摘要:
采用微弧氧化技術在AZ91鎂合金表面制備MgO陶瓷膜層,然后在該膜層通過化學鍍銅技術制備金屬銅層。利用SEM,XRD,EDS,電化學實驗及四探針測試等手段研究了復合膜層的顯微結構、相組成、耐蝕性和導電性。結果表明:微弧氧化處理獲得以MgO為主相的陶瓷層可有效提高鎂合金的耐蝕性,平均厚度為2.5 μm的化學鍍銅層連續均勻地覆蓋在微弧氧化陶瓷層表面,滲入并填充微弧氧化陶瓷層內部呈網狀分布的孔隙,形成交錯咬合狀態;復合膜層表面的導電性良好,與基體鎂合金相比,復合膜層的腐蝕電位提高了0.2 V,腐蝕電流密度下降了一個數量級。但由于化學鍍銅層與基體鎂合金之間產生的電偶腐蝕,導致復合膜層的耐蝕性較陶瓷層有所下降。
關鍵詞: 鎂合金 ; 微弧氧化 ; 化學鍍銅 ; 耐蝕性 ; 導電性
鎂合金由于具有重量輕、比強度高、電磁屏蔽性能優異等特點,在交通運輸、3C產品、國防軍工及生物醫用等領域應用前景廣闊[1,2,3]。但在所有的結構金屬中,Mg具有極低的電極電位 (標準電極電位為-2.37 V),活潑的化學和電化學特性使其極易產生腐蝕,耐蝕性差成為制約其發揮性能優勢的主要因素[4,5,6]。鎂合金微弧氧化處理能夠通過微區瞬間高溫燒結,在基體合金表面原位生成氧化物陶瓷膜層,可有效提高鎂合金表面的耐蝕、耐磨及耐高溫性[7,8,9]。但微弧氧化陶瓷膜層具有多孔特性,是微弧氧化過程中等離子體放電本質所決定的,膜層中孔隙越多,致密性越低,膜層的耐蝕性就越差[10]。因此,單一的微弧氧化表面改性技術不能從根本上解決鎂合金腐蝕性問題。目前,基于微弧氧化處理的鎂合金表面復合膜層的制備及研究掀起一股熱潮[11,12,13,14,15],通過復合表面改性,賦予膜層良好的表面耐蝕性能,但多數研究忽視甚至犧牲了鎂合金表面膜層的導電性,極大地限制了鎂合金在某些領域的應用。
化學鍍銅也叫沉銅或孔化 (PTH),是一種自身催化性氧化還原反應,主要是用于非金屬表面形成導電Cu層[16]。為提高鎂合金微弧氧化陶瓷膜層表面的導電能力,文中采用化學鍍銅技術在AZ91鎂合金陶瓷表面制備金屬銅層,既可發揮微弧氧化陶瓷層較好的耐蝕性能,又可利用金屬銅優異的導熱、導電性能,從而擴展鎂合金的應用領域。
1 實驗方法
基體材料為商用AZ91鎂合金,其化學成分 (質量分數,%) 為:A1 8.95~9.75,Zn 0.35~1.0,Mn 0.15~0.5,Si 0.022,Cu 0.021,Fe 0.003,Mg余量。采用線切割加工成30 mm×20 mm×5 mm的試樣,分別用240#,600#和1000#的砂紙進行打磨處理,再用丙酮和去離子水清洗,烘干備用。
用MAO120HD-II型微機控制全自動微弧氧化設備對打磨處理的AZ91鎂合金試樣進行微弧氧化處理。微弧氧化所用電解液為Na2SiO3體系的水溶液,添加少量的NaOH與KF;微弧氧化電源采用恒流雙脈沖模式,電流密度為2 A/dm2,正向電壓為450 V,反向電壓為90 V,氧化時間為5 min。微弧氧化處理后的試樣用丙酮、酒精和去離子水依次進行清洗并烘干,然后放入由100 mL/L HF和5 mL/L H3PO4所配的溶液中浸泡1 min進行敏化,再用去離子水沖洗干凈并吹干后放入0.06 mol/L AgNO3溶液中浸泡30 s進行活化處理,最后進行化學鍍銅。化學鍍銅過程在恒溫加熱磁力攪拌器水浴中進行,試樣懸掛在化學鍍銅鍍液中,轉速為10 r/min,保持溫度在30 ℃,施鍍時間30 min。化學鍍銅液組成為:主鹽CuSO4·5H2O,10 g/L;還原劑HCHO,14 mL/L;絡合劑EDTA·2Na,30 g/L 和C4O6H4KNa,40 g/L;穩定劑K4Fe(CN)6·3H2O,80 mg/L。用定量NaOH將鍍液的pH值調節在12~13之間。
借助VEGA3 TESCAN掃描電子顯微鏡 (SEM)觀察膜層的微觀形貌,并采用其上附帶的能譜儀 (EDS) 分析膜層的化學成分。膜層的物相分析在XRD-7000S型X射線衍射儀 (XRD) 上進行,掃描角度為20°~80°。動電位極化曲線測試選擇PARSTAT4000型電化學工作站,測試中所用的腐蝕液為3.5% (質量分數) NaCl溶液;采用三電極測試體系,其中待測試樣為工作電極,測試面積為1 cm2,Pt電極為輔助電極,Ag-AgCl電極為參比電極。將試樣置于三電極體系中,待開路電位穩定后進行動電位極化曲線測試,電位掃描范圍-2~2 V,掃描速率1 mV/s。用RTS-9型雙電測四探針測試儀測量復合膜層表面的方塊電阻,測試電流為45.32 mA,探針平均間距為1 mm,在試樣表面選取5個測量點,取平均值作為膜層的最終方阻。
2 結果與討論
2.1 微弧氧化陶瓷層及化學鍍銅層的相組成
采用X射線薄膜衍射法對微弧氧化陶瓷膜層及化學鍍銅層進行物相分析,其目的可有效避免襯底基體相衍射峰的干擾,從而僅獲得薄膜的表面衍射信息即膜層的衍射峰。圖1為AZ91鎂合金微弧氧化陶瓷膜層及化學鍍銅層的XRD譜。可以看出,陶瓷層的XRD譜中只存在MgO相的衍射峰,而化學鍍銅層的XRD譜中只存在Cu的衍射峰,說明微弧氧化陶瓷膜層的物相由高溫燒結相MgO組成,化學鍍銅層的物相由Cu相組成。
圖1 微弧氧化陶瓷層及化學鍍銅層的XRD譜
2.2 膜層的微觀形貌及成分
圖2為鎂合金微弧氧化陶瓷膜層及化學鍍銅層的表面形貌。由圖2a和b陶瓷層表面形貌可以看出,微弧氧化陶瓷膜中存在大量的微米級和納米級的微孔,微孔最大直徑不超過3 μm,這些孔洞互不連通,無規律地分布在陶瓷表面,形成微孔鑲嵌的網絡狀結構。微弧氧化膜層的這種微納多孔粗糙結構與其形成機制有關[17,18],其實質是殘留的微弧等離子放電通道。圖2c和d是化學鍍銅層的表面形貌,可以看到,化學鍍銅過程中沉積在陶瓷層表面的銅層以顆粒狀排列,鍍層較為致密,幾乎沒有孔洞。微弧氧化陶瓷層表面的多孔結構使其具有較大的真實表面積,經過敏化活化處理的鎂合金微弧氧化試樣浸入化學鍍銅溶液后,多孔表面吸附鍍液中的銅絡合離子和還原劑,Cu2+在微弧氧化陶瓷層活性表面及微孔內被還原成Cu,以顆粒狀進行三維方向生長,但各個方向生長速率不同,垂直方向生長速率要高于側向的,導致Cu顆粒向外生長,從而形成銅鍍層。化學鍍銅層完全覆蓋在微弧氧化陶瓷層表面,起到明顯的封孔效應。
圖2 微弧氧化陶瓷膜層及鍍銅層的表面形貌
圖3是微弧氧化與化學鍍銅復合處理后所得復合膜層的截面形貌。可以看出,整個截面由比較明亮的化學鍍層、暗灰色的微弧氧化陶瓷層和基體3部分組成,3層之間分界比較明顯。其中,化學鍍層的平均厚度約為2.5 μm,微弧氧化陶瓷層的平均厚度約為5 μm。在化學鍍銅過程中,正是由于微弧陶瓷層表面的多孔結構,使得化學鍍液容易滲入到微弧氧化膜孔隙內部,導致鍍層部分生長于微弧氧化膜孔隙內,與微弧氧化孔隙形成“鏈鎖”式結合。化學鍍層與多孔的微弧氧化膜緊密地結合在一起,自表面到結合層基本無缺陷。
圖3 復合膜層的截面形貌
對圖3復合膜層截面形貌中化學鍍層 (A點) 和微弧氧化陶瓷層 (B點) 分別進行EDS分析,結果如圖4所示。由圖4a可知,化學鍍層僅含有Cu,沒有出現O,說明化學鍍銅過程中所得鍍層中不存在CuO及Cu2O,獲得純Cu鍍層。由圖4b可以看出,微弧氧化陶瓷層含有Mg,O,Al,Si及Cu,其中Mg和O來自微弧氧化陶瓷層的物相MgO,Al來自基體鎂合金,少量Si為電解液中溶質離子在微弧等離子體放電過程中參與反應并進入陶瓷層,但XRD譜中未見有關Si和Al的物相,其主要原因是Si和Al的含量過低,XRD未檢測出;Cu是化學鍍銅過程中經氧化還原反應所形成的Cu通過微弧氧化陶瓷層表面的疏松層擴散到微弧氧化陶瓷層內部的。
圖4 圖3中復合膜層截面不同位置的EDS結果
2.3 膜層的電化學特性
圖5為AZ91鎂合金基體、微弧氧化陶瓷層以及復合膜層在3.5% (質量分數) NaCl溶液中的動電位極化曲線。對圖中3條曲線使用Corrview數據分析軟件進行擬合,得出了各試樣的腐蝕電流密度Icorr和腐蝕電位Ecorr,而極化電阻Rp可采用Stein-Geary方程[19,20]計算得到,具體數據見表1。
圖5 鎂合金基體、MAO膜層及復合膜層的極化曲線
表1 鎂合金基體、MAO膜層及復合膜層的電化學參數
Ecorr是熱力學參數,主要由材料本身的性質所決定,Ecorr越正,腐蝕傾向越小;而Icorr是動力學參數,Icorr越低,腐蝕速率越小[21]。由表1中的數據可知,基體AZ91鎂合金耐蝕性很差。經微弧氧化處理后Icorr降低了約3個數量級,而Ecorr提高了約150 mV,且在陽極區出現了大約70 mV的鈍化區,Rp提高了3個數量級。這些數據說明微弧氧化處理能較為顯著地提高鎂合金的耐蝕性。相對于基體鎂合金及微弧氧化陶瓷層而言,復合膜層的Ecorr最正,說明復合膜層的腐蝕傾向進一步降低。但由于表面的化學鍍銅層具有較正的電極電位,而基體鎂合金的電極電位較負,兩者之間存在約5 μm的多微孔陶瓷層,導致出現比較明顯的電偶腐蝕,故使得復合膜層的Icorr較陶瓷層有所下降,腐蝕速率增大。但與基體鎂合金相比,復合膜層的耐蝕性仍有所提高。復合膜層中的化學鍍銅層能夠填充微弧氧化陶瓷層表面微孔,較為致密的化學鍍銅層作為一個有效的物理阻擋層,能夠阻止腐蝕介質的侵入,化學鍍銅層和微弧氧化陶瓷層兩者綜合作用,保護鎂合金基體。
2.4 復合膜層的導電性
采用RTS-9型雙電測四探針測試儀測量化學鍍銅層的方塊電阻,在鍍銅層表面隨機測試5個位置的方阻值,結果分別為77,74,75,76,和70 mΩ/sq,其平均值74.4 mΩ/sq即為化學鍍銅層的方塊電阻。經測量化學鍍銅層的平均厚度為2.5 μm,根據電阻率與方阻之間的關系計算得到化學鍍銅層的電阻率為1.86×10-2 mΩ·cm。室溫下塊體金屬Cu的電阻率為1.7×10-3 mΩ·cm[22],而實測化學鍍銅層的電阻率比金屬Cu高一個數量級,即化學鍍銅層的導電性較塊體金屬Cu差。這主要是因為化學鍍銅層相對于金屬Cu并不是很致密,而且膜厚相對較薄,導電通道并不完整。這種特殊的薄層結構使其導電性區別于塊體金屬Cu的導電性,但正是由于化學鍍銅層的存在顯著改善了微弧氧化陶瓷層表面的導電性。
3 結論
(1) AZ91鎂合金經微弧氧化處理后,表面獲得由MgO組成的具有微納粗糙多孔結構的陶瓷層;微弧氧化陶瓷層經化學鍍銅處理后制備得到復合膜,化學鍍銅層連續均勻地覆蓋在微弧氧化陶瓷層表面,滲入并填充微弧氧化陶瓷層內部呈網狀分布的孔隙,形成交錯咬合狀態。
(2) 相對于基體鎂合金,微弧氧化陶瓷層的腐蝕電位提高了150 mV,腐蝕電流密度下降3個數量級,耐蝕性顯著提高。經微弧氧化及化學鍍銅處理所得復合膜層的腐蝕電位最正,膜層腐蝕傾向進一步降低。但由于化學鍍銅層與基體鎂合金之間產生的電偶腐蝕,導致復合膜層的耐蝕性較陶瓷層有所下降。
(3) 化學鍍銅層的電阻率為1.86×10-2 mΩ·cm,顯著提高了微弧氧化陶瓷層表面的導電性能。
免責聲明:本網站所轉載的文字、圖片與視頻資料版權歸原創作者所有,如果涉及侵權,請第一時間聯系本網刪除。
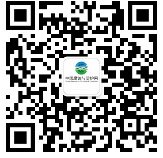
官方微信
《中國腐蝕與防護網電子期刊》征訂啟事
- 投稿聯系:編輯部
- 電話:010-62316606-806
- 郵箱:fsfhzy666@163.com
- 中國腐蝕與防護網官方QQ群:140808414