摘要
在2A12鋁合金基體上制備了無鉻鋯基轉化膜,對鋯基轉化膜的耐腐蝕性能、前處理及成膜過程中的顯微形貌演變和膜層成分進行了表征,重點探究了第二相對成膜過程的影響。結果表明,基體表面第二相對鋯基轉化膜成膜的影響主要體現在三方面:第一,堿洗和酸洗前處理后,合金表面第二相和大量蝕坑的存在造成基體表面凹凸不平;第二,成膜過程中,第二相的存在不利于轉化膜顆粒的均勻形核和長大;第三,成膜完成后,第二相被腐蝕破壞,嚴重影響膜層的致密性和均勻性。
關鍵詞: 轉化膜; 鋯基; 鋁合金; 腐蝕; 第二相
鋁合金具有密度低、比強度高、導電性和導熱性良好等一系列優點,廣泛應用于航空航天、交通運輸等各個領域。但當其處于含Cl-的環境中時易發生點蝕、晶間腐蝕和剝落腐蝕等局部腐蝕[1-3]。在鋁合金表面噴涂有機涂層是鋁合金眾多防護技術中應用最廣泛的方法,該方法使鋁合金與腐蝕介質之間形成物理阻擋層從而使基體免遭腐蝕破壞。然而,鋁合金表面氧化膜的存在不利于其與有機涂層的結合,導致有機涂層與鋁合金基體的界面結合力較差[4]。因此,鋁合金的表面改性成為了鋁合金防護的必然選擇。鋁合金的表面改性方法主要有化學轉化、陽極氧化、微弧氧化等[5],其中化學轉化膜技術具有成本低、操作簡單、適用范圍廣、可顯著提高與有機涂層的結合力等優點,已成為鋁合金涂裝前處理應用最廣泛的工藝[6]。鋁合金的化學轉化膜主要包括鉻酸鹽轉化膜[7-15]、稀土轉化膜[16-18]、三價鉻酸鹽轉化膜[19-22]、鋯/鈦基轉化膜[23-34]等。其中,以鉻酸鹽轉化膜的耐蝕性最好,但Cr6+的使用導致的環境和健康問題尤為嚴重,促使大量研究致力于開發可替代鉻酸鹽的化學轉化膜技術。
鋯/鈦基轉化膜目前已成功實現工業化應用,是最具希望代替鉻酸鹽轉化膜的處理工藝之一。影響成膜的因素眾多,例如轉化液的成分、轉化條件、鋁合金基體自身的表/界面狀態等[9,10,16,21-24]。隨著對化學轉化膜研究的不斷深入,針對轉化液成分、轉化條件和前處理過程的研究已非常廣泛[9-11,14-16,25-30],然而針對基體自身顯微組織對成膜過程影響的研究相對較少。
2系鋁合金是航空領域應用最多的輕合金結構材料,近年來有很多針對2系鋁合金表面轉化膜的研究[8-11,17,20,21,25,26,31-33],Coloma等[25]成功在2024鋁合金表面制備了Zr/Ti/Mn/Mo無鉻轉化膜,研究發現,該化學轉化膜雖然不能達到嚴格的工程化要求,但能明顯地提升鋁合金耐蝕性。Li等[31,32]在2024鋁合金表面制備了無鉻Zr/Zn轉化膜 (NCP),發現NCP對鋁合金基體幾乎沒有防腐蝕作用,同時評價了工業無鉻鋯/鈦基轉化膜Bonderite M-NT 5200在2024鋁合金上的應用,研究發現,該轉化膜對鋁合金的防護作用不大。不難發現,公開報道的2系鋁合金表面無鉻轉化膜的性能不夠理想[17,25,31-33],這無疑與其自身的顯微組織結構密切相關,找出成膜性能差的原因是解決這一問題的關鍵。
本文在2A12鋁合金上制備了無鉻鋯基轉化膜(ZrCC),重點探究鋁合金基體顯微組織結構對鋯基轉化膜成膜過程及性能的影響。通過動電位極化曲線和電化學阻抗譜評價耐蝕性能,利用掃描電子顯微鏡 (SEM) 表征前處理及成膜過程中鋁合金基體的顯微形貌變化,采用X射線光電子能譜 (XPS) 對獲得轉化膜的成分進行表征,以期能夠找出2系鋁合金上的成膜難點,為在2系鋁合金上開發高性能無鉻轉化膜奠定基礎。
1 實驗方法
基體材料采用固溶處理和自然時效后的2A12-T4鋁合金板材,其化學成分為 (質量分數,%):Si 0.085,Fe 0.29,Mn 0.61,Cu 4.51,Mg 1.51,Ni 0.005,Ti 0.035,Zn 0.14,Al為余量。試樣尺寸為20 mm×20 mm×2 mm,采用SiC砂紙依次將試樣打磨至2000#。ZrCC的制備流程包括除油、堿洗、酸洗和成膜4個過程。室溫下,將打磨好的試樣放入丙酮溶液超聲除油5 min,去離子水沖洗。將沖洗好的試樣放入0.5 mol/L的NaOH溶液中堿洗300 s,去離子水沖洗表面殘留堿液,隨后在10% (體積分數) HNO3+10% (體積分數) HF溶液中酸洗60 s,然后用去離子水沖洗表面。最后,將前處理后的試樣放入 (30±1) ℃轉化液中成膜1800 s,成膜后用去離子水沖洗試樣表面,室溫下老化12 h[27]。轉化液成分為:NaH2PO4 15 g/L,K2ZrF6 0.5 g/L,H3PO4 1 ml/L,NaF 5 g/L。
采用CHI660e電化學工作站分別對2A12鋁合金基體和ZrCC進行了動電位極化曲線測試和電化學阻抗譜測試,采用經典的三電極測試體系,待測樣品為工作電極,鉑電極為對電極,飽和甘汞電極 (SCE) 為參比電極,電解質溶液為3.5% (質量分數) NaCl溶液,在室溫下進行測試。
動電位極化曲線測試前先進行10 min的開路電位掃描,待電位穩定后進行動電位掃描,掃描區間從相對開路電位-300 mV開始,到陽極電流密度為1 mA/cm2時結束,掃描速度為0.333 mV/s。電化學阻抗譜測試前同樣先進行10 min的開路電位掃描,待電位穩定后進行測試,頻率測試范圍105~10-2 Hz,擾動振幅10 mV,采用Zsim Demo對得到的EIS數據進行擬合分析。
利用MIRA 3 型掃描電鏡 (SEM) 及自帶的能量色散X射線光譜 (EDS) 對2A12鋁合金基體、酸洗、堿洗和成膜過程中的顯微形貌和成分進行分析,利用ESCAIAB250型X射線光電子能譜 (XPS) 對成膜后膜層中各元素的具體存在狀態進行表征。
2 結果與討論
2.1 ZrCC對2A12鋁合金耐蝕性能的影響
圖1為鋁合金基體與ZrCC樣品在3.5%NaCl溶液中的動電位極化曲線。可以看出,2A12鋁合金基體和ZrCC樣品陽極均呈現活性溶解的特征,雖然成膜后鋁合金陽極受到了輕微的抑制,但陰極卻受到了極大的促進,導致成膜后的自腐蝕電流明顯增加。
圖1 2A12鋁合金基體及ZrCC的極化曲線
圖2為2A12鋁合金基體與ZrCC樣品的電化學阻抗譜圖。從Nyquist圖中可以看出 (圖2a),ZrCC樣品的容抗弧明顯小于基體,Bold圖 (圖2b) 顯示,2A12鋁合金基體和ZrCC均顯示兩個時間常數特征,同時考慮到ZrCC樣品表面轉化膜以及鋁合金基體表面氧化膜的存在,選用圖3的等效電路對兩者的數據進行了擬合,其中Rs為溶液電阻,Qdl為雙電層電容,Rct為電荷轉移電阻。Qf、Rf針對不同樣品所代表的物理意義有所不同。對于2A12鋁合金基體來說,Qf、Rf分別代表基體自身氧化膜的膜層電容和膜層電阻;對于ZrCC來說,Qf、Rf分別代表ZrCC的膜層電容和膜層電阻,擬合結果見表1。可以明顯看出,ZrCC樣品的膜層電阻Rf和電荷轉移電阻Rct均明顯小于鋁合金基體表面氧化膜,說明經鋯基轉化處理后的2A12鋁合金在3.5%NaCl溶液中較基體反而更容易發生腐蝕。
圖2 2A12鋁合金基體與ZrCC電化學阻抗譜
圖3 2A12鋁合金基體與ZrCC的擬合電路
表1 2A12鋁合金基體與鋯基轉化膜的擬合參數結果
從動電位極化曲線和電化學阻抗譜的結果可以看出,此種制備工藝在2A12鋁合金上制備出的ZrCC不僅未對基體提供防護,反而耐腐蝕性能相比于基體有所降低。造成這種結果的原因是2A12鋁合金自身的顯微組織結構嚴重影響了成膜過程,探究其中的原因為工藝的進一步改進至關重要。
2.2 前處理過程中2A12鋁合金基體的形貌演變
圖4為2A12鋁合金基體的顯微形貌及其EDS面掃描圖像。圖4a顯示鋁合金基體表面密集分布著形狀不規則的第二相,從圖4b~f中可以識別出,表面的第二相主要分為兩種富銅相,一種為Al(Cu,Mg) 相,另一種為Al(Cu,Fe,Mn) 相[1-4],隨機分布在基體表面,且Al(Cu,Mg) 相的數量明顯多于Al(Cu,Fe,Mn) 相。
圖4 2A12鋁合金SEM像及EDS面掃圖像
圖5為2A12鋁合金在前處理過程中堿洗和酸洗后的SEM形貌。圖5a顯示,經過堿洗之后,鋁合金基體表面部分第二相發生了明顯的腐蝕,由大塊顆粒被腐蝕成若干小塊。從圖5b可以看出,經酸洗后,基體表面第二相的數量明顯減少,并出現了大量蝕坑,蝕坑的產生一方面是由于第二相的脫落造成,另一方面是由于基體被酸洗溶液腐蝕造成的。對經過酸洗處理后樣品不同位置處的成分進行了EDS測試,如圖6所示,經過堿洗和酸洗后,2A12鋁合金基體表面氧化膜被破壞,但仍有部分Al(Cu,Mg) 相和Al (Cu,Fe,Mn) 相的殘留。
圖5 前處理過程中SEM像
圖6 酸洗后不同位置EDS結果
2.3 成膜過程中2A12鋁合金基體的形貌演變
前處理完成后,2A12鋁合金在ZrCC成膜過程中的開路電位變化如圖7所示。根據圖7開路電位的變化,可以將2A12鋁合金的成膜過程分成3個階段。第1個階段0~175 s (區域I),開路電路迅速上升;第2個階段175~1030 s (區域II),開路電路迅速下降后趨于平穩;第3個階段175~1030 s (區域III),開路電路平穩階段。
圖7 2A12鋁合金在鋯基轉化液中OCP隨浸泡時間的變化曲線
選取圖7 OCP曲線中典型的時間節點進行表面微觀形貌表征,如圖8所示。在成膜時間為75 s時,大量顆粒在鋁合金表面迅速形核長大,呈結節狀,僅有少部分區域未被覆蓋 (圖8a1和a2),隨著成膜時間增加至175 s,2A12鋁合金基體表面除第二相外,表面被結節狀顆粒完全覆蓋,顆粒尺寸較小約為1 μm,且第二相周圍的顆粒尺寸小于其他區域 (圖8b1和b2)。成膜進入到第二階段270 s時,轉化膜顆粒繼續堆垛成長 (圖8c1),第二相附近的顆粒尺寸約為500 nm,明顯小于其他位置處,隨著與第二相之間距離的增加,顆粒尺寸明顯增大,最大顆粒尺寸約為4 μm。同時,大顆粒頂部有著小粒子的生成,如圖8c2圓形標記所示。隨著成膜時間增加至1030 s,大顆粒頂部生成的小顆粒數量增加并且有所長大,如圖8d2中標記所示,第二相周圍的顆粒尺寸依然明顯小于其他區域。直到成膜1800 s時,可見鋁合金表面轉化膜表面并不均勻,第二相已被酸性轉化液完全腐蝕破壞,第二相附近的轉化膜顆粒尺寸大小不一 (圖8e1),前處理后留下的蝕坑依然存在 (圖8e2)。
圖8 2A12鋁合金ZrCC在轉化液中不同成膜時間的SEM形貌
2.4 顯微組織對ZrCC結構和成分的影響
圖9為2A12鋁合金成膜之后的表面和截面形貌,從表面形貌 (圖9a) 中可以看出,ZrCC表面凹凸不平,存在大量第二相顆粒以及大小不一的凹坑,同時轉化膜顆粒大小不一,靠近第二相的顆粒尺寸明顯小于無第二相處轉化膜顆粒尺寸,轉化膜均勻性較差。由截面形貌 (圖9b) 可知,鋁合金表面凹凸不平,第二相處存在凹坑,這是由前處理刻蝕后產生的。在凹凸不平的鋁合金表面覆蓋了一層1~1.5 μm厚度不均勻的膜層。表2為圖9中標記為“4”、“5”和“6”位置的EDS分析,可見轉化膜主要組成元素為:F、Na和Al,第二相處的膜層還存在Cu,同時膜層還存在少量的Zr、P和Mg。
圖9 成膜后的SEM顯微形貌
表2 ZrCC表面與截面EDS分析結果
圖10為2A12鋁合金ZrCC的XPS全譜,從全譜可以判斷出,ZrCC中主要含有Al、Na、O和F,同時含有少量的P和Zr。為了確定每一種元素的價態和存在形式,對以上元素進行了光電子譜擬合,如圖11所示。結合相關文獻及擬合結果可以判斷出[26-28],Al主要以正三價狀態存在,形成化合物為AlPO4和Na3AlF6,相應的結合能分別為74.36 eV和74.51 eV,同時P和O的擬合結果印證了AlPO4的存在 (圖11d和圖11f),F和Na的擬合結果印證了Na3AlF6的存在 (圖11b和圖11c),Zr主要以Zr(HPO4)2·H2O和ZrO2的形式存在,對應結合能分別為183.72 eV和183.16 eV (圖11e),同時P和O的擬合結果印證了兩種物質的存在 (圖11d和圖11f)。因此,可以得出2A12鋁合金ZrCC的主要成分有Na3AlF6、AlPO4、Zr(HPO4)2·H2O和ZrO2。
圖10 2A12鋁合金ZrCC的XPS總譜
圖11 2A12鋁合金ZrCC中不同元素的高分辨XPS譜
利用XPS分析了膜層的具體組成成分,結合已有相關文獻報道[23-28],可以推測出轉化過程中陽極發生鋁的溶解,陰極發生氧的還原和氫氣的析出,發生的電化學反應如下:
隨著反應的進行,鋁合金與溶液反應界面處局部pH升高,促進了ZrO2在鋁合金表面的沉積,反應方程式如下:
同時在轉化過程中生成的其他不溶性的顆粒同樣在鋁合金反應界面沉積,化學反應方程式如下:
綜合上述分析可知,此種制備工藝在2A12鋁合金上制備出的轉化膜未能提高基體耐腐蝕性能,且膜層厚度不均,膜層顆粒無法均勻地覆蓋在2A12鋁合金表面,導致膜層均勻性和致密性較差。可見基體的顯微組織對膜層的成膜的過程具有重要的影響。
首先,2A12鋁合金經前處理后,基體表面天然氧化膜和部分第二相被去除的同時,留下了大量蝕坑和部分未去除的第二相,導致鋁合金表面粗糙不平 (圖5)。轉化膜的好壞很大程度上取決于基體的表面狀態。在浸入轉化液進行成膜反應前,化學性質均一的基體表面有利于均勻、致密轉化膜的形成[11-13,25-28]。
其次,2A12鋁合金中富含銅元素,且第二相密集分布在2A12鋁合金表面。由于鋁合金第二相相對于基體表現為陰極相,使得鋁合金表面陰極位點增加,表面活性較高[24,30]。當成膜反應開始時,由于基體與第二相的電偶效應,第二相周圍基體優先溶解,轉化膜顆粒優先在第二相附近生成 (圖8a2),隨著成膜反應的進行,第二相附近顆粒的形核速度大于顆粒的生長速度,進而抑制了第二相附近的顆粒的長大[1,11,24-27,30],導致鋁合金表面形核不均勻,第二相附近的顆粒尺寸明顯小于其他顆粒尺寸 (圖8c2)。
最后,成膜反應后期轉化膜顆粒不斷長大,但蝕坑依然存在,第二相在酸性轉化液中被完全腐蝕破壞,被破壞的第二相及其附近存在蝕坑或縫隙,有利于轉化液與鋁合金基體間的離子交換,促進成膜反應正向進行以及轉化膜顆粒的持續長大,增大了膜層顆粒間尺寸差距。不規則長大的膜層顆粒、依然存在的蝕坑和殘留第二相導致成膜結束后的轉化膜表面凹凸不平,膜層致密性和均勻性受到嚴重影響 (圖9a),同時導致轉化膜致密度降低,缺陷增加,防腐蝕能力下降[1,18,30,32]。
3 結論
本文在2A12鋁合金基體上制備了ZrCC轉化膜,通過極化曲線、電化學阻抗譜、SEM/EDS以及XPS對2A12鋁合金ZrCC的耐蝕性、前處理及轉化過程中顯微形貌演變以及膜層成分進行了分析,得出以下結論:
(1) 2A12鋁合金ZrCC膜層厚度為1~2 ?m,膜層表面形貌凹凸不平,膜層顆粒大小不一,表現出較差的致密性和均勻性。ZrCC膜層成分主要由Na3AlF6、AlPO4、Zr(HPO4)2·H2O和ZrO2組成。
(2) 動電位極化曲線和電化學阻抗譜的測試結果均表明,制備的ZrCC并不能對基體提供有效的防護,具體表現為成膜后的自腐蝕電流明顯增加,成膜后ZrCC的膜層電阻Rf和電荷轉移電阻Rct明顯小于鋁合金基體。
(3) 2A12鋁合金基體表面的第二相對轉化膜的成膜過程具有重要的影響,主要表現為以下三個方面。首先,前處理后的鋁合金基體表面粗糙不平,含有大量蝕坑和未被去除的第二相;其次,2A12鋁合金基體表面的第二相作為陰極相,成膜過程中不利于轉化膜顆粒的均勻形核和長大;最后,成膜過程中轉化膜顆粒不斷長大,但蝕坑和第二相依然存在,被腐蝕破壞的第二相和依然存在的蝕坑嚴重影響膜層的致密性和均勻性。
參考文獻
[1] Bethencourt M, Botana F J, Cano M J, et al.
Behaviour of the alloy AA2017 in aqueous solutions of NaCl. Part I: Corrosion mechanisms
[J]. Corros. Sci., 2009, 51: 518
[本文引用: 4]
[2] Boag A, Taylor R J, Muster T H, et al.
Stable pit formation on AA2024-T3 in a NaCl environment
[J]. Corros. Sci., 2010, 52: 90
[3] Boag A, Hughes A E, Wilson N C, et al.
How complex is the microstructure of AA2024-T3?
[J]. Corros. Sci., 2009, 51: 1565
[本文引用: 1]
[4] Din R U, Bordo K, Jellesen M S, et al.
Accelerated growth of oxide film on aluminium alloys under steam: Part II: Effects of alloy chemistry and steam vapour pressure on corrosion and adhesion performance
[J]. Surf. Coat. Technol., 2015, 276: 106
[本文引用: 2]
[5] Li S H, Yin Y J, Liu J R, et al.
Surface treatment and its application to aluminum and aluminum alloy
[J]. Spec. Cast. Nonferrous Alloys, 2001, (2): 54
[本文引用: 1]
李淑華, 尹玉軍, 劉家儒等.
鋁及鋁合金的表面處理及應用
[J]. 特種鑄造及有色合金, 2001, (2): 54
[本文引用: 1]
[6] Li H, Wang M L.
The process research to the chemical conversion film of aluminium
[J]. Mod. Paint Finish., 2010, 13(3): 64
[本文引用: 1]
李航, 王明磊.
鋁材的化學轉化膜工藝探討
[J]. 現代涂料與涂裝, 2010, 13(3): 64
[本文引用: 1]
[7] Liu Y, Skeldon P, Thompson G E, et al.
Chromate conversion coatings on aluminium-copper alloys
[J]. Corros. Sci., 2005, 47: 341
[本文引用: 1]
[8] Campestrini P, Terryn H, Vereecken J, et al.
Chromate conversion coating on aluminum alloys: III. Corrosion protection
[J]. J. Electrochem. Soc., 2004, 151: B370
[本文引用: 1]
[9] Zhao J, Xia L, Sehgal A, et al.
Effects of chromate and chromate conversion coatings on corrosion of aluminum alloy 2024-T3
[J]. Surf. Coat. Technol., 2001, 140: 51
[本文引用: 2]
[10] Verdalet-Guardiola X, Fori B, Bonino J P, et al.
Nucleation and growth mechanisms of trivalent chromium conversion coatings on 2024-T3 aluminium alloy
[J]. Corros. Sci., 2019, 155: 109
[本文引用: 1]
[11] Campestrini P, van Westing E P M, de Wit J H W.
Influence of surface preparation on performance of chromate conversion coatings on Alclad 2024 aluminium alloy: Part I: Nucleation and growth
[J]. Electrochim. Acta, 2001, 46: 2553
[本文引用: 4]
[12] Long Z L, Zhou Y C, Xiao L.
Characterization of black chromate conversion coating on the electrodeposited zinc-iron alloy
[J]. Appl. Surf. Sci., 2003, 218: 124
[13] Brown G M, Shimizu K, Kobayashi K, et al.
The development of chemical conversion coatings on aluminium
[J]. Corros. Sci., 1993, 35: 253
[本文引用: 1]
[14] Brown G M, Shimizu K, Kobayashi K, et al.
The morphology, structure and mechanism of growth of chemical conversion coatings on aluminium
[J]. Corros. Sci., 1992, 33: 1371
[本文引用: 1]
[15] Chidambaram D, Clayton C R, Halada G P.
The role of hexafluorozirconate in the formation of chromate conversion coatings on aluminum alloys
[J]. Electrochim. Acta, 2006, 51: 2862
[本文引用: 1]
[16] Hinton B R W, Wilson L.
The corrosion inhibition of zinc with cerous chloride
[J]. Corros. Sci., 1989, 29: 967
[本文引用: 3]
[17] Yoganandan G, Premkumar K P, Balaraju J N.
Evaluation of corrosion resistance and self-healing behavior of zirconium-cerium conversion coating developed on AA2024 alloy
[J]. Surf. Coat. Technol., 2015, 270: 249
[本文引用: 2]
[18] Bethencourt M, Botana F J, Cano M J, et al.
High protective, environmental friendly and short-time developed conversion coatings for aluminium alloys
[J]. Appl. Surf. Sci., 2002, 189: 162
[本文引用: 2]
[19] Swain G M, Li L L.
Formation and structure of trivalent chromium process coatings on aluminum alloys 6061 and 7075
[J]. Corrosion, 2013, 89: 1205
[本文引用: 1]
[20] Guo Y, Frankel G S.
Characterization of trivalent chromium process coating on AA2024-T3
[J]. Surf. Coat. Technol., 2012, 206: 3895
[本文引用: 1]
[21] Saillard R, Viguier B, Odemer G, et al.
Influence of the microstructure on the corrosion behaviour of 2024 aluminium alloy coated with a trivalent chromium conversion layer
[J]. Corros. Sci., 2018, 142: 119
[本文引用: 2]
[22] Viroulaud R, ?wiatowska J, Seyeux A, et al.
Influence of surface pretreatments on the quality of trivalent chromium process coatings on aluminum alloy
[J]. Appl. Surf. Sci., 2017, 423: 927
[本文引用: 1]
[23] Lunder O, Simensen C, Yu Y, et al.
Formation and characterisation of Ti–Zr based conversion layers on AA6060 aluminium
[J]. Surf. Coat. Technol., 2004, 184: 278
[本文引用: 2]
[24] George F O, Skeldon P, Thompson G E.
Formation of zirconium-based conversion coatings on aluminium and Al-Cu alloys
[J]. Corros. Sci., 2012, 65: 231
[本文引用: 3]
[25] Coloma P S, Izagirre U, Belaustegi Y, et al.
Chromium-free conversion coatings based on inorganic salts (Zr/Ti/Mn/Mo) for aluminum alloys used in aircraft applications
[J]. Appl. Surf. Sci., 2015, 345: 24
[本文引用: 5]
[26] Milošev I, Frankel G S.
Review—conversion coatings based on zirconium and/or titanium
[J]. J. Electrochem. Soc., 2018, 165: C127
[本文引用: 2]
[27] Liu Y, Yang Y G, Zhang C Y, et al.
Protection of AA5083 by a zirconium-based conversion coating
[J]. J. Electrochem. Soc., 2016, 163: C576
[本文引用: 2]
[28] Hosseini R M, Sarabi A A, Mohammadloo H E, et al.
The performance improvement of Zr conversion coating through Mn incorporation: With and without organic coating
[J]. Surf. Coat. Technol., 2014, 258: 437
[本文引用: 3]
[29] Zhan W, Qian X Z, Gui B Y, et al.
Preparation and corrosion resistance of titanium-zirconium-cerium based conversion coating on 6061 aluminum alloy
[J]. Mater. Corros., 2020, 71: 419
[30] Chen X M, Li G Y, Lian J S, et al.
An organic chromium-free conversion coating on AZ91D magnesium alloy
[J]. Appl. Surf. Sci., 2008, 255: 2322
[本文引用: 4]
[31] Li L L, Whitman B W, Munson C A, et al.
Structure and corrosion performance of a non-chromium process (NCP) Zr/Zn pretreatment conversion coating on aluminum alloys
[J]. J. Electrochem. Soc., 2016, 163: C718
[本文引用: 3]
[32] Li L L, Whitman B W, Swain G M.
Characterization and performance of a Zr/Ti pretreatment conversion coating on AA2024-T3
[J]. J. Electrochem. Soc., 2015, 162: C279
[本文引用: 2]
[33] Carreira A F, Pereira A M, Vaz E P, et al.
Alternative corrosion protection pretreatments for aluminum alloys
[J]. J. Coat. Technol. Res., 2017, 14: 879
[本文引用: 2]
[34] Golru S S, Attar M M, Ramezanzadeh B.
Effects of surface treatment of aluminium alloy 1050 on the adhesion and anticorrosion properties of the epoxy coating
[J]. Appl. Surf. Sci., 2015, 345: 360
[本文引用: 1]
免責聲明:本網站所轉載的文字、圖片與視頻資料版權歸原創作者所有,如果涉及侵權,請第一時間聯系本網刪除。
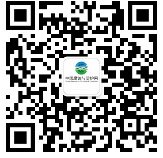
官方微信
《中國腐蝕與防護網電子期刊》征訂啟事
- 投稿聯系:編輯部
- 電話:010-62316606-806
- 郵箱:fsfhzy666@163.com
- 中國腐蝕與防護網官方QQ群:140808414