某大型燃料型原油加工企業,各類儲罐200多臺,其中原油儲罐34臺,計28臺采取內防腐措施。硫含量最高為巴士拉原油(2.65%);酸值最高為魁托油(3.44mgKOH/g),含硫油加工對儲罐系統造成腐蝕有所加劇,由于采取了多種防腐措施,有效控制了各類油罐腐蝕,保證了儲罐系統正常使用與運行。
油罐腐蝕現狀
1 原油罐
在所有油罐中,原油罐的腐蝕較為嚴重。以原油中轉站三臺20000m3原油罐為例,投用7年后發生罐底板腐蝕穿孔,最大蝕孔直徑達10cm,被迫換底,通過對原油中轉站原油罐進行水樣分析,發現積水中H2S、SO2、Cl-含量都很高。
2 半成品油罐
半成品油罐腐蝕性也較大,其中焦化粗汽油腐蝕更為嚴重,罐底(水相)主要表現為非均勻全面腐蝕和垢下腐蝕,腐蝕介質主要為水中溶解氧、H2S、無機鹽類,在粗汽油罐的上部及頂部氣液相交界處,由于在罐壁表面會形成一層薄薄的水膜,油品中揮發出來H2S及空氣O2溶解在水膜中形成腐蝕性較強介質,從而在該處表現為非均勻全面腐蝕,且多以坑點狀出現,最大蝕速在0.5~1mm/a。此外,拔頭油球罐曾出現濕H2S引起球罐的焊縫及熱影響區氫致裂紋。
3 污油污水罐及瓦斯氣柜
盡管污油污水罐與瓦斯氣柜中H2S及有機硫較成品、半成品油罐與原油要高出許多,但由于從一開始就采取重防腐措施,目前防腐涂層良好,沒有對罐體造成腐蝕。
腐蝕機理分析
1 微電池腐蝕
油罐底板積水是造成罐底板電化學腐蝕的重要原因,罐底所含各種離子雜質水溶液與罐底涂層脫落后裸露金屬表面構成許多微電池,原油中Ca2+、Fe2+、Mg2+等帶電離子增加了電解質水溶液的電導率,加快了腐蝕進程。以罐底板銹蝕為例,腐蝕過程反應產物Fe(OH)2在積水中溶解氧的氧化下生成Fe(OH)3,其進一步氧化成紅色鐵銹Fe2O3·3H2O。微電池腐蝕由表面開始,逐漸向下擴展形成鼓包和分層,隨著腐蝕不斷的加深和擴展,進而形成罐底板大面積銹蝕區域。
2 積水中二氧化硫腐蝕
罐底積水中二氧化硫對罐底防腐層脫落鋼板可發生酸的再生循環反應。首先由SO2、O2及Fe生成FeSO4,然后FeSO4水解形成氧化物和游離酸,游離酸又加速鐵的腐蝕,生成新FeSO4,如此反復循環加速對罐底板的銹蝕。
3 H2S-H2O型腐蝕
當原油罐中內設加熱盤管時,往往在加熱盤管周圍比其他區域腐蝕來得嚴重,這是由于MgCl2與CaCl2受熱水解,氯化氫在有水存在時腐蝕金屬。
4 濕H2S環境下的氫致開裂
三臺1000m316MnR材質球罐中發現濕H2S氫致開裂,由于焊后沒做熱處理,加之H2S達200×10-6,投用不長時間在下溫帶環焊縫熱影響區出現大量階梯狀裂紋。另外,液化氣球罐、輕油罐頂以及酸性水汽提裝置等都普遍存在濕H2S腐蝕問題。
5 細菌腐蝕
原油中淤泥對鋼鐵產生腐蝕作用的細菌有硫代硫酸鹽、硫氧化細菌等,細菌腐蝕促進了罐底鋼表面的陽極離子化反應,從而加速罐底板腐蝕。
防腐措施
1 犧牲陽極涂層聯合保護
由于罐底操作水層存在,油罐罐底主要表現為電化學腐蝕的特征。因此對罐底進行防腐時,必須進行噴砂處理,要求基材表面達Sa2.5級,然后刷兩道環氧導電涂層,選用適合鋁合金作陽極材料,施工中鋁合金陽極塊應均勻布焊在罐底,不得有虛焊,陽極外露表面應清潔,在陽極焊好后對每塊陽極進行電流測量確保有效電連接。以確保涂層部分脫落后,罐底能獲得有效的電化學保護。
2 熱噴涂噴鋁+抗靜電涂層封閉
熱噴涂噴鋁前為保證噴涂質量,基材表面需噴砂處理,一般要求Sa3級(即100%噴砂),采用線材火焰噴涂與電弧噴涂兩種施工方法,選用抗靜電涂料刷涂來封閉孔隙以免腐蝕介質進入基材,一般控制鋁層厚度為150μm,涂層總厚度210μm左右。
3 非金屬有機涂料
非金屬有機涂料涂層是油罐內防腐的重要手段。針對不同油種,選擇不同的防腐涂料體系極其重要。成品油罐與20000m3氣柜防腐工程,絕大多數油罐經6年使用,沒有出現涂層失效與脫落現象。
4 玻璃鋼防腐內襯
玻璃鋼襯里層主要起屏蔽作用,一般玻璃鋼襯里層由底層、膩子層、玻璃鋼增強層及面層組成。常用的有環氧、酚醛、呋喃等幾種材料。主要應用于含硫污水、污油罐作內防腐內襯。
免責聲明:本網站所轉載的文字、圖片與視頻資料版權歸原創作者所有,如果涉及侵權,請第一時間聯系本網刪除。
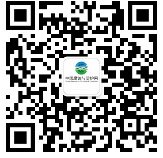
官方微信
《中國腐蝕與防護網電子期刊》征訂啟事
- 投稿聯系:編輯部
- 電話:010-62316606-806
- 郵箱:fsfhzy666@163.com
- 中國腐蝕與防護網官方QQ群:140808414