電化學噪聲 (EN) 是指電化學動力系統演化過程中系統狀態參量 (電極電位、外測電流密度等) 的隨機非平衡波動現象[1]。EN技術能夠原位、連續、無損地監測局部腐蝕萌生與發展,將其應用于腐蝕監測領域的關鍵是通過合適的信號處理方法提取有效的特征參數,然后關聯其與特定腐蝕機制或腐蝕發展過程。國內外有學者[1,2,3,4,5]針對EN技術在腐蝕領域的研究進行了綜述,然而他們更多關注的是EN技術在點蝕、涂層等方面的研究,對應力腐蝕開裂 (SCC) 關注較少,這一定程度上限制了EN在SCC研究中的應用。鑒于此,本文首先以評價腐蝕機制為背景介紹了EN信號處理技術的發展現狀,然后綜述了SCC研究中EN的測試方法及信號處理技術,最后討論了EN原位監測高溫高壓水SCC的研究狀況和存在的主要問題。
1 EN信號處理技術
EN信號通常是電位和電流的時間序列,這些時間序列中包含了豐富的與腐蝕機制相關的信息。最早人們嘗試通過觀察時間序列特征建立EN信號與腐蝕類型之間的對應關系。這種方法簡單有效,例如鈍化態具有類似白噪聲特征,亞穩態點蝕往往對應成對電位和電流暫態,而穩態點蝕的發生會伴隨著電位噪聲急劇降低、電流噪聲迅速增加等等。然而,許多情況下暫態混疊以及腐蝕系統的非周期性特點會使EN信號復雜化,單一觀察并不有效,因此多年來人們不斷提出新的方法處理EN信號。
1.1 統計分析
早期人們通過對噪聲時間序列進行統計分析,提取一些有用的特征參數。這些參數包括平均值、標準偏差、偏度、峰度以及由這些參數演繹而來的指標,比如:局部因子、點蝕因子、關聯系數、噪聲電阻等。
標準偏差及其演繹參數:一般而言,標準偏差與噪聲信號中暫態數目和幅度有關[6],暫態數目越多,幅度越大,標準偏差越大,反之亦然。電流噪聲暫態一般與局部腐蝕事件相關,而電位噪聲暫態則由局部腐蝕事件和膜雙電層電容所決定[7]。鈍化態由于暫態的缺失,標準偏差很小,點蝕則往往對應高標準偏差,而均勻腐蝕具有高幅度電流暫態和低雙電層電容特征,因此其電位標準偏差很小而電流標準偏差很大。噪聲電阻定義為電位標準偏差除以電流標準偏差,因而均勻腐蝕具有低噪聲電阻,鈍化態具有高噪聲電阻,而局部腐蝕的噪聲電阻則居于中間。需要注意的是,標準偏差和噪聲電阻均是有量綱參數,其在不同體系中的統一判別標準值得商榷。
根據平均值可以簡單快速判定腐蝕機制:高的電流噪聲平均值預示著腐蝕比較嚴重。偏度反映信號的不對稱性,峰度反映信號中快速暫態的存在,通常局部腐蝕可以造成高的偏度和峰度[8]。盡管統計參數可以快速監測腐蝕,但仍存在一些問題。首先,統計特征參數與直流漂移去除密切相關,合適的直流分量去除一定程度上決定了統計參數的判別效果。值得關注的是,直流漂移去除以后,平均值是否可以作為有效監測指標仍需考察。其次,計算統計參數時每部分包含的采樣點可能會對判別效果有一定影響,目前普遍接受間隔為512~1024 s。另外,很多時候統計參數具有很大的離散型,這會給決策者帶來一定的困擾。
1.2 頻域及時-頻分析
將時域信號通過傅里葉變換 (FFT) 或者最大熵方法 (MEM) 轉化為頻域信號進行功率譜密度 (PSD) 分析是信號分析中常用手段,腐蝕研究者關注的重點則是PSD中哪些參數可以與腐蝕機制建立有效關聯。目前普遍認為,PSD中低頻平臺、截止頻率和低頻衰減斜率可以用來進行腐蝕監測。Cheng等[9]認為低頻衰減斜率可以和不同的暫態類型建立關聯。Cottis等[10]發現截止頻率可以用來評價腐蝕機制。低頻平臺一般與信號強度密切相關,一些學者則提出截止頻率和低頻衰減斜率配合低頻平臺一起使用可能更加有效[11]。另外值得一提地是,頻域分析最大貢獻可能在于譜噪聲電阻的計算,譜噪聲電阻定義為電位噪聲PSD除以電流噪聲PSD。相比于時域噪聲電阻,譜噪聲電阻類似于阻抗模值具有頻率依賴性質,從而可以在不同頻率段進行分析,可一定程度地消除高頻噪聲干擾。Bertocci等[12]認為理論上低頻噪聲阻抗和低頻阻抗模值具有可比性。
進行頻域分析時一個重要假設是信號需滿足周期性條件,而腐蝕過程產生的噪聲信號顯然無法嚴格滿足。因此,一些學者提出了利用小波變換或者Hilbert-Huang變換進行時-頻分析,其中前者更是被腐蝕研究者稱為“腐蝕指紋”。一般通過離散小波變換后獲得小波系數能量分布圖,通過能量分布圖可以了解主導腐蝕事件的時間尺度,從而判別腐蝕機制。鈍化屬于高頻事件,均勻腐蝕對應低頻尺度,而點蝕屬于中低頻事件[13]。另外,一些學者認為小波熵也可以用來判斷腐蝕機制[14]。對于Hilbert-Huang變換,Homborg等[15,16]在評價腐蝕機制、微生物腐蝕監測等方面開展了一些研究。如Homborg所言,Hilbert-Huang可能是一種更加有效的EN分析方法,然而目前仍沒有充分證據表明Hilbert-Huang在判定腐蝕機制方面比小波分析有本質提升。
1.3 散粒噪聲
散粒噪聲理論認為腐蝕是由一系列短時、恒電荷的事件所組成。通過散粒噪聲理論可以從EN信號中提取出兩個特征參量:特征頻率 (fn) 和特征電荷 (q) 進行腐蝕機制的判定[8]。一般認為fn與腐蝕事件發生頻率有關,而q與單個腐蝕事件產生電荷相關。利用fn和q的二維交互圖可以快速判斷腐蝕機制:均勻腐蝕具有大q、大fn;局部腐蝕,比如點蝕具有大q、小fn;而鈍化具有小q、大fn。盡管散粒噪聲參數有一定的物理意義,其本質類似于統計參量和PSD分析結合的產物,二者在判別效果上具有相似之處。同時應注意的是,類似于噪聲電阻,散粒噪聲特征參數在判斷腐蝕機制時依靠的是不同腐蝕機制量值的差異,其在不同腐蝕體系中的判別效果同樣值得考究。
1.4 混沌分析
混沌分析屬于非線性分析方法范疇。不同于時-頻方法關注事件的時間尺度,混沌分析更多關注的是隨機信號的決定性行為。混沌分析一般將時域信號經過相空間重構獲取其系統軌跡,然后剝離出一些特征參數進行分析。Xia等[17]利用混沌分析對316L不銹鋼的典型腐蝕機制進行了判別,發現關聯維數可以較好的將點蝕從均勻腐蝕和鈍化中區分。此外,一些學者嘗試利用遞歸圖和定量遞歸分析對EN信號進行解析。一些遞歸參量比如遞歸率、決定率、香儂熵等在判別腐蝕機制、監測局部腐蝕動力學過程等方面顯示出很強的能力。Hou等[18]利用定量遞歸方法結合機器學習對Q235鋼不同腐蝕機制進行了區分,發現通過遞歸參量建立的機器學習模型可以很好區分均勻腐蝕、點蝕和鈍化。Hou等的工作基于統計分析,而對遞歸參量的物理意義關注較少。García-Ochoa等[19]利用定量遞歸分析研究了銅的點蝕動力學過程,發現決定率越高,點蝕傾向越大,而決定率接近于0則對應隨機信號。Yang等[20]認為決定率越高越容易穩態點蝕,而遞歸率與點蝕形核相關。Zhang等[21]研究了304不銹鋼在不同濃度FeCl3溶液中點蝕行為,發現亞穩態點蝕具有高遞歸率和決定率,而穩態點蝕遞歸率和決定率均偏低。可見,目前遞歸變量和點蝕動力學過程之間的內在關聯仍不清晰,這可能是由于不同材料體系點蝕所產生EN信號有所差異。未來需要對不同材料體系進行系統研究以獲取統一判據。
2 EN原位監測應力腐蝕開裂 (SCC)
2.1 EN測試方法
美國材料與試驗協會 (ASTM) 建議了實驗室EN測試的三電極體系:兩個名義相同的電極作為工作電極通過零電阻電流計 (ZRA) 耦合測試電流噪聲,其中一個工作電極與低噪聲參比電極連接測試電位噪聲。然而在SCC實驗中一個工作電極施加應力模擬SCC,這顯然無法滿足標準EN測試體系。目前,SCC研究中使用的電極體系有兩種。一是偽傳統方法。這種方法基本和上述傳統測試方式類似:加應力試樣為一個工作電極,用同材質、同大小或者大小一定比例的試樣作為另一個工作電極。這種方法最接近標準建議方法,目前使用最多。但值得注意的是它屬于非對稱電極體系,那么在進行后續信號分析時一些針對對稱電極體系的特征參數可能會不適用。二是電化學發射譜方法。這種方法要求一個工作電極為施加應力試樣,另一個工作電極為微陰極,例如很小的鉑絲。微陰極的存在對加應力試樣造成的極化影響基本可以忽略不記,因此可以進行準原位研究。這種方法最早由Chen等[22]提出。Wang等[23]和Du等[24]在點蝕或者SCC研究中使用了此種方法。然而,一些研究[25,26]認為這種方法的理論基礎存在缺陷。
實際上無論哪種測試方法,在利用EN技術進行SCC監測時,關鍵在于應使加應力試樣SCC產生的陽極電荷盡可能經過ZRA在另一個工作電極上消耗,從而形成可偵測的噪聲信號。在SCC研究中EN電極體系應盡量優化以使電流效率提高,從而盡可能完全反映出SCC裂紋萌生與擴展事件。因此在開展EN監測SCC的實驗中,施加應力工作電極的處理是一個需要重點關注的地方。一般需采取一些絕緣手段比如涂抹面漆、環氧樹脂粉末,盡可能只將標距段暴露于電解質溶液中從而將電流效率最大化。另外,Kovac等[27]工作表明:面漆邊緣最好避開標距段,這樣可以排除縫隙腐蝕的影響。
2.2 EN信號解析
2.2.1 時域分析
相比于點蝕的EN研究,SCC過程EN信號研究相對較少,且目前大部工作集中于將EN時域特征與SCC萌生與擴展過程相關聯。一些學者認為EN信號的直流分量可以與SCC動力學過程關聯。Kovac等[28]利用多種原位手段包括EN、聲發射 (AE) 和形貌觀察研究了敏化態304不銹鋼缺口板狀試樣在硫代硫酸鈉溶液中恒載荷加載SCC動力學過程,發現電流噪聲的直流分量隨著溶解強度增加而增加,并且直流分量與活性裂紋溶解產生的陽極區域面積有很好的關聯。Bolivar等[29]對敏化600鎳基合金的研究認為恒載荷加載下SCC遵循裂紋萌生數目快速增加、裂紋萌生與裂紋纏結競爭活性裂紋數目達到峰值、裂紋纏結和遮蔽效應占據主導活性裂紋數目下降的動力學過程,同時EN監測結果顯示:電位噪聲開始快速下降隨后趨于穩定,電流噪聲開始維持較高水平隨后下降,這與SCC動力學過程一致,因此他們認為EN直流趨勢可以反映SCC動力學過程。此外對于EN信號直流部分的物理意義,Macdonald等[30]研究了敏化態304不銹鋼緊湊拉伸 (CT) 試樣在硫代硫酸鈉溶液中的SCC裂紋擴展行為,發現耦合電流噪聲水平與應力強度因子和敏化程度具有很強關聯,而應力強度因子和敏化程度在一定程度上決定了SCC裂紋擴展速率,因此認為利用耦合電流噪聲水平可以表征裂紋擴展速率,然而目前仍缺乏二者之間的定量模型。
盡管上述研究表明直流趨勢可能包含反映SCC動力學過程的信息,但直流趨勢影響因素復雜,使得EN直流趨勢與SCC關聯的可靠性值得商榷。例如:上述研究均針對恒載荷加載,如果使用慢應變速率加載,那么塑性變形會對信號直流趨勢產生影響;另外電化學體系長時間內產生的漂移也會對信號解釋帶來一定困擾。因此,開展類似研究時應注意加載方式的選擇以及正式加載前電化學體系的穩定時間。
正是由于EN直流部分包含很多不確定性,因此大部分EN研究將直流部分去除,只關注信號的暫態特性。關于EN信號直流分量去除方法已有很多研究[31],這里不再贅述。將EN暫態與SCC關聯的重點是理解特殊SCC行為會產生何種特征暫態。大量研究均發現:SCC過程中會產生典型的快速上升和緩慢下降電流暫態,這與點蝕非常相似[32,33,34,35]。對于此種暫態人們利用膜破裂模型進行解釋,一般認為這種暫態預示著裂紋萌生。通過對暫態特征包括持續時間、形狀、積分電量等進行分析,研究者嘗試將不同暫態類型與一些特定的物理過程,比如韌帶撕裂、裂紋沿晶界擴展、裂紋纏結等對應。Watanabe等[36]研究了不同敏化程度的304不銹鋼慢應變速率加載下SCC過程的EN特征,發現低敏化和高度敏化程度試樣加載過程暫態很少,但高度敏化試樣一旦屈服,電流噪聲迅速增加,這可能和裂紋萌生和快速穩態擴展有關;而中等程度敏化試樣屈服以后出現大量暫態伴隨電流基線增加,這種特征和碳鋼亞穩態點蝕向穩態點蝕轉變極其類似,似乎對應于亞穩態微裂紋向穩態裂紋擴展;同時他們嘗試將暫態幅度與微裂紋尺度對應,發現這些暫態可能與長度10 μm的裂紋相關。Leban等[37]研究了敏化態304不銹鋼緩慢增加載荷加載下SCC過程EN信號的暫態特征,發現了兩種暫態:一種具有長持續時間,另一種持續時間較短。他們認為短持續時間暫態是由于金屬韌帶機械撕裂露出新鮮表面造成,長持續時間暫態則是由于SCC裂紋沿晶擴展造成。Breimesser等[38]研究了類似體系恒載荷加載SCC過程的EN特征,認為大于0.1 μA的臺階式電流暫態預示著裂紋的擴展;同時發現快速上升和持續數千秒下降的暫態可以對應于單個沿晶應力腐蝕開裂裂紋的萌生和擴展,而其他暫態則對應亞穩態點蝕、裂紋纏結或者裂紋擴展。
2.2.2 其他分析
如前所述,EN信號處理技術除了時域分析之外,還包括頻域、時-頻、混沌分析等。針對SCC產生的EN信號,一些研究者嘗試多角度分析這些信號,試圖提取簡單的特征參數,從而有效監測SCC,然而目前仍未形成統一標準。Anita等[39]對316不銹鋼U彎試樣在NaCl溶液中SCC過程的EN信號進行了統計和PSD分析,發現電位噪聲標準偏差和噪聲電阻可以區分裂紋萌生與擴展,而PSD低頻衰減斜率似乎對于SCC意義不大。Calabrese等[40]發現,恒載荷加載下散粒噪聲累積特征電荷可以很好的判定SCC孕育期、裂紋萌生和小裂紋擴展、穩態裂紋擴展和最終塑性斷裂。García-Ochoa等[41]則嘗試使用EN信號定量遞歸方法對316不銹鋼環境促進開裂進行了監測,發現在整個監測周期內點蝕產生的EN信號的決定率都很高,而一旦有裂紋形成則會使決定率降低;隨著裂紋擴展決定率會再次升高。對于SCC產生EN信號的時-頻域特征目前未見明確報道。
3 EN監測高溫高壓水SCC
我國目前正在大力發展核電,設備服役安全是影響核電發展的關鍵因素。核電結構材料長期服役高溫高壓且具有放射性水溶液中,腐蝕損傷特別是SCC時有發生,嚴重威脅核電站的安全運行。發展有效在線監測技術對于保障核電站安全運行意義重大。核電材料特殊的服役環境限制了可以采用的監測手段非常有限,而SCC的電化學本質與EN技術的連續、無損等特點決定了EN技術在監測核電設備SCC方面的潛在能力。針對EN監測高溫高壓水SCC,國外有少數研究組開展了相關工作,而國內在這方面的研究仍十分缺乏。
90年代Stewart等[42],Manahan和MacDonald[43]開創性將EN技術應用于高溫高壓水SCC研究中,探索了EN監測高溫高壓水環境SCC的可行性。Stewart等[42]在模擬沸水堆 (BWR) 環境中成功監測到了敏化304不銹鋼SCC過程產生的噪聲暫態信號,通過將暫態信號與裂紋特征關聯奠定了EN技術在監測高溫高水SCC裂紋萌生的可能性;Manahan和MacDonald[43]則更多關注EN技術在監測SCC裂紋擴展速率方面的能力。Manahan和MacDonald基于環境耦合模型成功實現了敏化304不銹鋼CT試樣在BWR環境中SCC產生的電流噪聲與應力強度因子之間的關聯,證明了EN技術監測高溫高壓水SCC裂紋擴展的能力。
此后,其他學者陸續對EN技術監測高溫高壓水SCC的能力進行了研究。不同工作各有創新之處,共同推進了EN技術在高溫高壓水環境中的應用。Watanabe等[44]研究了EN在壓水堆 (PWR) 環境中的應用,發現高壓泵引起的周期性波動是產生環境噪聲的主要因素,同時他們將噪聲信號與滑移溶解和氫致開裂機制關聯。Arganis-Juarez等[45]系統研究了固溶和敏化304不銹鋼在BWR環境中SCC過程的EN信號,重點關注了穿晶SCC和沿晶SCC的暫態特征。Kim等[46]利用EN技術監測了600鎳基合金Pb致SCC,他們工作的貢獻在于利用EN信號隨機分析方法將SCC過程從高溫高壓水氧化膜形成過程中區分出來,同時對SCC進行了定量比較。近期Paul Scherrer Institute (PSI) 實驗室重新考察了EN技術監測高溫高壓水SCC的能力[47,48],他們的研究結果強調了參比電極位置在監測電位暫態中的重要意義。由于高溫純水或者硼鋰溶液低電導率的特質,實驗中參比電極應盡量靠近裂紋尖端以使開裂事件盡可能在電位噪聲中反映出來。常規外置壓力平衡Ag/AgCl顯然無法達到這個要求,他們嘗試將鉑絲置于裂紋口附近。同時他們的另一個重大貢獻在于嘗試使用直流電位降 (DCPD) 技術與EN信號相互驗證[48]。盡管DCPD中直流電的存在會對EN信號產生干擾,但是他們的研究似乎指明了未來研究的方向。
4 存在問題與展望
綜上所述,EN技術具有原位監測SCC動力學過程的能力,具有工業化應用的可能性,且在監測高溫高壓水SCC方面有很好前景,但是目前這方面的研究仍存在一些問題,主要集中于以下幾點:
(1) EN特征參數眾多、優劣不一,局部腐蝕EN信號離散嚴重,將EN應用于工業在線監測時數據龐大,如何克服這些問題是將EN技術推向工業化應用必須考慮的關鍵。近期一些研究表明[49],將EN技術與人工智能技術相結合是一個可能的方向。
(2) SCC過程中EN監測的物理基礎仍不牢固,目前研究缺乏EN暫態與裂紋尺度之間明確的對應關系。例如:EN可監測最小裂紋尺度等。未來在小尺寸試樣上開展系統研究可能是建立二者之間對應關系的一個可能途徑。
(3) SCC過程中EN信號處理仍處于時域分析階段。將眾多先進的EN信號處理技術應用于SCC研究,獲取有效監測參數仍是未來需要努力的方向。
(4) EN技術監測高溫高壓水SCC目前國外仍處于測試方法的探索階段,國內基本為空白。未來在提高和驗證EN測試結果可靠性方面仍需探索,PSI實驗室經驗表明,將EN技術與其他監測手段耦合是一個有效的研究方向,而DCPD已被證明效果并不理想。嘗試將EN技術與其他高溫高壓水監測手段如AE技術耦合或許是一種可能的途徑。
參考文獻
[1] Zhang T, Yang Y G, Shao Y W, et al. Advances of the analysis methodology for electrochemical noise [J]. J. Chin. Soc. Corros. Prot., 2014, 34: 1
[1] (張濤, 楊延格, 邵亞薇等. 電化學噪聲分析方法的研究進展 [J]. 中國腐蝕與防護學報, 2014, 34: 1)
[2] Zhang J Q, Zhang Z, Wang J M, et al. Analysis and application of electrochemical noise— I. Theory of electrochemical noise analysis [J]. J. Chin. Soc. Corros. Prot., 2001, 21: 310
[2] (張鑒清, 張昭, 王建明等. 電化學噪聲的分析與應用— I. 電化學噪聲的分析原理 [J]. 中國腐蝕與防護學報, 2001, 21: 310)
[3] Xia D H, Song S Z, Behnamian Y. Detection of corrosion degradation using electrochemical noise (EN): Review of signal processing methods for identifying corrosion forms [J]. Corros. Eng. Sci. Technol., 2016, 51: 527
[4] Jamali S S, Mills D J. A critical review of electrochemical noise measurement as a tool for evaluation of organic coatings [J]. Prog. Org. Coat., 2016, 95: 26
[5] Ma C, Wang Z Q, Behnamian Y, et al. Measuring atmospheric corrosion with electrochemical noise: A review of contemporary methods [J]. Measurement, 2019, 138: 54
doi: 10.1016/j.measurement.2019.02.027
[6] Bahrami M J, Shahidi M, Hosseini S M A. Comparison of electrochemical current noise signals arising from symmetrical and asymmetrical electrodes made of Al alloys at different pH values using statistical and wavelet analysis. Part I: Neutral and acidic solutions [J]. Electrochim. Acta, 2014, 148: 127
doi: 10.1016/j.electacta.2014.10.031
[7] Cheng Y F, Luo J L. Electronic structure and pitting susceptibility of passive film on carbon steel [J]. Electrochim. Acta, 1999, 44: 2947
doi: 10.1016/S0013-4686(99)00011-0
[8] Sanchez-Amaya J M, Cottis R A, Botana F J. Shot noise and statistical parameters for the estimation of corrosion mechanisms [J]. Corros. Sci., 2005, 47: 3280
[9] Cheng Y F, Luo J L, Wilmott M. Spectral analysis of electrochemical noise with different transient shapes [J]. Electrochim. Acta, 2000, 45: 1763
[10] Cottis R A, Homborg A M, Mol J M C. The relationship between spectral and wavelet techniques for noise analysis [J]. Electrochim. Acta, 2016, 202: 277
[11] Shi Y Y, Zhang Z, Cao F H, et al. Dimensional analysis applied to pitting corrosion measurements [J]. Electrochim. Acta, 2008, 53: 2688
[12] Bertocci U, Gabrielli C, Huet F, et al. Noise resistance applied to corrosion measurements: 1. Theoretical analysis [J]. J. Electrochem. Soc., 1997, 144: 31
[13] Aballe A, Bethencourt M, Botana F J, et al. Using wavelets transform in the analysis of electrochemical noise data [J]. Electrochim. Acta, 1999, 44: 4805
[14] Moshrefi R, Mahjani M G, Jafarian M. Application of wavelet entropy in analysis of electrochemical noise for corrosion type identification [J]. Electrochem. Commun., 2014, 48: 49
doi: 10.1016/j.elecom.2014.08.005
[15] Homborg A M, Tinga T, Zhang X, et al. Transient analysis through Hilbert spectra of electrochemical noise signals for the identification of localized corrosion of stainless steel [J]. Electrochim. Acta, 2013, 104: 84
[16] Homborg A M, Morales C F L, Tinga T, et al. Detection of microbiologically influenced corrosion by electrochemical noise transients [J]. Electrochim. Acta, 2014, 136: 223
doi: 10.1016/j.electacta.2014.05.102
[17] Xia D H, Song S Z, Wang J H, et al. Determination of corrosion types from electrochemical noise by phase space reconstruction theory [J]. Electrochim. Commun., 2012, 15: 88
doi: 10.1016/j.elecom.2011.11.032
[18] Hou Y, Aldrich C, Lepkova K, et al. Monitoring of carbon steel corrosion by use of electrochemical noise and recurrence quantification analysis [J]. Corros. Sci., 2016, 112: 63
doi: 10.1016/j.corsci.2016.07.009
[19] Cazares-Ibá?ez E, Vázquez-Couti?o G A, García-Ochoa E. Application of recurrence plots as a new tool in the analysis of electrochemical oscillations of copper [J]. J. Electroanal. Chem., 2005, 583: 17
[20] Yang Y G, Zhang T, Shao Y W, et al. Effect of hydrostatic pressure on the corrosion behaviour of Ni-Cr-Mo-V high strength steel [J]. Corros. Sci., 2010, 52: 2697
doi: 10.1016/j.corsci.2010.04.025
[21] Zhang Z, Wu X Q. Correlated pitting stages of 304 stainless steel with recurrence quantification analysis of electrochemical noise [J]. Mater. Corros., 2019, 70: 197
[22] Chen J F, Bogaerts W F. Electrochemical emission spectroscopy for monitoring uniform and localized corrosion [J]. Corrosion, 1996, 52: 753
doi: 10.5006/1.3292068
[23] Wang C, Cai Y Z, Ye C Q, et al. In-situ monitoring of the localized corrosion of 304 stainless steel in FeCl3 solution using a joint electrochemical noise and scanning reference electrode technique [J]. Electrochem. Commun., 2018, 90: 11
[24] Du G, Li J, Wang W K, et al. Detection and characterization of stress-corrosion cracking on 304 stainless steel by electrochemical noise and acoustic emission techniques [J]. Corros. Sci., 2011, 53: 2918
[25] Cottis R A. The significance of electrochemical noise measurements on asymmetric electrodes [J]. Electrochim. Acta, 2007, 52: 7585
[26] Bautistia A, Huet F. Noise resistance applied to corrosion measurements: IV. Asymmetric coated electrodes [J]. J. Electrochem. Soc., 1999, 146: 1730
doi: 10.1149/1.1391834
[27] Kova? J, Leban M, Legat A. Detection of SCC on prestressing steel wire by the simultaneous use of electrochemical noise and acoustic emission measurements [J]. Electrochim. Acta, 2007, 52: 7607
doi: 10.1016/j.electacta.2006.12.085
[28] Kovac J, Alaux C, Marrow T J, et al. Correlations of electrochemical noise, acoustic emission and complementary monitoring techniques during intergranular stress-corrosion cracking of austenitic stainless steel [J]. Corros. Sci., 2010, 52: 2015
doi: 10.1016/j.corsci.2010.02.035
[29] Bolivar J, Frégonèse M, Réthoré J, et al. Evaluation of multiple stress corrosion crack interactions by in-situ Digital Image Correlation [J]. Corros. Sci., 2017, 128: 120
doi: 10.1016/j.corsci.2017.09.001
[30] Gomez-Duran M, Macdonald D D. Stress corrosion cracking of sensitized type 304 stainless steel in thiosulfate solution: I. Fate of the coupling current [J]. Corros. Sci., 2003, 45: 1455
doi: 10.1016/S0010-938X(02)00219-6
[31] Lentka L, Smulko J. Methods of trend removal in electrochemical noise data-Overview [J]. Measurement, 2019, 131: 569
doi: 10.1016/j.measurement.2018.08.023
[32] Luo J L, Qiao L J. Application and evaluation of processing methods of electrochemical noise generated during stress corrosion cracking [J]. Corrosion, 1999, 55: 870
doi: 10.5006/1.3284043
[33] Cottis R A, Loto C A. Electrochemical noise generation during SCC of a high-strength carbon steel [J]. Corrosion, 1990, 46: 12
doi: 10.5006/1.3585059
[34] Loto C A, Cottis R A. Electrochemical noise generation during stress corrosion cracking of the high-strength aluminum AA 7075-T6 alloy [J]. Corrosion, 1989, 45: 136
doi: 10.5006/1.3577831
[35] Loto C A, Cottis R A. Electrochemical noise generation during stress corrosion cracking of alpha-brass [J]. Corrosion, 1987, 43: 499
doi: 10.5006/1.3583893
[36] Watanabe Y, Kondo T. Current and potential fluctuation characteristics in intergranular stress corrosion cracking processes of stainless steels [J]. Corrosion, 2000, 56: 1250
doi: 10.5006/1.3280513
[37] Leban M, ? Bajt, Legat A. Detection and differentiation between cracking processes based on electrochemical and mechanical measurements [J]. Electrochim. Acta, 2004, 49: 2795
doi: 10.1016/j.electacta.2004.01.042
[38] Breimesser M, Ritter S, Seifert H P, et al. Application of electrochemical noise to monitor stress corrosion cracking of stainless steel in tetrathionate solution under constant load [J]. Corros. Sci., 2012, 63: 129
doi: 10.1016/j.corsci.2012.05.017
[39] Anita T, Pujar M G, Shaikh H, et al. Assessment of stress corrosion crack initiation and propagation in AISI type 316 stainless steel by electrochemical noise technique [J]. Corros. Sci., 2006, 48: 2689
doi: 10.1016/j.corsci.2005.09.007
[40] Calabrese L, Bonaccorsi L, Galeano M, et al. Identification of damage evolution during SCC on 17-4 PH stainless steel by combining electrochemical noise and acoustic emission techniques [J]. Corros. Sci., 2015, 98: 573
doi: 10.1016/j.corsci.2015.05.063
[41] Acu?a-González N, García-Ochoa E, González-Sánchez J. Assessment of the dynamics of corrosion fatigue crack initiation applying recurrence plots to the analysis of electrochemical noise data [J]. Int. J. Fatigue, 2008, 30: 1211
[42] Stewart J, Wells D B, Scoot P M, et al. Electrochemical noise measurements of stress corrosion cracking of sensitized austenitic stainless steel in high-purity oxygenated water at 288℃ [J]. Corros. Sci., 1992, 33: 73
doi: 10.1016/0010-938X(92)90018-X
[43] Manahan M P, MacDonald D D, Peterson A J. Determination of the fate of the current in the stress-corrosion cracking of sensitized type 304 SS in high temperature aqueous systems [J]. Corros. Sci., 1995, 37: 189
doi: 10.1016/0010-938X(94)00129-T
[44] Watanabe Y, Kain V, Kobayashi M. Electrochemical transients observed during slow strain rate test of alloy 600 in borated and lithiated high temperature water [J]. JSME Int. J. Ser. A, 2002, 45: 476
[45] Arganis-Juarez C R, Malo J M, Uruchurtu J. Electrochemical noise measurements of stainless steel in high temperature water [J]. Nucl. Eng. Des., 2007, 237: 2283
doi: 10.1016/j.nucengdes.2007.04.010
[46] Kim S W, Kim H P. Electrochemical noise analysis of PbSCC of Alloy 600 SG tube in caustic environments at high temperature [J]. Corros. Sci., 2009, 51: 191
doi: 10.1016/j.corsci.2008.10.014
[47] Ritter S, Seifert H P. Influence of reference electrode distance and hydrogen content on electrochemical potential noise during SCC in high purity, high temperature water [J]. Corros. Eng. Sci. Technol., 2013, 48: 199
doi: 10.1179/1743278212Y.0000000061
[48] Ritter S, Seifert H P. Detection of SCC initiation in austenitic stainless steel by electrochemical noise measurements [J]. Mater. Corros., 2013, 64: 683
[49] Hou Y, Aldrich C, Lepkova K, et al. Analysis of electrochemical noise data by use of recurrence quantification analysis and machine learning methods [J]. Electrochim. Acta, 2017, 256: 337
doi: 10.1016/j.electacta.2017.09.169
免責聲明:本網站所轉載的文字、圖片與視頻資料版權歸原創作者所有,如果涉及侵權,請第一時間聯系本網刪除。
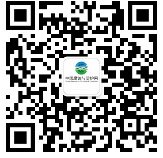
官方微信
《中國腐蝕與防護網電子期刊》征訂啟事
- 投稿聯系:編輯部
- 電話:010-62316606-806
- 郵箱:fsfhzy666@163.com
- 中國腐蝕與防護網官方QQ群:140808414