摘要
對高氮奧氏體不銹鋼在400 ℃不同相對流速 (0、0.92、1.27、1.61和2.01 m/s)、氧飽和的液態鉛鉍合金 (LBE) 中進行1000 h的腐蝕實驗。采用掃描電鏡 (SEM)、能譜儀 (EDS)、X射線衍射 (XRD) 對腐蝕后的試樣表面和截面進行分析。結果表明:相對流速對試樣的腐蝕行為有較大影響:靜態試樣,初始表面的氧化層可有效阻止高氮鋼的進一步氧化;動態試樣,表面初始氧化層遭到破壞,出現氧化腐蝕和溶解腐蝕共存狀態。相對流速從0增至0.92 m/s,初始氧化層的破壞導致表層以下的合金發生擴散氧化,以氧化腐蝕為主;相對流速從0.92 m/s增加到2.01 m/s,較大的相對流速將擴散至表面的合金元素及時帶走,溶解腐蝕占比逐漸增多,氧化腐蝕逐漸減少。氧化腐蝕產物為具有雙層結構的氧化物顆粒,外層為疏松多孔的Fe3O4,內層為 (Fe,Cr)3O4。
關鍵詞: 高氮奧氏體不銹鋼 ; 鉛鉍共晶合金 ; (LBE) ; 相對流速 ; 元素擴散 ; 氧化腐蝕
液態鉛鉍合金 (LBE) 因其優良的物理學和熱力學性能是第四代反應堆冷卻劑和加速器驅動次臨界系統 (ADS) 散列靶和冷卻劑的首選材料[1]。但LBE與結構鋼材料之間的相容性,一直是阻礙ADS開發和使用的關鍵問題,尤其是高溫流動的LBE,會通過溶解、沖刷等一系列物理化學作用,對結構鋼造成嚴重的腐蝕,從而威脅核反應堆的安全運行[2]。
奧氏體不銹鋼作為ADS系統的候選結構材料,關于其在LBE中的腐蝕行為,研究人員進行了一系列的研究[3,4]。文獻[5-7]對316L不銹鋼在靜態LBE中的腐蝕行為進行了詳細的研究,結果顯示,在腐蝕過程中出現了溶解腐蝕和氧化腐蝕,并指出其溶解機理為元素的選擇性浸出和非選擇性浸出導致的不銹鋼鐵素體化。Wang等[8]研究了結構鋼化學成分對腐蝕的影響,結果表明高Cr低Ni鋼表現出較好的抗LBE腐蝕性能。Zhang等[9]詳細地闡述了多種鋼在液態鉛鉍合金中的氧化腐蝕機制,研究表明氧濃度、LBE流速、結構鋼成分、以及溫度都在結構鋼的腐蝕中起著重要作用,其中氧化層厚度取決于氧化速率和傳質速率,而不同流速的LBE則會對物質的傳輸速率有較大影響。高氮奧氏體不銹鋼是以N代替Ni的新型奧氏體不銹鋼,滿足了核用結構鋼低Ni高Cr的要求[10]。但目前關于其在液態LBE中的腐蝕行為尚未見明確報道。
本文研究高氮奧氏體不銹鋼H1在400 ℃氧飽和LBE中1000 h的腐蝕行為,觀察不同相對流速 (0、0.92、1.27、1.61和2.01 m/s) 下試樣表面發生的變化,分析高氮奧氏體不銹鋼在流動的液態鉛鉍合金中的腐蝕機理,探索高氮奧氏體不銹鋼在未來核反應堆中應用的可能性,為高氮奧氏體不銹鋼在未來核反應堆冷卻劑主管道的應用提供可行性參考。
1 實驗方法
實驗材料為H1高氮奧氏體不銹鋼,化學成分(質量分數,%):C 0.032,Si 0.019,Mn 19.120,P 0.027,S 0.016,Cr 17.210,Mo 2.680,Ni 1.200,N 0.527,Fe余量。實驗用LBE成分 (質量分數) 為:Pb 44.500%,Bi 55.500%,雜質總含量不超過0.0001%。
實驗采用T型試樣,具體尺寸如圖1所示。實驗開始前,需將試樣打磨拋光、清洗干燥。
圖1 T型試樣尺寸
流動LBE腐蝕裝置如圖2所示,該裝置可使結構材料在流動 (0~5 m/s) 的氧飽和LBE中進行不同溫度 (≤600 ℃) 的腐蝕實驗。
圖2 腐蝕試驗裝置
試樣盤上從軸線到樣品的距離L分別為85 mm (P1)、120 mm (P2)、150 mm (P3)、190 mm (P4)。根據式 (1) 計算試樣中線處的線速度:
實驗轉速 (n) 為124 r/min,計算可得P1、P2、P3、P4的中心線速度 (V1) 分別為1.10、1.56、1.95、2.46 m/s。利用FLUENT仿真軟件模擬LBE在樣品表面的速度分布。圖3為試樣表面LBE速度的剖面圖。
圖3 FLUENT模擬的試樣表面LBE速度剖面圖
經分析確定LBE (V2) 在P1、P2、P3和P4位置的流速分別為0.178、0.288、0.343和0.455 m/s。試樣表面的相對速度 (V) 是試樣表面中心線速度 (V1) 和LBE (V2) 速度之差,因此,試樣的相對速度 (V) 分別為0.92、1.27、1.61和2.01 m/s。
實驗測試期間,將試樣安裝在圓盤試驗臺上,并在400 ℃下浸入LBE中。LBE中的氧飽和度 (Co) 通過下式計算[11]:
式中,T為LBE的溫度,(K)。當溫度為400 ℃時,Co為1.41×10-4% (質量分數)。實驗分為靜態與動態兩部分,靜態部分將試樣放入腐蝕裝置中,在400 ℃的靜態LBE中暴露1000 h,試樣標記為H1-0;動態部分將試樣依次放在試樣盤的不同位置,使試樣在400 ℃相對流速分別為0.92、1.27、1.61和2.01 m/s的液態LBE中暴露1000 h,試樣分別標記為H1-1、H1-2、H1-3、H1-4。同一相對流速均放置3個平行試樣。
腐蝕實驗結束后,從試樣中切下兩部分,一部分對試樣表面進行檢測,這些樣品在室溫下采用體積比為1∶1∶1的CH3COOH、H2O2、C2H5OH的混合溶液浸泡清洗,去除粘附的Pb-Bi[5];另一部分用于檢測橫截面,這部分試樣不經清洗直接嵌入環氧樹脂中,用砂紙打磨后,再進行機械拋光。
分別用FEI NovaNano450型掃描電鏡 (SEM) 及其配備的能譜儀 (EDS) 和D8 ADVANCE X射線衍射儀 (XRD) 對腐蝕試樣的表面和截面微觀形貌、元素組成及分布和表面物相進行觀察與分析。
2 結果與分析
2.1 腐蝕試樣表面分析
圖4為不同相對流速下腐蝕1000 h后試樣表面的SEM像。圖4a~e分別對應試樣H1-0、H1-1、H1-2、H1-3與H1-4,不同相對流速下的腐蝕試樣表面均出現了球狀化合物。圖4a試樣表面有極少量化合物;圖4b~e覆蓋在試樣表面的化合物較多,且分布具有方向性。在同一相對流速的試樣表面選擇5個區域,利用ImageJ軟件計算出金屬基體表面化合物覆蓋率并取其均值,不同相對流速下試樣表面的覆蓋率如圖5所示。化合物的覆蓋率隨相對流速的增加先增大后減小,在相對流速為0.92 m/s時達到最大,覆蓋率為61.59%。
圖4 不同相對流速下腐蝕1000 h試樣表面SEM像
圖5 不同相對流速下試樣表面化合物覆蓋率
為確定腐蝕試樣表面球狀化合物的物相,對圖4e局部區域放大觀察,結果如圖6a所示。分別對圖6a中A、B兩點進行EDS分析,結果如圖6b和c所示。
圖6 試樣H1-4腐蝕表面SEM像和EDS元素分析
圖6a點A處為試樣在LBE中腐蝕1000 h后表面出現的球狀化合物,主要元素為Fe和O,除此之外還有少部分Pb、Cr、N和Mn;點B處為腐蝕后的試樣基體,主要元素為Fe、Cr、Mn。
圖7為不同相對流速下腐蝕試樣表面XRD譜。XRD衍射峰的強度與物相的含量有一定關系,試樣H1-1、H1-2表面氧化物含量較多,XRD圖譜出現了Fe3O4和 (Fe,Cr)3O4衍射峰,而試樣H1-0、H1-3、H1-4表面氧化物含量較少,僅檢測出基體相。
圖7 不同相對流速下試樣腐蝕表面的XRD譜
2.2 腐蝕截面分析
圖8為不同相對流速下腐蝕1000 h后試樣截面SEM圖以及對應的EDS線掃描結果。圖8a中試樣基體與LBE交界處相對平坦,未出現明顯腐蝕現象,與圖4a結果一致。圖8b為試樣H1-0截面EDS線掃描結果。可見,從基體/LBE界面到基體方向出現了元素擴散層,主要表現為基體中的Fe、Cr、Mn向液態LBE中擴散,液態LBE中的Pb、Bi向金屬基體滲透。文獻[12]中提出,由于不銹鋼表面鈍化膜的存在,能在一定程度上阻礙基體元素擴散溶解以及Pb、Bi的滲透,延長試樣氧化所需的孕育期,但由于鈍化膜較薄,EDS也難以看出,因此起到的延緩作用有限。
圖8 不同相對流速下腐蝕截面SEM像和EDS圖
圖8c、e、g、i中試樣基體與鉛鉍合金交界處均出現顆粒狀腐蝕物,且腐蝕產物顆粒一部分暴露在金屬基體表面,一部分鑲嵌在基體中,兩部分相對于原始界面呈近似對稱分布。圖8d、f、h、j為試樣界面腐蝕產物顆粒EDS線處元素掃描結果,根據元素含量的變化趨勢可以看到,不同相對流速下試樣界面處的腐蝕產物均具有明顯的雙層結構,雙層結構以原始界面為分界線分為內外兩層,外層富Fe、O,還有少量的Pb、Bi,內層由Fe、O、Cr、Mn組成。根據O、Pb、Bi、Fe、Cr等元素含量的變化,將試樣H1-4截面腐蝕產物分為A、B兩個區域,如圖8i所示,并對每個區域進行EDS點分析,結果如圖8k和l所示。通過EDS分析可見,形成于原始界面LBE一側的外氧化層區域 (A區域),主要含有Fe和O;形成于原始界面基體一側的內氧化層區域 (B區域),主要含有Fe、Cr、O,結合表面和XRD分析結果,可知外氧化層A區域Fe3O4,內氧化層中Cr含量略高于基體,而XRD圖譜中并未出現Cr氧化物的衍射峰,據文獻[13]可知,Cr是以合金元素的形式固溶在Fe3O4中形成Fe-Cr尖晶石晶體,故內氧化層B區域為尖晶石結構的 (Fe,Cr)3O4。隨著相對流速的增大,內外氧化層中O、Cr含量不斷增加,Fe含量不斷降低,這是由于流速的增加導致界面處介質中合金元素濃度降低,化學勢增大,傳質效率提高,加速Cr、Fe向外擴散,O向內滲透,Cr在尖晶石中的擴散系數與Fe相比小三個數量級,因此Fe可以穿過尖晶石層與O反應,而Cr在尖晶石層富集[14]。另外根據內外層中Pb、Bi含量的變化,可以發現在外氧化層中含有一定量的Pb、Bi,這是由于外層Fe3O4疏松多孔,難以阻止Pb、Bi、O的滲透;而內氧化層是固溶形成的Fe-Cr尖晶石晶體,Cr原子半徑比Fe原子小,固溶形成的Fe-Cr尖晶石點陣常數小于Fe3O4,能夠更有效地阻止Pb、Bi的滲透,尤其是當相對流速增大時,傳質過程加快,尖晶石中的Cr含量升高,對阻礙Pb、Bi元素滲透作用更加明顯。
3 腐蝕機理分析
根據不同相對流速下腐蝕試樣表面和截面的分析,試樣表面的腐蝕與試樣所處的狀態有關。試樣H1-0表面氧化物數量極少,原因是當試樣處于靜止狀態且溫度不高時 (≤400 ℃),不銹鋼表面致密的氧化層能有效防止金屬氧化[15];由于金屬表面的氧化膜較薄,僅有1~10 nm,因此當試樣處于流動的LBE中時,金屬表面致密的氧化層遭到沖刷破壞,此時金屬的腐蝕由氧化和溶解共同控制[16]。當相對流速較小 (0.92 m/s) 時,試樣H1-1表面氧化物覆蓋率最高,原因是浸潤在LBE中的試樣在化學勢的驅動下,試樣表層的Fe、Cr、Mn擴散溶解進入LBE中,同時LBE中的Pb、Bi、O向試樣表層滲透,而此時由于相對流速較小,質量傳輸效率較低,基體LBE界面處合金元素濃度達到飽和或平衡的狀態,大量氧化物在試樣表面形核,由于Fe、Cr氧化物的標準生成自由能不同,在元素擴散過程中,Cr優先與O結合生成自由能較低的Cr氧化物,而Cr氧化物穩定性較差,很快與Fe反應生成 (Fe,Cr)3O4形成初始氧化層,隨著腐蝕的進行,基體中的Fe穿過含Cr氧化物層與液態LBE中的O結合形成Fe3O4,形成外氧化層,初始氧化物層轉變為內氧化層[17]。而初始氧化物的存在為周圍基體元素的擴散以及O的滲透提供快捷通道,由于Cr、Fe在尖晶石晶體中擴散系數不同,內外氧化層以球狀的方式向四周生長。當流速增大時,試樣表面的氧化物隨相對流速的增加逐漸減少,且從試樣截面氧化物處線掃描結果可以發現,內氧化層中的Fe濃度隨相對流速的增加不斷下降,Cr濃度不斷增加 (如圖8f、h、j所示),這是由于流速的增加使得質量遷移速率增加[18],溶解于LBE中的合金元素很快被帶走,導致試樣周圍LBE中合金元素濃度較低,化學勢增大,合金元素的擴散速度加快,金屬的腐蝕逐漸由以氧化腐蝕為主轉變為以溶解腐蝕為主[8]。腐蝕試樣表面氧化物分布具有方向性,且方向與機械拋光留下的劃痕以及LBE流向相同,原因在于劃痕的存在增大了反應表面積,導致劃痕處的界面能升高,氧化物在劃痕處優先生長[19]。
4 結論
(1) 高氮奧氏體不銹鋼H1在不同相對流速下腐蝕1000 h后,靜態試樣表面原始氧化膜能夠有效阻止合金元素溶解,試樣未出現明顯的氧化現象;動態試樣,由于液態LBE的沖刷作用,試樣表面原始氧化膜遭到破壞,試樣的氧化和溶解同時進行。
(2) 隨著相對流速從0增至0.92 m/s,試樣表面氧化物增多,原因是初始氧化層的破壞導致表層以下的合金發生擴散氧化,試樣主要發生氧化腐蝕;相對流速從0.92增加到2.01 m/s,試樣表面氧化物隨流速的增加逐漸減少,這是由于較大的相對流速將擴散至表面的合金元素及時帶走,腐蝕逐漸由氧化腐蝕轉變為溶解腐蝕。
(3) 氧化腐蝕產物為具有雙層結構的氧化物顆粒,外層為疏松多孔的Fe3O4,內層為尖晶石結構的 (Fe,Cr)3O4。
參考文獻
1 Kurata Y, Futakawa M, Saito S. Corrosion behavior of steels in liquid lead bismuth with low oxygen concentrations [J]. J. Nucl. Mater., 2008, 373: 164
2 Zhang J, Li N, Chen Y T, et al. Corrosion behaviors of US steels in flowing lead bismuth eutectic (LBE) [J]. J. Nucl. Mater., 2005, 336: 1
3 Wu Y C, Huang Q Y, Bai Q Y, et al. Preliminary experimental study on the corrosion of structural steels in liquid lead bismuth loop [J]. Chin. J. Nucl. Sci. Eng., 2010, 30: 238
3 吳宜燦, 黃群英, 柏云清等. 液態鉛鉍回路設計研制與材料腐蝕實驗初步研究 [J]. 核科學與工程, 2010, 30: 238
4 Aiello A, Azzati M, Benamati G, et al. Corrosion behaviour of stainless steels in flowing LBE at low and high oxygen concentration [J]. J. Nucl. Mater., 2004, 335: 169
5 Sapundjiev D, Van Dyck S, Bogaerts W. Liquid metal corrosion of T91 and A316L materials in Pb-Bi eutectic at temperatures 400-600℃ [J]. Corros. Sci., 2006, 48: 577
6 Yamaki E, Ginestar K, Martinelli L. Dissolution mechanism of 316L in lead-bismuth eutectic at 500 ℃ [J]. Corros. Sci., 2011, 53: 3075
7 Koury D, Johnson A L, Ho T, et al. Analysis of bi-layer oxide on austenitic stainless steel, 316L, exposed to lead-bismuth eutectic (LBE) by x-ray photoelectron spectroscopy (XPS) [J]. J. Nucl. Mater., 2013, 440: 28
8 Wang Z H, Chen H. Flowing liquid metal corrosion of structural steels in the Pb-Bi eutectic [J]. Adv. Mat. Res., 2012, 581: 1040
9 Zhang J S, Li N. Review of the studies on fundamental issues in LBE corrosion [J]. J. Nucl. Mater., 2008, 373: 351
10 Shi F, Cui W F, Wang L J, et al. Advance in the research of high-nitrogen austenitic stainless steels [J]. Shanghai Met., 2006, 28(5): 45
10 石鋒, 崔文芳, 王立軍等. 高氮奧氏體不銹鋼研究進展 [J]. 上海金屬. 2006, 28(5): 45
11 Martinelli L, Balbaud-Célérier F, Terlain A, et al. Oxidation mechanism of Fe-9Cr-1Mo steel by liquid Pb-Bi eutectic alloy (part Ⅲ) [J]. Corros. Sci., 2008, 50: 2549
12 Chakraborty P, Singh V, Bysakh S, et al. Short-term corrosion behavior of indian RAFM steel in liquid Pb-Li: Corrosion mechanism and effect of alloying elements [J]. J. Nucl. Mater., 2019, 520: 208
13 Li M Y, Zhang Z Z, Chen L L, et al. Study on corrosion products of T91 and 316L steels in oxygen controlled LBE for 600 hrs [J]. Nucl. Sci. Eng., 2018, 38: 784
13 李明楊, 張志忠, 陳劉利等. T91和316L鋼在氧控鉛鉍中600小時后腐蝕產物分析 [J]. 核科學與工程, 2018, 38: 784
14 Luo M, Lei Y C, Chen G, et al. Effect of flow rate on corrosion behavior of 316L stainless steel welding seam in liquid lead bismuth [J]. Trans. China Weld. Inst., 2019, 40(3): 65
14 羅夢, 雷玉成, 陳鋼等. 相對流速對316L鋼焊縫在液態鉛鉍合金中腐蝕行為的影響 [J]. 焊接學報, 2019, 40(3): 65
15 Xie B, Hu R, Weng K P. Study of surficial corrosion of 304L stainless steel in liquid LiPb alloy [J]. Sichuan. Chem. Ind., 2009, 12(1): 30
15 謝波, 胡睿, 翁葵平. 304L不銹鋼在液態鋰鉛合金中的表面腐蝕研究 [J]. 四川化工, 2009, 12(1): 30
16 Kamachi M U, Baldev R. Translated by Li J, Huang Y H. High Nitrogen Steels and Stainless Steels-manufacturing, Properties and Applications [M]. Beijing: Chemical Industry Press, 2006: 110
16 卡曼奇·曼德里U, 貝德威R著, 李晶, 黃運華譯. 高氮鋼和不銹鋼-生產、性能與應用 [M]. 北京: 化學工業出版社, 2006: 110
17 Tsisar V, Schroer C, Wedemeyer O, et al. Corrosion behaovior of austenitic 1.4970, 316L and 1.4571 in flowing LBE at 450 and 550 with 10-7mass% dissolved oxygen [J]. J. Nucl. Mater., 2014, 454: 332
18 Ju N, Lei Y C, Chen G, et al. Corrosion behavior of stainless steel 410 in flowing lead-bismuth eutectic alloy at 550 ℃ [J]. Mater. Rep., 2019, 33: 3489
18 鞠娜, 雷玉成, 陳鋼等. 410不銹鋼在550 ℃流動的鉛鉍共晶合金中的腐蝕行為 [J]. 材料導報, 2019, 33: 3489
19 Zhang Z M, Wang J Q. Effects of surface condition on corrosion and stress corrosion cracking of alloy 690TT [J]. J. Chin. Soc. Corros. Prot., 2011, 31: 441
19 張志明, 王儉秋. 表面狀態對690TT合金腐蝕及應力腐蝕行為的影響 [J]. 中國腐蝕與防護學報, 2011, 31: 441
免責聲明:本網站所轉載的文字、圖片與視頻資料版權歸原創作者所有,如果涉及侵權,請第一時間聯系本網刪除。
-
標簽: 高氮奧氏體不銹鋼, 鉛鉍共晶合金(LBE), 相對流速, 元素擴散, 氧化腐蝕
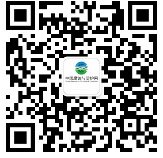
官方微信
《中國腐蝕與防護網電子期刊》征訂啟事
- 投稿聯系:編輯部
- 電話:010-62316606-806
- 郵箱:fsfhzy666@163.com
- 中國腐蝕與防護網官方QQ群:140808414