摘要
研究了化學(xué)組分和顯微組織結(jié)構(gòu)對(duì)AZ31,AZ91,AM60和ZK61等4種鎂合金在含有不同濃度NH4NO3的0.1 mol/L NaCl溶液中腐蝕行為的影響。通過浸泡實(shí)驗(yàn)、電化學(xué)測(cè)試、SEM和CLSM表面分析等探討了4種鎂合金的腐蝕機(jī)理。結(jié)果表明,NH4NO3的存在會(huì)加快鎂合金的腐蝕;并且由于在特定濃度范圍內(nèi),Cl-,NH4+和NO3-的協(xié)同作用,會(huì)發(fā)生自催化點(diǎn)蝕。不同鎂合金的耐蝕性與合金的化學(xué)成分和顯微組織密切相關(guān)。
關(guān)鍵詞: 鎂合金; 硝酸銨; 自催化點(diǎn)蝕; 化學(xué)組分; 顯微結(jié)構(gòu)
鎂合金是最輕的一種金屬結(jié)構(gòu)材料,由于其低密度和良好的力學(xué)性能而受到越來越多的關(guān)注 [1],被廣泛應(yīng)用于航空、航天和汽車工業(yè)[2-4]。然而,由于較差的耐腐蝕性能[5],其應(yīng)用范圍比鋁合金更受限制。霧霾的存在對(duì)金屬的腐蝕行為有一定的影響。Cui等[6]研究了AZ31鎂合金在Cl--NH4+-NO3-溶液體系內(nèi)的腐蝕機(jī)制,研究結(jié)果表明特定的溶液體系會(huì)影響暴露在霧霾環(huán)境中鎂合金的腐蝕過程。
對(duì)于鎂合金而言,Al可以通過形成第二相 (β-Mg17Al12) 顯著提高合金的抗拉強(qiáng)度[7]。添加一定量的Al會(huì)提高鎂合金中β相的含量,當(dāng)β相形成連續(xù)網(wǎng)狀結(jié)構(gòu)時(shí),會(huì)顯著改善材料的耐腐蝕性[8]。Zn對(duì)于鎂合金的強(qiáng)度也有著至關(guān)重要的影響,它的存在可以抑制Fe及Ni對(duì)鎂合金腐蝕的不利影響。當(dāng)Zn含量較少時(shí) (Zn<1%),可以提高Al在鎂合金中的固溶度,提高Al的固溶強(qiáng)化作用[9]。Song等[10]認(rèn)為,為保證鎂合金的耐蝕性能,AZ系鎂合金中的Zn添加量應(yīng)該控制在1%~3% (質(zhì)量分?jǐn)?shù))。Mn在鎂合金中會(huì)與Fe形成熔渣,可以在一定程度上消除Fe對(duì)于鎂合金耐腐蝕性的不利影響。因此,一般耐腐蝕的鎂鋁合金中都含有一定量的Mn。除以上合金元素外,Zr也是一種較常見的元素,通常被添加到非鋁系鎂合金中。添加到鎂合金中的Zr不僅能很好地細(xì)化晶粒,而且可以有效地去除雜質(zhì)[11]。在熔融的鎂基體中,Zr與Fe反應(yīng)形成Fe-Zr金屬間化合物,由于該金屬間化合物具有較高密度,會(huì)快速沉積,因而可以提高鎂合金的純度,這在一定程度上改善了鎂合金的耐蝕性。然而,Zr在非鋁合金晶粒中通常分布不均勻,Zr會(huì)富集在晶粒的中心。此外,不能固溶的Zr顆??赡軙?huì)作為腐蝕電偶的陰極從而加速鎂合金的腐蝕速率,因此應(yīng)該注意避免Zr的過量添加。
基于此,本文研究了不同化學(xué)組分和顯微結(jié)構(gòu)的鎂合金 (AZ31,AZ91,AM60和ZK61) 在模擬濱海霧霾環(huán)境下的腐蝕行為。研究采用在NaCl溶液中添加NH4NO3模擬濱海霧霾環(huán)境,探討了NH4+和NO3-對(duì)4種鎂合金在NaCl溶液中腐蝕行為的影響,以及它們發(fā)生點(diǎn)蝕和均勻腐蝕的演變過程。
1 實(shí)驗(yàn)方法
本實(shí)驗(yàn)采用的實(shí)驗(yàn)材料為軋制的AZ31 (Mg2.6Al1.0) 和AZ91 (Al8.2Zn0.4) 板材以及AM60 (Al5.9Mn0.3Zn0.001) 和ZK61 (Zn5.5Zr0.5Mn0.008) 鑄錠。溶液環(huán)境為0.1 mol/L NaCl溶液和添加不同濃度NH4NO3的0.1 mol/L NaCl溶液,溶液的初始pH是直接通過pH計(jì)測(cè)量得到。實(shí)驗(yàn)中所有使用的化學(xué)藥品都為分析級(jí)試劑。在整個(gè)實(shí)驗(yàn)過程中,溶液溫度控制在 (25±1) ℃。
試樣加工成20 mm×20 mm×3 mm的方形試樣,用砂紙打磨到1500#,之后用酒精脫脂并用去離子水清洗后冷風(fēng)干燥。為保證實(shí)驗(yàn)結(jié)果具有重復(fù)性,每個(gè)條件均使用5個(gè)平行試樣。用分析天平對(duì)樣品原始重量 (w0) 進(jìn)行稱量并記錄,試樣在300 mL的溶液中浸泡12 h。之后,將試樣放置在除銹液 (200 g/L CrO3,10 g/L AgNO3和20 g/L BaNO3) 中浸泡去除腐蝕產(chǎn)物,用去離子水沖洗并冷風(fēng)干燥。對(duì)干燥好的試樣進(jìn)行稱重并記錄最終質(zhì)量 (w1)。試樣的失重 (C,mg/cm2) 由下式得到:
其中,A是試樣的暴露面積。
電化學(xué)測(cè)試所用儀器為CS350電化學(xué)工作站,試樣加工成10 mm×10 mm×3 mm方形試樣,測(cè)試采用傳統(tǒng)的三電極體系,以試樣為工作電極,Pt片為對(duì)電極,飽和甘汞電極 (SCE) 為參比電極。測(cè)試前用砂紙將工作面逐級(jí)打磨到1500#,之后用酒精和去離子水對(duì)工作面進(jìn)行仔細(xì)清洗并用冷風(fēng)干燥。以開路電位 (OCP) 為測(cè)試起始點(diǎn),分別對(duì)試樣動(dòng)電位極化曲線的陽極分支和陰極分支進(jìn)行測(cè)試,動(dòng)電位掃描速率為0.333 mV/s。
采用掃描電鏡 (SEM,Quanta 250) 對(duì)浸泡試樣表面的腐蝕形貌進(jìn)行表征,之后采用激光共聚焦顯微鏡 (CLSM, KEYENCE VK-X250) 對(duì)試樣表面點(diǎn)蝕坑進(jìn)行表征和分析。CLSM的每個(gè)視場(chǎng)面積為0.015 cm2,每個(gè)試樣選取5個(gè)視場(chǎng)進(jìn)行統(tǒng)計(jì)分析。
2 結(jié)果與討論
2.1 原始微觀組織結(jié)構(gòu)
AZ31,AZ91,AM60和ZK61合金的原始組織如圖1所示。從圖1a和b中可以看出,AZ91合金的SEM像包含更多的β相 (Mg17Al12),而在AZ31合金中幾乎看不到β相。從圖1c中可以看出,除基體相外,AM60合金的顯微組織還包含β相和Al8Mn5相。圖1d中顯示,ZK61合金的微觀組織還包含基體Mg相和Zn2Zr。除基體α相外,共晶α相在腐蝕系統(tǒng)中充當(dāng)陰極,這會(huì)促進(jìn)基體α相的腐蝕,從而導(dǎo)致ZK61合金的耐腐蝕性較差。
圖1 AZ31,AZ91,AM60和ZK61合金的微觀結(jié)構(gòu)
2.2 失重及腐蝕速率比較
圖2是4種鎂合金的失重和腐蝕速率??梢钥闯觯尤隢H4NO3后,4種鎂合金的重量損失都有所增加,但增幅各不相同,這歸因于鎂合金的化學(xué)組成和微觀結(jié)構(gòu)的差異。
圖2 AZ31,AZ91,AM60和ZK61 4種鎂合金在0.1 mol/L NaCl和0.1 mol/L NaCl+0.01 mol/L NH4NO3兩種溶液中浸泡12 h的失重和腐蝕速率
鎂合金腐蝕速率的計(jì)算公式如下[12]:
其中,V是腐蝕速率 (mg·cm-2·d-1);t是浸泡時(shí)間 (h)。通過等式PW?=?2.1 V將V值轉(zhuǎn)換為腐蝕速率 (PW,mm/a),如圖2b所示。在0.1 mol/L NaCl溶液中,AZ91合金的腐蝕速率最低,ZK61合金的腐蝕速率最高。加入0.01 mol/L NH4NO3溶液之后,4種鎂合金的腐蝕速率均有所提高,而AM60合金的腐蝕速率最低,表明AM60合金在該溶液體系中具有更好的耐蝕性。ZK61合金的腐蝕速率仍然是最高的,說明ZK61合金的耐蝕性較差,這些結(jié)果也可從表1中得出。
表1 NH4NO3對(duì)4種鎂合金的腐蝕加速倍率
圖3分別顯示了AZ31,AZ91,AM60和ZK61合金在未含有和含有0.01 mol/L NH4NO3的0.1 mol/L NaCl溶液中的極化曲線。在圖3a中,ZK61合金的陰極Tafel斜率明顯高于其他3種鎂合金,另外3種鎂合金的陰極極化曲線在0.1 mol/L NaCl溶液中具有相同的變化趨勢(shì),均為典型的氫析出反應(yīng),具有極為接近的Tafel斜率。從表2中可以看出,圖3a中的陰極曲線依次向右移動(dòng) (從左至右依次為AZ91,AM60,AZ31和ZK61合金) ,腐蝕電流密度依次增加,表明腐蝕速率依次增加。ZK61合金的腐蝕電流密度比AZ91和AM60合金的高出一個(gè)數(shù)量級(jí),約是AZ31合金的6~7倍,這表明ZK61合金的腐蝕速率遠(yuǎn)高于其他3種合金的。表2為4種鎂合金在0.1 mol/L NaCl溶液中極化曲線的擬合數(shù)據(jù),參照之前的研究表明,腐蝕電流可以作為腐蝕速率的標(biāo)準(zhǔn)度量之一,即腐蝕電流越小,耐腐蝕性越好[13]。綜上所述,4種鎂合金耐蝕性的順序依次為:AZ91>AM60>AZ31>ZK61,極化曲線測(cè)試結(jié)果與失重實(shí)驗(yàn)一致。
圖3 AZ31,AZ91,AM60和ZK61鎂合金在0.1 mol/L NaCl和0.1 mol/L NaCl+0.01 mol/L NH4NO3溶液中的極化曲線
表2 4種鎂合金在0.1 mol/L NaCl溶液中的自腐蝕電流密度 (Icorr) 和腐蝕速率 (Pi)
與圖3a中的曲線相比,添加NH4NO3后,極化曲線發(fā)生了很大變化。圖3b中掃描曲線的陰極部分表明,AZ91合金的氫析出電流密度值低于其他合金的,AM60,AZ31和ZK61合金的依次降低。這表明從動(dòng)力學(xué)上來講,ZK61合金的陰極反應(yīng)比其他3種合金更容易發(fā)生,這可能是由于ZK61合金中存在更多的陰極第二相,這可能會(huì)導(dǎo)致電偶腐蝕。圖3b中AZ91和AM60合金掃描曲線的陽極部分有明顯的拐點(diǎn),在此之前電流密度緩慢增加,然后隨著電位的增加而迅速增加。但是,隨著電流密度的增加,ZK61合金的陽極曲線上沒有明顯的拐點(diǎn)。Song等[14]認(rèn)為,極化曲線掃描過程中腐蝕電位的差異是由于未腐蝕表面的陰極氫逸出速率不同所致。如果陽極過程沒有明顯改變,較低的陰極極化曲線通常會(huì)導(dǎo)致更大的負(fù)腐蝕電位[13]。
2.3 腐蝕形貌觀察
2.3.1 SEM形貌觀察
前期研究[6]表明,AZ31鎂合金在含有NH4NO3的NaCl溶液中發(fā)生了明顯的點(diǎn)蝕行為,且與傳統(tǒng)鎂合金點(diǎn)蝕橫向生長(zhǎng)不同,這種情況下的點(diǎn)蝕沿深度方向生長(zhǎng)。為了探討合金元素對(duì)自催化點(diǎn)蝕的影響,本文通過添加不同NH4NO3含量,研究4種鎂合金的“自催化”點(diǎn)蝕的離子濃度區(qū)間。圖4顯示了去除腐蝕產(chǎn)物的AZ31,AZ91和ZK61合金的SEM形貌 (AM60合金沒有出現(xiàn)“自催化”點(diǎn)蝕行為)。可以看出,AZ31,AZ91和ZK61 3種合金在去除腐蝕產(chǎn)物后顯示出各不相同的腐蝕形態(tài)。此外,3種鎂合金發(fā)生自催化點(diǎn)蝕的NH4NO3濃度范圍也不同。
圖4 AZ31,AZ91和ZK61合金在NaCl溶液中浸泡12 h后的腐蝕形貌
由圖4a可以看出,隨著NH4NO3濃度的逐漸增大,AZ31試樣表面由淺坑到強(qiáng)點(diǎn)蝕再到均勻腐蝕,自催化點(diǎn)蝕濃度在0.001~0.1 mol/L之間。在圖4b和c中可以看到相似的腐蝕趨勢(shì),AZ91合金的自催化點(diǎn)蝕濃度在0.007~0.04 mol/L之間,ZK61合金的自催化點(diǎn)蝕濃度在0.0002~0.09 mol/L之間。濃度區(qū)間的大小可以反映出鎂合金的耐蝕性差異,AZ91合金的耐蝕性優(yōu)于AZ31和ZK61鎂合金的。對(duì)于AM60合金來說,沒有特定的自催化點(diǎn)蝕的NH4NO3濃度范圍,僅在某些濃度 (0.001和0.01 mol/L NH4NO3) 時(shí)出現(xiàn)少量的腐蝕坑。這些腐蝕特征可以在圖5中看出。
圖5 4種鎂合金在0.1 mol/L NaCl和0.1 mol/L NaCl+0.01 mol/L NH4NO3兩種溶液環(huán)境中的點(diǎn)蝕參數(shù)
2.3.2 點(diǎn)蝕參數(shù)統(tǒng)計(jì)
點(diǎn)蝕參數(shù)具有6種指標(biāo),如圖5所示。除了AZ91合金外 (圖5a),其他合金的點(diǎn)蝕密度在添加0.01 mol/L NH4NO3的NaCl溶液中發(fā)生下降,這表明點(diǎn)蝕坑合并或某些點(diǎn)蝕坑的優(yōu)先生長(zhǎng)取決于NH4NO3的濃度。在兩種溶液中,最大點(diǎn)蝕深度 (圖5b) 和平均點(diǎn)蝕深度 (圖5c) 有所不同。加入NH4NO3后,ZK61合金的最大點(diǎn)蝕深度 (圖5b) 和平均點(diǎn)蝕深度 (圖5c) 增加了約100倍。說明在含0.01 mol/L NH4NO3的NaCl溶液中,ZK61合金的耐腐蝕性最差。添加NH4NO3后,點(diǎn)蝕坑直徑 (圖5d) 與點(diǎn)蝕坑深度的變化趨勢(shì)相同。AZ31和AZ91合金的單個(gè)點(diǎn)蝕坑體積 (圖5e) 變化不大,加入0.01 mol/L NH4NO3后,AM60合金的點(diǎn)蝕坑體積減小。ZK61合金的點(diǎn)蝕坑體積在添加NH4NO3后會(huì)成倍增加,腐蝕坑由淺變深。圖5f所示的點(diǎn)蝕坑的幾何形狀是用于闡明點(diǎn)蝕坑特性的有效參數(shù)[15]。根據(jù)點(diǎn)蝕坑直徑 (d) 與點(diǎn)蝕坑深度 (D) 的比值,點(diǎn)蝕坑形狀可以簡(jiǎn)單地分為半圓形 (d/2D=1),深孔形 (d/2D<1) 和淺碟形 (d/2D>1)。與其他3種鎂合金相比,ZK61合金的d/2D值下降最多,這間接表明ZK61合金的耐腐蝕性最差。
2.4 討論
合金元素在一定程度上決定著鎂合金的微觀結(jié)構(gòu)。然而,鎂合金的不均勻組織容易造成微電偶腐蝕[16,17]。因此,鎂合金的微觀結(jié)構(gòu)在其腐蝕機(jī)理中起著重要作用。
Pardo等[16]指出,β相在腐蝕過程中具有雙重作用。根據(jù)β相的數(shù)量和分布,可以起到腐蝕阻擋層或加速陰極電偶的作用。本文中AZ91合金的β相呈網(wǎng)狀結(jié)構(gòu)連續(xù)地分布在基體相中,可以有效地阻止AZ91合金進(jìn)一步發(fā)生腐蝕。相反,AZ31合金中很少且不連續(xù)分布的β相會(huì)起到加速腐蝕的作用。在Cl--NH4+-NO3-溶液體系中,連續(xù)的β相也可以起阻礙腐蝕的作用,可以明顯看到AZ91合金的耐蝕性要優(yōu)于AZ31合金的。
Zn有助于克服Fe和Ni的有害腐蝕作用,但高含量的Zn會(huì)導(dǎo)致第二相沉淀物的形成,從而導(dǎo)致不可避免的電偶腐蝕。Huan等[18]證明了ZK30合金的耐腐蝕性優(yōu)于ZK60合金的,認(rèn)為ZK30合金中Zn含量較低,形成較少的第二相顆粒和微電偶腐蝕。當(dāng)Zn含量超過3% (質(zhì)量分?jǐn)?shù)) 時(shí),根據(jù)Mg-Zn二元相圖可知[19],大量形成的Mg7Zn3相將導(dǎo)致微電流與基質(zhì)偶聯(lián),從而加速材料的腐蝕。從圖1d可以看出,ZK61合金中存在一些Mg2Zn相和枝晶,這可能會(huì)導(dǎo)致微電偶腐蝕,是ZK61合金耐腐蝕性差的原因之一。Zn含量的差異會(huì)影響4種鎂合金在含有0.01 mol/L NH4NO3的NaCl溶液中的腐蝕行為。Zn可與溶液環(huán)境中的NH4+絡(luò)合,導(dǎo)致鎂基體脫落并腐蝕。4種鎂合金中自催化點(diǎn)蝕的NH4NO3濃度范圍最大的是ZK61合金,這可能與其Zn含量較高有關(guān)。
Zr可以細(xì)化晶粒,在一定條件下,Mg-Zn-Zr合金具有良好的耐蝕性。但是,如果Zr含量過高會(huì)導(dǎo)致鎂合金的耐蝕性降低。Song等[8]研究表明,當(dāng)Zr含量超過0.48%時(shí),鎂合金的腐蝕速率會(huì)增加,這與Zr在鎂合金中的固溶度有關(guān)。當(dāng)Zr含量超過其在鎂合金中的固溶度時(shí)會(huì)析出沉淀,含Zr沉淀充當(dāng)鎂合金中的有效陰極相,從而加速了鎂合金基體相的腐蝕。在該實(shí)驗(yàn)中,ZK61合金含有0.512%的Zr,超過文獻(xiàn)中的0.48%,這可能是ZK61合金耐腐蝕性差的另一個(gè)原因。
Mn可通過去除Fe和其他重金屬元素來避免形成有害的金屬間化合物,從而提高合金的耐腐蝕性。AM60合金中的Mn可以形成AlMnFe相,降低合金中Fe的含量,凈化合金,從而提高合金的耐腐蝕性。Mn被添加到大多數(shù)Mg-Al合金中以去除雜質(zhì)Fe和Ni,對(duì)于AZ91和AM60合金,通常添加足夠的Mn以確保Fe:Mn比小于0.032,從而顯著提高耐腐蝕性[10,20]。另外,AM60鎂合金中不含Zn,其也未觀察到“自催化”點(diǎn)蝕區(qū)間,這進(jìn)一步說明,Zn的存在可能是引起鎂合金“自催化”點(diǎn)蝕的重要因素。這一部分內(nèi)容將通過煉制不同含量的Mg-xZn合金來進(jìn)一步研究。
實(shí)驗(yàn)結(jié)果表明,引入NH4NO3會(huì)加快4種鎂合金的腐蝕速率,原因主要在于NH4NO3的引入會(huì)降低溶液的pH,酸性環(huán)境下鎂合金會(huì)更容易腐蝕;再者由于NH4+的緩沖作用,添加NH4NO3會(huì)使Mg(OH)2保護(hù)膜遭到破壞并促進(jìn)陰極NO3-的還原反應(yīng),從而加速了鎂合金的腐蝕。
3 結(jié)論
(1) 在0.1 mol/L NaCl溶液中添加0.01 mol/L NH4NO3可加快AZ31,AZ91,AM60和ZK61 4種鎂合金的腐蝕速率。
(2) 在0.1 mol/L NaCl溶液中,4種鎂合金的腐蝕速率排序?yàn)閆K61>AZ31>AM60>AZ91;而在0.1 mol/L NaCl溶液中添加0.01 mol/L NH4NO3時(shí),4種鎂合金的腐蝕速率排序變?yōu)椋篫K61>AZ31>AZ91>AM60。
(3) 當(dāng)在溶液中添加0.001~0.1 mol/L NH4NO3時(shí),AZ31鎂合金就會(huì)出現(xiàn)“自催化”點(diǎn)蝕;當(dāng)溶液中添加0.007~0.04 mol/L NH4NO3時(shí),AZ91鎂合金會(huì)出現(xiàn)自催化點(diǎn)蝕。ZK61鎂合金自催化點(diǎn)蝕發(fā)生在溶液中NH4NO3的濃度范圍為0.0002~0.09 mol/L時(shí),AM60鎂合金未發(fā)現(xiàn)自催化點(diǎn)蝕。
(4) Zn可能是導(dǎo)致鎂合金在一定NH4NO3濃度區(qū)間發(fā)生自催化點(diǎn)蝕的關(guān)鍵因素。
免責(zé)聲明:本網(wǎng)站所轉(zhuǎn)載的文字、圖片與視頻資料版權(quán)歸原創(chuàng)作者所有,如果涉及侵權(quán),請(qǐng)第一時(shí)間聯(lián)系本網(wǎng)刪除。
-
標(biāo)簽: 鎂合金, 硝酸銨, 自催化點(diǎn)蝕, 化學(xué)組分, 顯微結(jié)構(gòu)
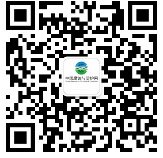
官方微信
《中國(guó)腐蝕與防護(hù)網(wǎng)電子期刊》征訂啟事
- 投稿聯(lián)系:編輯部
- 電話:010-62316606-806
- 郵箱:fsfhzy666@163.com
- 中國(guó)腐蝕與防護(hù)網(wǎng)官方QQ群:140808414