摘要
采用浸泡實驗、腐蝕形貌觀察、腐蝕產(chǎn)物分析及電化學(xué)測試研究了5083鋁合金和30CrMnSiA鋼電偶對在不同Cl-濃度下的電偶腐蝕行為,并分析了電偶對在0.6 mol/L NaCl溶液中的電偶腐蝕機制。隨著NaCl濃度從0.05 mol/L增加到0.85 mol/L,Cl-的活性減弱,溶解氧含量降低,陰極反應(yīng)速率降低;電偶對在0.85 mol/L NaCl溶液中的電偶電流密度最小。動電位極化曲線和阻抗譜測試結(jié)果表明,電偶腐蝕過程中,鋁合金的耐蝕性先降低再增大,表面生成的腐蝕產(chǎn)物抑制了鋁合金的溶解;30CrMnSiA鋼的腐蝕速率前期較小,后隨著腐蝕時間延長而增大;腐蝕15 d后,鋼的腐蝕產(chǎn)物參與陰極反應(yīng),加快電荷傳遞速率,導(dǎo)致5083鋁合金和30CrMnSiA結(jié)構(gòu)鋼的腐蝕速率增大。
關(guān)鍵詞: 5083鋁合金 ; 30CrMnSiA鋼 ; 電偶腐蝕 ; Cl-濃度 ; 腐蝕行為
鋁合金密度低,抗疲勞性能較高,具有較高的比強度、比剛度,是工業(yè)中應(yīng)用廣泛的有色金屬結(jié)構(gòu)材料之一。其耐腐蝕性能[1]良好,在海洋工程中的應(yīng)用也越來越廣泛。其中,5083鋁合金是Al-Mg系鋁合金,具有極佳的成形加工、焊接性能和優(yōu)良的耐腐蝕性能,在船舶、汽車、飛機、地鐵、輕軌等有大量應(yīng)用。鋁合金表面可自發(fā)生成一層鈍化膜,對基體起到保護作用,使其具有較強的耐蝕性。但是,在使用過程中,鋁合金會出現(xiàn)不同形式的腐蝕現(xiàn)象[2,3]。30CrMnSiA高強鋼具有良好的加工性,抗疲勞性能較高,被應(yīng)用于飛機各種特殊耐磨零配件的制作。在實際應(yīng)用過程中,鋁合金與高強鋼不可避免地會發(fā)生接觸,當(dāng)存在電解質(zhì)溶液時,由于材料間自腐蝕電位的差異[4],極易發(fā)生電偶腐蝕[5]。沿海地區(qū)的飛機服役區(qū)域廣,面臨的腐蝕環(huán)境復(fù)雜,特別是在高氯和高濕度的海洋大氣環(huán)境下[6],飛機結(jié)構(gòu)件極易發(fā)生腐蝕[7],航空材料的耐蝕性對飛機的安全性有直接的影響。鋁合金的表面極易產(chǎn)生鈍化膜,具有較好的耐腐蝕性,但海洋大氣中的陰離子[8] (主要是Cl-) 會破壞鋁合金表面的鈍化膜并誘發(fā)點蝕[9],從而加速鋁合金的腐蝕。距離海岸線越近,大氣中Cl-含量越高[10,11],鋁合金的腐蝕愈嚴(yán)重,Cl-對鋁合金具有較強的腐蝕作用。陳躍良等[12]研究了7B04鋁合金和30CrMnSiA合金鋼試樣的電化學(xué)性能,結(jié)果表明,隨著NaCl濃度增大,自腐蝕電流變大;電偶電流與陰陽極面積比和NaCl濃度有關(guān),陰陽極面積比增大或NaCl濃度升高[13]均會導(dǎo)致電偶腐蝕效應(yīng)增強。Yao等[14]研究了5383鋁合金分別與907鋼和鋁青銅組成的兩種電偶體系的早期電偶腐蝕平面分布,結(jié)果表明5383鋁合金為陽極,907鋼和鋁青銅則始終為陰極受到保護;與偶接點的距離增大,電偶電流降低,且遠端的電流分布較為均勻。當(dāng)鋁合金和低合金鋼接觸發(fā)生電偶腐蝕時,鋁合金的自腐蝕電位低,通常作為電偶腐蝕反應(yīng)的陽極,其腐蝕速率被加速,低合金鋼作為陰極也會發(fā)生腐蝕,對電偶體系產(chǎn)生影響。在這種電偶腐蝕體系下,陰陽極的腐蝕行為及過程較復(fù)雜。目前關(guān)于電偶對中陰陽極都發(fā)生腐蝕的復(fù)雜電偶腐蝕行為的研究較少,對其電偶腐蝕機制的探討不夠深入,因此研究鋁合金和高強鋼的電偶腐蝕行為對材料的應(yīng)用具有重要意義。
本文以5083鋁合金和30CrMnSiA鋼為研究對象,分析了電偶對在不同濃度NaCl溶液中電偶腐蝕行為,以及電偶對在0.6 mol/L NaCl溶液短期浸泡后的電偶腐蝕機制,為鋁合金的防腐工作提供依據(jù)。
1 實驗方法
實驗用材料30CrMnSiA鋼及5083鋁合金成分如表1所示。兩種合金試樣都加工成10 mm×10 mm×4 mm方片。用于電化學(xué)測試的試樣用銅導(dǎo)線焊接,環(huán)氧樹脂密封,暴露的工作面積為1 cm2。兩種試樣的工作面用砂紙水磨至1200目,清洗,干燥,置于干燥器中備用。30CrMnSiA鋼及5083鋁合金電偶對試樣處于電連接狀態(tài),間距為3 cm,分別浸泡在0.05、0.1、0.6和0.85 mol/L NaCl溶液中,溫度為25 ℃,腐蝕周期為15 d。每天測量電偶對的電偶電流和電偶電位;在腐蝕周期為1,5,7,10和15 d時,分別測量0.6 mol/L濃度下兩個電極的弱極化曲線和電化學(xué)阻抗譜。
表1 5083鋁合金和30CrMnSiA鋼的化學(xué)成分表
采用CHI660E電化學(xué)工作站測試電偶對的開路電位 (OCP)、動電位極化曲線和電化學(xué)阻抗譜 (EIS)。采用三電極體系,其中試樣為工作電極,飽和甘汞電極 (SCE) 為參比電極,鉑片作為輔助電極,介質(zhì)為NaCl溶液,試樣在溶液中穩(wěn)定30 min后測試開路電位1800 s,動電位極化曲線掃描區(qū)間為-300~+700 mV vs OCP,掃描速度為1 mV/s。EIS測試在開路電位下進行,掃描頻率范圍為105~10-2 Hz,信號幅值為10 mV。
實驗進行到15 d時,取出電極,用ZEISS SUPRA 55掃描電鏡 (SEM) 對試樣表面的腐蝕形貌進行微觀分析,并結(jié)合D/MAX-RA12KW型X射線衍射儀 (XRD) 分析腐蝕產(chǎn)物的物相組成。
2 結(jié)果與討論
2.1 腐蝕形貌分析
圖1和2分別是5083鋁合金和30CrMnSiA鋼電偶對在不同Cl-濃度溶液中腐蝕1 d后的宏觀和SEM微觀形貌圖。由圖1可知,鋼表面腐蝕較輕微,而鋁合金表面失去金屬光澤,表面氧化膜層被破壞,說明鋁合金在電偶腐蝕效應(yīng)中加速腐蝕,為電偶對的陽極,鋼為陰極。從SEM形貌圖中可見,鋁合金表面生成顆粒狀和絮狀腐蝕產(chǎn)物,在0.05和0.1 mol/L NaCl溶液中表面腐蝕程度較大,腐蝕產(chǎn)物層開裂;在0.6和0.85 mol/L NaCl溶液中表面分布著疏松的絮狀腐蝕產(chǎn)物,在前一條件下的腐蝕產(chǎn)物有輕微地開裂,在后一條件下腐蝕程度較輕微。圖3是鋁鋼電偶對在不同Cl-濃度溶液中腐蝕15 d后的腐蝕產(chǎn)物SEM圖。看出,鋁合金表面覆蓋一層較為致密的腐蝕產(chǎn)物,腐蝕產(chǎn)物龜裂成不規(guī)則的片狀;隨著NaCl溶液濃度的增大,腐蝕產(chǎn)物層增多,外表面的腐蝕產(chǎn)物比較疏松,呈塊狀堆積,容易脫落,存在明顯的裂紋。鋼表面腐蝕產(chǎn)物大而密集,腐蝕產(chǎn)物覆蓋在表面,呈苞狀分布;隨著溶液濃度增大,表面腐蝕產(chǎn)物有部分開裂,腐蝕程度加重。在0.85 mol/L的溶液中,外層腐蝕產(chǎn)物致密地覆蓋著,內(nèi)層腐蝕產(chǎn)物出現(xiàn)裂紋,腐蝕產(chǎn)物對基體的保護性下降,溶液中Cl-等含有腐蝕性的離子可以通過裂縫滲透到基體,導(dǎo)致腐蝕加劇。
圖1 5083鋁合金和30CrMnSiA鋼電偶對在不同Cl-濃度溶液中浸泡1 d后的宏觀形貌
圖2 電偶對在不同Cl-濃度溶液中浸泡1 d后5083鋁合金的腐蝕形貌
圖3 5083鋁合金和30CrMnSiA鋼在不同Cl-濃度溶液中浸泡15 d后的腐蝕形貌
2.2 腐蝕產(chǎn)物分析
在不同Cl-濃度溶液中浸泡后的5083鋁合金和30CrMnSiA鋼電偶對中5083鋁合金EDS分析結(jié)果如表2所示。圖4是電偶對在不同Cl-濃度溶液中浸泡后的腐蝕產(chǎn)物XRD譜。從圖4并結(jié)合EDS分析可知,在不同Cl-濃度溶液中,Al2O3和Al(OH)3是鋁合金表面腐蝕產(chǎn)物的主要物相,在形貌圖中呈白色;鋼表面腐蝕產(chǎn)物主要有FeOOH和Fe3O4,電極表面內(nèi)層是暗黑色的Fe3O4腐蝕產(chǎn)物,電極表面生成了更加穩(wěn)定的FeOOH,說明其中部分的Fe3O4會轉(zhuǎn)化為FeOOH[15]。
表2 在不同Cl-濃度溶液中浸泡15 d后的電偶對中鋁合金腐蝕區(qū)域的EDS分析結(jié)果
圖4 5083鋁合金和30CrMnSiA鋼在不同Cl-濃度溶液中浸泡15 d后的腐蝕產(chǎn)物XRD譜
2.3 開路電位分析
圖5是5083鋁合金和30CrMnSiA鋼在0.6 mol/LNaCl溶液中的開路電位圖。鋼和鋁合金的開路電位分別為-0.67和-0.76 V,電位差值為90 mV,大于電偶腐蝕發(fā)生的闕值 (50 mV)。從熱力學(xué)角度看,鋁合金和鋼組成電偶對會發(fā)生電偶腐蝕,鋁合金做陽極被加速腐蝕;鋼為陰極,腐蝕速率減緩,這與宏觀形貌觀察的結(jié)果一致。
圖5 5083鋁合金和30CrMnSiA鋼在0.6 mol/L NaCl溶液中的開路電位圖
2.4 動電位極化曲線分析
圖6分別為5083鋁合金和30CrMnSiA鋼在不同Cl-濃度下的動電位極化曲線圖,表3為陰極外推法獲得的電化學(xué)參數(shù)。由圖6可知,當(dāng)溶液濃度分別為0.05、0.1和0.6 mol/L時,極化曲線中的陰極區(qū)出現(xiàn)擴散特征,表示陰極反應(yīng)由傳質(zhì)過程控制;極化曲線的陽極段出現(xiàn)鈍化區(qū),鈍化區(qū)較窄。由表3可知,鋁合金在0.05、0.1和0.6 mol/L下的點蝕電位 (Epit) 分別為-660、-700和-754 mV,而在0.85 mol/L下未出現(xiàn)點蝕電位。隨著濃度增大,腐蝕電位 (Ecorr) 和點蝕電位都負向移動,說明隨著濃度增大,5083鋁合金點蝕電位降低,電極的耐蝕性降低。由鋼在不同濃度下的動電位極化曲線可知,隨著濃度從0.05 mol/L增加到0.6 mol/L,鋼的腐蝕電位正移,腐蝕傾向降低,在0.6 mol/L時達到-452 mV (表3);在0.85 mol/L時,腐蝕電位負移,腐蝕傾向增加。鋼的腐蝕電流密度在濃度為0.6 mol/L時最大,達到23.33 μA·cm-2。不同Cl-濃度的溶液對30CrMnSiA鋼的腐蝕行為具有一定的影響,極化曲線中的陰極區(qū)有擴散特征,說明陰極反應(yīng)過程受溶解氧含量的控制。在陽極極化區(qū),發(fā)生陽極溶解,電流密度隨過電位的增加而迅速增大,沒有鈍化區(qū);隨著過電位的增加,逐漸達到極限電流密度區(qū),電流密度不在增加。
圖6 5083鋁合金和30CrMnSiA鋼在不同Cl-濃度溶液中的動電位極化曲線圖
表3 5083鋁合金和30CrMnSiA鋼在不同Cl-濃度中的電化學(xué)參數(shù)
2.5 電偶電流分析
圖7a是鋼和鋁合金電偶對在不同濃度中電偶電流密度隨時間的變化曲線。由圖可得,在0.05、0.1、0.6和0.85 mol/L濃度下,電偶電流密度分別為20.15,30.58,5.08以及14.12 μA·cm-2。由此可知,在0.1 mol/L濃度下電偶電流密度最大,在0.85 mol/L濃度中最小。從0.05 mol/L增大到0.1 mol/L過程中,活性Cl-具有較強的反應(yīng)能力,鋁合金表面的氧化膜難以穩(wěn)定存在,容易被Cl-破壞,失去對基體的保護性。隨著濃度進一步增大,從0.6到0.85 mol/L,Al3+進入溶液的速度減慢,抑制了鋁合金的陽極極化,氧氣的溶解度降低,陰極反應(yīng)受到抑制,導(dǎo)致電偶電流密度減小。圖7b是鋼和鋁電偶對在不同濃度下浸泡不同周期時溶液pH的變化圖。由圖可知,在整個電偶腐蝕過程中,溶液的pH在5~8范圍內(nèi)變化,溶液最初呈弱酸性,并且在腐蝕的第1 d內(nèi)pH值變化趨勢最大;隨著周期增加,pH逐漸上升,最后穩(wěn)定在7.30附近。在腐蝕周期內(nèi),0.05和0.1 mol/L NaCl溶液的pH略大于0.6和0.85 mol/L NaCl溶液的值,說明在0.05和0.1 mol/L溶液中,鋁合金腐蝕溶解程度較大,反應(yīng)生成Al的氫氧化物較多,導(dǎo)致其pH略高。
圖7 5083鋁合金和30CrMnSiA鋼電偶對在不同濃度下電偶電流密度和pH隨時間的變化曲線
2.6 電偶腐蝕機理分析
圖8是5083鋁合金和30CrMnSiA鋼電偶對在0.6 mol/L NaCl溶液中浸泡不同時間的動電位極化曲線圖,采用陰極外推法獲得各極化曲線的電化學(xué)參數(shù)列于表4中。5083鋁合金作為陽極,在前期鋁合金加速溶解,腐蝕電流密度逐漸增加,第1 d為0.31 μA·cm-2,5 d后增大為2.37 μA·cm-2;同時其腐蝕電位逐漸負移,第7 d為-928 mV,相比第一天負移了87 mV。隨著腐蝕周期的增加,鋁合金表面被腐蝕產(chǎn)物覆蓋,阻礙了Al的進一步溶解,陽極腐蝕速率減小,O的含量下降,陰極反應(yīng)受到抑制。鋼的腐蝕電位 (Ecorr) 在前7 d正移,7 d后電位負移,15 d后的腐蝕電位為-640 mV,小于第1 d的腐蝕電位 (-617 mV),腐蝕趨勢先減小,7 d后腐蝕傾向增大;第1 d的腐蝕電流密度為4.40 μA·cm-2,15 d后的腐蝕電流密度增大到15.67 μA·cm-2,說明鋼在前期作為陰極時,腐蝕速率較小;在后期腐蝕速率有所增加,鋼表面產(chǎn)生的腐蝕產(chǎn)物參與了反應(yīng),形成了微電池反應(yīng)。
圖8 5083鋁合金和30CrMnSiA鋼在0.6 mol/L NaCl溶液中的動電位極化曲線
表4 5083鋁合金和30CrMnSiA鋼在0.6 mol/L NaCl溶液中的電化學(xué)參數(shù)表
圖9分別為5083鋁合金和30CrMnSiA鋼電偶對在0.6 mol/L NaCl溶液浸泡不同時間的Nyquist圖和Bode圖。鋁合金的Nyquist曲線圖由一個半圓弧和直線組成,高中頻區(qū)表現(xiàn)為電荷傳遞控制;低頻區(qū)出現(xiàn)Weber阻抗,說明在低頻區(qū),電極反應(yīng)由表面的反應(yīng)物或產(chǎn)物的擴散控制。整個過程由電荷傳遞和擴散過程共同控制。鋁合金表面生成的腐蝕產(chǎn)物覆蓋在表面,O和電荷在電極表面?zhèn)鬏斔俾蕼p小,表現(xiàn)為電極表面反應(yīng)受擴散控制。第1 d到第5 d,鋁合金阻抗譜圖中容抗弧半徑逐漸減小,電荷轉(zhuǎn)移電阻減小,電極表面對電極反應(yīng)的阻力減弱,腐蝕速率加快;第7 d到第15 d,容抗弧半徑增大,電荷轉(zhuǎn)移電阻增大,腐蝕速率降低。鋼的阻抗譜中表現(xiàn)為具有一個時間常數(shù)的容抗弧,說明電極反應(yīng)速率受電荷傳遞過程控制,容抗弧的半徑大小反映了電荷傳遞電阻的大小,在低頻區(qū)表現(xiàn)為電荷在電極表面?zhèn)鬟f的阻抗大小,阻抗值越大,說明電極表面的耐蝕性越好。由圖可知,鋼在低頻區(qū)的阻抗值隨著腐蝕周期的增加,其耐蝕性降低,在前期鋼的阻抗值較大,第15 d時鋼的阻抗值迅速下降,鋼的腐蝕反應(yīng)速率增加,電荷轉(zhuǎn)移過程易于進行。
圖9 5083鋁合金和30CrMnSiA鋼電偶對在0.6 mol/L NaCl溶液浸泡不同周期的Nyquist圖和Bode圖
圖10是用Zsimpwin軟件對圖9a和b進行擬合得到的等效電路圖。圖10a和b分別是鋁合金腐蝕前期和后期的等效電路圖,擬合數(shù)據(jù)見表5和6;鋼腐蝕過程的等效電路圖如圖10c所示。圖中,Rs表示溶液電阻,Q (CPE) 表示常相位角元件。指數(shù)n反映了電極表面粗糙度和偏離理想電容的程度,n=1時,元件為純電容 (C);n=0.5時,元件為Weber阻抗(W);n=0時,元件為純電阻 (R)。Cdl表示雙電層電容,圖10a中用Qdl來代替雙電層電容,受電極表面不均勻性而導(dǎo)致偏離雙電層電容。Rf為溶液與電極表面的電阻,Rct表示電荷傳遞電阻,Qdiff來描述傳輸及擴散過程。圖10b是電偶腐蝕15 d后鋁合金阻抗譜的等效電路圖,其中Cb和Rb分別是腐蝕產(chǎn)物層的電容和電阻。電荷的傳遞速率與腐蝕電化學(xué)過程的快慢呈正相關(guān),用Rct-1來表示腐蝕速率的快慢,Rct-1越大,腐蝕速率越快。由擬合參數(shù)可知,鋁合金在前期受電偶腐蝕效應(yīng)的影響腐蝕速率加快,鋼的腐蝕速率受到抑制;隨著電偶腐蝕的加劇,鋁合金表面和鋼表面都發(fā)生了不同程度的腐蝕,表面生成腐蝕產(chǎn)物,此時陰極反應(yīng)的電荷傳遞速率受阻,鋁合金的陽極溶解速率降低;電偶腐蝕進行到15 d時,鋼表面的電荷傳遞電阻減小,腐蝕速率增大,鋁合金陽極腐蝕反應(yīng)速率加快。
圖10 30CrMnSiA鋼及5083鋁合金阻抗譜的等效電路圖
表5 5083鋁合金阻抗譜擬合的等效電路參數(shù)
表6 30CrMnSiA鋼阻抗譜擬合的等效電路參數(shù)
2.7 電偶腐蝕機制討論
5083鋁合金和30CrMnSiA鋼組成的電偶對浸泡在0.6 mol/L NaCl溶液中時,會發(fā)生電偶腐蝕,鋁合金作陽極,發(fā)生金屬的溶解加速反應(yīng);鋼為陰極,腐蝕速率減緩,電極反應(yīng)如下:
由此可知,當(dāng)鋁合金表面腐蝕產(chǎn)物膜穩(wěn)定存在對基體產(chǎn)生保護作用時,同時鋼的表面覆蓋了低價態(tài)的腐蝕產(chǎn)物,鋁合金的腐蝕速率降低;腐蝕15 d后,鋼上腐蝕產(chǎn)物作為去極化劑參與電極反應(yīng),此時鋼的腐蝕速率增大,鋼的電荷傳遞電阻減小。
3 結(jié)論
(1) 5083鋁合金和30CrMnSiA鋼組成電偶對時,5083鋁合金作為陽極被加速腐蝕,30CrMnSiA鋼作為陰極腐蝕速率減緩;電偶對在0.05和0.1 mol/L NaCl溶液中的腐蝕程度大于在0.6和0.85 mol/L NaCl溶液中的;隨著濃度增大,Cl-的活性減弱,溶解氧含量降低,陰極反應(yīng)速率下降。
(2) 電偶對腐蝕過程中,鋁合金的耐蝕性先降低再增大,前期鋁合金受電偶腐蝕的影響溶解加速,隨著表面腐蝕產(chǎn)物的增加,鋁合金表面生成的腐蝕產(chǎn)物抑制了鋁合金的溶解;鋼的腐蝕速率前期較小,隨著腐蝕時間的增加腐蝕速率增大;在腐蝕15 d后,鋼的腐蝕產(chǎn)物參與陰極反應(yīng),電荷傳遞速率加快,導(dǎo)致鋁合金和鋼的耐蝕性降低,腐蝕速率增大。
參考文獻
1 Zaid B, Saidi D, Benzaid A, et al. Effects of pH and chloride concentration on pitting corrosion of AA6061 aluminum alloy [J]. Corros. Sci., 2008, 50: 1841
2 Knight S P, Salagaras M, Trueman A R. The study of intergranular corrosion in aircraft aluminium alloys using X-ray tomography [J]. Corros. Sci., 2011, 53: 727
3 Lee H, Kim Y, Jeong Y, et al. Effects of testing variables on stress corrosion cracking susceptibility of Al 2024-T351 [J]. Corros. Sci., 2012, 55: 10
4 El-Dahshan M E, El Din A M S, Haggag H H. Galvanic corrosion in the systems titanium/316 L stainless steel/Al brass in Arabian Gulf water [J]. Desalination, 2002, 142: 161
5 Varela F E, Kurata Y, Sanada N. The influence of temperature on the galvanic corrosion of a cast iron-stainless steel couple (prediction by boundary element method) [J]. Corros. Sci., 1997, 39: 755
6 Liu Y J, Wang Z Y, Wang B B, et al. Mechanism of galvanic corrosion of coupled 2024 Al-alloy and 316L stainless steel beneath a thin electrolyte film studied by real-time monitoring technologies [J]. J. Chin. Soc. Corros. Prot., 2017, 37: 261
6 劉艷潔, 王振堯, 王彬彬等. 實時監(jiān)測技術(shù)研究薄液膜下電偶腐蝕的機理 [J]. 中國腐蝕與防護學(xué)報, 2017, 37: 261
7 Ding Q M, Qin Y X, Cui Y Y. Galvanic corrosion of aircraft components in atmospheric environment [J]. J. Chin. Soc. Corros. Prot., 2020, 40: 455
7 丁清苗, 秦永祥, 崔艷雨. 大氣環(huán)境中飛機構(gòu)件的電偶腐蝕研究 [J]. 中國腐蝕與防護學(xué)報, 2020, 40: 455
8 Li T, Dong C F, Li X G, et al. Influence of environmental factors on atmospheric corrosion of aluminum alloys and its dynamic time dependence [J]. Corros. Sci., 2009, 30: 215
8 李濤, 董超芳, 李曉剛等. 環(huán)境因素對鋁合金大氣腐蝕的影響及其動態(tài)變化規(guī)律研究 [J]. 腐蝕與防護, 2009, 30: 215
9 Sun F L, Li X G, Lu L, et al. Corrosion behavior of 5052 and 6061 aluminum alloys in deep ocean environment of South China Sea [J]. Acta Metall. Sin., 2013, 49: 1219
9 孫飛龍, 李曉剛, 盧琳等. 5052和6061鋁合金在中國南海深海環(huán)境下的腐蝕行為研究 [J]. 金屬學(xué)報, 2013, 49: 1219
10 Zhu H M, Zheng Q F, Xie S S. Study on atmospheric corrosion of aluminium and its alloy at different distance away from seashore in wannine maring environments [J]. Chin. J. Rare Met., 2002, 26: 456
10 朱紅嫚, 鄭棄非, 謝水生. 萬寧地區(qū)鋁及鋁合金不同距海點的大氣腐蝕研究 [J]. 稀有金屬, 2002, 26: 456
11 Hu J Z, Liu Q B, Hu H H, et al. Cl- sedimentation rate in atmosphere of tropical island [J]. Corros. Prot., 2018, 39: 463
11 胡杰珍, 劉泉兵, 胡歡歡等. 熱帶海島大氣中氯離子沉降速率 [J]. 腐蝕與防護, 2018, 39: 463
12 Chen Y L, Zhao H J, Wang C G, et al. Short-term electrochemical corrosion behavior of 7B04 aluminum alloy and 30CrMnSiA Steel [J]. Equip. Environ. Eng., 2018, 15(1): 34
12 陳躍良, 趙紅君, 王晨光等. 7B04鋁合金和30CrMnSiA鋼短期腐蝕的電化學(xué)行為研究 [J]. 裝備環(huán)境工程, 2018, 15(1): 34
13 Palani S, Hack T, Deconinck J, et al. Validation of predictive model for galvanic corrosion under thin electrolyte layers: An application to aluminium 2024-CFRP material combination [J]. Corros. Sci., 2014, 78: 89
14 Yao X, Cai C, Li J F, et al. Early stage galvanic corrosion of 5383Al alloy coupled with 907 steel and aluminum bronze in 3.5% NaCl solution [J]. Corros. Sci. Prot. Technol., 2015, 27: 419
14 姚希, 蔡超, 李勁風(fēng)等. 5383鋁合金與907鋼和鋁青銅早期電偶腐蝕的平面分布 [J]. 腐蝕科學(xué)與防護技術(shù), 2015, 27: 419
15 Tamura H. The role of rusts in corrosion and corrosion protection of iron and steel [J]. Corros. Sci., 2008, 50: 1872
16 Li W J. Study of the catalytic and cooperating action of Fe(Ⅱ) in the process of transformation from Fe(OH)2 to γ-FeOOH [D]. Shijiazhuang: Hebei Normal University, 2005
16 李文君. Fe(Ⅱ) 在空氣氧化Fe(OH)2形成γ-FeOOH過程中的協(xié)同催化作用 [D]. 石家莊: 河北師范大學(xué), 2005
17 Yan M C, Sun C, Xu J, et al. Role of Fe oxides in corrosion of pipeline steel in a red clay soil [J]. Corros. Sci., 2014, 80: 309
18 Hao L, Zhang S X, Dong J H, et al. Evolution of corrosion of MnCuP weathering steel submitted to wet/dry cyclic tests in a simulated coastal atmosphere [J]. Corros. Sci., 2012, 58: 175
免責(zé)聲明:本網(wǎng)站所轉(zhuǎn)載的文字、圖片與視頻資料版權(quán)歸原創(chuàng)作者所有,如果涉及侵權(quán),請第一時間聯(lián)系本網(wǎng)刪除。
-
標(biāo)簽: 5083鋁合金, 30CrMnSiA鋼, 電偶腐蝕, 氯離子濃度, 腐蝕行為
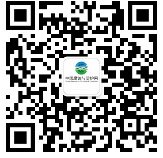
官方微信
《中國腐蝕與防護網(wǎng)電子期刊》征訂啟事
- 投稿聯(lián)系:編輯部
- 電話:010-62316606-806
- 郵箱:fsfhzy666@163.com
- 中國腐蝕與防護網(wǎng)官方QQ群:140808414