Oxford X-Max20能譜儀 (EDS) 進行分析。樣品表面尖錐結構和尺寸采用Bruker MultiMode8型AFM進行觀察和分析。
樣品的物相組成采用Bruker D8 Advance型X射線衍射儀 (XRD) 進行分析。
1.4 接觸角測試
樣品表面靜態接觸角測量采用DSA100接觸角測量儀,測量水滴 (8 μL) 在試樣表面的接觸角,在試樣的5個不同位置測試取平均值,利用儀器附帶軟件計算靜態接觸角。
2 結果與討論
2.1 電沉積電流密度范圍的優化
316L不銹鋼在含有結晶調節劑的電解液中的循環伏安曲線如圖1所示。可以看出,陰極電沉積分為兩個過程,分別是過程I和過程II。隨著陰極極化過程的進行,陰極極化電流密度急劇增加,這主要是由于電解液中Ni2+獲得電子后,還原生成吸附Ni+;吸附Ni+繼續還原,在316L不銹鋼表面沉積生成鎳單質,這屬于電沉積過程I的第一部分。隨著陰極極化過程的繼續進行,結晶調節劑鹽酸乙二胺參與到電化學反應過程中,利用結晶調節劑在316L不銹鋼基體的吸附效果,結晶調節劑鹽酸乙二胺與吸附Ni+生成吸附型的鹽酸乙二胺鎳離子配合物,該配合物繼續在陰極極化過程中在316L不銹鋼表面吸附點局部放電產生單質鎳的沉積層,在循環伏安曲線上表現為局部的電流平階區域,這屬于電沉積過程I的第二部分。陰極極化過程繼續進行,達到了電解液中H+的氧化還原電位,H2大量析出,表現為陰極極化電流密度再次急劇增加,但是這對于電沉積鍍層是非常有害的,H2產生的鼓泡會破壞鍍層自身的結構和結合性能[8]。達到回掃電位后,從循環伏安曲線可以看出,陽極氧化曲線逐漸趨于平臺期,說明陰極還原生成的單質鎳與316L基體冶金結合良好,無明顯陽極溶解狀況。上述反應的機理如方程 (1)~(6) 所示:
選擇陰極電沉積電流密度范圍為1~11 A·dm-2,可獲得較穩定的電沉積鎳涂層。通過結晶調節劑的作用,可以有效控制鎳離子在局部放電,生成一級微納結構,同時避免H2析出產生鼓泡破壞微納結構[8]。
圖1 316L不銹鋼在含有結晶調節劑的電解液中的循環伏安曲線
2.2 初次電沉積電流密度的優化
保證結晶調節劑的濃度為1.5 mol/L,總庫侖電量為48 C,也即電沉積電流密度與電沉積時間的乘積保持恒定條件下,316L不銹鋼表面不同初次電沉積電流密度條件下E-t曲線如圖2所示。可以看出,隨著陰極沉積電流密度的增加,陰極極化電位逐漸變負,這符合Bulter-Volmer方程[13];隨著陰極極化電流密度的增加,沉積所需的過電位逐漸增加,因此陰極極化電位逐漸變負。從E-t曲線形狀可以看出,所有的曲線都經歷了電位先正移后保持平穩的過程,這是由于施加陰極沉積電流的短時間內大量的Ni離子參加反應,沉積反應后局部Ni離子濃度低,擴散困難,導致電位迅速正移后保持平階。結合循環伏安曲線,陰極極化電位低于-0.8 V (vs SCE) 易析氫破壞鍍層結構,因此選擇5 A·dm-2。
圖2 316L不銹鋼表面不同初次電沉積電流密度條件下E-t曲線
316L不銹鋼表面不同初次電沉積電流密度條件下所制備鍍層的SEM像如圖3所示??梢钥闯?,樣品表面呈現明顯的微米級尖錐狀結構分布,且隨著陰極電沉積電流密度的增加,尖錐高度大小不一,在陰極電沉積電流密度達到5 A·dm-2時,尖錐在表面均勻分布,高度趨于一致;當陰極電沉積電流密度達到10 A·dm-2時,納米尺寸的尖錐開始橫向生長,無法保證初次沉積所獲得的單一尖錐的形態結構。
圖3 316L不銹鋼表面不同初次電沉積電流密度條件下所制備鍍層的SEM像
316L不銹鋼表面不同初次電沉積電流密度條件下接觸角變化如圖4所示??梢钥闯觯S著陰極電沉積電流密度的增加,接觸角逐漸增加,當陰極電沉積電流密度增加到2和5 A·dm-2時,接觸角逐漸趨于平階;陰極電沉積電流密度繼續增加,接觸角急劇增加。這與微納結構有很大關系,尖錐結構發展出納米級晶須促使表面的疏水性能獲得較大提升,但是較高的陰極電沉積電流密度可能會在局部獲得微納米二級結構,隨著H2的逐漸析出產生鼓泡而破壞微納米二級結構的完整性,宏觀形貌圖的結果印證了這一說法。
圖4 316L不銹鋼表面在不同初次電沉積電流條件下所制備鍍層的接觸角
綜上所述,低電流密度不利于基體表面活性點的增加,不利于形核生成局部凸起尖錐,較高的電流密度又容易抑制尖錐的定向生長,綜上分析選擇適宜的電流密度為5 A·dm-2。
2.3 初次電沉積時間的優化
在結晶調節劑濃度為1.5 mol/L,陰極沉積電流密度為5 A·dm-2的條件下,316L不銹鋼表面不同初次電沉積電流條件下E-t曲線如圖5所示??梢钥闯觯陉帢O沉積電流密度為5 A·dm-2的條件下隨著沉積時間的延長,極化電位在-0.73~0.75 V (vs SCE) 區間范圍內,并保持穩定。僅從E-t曲線圖分析,陰極沉積時間對沉積過程的影響不大。
圖5 316L不銹鋼表面不同初次電沉積時間條件下E-t曲線
316L不銹鋼表面不同初次電沉積時間條件下所制備鍍層的接觸角如圖6所示??梢钥闯?,當陰極沉積時間為480 s時,水接觸角約為140°;當陰極沉積時間達到1440 s時,接觸角迅速降低到約100°。這說明增加陰極沉積時間,破壞了鎳微米尖錐的分布,導致大量缺陷的出現,對疏水性能產生不利影響。
圖6 316L不銹鋼表面不同初次電沉積時間條件下所制備鍍層的接觸角
隨著電沉積時間的增加,粗糙度呈現逐漸增加的趨勢,接觸角卻呈現相反的變化。5 A·dm-2條件下960和1440 s時長的沉積,宏觀表面出現了大量的麻點,可能由于電沉積液腐蝕導致缺陷出現,破壞了表面規則的尖錐陣列結構,造成粗糙度的增加,接觸角減小,疏水性能降低。因此,選擇480 s作為優化后的沉積時間。
2.4 初次電沉積結晶調節劑濃度的優化
當陰極電沉積電流密度為5 A·dm-2,總庫侖電量為48 C,改變結晶調節劑濃度,316L不銹鋼表面不同結晶調節劑條件下E-t曲線如圖7所示。可以看出,不同濃度的結晶調節劑的E-t曲線均呈現先急劇增加后緩慢增加,接下來保持平穩的變化趨勢。這可能是結晶調節劑在316L不銹鋼表面吸附后,迅速吸附在微納結構表面上,導致微納結構表面的結晶調節劑擴散困難,從而造成電位曲線呈現上述變化趨勢。不同濃度結晶調節劑條件下陰極極化電位依然主要分布在-0.74~0.77 V (vs SCE) 區域范圍內。僅從E-t曲線分析,結晶調節劑對電化學沉積過程影響不大。
圖7 316L不銹鋼表面不同濃度結晶調節劑條件下E-t曲線
316L不銹鋼表面不同結晶調節劑濃度條件下所制備鍍層的接觸角如圖8所示??梢钥闯觯Y晶調節劑濃度對電沉積鎳微納結構表面的潤濕性能有明顯的影響,隨著結晶調節劑濃度的增加,接觸角先增加后減少,在結晶調節劑濃度為1.5 mol/L時,接觸角最大,約為150°。
添加結晶調節劑的目的是促進表面沉積離子的定向放電、定向生長。增加結晶調節劑濃度,可一定程度上促進微納米尖錐的縱向生長,表現為粗糙度的增加和接觸角的增大,但是結晶調節劑濃度不宜過高,否則由于在微納米尖錐的飽和吸附競爭造成尖錐生長的混亂,從而破壞規則的微納米尖錐陣列結構,造成粗糙度的下降和接觸角的降低。因此,選擇1.5 mol/L作為適宜的結晶調節劑濃度。
圖8 316L不銹鋼表面不同結晶調節劑濃度條件下所制備鍍層的接觸角變化
2.5 二次電沉積時間的優化
選擇二次電沉積電流密度為10 A·dm-2,結晶調節劑濃度為1.5 mol/L,改變二次電沉積時間,316L不銹鋼表面不同二次沉積時間條件下E-t曲線如圖9所示??梢钥闯?,電位表現出兩次先增長后降低的變化趨勢,隨著恒流沉積時間的延長,陰極極化電位趨于穩定,不同二次電沉積時間陰極極化電位在-0.845~-0.835 V (vs SCE) 范圍內。經過二次電沉積的過程,微納米結構表面中微米級鎳尖錐轉變為帶有納米晶須的微米級鎳尖錐,實現了微納二級結構。
316L不銹鋼表面不同二次沉積時間條件下所制備鍍層的接觸角如圖10所示。可以看出,二次電沉積時間為60 s的條件下接觸角最高,大于150°。
二次大電流沉積是制備微納米分級結構的關鍵。通過大電流二次沉積使得沉積原子在原有微納米尖錐上繼續生長,并大量形核,形成微米尖錐和納米微凸體的分級結構,表現為花瓣狀結構[14]。隨著10 A·dm-2大電流條件下沉積時間的延長,且沉積電位處于析氫區間,宏觀表面出現了部分麻點缺陷,破壞了表面規則的尖錐陣列結構,造成粗糙度的增加,卻降低了接觸角。因此,選擇60 s為最佳二次沉積時間。
2.6 316L不銹鋼表面不同參數工藝條件下所制備鍍層的擇優生長方向分析
316L不銹鋼表面不同工藝參數條件下所制備鍍層的擇優生長方向變化如圖11所示。可以看出,不同工藝參數條件下316L不銹鋼表面微納結構主要由Ni和Fe組成,單質鎳作為fcc晶體結構類型,從圖中可以看出,不同電沉積條件下擇優取向晶面均為 (110) 晶面。隨著工藝參數的變化,擇優取向晶面 (110) 可能為微納米尖錐生長晶面,微結構頂端可能由 (100) 和 (111) 晶面搭臺形成擇優取向 (110) 晶面作為生長晶面。這可能是由于結晶調節劑在低表面能晶面的特性吸附導致了這種晶面生長方式。
圖9 316L不銹鋼表面不同二次沉積時間條件下E-t曲線
圖10 316L不銹鋼表面不同二次沉積時間條件下所制備鍍層的接觸角
圖11 316L不銹鋼表面不同工藝參數條件下所制備鍍層的擇優生長方向變化
2.7 最佳工藝條件下316L不銹鋼所制備鍍層的形貌及元素分析
利用AFM進一步分析微納米尖錐的結構和尺寸,二次電沉積優化工藝條件下316L不銹鋼表面所制備鎳鍍層微納結構表面AFM像見圖12??梢钥闯?,微納結構分布均勻,尖錐高度約為0.4~0.6 μm,尖錐底部直徑約為0.5 μm,與SEM觀察結果一致。
圖12 二次電沉積優化工藝條件下316L不銹鋼表面所制備鍍層的表面形貌
進一步通過EDS分析二次電沉積優化條件下316L不銹鋼表面所制備鍍層的元素成分,結果見圖13。鍍層表面主要由O,Ni和Fe構成。推測Fe主要來源于基體;Ni是表面物相組成主要元素,可能是Ni鍍層。因此,表面Ni鍍層和鎳基微納結構可能是超疏水性能的原因。
圖13 二次電沉積優化工藝條件下316L不銹鋼表面所制備鍍層的元素成分分析
2.8 316L不銹鋼表面所制備鎳鍍層的電沉積生長機理和超疏水性機理
微納結構表面電沉積生長機理如圖14所示。綜合不同工藝參數優化的結果和最佳工藝條件下一次電沉積和二次電沉積316L不銹鋼表面鎳鍍層微納結構分析結果,并結合Watanabe提出的納米電鍍的理論,提出微納結構電沉積的生長機理[5]。在陰極極化條件下,在316L不銹鋼表面的鎳離子充足供給區域,產生局部放電效應,在局部有單質鎳凸點生成;隨著極化電流密度的增加,極化時間的延長,單質鎳凸點處繼續放電,形成多個晶粒的生長和聚焦。而在得不到鎳離子充足供應的區域,即凹點,這些凹點分布在逐漸長大的凸點形成的尖錐結構之間,增加了微納結構表面的粗糙度。此外,結晶調節劑在電沉積過程中會吸附在某個特定晶面,抑制該晶面的外延生長,電沉積鎳單質主要是fcc晶體結構,鹽酸乙二胺主要吸附在fcc的 (100) 晶面,這就導致 (100) 晶面的平行擴展受到強烈阻礙,促使在凸點處聚焦的晶粒群向縱向生長[14]。而 (111) 晶面為最低表面能晶面,并與基體襯底平行,最后結果是 (110) 晶面迅速生長,其表面主要由 (111) 和 (100) 兩種晶面搭合,進而形成LCSM和SEM觀察到的尖錐狀結構體。此外,二次大電流電沉積陰極極化條件下,由于已經形成的微米錐形結構對結晶調節劑的擴散阻礙作用,使得結晶調節劑在縱向晶面的吸附狀況不同,一定程度無法抑制 (100) 和 (111) 晶面的生長,此時微米錐形結構在縱向生長速度減慢,而在 (100) 和 (111) 晶面的生長獲得發展,最終形成了花瓣狀錐形結構。
圖14 316L不銹鋼表面所制備鎳鍍層微納結構表面電沉積生長機理
316L不銹鋼表面所制備鎳鍍層微納結構表面超疏水形成模型如圖15所示。從自然界獲得啟發,結合天然超疏水表面結構包括荷葉、蟬翼和水蠅腿,國內外學者提出了多種超疏水理論模型,其中Cassie模型和Lotus模型適合解釋一次和二次陰極電沉積制備具有微納表面結構的疏水和超疏水性能表面[15]。Cassie模型理論提出,對于存在空氣的粗糙低表面能物質覆蓋的表面,水滴在這種表面只有極少部分面積是和固體接觸,大部分面積是和空氣接觸,Cassie方程可以很好地解釋Cassie模型和Lotus模型:
cos θ c = Φ s ( cos θ e + 1 ) - 1(7)
式中,θc和θe分別代表水滴在粗糙和光滑表面的接觸角,Φs代表水滴與固體表面的接觸面積,1-Φs則為水滴和空氣的接觸面積。
對于316L不銹鋼基體和一次電沉積條件下316L不銹鋼表面鎳鍍層微納結構,接觸角分別為104.65°和140.79°,也即θc為140.79°,θe為104.65°。通過計算獲得Φs為0.3014,即液滴與316L不銹鋼基體接觸面積占30.14%,而截留空氣比率達69.86%。對于316L不銹鋼和二次電沉積條件下316L不銹鋼表面鎳鍍層微納結構,接觸角分別為104.65°和150.74°,也即θc為150.74°,θe為104.65°。通過計算獲得Φs為0.1714,二次電沉積后液滴與316L不銹鋼基體接觸面積明顯降低至17.14%,而截留空氣比率明顯提高至82.86%。這是由于一次電沉積形成微米錐形結構和二次電沉積形成的微納米花瓣狀結構截留了大量空氣,空氣是最理想的疏水介質,接觸角高達180°,這些截留的空氣對腐蝕介質的擠出效應明顯,腐蝕介質很難深入到表面粗糙結構中,通過一次電沉積和二次電沉積在316L不銹鋼表面構建微納二級結構最終實現了超疏水性能。
圖15 316L不銹鋼表面所制備鎳鍍層微納結構表面超疏水形成模型圖
3 結論
(1) 利用電沉積技術可在316L不銹鋼表面制備穩定的具有微納米結構陣列的鎳鍍層。最優化電沉積參數為:初次電沉積電流密度5 A·dm-2,電沉積時間為480 s,結晶調節劑濃度為1.5 mol/L,二次電沉積條件為10 A·dm-2,60 s。
(2) 特定電沉積條件下制備的鎳鍍層陣列微納米結構具有典型的花瓣狀分級結構和較好的超疏水性能,陣列微納米結構具有 (110) 擇優取向晶面的針錐陣列結構,陣列結構的生長經歷從針錐向花瓣結構的轉變,接觸角從140.79°增加到150.74°,花瓣狀分級微納結構表現出較好的超疏水性能。
免責聲明:本網站所轉載的文字、圖片與視頻資料版權歸原創作者所有,如果涉及侵權,請第一時間聯系本網刪除。
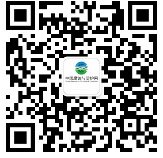
官方微信
《中國腐蝕與防護網電子期刊》征訂啟事
- 投稿聯系:編輯部
- 電話:010-62316606-806
- 郵箱:fsfhzy666@163.com
- 中國腐蝕與防護網官方QQ群:140808414