摘要
針對所提出的恒電位脈沖電沉積銅錫技術(shù),研究工藝條件對鍍層成分、晶粒尺寸及耐蝕性能的影響規(guī)律,摸索恒電位脈沖電沉積高錫青銅的最優(yōu)工藝。利用SEM觀察分析恒電位脈沖與恒電流脈沖電沉積銅錫鍍層的形貌及晶粒尺寸,結(jié)合EDS分析電沉積方式對鍍層成分分布的影響規(guī)律,使用電化學(xué)工作站表征鍍層的耐蝕性。結(jié)果表明,使用占空比33%、沉積電位3 V的恒電位脈沖電沉積工藝,降低了鍍層溶解幾率而維持絡(luò)合離子遷移、沉積驅(qū)動力,因而對不同尺寸零件均可穩(wěn)定獲得高錫青銅鍍層。相同初始條件下,恒電流脈沖鍍層平均厚度約6 μm;而恒電位脈沖具有更大的沉積速率,膜層厚度在10 μm以上,且鍍層成分比恒電流脈沖鍍層更均勻、孔隙率低、晶粒團(tuán)簇少、耐蝕性能優(yōu)良,在截面積為78.5 mm2的試樣上鍍層阻抗較恒電流脈沖提高了兩倍。恒電位脈沖還可獲得納米Cu-Sn鍍層,晶粒尺寸小于100 nm。相對恒電流脈沖,恒電位脈沖電沉積提高了銅錫鍍層質(zhì)量及耐蝕性,且有利于復(fù)雜零件的成分控制及自動化生產(chǎn)。
關(guān)鍵詞: 高錫青銅; 恒電位脈沖; 恒電流脈沖; 電沉積; 耐蝕性
銅錫合金鍍層平整光亮,耐蝕性能和耐磨性能優(yōu)異,在液壓支柱、千斤頂?shù)戎谐W鳛榉雷o(hù)性鍍層[1-4]。銅錫合金中按銅錫組分差異一般分為低錫青銅、中錫青銅和高錫青銅。低錫青銅為含錫15%(質(zhì)量分?jǐn)?shù)) 以下的銅錫合金,其在空氣中易氧化變色,而中錫青銅含錫15%~30%,二者均不宜做表面鍍層。含錫40%以上的銅錫合金為高錫青銅,其在空氣中穩(wěn)定性好、硬度高、耐蝕性能優(yōu)異,在五金件中常作防護(hù)裝飾層[5,6]。傳統(tǒng)電沉積銅錫工藝主要采用恒流電鍍[7],其制備的鍍層晶粒大、滲氫嚴(yán)重,在使用中易出現(xiàn)鼓泡現(xiàn)象。脈沖電沉積可降低陰極濃差極化[8,9],有效減少滲氫,改善銅錫鍍層性能。目前,已有恒電流脈沖電沉積銅錫的相關(guān)研究[10-12]。吳珂[10]在焦磷酸鹽-錫酸鹽體系通過恒電流脈沖方式獲得了銅錫合金鍍層,研究該鍍層腐蝕形貌顯示其腐蝕時主要為小孔腐蝕。李福永等[11]對比了直流電鍍與恒流脈沖電鍍銅錫合金的滲氫行為,研究顯示恒電流脈沖電沉積銅錫鍍層滲氫量較直流電沉積減小,占空比和脈沖頻率對鍍層滲氫影響顯著。恒電流脈沖電沉積銅錫由于鍍層性能較佳,無須使用參比電極及鍍層厚度可控而得到應(yīng)用。該工藝的不足在于鍍層成分不易控制,且對于不同尺寸的零件需要重新計算和調(diào)整電流密度,操作復(fù)雜,不利于自動化控制[13]。而恒電位脈沖電沉積由于需要增加參比電極且可能因鍍層-溶液界面電阻與施加電位接近而發(fā)生重新溶解,其研究及應(yīng)用一直受限。目前,恒電位脈沖電沉積高錫青銅工藝的研究未見報道。恒電位脈沖電沉積可適應(yīng)零件尺寸變化自動調(diào)整電流,有學(xué)者通過該方式制備了晶粒尺寸100 nm以下的納米Ni-Fe-Cr、納米Co-Ni等,表明恒電位脈沖電沉積還可細(xì)化晶粒[14-17]。因此,本文嘗試將恒電位脈沖電沉積法運用于高錫青銅耐蝕鍍層制備,探究其與恒電流脈沖電沉積銅錫工藝在鍍層成分、晶粒尺寸及其耐蝕性能的異同,為提高企業(yè)鍍層質(zhì)量及自動化程度提供理論與實際指導(dǎo)。
1 實驗方法
1.1 基體預(yù)處理
選用27SiMn鋼為基材,加工成橫截面積分別為78.5和270 mm2的試樣 (分別標(biāo)記為試樣A和試樣B),用于不同尺寸零件脈沖電沉積。基體試樣經(jīng)砂紙打磨后,置于60 g/L NaOH+30 g/L Na2CO3+46.5 g/L Na3PO4·12H2O+11.5 g/L Na2SiO3·9H2O的堿液中,于70 ℃除油10 min。再用10% (質(zhì)量分?jǐn)?shù)) 氫氟酸+ 10%硫酸溶液進(jìn)行活化,時間為30 s。每步工序后均使用蒸餾水清洗、吹干。
1.2 恒電位脈沖和恒電流脈沖方式電沉積銅錫鍍層
以無氰焦磷酸鹽為基礎(chǔ)鍍液,鍍液配比為:CuSO4·5H2O 15 g/L,SnCl2·2H2O 8.05 g/L,K4P2O7·3H2O 250 g/L,K2HPO4·3H2O 60 g/L,C6H5Na3O7·2H2O 20 g/L,H3PO4 2 mL/L,C6H15O3N 2 mL/L。使用NHDP-12V6A智能脈沖電源進(jìn)行銅錫合金鍍層制備。恒電位脈沖沉積工藝參數(shù)為:輸出電壓3 V,占空比33%,電鍍30 min。恒電流脈沖電沉積工藝參數(shù)為:輸出電流0.2 A,占空比33%,電鍍時間10 min。圖1為恒電流和恒電位脈沖電沉積工藝參數(shù)示意圖。銅板為陽極,基材為待鍍電極,作為陰極,恒電位脈沖沉積時使用甘汞電極作為參比電極。鍍膜后的樣品經(jīng)蒸餾水清洗。
圖1 脈沖電沉積工藝示意圖
1.3 鍍層檢測與分析
采用SU6600型掃描電鏡 (SEM) 進(jìn)行鍍層表面形貌及晶粒尺寸觀察,結(jié)合能譜儀 (EDS,Octane Elect Plus) 和NexION 350DICP-MS等離子體質(zhì)譜儀分析鍍層元素組成及分布,采用TIME2600涂層測厚儀對電沉積膜層進(jìn)行厚度測試。室溫下利用Im6/Im6ex電化學(xué)工作站對鍍層進(jìn)行開路電位與阻抗測試,介質(zhì)為自來水。測試時采用三電極體系,飽和甘汞電極為參比電極,鉑片為對電極,工作電極為待測樣品。阻抗測試時擾動電壓幅值為10 mV。
2 結(jié)果與討論
2.1 銅錫鍍層的微觀形貌與成分分析
圖2和3為不同截面尺寸的兩種試樣上脈沖方式電沉積膜層的SEM像及EDS線掃描分析結(jié)果。可知,陰極為截面積270 mm2的試樣時,采用恒電流脈沖電沉積的鍍層其Sn特征X射線計數(shù)強度在80~115,而Cu計數(shù)強度為120~180;恒電位脈沖鍍層Sn計數(shù)強度為80~145,Cu計數(shù)強度為110~160。在線掃描中,元素特征X射線計數(shù)強度可表征元素含量,計數(shù)強度大,元素含量高。因此,對于27SiMn鋼基體,恒電流脈沖電沉積鍍層Sn含量波動較小,而恒電位脈沖法Cu含量波動較小;二者銅錫元素整體分布接近,鍍層無顯著優(yōu)劣。
圖2 不同截面尺寸試樣上脈沖方式電沉積膜層的SEM像
圖3 不同截面尺寸試樣上不同脈沖方式電沉積膜層的線掃描分析結(jié)果
而陰極為截面積78.5 mm2的試樣時,恒電流脈沖電沉積鍍層Cu特征X射線計數(shù)強度為120~450,其Sn計數(shù)強度為300~460;而恒電位脈沖鍍層Cu計數(shù)強度為20~110,Sn計數(shù)強度為85~300。恒電流脈沖電沉積鍍層Sn計數(shù)強度波動與恒電位脈沖下的基本相近,但Cu的波動明顯大于恒電位脈沖下的;且元素分布嚴(yán)重不均,宏觀形貌上表現(xiàn)為顏色不均勻。這是由于恒電流脈沖沉積,在恒定0.2 A脈沖電流條件下,待鍍件A截面積較小,膜層實際電流密度超過了其極限電流密度,導(dǎo)致鍍層局部燒焦,成分不均。而恒電位脈沖條件下,截面積小的A試樣電沉積阻力大,電流可自發(fā)減小至極限電流密度之下,銅錫離子正常遷移、沉積,因而其鍍層中銅錫含量波動較小。
恒溫50 ℃下,使用含硝酸5% (質(zhì)量分?jǐn)?shù))、鹽酸5%的混合溶液將鍍層溶解,待鍍層完全溶解后,對溶液進(jìn)行NexION 350DICP-MS等離子體質(zhì)譜分析,得到不同截面尺寸的試樣上電沉積鍍層的Sn含量,如表1所示。
表1 不同截面尺寸試樣上不同脈沖方式電沉積膜層中的Sn含量
由表1可知,對于B試樣,恒電流脈沖電沉積銅錫鍍層中的平均Sn含量約為37.5%,為中錫青銅;而A試樣上鍍層Sn含量達(dá)55.9%,為高錫青銅。這表明,恒電流脈沖電沉積于不同尺寸零件上制備的銅錫鍍層存在顯著差異,這不易于控制鍍層成分,因而該工藝在更換零件尺寸時必須重新計算與設(shè)定脈沖參數(shù)。值得注意的是,圖2a與c中Cu含量增加集中于最外層質(zhì)點,Cu含量降低則發(fā)生于內(nèi)層質(zhì)點,即恒電流脈沖工藝還易造成鍍層沿厚度方向分布不均。結(jié)合恒流電沉積過程中槽電壓逐漸下降的現(xiàn)象,分析鍍層厚度方向分布不均的原因為:恒電流脈沖電沉積時,隨膜層增厚,電沉積阻力減小,槽電壓減小。槽電壓減小,則體系中主要的絡(luò)合離子[Cu(P2O7)2]6-與[Sn(P2O7)2]6-遷移及還原受阻[18,19],外層沉積的質(zhì)點中Sn含量減少,Cu比例上升,鍍層沿厚度方向分布不均。
而恒電位脈沖法結(jié)果與之不同。截面積為270 mm2的A試樣,恒電位脈沖電沉積銅錫鍍層中平均Sn含量為46.1%,而截面積為78.5 mm2的B試樣其鍍層平均Sn含量約為51.7%,二者相差不大,均為高錫青銅。這表明,恒電位脈沖電沉積較恒電流脈沖更利于成分控制,穩(wěn)定獲得高錫青銅鍍層,且可根據(jù)零件尺寸靈活調(diào)整施鍍電流,便于實現(xiàn)某一特定成分、不同尺寸零件的自動化生產(chǎn)。圖2b和d中,Cu含量在最外層質(zhì)點與內(nèi)層質(zhì)點均有出現(xiàn)增加,這表明薄膜內(nèi)外層銅錫比例接近,元素沿厚度方向無差異。其原因為,恒電位脈沖電沉積時,槽電壓維持定值,整個沉積過程中體系中主要的絡(luò)合離子遷移、還原驅(qū)動力不發(fā)生改變,故而鍍層內(nèi)外銅錫原子比例接近定值,最終鍍層成分較為均勻。
2.2 銅錫鍍層的晶粒尺寸分析
由圖2a和c可知,A和B試樣于恒電流脈沖電沉積銅錫晶粒尺寸分別為0.11~1.7和0.12~1 μm。B試樣上鍍層晶粒呈球狀,連接緊密,且晶粒尺寸相對接近 (其中亮白色物質(zhì)為雜質(zhì))。而A試樣的鍍層中有較多不規(guī)則的團(tuán)聚粒子且比較疏松,存在大量孔隙;這是由于恒電流下,通過截面積小的柱狀試樣表面的電流密度高,形核、生長快,原子沉積量大,導(dǎo)致突出點迅速增長,顆粒明顯長大;而空隙的形成原因為電流密度過大,析氫副反應(yīng)加快,引起鍍層疏松多孔。
由圖2b和d可知,A和B試樣于恒電位脈沖電沉積銅錫鍍層的晶粒尺寸分別為和0.09~0.5和0.16~1.5 μm。B試樣塊狀樣品下鍍層亦主要呈球狀,連接緊密 (其中,亮白色物質(zhì)為雜質(zhì))。A試樣樣品下電沉積鍍層主要為小球狀,其晶粒極小,為小于100 nm的納米晶。這是由于截面積較小,槽電壓恒定時其電流增大,而低于極限電流密度時電流適度增大可促進(jìn)粒子快速尋找到最低能量點沉積,在斷電周期,晶體停止生長,電流再次導(dǎo)通時新晶核生成。因此,沉積粒子不易團(tuán)簇、生成枝晶,從而晶粒得到細(xì)化,獲得納米晶。
2.3 銅錫鍍層厚度分析
使用TIME2600涂層測厚儀對不同截面尺寸試樣上脈沖方式電沉積膜層進(jìn)行了厚度測試,結(jié)果如表2所示。可知,對于不同截面尺寸的試樣,恒電流脈沖電沉積鍍層平均厚度接近,約為6 μm;而恒電位脈沖電沉積鍍層平均厚度均在10 μm以上。這表明相同條件下,恒電位脈沖電沉積具有更高的沉積速率。故而在恒定時間內(nèi),恒電位脈沖鍍層較恒電流脈沖鍍層更厚。
表2 不同截面尺寸試樣上脈沖方式電沉積鍍層的厚度
試樣B上恒電流和恒電位脈沖電沉積鍍層橫截面微觀形貌如圖4所示。可知,試樣橫截面均出現(xiàn)了顯著的襯度差異,自下而上依次為牙托粉層 (鑲嵌樣品)、銅錫膜層和基體層。牙托粉與膜層間存在間隙,而膜層與基體結(jié)合較為緊密。此外,恒電勢脈沖電沉積鍍層厚度均在10 μm以上,而恒電流脈沖電沉積鍍層平均厚度僅為6 μm。這再次表明恒電位脈沖電沉積具有更高的沉積速率,與前述測試分析結(jié)果相吻合。
圖4 不同脈沖方式制備鍍層的截面微觀形貌
2.4 銅錫鍍層耐腐蝕性能
在室溫下測定基體、試樣B上恒電流脈沖鍍層、試樣A上恒電位脈沖鍍層的阻抗如圖5和6所示。由圖5可知,對于試樣B,基體、恒電流脈沖鍍層、恒電位脈沖鍍層三者在低頻0.01 Hz時,阻抗分別為1500,12200和14500 Ω·cm2。恒電位脈沖電沉積的鍍層阻抗最大,發(fā)生腐蝕時傳遞阻力大,抵抗腐蝕能力最強,比基體提高了6倍以上,優(yōu)于恒電流脈沖方式下獲得鍍層的。圖6表明,對于截面積較小的試樣A,恒電位脈沖電沉積鍍層優(yōu)越的耐蝕性能更為凸顯,0.01 Hz時其阻抗約為恒電流脈沖鍍層的兩倍。這是由于截面積較小時,恒電流脈沖鍍層易燒焦,鍍層成分不均勻,為中錫青銅,其在腐蝕介質(zhì)中容易發(fā)生點蝕,耐蝕性能較差;而恒電位脈沖較恒電流脈沖電沉積速率快,相同條件下鍍層更厚,增厚的膜層可有效防止腐蝕介質(zhì)中侵蝕性離子向基體滲透,延緩了微型腐蝕電池的形成;同時鍍層成分均勻,為Sn含量46%以上的高錫青銅,在腐蝕介質(zhì)中化學(xué)性質(zhì)穩(wěn)定,故其阻抗值高、耐蝕性能優(yōu)異。
圖5 試樣B及其在不同脈沖方式沉積鍍層的Bode圖
圖6 試樣A及其在不同脈沖方式沉積鍍層的Bode圖
2.5 恒電位脈沖電壓法鍍層的溶解問題
恒電流脈沖可瞬時恢復(fù)電沉積初始條件,而恒電位脈沖在脈沖結(jié)束時存在一定的恢復(fù)過程,故可能發(fā)生沉積金屬的溶解。為此,對恒電位脈沖電壓法下制備的鍍層進(jìn)行開路電位測試,其結(jié)果如圖7所示。可知,恒電位脈沖電沉積鍍層-溶液的穩(wěn)定電位在0.45~0.5 V。無外加電流時,金屬材料在腐蝕溶液中達(dá)到穩(wěn)定狀態(tài)的電位為自腐蝕電位,此時金屬材料發(fā)生金屬溶解與去極化劑還原的共軛反應(yīng)。恒電位脈沖電沉積未得到廣泛應(yīng)用的局限之一正在于電位脈沖結(jié)束后重新達(dá)到初始電位時,在自腐蝕電位附近可能出現(xiàn)金屬鍍層的溶解。因此,本研究使用高占空比 (33%),延長脈沖周期,從而減少電位恢復(fù)次數(shù);同時選用脈沖電位3 V,與自腐蝕電位0.45~0.5 V保持較大差值。二者協(xié)同作用,有效降低鍍層的溶解幾率,利于提高銅錫電沉積速率,制備出較厚膜層。鍍層厚度實驗結(jié)果與之吻合。此外,高占空比 (30%) 條件下,陰極消耗的Cu2+與Sn2+獲得了充分的補充時間,有效減少了氫離子的還原,減輕了鍍層滲氫[11]。同時,高占空比下通斷時間較長,晶粒團(tuán)簇和生長被抑制,晶粒細(xì)化,從而利于獲得質(zhì)量較佳的鍍層。實驗結(jié)果也證實,該工藝制備的銅錫鍍層成分均勻,最小晶粒尺寸小于100 nm。綜上可知,30%高占空比、恒電位3 V進(jìn)行脈沖電沉積,可克服恒電位脈沖沉積鍍層溶解缺陷,獲得綜合性能優(yōu)異的高錫青銅鍍層。
圖7 恒電位脈沖電沉積鍍層的開路電位
3 結(jié)論
(1) 恒電位脈沖電沉積可自發(fā)適應(yīng)零件尺寸變化制備高錫青銅,鍍層成分均勻;而恒電流脈沖在不同零件上制備的鍍層成分差距大,沿厚度方向分布不均,且不能穩(wěn)定獲得高錫青銅層。
(2) 采用恒電位脈沖模式在截面積為78.5 mm2的27SiMn試樣上獲得了納米Cu-Sn鍍層,晶粒尺寸小于100 nm。而采用恒電流脈沖模式時,由于試樣截面積較小而表面電流密度較高,鍍層形核、生長較快,原子沉積量大,突出點迅速增長,顆粒明顯長大;且電流密度高引起析氫副反應(yīng)加快,造成鍍層孔隙率高。
(3) 33%的高占空比、3 V沉積電位下進(jìn)行恒電位脈沖電鍍銅錫,因可以減少電位恢復(fù)且遠(yuǎn)離自腐蝕電位而克服了鍍層溶解缺陷;且電沉積速率高,所制備的高錫青銅耐蝕性能強,其阻抗值高于恒電流脈沖鍍層的,綜合性能更優(yōu)。
免責(zé)聲明:本網(wǎng)站所轉(zhuǎn)載的文字、圖片與視頻資料版權(quán)歸原創(chuàng)作者所有,如果涉及侵權(quán),請第一時間聯(lián)系本網(wǎng)刪除。
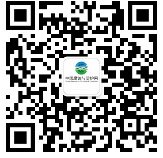
官方微信
《中國腐蝕與防護(hù)網(wǎng)電子期刊》征訂啟事
- 投稿聯(lián)系:編輯部
- 電話:010-62316606-806
- 郵箱:fsfhzy666@163.com
- 中國腐蝕與防護(hù)網(wǎng)官方QQ群:140808414