鋁是現代工業體系中應用十分廣泛的金屬元素,在金屬材料中的使用量僅次于鋼鐵[1]。鋁合金具有高比強度、低密度、低熔點、優良的加工性能及耐腐蝕性能等特點[2],隨著全球能源和環境問題日益突出,其在機械、建筑、電器、交通運輸、復合材料、涂層材料等領域發揮著愈加重要的作用[3-4],尤其是在防腐噴涂材料方面,鋁合金具有得天獨厚的優勢,熱噴鋁涂層被廣泛應用到結構鋼的防腐工程中。
鋁合金因其表面會形成一層非常致密的氧化膜,隔絕了鋁基體和外界環境的直接接觸,因此其有著良好的耐腐蝕性能。但是在某些環境狀況較差,頻繁出現酸雨、大霧等極端天氣的地區,環境中的SO42- 、Cl-等具有一定腐蝕性的陰離子破壞鋁合金表面的氧化膜,導致其出現點腐蝕等多種形式的腐蝕現象[5]。目前,對鋁合金暴露在不同環境中的腐蝕行為的研究已有很多報道,楊敏杰[6]對7075 鋁合金在3.5%NaCl 溶液中的腐蝕規律隨時間的變化進行了探究,發現在腐蝕初期,由于7075 鋁合金氧化膜的阻隔,其腐蝕速度非常緩慢,而在氧化膜被破壞后,基體暴露在腐蝕壞境中,腐蝕速度加快。侯丹丹[7]研究了6082 鋁合金的晶間腐蝕行為,結果顯示,腐蝕初期,縱向腐蝕深度逐步增加,隨著腐蝕時間的延長,縱向腐蝕深度的增加幅度變得很小,橫向腐蝕范圍和腐蝕程度會逐漸加大。Zhao 等[8]探究了7A85鋁合金在青島工業-海洋大氣環境中的腐蝕行為及機理,結果表明,裸露的7A85 鋁合金在工業-海洋大氣環境中會發生點腐蝕和晶間腐蝕,其力學性能隨著腐蝕時間延長逐步惡化。目前國內外對于鋁合金在高腐蝕性環境中的腐蝕行為研究報道很少,對鋁合金在高腐蝕性條件下的腐蝕機制研究也比較少[9],缺乏對高腐蝕性環境鋁合金的腐蝕規律的認識。因此,筆者將多種鋁合金在高腐蝕性環境中長時間浸泡腐蝕,通過研究鋁合金在高腐蝕性環境中表征和力學性能的變化來探究鋁合金在高腐蝕性環境中的腐蝕規律,為選擇耐腐蝕性能良好的熱噴涂材料提供依據。
1 實驗材料與方法
1.1 實驗材料
腐蝕實驗所采用的材料為某公司提供的6 mm 板厚的6061 鋁合金、7075 鋁合金及2195鋁鋰合金板材,其中6061 鋁合金為6XXX 系列鋁合金,其主要合金元素有Al、Mg、Si 等3 種元素。7075 鋁合金和2195 鋁鋰合金為高強鋁合金,2195 鋁鋰合金主要合金元素為Al、Cu、Li、Mg、Ag 等5 種元素,7075 鋁合金主要合金元素有Al、Zn、Mg、Cu 等4 種元素。3 種合金的成分表1~3 所示。
1.2 實驗過程
參照GB/T 19745-2018,本次腐蝕試驗所選用的腐蝕溶液的配比為1 L 5%NaCl 溶液+2 mL 硝酸(HNO3, ρ=1.42 g/mL)+5 mL 硫酸(H2SO4,ρ=1.84 g/mL),然后加入適量的NaOH 溶液來調節溶液的PH 值到規定值3.5。分別選取10 mm?10 mm?6 mm(板厚)6061鋁合金、2195 鋁鋰合金和7075 鋁合金的塊狀試樣及特定尺寸的拉伸試樣進行浸泡腐蝕試驗,試驗時間為0,6,12,24,48,96,168 h。實驗前依次用600#、1000#和1200#砂紙打磨塊狀試樣和拉伸試樣,然后對塊狀試樣特定面進行拋光處理,并用乙醇清潔,吹干。
1.3 表征與性能分析
采用TESCAN MIRA3 場發射掃描電子顯微鏡觀察腐蝕后的鋁合金的微觀形貌,分析其腐蝕層厚度。用能譜儀(EDS)分析腐蝕區的化學成分。采用Rigaku D/max 2500PC X 射線衍射儀(XRD)測試分析腐蝕區域的物相組成。分別對不同腐蝕時間的3 種鋁合金拉伸試樣進行室溫拉伸實驗,測試其拉伸性能隨著腐蝕時間的變化規律。拉伸實驗所選取的樣品腐蝕時間和表征樣品腐蝕時間一一對應,分別為6,12,24,48,96,168 h。為了保證實驗結果的準確性,每一組拉伸試樣的平行試樣為3 個,取平均值作為最后的實驗結果。室溫拉伸實驗樣品如圖1 所示,采用SANS-CMT5105 型微機控制電子萬能試驗機進行拉伸實驗,樣品兩端夾緊,拉伸速率為1 mm/min。
圖1 室溫拉伸樣品圖(單位:mm)
2 鋁合金腐蝕過程中表面微觀形貌與成分演變
經過不同腐蝕時間腐蝕的3 種鋁合金試樣表面的腐蝕形貌如圖2 所示。從圖中可以觀察到,6061 鋁合金在腐蝕介質中的腐蝕速度非常快,僅腐蝕6 h 后就出現了大面積的腐蝕凹坑,這些腐蝕凹坑大小不一,形狀不規則,遍布試樣表面。這是鋁合金點蝕的典型形貌,其形成原因可用氧化膜破壞理論和吸附理論兩種理論來解釋[10]。隨著腐蝕時間推移,樣品表面的原始的平整面積逐步減少,腐蝕凹坑面積逐步增大,可以觀察到,腐蝕48 h 后樣品原始表面已經完全被腐蝕,呈現出高低起伏的腐蝕坑洞。腐蝕凹坑的快速增加是因為在腐蝕坑形成后,其內外部的電化學條件發生顯著變化[11],坑內發生鋁合金的溶解反應,坑外部發生耗氧腐蝕反應[12],氧化鋁在坑外不斷堆積,使腐蝕坑內部形成閉塞區域,加速了腐蝕坑的加深與擴展[13],大面積的腐蝕凹坑就是由于各個點蝕坑在持續腐蝕過程中不斷擴大,最后連接在一起形成的腐蝕樣貌。從6061 鋁合金腐蝕形貌中還觀察到腐蝕坑具有形狀規則的方形結構,這種結構比較松散,加大了材料與腐蝕介質之間的接觸面積,腐蝕液可以穿過這些松散的結構孔洞,對基體進行持續大面積的腐蝕,因此腐蝕速度非常快。對腐蝕48 h 后6061鋁合金樣品表面點掃描(如圖3 所示)發現表面仍然是基體元素,未發現S、N 和Cl 等腐蝕性元素。這可能是由于這些腐蝕性元素在腐蝕過程中起催化作用,并未參與到腐蝕反應中。相比之下,2195 鋁鋰合金在酸性腐蝕液中的腐蝕速度比較慢,其SEM 圖像顯示腐蝕6 h后的2195 基體上僅存在少量鼓泡,沒有出現其它明顯的腐蝕形貌。少數鼓泡的出現是由于鋁合金表面發生了輕微的點腐蝕,這些點腐蝕優先在富銅相的位置形成,因為富銅相與周圍鋁基體存在電位差[14],極易在其位置發生電化學反應而引起腐蝕。腐蝕24 h 的2195 鋁鋰合金試樣表面的點腐蝕情況也不明顯,僅有少數點腐蝕坑出現,這可能是因為本次浸泡實驗腐蝕的誘導因素是帶有腐蝕性的氯離子(Cl–)和硫酸根離子(SO42-),這些離子對鋁合金表面生成的致密氧化膜造成了破壞,Cl– 離子因其半徑小而具有非常強的穿透能力,容易被吸附在鋁合金表面氧化膜破損、材質不均勻等活性位置,腐蝕性陰離子與表面氧化膜發生化學反應,隨著時間延長,氧化膜變薄、破裂,直到鋁合金基體裸露而后發生溶解[15-17]。由于腐蝕前期鋁合金表面僅僅出現少量鼓泡,大部分表面致密的氧化膜還比較完整,所以腐蝕坑的形成進展緩慢。隨著腐蝕時間繼續延長,在腐蝕48 h 后,點蝕坑在長大過程中不斷與其它點蝕坑合并,形成非常大的腐蝕坑。我們還觀察到2195 鋁鋰合金在腐蝕過程中,隨腐蝕時間增加,其表面覆蓋的一層黑色的薄膜越來越黑,這層薄膜非常薄并且極易掉落,可能是表面被腐蝕留下的腐蝕產物。通過對腐蝕48 h 的樣品表面進行EDS 點掃描(圖4),發現腐蝕48 h 后2195 鋁合金表面基本上還是以Al 為主,未見S、N 和Cl 等腐蝕性元素,這可能是由于生成的腐蝕產物掉落溶解到腐蝕液中了。
7075 鋁合金腐蝕行為類似于2195 鋁鋰合金,在腐蝕初期就出現一些零散的絮狀腐蝕產物覆蓋在樣品表面。這是由于7075 鋁合金表面的氧化膜被破壞后,其鋁基體與腐蝕介質中的Cl-發生電化學反應,在鋁合金表面生成一層比較粗糙和疏松的腐蝕產物[18]。腐蝕24 h 后覆蓋在樣品表面的腐蝕產物越來越多,腐蝕48 h 后覆蓋在樣品表面的腐蝕產物進一步增多,并出現龜殼狀裂紋,這是晶間腐蝕的典型特征。用EDS 能譜分析腐蝕48 h 后的7075 鋁合金表面特征點,所得點譜圖如圖5 所示。腐蝕48 h 后7075 鋁合金表面主要存在Al 元素和O 元素,說明覆蓋在基體上的腐蝕產物為氧化鋁。S、N、Cl 等腐蝕性元素并未參與腐蝕反應,可能只起到了腐蝕催化作用。
圖2 三種鋁合金腐蝕形貌隨腐蝕時間變化圖
圖3 腐蝕48h 后6061 鋁合金表面EDS 點譜圖
圖4 不同腐蝕時間2195 鋁合金腐蝕層深度變化
圖5 腐蝕48h 后7075 鋁合金表面EDS 點譜圖
圖6 為3 種鋁合金腐蝕層厚度形貌圖,圖7 為3 種鋁合金腐蝕層厚度隨腐蝕時間的變化曲線圖。從圖中可以看出,3 種鋁合金腐蝕層深度隨腐蝕時間延長在不斷增加,在腐蝕6 h后6061、2195、7075 鋁合金的腐蝕層深度分別為8.34 μm、0 μm 和0.81 μm;6061 鋁合金的腐蝕速度最快,7075 鋁合金次之,2195 鋁鋰合金還未見明顯腐蝕。在腐蝕48 h 后,6061、2195、7075 鋁合金的腐蝕層厚度分別為21.6,2.25,12.8μm;6061 鋁合金腐蝕速度最快,2195鋁鋰合金腐蝕最慢,這也比較符合3 種鋁合金表面腐蝕形貌的結果。
圖6 不同腐蝕時間3 種鋁合金腐蝕層厚度
圖7 三種鋁合金腐蝕層深度變化
3 鋁合金腐蝕過程中的力學性能演變
對6061 鋁合金母材(BM)和經過不同腐蝕時間腐蝕的樣品進行室溫拉伸實驗,所得工程應力應變曲線如圖8 所示。圖9 為其強度和塑性的變化統計圖,圖中sb 為抗拉強度,s0.2為屈服強度,d為延伸率。未經過腐蝕的6061 鋁合金抗拉強度為215 MPa 左右,延伸率為14.6%。隨著腐蝕時間延長,其強度并未發生比較大變化,腐蝕1 周(168 h)后的樣品仍然保持在214 MPa 左右,而塑性在經過腐蝕后出現了輕微的下降,從母材的14.6%降至腐蝕1周后的12.6%。從掃描電鏡中,我們觀察到6061 鋁合金經過腐蝕后,其表面被腐蝕得很嚴重,但強度和塑性并沒有特別劇烈的改變,因此,在腐蝕環境中6061 鋁合金的性能具有比
圖8 6061 不同腐蝕時間的6061 鋁合金工程應力應變曲線
圖9 不同腐蝕時間6061 鋁合金強度和塑性變化圖
2195 鋁鋰合金作為第三代高強鋁鋰合金,具有比較高的強度和良好的塑性,圖10 為2195鋁鋰合金母材和腐蝕不同時間后的樣品的工程應力應變曲線,其強度和塑性的變化見圖11。在被腐蝕后2195 鋁鋰合金的強度和塑性都明顯地降低了,2195 鋁鋰合金母材強度為490 MPa,延伸率為22.5%,隨著被腐蝕時間延長,強度逐步降低,腐蝕1 周后的樣品強度僅為310 MPa,延伸率降低至3.5%,強度和塑性相比母材分降低了180 MPa 和19%,這說明2195 鋁鋰合金在被腐蝕后性能變動大,耐腐蝕性能相對較差。
圖10 不同腐蝕時間的2195 鋁鋰合金工程應力應變曲線
圖11 不同腐蝕時間2195 鋁鋰合金強度和塑性變化圖
圖12 為7075 鋁合金母材與經過不同腐蝕時間腐蝕后的樣品的工程應力應變曲線,其強度和塑性的變化見圖13。被腐蝕后7075 鋁合金的強度和塑性隨時間延長逐步降低,7075鋁合金母材抗拉強度為558 MPa,屈服強度為534 MPa,延伸率為11.3%,腐蝕時間延長至24 h 后,其抗拉強度為524 MPa,屈服強度為500 MPa,延伸率為8.3%,分別降低了34MPa、34MPa 和3%。當腐蝕時間延長至1 周后,其抗拉強度降低至460 MPa,屈服輕度降低至430 MPa,延伸率僅為3.1%。這說明在高腐蝕性環境中7075 鋁合金的耐腐蝕性能也比較差。
圖12 不同腐蝕時間的7075 鋁合金工程應力應變曲線
圖13 不同腐蝕時間7075 鋁合金強度和塑性變化圖
4 結 論
1) 3 種鋁合金的腐蝕行為不盡相同,6061 鋁合金和2195 鋁鋰合金在高Cl-、NO3-、SO42-的腐蝕液中的腐蝕方式是由點腐蝕向面腐蝕的轉變,而7075 腐蝕方式是逐步出現大面積龜甲狀裂紋,并且7075 鋁合金和2195 鋁鋰合金腐蝕后表面會覆蓋一層腐蝕產物薄膜,而6061鋁合金的腐蝕產物溶解到腐蝕液中。
2) 在被腐蝕后6061 鋁合金的強度和塑性都沒有明顯的變化,而2195 鋁合金和7075鋁合金隨著被腐蝕時間延長,其強度和延伸率都明顯地降低,說明6061 鋁合金的力學性能具有比較好的腐蝕穩定性,2195 和7075 鋁合金鋁鋰合金的耐腐蝕性能不佳。
參考文獻:
[1] 鐘掘.輕合金加工技術,2002,30(05):1.
[2] 葉浩. 2024鋁合金的熔鑄及形變熱處理工藝研究[D].湖南大學,2012.
[3] 白志玲.鋁合金的研究現狀及應用[J].科技廣場,2015(12):18-20.
[4] 宋海林,高萌,邢娜,王成龍,陳永斌.2種鹽霧環境下6061車用鋁合金的加速腐蝕行為研究[J].材料保護,2020,53(11):21-25+31.
[5] Yang Minjie.Study on corrosion property and mechanism of sprayformed 7055 aluminum alloy[D].Lanzhou: Lanzhou University of Technology, 2014.
[6] H-Y Ding, G-H Zhou, D Hui. Friction and wear performance of an aluminium alloy in artificial seawater[J]. Proceedings of the Institution of Mechanical Engineers, 2011, 225(1): 43–49. doi: 10.1243/09544070JAUTO1462.
[7] 陶永奇, 劉剛, 黎業生, 等. 海水環境下2024鋁合金腐蝕磨損性能研究[J]. 中國腐蝕與防護學報, 2016, 36(6): 587–594.
[8] 李琳琳. 6×××系鋁合金中第二相Mg_2Si的局部腐蝕機理研究[D].沈陽工業大學,2017.
[9] 李曉剛.材料腐蝕與防護概論[M].北京:機械工業出版社,2017.
[10] 徐火平,劉慧叢,朱立群,劉建中,葉序彬,胡本潤.鹽霧環境中高強鋁合金點腐蝕行為與暴露面積的關系[J].航空材料學報,2010,30(04):59-64.
[11] 李亞萍,曲鳴飛.機械裝備用6xxx系鋁合金在氯鹽溶液中的腐蝕行為及其防護[J].電鍍與環保,2019,39(06):42-44.
[12] 魏立艷. 微觀組織結構對鋁及鋁合金腐蝕行為的影響[D].哈爾濱工程大學,2009.
[13] 殷士焜. 2198鋁鋰合金激光焊接接頭的腐蝕行為及機理研究[D].北京工業大學,2016.
[14] 李云濤,李曉寧,包俊成,周世杰.2024鋁合金鹽霧腐蝕評估及腐蝕形貌分析[J].腐蝕與防護,2015,36(09):864-868.
[15] 張仁群,王斌,岳濤,趙曉林.淺析國軍標GJB150與美軍標MIL-STD-810F鹽霧試驗[J].環境技術,2008(05):42-45+26.
[16] 程文禮,楊慧,任德杰,何二鋒,李玉峰.表面處理對鋁合金鹽霧環境下的腐蝕特性試驗研究[J].航空制造技術,2020,63(12):92-96.
[17] Zhang Y, Yin X, Wang J, et al. Influence of microstructureevolution on tribocorrosion of 304SS in artificial seawater[J].Corrosion Science, 2014, 88(11): 423–433.
免責聲明:本網站所轉載的文字、圖片與視頻資料版權歸原創作者所有,如果涉及侵權,請第一時間聯系本網刪除。
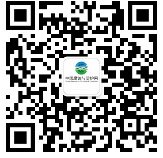
官方微信
《中國腐蝕與防護網電子期刊》征訂啟事
- 投稿聯系:編輯部
- 電話:010-62316606-806
- 郵箱:fsfhzy666@163.com
- 中國腐蝕與防護網官方QQ群:140808414