穩定化處理的目的
奧氏體不銹鋼的晶間腐蝕產生原因有一個著名的晶間貧鉻理論。即如果不銹鋼在450-850℃的溫度范圍內(俗稱敏化溫度區間)長時間停留,鋼中的碳會向奧氏體晶界擴散,并在晶界處與鉻化合析出碳化鉻,于是碳化物兩側出現含鉻低于11.4%、厚度約為數十至數百納米的貧鉻區。這種貧鉻區使晶間不能抵抗某些介質的侵蝕。所以,這樣的晶間對腐蝕介質就十分敏感。
為了減少晶間貧鉻現場的產生,提高不銹鋼的抗晶間腐蝕能力,一般有三個辦法:第一,采用超低碳奧氏體不銹鋼,降低不銹鋼中的碳元素含量,避免大量碳化鉻的形成。第二個辦法,不銹鋼冶煉過程中的固溶+速冷熱處理,將其加熱到1050~1150℃保溫,然后水淬速冷。室溫下快速得到單相奧氏體組織,避免在450-850℃敏化區形成大量的碳化鉻。注意,這個是常規操作。第三個辦法,采用穩定化不銹鋼。在奧氏體不銹鋼冶煉時加入數倍于含碳量的鈦或鈮元素(TP321或TP347),可在形成碳化鉻之前的875度以上溫度時優先形成鈦或鈮的碳化物,這些碳化物幾乎不固溶于奧氏體中。材料從高溫冷卻時,即使經過易析出Cr23C6的敏化溫度區間(450~850℃)時也不會沿晶界大量析出碳化鉻,從而大大提高了抗晶間腐蝕的能力。
為了使鋼達到最大的穩定度,還應作穩定化處理,即將構件加熱至900℃使碳化鉻充分溶解,而此時讓鈦和鈮充分形成非常穩定的碳化鈦和碳化鈮。然后在空氣中冷卻,即使經過敏化溫度時,也無碳化鉻在晶界析出。經穩定化處理后的奧氏體不銹鋼便大大降低了晶間腐蝕的可能性。
穩定化處理存在的問題
隨著國內煉油石化行業的大發展和裝置大型化,施工過程中TP347 、TP321材質管道焊縫經過穩定化熱處理后,部分焊縫出現裂紋,隨著壁厚的增加,裂紋程度越嚴重。經統計,隨著壁厚的增加,特別是壁厚大于40mm時,裂紋出現的機率增加。裂紋多發生在直管與法蘭對焊連接的部位以及直管與管件( 如彎頭) 對焊連接的部位,而直管與直管對焊連接的部位出現的裂紋極少。裂紋多為沿焊縫方向的縱向裂紋,橫向裂紋極少,裂紋出現的位置基本上多位于焊縫邊緣靠近熔合線附近。
據推測,裂紋屬于熱處理過程中產生的再熱裂紋,裂紋與壁厚和焊接接頭拘束度密切相關,壁厚越大,焊接接頭拘束度越大,越容易產生裂紋。裂紋出現的原因: 一方面現場的管道焊縫焊后熱處理基本上采用局部加熱,由于壁厚較厚,沿管道厚度方向存在較大的溫度梯度,從而造成較大的溫度應力,同時焊接過程中產生的焊接殘余應力隨壁厚和拘束度的增加而增大; 另一方面,鋼管母材晶粒度對裂紋的產生也有較大的影響,母材的晶粒度越粗大,管道發生再熱裂紋的概率越高。
現狀
近二十來來,我們看到國內很多優秀的管道技術專家對此做了非常充分的調研和判斷,形成了較多有意義的成果,并經過復雜工程的實踐,結果可靠。比如由中國神華煤制油公司和中國特檢院諸位專家起草的NB/T10068-2018《含穩定化元素不銹鋼管道焊后熱處理規范》,該規范的核心觀點如下:
(1)425℃(450℃)<操作溫度<500℃(此溫度剛進入敏化溫度區間),做穩定化處理焊接裂紋風險小(壁厚<40mm)的管道盡量都做穩定化處理。

(2)500℃≤操作溫度,已經處于敏化溫度區間中段,任意壁厚都需要做穩定化處理。
(3)注意備注b,壁厚≥40mm的管道,操作溫度低于500℃時,一般不進行穩定化處理,可按照附錄A進行中和清洗、沖氮保護、干空氣防止液態水生成等措施來彌補,并增加技術措施,如嚴格按規范控制焊接工藝,多層焊道焊接,控制層間溫度降低焊接線能量,再如焊接工藝評定時增加晶間腐蝕評定(按GB4334-E法);以及加強現場管理、嚴格無損檢測等。
免責聲明:本網站所轉載的文字、圖片與視頻資料版權歸原創作者所有,如果涉及侵權,請第一時間聯系本網刪除。
相關文章
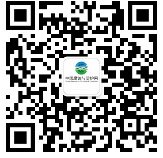
官方微信
《中國腐蝕與防護網電子期刊》征訂啟事
- 投稿聯系:編輯部
- 電話:010-62316606-806
- 郵箱:fsfhzy666@163.com
- 中國腐蝕與防護網官方QQ群:140808414
點擊排行
PPT新聞
“海洋金屬”——鈦合金在艦船的
點擊數:7130
腐蝕與“海上絲綢之路”
點擊數:5741