1.引言
開展管道內檢測,是管道完整性管理要求的一項內容,按照GB32167-2015《油氣輸送管道完整性管理規范》、TSG D7003-2010《壓力管道定期檢驗規則——長輸(油氣)管道》以及GB/T 27699-2011《鋼質管道內檢測技術規范》等要求,規定完整性評價宜優先選擇基于內檢測數據的適用性評價方法進行完整性評價,新建管道應當在投產3年內實施首次內檢測。內檢測收集的數據,可以有效的反應管道內部腐蝕金屬缺失情況,也能對外部腐蝕深度,面積等給出精確定位,這樣準確、可靠的內檢測數據,有效的提高了管輸企業對在役管道的綜合防護能力。利用承壓計算軟件,測算管道剩余壽命、剩余強度等,為管道運行設定合理的參數提供依據,保證管道安全長效的運行,也可以最大程度的防止管道腐蝕穿孔事故的發生,降低管輸企業的運行維修成本。然而,在役管道內檢測項目開展過程中存在著技術、人員、外部環境、合同等諸多方面的風險因素,這些風險的存在和發生的可能性會影響整個項目。以某老舊管線為例,重點介紹了管線內檢測項目內容、內檢測項目風險管理現狀以及現場配合工作風險識別等內容。
2.某老舊管線內檢測項目內容
根據此老舊管線的材質、設計壓力和生產運行的時間情況,在多種檢測方法中,選擇幾何變形檢測和漏磁檢測相結合的檢測方法。要求在前期清管達到清潔度的基礎上,利用加帶測徑板的檢測器,進一步對管線通過性進行驗證,然后采用漏磁檢測有效的對管線內外部缺陷情況進行確認,圖1是內檢測項目流程圖。
圖1 內檢測現場實施流程圖
2.1前期準備
項目的前期工作是指該項目從謀劃到實施之前所進行的全部工作,是整個項目實施程序中一個非常重要的階段。此老舊管線內檢測項目的前期工作,特別針對公司的屬性和特有的工作流程及申報程序,與一般項目存在著一定的差異。該老舊管線內檢測項目前期需要完成根據公司上級主管部門批復的文件精神,辦理項目的立項。成立以公司人員為主的組織機構,明確各小組人員及分工職責。邀請有資質的單位開展技術交流,從而確定工藝改造的具體內容,完成一系列的隊伍選擇合同簽訂。按照項目整體實施計劃編制項目統籌規劃書,明確各重要事件時間節點。提前做好對管線上閥門開關度和管線上三通有無檔條進行確認工作。做好整個項目的前期工作,可以提高項目實施的成功率,避免一定的風險。
2.2工藝改造
經過現場考察,該單位現有收發球裝置不能滿足管線內檢測需求,需要對收發球裝置進行改造,同時現場老舊管線施工安裝難度較大。
2.3管線清管
此管線在運行8年過程中從未進行過清管作業,對管線內實際的雜質堆積情況及管線的可通過性能并不掌握;且清管是管道內檢測作業前的必要步驟,為內檢測工作排除運行風險并保證對管道清潔度的要求,從而保證內檢測工作的安全有效。首先由檢測單位編制清管方案,人員到位后實施清管作業,最重要的環節是在檢測單位與管道運行公司人員同時在現場做清管效果驗證,推出的管道內雜質不超過5Kg,測徑板變形不超過20%,則視為達到驗收標準。
2.4智能檢測
由檢測單位編制此老舊管線內檢測實施方案,確定各分組人員。沿線埋設定標盒開挖監聽坑,并對所使用的設備進行初步安裝調試,待所有的條件都確認后實施內檢測作業,采用電子幾何變形檢測器,檢測定位管道發生較大變形的準確位置;最后采用漏磁金屬損失檢測器,對管線內腐蝕點進行測定,并根據跟蹤定位盒進行定位。
2.5數據分析
將內檢測器存儲數據導出,根據此老舊管線實際情況建立分析模型,將檢測數據進行分析,完成最嚴重腐蝕點情況報告及初步缺陷評價,最終的腐蝕數據位置需要根據驗證修正后給出。
圖2管線缺陷分布圖
2.6開挖驗證
依據初步數據分析結果,選擇其中5個點進行驗證,開挖點一般選擇檢測結果異常的地方進行驗證,包括深度、長度、寬度、缺陷的方位。開挖坐標位置按照之前預埋的定位盒進行確定,選擇幾個特征點附近的環狀焊縫來進行驗證。將開挖驗證點的測量結果與檢測結果進行比對,確認實際檢測精度是否滿足檢測器的精度指標,從而修正建立的分析模型,對檢測數據進行數據校準。
圖3管線缺陷開挖圖
2.7缺陷修復
根據開挖后對存在的缺點進行初步的處理,打磨防腐層,除去鐵銹,測量銹蝕點的參數。具體修補方法需要根據對腐蝕情況進行判斷后做出。
無泄漏缺陷或破壞的永久修復的方法(1)切除管道;(2)通過打磨去除缺陷(只有非刻痕缺陷);(3)通過堆焊金屬修復外在腐蝕引起的金屬減薄;(4)A型套筒或環氧鋼殼技術;(5)復合材料補強修復(只用于外部腐蝕引起的金屬減薄);(6)開孔封堵;(7)炭纖維補強,粘纏體防腐,電火花撿漏。
泄漏的永久修復可采用如下方法:(1)停輸切除管道;(2)B型套筒;(3)不停輸開孔封堵。
2.8系統評估
由檢測單位出具最終檢測報告,對被檢測管線進行管道缺陷評價,計算管道的剩余強度、剩余壽命和五年維修計劃等,同時提出管段承壓與在線運行的意見。
3.某老舊管線內檢測項目風險管理現狀
3.1某老舊管線內檢測項目風險的特點
某老舊管線內檢測項目與一般管道施工、煉廠設備建設等項目一樣,具有項目投資大、涉及工作和工序繁多,易受外界因素及不可抗力影響等特點,但某老舊管線內檢測項目也有自身的特點:
(1)此管線運行8年的過程中,從未進行過清管作業,對管線實際的雜質堆積情況及管線的可通過性并不掌握;
(2)管線投產以來施工改線處較多;
(3)管線不具備內檢測器收發條件,現場工藝改造復雜;
(4)此管線擔負著向某煉化企業輸送原油任務,由于是單一油源,一旦停輸對企業效益影響巨大,無法停輸,因此,是在不停輸的情況下,進行管道在役檢測;
(5)人員上不具備經驗,特別是在內檢測項目風險管理及控制上缺乏經驗。
3.2某老舊管線內檢測項目風險的特點
由于某老舊管線內檢測是某煉化企業運行10年來開展的首次管線內檢測工作,存在問題主要為:
(1)沒有完整的油氣輸送管道內檢測風險管理體系;
(2)可借鑒的同類項目經驗不多,開展工作主要抱著“摸著石頭過河”的心態;
(3)對風險分級管理措施不夠明確,因此不能制定有針對性的應對措施。
3.3某老舊管線內檢測項目風險控制架構
根據此老舊管線內檢測項目風險特點,建立相應的風險控制架構,主要包括組織結構、風險識別、風險評價及風險應對等四部分內容,四部分間各要素緊密相關,相互滲透,以實現此管線內檢測項目風險控制的總體目標。某老舊管線內檢測項目風險控制架構如圖4所示。
圖4 某老舊管線內檢測項目風險控制架構
4.現場配合工作風險識別
對于面臨的各類風險必須在現場實施方案中全面識別,制定相應的預防措施。同時,現場跟球過程中應成立后勤保障組,控制人員面臨的風險,保障現場安全。現場配合工作中主要面臨的風險有以下兩個方面。
4.1人員面臨的風險
人員面臨的風險主要有以下幾個方面:在裝載和收發球區域組建并操作檢測工具以及所有的支持設備,被卡車、叉車、載荷、車輛后擋板/側擋板撞擊,造成擠壓傷害、骨折、切割傷& 擦傷。遇到雨雪天氣,道路泥濘,導致車輛側翻或者陷入泥土中;跟球人員徒步進入監測點可能導致滑倒、跌傷等傷害;收發球間距較長,流速減慢,跟球時間長,人員不足,不可避免地導致跟球駕駛員長時間疲勞駕駛帶來的交通風險;由于輸氣管道站間距較長,跟球人員過度疲勞帶來的生理、心理危害,誘發疾病,以及跟球過程中遭受野外蚊子、昆蟲等叮咬致病;搭建發球裝備以及在使用后撤離發球裝備,包括任何專用設備的組裝和拆裝、使用木頭設置擺放托盤的平臺以及使用推車,擺放墊木、連接支腿、操作推動盤、調整托盤高度或連接反應式驅動設備(如果適用的話)時造成手指/手掌擠壓傷或剪切傷。尖銳或粗糙邊緣可能造成手和腿的擦傷和切割傷;收發球過程中對球筒實施氮氣置換,并在現場配備可燃氣體探測器,防止可燃氣體的聚集。除非在進行了多次清管或者檢測后,經過對推出的污物進行分析,證明推出的污物中不存在硫化亞鐵等可能會導致自燃的物質存在,可考慮不進行氮氣置換,否則,必須進行氮氣置換。
4.2設備面臨的風險
設備面臨的風險主要有以下幾個方面:檢測器跟蹤儀可能因為電池不足,壓力、溫度、振動等原因導致跟蹤儀信號丟失;檢測器可能由于管道變形、彎頭曲率半徑過小、閥門沒有完全打開等原因導致卡堵;如果管道內存在大量的游離水,在高壓下可能會在管道的特殊點(如閥門、壁厚變化處、缺陷處等)生產冰,大量的冰被檢測器推動而集結有造成冰堵的風險;管線沿線大于管徑30%的三通有些沒有擋條或擋板,可能會導致三通停球;由于管道內部條件、皮碗質量原因,可能會導致皮碗過度磨損,從而使檢測器喪失動力而停滯。
5.總結
針對某老舊原油管線,詳細闡述了該管線進行內檢測實施流程,分析了該老舊管線的風險管理現狀,并提出了現場配合風險識別,指出現場配合工作的好壞在一定程度上決定著內檢測工作的成敗,對于獲取高質量的檢測數據也具有至關重要的作用,為管道完整性管理、基礎評價提供基礎資料,提高管道本身的綜合防護能力,保證在役管道安全長效的運行。
作者簡介:馬義來(1987-),博士,工程師,主要從事油氣管道漏磁無損檢測方面的研究工作。E-mail:chantal1314@163.com。
通訊作者:靳陽(1991-),碩士,助理工程師,主要從事油氣管道漏磁無損檢測方面的研究工作。地址:北京市朝陽區和平西苑2號賽福特大廈C305;郵編:100029;Tel:010-59068232,18811307759;E-mail:jy78987@163.com。
免責聲明:本網站所轉載的文字、圖片與視頻資料版權歸原創作者所有,如果涉及侵權,請第一時間聯系本網刪除。
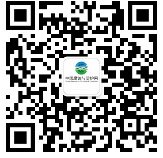
官方微信
《中國腐蝕與防護網電子期刊》征訂啟事
- 投稿聯系:編輯部
- 電話:010-62316606-806
- 郵箱:fsfhzy666@163.com
- 中國腐蝕與防護網官方QQ群:140808414