摘要
電鍍技術常用來對已破損的零件進行修復與再制造,然而其耐磨性及耐腐蝕性能需要進一步改善。在電鍍技術的基礎上向鍍液中添加不同濃度的 CeCl3 化合物(0、0.5、1、1.5 g / L)制備出復合鍍層以探究其對電鍍層性能的影響。結果表明: 在鍍液中添加 CeCl3 化合物會使復合鍍層中鐵晶粒呈現較好的擇優取向性;隨著鍍液中 CeCl3 化合物濃度的逐漸提升,復合鍍層的顯微硬度、耐磨性、耐腐蝕性均呈現出先提高后減弱的狀態;當鍍液中 CeCl3 化合物濃度為 0.5g / L 時,復合鍍層的表面結構更為均勻、鍍層中鐵晶粒的排列更加致密,其顯微硬度達到 611.4 HV,具有最佳的耐磨性和耐腐蝕性能。研究成果表明鍍液中添加稀土 CeCl3 化合物可以大幅度提高鍍層的耐腐蝕性,并在一定程度上提高鍍層的耐磨性,可為實際生產中提高鍍鐵層的耐磨性及耐腐蝕性能提供理論指導。
關鍵詞: 電鍍 ; 復合鍍層 ; 梯度濃度 ; 顯微硬度 ; 耐磨性 ; 耐腐蝕性
0 前言
在遠洋運輸行業中,許多船舶機械零部件及船舶設備,如船舶柴油機活塞環、曲軸、軸瓦在經過長時間工作后,不可避免地會發生磨損,造成船舶設備的失效,這會極大地影響船舶運行過程中的安全性。所以,采用高效、成本較低的手段對船舶機械零部件進行強化處理是必不可少的一環,可以達到減少零件磨損和磨損后修復的作用[1]。常見的表面修復手段及修復工藝有離子注入、滲氮、滲碳或碳氮共滲等以及鋼鐵表面淬火、熱噴涂、物理氣相沉積、化學氣相沉積、激光熔覆等。但是,它們都存在一定的缺點,鍍鐵技術與它們相比,具有明顯的優勢,它的沉積效率較高、成本較低,對環境污染較小,尤其在鋼鐵表面進行鍍鐵,由于兩者晶格屬性相同,可以制備出與基體結合強度很高的鍍層。為了降低資源的消耗率,提高設備的使用壽命,可以從兩方面進行改善:一是提高船舶零部件材料的耐用性,二是提高受損零部件的修復率。其中有關鍍鐵的表面處理技術作為成熟的工藝廣泛地應用于再制造領域,并且創造了可觀的社會價值和經濟效益。低溫無刻蝕鍍鐵技術是一種常見的機械零部件修復技術,在維修受損的機械零部件和需要對一些特殊材料的表面預處理時發揮著至關重要的作用[2]。該技術目前主要應用于對受損發動機曲軸、凸輪軸、傳動軸、液壓支柱等重要零部件的修復過程中[3]。隨著科學技術的進步,傳統的鍍鐵層已經不能滿足現代工業的要求,許多研究人員通過在電鍍液中加入SiC、Al2O3、MoS等制備出性能優良的多元合金鍍層,使其具有優良的物化性能[4-6]。電鍍技術具有效率高、成本低、操作簡單、環境友好等優點,適用于復合鍍層的制備[7-8]。
近期研究成果表明,在鍍液中加入稀土元素改變鍍液的性質[9],可以制備出性能更為優越的復合鍍層。稀土元素的原子半徑較大、電子結構為特殊的4f層、電負性較低和化學性能更為活潑的優點,較少的添加量即可以達到顯著的改良效果,被譽為 “優異的多功能添加劑”[10]。而稀土氯化物CeCl3 因其具有獨特的氧化性和極強的吸附性能,可作為添加鹽應用于鍍層的強化中[11]。目前稀土添加劑主要應用于鍍鎳與鍍鉻的研究中,在鍍鐵中相關研究較少。由于Ce鹽可以較好的溶于鍍液中,對鍍液性能的影響較小,因此本文采用在鍍液中添加不同濃度CeCl3 (0、0.5、1、1.5g/L) 化合物對復合鍍層表面形貌與性能的影響,并對復合鍍層的耐磨性、耐腐蝕性能進行研究,為復合鍍鐵層的發展提供更多理論參考。
1 試驗材料與方法
基體材料為120mm×10mm×6mm的45# 鋼,主要化學組成(質量分數/%)為:C(碳)0.42%~0.50%, Si(硅)0.170%~0.37%,Mn(錳)0.50%~0.80%, Cr(鉻)≤0.25%,S(硫)≤0.035%,P(磷) ≤ 0.035 %,Ni(鎳)≤0.30%,Cu(銅)≤0.25%, Fe(鐵)余量[12]。所添加化合物為CeCl3·7H2O,濃度分別為0、0.5、1、1.5g/L。在電鍍試驗進行前,需對45# 鋼進行前處理,試樣表面依次使用金相砂紙進行打磨,經無水乙醇超聲清洗15min后放入烘干箱進行烘干,最后放入密封袋里以供使用。本次試驗使用的電鍍槽為50L的玻璃槽,電鍍液為自制鍍液,鍍液主要成分為FeCl2·4H2O[13],在電鍍前需將鍍液活化,并維持其pH值為1左右,溫度在20~35℃,電鍍過程分為5個階段:交流活化預處理、交流起鍍、不對稱交流、小直流電鍍、大直流電鍍。表1列出了在電鍍過程中5個階段的工藝參數。
表1 電鍍工藝參數
利用線切割機將電鍍后的試樣割成13mm× 3mm× 2mm的試樣。切割后的試樣經過200~800目的砂紙逐級打磨,直至表面光滑平整之后,使用馬爾文帕科Empyrean智能X射線衍射儀(XRD) 對鍍層進行物相分析,掃描速度為2(°)/min,衍射角范圍為0°~90°,加速電壓為40kV,管電流為30mA。將切割后的鍍層試樣進行鑲嵌,對界面打磨拋光后采用德國卡爾蔡司(ZEISS)的掃描電子顯微鏡(SEM)及EDS對試樣表面進行微觀形貌觀察,確定其元素分布。使用Cratos W50全自動顯微硬度測試儀對鍍層進行硬度測試,在鍍層表面選取三個點,載荷為1N,載荷時間持續10s每個試樣取三個點進行測試取平均值,使用Thermo Kalpha X射線電子能譜儀(XPS)對鍍層元素化合價態進行分析,使用自制往復式摩擦磨損試驗機測試復合鍍層的摩擦力、抗黏著情況及磨損質量損失。在進行摩擦磨損試驗前,使用200~800目砂紙對試樣進行逐級打磨,保證所有試驗試樣鍍層表面粗糙度為20 μm的平面。摩擦磨損試驗采用直徑為5mm、硬度為600HV以上的440C不銹鋼銷子作為摩擦副,在復合鍍層表面做線性往復運動。試驗機頻率為40Hz,在進行摩擦磨損試驗時載荷為10MPa,供油量為0.07mL/min,沖程為60mm,磨損時間為7h。采用電化學工作站測試復合鍍層的極化曲線和阻抗譜的測量。試驗試樣的工作面積為1cm2,工作環境為3.5%的NaCl溶液,參比電極為飽和氯化鉀電極,輔助電極為鉑電極,掃描速度為10mV/s。
2 結果與討論
2.1 鍍層的形貌分析
圖1 為不同濃度CeCl3 化合物所制備的復合鍍層的表面形貌。由圖1可見,采用電鍍技術制備的鍍層均呈現條紋結構。圖1a為未摻雜CeCl3 化合物的鍍層。由圖可以看出,未加入CeCl3 化合物的鍍層表面粗糙,存在裂痕,且鍍層表面有凹坑與凸起[14]。這是由于在電沉積的過程中,基體與鍍層間存在一定的滲氫現象,即氫氣在鍍層表面不斷沉積形成氫氣泡,造成金屬間晶格畸變,使鍍層中內應力增大,造成鍍層表面缺陷[15]。當鍍液中加入不同濃度的CeCl3 鹽后的表面形貌分別如圖1b~1d,可以看出,復合鍍層的微觀形貌有了一定程度的改變,鍍層表面裂紋、氣孔等缺陷減少,致密性得到大幅度提高。對比圖1b、 1c和1d可知,鍍液中CeCl3 鹽濃度為0.5g/L的鍍層表面結構致密,鐵晶粒呈規律狀緊密排列且晶粒間沒有明顯分界線。而繼續增加鍍液中CeCl3 化合物的濃度,鍍層表面的致密性有所下降,且鍍層表面出現凹坑、凸起和裂紋。圖1的結果表明,在鍍液中添加一定濃度的CeCl3 鹽可以明顯抑制電鍍過程中的滲氫現象,從而提高鍍層的表面質量。
圖1 不同CeCl3 濃度下鍍層的表面形貌
圖2 為在鍍液中添加不同濃度CeCl3 制備的鍍層的截面形貌。由圖2可以看出,鍍液中CeCl3 濃度為0g/L時,鍍層截面出現氣孔與裂痕,且與基體結合存在一定縫隙,結合強度較差,隨著鍍液中CeCl3 濃度在一定濃度范圍內逐漸提升,鍍層截面結構致密,且與基體結合較好,未出現明顯的分界線,且表面無明顯的裂痕及剝脫區域出現。分析認為,由于Ce3+ 具有特殊的4f電子結構,其在鍍液中可以在一定程度上抑制Fe2+ 的還原反應,提高陰極的電位,同時,Ce3+ 易吸附在鍍層表面的活性點處,Ce3+ 的原子半徑相對較大,可以抑制Fe晶體的形成和長大,起到細化晶粒的作用。而隨著CeCl3 的逐漸加入,鍍液中的Ce3+ 的含量逐漸提升,當其達到一定濃度以后,Ce離子抑制析氫的作用愈發明顯,H+ 較難形成H2 析出,反而與Fe離子共同沉積進入鍍層,使鍍層中內應力增加,進而導致鍍層表面形成裂痕、鍍層與基體的結合強度變差。綜合分析認為,在鍍液中添加0.5g/L的CeCl3 化合物可以起到抑制電鍍過程中的滲氫并阻止Fe晶體長大的作用,而當鍍液中CeCl3 濃度高于0.5g/L時,抑制滲氫現象過于明顯,鍍層的表面、截面形貌反而變差。
圖2 不同CeCl3 濃度下鍍層的截面形貌
2.2 鍍層的物相結構和成分分析
圖3 為不同CeCl3 濃度下鍍層的XRD圖譜。從圖中可以看出鍍層在2θ 為44.67°、65.00°、 82.17°附近出現三處特征衍射峰,鍍液中CeCl3 濃度為0g/L時鍍層最高峰峰值較低,主要延Fe(110)、(200)、(211) 三個方向生長,在鍍液中添加CeCl3 化合物后,鍍層中Fe元素在三個取向上的峰強發生明顯變化,各個衍射峰強度呈現出先提高后降低的趨勢,在鍍液中CeCl3 濃度為0.5g/L時,鍍層的峰值最高,而當鍍液中CeCl3 濃度達到1.5g/L時,鍍層的峰值有一定程度的下降,但仍優于普通鍍層。鍍層中Fe晶粒的平均粒徑可以采Debye-Scherrer方程[16-17]估算:
λ 可由Cu-k 1靶材的波長所得到,β 可以從XRD的最強峰的峰寬(FWHM)計算得到。隨著鍍液中CeCl3 濃度的逐漸提升,其鍍層的晶粒尺寸分別為87、19、51、51nm。CeCl3 的加入可以使鍍層的鐵晶粒發生明顯的細化。分析認為鍍液中CeCl3 作為表面活性元素,易吸附在鍍層晶體的活性點上如鍍層的“生長點”或“生長線”處,可以有效抑制鍍層中Fe晶粒的生長,起到超強的細化晶粒的作用,而鍍液中Ce3+ 的含量過高時,會抑制鍍液中Fe2+ 的沉積,且稀土離子之間的相互吸附會導致鍍層的分布不均,影響鍍層的質量,CeCl3 帶來的優勢反而不明顯。
圖3 不同CeCl3 濃度下鍍層的XRD圖譜
圖4 為鍍液中不同濃度CeCl3 化合物濃度制備的鍍層經過面掃描后的EDS圖譜。可以看出,所有能譜中出現了C、O、Fe元素,且在鍍液中加入適量濃度的CeCl3 化合物后,鍍層表面的能譜皆出現了Ce元素峰,且Fe元素峰有明顯的提高 (圖4b~4d)。這說明在基體表面成功制備出含有Ce元素的復合鍍層,且Ce元素在鍍層表面起到了明顯的改善作用。當鍍液中CeCl3 濃度為0.5g/L時,復合鍍層表面Ce元素峰最強,且Fe元素峰強度也最高,說明復合鍍層中的Ce元素起到了較好的改善作用。但當鍍液中的CeCl3 濃度繼續提高時,復合鍍層表面Ce元素峰與Fe元素峰皆有一定程度減小。
圖4 不同CeCl3 濃度下鍍層的EDS能譜
圖5 為本文根據XPS圖譜對含有CeCl3 的復合鍍層的化學成分及鍵合結構型作進一步分析的結果。可以看出,向鍍液中添加不同濃度的CeCl3 化合物,發現復合鍍層表面圖譜中已經出現了Ce元素特征峰。圖譜中不同濃度的Ce3d的XPS分譜如圖5所示,V和U對應自旋分裂軌道3d5/2和3d3/2 [18-19]。分譜可以分為兩組特征峰,分別對應Ce的 +3和 +4價態。在904.8eV和885.6eV出現的被標記為U' 和V' 的峰是Ce3+ 的特征峰,其他標記為U、U''、U''' 和V、V''、V''' 則對應Ce4+[14],這表明鍍液中的CeCl3 隨著沉積反應的進行在鍍層中形成CeO2 與Ce2O3 兩種化合物。Fe2p的分譜中可以分離出4個較為明顯的有效峰,它們的形成分別與Fe2+ (710.9eV為Fe2+2p3/2和723.6eV為Fe2+2p3/2)和Fe3+(716.3eV為Fe3+ 2p3/2和730.0eV為Fe3+2p1/2)有關。
圖5 不同CeCl3 濃度下鍍層的XPS圖譜
通過對比圖5a與圖5b,鍍液中CeCl3 濃度為0.5g/L時,Ce元素峰值強度更高,波形更為明顯,且Ce4+ 化合物含量更多。對比圖5c與圖5d可以看出,鍍液中未加入CeCl3 所制備的鍍層中Fe3+ 化合物含量更多,通過向鍍液中添加CeCl3,鍍層中的Fe3+ 化合物含量明顯減少。分析認為Ce元素處在元素周期表的第三副族,具有較大的電荷數,可以將鍍液中的Fe3+ 還原成Fe2+,阻止其與陰極區附近的OH- 結合形成Fe(OH)3 沉積在鍍層中,從而提高鍍層質量。
2.3 鍍層的顯微硬度
試驗測得未加入CeCl3 化合物的鍍層顯微硬度為517.8HV,由圖6鍍層的顯微硬度圖可以看出,鍍液中添加CeCl3 所制備的鍍層硬度,隨著鍍液中CeCl3 化合物濃度的增加呈現出先提高后降低的趨勢,其硬度處于530~600HV,與普通鍍層相比得到小幅度提高。當鍍液中CeCl3 化合物濃度為0.5g/L時,鍍層的平均顯微硬度最大,為611.4HV,相比于未加入CeCl3 的鍍層有接近18.05%的提高,有一定的提升效果。但當CeCl3 化合物濃度達到1g/L時,鍍層的質量變差,顯微硬度有所下降,但仍優于普通鍍層。
圖6 不同CeCl3 濃度下鍍層的顯微硬度
圖7 為鍍液電導率,隨著鍍液中CeCl3 化合物濃度的提升表現出先迅速提高后小幅度降低的趨勢。分析其原因,可能是Ce原子較為活潑,具有較強的活動性,當Ce原子內部電子軌道未被填滿時,對鍍液中游離的電子具有較強的吸附能力,可以起到導電的作用,從而提高鍍液的電導率、鍍層的沉積速率,在相同時間內鍍層厚度更大,且Ce原子在一定程度上可以抑制鍍層中鐵晶粒的生長,細化晶粒[20]。而鍍層邊界所聚集的Ce離子與其他元素形成稀土化合物,可以在鍍層的邊界起到黏結的作用,有效提高鍍層的強度與硬度。但鍍層中Ce離子的包覆能力有限,當鍍液中的Ce離子達到一定濃度后,鍍液中的電導率變化趨于平緩,鍍液中Fe離子的沉積速率基本穩定,鍍層中的Ce離子便不能有效抑制鍍層中鐵晶粒的生長,反而會使鍍層中鐵晶粒變粗,鍍層的硬度變小,鍍層的質量降低[21]。
圖7 不同CeCl3 濃度下鍍液的電導率
2.4 鍍層的耐磨性
表2 列示了鍍液中加入不同濃度CeCl3 化合物所制備的復合鍍層經過摩擦磨損后質量損失,通過激光共聚焦表征不同CeCl3 濃度的復合鍍層的磨痕及其三維形貌如圖8、9所示。
表2 摩擦磨損質量損失
圖8 不同CeCl3 濃度下鍍層磨痕的三維形貌
圖9 不同CeCl3 濃度下鍍層的磨痕形貌
由表2可以看出,鍍層進行7h摩擦磨損試驗后,鍍層的質量損失隨著鍍液中CeCl3 化合物濃度的提升呈現出先減小后增加的趨勢,當鍍液中CeCl3 化合物濃度為0.5g/L時,鍍層的磨損質量損失最小,為0.17g,鍍液中CeCl3 化合物濃度為1.5g/L時,復合鍍層的磨損質量損失增加到0.41g,但仍小于普通鍍鐵層。由圖9a可以看出,當鍍液中未添加CeCl3 化合物時,鍍層在磨損后出現燒蝕現象,磨損形式以黏著磨損為主。這是因為未加入CeCl3 的鍍層表面較為粗糙,局部鍍層在摩擦力的作用下發生塑性變形,表面的一些裂紋、凸起在摩擦磨損過程中會被剪切,從鍍層表面剝離,在鍍層與對磨件間發生黏著磨損,造成鍍層局部脫落,在長期切削應力的作用下,鍍層不足以承受外加載荷,最終因疲勞磨損而脫離基體。在摩擦磨損的過程中會產生熱量,鍍層在摩擦熱的作用下發生軟化,當溫度過高時,鍍層會發生燒蝕,使磨痕變黑。而鍍液中添加適量濃度的CeCl3 化合物后,鍍層表面局部脫落及塑性變形的現象減輕,鍍層的磨損形式由最開始的黏著磨損轉化為磨粒磨損。鍍層表面經7h摩擦磨損后未出現明顯的剝落,鍍層的耐磨性能得到明顯的提高。而當鍍液中CeCl3 為0.5g/L時,表面僅出現由磨粒磨損造成的輕微劃痕且劃痕最淺,如圖9b所示。
鍍液中的CeCl3 可以起到細化晶粒[22]的作用,且會使鍍層中鐵晶粒的排列更加規則,呈現擇優取向性,使得鍍層中鐵晶粒排列更為均勻致密,且因為Ce離子原子半徑較大,可以填補在鍍層中鐵晶粒的缺陷相,減少鍍層表面的缺陷及裂痕,提高鍍層的質量。而Archard定律表明,鍍層的摩擦磨損性能與其硬度成正比,鍍層表面硬度的提高對鍍層的耐磨性極為有利[23]。但隨著鍍液中CeCl3 濃度的繼續提升,Ce離子的存在反而會抑制鍍液中Fe離子的沉積,使鍍層中鐵晶粒分布不均勻,鍍層內應力集中,鍍層易產生裂痕剝落,磨削現象更加嚴重,鍍層的耐磨性也會隨之降低。
2.5 鍍層的耐腐蝕性能
圖10 為經過電鍍所制備的試樣在3.5%NaCl溶液中的Tafel極化曲線,利用Tafel外推法可以計算電化學腐蝕相關特征參數如表3所示。由圖10和表3可以清晰地看出,鍍液中添加CeCl3 化合物后,鍍層的腐蝕電位正移,腐蝕電流密度降低,鍍層的耐腐蝕性能得到提高;并且隨著鍍液中CeCl3 化合物濃度的逐漸增加,鍍層的抗腐蝕性能呈現先提高后降低的趨勢,鍍液中CeCl3 化合物濃度為0.5g/L時鍍層的耐腐性能達到最佳,腐蝕電位從-1.027V提高至-0.780V,腐蝕電流密度由116降低到73.86 μA·cm-2。當鍍液中CeCl3 濃度增加到1g/L時,鍍層的表面質量下降,開始出現凹坑與裂痕,腐蝕電流密度增大,但仍優于未添加CeCl3 化合物的鍍層。因此,鍍液中添加CeCl3 化合物所制備的復合鍍層擁有更加優越的耐腐蝕性能[24]。
圖10 不同CeCl3 濃度下鍍層的極化曲線
表3 極化曲線參數值
進一步地,采用電化學阻抗譜(EIS)法對不同濃度樣品鍍層的腐蝕電化學性質進行了比較。圖11是不同濃度樣品鍍層的Nyquist阻抗譜圖(Nyquist Plot),Zre為阻抗值的實部,Zim為阻抗值的虛部,所有Nyquist曲線存在高頻下的半圓,而半圓的直徑即表示電荷轉移電阻(R p),從 R p的大小能夠得出樣品耐腐蝕性的強弱。基本的規律是:R p越大,即圓弧的直徑越大,則樣品的耐腐蝕性越好。為了更加具體地比較不同濃度樣品鍍層的耐腐蝕性能,進一步用Z-view軟件對Nyquist圖進行擬合,可以得到確切的阻抗數值,采用的等效電路模型如圖11插圖所示,其中,R s 和 R p分別代表溶液阻抗和電荷轉移阻抗,CPE代表常相位角元件[25]。表4列出了根據擬合結果計算得到的各個元件的參數值。
圖11 不同CeCl3 濃度下鍍層的交流阻抗譜
表4 等效電路參數值
結果表明,鍍液中CeCl3 濃度為0g/L所制備的鍍層具有最小的 R p,只有565.0 ,表明不添加CeCl3 化合物時,鍍層的防腐蝕性能不理想。 0.5g/L的樣品具有最大的 R p,高達942.3 ,表明在這個添加濃度下,復合鍍層的內阻較大,電荷傳遞過程容易受阻,不容易發生腐蝕反應,即添加了CeCl3 化合物后,鍍層的防腐蝕性能顯著提高了。隨著CeCl3 含量的進一步升高,復合鍍層的 R p 值逐漸降低,在1.5g/L的樣品中,復合鍍層具有較小的 R p,為663.2 。
綜合結果表明:本試驗采用0.5g/L的CeCl3 添加進入鍍層后,可以顯著提高鍍層的耐腐蝕性能,這主要是因為CeCl3 的添加使得鍍層的表面缺陷位置減少,鍍層中鐵晶粒的排列更加規則,鍍層表面更加致密,在3.5%NaCl溶液中暴露腐蝕區域較少;鍍液中Ce離子可以有效抑制鍍液中H+ 與Fe3+ 的沉積,因此可以有效抑制在電鍍過程中的滲氫反應,阻止Fe(OH)3 夾雜在鍍層中[26];夾雜在鍍層中的Ce離子可以使鍍層具有更好的擇優取向性能,鍍層內部的電位差減小,使得鍍層的腐蝕阻力有所增大,因此鍍層的電化學腐蝕傾向降低。但是,當鍍液中CeCl3 濃度超過0.5g/L的時候,較高濃度的CeCl3 可能會形成膠狀的氫氧化物而沉淀,破壞了金屬離子的有序沉積,鍍層的缺陷位置暴露出來,因此耐腐蝕性能反而降低了。
3 結論
(1)鍍液中的CeCl3 可以起到細化晶粒的作用,使鍍層的顯微硬度大幅度提升。當鍍液中CeCl3 化合物濃度為0.5g/L時,復合鍍層的顯微硬度最大,為611.4HV。
(2)復合鍍層經過7h的摩擦磨損后的磨痕寬度、深度隨著鍍液中CeCl3 化合物濃度的增加呈現出先降低后升高的規律。鍍液中未添加CeCl3 化合物所制備的鍍層發生較為嚴重的黏著磨損,添加適量的CeCl3 化合物后,鍍層的耐磨性得到大幅提升,鍍液中CeCl3 化合物濃度為0.5g/L時,復合鍍層的耐磨性最佳。
(3)與單純鍍鐵層相比,添加適量濃度CeCl3 化合物的復合鍍層腐蝕電位更高,腐蝕電流密度較低,電荷轉移電阻更大,復合鍍層具有更好的耐腐蝕性能。當鍍液中CeCl3 化合物濃度為0.5g/L時,復合鍍層的耐腐蝕性能最佳。稀土組分的引入為電鍍技術提供了新思路。
參考文獻: 略
免責聲明:本網站所轉載的文字、圖片與視頻資料版權歸原創作者所有,如果涉及侵權,請第一時間聯系本網刪除。
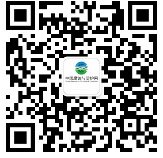
官方微信
《腐蝕與防護網電子期刊》征訂啟事
- 投稿聯系:編輯部
- 電話:010-62316606-806
- 郵箱:fsfhzy666@163.com
- 腐蝕與防護網官方QQ群:140808414