摘要
采用多弧離子鍍技術在鎳基高溫合金上沉積NiCoCrAlY涂層,通過真空熱處理消除涂層內部孔洞。研究了950、1000和1050 ℃熱處理后的涂層在1000 ℃下的氧化實驗,以探究最優的熱處理溫度。采用XRD、SEM和EDS觀察分析涂層的物相組成和表截面形貌。結果表明,真空熱處理后,基體與涂層結合緊密,氧化增重相對緩慢,涂層表面能形成均勻致密的氧化膜。其中,1000 ℃下真空熱處理的涂層表現出了良好的抗氧化和防剝落性能。
關鍵詞: MCrAlY涂層 ; 高溫氧化 ; 真空熱處理 ; 多弧離子鍍 ; 高溫防護涂層
鎳基高溫合金由于具有良好的高溫力學性能和抗腐蝕性能,被廣泛用作渦輪發動機和燃氣輪機的關鍵組件[1,2]。在高溫環境下,合金中的Al和Cr會擴散到基體表面形成致密的氧化膜,從而減緩合金的氧化進程。其中,具有等軸晶結構的穩定α-Al2O3被認為是最有效的抗氧化保護膜。但由于合金本身所含Al/Cr的含量較低[3],在長期高溫氧化的過程中會逐漸被消耗至較低水平,當其低于生成保護性氧化膜的臨界濃度時,外界中的氧氣就會擴散進入基體內部引起合金失效。因此為滿足長期在高溫環境下的服役要求,通常會在合金表面施加Al/Cr含量高的防護涂層。
在高溫防護涂層中,MCrAlY涂層 (M=Ni,Co或Ni+Co) 因其良好的抗高溫氧化性和耐疲勞性,被廣泛鍍覆在鑄造、定向凝固以及單晶高溫合金表面上[4]。MCrAlY涂層制備技術主要包括多弧離子鍍 (AIP)[5]、磁控濺射 (MS)[6,7]、電子束物理氣相沉積 (EB-PVB)[8]以及等離子噴涂 (PS)[9]等。其中真空環境下進行多弧離子鍍有效避免了涂層的氧化和雜質污染,能使涂層與基體之間形成冶金結合。其次,多弧離子鍍有很好的繞鍍性,轟擊產生的氣體離子會不斷與爐腔中的氬氣等惰性氣體碰撞,發生散射現象,很好地避免了陰影效應,使不對著靶材的基體側面也能鍍上涂層[10]。因此,多弧離子鍍更適用于形狀較為復雜的飛機發動機葉片涂層的沉積。但AIP技術也存在著一些缺點,涂層制備過程中仍然會在涂層內部及涂層基體界面處產生不可避免的孔隙[11],這些孔隙中的氧在后期高溫氧化過程中與涂層中金屬元素結合,使涂層快速發生內氧化,降低了涂層的抗氧化性能。Yuan等[12]將通過冷噴涂技術在鎳基高溫合金上沉積得到的NiCoCrAlY涂層在1120 ℃下真空熱處理2 h,表明熱處理后的NiCoCrAlY涂層出現了典型的β/γ相,在隨后的恒溫氧化實驗中形成氧化層的總體生長速率明顯低于沉積態涂層。田曄等[13]研究表明通過熱處理能夠促進涂層與高溫合金基體之間發生元素擴散,提高涂層與基體之間的結合強度。目前關于MCrAlY涂層的研究主要集中在對涂層自身成分的優化設計,而對通過真空熱處理提高涂層性能的研究較少,涉及熱處理參數對涂層性能影響的研究還尚未有報道。
本文采用多弧離子鍍技術在鎳基高溫合金K417G表面制備NiCoCrAlY涂層,研究了在不同溫度下真空熱處理試樣在1000 ℃下氧化實驗,通過對比分析其微觀形貌和物相組成,探究最優的真空熱處理溫度,并討論了熱處理對氧化行為影響機理。
1 實驗方法
實驗基體材料采用K417G合金 (樣品尺寸20 mm×10 mm×3.5 mm),合金的化學成分 (質量分數,%) 為:C 0.13~0.22,Cr 8.5~9.5,Co 9.0~11,Al 4.8~5.7,Mo 2.5~3.5,Ti 4.1~4.7,V 5~0.9,Ni余量。采用DH-4型多弧離子鍍設備制備NiCoCrAlY涂層,涂層名義成分 (質量分數,%) 為:Cr 27.0,Co 19.0,Al 11.0,Y 0.5,Hf 0.2,Si 0.1,Ni余量。涂層沉積前對試樣進行研磨、濕噴砂和清洗處理。裝爐后,通入氬氣至0.2 MPa,對試樣表面進行約20 min的弧光轟擊以清洗掉表面的雜質。采用合金靶材來沉積NiCoCrAlY涂層,沉積時間為11 h,得到厚度約45 μm的NiCoCrAlY涂層。
涂層沉積完成后,設置退火溫度為950、1000和1050 ℃ (稱為950 ℃組、1000 ℃組和1050 ℃組,統稱為熱處理組),將樣品置于真空度≤6.67×10-3 Pa的退火爐中保溫4 h后隨爐冷卻,每個退火溫度下設置3個平行樣品,并設置3個未進行熱處理的試樣作為對照組 (稱為未處理組)。
將試樣置于1000 ℃的管式爐中進行氧化實驗。每隔20 h取出,隨環境冷卻至室溫,連同坩堝一起用精度為0.01 mg的電子天平進行稱重。稱重結束后,樣品繼續放回管式爐繼續進行氧化。每組試樣的氧化增重為3個試樣氧化增重的平均值。
采用X'Pert PRO型X射線衍射儀 (XRD) 測定涂層的物相結構;利用帶能譜 (EDS) 的Inspect F50場發射掃描電子顯微鏡 (SEM) 觀察涂層的表面和截面形貌以及微區的元素分布,綜合分析涂層的氧化行為。
2 結果與分析
2.1 熱處理后涂層的微觀形貌與物相組成
圖1是熱處理組試樣的表截面形貌。由圖1a~c可知,通過多弧離子鍍技術制備的涂層經不同溫度下熱處理后的表面形貌相差不大,均勻分布著微米級的熔滴。由圖1d~f可知,熱處理后涂層內部析出較多灰色顆粒,形成致密組織。
圖1 熱處理后3組試樣的表面及截面形貌
圖2中的XRD圖譜顯示經熱處理后的涂層由單一的γ/γ′固溶體轉變為β+σ+γ/γ′的多相平衡組織。其中,β-NiAl富鋁相的產生為后期高溫氧化過程中在涂層表面形成致密的Al2O3層提供了充足的Al源[14]。
圖2 沉積態和真空熱處理后涂層的XRD譜
2.2 氧化動力曲線
試樣在1000 ℃下空氣中氧化100 h的動力學曲線如圖3a所示。總體而言,各組實驗的氧化增重趨勢大致相同,動力學曲線基本符合拋物線規律。在氧化前20 h,試樣氧化增重較快,這是由于涂層在高溫氧化時,表面會快速的形成一層抗高溫氧化膜。它將涂層與氣相隔開,反應物質需通過氧化膜擴散才能進一步氧化,使得氧化機制由界面反應控制轉變為擴散控制,有效地減緩了氧化過程[15,16],表現為動力學曲線上20~80 h的緩慢增重過程。與此同時,氧化物層也會隨氧化時間延長而生長增厚,在內應力的作用下,發生開裂和剝落,隨后氧化層剝落露出的涂層表面會迅速被氧化形成氧化層,這解釋了80~100 h氧化增重的加快的原因,其中熱處理950 ℃組和1050 ℃組尤為明顯。
圖3 試樣在1000 ℃下空氣中氧化100 h的氧化動力學曲線及拋物線速率常數
通過公式 (1) 計算出涂層穩定增長階段 (80 h以內) 動力學拋物線速率常數:
(1)
式中,Δw為試樣單位面積的增重,t為氧化時間。使用最小二乘法線性擬合得到圖3b,未處理組及3組熱處理組的氧化動力學數據 (Kp) 分別為:3.99×10-3,1.77×10-3,2.36×10-3和2.18×10-3 mg2·cm-4·h-1。可以看出,熱處理組的拋物線速率常數都保持在1.77×10-3~2.36×10-3 mg2·cm-4·h-1范圍內,而未處理組拋物線速率常數將近熱處理組的兩倍。說明熱處理能有效降低涂層試樣的氧化速率。
2.3 涂層氧化后的物相組成
圖4是試樣在1000 ℃下氧化100 h的XRD衍射譜。可見,熱處理和未處理組涂層的相組成基本相同,均為涂層主相γ/γ′和氧化產物Al2O3。
圖4 試樣在1000 ℃下氧化100 h的XRD譜
2.4 涂層的形貌分析
圖5a~h是試樣在1000 ℃下氧化100 h后的表面形貌。EDS分析顯示表面氧化物主要含Al和O,結合XRD推測氧化物為α-Al2O3。未處理組表面氧化物疏松 (如圖5a),出現較多裂紋。熱處理組中,相較于1050 ℃組,950 ℃組和1000 ℃組涂層表面顆粒較為細小致密。此外,在950 ℃組和1050 ℃組試樣表面出現了孔洞。
圖5 試樣在1000 ℃下氧化100 h的表面形貌及截面形貌
圖5e~h是試樣在1000 ℃下氧化100 h的截面形貌。圖5e中未處理組涂層表面氧化膜起伏較大,部分灰色的氧化膜已經脫離了涂層表面,推測可能是氧化前期產生脆性大的尖晶石等氧化產物在后期氧化過程中逐漸開裂剝落[17]。其次,未處理組涂層發生了明顯的內氧化現象,在靠近涂層表面的地方出現了裂紋和顆粒狀黑色氧化物,EDS分析顯示此處主要是Cr、Ni和O,推測內氧化產物為Cr2O3或尖晶石。相較于未處理組,熱處理組中氧化膜較致密,未出現剝落。但950 ℃組表面氧化膜厚度不均勻,最薄處僅有1 ?m;1050 ℃組外層氧化膜的生長出現了明顯的不均勻性,向涂層的一些部位優先生長,呈現為V型,這種V型熱生長氧化物部位及界面的起伏會改變局域應力的分布,產生垂直于界面的拉應力,從而為裂紋的形成和擴展提供驅動力,加速氧化膜的剝落[18,19]。而在1000 ℃下熱處理試樣的表面形成了厚度均勻,連續致密的氧化膜。
綜合考慮認為1000 ℃組涂層表面氧化膜具有最好的抗氧化和抗剝落性能。
3 討論
利用多弧離子鍍進行涂層沉積時,蒸汽靶材粒子在到達基體的過程中,會與真空室中的氬氣分子碰撞損失一部分能量。因此,部分靶材粒子可能沒有足夠的動能與基體碰撞形成致密的涂層,從而導致涂層中出現氣體夾雜物,即孔洞的形成[20]。熱處理后,在涂層內原孔洞部分析出了深灰色的相,使得涂層組織變得更加致密。這是由于沉積態涂層主相γ/γ′為面心立方結構,晶格常數分別為0.3523和0.3572 nm。經過熱處理后發生相轉變,析出正方結構的σ相,其晶格常數為a=0.881 nm,c=0.456 nm,導致了體積膨脹,填補了涂層內部的微小孔洞。
在本實驗中,未處理組氧化膜發生了明顯的開裂與剝落 (圖5a和e),這是由于氧化膜中累積內應力超過自身結合強度導致的。氧化層中通常存在兩種類型的應力:氧化過程中產生的生長應力和氧化試樣冷卻至室溫時產生的熱應力[19]。生長應力是由氧化物與形成氧化物的金屬之間的體積差產生,體積差異一般用PBR值 (pilling-bedworth ratio) 值表示[21],公式如下 (2) 所示:
(2)
其中,Voxides和Valloy分別是氧化物和金屬的體積。查閱數據[22]可得Al2O3、Cr2O3和NiCr2O4的PBR值分別為1.28、1.29和2.05。體積的差異會導致生長應變ε,由下式可得:
(3)
一般認為,當PBR>1時,氧化層中會產生壓應力。基于生長應變,生長應力σG可以通過Hooke定律估計:
(4)
其中,Eoxides是氧化物的Young's模量,查閱文獻可知[21],Al2O3、Cr2O3和NiCr2O4的Young's模量約為325、260和233 GPa,計算得到其生長應力分別為27.85、23.03和62.99 GPa。可以看到未處理組氧化產物NiCr2O4引起的生長應力明顯大于熱處理組氧化產物Al2O3引起的生長應力,即更容易引起氧化層的開裂與剝落。
此外,由于氧化膜和涂層之間的熱膨脹系數不同,使得試樣在空冷過程中氧化層與涂層的熱變形量不同,產生形變熱應力。熱應力可以表示為:
(5)
其中,αcoating和αoxides分別是涂層和氧化物的膨脹系數,△T是冷卻過程中的溫差。由文獻可知[23,24],NiCoCrAlY涂層、Al2O3、Cr2O3和NiCr2O4的熱膨脹系數依次為18.5、9.7、9.6和7.6 10-6/℃,通過計算得到各氧化物產生熱應力分別為2.79、2.26和2.48 GPa。可以看出各氧化物引起的熱應力的數值差距不大,且遠小于生長應力,說明生長應力是引起氧化膜層剝落的主要原因。涂層的熱膨脹系數遠高于氧化物的熱膨脹系數,因此氧化物產生的熱應力應該是壓應力方向,這與生長應力作用效果相同。
在恒溫氧化初期,未處理組涂層中Al、Cr和Ni元素會向外擴散在涂層表面形成Al2O3、Cr2O3和NiO的混合氧化物層。其中,Cr2O3和NiO會快速發生反應生成NiCr2O4。由上式 (2~4) 可知,NiCr2O4會產生較大的生長應力,隨著氧化實驗的進行,膜內的應力積累也越來越大,當應力超過氧化膜自身的結合強度時,氧化膜便破裂、剝落[25],這也與圖7a未處理組中氧化膜灰色部分的剝落相符。同時,氧化膜的破裂、剝落也為外界環境中的O原子向涂層內部擴散提供了通道[26]。當O原子經由涂層內部孔隙處擴散至Al的貧化區時,會與涂層中的Ni和Cr發生氧化反應生成Cr2O3或NiCr2O4。然而,Cr2O3僅在低溫環境下保護底層合金免受氧化,在高于1000 ℃的溫度會生成揮發性氧化物CrO3,在涂層內部留下孔隙,這使得O原子在涂層內部的擴散更為便捷,加速了涂層的氧化失效[27]。未處理組在氧化初期和后期均產生了混合氧化物,這使得其在宏觀動力學曲線上始終保持較大的氧化增重和較快的增重速率。
而涂層經熱處理后析出了β-NiAl富鋁相,涂層表面附近Al的富集使得氧化初期在涂層表面優先生成低生長應力的Al2O3層,在隨后的氧化過程中未出現明顯的剝落。且熱處理使得涂層內部組織緊密,有效抑制了O原子在后期氧化過程中向涂層內部擴散。其中,950和1050 ℃組涂層在后期氧化過程中氧化層表面出現了孔洞,為O原子進入涂層內部發生內氧化提供機會,這也表現在950 ℃和1050 ℃組宏觀動力學曲線上80~100 h的迅速增重。
4 結論
(1) 沉積態涂層為單一的γ/γ′相,在恒溫氧化過程中表面會形成結構疏松的氧化物,在涂層內部發生明顯的內氧化,導致氧化增重速率較快。
(2) 真空熱處理使涂層形成了β+σ+γ/γ′多相平衡組織,消除了涂層內部孔隙。在恒溫氧化過程中,表面會形成致密的Al2O3層,降低了其發生內氧化的可能,使得氧化增重明顯小于沉積態涂層。
(3) 1000 ℃下真空熱處理的涂層恒溫氧化后生成了平整致密的Al2O3層,且表面沒有孔洞,顯示出好的抗高溫氧化和抗剝落性能。
參考文獻
1 Smith R J, Lewi G J, Yates D H. Development and application of nickel alloys in aerospace engineering [J]. Aircr. Eng. Aerosp. Technol., 2001, 73: 138
2 Cruchley S, Evans H E, Taylor M P, et al. Chromia layer growth on a Ni-based superalloy: Sub-parabolic kinetics and the role of titanium [J]. Corros. Sci., 2013, 75: 58
3 El-Awadi G A, Abdel-Samad S, Elshazly E S. Hot corrosion behavior of Ni based Inconel 617 and Inconel 738 superalloys [J]. Appl. Surf. Sci., 2016, 378: 224
4 Li Y, Li C J, Yang G J, et al. Thermal fatigue behavior of thermal barrier coatings with the MCrAlY bond coats by cold spraying and low-pressure plasma spraying [J]. Surf. Coat. Technol., 2010, 205: 2225
5 Zhu L J, Zhu S L, Wang F H, et al. Comparison of the cyclic oxidation behavior of a low expansion Ni+CrAlYSiN nanocomposite and a NiCrAlYSi coating [J]. Corros. Sci., 2014, 80: 393
6 Cheruvu N S, Wei R, Govindaraju M R, et al. Cyclic oxidation behavior and microstructure of nanocrystalline Ni-20Cr-4Al coating [J]. Oxid. Met., 2010, 73: 493
7 Wang F H. The effect of nanocrystallization on the selective oxidation and adhesion of Al2O3 scales [J]. Oxid. Met., 1997, 48: 215
8 Peng H, Guo H B, He J, et al. Oxidation and diffusion barrier behaviors of double-layer NiCoCrAlY coatings produced by plasma activated EB-PVD [J]. Surf. Coat. Technol., 2011, 205: 4658
9 Wu Y N, Zhang G, Feng Z C, et al. Oxidation behavior of laser remelted plasma sprayed NiCrAlY and NiCrAlY-Al2O3 coatings [J]. Surf. Coat. Technol., 2001, 138: 56
10 Xie S M, Lin S S, Shi Q, et al. A study on the mechanical and thermal shock properties of MCrAlY coating prepared by arc ion plating [J]. Surf. Coat. Technol., 2021, 413: 127092
11 Ghadami F, Aghdam A S R, Ghadami S. Microstructural characteristics and oxidation behavior of the modified MCrAlX coatings: A critical review [J]. Vacuum, 2021, 185: 109980
12 Yuan K, Peng R L, Li X H, et al. Some aspects of elemental behaviour in HVOF MCrAlY coatings in high-temperature oxidation [J]. Surf. Coat. Technol., 2015, 261: 86
13 Tian Y, Guo S L, Yang X J. Effects of heat treatment on microstructure and properties of NiCoCrAlY coating with HVOF spraying [J]. Therm. Spray Technol., 2018, 10(3): 19
13 田曄, 郭素麗, 楊曉劍. 熱處理對超音速火焰噴涂NiCoCrAlY涂層組織性能的影響 [J]. 熱噴涂技術, 2018, 10(3): 19
14 Ullah A, Khan A, Bao Z B, et al. Effect of vacuum annealing on initial oxidation behavior and alumina transition of NiCoCrAlY coatings [J]. Surf. Coat. Technol., 2020, 404: 126441
15 Guo C, Zhou F, Chen M H, et al. An in-situ formed ceramic/alloy/ceramic sandwich barrier to resist elements interdiffusion between NiCrAlY coating and a Ni-based superalloy [J]. J. Mater. Sci. Technol., 2021, 70: 1
16 Yang H Z, Zou J P, Shi Q, et al. Recent advances for interface diffusion behavior in MCrAlY coatings at elevated temperature oxidation [J]. Rare Met. Mater. Eng., 2020, 49: 2240
16 楊洪志, 鄒儉鵬, 石倩等. MCrAlY涂層高溫氧化界面擴散行為研究進展 [J]. 稀有金屬材料與工程, 2020, 49: 2240
17 Yang S W, Wang J Y, Sun J, et al. High temperature oxidation of the DZ4 directionally-solidified superalloy [J]. J. Harbin Eng.Univ., 2008, 29: 95
17 楊世偉, 王俊一, 孫杰等. DZ4定向凝固合金的抗高溫氧化行為研究 [J]. 哈爾濱工程大學學報, 2008, 29: 95
18 Du H Q, Tian S G, Yu X F, et al. Influences of NiCoCrAlYSi coating on high temperature oxidation characteristic of single crystal nickel-base superalloy [J]. Rare Met. Mater. Eng., 2008, 37: 1555
18 杜洪強, 田素貴, 于興福等. NiCoCrAlYSi涂層對鎳基單晶合金高溫氧化特性的影響 [J]. 稀有金屬材料與工程, 2008, 37: 1555
19 Zheng L, Zhang M C, Chellali R, et al. Investigations on the growing, cracking and spalling of oxides scales of powder metallurgy Rene95 nickel-based superalloy [J]. Appl. Surf. Sci., 2011, 257: 9762
20 Shen M L, Zhao P P, Gu Y, et al. High vacuum arc ion plating NiCrAlY coatings: microstructure and oxidation behavior [J]. Corros. Sci., 2015, 94: 294
21 Li W Z, Li Y Q, Yi D Q, et al. Microstructural evolution and failure mechanism of NiCrAlY coating systems during different cycled oxidations [J]. Chin. J. Nonferrous Met., 2013, 23: 417
21 李偉洲, 李月巧, 易丹青等. 不同冷熱循環條件下NiCrAlY涂層體系的微觀組織演變規律及失效機理 [J]. 中國有色金屬學報, 2013, 23: 417
22 Wang H T. Effects and mechanism of composite oxide scale on oxidation resistance of ferro based supperalloys [D]. Ji'nan: Shandong University, 2010
22 王海濤. 復合氧化膜對鐵基高溫合金抗氧化性能影響與機理研究 [D]. 濟南: 山東大學, 2010
23 Yang S S, Yang L L, Chen M H, et al. Understanding of failure mechanisms of the oxide scales formed on nanocrystalline coatings with different Al content during cyclic oxidation [J]. Acta Mater., 2021, 205: 116576
24 Haynes J A, Pint B A, Porter W D, et al. Comparison of thermal expansion and oxidation behavior of various high-temperature coating materials and superalloys [J]. Mater. High Temp., 2004, 21: 87
25 Birks N, Meier G H, Pettit F S. Introduction to the High Temperature Oxidation of Metals [M]. 2nd ed. Cambridge: Cambridge University Press, 2006
26 Jia Y X, Zhu S L, Liu Z L, et al. Effects of oxygen incorporation in low expansion Ni+CrAlYN nanocomposite coatings on the oxidation behavior [J]. Corros. Sci., 2020, 167: 108550
27 Li M S. High Temperature Corrosion of Metals [M]. Beijing: Metallurgical Industry Press, 2001
27 李美栓. 金屬的高溫腐蝕 [M]. 北京: 冶金工業出版社, 2001
免責聲明:本網站所轉載的文字、圖片與視頻資料版權歸原創作者所有,如果涉及侵權,請第一時間聯系本網刪除。
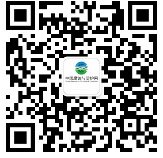
官方微信
《腐蝕與防護網電子期刊》征訂啟事
- 投稿聯系:編輯部
- 電話:010-62316606-806
- 郵箱:fsfhzy666@163.com
- 腐蝕與防護網官方QQ群:140808414