1 塔頂油氣線檢驗及損傷情況
焦化裝置分流塔頂系統存在H2S-HCL-NH3-H2O低溫腐蝕,是裝置的重點腐蝕部位,為此塔頂油氣線是日常腐蝕監控的重點,需要定期用定點測厚等檢測手段對油氣線進行腐蝕情況的判定,以防止腐蝕泄漏的發生并對工藝防腐措施進行驗證。在裝置定點測厚檢驗時,測厚發現塔頂油氣線自分餾塔(C202)頂出口第1個彎頭,厚度損失大于50%。見圖1(以下簡稱:油氣線彎頭),按有關規范判定及強度校核,已不能安全使用,對彎頭進行了更換,管線其他部位正常。
塔頂油氣線自分餾塔(C202)頂出來,終點至空冷器(A201)入口,管線規格:φ377×9.5mm,材質:20,介質:塔頂油氣、水汽、焦粉等,設計溫度250℃,操作溫度:135℃,設計壓力:1.0 MPa,操作壓力:0.14MPa。該管線2011年投用至今,上次檢修(一年)因腐蝕減薄對部分管段進行了更換。
圖1 油氣線管道示意圖
2 上一周期停工檢修檢驗結果及分析
在一年前的停工大檢修中,對分餾塔C202、空冷器A-201及塔頂油氣線均進行了檢驗及腐蝕調查,結果表明分餾塔C202整體狀況良好,分餾塔底及1至3層塔盤上存在大量焦粉,各層塔盤無脫落,無腐蝕。空冷器A201,宏觀檢測發現管板、焊縫、管口內壁有結垢現象,管外壁包裹一層銹垢,除銹后管外壁密集坑蝕,存在嚴重垢下腐蝕。渦流檢測:換熱管普遍存在均勻腐蝕加局部坑蝕,個別壁厚損失大于40%,進行了堵管處理剩余換熱管壁厚損失20%~40%。說明存在硫氫化銨(NH4HS)結鹽腐蝕。
圖2 空冷器A-201水冷管(a)(b)、空冷管(c)(d)管箱外觀,管束外壁密集坑蝕
塔頂油氣線經檢驗發現有三個彎頭減薄嚴重。最薄處4.86mm,進行了更換,直管段厚度正常。
3 理化失效分析
檢驗中發現油氣線彎頭厚度損失大于50%,為進一步查找原因,對該管線進行理化分析
3.1 超聲波測厚及強度校核
對油氣線彎頭外側、及兩側部位進行厚度檢測,外側厚度范圍:4.1mm-7.4mm,距外側中心線7mm距離,測得兩側部位厚度范圍:4.1mm-7.1mm。彎頭兩側測厚范圍:8.5-9.2mm,該彎頭減薄最嚴重部位在外側,厚度最薄4.1mm。(強度校核主要參數見表1)
表1 油氣線強度校核主要參數
圖3 油氣線彎頭測厚部位示意圖
有效厚度計算公式:
式中:tw—計算厚度,mm;P—設計壓力, MPa;D—管外徑,mm;S—設計溫度下許用應力,MPa;φ—焊縫接頭系數;Y—計算因數,鐵素體鋼,在當前溫度下取0.4;I—計算系數,
當計算彎管或彎頭的外側厚度時計算公式:
計算I=0.93
計算設計最小厚度(單位mm):
tw =(1.0×377)/(2×(137×0.6/0.93+1.0×0.4))=2.12
強度校核壁厚(有效壁厚計算)(單位mm):
t=實測最小壁厚- 下一檢驗周期腐蝕余量C
=4.1-((9.5-4.1)/(2019-2011))×3=4.1-2.03=1.97
強度校核壁厚t< 最小設計壁厚tw
依據《壓力管道定期檢驗規則》3.2.3管子、管件壁厚全面減薄評級,耐壓強度校核不合格。
3.2化學成分分析
使用PMI-Master Pro/13M0067全譜儀對其油氣線彎頭進行化分成分分析,結果見表2,可見彎頭所用的20號鋼化學成分符合GB9948-2013《石油裂化用無縫鋼管》標準要求。
表2 化學成分分析結果(質量分數)
3.3 內壁腐蝕狀態及能譜分析
將失效的油氣線彎頭拆下,沿縱向剖開(見圖4),觀察內壁附著有大量黑色油氣產物,截取一部分將其表面清洗干凈,發現表面有大面積腐蝕坑,腐蝕坑深度較淺,伴有沖刷痕跡。
圖4 油氣線彎頭內壁形貌
對油氣線彎頭的腐蝕產物進行能譜分析,得到的腐蝕產物元素組成結果見表3。表3顯示,垢物中的元素主要有C、O、Al、Si、S、Fe,垢物中Fe、S元素含量較高, Al,Si元素含量很少。結合表3和油氣線介質情況進行分析,判斷腐蝕產物主要為含S元素的氧化物或其化合物混合而成,即鐵的硫化物,氧化物和過氧化物,屬濕硫化氫腐蝕產物。
表3 能譜成分分析結果(質量分數)
3.4 金相分析
按照GB/T13298-2015《金相顯微組織檢驗方法》,經過切割鑲嵌制備金相試樣,再由多道砂紙預磨、精磨、研磨、拋光和4%硝酸酒精侵蝕,利用德國AXIOPALAN直立光程金相顯微鏡進行金相分析。
取油氣線彎頭減薄部位的縱截面,制取金相試樣,觀察是由管內壁向外壁逐漸減薄。其金相組織為:鐵素體+珠光體,晶粒度為8級,夾雜物未發現超標現象(圖5)。
圖5 油氣線彎頭金相組織
4 分餾塔頂系統腐蝕機理及控制分析
分餾塔頂部腐蝕主要為低溫H2S-HCL-NH3-H2O型腐蝕,原油中大部分氮化物、硫化物和電脫鹽后原油含有少量的氧化物經過常減壓裝置分離以后進入渣油中、它們在焦化過程中裂解,分別生成NH3、H2S和HCL(也可能由裝置注水中帶人的氯化物)。干態的NH3、H2S和HCL對金屬無腐蝕性,但隨著塔頂溫度的降低,介質中的微量水冷凝,上述腐蝕產物溶解于冷凝水中,形成稀鹽酸及濕硫化氫腐蝕環境,對分餾塔頂部塔壁及塔盤、塔頂冷凝冷卻系統和塔頂回流系統的設備及管線產生腐蝕。該類腐蝕對碳鋼及低合金鋼而言,主要表現為稀鹽酸對金屬均勻腐蝕減薄及局部的點蝕及坑蝕和濕硫化氫應力腐蝕開裂,主要影響因素有腐蝕產物濃度、流速及溫度,其中控制露點溫度不形成腐蝕產物是工藝防腐的關鍵。
據計算分餾塔頂露點溫度為92.3℃,為滿足防腐需求,工藝防腐指標要求應控制分餾塔頂溫度高于露點溫度14℃。分餾塔頂操作溫度實際最小值為125℃,符合工藝防腐指標規定。從實際運行結果得知,分餾塔頂及油氣線未發生應力開裂,均勻腐蝕輕微,說明合理的露點溫度控制了稀鹽酸及濕硫化氫腐蝕。
對焦化分餾塔頂系統,NH4CL及NH4HS結鹽是另一種腐蝕形式,其主要原理為焦化過程中裂解生成的氣相NH3和HCL、H2S,在一定的溫度下結晶形成NH4CL及NH4HS固體銨鹽,在設備、管線的低流速部位沉積造成堵塞,影響換熱器、空冷器的換熱效率。同時NH4CL及NH4HS固體銨鹽極易吸水,吸水后形成腐蝕性很強物質,對設備和管線造成垢下腐蝕或其形成的水溶液對金屬表面產生磨損腐蝕。NH4CL及NH4HS銨鹽水溶液對金屬表面的腐蝕主要決定于其濃度和流速,特別是在變徑、變向處如大小頭、彎頭、空冷器入口易造成沖刷腐蝕。上述空冷器(A201)檢查所呈現的結垢、腐蝕現象證明焦化分餾塔頂系統存在銨鹽結晶,同時油氣線腐蝕減薄部位在沖刷嚴重的彎頭外側,說明銨鹽水溶液的沖刷腐蝕是油氣線彎頭減薄的主要原因。
5 綜合分析
通過理化檢測分析,油氣線彎頭化學成分及金相組織未見異常,說明管子本身無質量問題。但通過彎頭內壁形貌看出,是從內壁方向腐蝕減薄,且有大面積均勻腐蝕坑,局部減薄嚴重,并且減薄最嚴重部位在外側,厚度最薄4.1mm。能譜檢測發現垢物中含有大量硫元素,形成的腐蝕產物,從而會導致彎頭由內向外的腐蝕減薄。
根據分餾塔頂系統上一周期檢驗、腐蝕檢查情況及本次在線檢測結果表明,分餾塔(C202)、塔頂油氣線除上述失效彎頭外,整體未發生異常的金屬均勻腐蝕減薄及局部的點蝕及坑蝕和濕硫化氫應力腐蝕開裂,說明控制露點溫度到位,使塔頂系統低溫H2S-HCL-NH3-H2O型腐蝕得到了有效控制??绽淦鳎ˋ201)檢驗發現管板、焊縫、管口內壁有結垢及換熱管普遍存在堵塞和腐蝕減薄現象說明,塔頂系統存在NH4CL及NH4HS銨鹽結鹽腐蝕。結合以上事實,說明銨鹽的沖刷腐蝕是油氣線彎頭減薄的主要原因。
6 結論及建議
通過對裝置檢查中發現的油氣線彎頭減薄問題,分析所知該管線是由于銨鹽的沖刷腐蝕造成。為了達到裝置“四年一修”保障裝置安全運行,裝置目前需要增加和完善的防腐措施,建議從原料性質入手,通過調節上游原料渣油的性質,將原料性質控制在裝置設防值的指標范圍內,以控制銨鹽結晶,同時增加頂循系統的緩蝕劑及水的設施。
加強分餾系統的腐蝕監、檢測,發現問題及時處理。根據國內外同類裝置經驗,煉制高含硫原油后,由于工藝等因素,給分餾系統帶來的腐蝕問題,應從工藝防腐蝕和材料升級方面考慮減緩腐蝕。建議加強該部位的腐蝕監、檢測,尤其是定點測厚,發現問題及時處理。
作者簡介:劉媛媛(1984-),主要從事石油化工設備檢驗、理化分析、腐蝕與防護工作。E-mail:liuyyws@petrochina.com
免責聲明:本網站所轉載的文字、圖片與視頻資料版權歸原創作者所有,如果涉及侵權,請第一時間聯系本網刪除。
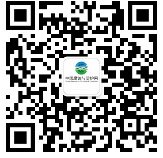
官方微信
《中國腐蝕與防護網電子期刊》征訂啟事
- 投稿聯系:編輯部
- 電話:010-62316606-806
- 郵箱:fsfhzy666@163.com
- 中國腐蝕與防護網官方QQ群:140808414