摘要
綜述了鎳基高溫合金上抗高溫氧化的Pt改性β-(Ni,Pt)Al涂層和γ-γ′型涂層,重點介紹了Pt改性鋁化物涂層制備工藝,不同工藝條件下涂層的微觀結構,Pt增強鋁化物涂層抗氧化性能的作用機理,Al對涂層高溫氧化性能的影響,并從元素互擴散、相變、表面起伏等方面描述了涂層退化過程,最后對Pt改性鋁化物涂層發展進行展望。
關鍵詞: Pt改性鋁化物涂層 ; 微觀結構 ; 高溫氧化性能 ; 研究展望
經歷了上百年的技術突破和行業變革,目前航空發動機葉片材料以鐵基、鈷基和鎳基高溫合金為主,其中鎳基高溫合金在航空發動機熱端部件的應用最為廣泛[1,2],其主要成分為Ni、Cr、Co、Mo、W、Ta、Nb、Al等[3]。高溫防護涂層技術隨著高溫合金在發動機服役溫度不斷提高[4]而快速發展,其中鋁化物涂層以其優異的綜合性能,及可以單獨使用或作為熱障涂層系統中的粘結層使用而得到廣泛應用。制備鋁化物涂層的工藝方法有很多種,包括包埋滲鋁、氣相滲鋁、化學氣相沉積 (CVD) 滲鋁等[5]。包埋滲鋁滲劑與樣品表面直接接觸,涂層內易引入雜質[6]。氣相滲鋁在涂層涂覆均勻性、工藝穩定性等方面存在著不足,且工藝參數難以控制[7]。CVD滲鋁相比包埋滲鋁和氣相滲鋁的優越性在于它能夠適用復雜型腔及微小冷卻通道表面滲鋁,并且可通過調控反應參數 (反應溫度、反應時間、反應氣體和滲劑種類) 制備出不同結構、不同性能的 (改性) 鋁化物涂層[8,9]。近年來,國內外研究者大多采用CVD制備鋁化物涂層[10-15]。
然而單一鋁化物涂層在長期高溫氧化環境中表面易剝落,通過添加Pt、Si、Hf、Pd、稀土等元素制備改性鋁化物涂層,以提高抗高溫氧化性能[16-19]。在鎳基高溫合金上制備的Pt改性鋁化物涂層已成功應用在航空發動機葉片[20-29],研究者仍不斷探索涂層的抗高溫氧化機理和退化過程,并不斷優化涂層的成分、組織結構及制備工藝,以期進一步提高其抗高溫氧化性能。本文對鎳基高溫合金上抗高溫氧化的Pt改性β-(Ni,Pt) Al涂層和γ-γ‘型鋁化物涂層重點進行闡述,并綜述了其制備工藝及微觀結構、氧化行為的研究現狀及展望。
1 Pt改性鋁化物涂層的制備過程及微觀結構
1.1 制備過程
Pt改性的鋁化物涂層制備過程一般包括四個步驟[15]。(1) 制備鍍Pt層:采用電鍍、熔鹽電沉積或物理氣相沉積 (PVD) 等方法在基體表面沉積一層Pt (3~10 μm);(2) 預擴散處理:對鍍Pt后的樣品進行真空退火,以提高Pt層與基體合金的結合力,同時降低樣品表面Pt濃度;(3) 擴散滲鋁:采用包埋滲鋁、氣相滲鋁或CVD方法進行滲鋁處理,引入Al形成Pt改性鋁化物涂層;(4) 后續熱處理 (根據工藝需要):進一步完成涂層的形成,提高基體合金與涂層的結合力,同時有助于基體合金恢復滲鋁過程中損失的力學性能。通過調整預擴散處理和擴散滲鋁的溫度、時間以及滲鋁工藝的類型,可獲得傳統的β-(Ni,Pt)Al涂層和新型的γ-γ’型涂層。
1.2 Pt改性鋁化物涂層的微觀結構
1.2.1 β-(Ni,Pt)Al涂層
傳統的β-(Ni,Pt)Al涂層微觀結構與單一鋁化物涂層的微觀結構相似。單一鋁化物涂層根據制備過程中擴散機理不同,可分為向內生長型 (低溫高活性) 滲鋁和向外生長型 (高溫低活性) 滲鋁[30-32]。在向內生長型涂層制備過程中,涂層形成機制是通過Al原子向內擴散與Ni原子反應而生長的。涂層的微觀結構如圖1a所示[30],涂層由三層組成,外層和中間層由β-NiAl組成,外層含有大量細小的沉淀相,中間層為析出相;內層是互擴散區,該層分布有含β基體相的大量復雜沉淀相。在向外生長型涂層制備過程中,涂層形成機制是以基體合金表面為初始界面向外生長。涂層的微觀結構如圖1b所示[30],涂層由兩層組成,外層由β-NiAl組成,內層互擴散區成分與向內生長型涂層互擴散區類似。
圖1 單一鋁化物涂層的典型微觀結構[30]
制備向內生長型β-(Ni,Pt)Al涂層,通常包括兩個步驟[33-36],(1) Al化處理:在相對較低的溫度 (700~850 ℃) 下進行,將Al原子從反應室擴散進入到基體合金中;(2) 后續熱處理:對滲鋁樣品進行高溫 (通常高于1000 ℃) 熱處理,使涂層中各種原子發生再分布形成最終的涂層組織。涂層的微觀結構如圖2所示[35,36],涂層由外層、中間層和互擴散區三層組成。互擴散區分布有大量復雜沉淀相,中間層有一些細小的析出相以及有一定量的Pt固溶在β-NiAl相中,外層富Pt層根據工藝條件不同有不同的微觀結構。第一種情況如圖2a所示,外層由單相ξ-PtAl2組成;第二種情況如圖2b所示,外層為Pt固溶的單相β-NiAl結構;圖2c所示為介于第一和第二種情況之間,外層由ξ和β相組成的兩相組織。
圖2 向內生長型的Pt改性鋁化物涂層中的微觀結構[35,36]
制備向外生長型β-(Ni,Pt)Al涂層通常是在1000 ℃以上一步進行,多采用氣相滲鋁或CVD滲鋁方法[37-41]。涂層的微觀結構如圖3所示[42],涂層外層由Pt固溶的β-NiAl相和互擴散區 (與向內生長型類似) 兩層結構組成,涂層表面呈網狀結構。與向內生長型涂層相比,向外生長型涂層的外層β-(Ni,Pt)Al成分純凈,幾乎不包含任何沉淀相,而且互擴散區較厚。
圖3 向外生長型的Pt改性鋁化物涂層中的微觀結構[41]
1.2.2 Pt改性γ-γ‘型鋁化物涂層
鎳基高溫合金基體含有一些難熔元素 (如Re、W、Mo),傳統的β-(Ni,Pt)Al涂層中Al含量較高,在滲鋁或服役過程中富含難熔元素的有害拓撲密堆積 (TCP) 相在基體合金中析出[42];同時涂層中較高的Al和較低的Ni含量使涂層與基體合金之間產生互擴散,形成二次反應區 (SRZ),導致基體合金沿晶胞邊界開裂引起蠕變性能退化[43,44]。且在服役過程中,隨著涂層中Al的消耗,涂層內部發生β-(Ni,Pt)Al向γ和γ′相的馬氏體相變,從而引起體積變化,導致涂層表面產生“起伏”現象;當β-(Ni,Pt)Al作為熱障涂層粘結層使用時[20,45],“起伏”現象產生的界面應力導致陶瓷層脫落[20]。為了克服β-(Ni,Pt)Al涂層存在的問題,近年發展了一種由γ和γ′相組成的新型Pt改性鋁化物涂層,稱為Pt改性γ-γ’型涂層,此涂層與基體合金的化學和機械相容性得到提高[46-49]。
制備Pt改性γ-γ′型涂層的方法與傳統的β-(Ni,Pt)Al涂層相似,在基體合金表面制備一層Pt,不同的是滲鋁過程中使用NaCl等穩定的活化劑,并適當地保持滲鋁介質中的Al含量,使涂層的Al含量足夠低 (通常為27%,原子分數),涂層中就會形成γ-γ′相結構[50]。滲鋁過程中使用的活化劑是實現涂層γ-γ′相結構的關鍵,使用NH4X (X=Cl,Br,I) 作為活化劑會導致β-NiAl相的形成,因為在滲鋁的初始階段,Al的沉積速度很高[51]。圖4為一種典型的Pt改性γ-γ′型涂層的微觀結構[52],該涂層呈兩層結構,類似于向外生長型的β-(Ni,Al)Pt涂層。與β-(Ni,Al)Pt涂層不同的是,γ-γ′型涂層的外層主要由γ′相組成,互擴散區由γ和γ′相組成,由于難熔元素在γ′相中的溶解度相對γ相較低,沉淀相主要在互擴散區的γ′相中形成。此外,與β-(Ni,Al)Pt涂層相比,由于難熔元素在γ′中的溶解度比在β-NiAl相中的溶解度高,所以γ-γ′型鋁化物涂層的互擴散區中形成了更少的沉淀相。
圖4 鎳基高溫合金上Pt改性γ-γ′型鋁化物涂層典型微觀結構[52]
2 Pt改性鋁化物涂層的高溫氧化行為
2.1 Pt對抗氧化性能的作用
Pt可以顯著提高鋁化物涂層抗高溫氧化性能,目前Pt的主要作用機理包括以下幾個方面。(1) Pt的釘扎作用:在擴散型[53]和MCrAlY (M=Fe/Ni/Co) 型[54]涂層中,Pt形成的氧化物通過釘扎生長從涂層進入基體,使涂層和基體界面結合更加緊密,增強了Al2O3保護膜的粘附性,提高了鋁化物涂層抗高溫氧化性能。(2) 影響元素擴散:Pt能促進Al的選擇性氧化形成Al2O3保護膜,具體表現[55,56]為Pt促進Al從基體擴散到涂層中,補充Al的選擇性氧化所需的Al;由Ni-Al-Pt三元相圖[48]和第一性原理研究[57]結果可知,在保持相中Al含量不變的情況下,Pt能取代γ′-Ni3Al相中的Ni,減少β-(Ni,Pt)Al相轉化為在高溫氧化環境中形成氧化膜易剝落的γ‘-Ni3Al相;此外Pt能抑制Al的內擴散、Ni的外擴散、難熔元素Mo、V、W等的外擴散,維持涂層中所需的Al、Ni,降低難熔元素在涂層表面形成氧化物,得到更加純凈的Al2O3保護膜[58-61]。(3) 抑制涂層界面孔洞的形成:基于第一性原理與密度泛函理論的研究結果表明,Pt能降低β-NiAl中點缺陷和缺陷群形成所需的能量來提高涂層整體擴散系數,增加Al擴散進入β-NiAl中的幾率,補充因元素互擴散造成Al空位所需的Al,從而抑制涂層界面Al2O3保護膜形成孔洞[62];Pt還能增加氧化物和金屬之間的接觸面積,抑制涂層界面孔洞的形成,減少Al2O3保護膜的剝落[63]。此外,在高溫環境中1 mg/L S就會從涂層中擴散至氧化膜界面處富集而產生微孔洞[64],使得氧化膜結構疏松多孔以及降低氧化膜粘附性。對于Pt改性鋁化物涂層,Pt能減少一定量的S在界面上的偏析[65,66],改善涂層粘附性。但S含量過高仍會導致Al2O3保護膜粘附性變差[67]。
2.2 Al在高溫氧化行為中的影響
在Pt改性鋁化物涂層中Al形成Al2O3保護膜及增加涂層厚度,適當增加Al濃度能提高涂層的抗高溫氧化性能。β-(Ni,Pt)Al涂層 (高活性滲鋁制備的RT-22涂層) 1050 ℃高溫循環氧化試驗結果表明,含52% (原子分數) Al的涂層抗高溫氧化性能優于含30% (原子分數) Al的涂層[68];低活性滲鋁制備的β-(Ni,Pt)Al涂層1200 ℃高溫循環氧化試驗結果表明,隨著Al濃度的增加涂層的厚度不斷增加,當Al濃度達到一定范圍時涂層的抗高溫氧化性能最佳,超過此范圍涂層太厚不利于葉片實際使用,且涂層的抗高溫氧化性能不再增加[69]。
2.3 Pt改性鋁化物涂層的退化
雖然Pt改性鋁化物涂層的綜合性能較穩定,但長期暴露在高溫氧化環境中,涂層的抗高溫氧化性能仍會發生退化,以下為涂層退化的主要機理及過程。
2.3.1 元素互擴散
滲鋁后,涂層中的Al含量比基體中的Al含量高,Ni含量則較低,因而涂層與基體之間形成濃度梯度,導致Al、Ni和其他元素在涂層和基體之間發生相互擴散。CM247 (LC) 鎳基高溫合金上高活性滲鋁制備的Pt改性鋁化物涂層1100 ℃恒溫氧化試驗結果表明[43],Ni從基體向外擴散到涂層表面,導致互擴散區厚度增加,從而增加整個涂層的厚度,涂層外層Al2O3保護膜不夠致密是涂層退化的主要原因。CMSX-4鎳基單晶高溫合金基體上采用高活性滲鋁制備的不同鍍Pt層的SS82A涂層和RT22涂層,1050 ℃高溫氧化試驗結果表明[70],Al從互擴散區向基體表面擴散,導致Co,Cr等難熔金屬在互擴散區析出,且Ni從基體向涂層表面擴散,涂層中的β-NiAl相轉變為γ′-Ni3Al相,導致涂層發生退化。相比于單一鋁化物涂層,Pt改性鋁化物涂層中元素在互擴散區層互擴散有所改善,且針尖狀TCP析出量顯著減少[71,72]。
2.3.2 相變
在高溫氧化環境中,伴隨著氧化溫度的改變和Al的消耗,涂層中的物相會發生以下兩種相變。第一種相變是由溫度引起的[73],采用CVD滲鋁工藝制備的β-(Ni,Pt)Al涂層1150 ℃×100 h恒溫氧化實驗結果發現,涂層組織由B2-CsCl結構的單相β相完全轉變為fctL10結構的馬氏體相,這種相變使涂層表面起伏開裂,導致涂層發生退化。第二種相變是由Al消耗引起的[74],隨著Al向基體內擴散,同時Al向外擴散形成Al2O3保護膜,涂層中的Al含量不斷降低,使β-(Ni,Pt)Al相轉變為γ′-(Ni,Pt)3Al相,導致涂層表面部分Al2O3保護膜剝落,涂層退化。
2.3.3 涂層表面起伏
文獻[45,63,75-77]對Pt改性鋁化物涂層的表面起伏現象進行了研究。涂層表面產生起伏的原因主要有:其一,由于涂層中Al的消耗和難熔元素從基體擴散進入涂層形成氧化物,導致β-(Ni,Pt) Al相的分解,Al2O3保護膜剝落,涂層局部體積發生變化 (圖5);其二,高溫氧化周期長、氧化速率高、涂層表面粗糙度大等因素也會使涂層表面起伏;其三,涂層組織由B2-CsCl結構的單相β相完全轉變為fctL10結構的馬氏體相,也會使涂層表面產生起伏;其四,涂層與基體的熱膨脹系數差異而產生的熱應力成為涂層表面起伏的驅動力。近年來關于涂層表面起伏新的研究結果表明,Pt改性鋁化物涂層中由于Pt的加入形成具有良好致密性的Al2O3保護膜,且當涂層中添加Hf、Y等元素共改性時,涂層氧化速率明顯降低,涂層與基體的結合力顯著增加,涂層表面起伏得到很好的改善[78]。
圖5 涂層氧化過程中主要擴散通量以及導致起伏和孔洞形成的微觀結構[73]
2.3.4 涂層退化的其他變化
高溫氧化環境中,高活性滲鋁制備的Pt改性鋁化物涂層中,β-(Ni,Pt)Al相內有細小的NiO、CoO等氧化物析出,這些析出物在氧化過程中有的會溶解在Al2O3保護膜中導致其致密度下降,有的會長大粗化導致涂層表面開裂[33]。此外。隨著氧化過程中Al、Ni和其他元素在基體和涂層之間發生相互擴散,由于基體和涂層兩側原子擴散通量不相等,導致在基體和涂層界面附近產生柯肯達爾孔洞[45]。
3 結論與展望
本文綜述了在鎳基高溫合金上制備的Pt改性β-(Ni,Pt)Al涂層和γ-γ’型涂層制備工藝、微觀結構和抗高溫氧化性能的研究進展。通常,γ-γ‘型涂層較β-(Ni,Pt)Al涂層含有更少的Al,且γ-γ’型涂層與基體合金的化學和力學相容性較好。在β-(Ni,Pt)Al涂層中,根據滲鋁過程中生長機理的不同,可分為向內生長型涂層和向外生長型涂層。其次,介紹了Pt增強鋁化物涂層抗氧化性的作用機理,Al對涂層抗氧化性能的影響,并從元素互擴散、相變、表面起伏等方面描述了涂層退化過程。
為了進一步探究Pt改性鋁化物涂層,未來的研究工作重點在于:(1) 優化鍍Pt工藝,減少鍍Pt時雜質的引入;采用PVD方法鍍Pt,完善CVD滲鋁過程中可調控參數,制備出高純的Pt改性鋁化物涂層。
(2) 研究Pt結合活性等元素進行多元改性,探索其涂層的微觀結構、抗高溫氧化性能及作用機理。
(3) 不斷探究新型Pt改性γ-γ‘型涂層的作用機理,涂層的退化過程;并不斷優化涂層的成分及制備工藝,以期進一步提高涂層的抗高溫氧化性能。
免責聲明:本網站所轉載的文字、圖片與視頻資料版權歸原創作者所有,如果涉及侵權,請第一時間聯系本網刪除。
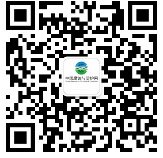
官方微信
《中國腐蝕與防護網電子期刊》征訂啟事
- 投稿聯系:編輯部
- 電話:010-62316606-806
- 郵箱:fsfhzy666@163.com
- 中國腐蝕與防護網官方QQ群:140808414