斷裂失效分析
金屬斷裂的基本概念
在機電裝備的各類失效中以斷裂失效最主要,危害最大。斷裂失效的分析與預防已發展為一門獨立的邊緣學科。
目前對斷裂行為的研究有兩種不同的方法:
一種是斷裂力學的方法,其根據彈性力學及彈塑性理論,并考慮材料內部存在有缺陷而建立起來的一種研究斷裂行為的方法。
另一種是金屬物理的方法,從材料的顯微組織、微觀缺陷、甚至分子和原子的尺度上研究斷裂行為的方法。
斷裂失效分析則是從斷口的宏觀、微觀特征入手,研究斷裂過程和形貌特征與材料性能、顯微組織、零件受力狀態及環境條件之間的關系,從而揭示斷裂失效的原因。它在斷裂力學方法和金屬物理方法之間架起聯系的橋梁。
斷裂與斷口
構件或試樣在外力作用下導致裂紋形成擴展而分裂為兩部分(或幾部分)的過程稱為斷裂。它包括裂紋萌生、擴展和最后瞬斷三個階段。斷裂形成的斷面稱為斷口。斷口上詳細記錄了斷裂過程中內外因素的變化所留下的痕跡與特征,是分析斷裂機理與原因的重要依據。
斷裂分類
斷裂可按具體的需要和分析研究的方便進行分類。
1 按斷裂性質分類
根據零件斷裂前所產生的宏觀塑性變形量的大小分為:
塑性斷裂,斷裂前發生較明顯的塑性變形。延伸率大于5%的材料通常稱為塑性材料;
脆性斷裂,斷裂前幾乎不產生明顯的塑性變形。延伸率小于3%的材料通常稱為脆性材料;
塑性-脆性混合型斷裂,又稱為準脆性斷裂。
2 按斷裂路徑分類
依斷裂路徑的走向可分為穿晶斷裂和沿晶斷裂兩類。在實際斷裂失效斷口上,多數情況是既有沿晶斷裂,又有穿晶斷裂的混合型斷裂。
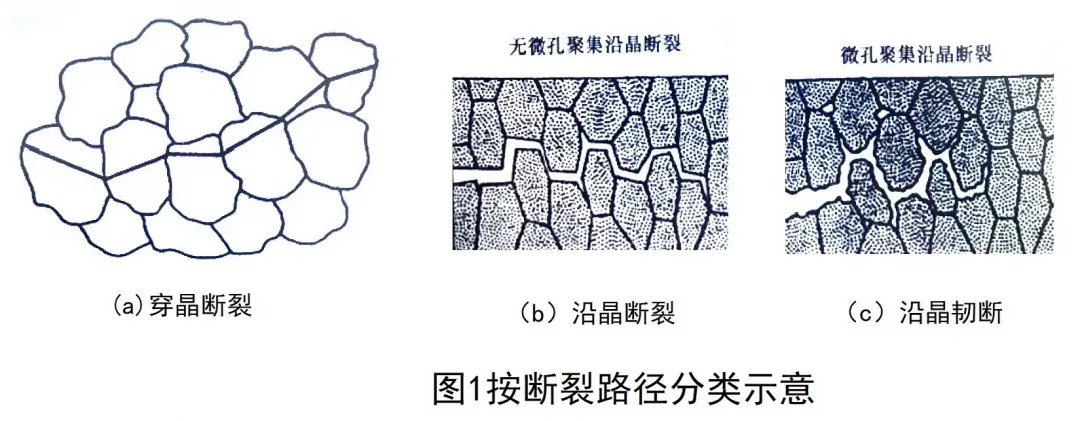
3 按斷面相對位移形式分類
按兩斷面在斷裂過程中相對運動的方向可分為:
張開型(Ⅰ型);
前后滑移型(Ⅱ型);
剪切性(Ⅲ型)。
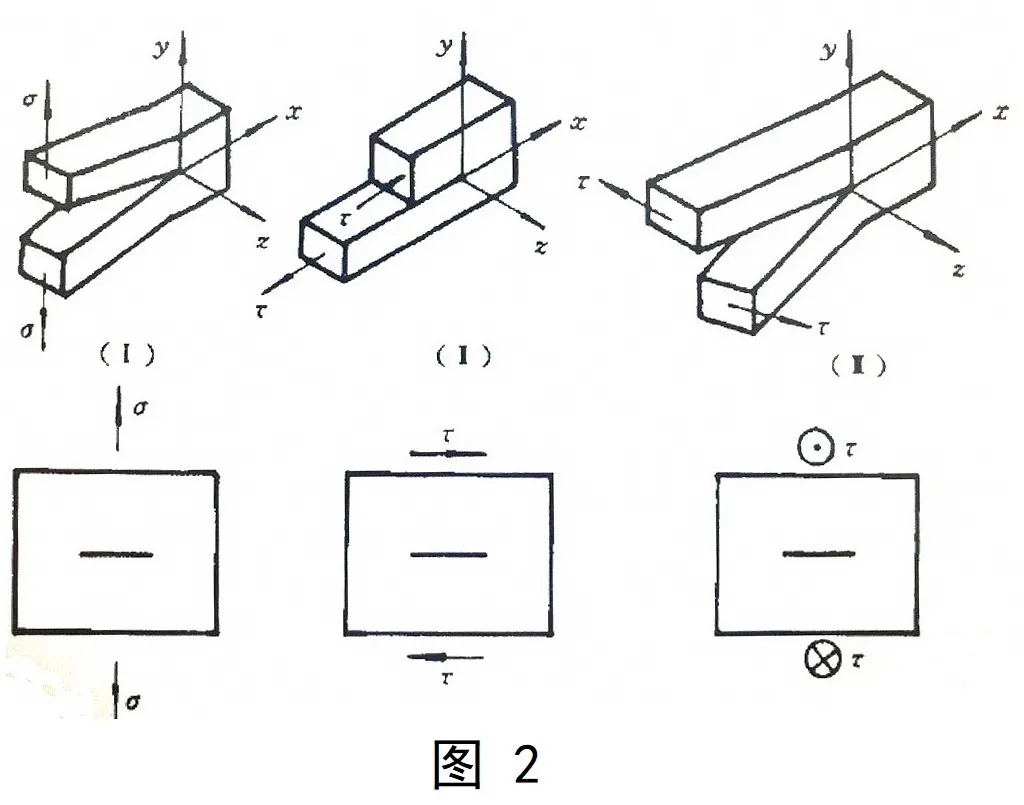
4 按斷裂方式分類
按斷面所受的外力類型的不同分為正斷、切斷及混合斷裂三種。
5 按斷裂機制分類
可分為解理、準解理、韌窩、滑移分離、沿晶及疲勞等多種斷裂。
6 其它分類法
可分為解理、準解理、韌窩、滑移分離、沿晶及疲勞等多種斷裂。
按應力狀態分類,可分為靜載斷裂(拉伸、剪切、扭轉)、動載斷裂(沖擊斷裂、疲勞斷裂)等。
按斷裂環境分類,可分為低溫斷裂、中溫斷裂、高溫斷裂、腐蝕斷裂、氫脆及液態金屬致脆斷裂等。
按斷裂所需能量分類,可分為高能、中能及低能斷裂等三類。
按斷裂速度分類,可分為快速、慢速以及延遲斷裂三類。
按斷裂形成過程分類,可分為工藝性斷裂和服役性斷裂。
過載斷裂的宏觀斷口三要素
在金屬光滑圓試樣室溫拉伸或沖擊斷口上,通常可分為三個宏觀特征區,即如圖所示的纖維區、放射區和剪切唇區。
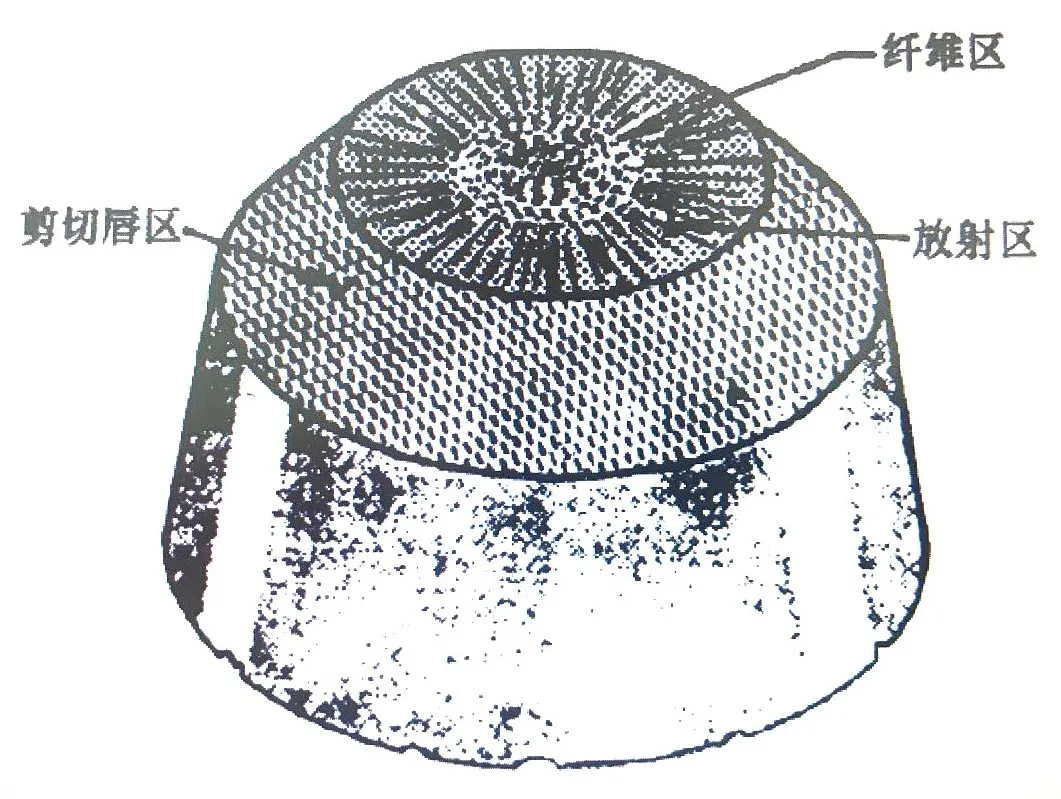
圖3光滑圓試樣拉伸斷口三要素示意圖
使用斷口三要素的應用案例:圖4
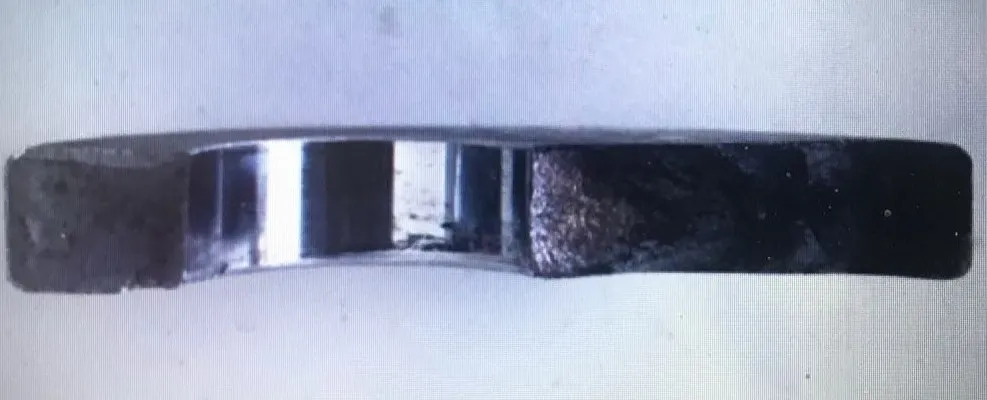
圖4某飛機前起落架斷裂耳片主、次兩個斷口
某型飛機起落架進行疲勞試驗的過程中,試驗耳片發生早期斷裂。前起落架斷裂耳片有兩個斷面剪切唇、放射區的人字紋特征明顯。
斷裂失效分析
金屬斷裂的微觀機理與典型形貌
工程材料的顯微結構都比較復雜,特定的顯微結構在特定的外界條件下有特定的斷裂物理機制和微觀形貌特征。
穿晶韌窩斷裂
韌窩是金屬延性斷裂的主要微觀特征。韌窩又稱作迭波、孔坑、微孔、微坑等。韌窩是材料在微區范圍內塑性變形產生的顯微空洞,經形核、長大、聚集,最后相互連接而導致斷裂后,在斷口表面所留下的痕跡。雖然韌窩是延性斷裂的微觀特征,但不能僅僅據此就作出斷裂屬延性斷裂的結論。
1 韌窩的形成
韌窩形成的機理比較復雜,大致可分為顯微空洞的形核、顯微空洞的長大和顯微空洞的聚集三個階段。
2 韌窩的形狀韌窩的形狀
韌窩的形狀主要取決于所受的應力狀態,最基本的韌窩形狀有等軸韌窩、撕裂韌窩和剪切韌窩三種。
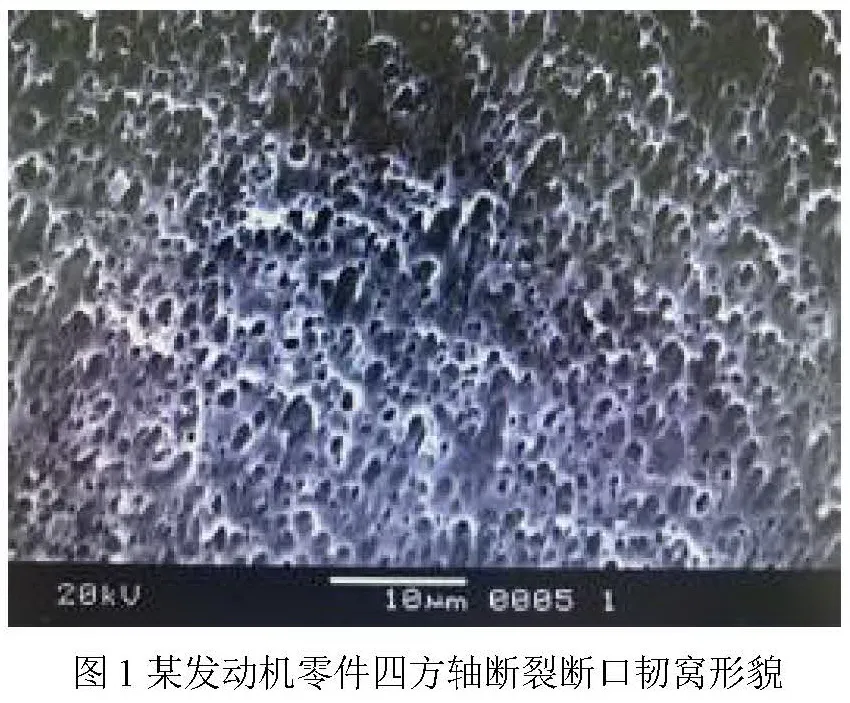

滑移分離
金屬斷裂過程均起始于變形。金屬的塑性變形方式主要有滑移、孿生、晶界滑動和擴散性蠕變四種。孿生一般在低溫下才起作用;在高溫下,晶界滑動和擴散性蠕變方式較為重要。而在常溫下,主要的變形方式是滑移。過量的滑移變形出現滑移分離,其微觀形貌有滑移臺階、蛇形花樣、漣波等。晶體材料的滑移面與晶體表面的交線稱為滑移線。滑移部分的晶體與晶體表面形成的臺階稱為滑移臺階。由這些數目不等的滑移線或滑移臺階組成的條帶稱為滑移帶。
滑移分離斷口形貌
滑移分離的基本特征:斷面傾斜,呈45°角;斷口附近有明顯的塑性變形,滑移分離是在平面應力狀態下進行的。滑移分離的主要微觀特征是滑移線或滑移帶、蛇形花樣、漣波花樣、延伸區。
蛇形花樣,多晶體材料受到較大的塑形變形產生交滑移,導致滑移面分離,形成起伏彎曲的條紋,通常稱為蛇形滑移花樣。
若變形程度加劇,則蛇形滑移花樣因變形而平滑化,形成漣波花樣。
如若繼續變形,漣波花樣也將進一步平坦化,在斷口上留下了沒有什么特殊形貌的平坦區,稱為延伸區。
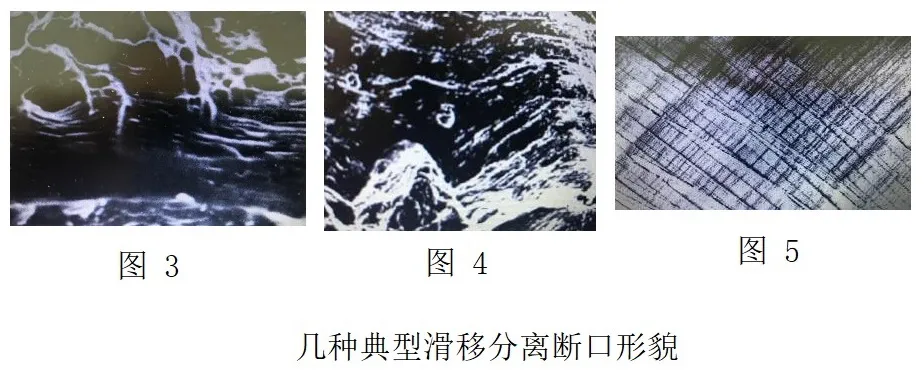
解理斷裂
解理斷裂是金屬在正應力作用下,由于原子結合鍵的破壞而造成的沿一定的晶體學平面(即解理面)快速分離的過程。解理斷裂是脆性斷裂的一種機理,屬于脆性斷裂,但并不是脆斷的同義語,有時解理可以伴有一定的微觀塑性變形。解理面一般是表面能量最小的晶面。面心立方晶系的金屬及合金,在一般情況下,不發生解理斷裂。
解理斷裂的形貌特征
典型的解理斷口微觀形貌有以下重要特征:解理臺階、河流花樣、“舌”狀花樣、魚骨狀花樣、扇形花樣等。
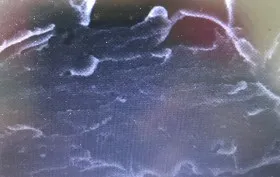
圖6舌狀花樣
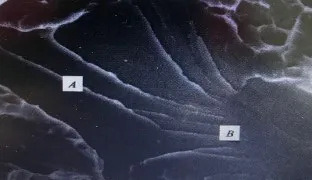
圖7 典型的解理斷口形貌特征 A臺階 B河流花樣
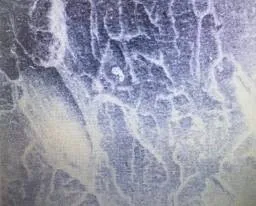
圖8解理扇形花樣
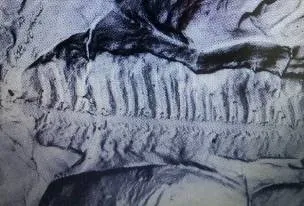
圖9魚骨狀花樣
某設備裝配脫板螺母后發現有多個該型螺母在橢圓形收口處存在細小裂紋。裂紋附近未觀察到塑性變形痕跡,裂紋較平直,由此說明裂紋開裂為脆性開裂。
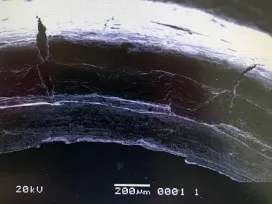
圖10裂紋形態
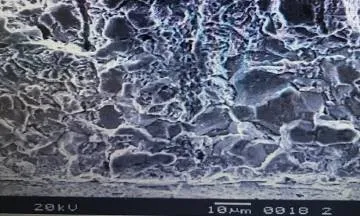
圖11裂紋斷口區域為解理+沿晶斷裂的脆性斷裂特征
準解理斷裂
是介于解理斷裂和韌窩斷裂之間的一種過渡斷裂形式。首先在不同部位,同時產生許多解理裂紋核,然后按解理方式擴展成解理小刻面,最后以塑性方式撕裂,與相鄰的解理小刻面相連,形成撕裂棱。
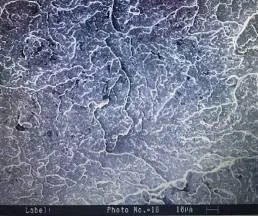
圖12某設備十字槽扁圓頭螺釘斷口準解理斷面形貌
準解理斷口宏觀形貌比較平整。基本上無宏觀塑性或宏觀塑性變形較小,呈脆性特征。其微觀形貌有河流花樣、舌狀花樣及韌窩與撕裂棱等。
案例:某廠設備彈簧發生斷裂,斷口如圖呈準解理斷裂形貌。
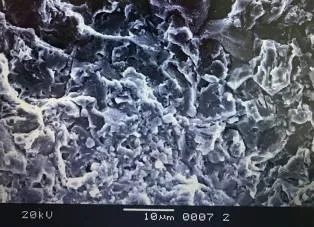
圖13準解理斷裂形貌
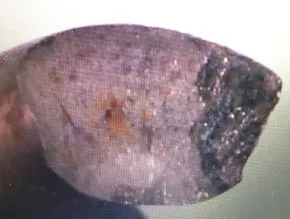
圖14彈簧斷口
沿晶斷裂
沿晶斷裂又稱晶間斷裂,它是多晶體沿不同取向的晶粒所形成的沿晶粒界面分離,即沿晶界發生的斷裂現象。
按斷面的微觀形貌,通常可將沿晶斷裂分為兩類:沿晶韌窩斷裂和沿晶脆性斷裂。
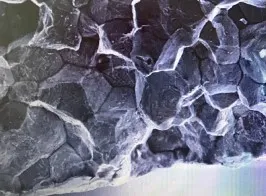
圖15沿晶脆性斷裂
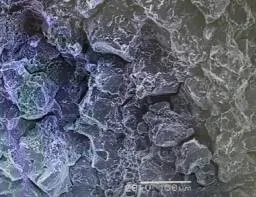
圖16沿晶韌窩斷裂
回火脆、氫脆、應力腐蝕、液體金屬致脆以及因過熱、過燒引起的脆斷斷口大都為沿晶脆性斷裂特征;而蠕變斷裂、某些高溫合金的室溫沖擊或拉伸斷口往往為沿晶韌窩形貌。
另外還有兩種情況也屬沿晶斷裂范疇。一是沿結合面發生的斷裂,如沿焊接結合面發生的斷裂;二是沿相界面發生的斷裂,如在兩相金屬中沿兩相的交界面發生的斷裂。
案例:
某發動機調試過程中,成功起動至慢車時,信號盤出“斷開空調”信息,停車進行檢查,發現空調系統中燃油—空氣散熱器出口處卡箍斷裂(位置如圖17)。
根據氫含量測定結果可知,鋼帶中的氫含量均遠遠高出一般鋼中對氫含量的要求值,可以判斷為氫脆導致沿晶斷裂。
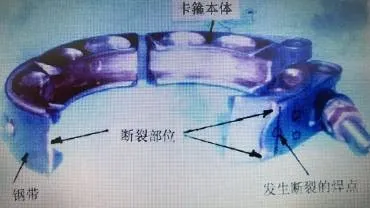
圖17
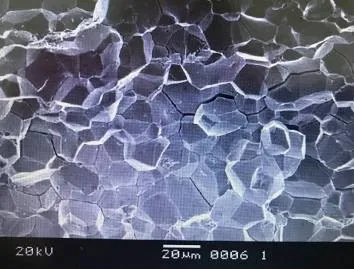
圖18基體區域的沿晶斷裂特征
疲勞斷裂
1 定義
疲勞斷裂是材料(或構件)在交變應力反復作用下發生的斷裂。
2 疲勞斷裂的危害性形狀
多數機件承受的應力是周期性變動的;
疲勞破壞表現為突然斷裂,斷裂前無顯著變形;
造成疲勞破壞時,循環交變應力中的最高應力一般遠低于靜載荷下材料的強度極限;
零件的疲勞斷裂不僅取決于材質,而且對零件的形狀、尺寸、表面狀態、使用條件、外界環境等非常敏感;
很大一部分機件承受彎曲扭轉應力。
3 疲勞斷裂過程
疲勞裂紋的萌生、穩定擴展及失穩斷裂三個階段。
4 疲勞裂紋的萌生
交變載荷產生局部滑移→滑移線變粗形成滑移帶→駐留滑移帶的形成→駐留滑移帶擠入槽和擠出峰的形成→萌生疲勞裂紋。
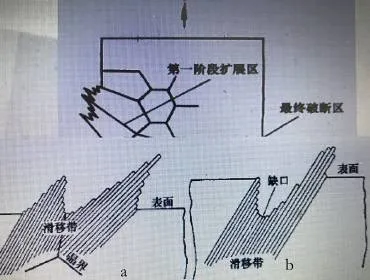
(a)在晶界附近起源 (b)在滑移帶的缺口處起源
圖19疲勞裂紋的萌生示意圖
5 疲勞裂紋穩定擴展的兩個階段
疲勞裂紋穩定擴展第一階段
與正應力呈45°,擴展深度很淺。
斷裂形貌特征:
√類解理小平面
√平行鋸齒狀斷面
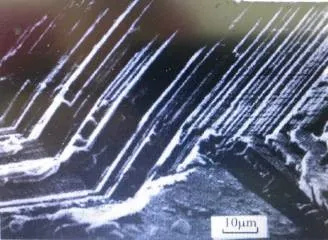
圖20葉片疲勞斷裂第一階段鋸齒狀斷面
疲勞裂紋穩定擴展第二階段
疲勞裂紋按第一階段方式擴展一定距離后,將改變方向,沿著與正應力相垂直的方向擴展。此時正應力對裂紋的擴展產生重大影響。這就是疲勞裂紋穩定擴展的第二階段,疲勞裂紋擴展第二階段斷面上最重要的顯微特征是疲勞條帶,又稱疲勞輝紋。
6 疲勞條帶的類型與形態
延性疲勞條帶(晶體學和非晶體學)、脆性疲勞條帶(晶體學和非晶體學)
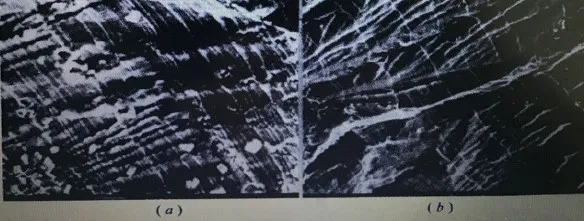
圖21 a.延性疲勞條帶 b.脆性疲勞條帶
案例:某蓄壓油箱疲勞裂紋
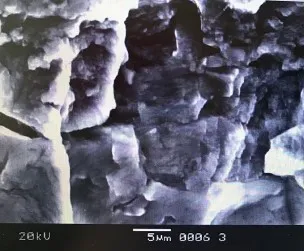
圖22 源區處疲勞條帶
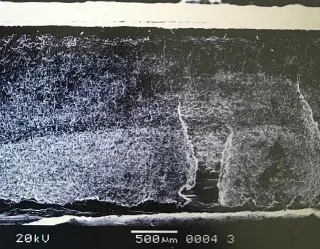
圖23 源區位置疲勞弧線
斷裂失效分析
疲勞斷裂
分類
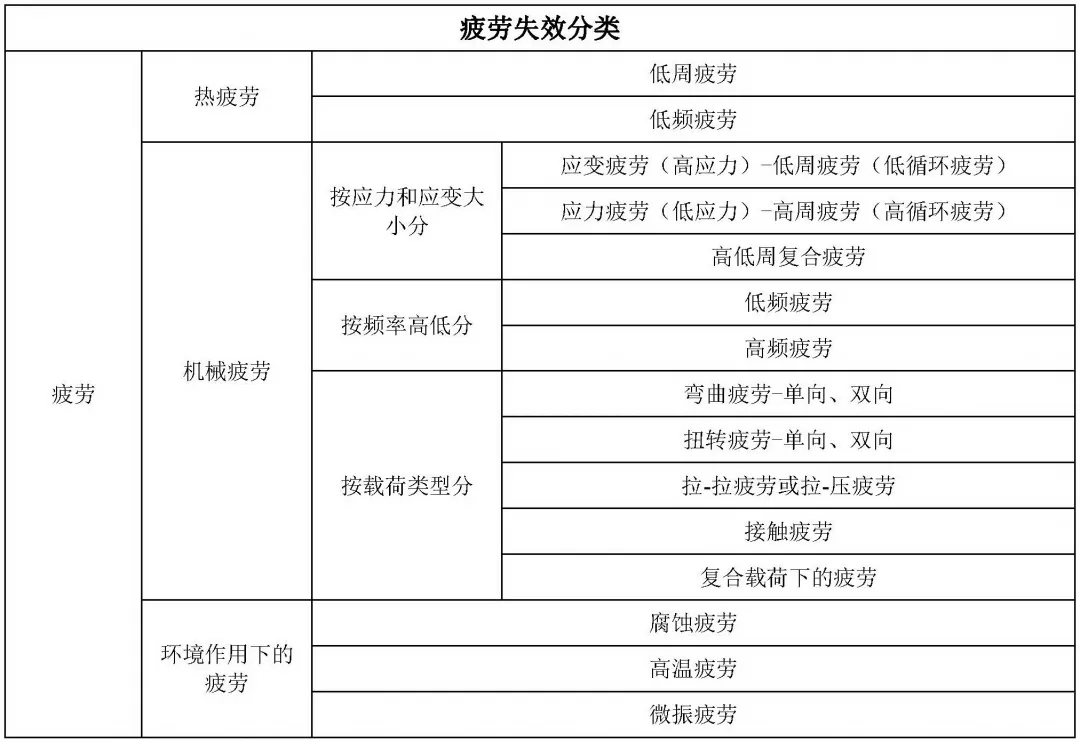
疲勞斷裂的宏觀分析
典型的疲勞斷口按照斷裂過程的先后有三個明顯的特征區,即疲勞源區、擴展區和瞬斷區。
01 源區的宏觀特征
氧化或腐蝕嚴重,顏色較深;
斷面平坦、光滑、細密,有些可見閃光小刻面;
有放射臺階或放射棱線;
向外發射疲勞弧線的中心。
02 擴展區的宏觀特征
斷面平坦、與主應力垂直,顏色介于源區和瞬斷區,最基本的特征是疲勞弧線,也稱海灘花樣或貝殼花樣。
03 瞬斷區的宏觀特征
與靜載拉伸斷口相近,瞬斷區面積的大小取決于載荷的大小、材料的性質環境介質等因素。
案例:某電氣控制盒固定腳焊縫附近斷裂,斷口可見疲勞弧線和源區的磨損特征,擴展較充分,瞬斷區面積較小,斷口具有典型的疲勞斷裂特征。
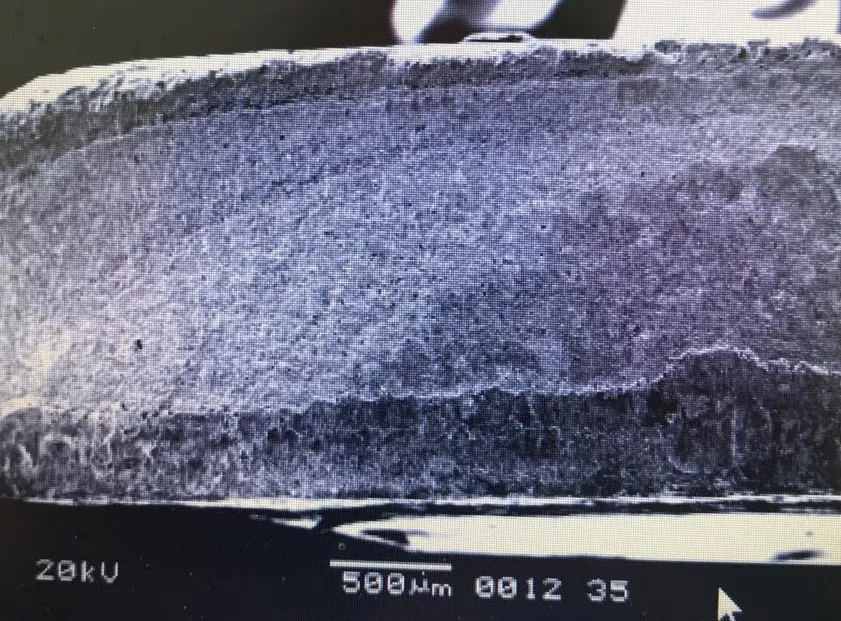
圖1 斷口疲勞弧線與源處的磨損

圖2 斷口宏觀形貌
疲勞斷口的微觀分析
疲勞斷裂的微觀分析一般包括以下內容:
01 源區的微觀分析
具體位置:多源疲勞:主源、次源;微觀形貌特征:加工及材質缺陷
02 擴展區的微觀分析
第一擴展區:有無疲勞條帶、韌窩、臺階二次裂紋等;
第二擴展區:有無疲勞條帶及疲勞條帶的性質。
03 瞬斷區的微觀分析(韌窩形態)
低周疲勞斷裂的判斷依據
01 宏觀特征
多源,且多為線狀;
瞬斷區面積大;
疲勞弧線間距大,穩定擴展區棱線粗、短;
斷口高差較大。
02 微觀特征
對低周疲勞,由于宏觀塑性變形較大,靜載斷裂機理就會出現在疲勞斷裂過程中,在斷口上出現各種靜載斷裂所產生的斷口形態。
案例:
某發動機的渦輪葉片和輪盤上多個榫齒出現了超過修理標準的裂紋,且裂紋部位基本上在第三齒,多數為單裂,少數為對裂,亦有鄰裂的情況。
斷口源區為穿晶滑移類解理斷裂形貌,呈多源特征,擴展區主要為扇形解理擴展形貌和疲勞條帶特征,為起始應力較大的以低周疲勞為主的疲勞開裂。

圖3 葉片槽位處裂紋斷口低倍

圖4 擴展區載荷變化較大的條帶特征
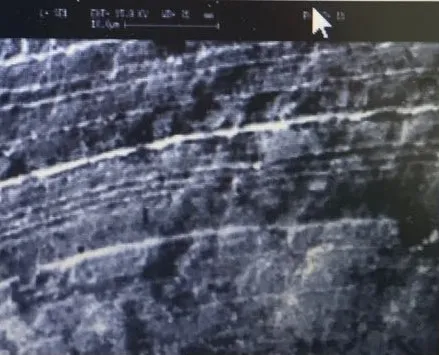
圖5 據源區較遠處條帶特征
腐蝕疲勞斷裂失效分析
腐蝕疲勞斷裂是在腐蝕環境與交應載荷協同、交互作用下發生的一種失效模式。
01 腐蝕疲勞的斷裂特征
斷口低倍呈現明顯的疲勞弧線;
源區和擴展區一般有腐蝕產物;
一般起源于表面腐蝕損傷處;
擴展區具有某些明顯的腐蝕特征,如腐蝕坑、泥紋花樣等;
穿晶解理脆性疲勞條帶是其重要的微觀特征;
若腐蝕損傷占主導地位,則斷口呈現穿晶與沿晶混合型;
當Kmax> KIscc,在頻率很低的情況下,其斷口呈現出穿晶解理與韌窩的混合特征。
02 影響腐蝕疲勞斷裂的因素
環境、受力狀態、材質
03 腐蝕疲勞斷裂失效分析的判斷依據
交變應力和腐蝕環境;
斷面灰暗、無金屬光澤,有明顯疲勞弧線;
有腐蝕產物和腐蝕損傷的痕跡;
疲勞條帶多有脆性解理特征。
熱疲勞斷裂失效分析
零件在沒有外加載荷的情況下,由于工作溫度的反復變化而導致的開裂叫熱疲勞。
熱疲勞斷口的形貌特征
01 熱疲勞裂紋易產生于應變集中處;
02 光滑表面零件,則易產生于溫度高,溫差大的部位,可發現熱疲勞裂紋發展極不規則,裂紋多為沿晶開裂;
03 微觀形貌為韌窩和疲勞條帶;
04 熱疲勞裂紋附近,顯微硬度降低。
斷裂失效分析
沿晶斷裂
金屬零件的沿晶斷裂大都歸入脆性斷裂失效范疇,主要包括熱脆、低溫脆、銅脆、回火脆、氫脆、應力腐蝕致脆、液態金屬致脆等。
沿晶斷裂失效模式的判別
01 金屬零件沿晶斷裂失效的主要宏觀特征是:
斷口的兩匹配面很好地吻合一致,斷口附近沒有或極少有塑性變形,絕大部分斷面結構粗糙呈顆粒狀,稱為“巖石狀”斷口、斷面平齊,邊緣無剪切唇、一般與主應力軸垂直;
斷面無纖維狀和放射狀特征,一般看不出加載速度影響,且宏觀上難以判明裂紋擴展方向;
02 沿晶斷裂的典型微觀特征是:
沿晶分離,晶界面光滑無特征,呈冰糖塊狀,或者顯示撕裂痕和細小的韌窩花樣。
沿晶斷裂失效原因分析
產生沿晶斷裂的原因除環境介質作用外還有以下3種情況:
01 晶界沉淀相引起的沿晶斷裂
由晶界沉淀相所造成的沿晶斷裂多是沿晶韌窩斷裂。在晶界,沉淀相總是以分散粒子的形式存在,并且不連續;
合金的成分、熱加工中的加熱溫度、冷卻速度、熱處理制度等都有可能引起第二相在晶界析出,弱化晶界,引起沿晶韌窩斷裂;
引起沿晶韌窩斷裂的主要因素有:微量元素引起第二相質點沿晶析出和緩冷引起第二相質點沿晶析出。
02 雜質元素在晶界偏聚引起的沿晶斷裂
沿晶斷裂的另一個主要原因是某些雜質元素在晶界上聚集,降低了晶界的聚合能,最常見的脆性雜質元素有Si、Ge、Sn、P、As、Sb、S、Se、Te等;
包括第一類回火脆引起的沿晶斷裂和第二類回火脆引起的沿晶斷裂。
03 金屬過熱、過燒引起的沿晶斷裂
金屬零件在熱加工過程中,或使用過程中在過熱、過燒溫度區間內長期或短期停留,均會引起零件整件、或局部過熱與過燒,從而在應力作用下導致沿晶脆性斷裂;
過熱、過燒斷口宏觀上呈粗大的顆粒狀,無明顯的斷裂起源特征,斷口附近無明顯變形,過燒斷口無金屬光澤。過熱斷口微觀形貌為晶粒粗大,晶界分離面上有細小的韌窩。過燒斷口微觀形貌為晶粒粗大,晶界粗而深,晶界分離面上有氧化膜、熔化的孔洞等特征。
故障概述
某活塞桿進行電鍍后發現活塞桿表面中間部位存在裂紋。該活塞桿的工藝過程為:管材→機加→焊接→探傷→熱處理→校正→機加→磁粉探傷→表面電鍍處理(鍍鉻)→表面精加工→交工。一根活塞桿在外表面去鍍后發現表面存在裂紋,另一根在外表面二次電鍍后發現表面存在裂紋。活塞桿所用材料為30 CrMnSiA。
◆宏觀觀察
斷口表面為黃褐色,銹蝕較嚴重。可見明顯的從外表面向內表面的放射棱線特征。
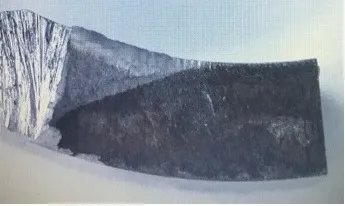
◆微觀觀察
裂紋起始于外表面,線源。源區局部為沿晶斷裂特征,未見明顯的冶金缺陷。
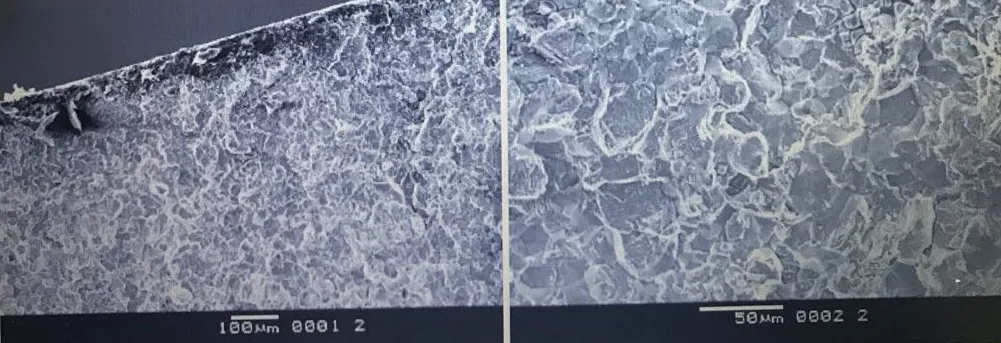
源區另一處放大后的形貌主要為龜裂特征,為典型的腐蝕產物特征;擴展區主要為沿晶斷裂特征,存在大量的二次裂紋。
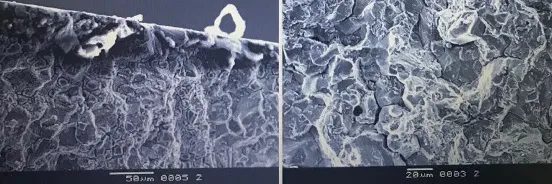
◆能譜分析
對活塞桿斷口進行微區能譜分析,除二次電鍍活塞源區沿晶處存在少量的CL元素外,兩個斷口上發生龜裂及裂紋擴展區均未發現腐蝕性元素存在。另外,整個斷口上的Cr元素含量均高于鋼自身的Cr含量(0.8~1.10wt%),且源區的Cr含量高于擴展區的Cr含量,說明斷口受到了鍍鉻與去鉻工藝的污染,裂紋應該在鍍鉻過程中已經產生。
◆金相組織檢查
在斷口附近制取試樣,經腐蝕后在金相顯微鏡下觀察,為回火馬氏體組織,組織未見異常。
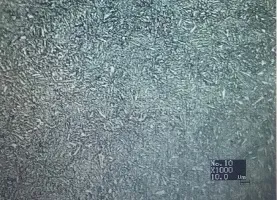
◆硬度檢測:
平行于斷口方向截取試樣進行洛氏硬度檢測,結果表
明活塞桿的硬度符合相關技術要求。
◆氫含量測定
在兩個活塞桿裂紋打開斷口附近截取試樣進行氫含量測試,結果表明活塞桿的氫含量均低于0.1ppm
◆結果分析與討論
★根據斷口觀察可知,兩個活塞桿裂紋打開的斷口均為典型的沿晶脆性斷裂。
★能譜分析結果表明,兩個活塞桿表面裂紋是在鍍鉻過程中產生的。
★斷口觀察源區未見明顯的冶金缺陷,金相組織檢查組織未見異常,說明裂紋的產生與材料本身質量無關。
★材料產生沿晶脆性斷裂有三種可能原因:氫脆、液態金屬致脆與應力腐蝕。根據氫含量測定可以看出,活塞桿氫含量均低于0.1ppm,30 CrMnSiA鋼自身的強度不是很高,對氫脆不是很敏感,可以排除氫脆的可能;另外斷口觀察表明,斷口上未見明顯的低熔點金屬,活塞桿在制備過程中也未曾與液態金屬接觸,所以也可以排除液態金屬致脆的可能;兩個活塞桿裂紋打開的斷口觀察表明,源區存在大量的龜裂特征,為典型的腐蝕特征,可以確定兩個活塞桿表面裂紋是由于應力腐蝕所致。
★活塞桿采用30CrMnSiA制造,該材料對應力腐蝕敏感,在潮濕的空氣中或腐蝕介質環境下極易產生應力腐蝕。斷口表面存在大量的龜裂特征,說明其受到了腐蝕介質的作用。斷口表面能譜分析只有源區局部存在腐蝕介質元素,可能是由于斷口表面銹蝕較嚴重,影響了能譜分析的結果。
◆結論
裂紋位于活塞桿表面的中間部位,在活塞桿校正后此處存在較大的殘余應力,在去應力退火時殘余應力沒有完全消除,在隨后的電鍍過程中發生了應力腐蝕。
◆故障概述
某廠生產的搖臂軸在裝配后放置一段時間發現搖臂軸端部螺紋根部斷裂。搖臂軸材料為20 CrMnTi。基本的機械加工及熱處理過程為:鍛造→粗加工→滲碳+直接淬火→局部(螺紋部分)高頻回火→精磨→裝配。
◆宏觀觀察
無明顯宏觀塑性變形,斷口比較平齊,斷面較粗糙,斷口局部存在明顯的擦傷形貌。斷口上存在一個明顯的弧形凸起臺階特征,將斷口分為兩部分。斷口較平坦,裂紋從外表面呈線性起源,源區較平坦,呈黑色,與擴展區相比氧化較嚴重。從整個斷口的宏觀特征來看,斷裂是從兩部分區域外表面同時呈線性起源,并向心部擴展,最終兩部分裂紋在中心附近區域交匯,形成斷口上弧形的凸起特征。
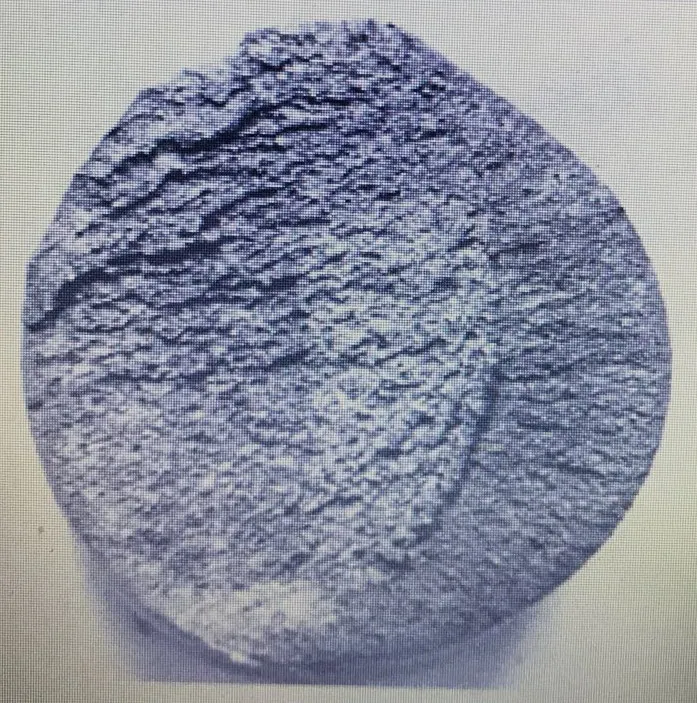
◆微觀觀察
源區:裂紋均是起源于零件表層以下約幾十個微米的次表面,呈線性起源特征,源區均呈典型的冰糖狀沿晶斷裂特征,晶面平坦,沒有附著物,并且局部區域存在雞爪形的撕裂棱線,二次裂紋較少。

擴展區微觀形貌也均以沿晶斷裂特征為主;交界區域附近斷口存在少量的韌窩,并且可見二次裂紋特征。
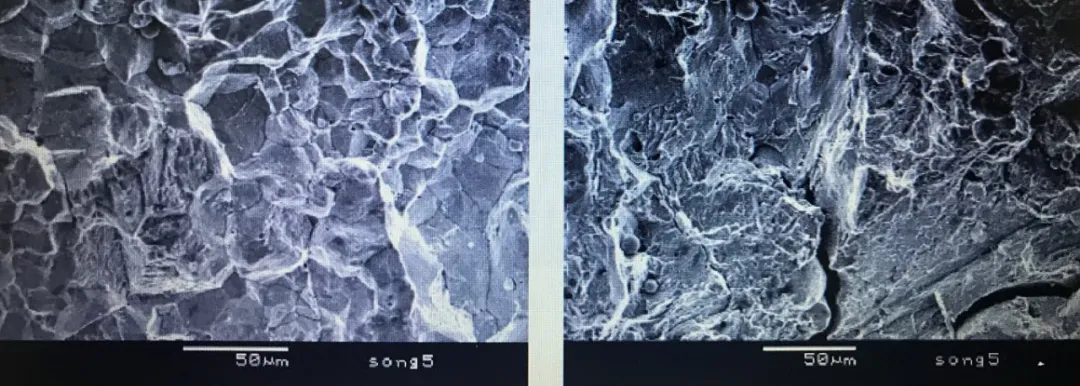
◆能譜成分分析
結果表明斷口表面無腐蝕性元素,斷口上也未發現冶金等材質缺陷。
◆硬度測定
斷口處硬度值在HRC35左右;斷裂區域硬度值較高,與其組織有關。
◆氫含量測定
搖臂軸螺紋段的氫元素分布比較均勻,含氫量較高5ppm。
◆化學成分分析
符合GB/T3077的要求
◆分析與討論
搖臂軸的化學成分符合要求,硬度值也符合零件設計要求,且搖臂軸斷裂部位未發現材質缺陷,可以判斷此次搖臂軸的斷裂與材質無關。在搖臂軸斷口上沒有發現有腐蝕產物以及腐蝕性元素,也可以排除是由于應力腐蝕而造成搖臂軸斷裂的可能。
●搖臂軸宏觀斷口無明顯塑性變形,斷口比較平齊,有放射花樣;
●微觀斷口沿晶分離,晶粒輪廓鮮明,晶界面上伴有變形線(雞爪痕),二次裂紋較少,撕裂棱較多;
●失效部位由于結構、裝配以及加工刀痕等因素,存在應力集中,斷裂源位于次表面;
●工作應力主要是靜拉伸應力;
●搖臂軸斷裂部位硬度偏高,造成強度偏高,對氫脆的敏感性增加;
●搖臂軸斷口氫含量基本在5×10-6,達到了產生氫脆斷裂的氫含量范圍。
符合氫脆判定條件①、③、④、⑤、⑥、⑦
判斷依據:
①宏觀斷口表面潔凈,無腐蝕產物,斷口平齊,有放射花樣。氫脆裂區呈結晶顆粒狀亮灰色;
②顯微裂縫呈斷續而曲折的鋸齒狀,裂紋一般不分叉;
③微觀斷口沿晶分離,晶粒輪廊鮮明,晶界面上伴有變形線(發紋線或雞爪痕),二次裂紋較少,撕裂棱或韌窩較多;
④失效部位應力集中嚴重,氫脆斷裂源位于表面;應力集中小,氫脆斷裂源位于次表面;
⑤失效件存在工作應力主要是靜拉應力,特別是三向靜拉應力;
⑥氫脆斷鮮明的臨界應力極限隨著材料強度的升高而急劇下降;一般硬度低于HRC=22時不發生氫脆斷裂而產生鼓泡。
⑦一般鋼中的含氫量在(5-10)×10-6以上時就會產生氫致裂紋,但對高強鋼,即使鋼中含氫量在1×10-6以下,由于應力的作用,處在點陣間隙中的氫原子會通過擴散集中于缺口所產生的應力集中處,氫原子與位錯的交互作用,使位錯線被釘扎住,不能再自由活動,從而使基體變脆。
發生氫脆斷裂必須同時具備三個條件:一定的氫含量,對氫脆敏感的組織,一定的拉應力。
▲搖臂軸的氫脆斷裂氫的來源于滲碳熱處理過程中,是由于甲醇和丙酮在高溫下分解形成氫原子,且氫在金屬中的溶解度隨著溫度而變化,當溫度降低或組織轉變,氫的溶解度由大變小時,氫便從固溶體中析出,而由于冷卻速度較快,就會殘留在金屬材料基體中。
▲通過金相組織觀察可知,發生斷裂的位置仍為馬氏體組織,而且其硬度和強度均較高,而隨著強度的升高材料對氫脆斷裂的敏感性必然增大,因此,從這個角度說搖臂軸也具備了發生氫脆斷裂的條件。
▲搖臂軸斷裂位置正好位于螺紋與花鍵的圓弧過渡處,該處應力集中較大,無論是加工過程中的殘余應力還是裝配時的裝配應力都會在該處產生應力集中,使零件實際受力增大,而且零件裝配應力在該處也屬于拉應力
◆改進措施
●降低材料內部的氫含量:加大除氫時間改進滲碳工藝,如滲碳后空冷,再重新進行加熱淬火,這樣滲碳時產生的氫就會在淬火加熱時從材料內部析出,這樣改進后零件材料內部的氫含量會大大降低,從而也會使其發生氫脆的可能性減小。
●減小應力集中:從零件加工角度考慮,應盡量提高加工精度,從而降低該處的應力集中,這樣也會大大降低該處發生氫脆斷裂的幾率。
●應從設計和生產兩個方面進行綜合治理,一方面在工藝設計上進行改進,另一方面加強生產過程的質量控制。
免責聲明:本網站所轉載的文字、圖片與視頻資料版權歸原創作者所有,如果涉及侵權,請第一時間聯系本網刪除。
相關文章
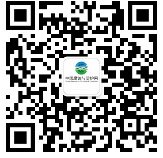
官方微信
《中國腐蝕與防護網電子期刊》征訂啟事
- 投稿聯系:編輯部
- 電話:010-62316606-806
- 郵箱:fsfhzy666@163.com
- 中國腐蝕與防護網官方QQ群:140808414
點擊排行
PPT新聞
“海洋金屬”——鈦合金在艦船的
點擊數:7130
腐蝕與“海上絲綢之路”
點擊數:5741