摘要
為了探討脈沖電流對1050鋁合金微弧氧化過程的影響規律,利用渦流測厚儀和粗糙度儀分別測量陶瓷層厚度和表面粗糙度,采用SEM觀察陶瓷層微觀形貌,借助動電位極化曲線測試評價陶瓷層耐蝕性,并根據電壓變化曲線計算微弧氧化過程能量消耗。結果表明:隨著脈沖電流由100 A增加至800 A,微弧誘發時間由360 s縮短至15 s,誘發電壓由341 V 升高至887 V;陶瓷層表面放電微孔孔徑增大,微孔數量減少,陶瓷層厚度和表面粗糙度增加,耐蝕性略有下降;微弧誘發過程能量消耗先減少后增加,并在200 A時達到最小值僅為18.3 kJ;陶瓷層生長過程能量消耗隨脈沖電流增大近似線性增加。
關鍵詞: 鋁合金 ; 微弧氧化 ; 脈沖電流 ; 耐蝕性 ; 能量消耗
微弧氧化 (MAO)[1,2,3,4]技術是以Al、Mg、Ti等有色金屬及其合金作為陽極,不銹鋼為陰極,置于脈沖電場環境的電解液中,在熱化學、等離子體化學和電化學的共同作用下使金屬表面產生微弧放電而生成一層與基體以冶金方式結合的陶瓷質氧化膜。鋁合金經MAO處理后極大提高了其表面的硬度、耐磨、耐蝕、耐壓絕緣及抗高溫沖擊等特性[5,6],但處理成本過高限制其推廣應用[7,8]。眾多研究[4,7-9]表明,MAO工藝主要依靠電源供給能量實現金屬自我氧化,因此研究能量的消耗是降低鋁合金MAO處理過程成本的重要方式。
電參量的模式是改變MAO過程能量消耗的主要因素[8],直流脈沖MAO電源因有較高的成膜效率且有良好的膜層性能而被廣泛應用[10,11,12]。目前,國內外對MAO技術的主要研究集中在電參數和電解液對膜層性能以及微觀結構的影響等方面[13,14,15,16],而脈沖電流對鋁合金MAO過程能量消耗的影響規律尚不清楚。針對工藝過程環保、陶瓷層性能優異的MAO技術在成本組成中能量消耗太高限制其應用推廣這一工程學問題,本文采用直流脈沖電源研究不同脈沖電流下1050鋁合金MAO過程中能量的消耗,分析微弧誘發時間和電壓,測量陶瓷層厚度和表面粗糙度,觀察表面和截面形貌,比較耐蝕性,計算能量消耗,探尋脈沖電流對鋁合金MAO過程能量消耗的影響,為低能耗MAO過程的電參數設置提供理論依據。
1 實驗方法
實驗采用1050工業鋁合金,其化學成分 (質量分數,%) 為:Si 0.25,Fe 0.4,Mn 0.05,Zn 0.05,Cu 0.05,Mg 0.05,Al余量。試樣尺寸為100 mm×50 mm×2 mm,并在其頂端鉆一個Φ2 mm的通孔用于連接陽極。MAO電解槽容積為50 L,內置不銹鋼板作為陰極,試樣作為陽極,按濃度15 g/L Na2SiO3 (分析純,西安三浦精細化工)、5 g/L (NaPO3)6 (分析純,西安三浦精細化工)、5 g/L KOH (分析純,西安三浦精細化工) 以及少量無機添加劑加入到去離子水中配置電解液。采用西安理工大學研制的MAO-PM500型直流脈沖電源來進行MAO處理,電源控制模式是脈沖電流控制。電源輸出參數控制示意圖見圖1,其中,ip為脈沖電流,Δt為電流導通時間即脈沖寬度 (以下簡稱脈寬),N為頻率,3個電參量均獨立可變。鋁合金于電解液中設置Δt為30 μs,N為500 Hz,ip分別為100,200,300,400,600和800 A進行MAO處理。鋁合金試樣MAO工藝流程為:表面打磨清洗→MAO→去離子水清洗→干燥。
圖1 電源輸出參數示意圖
采用TT-240型渦流測厚儀測量陶瓷層厚度,試樣正反面各取5個點,對所測數據求平均值;使用TR-240型表面粗糙度測試儀測量陶瓷層表面粗糙度,計算輪廓算術平均偏差Ra,試樣正反面各取5個點,對所測數據求平均值;使用JSM-6700F型掃描電子顯微鏡 (SEM) 觀察陶瓷層微觀形貌;使用CHI660D型電化學工作站測量動電位極化曲線,腐蝕介質為3.5% (質量分數) NaCl溶液,同時保證腐蝕區域為10 mm×10 mm,分析Tafel曲線并通過腐蝕電位和電流比較耐蝕性。
MAO過程中能量的消耗是指整個通電過程中直流脈沖電源輸出的總能量。從圖1可知,能量消耗Q為通電時間內單脈沖能量作用在兩極間的總和,如下式:
(1)
式中,T為通電時間 (s),Wsi為單個脈沖所含的能量 (J)。Wsi計算式如下:
(2)
式中,Ut為電壓。
根據電流等通量變換原理,可知ip與平均電流ia的關系如下:
(3)
由于ip保持不變,將式 (3) 進行轉換可以得到下式:
(4)
通過式 (2) 和 (4) 對式 (1) 進行轉變,最后可以得到能量的計算公式如下:
(5)
通電至鋁合金試樣表面均勻布滿微弧等離子體放電斑點的等待時間為微弧誘發時間,此時陰陽兩極間電壓值即為誘發電壓,該過程能量消耗即為微弧誘發過程能耗Q1。鋁合金試樣表面微弧誘發后至停止通電,此過程能量消耗為生長過程能耗Q2。生長單位厚度陶瓷層能量消耗Q3計算公式如下:
(6)
其中,D為陶瓷層厚度。
2 結果與討論
2.1 微弧等離子體誘發時間和電壓
鋁合金試樣于電解液中設置Δt為30 μs,N為500 Hz,ip分別100,200,300,400,600和800 A進行MAO處理,試樣表面發生MAO放電現象后記錄時間及電壓,結果見圖2。可以看出,隨著脈沖電流增加,鋁合金試樣誘發時間迅速降低并趨于穩定,由最長360 s縮短至15 s;微弧誘發電壓近似于線性增長,由最低341 V至最高887 V。由單脈沖能量計算式 (2) 可知,脈沖電流是影響單脈沖能量的重要因素,隨脈沖電流增大,單個脈沖能量也隨之增加,更高能量作用于試樣表面,間接造成了試樣兩端電壓上升速度增加,有效促進鋁合金MAO過程的進行,因此微弧誘發時間縮短,誘發電壓升高。
圖2 脈沖電流對鋁合金微弧誘發時間和電壓的影響
1050鋁合金試樣在不同脈沖電流的條件下MAO處理5 min,記錄電壓變化曲線見圖3。通過對比電壓變化曲線可看出,在相同時間點試樣兩端電壓值隨著脈沖電流的增大也相對較高;在脈沖電流一定的條件下,試樣兩端電壓整體也呈增大趨勢,但通電初期迅速增大,在時間推移過程中增速變緩,兩個階段基本上以微弧誘發為分界點。根據相關文獻[7,10]分析可知,電源開始提供能量時,鋁合金試樣表面層的阻抗值迅速增加,促使試樣兩端電壓急速上升,當阻抗層達到一定厚度且電壓超過擊穿電壓時,試樣表面出現擊穿微弧放電現象,之后膜層生長的過程重復“擊穿-熔融-淬冷”,因此膜層厚度增加使得擊穿放電變得很困難,最終造成電壓增速變緩。
圖3 脈沖電流對鋁合金MAO過程中電壓的影響
2.2 MAO膜層的微觀結構
表1為測得的鋁合金試樣表面MAO膜層的厚度和表面粗糙度。對比可見,在脈寬、脈數以及處理時間不變的條件下,當脈沖電流由100 A增加到800 A,膜層厚度逐漸增加,表面的粗糙度也逐漸增大。
表1 不同脈沖電流下鋁合金MAO陶瓷層的厚度和粗糙度
采用SEM觀察試樣表面以及截面的形貌,結果見圖4和5。從圖4可以看出,當脈沖電流由100 A增加到800 A,試樣表面放電微孔的孔徑增大,放電微孔的數量減少,表面平整性變差,與表1中粗糙度測試結果一致。利用Nano Measurer隨機選取5個微孔統計可得陶瓷層表面放電微孔的平均孔徑。脈沖電流為100 A時,試樣表面放電微孔孔徑小于0.5 ?m;脈沖電流為200和300 A時,放電微孔孔徑為0.8~1 ?m,數量略有減少;脈沖電流為400 A時,試樣表面放電微孔孔徑增大,平均為1.8 ?m,同時出現典型的“火山堆”狀結構 (圖4d中黑色圓圈所示);脈沖電流為600和800 A時,放電微孔孔徑進一步增至3~4 ?m,試樣表面出現大量微裂紋,同時局部還有大孔套小孔現象 (圖4f黑色圓圈所示),說明局部發生了重復擊穿,這種特殊結構導致陶瓷層致密度下降。從圖5可以看出,脈沖電流為200,400和800 A時,膜層厚度分別為3.5,4.6和8.6 ?m,和渦流測厚儀測量出的結果 (表1) 基本一致。當脈沖電流由200 A增加至800 A,膜層的厚度增加,缺陷的數量增加,致密度也下降,直到出現較大放電微孔 (圖5c黑色圓圈處),與表面形貌觀察的結果一致。
圖4 脈沖電流對鋁合金MAO陶瓷層表面形貌的影響
圖5 脈沖電流對鋁合金MAO陶瓷層截面形貌的影響
從能量角度分析,當脈沖電流增大,單個脈沖承載的能量也就隨之增大,使得微弧誘發之后電源所輸出到鋁合金表面的總能量增大,更大的能量會在單位時間產出更多熔融物,形成更大的放電微孔,然后在速冷的過程中形成了更厚的膜層。因此,在同樣的時間內,脈沖電流越大,膜層的生長速度就越快。膜層表面與截面形貌表明,脈沖電流增大雖然能獲得更厚的膜層,但是其表面的粗糙度增大,膜層質量也相對較差。
2.3 MAO陶瓷層耐蝕性分析
鋁合金MAO陶瓷層的耐蝕性是由膜層組成、厚度和顯微結構等各種因素綜合作用決定[2]。不同脈沖電流下制備鋁合金MAO陶瓷層的耐蝕性通過在3.5%NaCl溶液中進行動電位極化曲線測試來評價,極化曲線見圖6。
圖6 脈沖電流對鋁合金MAO陶瓷層在3.5%NaCl溶液中動電位極化曲線的影響
由Tafel區域外推法從圖6極化曲線得到基體和不同厚度陶瓷層的陰/陽極Tafel斜率 (ba和bc)、腐蝕電位 (Ecorr) 和腐蝕電流密度 (Icorr),結果列于表2。從熱力學上講,Ecorr主要是由材料本身性質決定,材料腐蝕電位越正,腐蝕傾向越低。表2中陶瓷層的Ecorr與基體相比略有正移,說明腐蝕傾向減小;同時,隨脈沖電流增加,Ecorr基本趨于穩定。但Ecorr只能說明腐蝕傾向,判斷耐蝕性還要看其在具體腐蝕環境中的腐蝕電流密度。從表2還可以看出,與基體相比,陶瓷層的Icorr降低3個數量級,說明經過MAO處理的1050鋁合金耐蝕性明顯提高;同時隨著脈沖電流增大,陶瓷層的Icorr逐漸增大,因此耐蝕性呈下降趨勢。結合表2陶瓷層厚度和圖5截面形貌綜合分析,脈沖電流為800 A時,盡管所得陶瓷層很厚,但是其致密度相對較差,導致Icorr增大,耐蝕性變差。
表2 鋁合金試樣在3.5%NaCl溶液中動電位極化曲線計算結果
2.4 MAO過程能量消耗計算
為了研究脈沖電流對1050鋁合金MAO過程能量消耗的影響,按照式 (5) 對圖3中電壓變化曲線以微弧誘發時間為分界點進行分段積分,得到不同脈沖電流下微弧誘發過程能耗Q1和陶瓷層增厚生長過程能耗Q2,結果見圖7。分析圖7中Q1的變化曲線可以看出,隨著脈沖電流增大,Q1先減小后增大。由式 (5) 分析可知,Q1是由電壓、時間和平均電流這3個參量共同決定的,脈沖電流較小時 (如100 A),雖然微弧誘發的電壓低且平均電流比較小,但是消耗時間卻很長,所以Q1很大;脈沖電流比較大時 (如600和800 A),雖然微弧誘發時間較短,但是誘發電壓比較高且平均電流較大,所以Q1較高。綜合對比微弧誘發的電壓和時間,脈沖電流為200 A時Q1達到最小值僅為18.3 kJ。從圖7中Q2的變化曲線可以看出,隨著脈沖電流增大,Q2基本呈現線性增加。在脈寬和脈數一定條件下,隨著脈沖電流由200 A增大至800 A,根據式 (4) 可知,作用于樣品兩端的平均電流成倍地增大,與此同時樣品兩端的電壓也相對較高,所以Q2近似成倍增大。
圖7 脈沖電流對微弧誘發和陶瓷層生長過程能量消耗的影響
鑒于各種脈沖電流下鋁合金表面的MAO膜層厚度不一致,為了讓能量的消耗更加有可比性,根據式 (6) 計算出生長單位厚度膜層能量消耗Q3,結果見圖8。可以看出,隨著脈沖電流的增大,長出單位厚度膜層所消耗的能量呈線性增加趨勢,在200 A達到最小值42.1 kJ/?m。MAO膜層增厚過程是試樣表面在脈沖電場作用下“擊穿-熔融-淬冷”循環作用后的結果,在相同擊穿次數下單脈沖擊穿所產出熔融物的數量是決定膜層生長速率的關鍵因素。因此,脈沖電流越大,熔融產物相對也越多,膜層生長的速度越快,生長單位膜層厚度需要消耗能量也就越多。結合微觀結構分析,小脈沖電流輸出模式下,鋁合金的MAO效率比較低,雖然膜層生長的速度慢,但是膜層質量較好,生長單位厚度所消耗的能量較少;大脈沖電流輸出模式下,鋁合金的MAO效率比較高,膜層生長的速度快,但是膜層質量較差,生長單位厚度所消耗的能量較多。
圖8 脈沖電流對MAO陶瓷層生長單位厚度能量消耗的影響
3 結論
(1) 隨著脈沖電流由100 A增至800 A,1050鋁合金微弧誘發時間由360 s縮短至15 s,誘發電壓由341 V升高至887 V。
(2) 微弧誘發過程能量消耗隨脈沖電流增大先減少后增加,并在200 A時達到最小值18.3 kJ;陶瓷層生長過程能耗隨脈沖電流增大近似成倍增加。
(3) 小脈沖電流輸出模式下,1050鋁合金MAO效率較低,陶瓷層生長速度慢,但膜層質量好,生長單位厚度消耗的能量少;大脈沖電流輸出模式下,1050鋁合金MAO效率較高,陶瓷層生長速度快,但膜層質量差,生長單位厚度消耗的能量多。
(4) 隨脈沖電流增加,陶瓷層表面放電微孔孔徑增大,微孔數量減少,陶瓷層厚度增加的同時表面粗糙度升高,耐蝕性略有降低。
參考文獻
[1] Lia H X, Rudnev V S, Zheng X H, et al.Characterization of Al2O3 ceramic coatings on 6063 aluminum alloy prepared in borate electrolytes by micro-arc oxidation[J]. J. Alloy. Compd., 2008, 462: 99
[2] Wang C J, Jiang B L, Liu M, et al.Corrosion characterization of micro-arc oxidization composite electrophoretic coating on AZ31B magnesium alloy[J]. J. Alloy. Compd., 2015, 621: 53
[3] Guo P Y, Wang X F, Shao Y.Formation mechanism and corrosion behavior of micro-arc oxidation ceramic layers on 1050 pure aluminum[J]. Corros. Sci. Prot. Technol., 2011, 23: 490(郭平義, 王曉璠, 邵勇. 1050純鋁微弧氧化陶瓷層的生長動力學與腐蝕性能研究[J]. 腐蝕科學與防護技術, 2011, 23: 490)
[4] Gupta P, Tenhundfeld G, Daigle E O, et al.Electrolytic plasma technology: Science and engineering?An overview[J]. Surf. Coat. Technol., 2007, 201: 8746
[5] Jaspard?Mécuson F, Czerwiec T, Henrion G, et al. Tailored aluminum oxide layers by bipolar current adjustment in the plasma electrolytic oxidation (PEO) process[J]. Surf. Coat. Technol., 2007, 201: 8677
[6] Jiang B L, Zhang X F.Growth process and corrosion resistance ofceramic coatings formed by micro-oxidation on magnesium alloy[J]. J. Chin. Soc. Corros. Prot., 2005, 25: 97(蔣百靈, 張先鋒. 鎂合金微弧氧化陶瓷層的生長過程及其耐蝕性[J]. 中國腐蝕與防護學報, 2005, 25: 97)
[7] Ge Y F, Jiang B L, Shi H Y.Effect of current pulse width on micro-arc oxidation process for aluminum alloy[J]. Trans. Mater. Heat Treat., 2013, 34: 165(葛延峰, 蔣百靈, 時惠英. 電流脈沖寬度對鋁合金微弧氧化過程的影響[J]. 材料熱處理學報, 2013, 34: 165)
[8] Jiang B L, Liu D J.Scientific aspects of restricting development and application of micro-arc oxidation technology[J]. Chin. J. Nonferrous Met., 2011, 21: 2402(蔣百靈, 劉東杰. 制約微弧氧化技術應用開發的幾個科學問題[J]. 中國有色金屬學報, 2011, 21: 2402)
[9] Yerokhin A L, Shatrov T A, Samsonov V, et al.Oxide ceramic coatings on aluminium alloys produced by a pulsed bipolar plasma electrolytic oxidation process[J]. Surf. Coat. Technol., 2005, 199: 150
[10] Liu R M, Guo F, Li P F.Effect of voltage on formation of ceramic coating prepared by micro-arc oxidation on aluminum alloy[J]. Trans. Mater. Heat Treat., 2008, 29: 137(劉榮明, 郭鋒, 李鵬飛. 電壓對鋁合金微弧氧化陶瓷層形成的影響[J]. 材料熱處理學報, 2008, 29: 137)
[11] Hou W A, Hu J H, Song X J.The influence of power supply modeon the process and performance of coating of micro-arc oxidation[J]. Nonferrous Met.(Extr. Metall.), 2007, (S1): 122(侯偉驁, 胡江輝, 宋希劍. 電源工作模式對微弧氧化過程和膜層性能的影響[J]. 有色金屬 (冶煉部分), 2007, (S1): 122)
[12] Yerokhin A L, Snizhko L O, Gurevina N L, et al.Discharge characterization in plasma electrolytic oxidation of aluminium[J]. J. Phys. D: Appl. Phys., 2003, 3: 2110
[13] Cui X J, Wang R, Wei J S, et al.Effect of electrical parameters on micromorphology and corrosion resistance of micro-arc oxidation coating on AZ31B Mg alloy[J]. J. Chin. Soc. Corros. Prot., 2014,34: 495(崔學軍, 王榮, 魏勁松等. 電參數對AZ31B 鎂合金微弧氧化膜微觀形貌及耐蝕性的影響[J]. 中國腐蝕與防護學報, 2014, 34: 495)
[14] Jiang B L, Zhang S F, Wu G J.Study of corrosion resistance on ceramic coatings formed by micro-arc oxidation on magnesium alloys[J]. J. Chin. Soc. Corros. Prot., 2002, 22: 300(蔣百靈, 張淑芬, 吳國建等. 鎂合金微弧氧化陶瓷層耐蝕性的研究[J] .中國腐蝕與防護學報, 2002, 22: 300)
[15] Zhao J, Song R G, Li H X, et al.Effects of nano-additive on microstructure and properties of micro-arc oxidation coatings on 6063 aluminum alloy[J]. Trans. Mater. Heat Treat., 2010, 31: 125(趙堅, 宋仁國, 李紅霞等. 納米添加劑對6063鋁合金微弧氧化層組織與性能的影響[J]. 材料熱處理學報, 2010, 31: 125)
[16] Lv G H, Gu W C, Chen H, et al.Characteristics of ceramic coatings on aluminum formed by plasma electrolytic oxidation in silicate and phosphate electrolyte[J]. Appl. Surf. Sci., 2006, 253: 947
免責聲明:本網站所轉載的文字、圖片與視頻資料版權歸原創作者所有,如果涉及侵權,請第一時間聯系本網刪除。
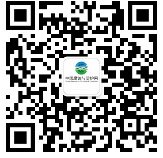
官方微信
《中國腐蝕與防護網電子期刊》征訂啟事
- 投稿聯系:編輯部
- 電話:010-62316606-806
- 郵箱:fsfhzy666@163.com
- 中國腐蝕與防護網官方QQ群:140808414