案件背景
金屬零部件在外加載荷的作用下,當應力達到材料的斷裂強度時,發生斷裂。其中80%以上的斷裂是由于疲勞引起的,極易造成人身事故以及經濟損失。因此認識疲勞現象,研究疲勞破壞規律,防止疲勞失效是非常重要的。我司昆山實驗室收到客戶委托,客戶產品為45#鋼傾油缸接頭,在模擬使用條件下進行加速實驗約2萬次時,發生斷裂現象,委托優爾鴻信檢測分析其斷裂原因。
測試方案
斷口形貌觀察:樣品斷口形貌分析,初步判斷其斷裂形式;
顯微金相組織分析/洛氏硬度測試:查看其熱處理工藝;
化學成分測試:分析判斷其含量是否符合國家標準。
SEM斷口形貌
2#-20X
5#-20X
掃描電鏡觀察斷口形貌,通過SEM掃描照片可知:圖2#-20X和5#-20X為樣品斷口裂紋源低倍形貌,可見樣品外緣存在多個臺階,呈明顯的線源特征,結合樣品宏觀形貌,肉眼可見斷口邊緣區域有擠壓摩擦變亮痕跡,可判斷裂紋起源于軸根部外表面螺紋凹痕處,該斷口屬多源且有應力集中現象。將裂紋源附近放大后觀察,可見明顯的疲勞輝紋,呈疲勞斷裂特征。
1#到6#位置SEM照片可以看出樣品內部存在明顯的疲勞輝紋及大量的二次裂紋,在部分區域可觀察到機械損傷的犁痕和氧化特征,犁痕方向與斷裂過程的受力方向基本一致。疲勞輝紋的擴展方向大部分由斷口表面兩側向中間位置擴展。7#位置中部發現韌窩結構,因此中間軸區域為最終斷裂階段。大致斷裂方向如圖箭頭所示。
金相組織分析
樣品斷口附近取樣,經過研磨機械拋光制成金相試樣,用4%硝酸酒精溶液腐蝕后,用金相顯微鏡觀察金相組織可見:材料內部存在夾雜物及孔洞,斷口附近金相組織主要由網狀鐵素體+少量塊狀鐵素體+珠光體組成,不符合調質組織。
洛氏硬度分析
將樣品表面漆層打磨掉,用洛氏硬度計測試樣品硬度值可知,洛氏硬度值為86.3HRB,硬度偏低。
化學成分分析
備注:所給成分結果為質量百分比
將樣品表面漆層打磨掉,用火花原子放射光譜儀測試化學成分可知,化學成分符國家標準中45#鋼成分要求。
原因分析
斷口宏觀和微觀分析結果表明:裂紋源位于螺紋凹痕位置外表面,裂紋源存在多個臺階,呈明顯的線源特征,斷口上可見明顯疲勞輝紋,因此可判定樣品斷裂模式為多源疲勞斷裂,且有應力集中現象。
斷口臺階是多個疲勞源萌生的裂紋交匯臺階,一般在高應力集中疲勞斷口中
常見,加速實驗過程中,螺紋凹痕處造成應力集中,使凹痕根部的最大實際應力遠大于零件所能承受的名義應力。在循環應力作用下,凹痕截面上的應力狀態發生變化,從而影響試件的力學性能,對零件產生疲勞破壞。較大尺寸的非金屬夾雜物也是疲勞裂紋的啟裂源。
試樣內部存在孔洞及夾雜物、組織分布不均勻、熱處理不當等因素可導致試樣的實際承載能力和安全性能大大降低。金相組織存在網狀鐵素體和少量塊狀鐵素體,造成材料軟點,硬度偏低。
結合以上試驗結果,對樣品發生疲勞斷裂的原因分析如下:
(1)熱處理不當
材料的微觀組織與工藝、性能密切相關,原材料可能未經調質處理或調質處理不當,造成該試樣的力學性能較低。
(2)應力集中
試樣在加速實驗過程中承受雙向彎曲載荷的作用,螺栓螺牙處應力集中使局部區域的應力值超過了該軸按預定壽命所能承受的應力水平,致使裂紋在軸表面萌生。
建議
為避免傾油缸接頭發生類似斷裂失效問題,應從材料熱處理工藝、表面加工質量等方面層層把關,嚴格執行標準技術要求。
免責聲明:本網站所轉載的文字、圖片與視頻資料版權歸原創作者所有,如果涉及侵權,請第一時間聯系本網刪除。
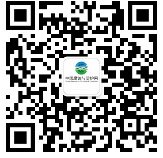
官方微信
《腐蝕與防護網電子期刊》征訂啟事
- 投稿聯系:編輯部
- 電話:010-62316606-806
- 郵箱:fsfhzy666@163.com
- 腐蝕與防護網官方QQ群:140808414