摘要
從大氣腐蝕加速試驗方法、大氣腐蝕電化學方法及大氣腐蝕監檢測技術對大氣腐蝕試驗方法進行了綜述。大氣腐蝕加速試驗中,多因子循環復合腐蝕試驗已經成為模擬大氣腐蝕加速試驗的主要發展方向;同時,隨著電化學方法空間分辨率的提升,大氣腐蝕電化學方法也從宏觀電化學技術向微區電化學技術延伸;另外,隨著物聯網及計算機技術的發展,基于數據挖掘及機器學習等現代化的數據處理技術也在大氣腐蝕監檢測技術中得到了應用。
關鍵詞: 加速腐蝕試驗 ; 電化學方法 ; 監測技術 ; 大數據
統計[1]表明,由材料大氣腐蝕造成的經濟損失占各類環境腐蝕總和的一半以上,材料大氣腐蝕造成了重大的經濟損失。例如,大氣環境中服役的鋼結構的塔架、橋梁、大型儲罐、車間、工程設備等設施,在長期的服役過程中會遭受不同程度的腐蝕破壞,銹蝕后的鋼結構力學性能降低,嚴重威脅建筑或工程設備的安全運行。盡管大多數鋼結構表面做了有效的防護處理 (如表面鍍鋅),但在多種環境因子的多重作用下,表面依舊會發生化學腐蝕和電化學腐蝕。工業城市中大氣含有的Cl-、SO2、NO2等腐蝕介質濃度較高,對鋼結構的腐蝕更為嚴重[2]。因此,需要人們發展大氣腐蝕試驗方法與評價技術,探討環境因素對材料大氣腐蝕的機理及規律,并根據腐蝕機理及規律來發展先進的監檢測方式評估材料的腐蝕狀態,減少由于未能及時發現腐蝕損傷而導致的安全事故。同時,這也是發展高品質耐大氣腐蝕新材料的基礎。
美國試驗與材料學會 (ASTM) 自20世紀初便開始大氣腐蝕的研究,首先建立大氣腐蝕試驗站。Larrabee等[3,4]先后進行大氣腐蝕數據積累工作,總結、探討材料腐蝕規律。我國于20世紀50年代開始建立大氣、海水、土壤腐蝕試驗網站,到1980年全面展開常用材料在大氣、海水、土壤環境中長期、系統的腐蝕研究,并取得了大量有價值的研究成果。
傳統的大氣腐蝕試驗方法與評價技術通過曝曬樣品來評價材料的大氣腐蝕性。目前已經發展了多種曝曬方式,用于評估不同材料 (鋼材、高分子材料、混凝土材料、涂料等) 在大氣中的腐蝕情況,如高分子材料大氣環境腐蝕試驗、建筑涂料大氣環境腐蝕試驗等。但由于自然環境下的曝曬試驗周期長、速度慢,嚴重制約了耐蝕新材料的研發速度。因此,微區電化學理論、測試技術、大數據和物聯網技術的快速發展,給腐蝕試驗與評價技術提供了新的動力和基礎,材料大氣腐蝕試驗與評價技術也取得了長足的進步。在大量的研究基礎上發展了基于微區電化學和大數據的多種室內大氣腐蝕加速試驗方法、電化學研究方法、大氣腐蝕監測技術等,加深了對材料在大氣環境下的腐蝕機理與規律的認識,提升了基于室內外相關性的材料大氣腐蝕性的快速評價技術水平。本文對近20年來國內外的材料大氣腐蝕試驗與評價技術的最新進展進行了綜述,比較了這些試驗與評價技術的優劣,指出材料大氣腐蝕大數據監測與評價技術,可以獲得以前片段化數據無法得到的腐蝕機理與規律研究結果,將成為高品質耐蝕新材料開發和設備腐蝕壽命精確評定的最重要基礎。
1 大氣腐蝕加速試驗方法
在自然環境下將材料直接曝露于大氣環境中是研究大氣腐蝕試驗最常用的方法,所得到的數據結果接近于實際使用情況下的數據結果[5,6]。但試樣在傳遞過程中會出現損壞、試驗結果存在累積誤差、數據離散,無法滿足新鋼種的研發和材料壽命的預測與評估。其次隨著材料的種類越來越多,如耐候性的鋼材、耐蝕性的鋼材、耐候性的高分子材料、超疏水性能的涂層等,直接將材料置于大氣環境下曝曬,試驗周期長、成本高。因此,越來越多的人開始關注在短時間內就可得到結果的加速腐蝕試驗,通過實驗室內的短期加速腐蝕試驗結果來推測戶外長期曝曬的試驗結果,進而推測材料的大氣腐蝕壽命。目前常用的室內模擬加速試驗方法有鹽霧試驗、濕熱試驗、電解加速腐蝕試驗、干濕周浸循環試驗、多因子循環復合腐蝕試驗等。
鹽霧試驗方法是用于評價金屬材料的耐蝕性及涂/鍍層對金屬的保護程度的加速試驗方法。1962年ASTM制定的中性鹽霧試驗 (NSS)、醋酸鹽霧試驗 (ASS)、醋酸氯化銅鹽霧試驗 (CASS) 3種標準上增加了交變鹽霧試驗,這是一種綜合鹽霧試驗,在中性鹽霧試驗的基礎上增加恒定濕熱試驗,主要用于試驗空腔型的整機產品。但大量研究表明,鹽霧試驗只能作為一種人工加速試驗方法,不能預測材料在實際環境下的使用壽命。其次,單一的鹽霧試驗不能模擬真實環境下試樣表面液膜隨氣象的變化出現變薄、變厚、消失的循環過程,因此出現了CASSER-ISO-ZFCY型周期噴霧試驗機,在干/濕交替的循環輔助系統上,增加了可通入工業氣體、鹽水浸漬、低溫等系統。較好的模擬了Zn在典型地區的大氣腐蝕行為,且可針對Zn在典型地區的大氣腐蝕行為進行一定程度的預測[7]。
濕熱試驗通過控制溫度和濕度兩個影響因子來加速材料腐蝕,分為恒定濕熱試驗和交變濕熱試驗。恒定濕熱試驗用于檢測材料在各種環境下設備及各種材料的耐熱、耐寒、耐干、耐濕性能,交變濕熱試驗用于電子電器零組件、自動化零部件通訊組件、汽車配件、金屬、化學材料、塑膠等行業。濕熱試驗過程中在材料表面覆蓋一層疏松、多孔、透氣性好的鏡頭紙,使材料表面形成均勻、有一定厚度和易于控制重現的水膜[8],并有規律地通入SO2氣體進行化工氣體試驗,8 h加熱和通入SO2,16 h停止加熱或不通SO2交替循環進行,可有效地模擬工業大氣環境。
電解加速腐蝕試驗 (EC) 最早用于研究金屬涂層的耐腐蝕性,是在CASS試驗原理發展來的。GB 6466-86規定了將電解加速試驗方法作為快速而準確地評價鋼或鋅合金鑄件上銅-鎳-鉻電沉積戶外耐腐蝕性方法。EC試驗與CASS相比,具有時間短、方法簡單、結果與真實值接近的特點。現在電解加速腐蝕試驗朝著特殊腐蝕環境、特殊材料腐蝕機理等方向發展,如研究高壓直流柱絕緣子金屬部件在污穢條件下的腐蝕機理和影響因素[9]、錨桿在不同溫度及污染物濃度下的腐蝕特性等[10]。
干濕周浸循環試驗用來研究大氣腐蝕時試樣表面干濕交替變化的過程[11]、模擬加速腐蝕試驗、應力腐蝕研究、其它非標試驗等。研究結果表明,周期浸潤試驗幾個星期的結果與自然環境下暴露一年或是更長時間的結果相當。1980年制成的DUV-VD-3型浸漬腐蝕試驗機具有浸漬-濕潤-干燥或者浸漬-干燥-濕潤兩種試驗循環順序,適用于金屬材料及電鍍、涂漆、防銹油等表面處理后的耐蝕性試驗。按照ASTM G44和HB 5194要求研制的采用微機控制的干濕循環加速腐蝕試驗機可自動控制試驗條件、自動采集和記錄數據,并實現溶液的自動補給。利用該試驗機對低碳鋼的銹蝕規律進行探究,得出沿海大氣環境下得到的大氣腐蝕速率方程可以預測材料長周期的大氣腐蝕行為,預測結果與實際結果一致[12]。采用干/濕交替的試驗方法模擬O3/SO2復合大氣環境中鋼的腐蝕演化特性,發現O3和SO2的交互作用對鋼的腐蝕有明顯的抑制作用[13]。
將周期噴霧試驗與周期浸潤試驗相結合出現了多因子循環復合試驗。ACCE試驗機可調控八種環境因子對材料的加速腐蝕影響,實現了降雨、凝露、噴霧、濕度、溫度、光照、風速和通入腐蝕性氣體 (SO2) 等環境因子的控制,還可以模擬多種氣象條件下的大氣腐蝕,獲得與真實數據相近的結果[14]。Q-FOG循環腐蝕試驗箱具有更優越的霧分散功能,可獨立改變沉降量和距離,能夠快速地改變溫度,達到快速循環。針對涂層、油漆、塑料、建筑材料等制造的QUV加速耐候試驗機通過控制陽光、濕氣的交互循環可再現陽光、雨水、露水、溫度對材料產生的破壞,試驗機內幾天或幾周的時間可達到戶外數月或數年產生的破壞。
在進行加速腐蝕試驗時,需要考慮試樣在大氣中腐蝕的本質規律,而不是簡單的模擬大氣腐蝕現象。大氣環境繁多且復雜多變,使用單一的環境模擬加速試驗來模擬世界各國不同的大氣環境,其結果與真實結果不吻合。因此,大多采用復合型的加速腐蝕試驗方法來模擬加速試驗。
2 大氣腐蝕微區電化學方法
金屬的大氣腐蝕過程與完全浸在電解液中的腐蝕過程有所不同。大氣腐蝕的介質是微量電解質溶液,傳統的電化學測量方法 (如:極化、阻抗、電化學噪聲測量等) 無法精確的對這種微量電解質體系進行測量。在薄液膜下,溶液的歐姆降很大,電流在工作電極表面分布不均勻,參比電極里微量的離子 (Cl-) 污染,這就給薄液膜的微量體系帶來干擾,使得測量誤差較大。但探討大氣腐蝕的機理時,電化學測量技術必不可少,因此,人們做了大量的研究后,發展了微區電化學技術,如掃描開Kelvin探針測量技術、微區電化學阻抗技術、掃描振動參比電極技術、掃描電化學顯微鏡技術、微液滴下的微區電化學技術等。
2.1 掃描Kelvin探針測量技術 (SKP)
Kelvin首次提出Kelvin方法[15],并測出金屬間的金屬電勢差。Zisman[16]采用振動電容平板的方法對其進行改進后衍生出SKP技術。Stratmann[17]首次將SKP技術應用于測量Mg、Al、Fe、Cu、Ni和Ag等6種純金屬在薄液膜下的開路電位與表面電勢分布曲線之間存在的線性關系。后來將SKP技術用于檢測金屬在大氣環境下的腐蝕規律、金屬表面腐蝕產物的形成及對腐蝕的影響、金屬表面帶缺陷的有機涂層的脫附現象,還用于檢測極薄液層下金屬的腐蝕電位的分布來確定金屬的腐蝕部位及腐蝕程度[18-21]。
掃描Kelvin探針顯微鏡技術 (SKPFM) 首次應用于材料腐蝕研究[22,23]。在研究了Al 2024中金屬間化合物的局部相對活性之后,SKPFM技術便廣泛用于研究金屬材料的局部電偶腐蝕行為或原位檢測金屬在潮濕大氣環境中局部微區的自腐蝕電位。使用SKPFM技術研究了退火溫度對2507雙相不銹鋼中奧氏體或奧氏體與鐵素體晶界捕捉氫的影響[24]、雙相不銹鋼晶間的貧化效應對腐蝕的影響[25]、鉻氮化合物對雙相不銹鋼腐蝕行為的影響[26]以及氧化夾雜物對不銹鋼的局部腐蝕行為的影響[27]。但SKPFM技術的分辨率受多種因素的影響,如探針幾何尺寸、實驗環境、樣品微觀形貌和探針針尖與樣品之間的距離等。因此,SKPFM技術只能作為一種半定量技術,若要確認特定體系下的局部腐蝕,往往需要結合SEM、TEM、EC-AFM等成像技術[28,29]。
2.2 微區電化學阻抗技術 (LEIS)
LEIS技術通過測定兩電極之間的電壓后,由歐姆定律得到局部交流電流密度 (ILocal),然后測量金屬表面上的局部阻抗[30]:

式中,k為電解溶液的導電率;d為兩個Pt電極之間的距離;Vapplied為施加的微擾電壓。公式 (1) 和公式 (2) 可以得到局部阻抗值ZLocal。
由于金屬點蝕常發生在微小的區域,EIS只能得出金屬整體的阻抗信息,很難區分鈍化區和活化區的阻抗譜,無法解釋點蝕的機理和動力學。將LEIS技術應用于腐蝕研究領域,不僅可以研究材料表面在微小區域內阻抗的變化情況,并描述和圖形化樣品上應力的分布情況[31,32],還可用于檢測涂層的完整性、均勻性、涂層下金屬的局部腐蝕和金屬的鈍化等對金屬腐蝕產生的影響[33]。
2.3 掃描振動參比電極技術 (SVET)
由于多種環境因素的影響,在金屬-電解質溶液界面,陽極和陰極區表現出不同的特性。常規的電化學方法無法深入研究腐蝕行為和機理,掃描振動參比電極技術 (SVET) 正好彌補這方面的不足。SVET技術可以在探針不接觸樣品表面的情況下,測量局部電流、電位隨遠離被測電極表面位置的變化以及樣品在溶液中的局部腐蝕電位。20世紀70年代Issacs等[34]將該技術引入腐蝕研究中,利用振動電極、轉變測量信號以及鎖相放大器,消除微區掃描過程中的噪聲干擾,從而有效地提高測量精度和靈敏度。
SVET技術由于具有較好的空間分辨率,可觀察材料表面發生氧化反應及還原反應的區域,并檢測到點蝕坑周圍和上方的電流波動,被廣泛用于研究金屬的點蝕、表面涂層對基體的保護作用、有機涂層缺陷或破壞、改性涂層的腐蝕性能以及緩蝕劑對材料腐蝕的緩釋性能等。在使用SVET技術研究涂層中所含物質對點蝕的發展過程的影響中,已檢測出涂層中的Mg可以阻止點蝕的形核和抑制已有點蝕的發展[35];而在檢測緩蝕劑對材料的緩釋性能時,SVET技術檢測出緩蝕劑在酸性和中性條件下都能起到較好的緩蝕效果[36]。
2.4 掃描電化學顯微鏡技術 (SECM)
掃描電化學顯微鏡技術 (SECM)[37]可以在溶液體系中對研究系統進行實時、現場、三維空間觀測,有獨特的化學靈敏性,其使用范圍從測量探頭與基體之間的異相反應動力學過程及本體溶液中的均相反應動力學過程到研究腐蝕與晶體溶解等復雜過程。
已有研究者使用SECM技術研究金屬表面點蝕的萌生過程、金屬離子對局部腐蝕的影響、第二相粒子與腐蝕的關系以及涂層與涂層下金屬腐蝕行為的研究[38]。在研究點蝕萌生過程中,得到點蝕的早期過程包括成核階段、亞穩態階段和穩態階段,且在亞穩態階段時掃描到pA級的鈍化電流密度,并與石英晶體微天平技術或其它電化學技術聯合使用研究單個腐蝕點在不同溶液中的擴展和腐蝕情況[39,40]。金屬腐蝕的過程中,離子對腐蝕的影響較嚴重,SECM技術可以測試離子流量、離子濃度與腐蝕電流及電位的關系,并成功檢測到離子是來自溶液還是電極表面。而當金屬內部或表面鈍化膜內存在第二相粒子時,表面活性會隨著第二相粒子的溶解而降低,SECM技術與AFM技術相結合得到了局部腐蝕行為與金屬間化合物粒子之間的關系[38]。掃描電化學顯微鏡技術也用于研究表面涂層的腐蝕性能以及涂層/金屬界面的腐蝕,以及通過阻抗的變化反映涂層是否存在缺陷、缺陷的尺寸以及涂層與基體之間大多由于局部破壞或極小的缺陷導致的失效[41]。
2.5 微液滴下的微區電化學技術
當金屬材料表面由于不均勻而存在各種缺陷,或表面上沉積有可溶性固體顆粒,則水蒸氣優先在金屬表面上的這些活性部位發生凝聚或吸附,進而長大形成液滴,液滴的存在加速了金屬大氣腐蝕的過程[42-45]。王佳等[46]觀察到了一種新的試驗現象—微液滴現象,并探究了影響微液滴形成和擴展的因素。研究表明,在一定濕度下,溫度越高,氣相中水分子密度越大,越有利于水蒸氣的吸附和凝聚,微液滴也更容易形成和擴展;其次,主液滴濃度和表面粗糙度都會影響微液滴的擴展[47]。同時使用掃描Kelvin探針和電化學極化等方法研究了微液滴現象與大氣腐蝕電化學過程之間的相關性,證明了微液滴的形核速率隨極化電流的增加而線性加速,促使大氣腐蝕過程發生的電位差和相應的腐蝕電流是微液滴形成和發展的推動力[48,49]。尤其是在干濕交替的大氣環境下,微液滴的擴展與腐蝕電流之間相互影響及相互促進[50]。
當材料發生點蝕、應力腐蝕開裂等局部腐蝕時,常規的探測整個樣品的宏觀變化就會忽略局部腐蝕對材料產生的影響,需要使用微區電化學技術 (SKP、LEIS、SVET、SECM等) 區分材料在不同區域的電化學特性差異,同時結合TEM、SEM、AFM、XRD等測試技術來進一步的探究材料腐蝕機理。
3 大氣腐蝕大數據評價方法
3.1 石英晶體微天平技術
材料的質量會由于腐蝕作用而發生變化,在此理論基礎上用質量增重法和質量減少法來評定材料腐蝕速度和耐蝕性。但質量增重法得到的數據具有間接性,而質量減少法得到的腐蝕速度通常表示試驗周期內全面腐蝕的平均腐蝕速度,這就限制了質量增重法和質量減少法的應用范圍。材料隨時間變化的腐蝕過程未必是線性的,短期的腐蝕情況不一定能預測長期的腐蝕情況。因此,在研究大氣腐蝕時,不僅要考慮大氣腐蝕的宏觀行為,還要考慮微觀信息。
石英晶體微天平 (QCM) 技術具有靈敏度高、精度高 (10-9 g) 的特點。1959年德國科學家Sauerbery將晶體材料質量與密度結合,建立了共振頻率與小質量增量 (?M) 之間的線性關系Sauerbery方程 (3)[51]:

式中,f0表示諧振頻率變化,E表示剛度 (Young's模量),ρ表示密度,A表示材料表面積。Sauerbery方程根據獲得的總頻率變化來估計吸附體的總質量,或者建立頻率變化 (信號) 與質量之間的直接關系[52]。
由于QCM不能對腐蝕產物進行定量分析,90年代中期,Aastrup和Leygraf[53,54]將其與可分析金屬表面化學成分的紅外光譜儀結合研究了金屬大氣腐蝕的原位動態變化,定性地檢測微量組分的組成,利用紅外光譜峰強度的變化對金屬大氣腐蝕產物的組成進行定量或半定量分析[55];進一步與原子力顯微鏡結合從微觀信息 (成鍵特征、電荷轉移、溶劑化等) 與宏觀信息 (化學組成、形貌變化、質量變化) 兩方面來探索和研究金屬的大氣腐蝕機理[56,57]。而Itoh等[58]將QCM和紅外光譜有機組合得出金屬銅在高濕度的腐蝕氣體環境下表面的腐蝕層生長呈現出拋物線的趨勢。這些研究都是從多角度原位監測材料在大氣環境下的腐蝕,改變了傳統質量法不能實時反映金屬的腐蝕行為以及數據不連續、不能監測短時間內材料腐蝕變化的缺點。
3.2 探針監測技術
常用的探針監測技術有電阻探針、電位探針、電偶探針、電流探針、線性極化探針、電化學阻抗探針、氫探針等。
電阻探針技術首先由Dravnieks和Freedman[59,60]提出并改進,主要測量由于腐蝕導致的材料厚度變化。這種技術可以在不破壞監測系統的情況下獲得腐蝕速率信息以及電阻比。金屬或合金的電阻由公式 (4) 得到:

式中,ρ為金屬樣片導電率,R為金屬試樣電阻,A為金屬試樣通電截面積,l為金屬樣片長度。由腐蝕造成的試樣橫截面的減少反映為電阻成比例的增加。因此,電阻探針可以通過確定在規定時間間隔內的累積腐蝕減少量來得到腐蝕速率的信息。然而,電阻探針的靈敏度由材料的厚度決定,其次,不能實時監測局部腐蝕和瞬態腐蝕,因此,需要綜合考慮探針的靈敏度和使用壽命來決定材料的厚度,同時對傳感器進行測試檢查,以驗證結果并確定腐蝕的形式[61]。目前,主要使用電阻探針去研究各種環境因素對材料腐蝕性能的影響,并證明了電阻探針不受材料所處環境和介質的影響。如利用電阻探針監測不銹鋼在鹽酸液膜環境中的鈍化與點蝕[62]、含磷無氧銅在含菌和無菌的缺氧水環境中的腐蝕行為[63]、Q235鋼在大氣環境下的實時腐蝕狀態[64]以及AISI304不銹鋼在高孔隙砂漿試件中的腐蝕情況[65]等。
在電偶探針監測原理[66]的基礎上制備成了大氣腐蝕監測儀 (ACM)。1976年,Mansfeld等[67]首次利用ACM研究了薄液膜下的電化學腐蝕過程。20世紀80年代,已將ACM技術用于研究碳鋼在不同濕度、污染物及不同鹽類濃度環境下的腐蝕動力學,并間接性證明了材料在大量電解液中測得的腐蝕電流與真實大氣環境下的腐蝕電流存在差異[68]。為使ACM在實際應用中有更大的價值,李曉剛團隊利用ACM儀得到環境影響因素對腐蝕影響的大小排序:降雨>相對濕度>溫度,而當大氣污染物濃度較低時,污染物不構成材料腐蝕的主要影響因素[69]。利用ACM技術得到數據實時性的特點,將所得數據與銹層的生長、動態環境因素、先進的數據處理方法和建模方法相結合,可預測材料的大氣腐蝕動態過程以及環境對實時電流的影響規律。現在,ACM也已經能夠快速、量化、準確的評估耐蝕鋼、耐候鋼等材料的耐蝕差異[70]。
基于電化學阻抗探針技術原理[71]將其應用于監測材料表面薄液膜下的干濕交替加速試驗的電化學行為及材料的腐蝕速率,并根據高頻阻抗表征材料表面的濕潤時間。探究如何將交流阻抗應用于大氣腐蝕監測的研究中,通過監測不同濕度下薄液膜的電阻變化來反映材料的腐蝕程度,用電化學阻抗得出的極化電阻的倒數來評估腐蝕速率的變化。已有實驗采用電化學阻抗探針監測出大氣環境下由于干濕交替影響了電解液中的離子濃度和氧的擴散速度,從而影響材料的腐蝕速率[71]。
3.3 無損檢測技術
常用檢測材料腐蝕的無損檢測方法有超聲檢測、渦流檢測、聲發射檢測、滲透檢測、射線照相檢測技術等。其中脈沖回波法是應用最廣泛的方法。發射電路通過一定高壓和頻率產生窄脈沖加載在超聲換能器探頭上,利用逆壓電效應使傳感器發出超聲波,中間利用耦合劑來測試被測材料,超聲波穿過被測材料,從另一側表面反射回來,反射回的信號被探頭接收,利用正壓電效應轉化成電信號,完成數據采集。材料厚度可由公式 (5) 計算得出:

式中,L為管道厚度,v0為超聲波信號傳輸速度,(t-t0)為信號射出時間與反射信號傳播時間的差值。在使用超聲波檢測管道厚度時,由于管道內壁的局部腐蝕,為使測量數據準確以及避免超聲波在空氣中的快速衰減,檢測時通常使用水或油等傳播介質[72]。
3.4 大數據監測技術
大數據監測技術是在探針監測 (如電偶探針、電流探針、電阻探針、電位探針、阻抗探針等) 技術基礎上,通過連續的在線監測,實現對材料腐蝕過程或環境腐蝕性實時觀測的一種方法。大數據監測技術得到的數據具有數據量越大,可靠性越高的特點。
通過對材料腐蝕大數據進行挖掘與建模分析來研究材料的腐蝕規律、腐蝕機理、腐蝕預測等關鍵問題。以往的腐蝕性試驗中常用的數據處理方法為統計分析方法、曲線擬合法、主因子分析和相關分析方法等。這些方法更多的是關注數據之間的相關性,忽略了環境因素與試驗結果之間的因果關系,而且數據碎片化較嚴重,只能反映一個周期中的大致趨勢,對于環境中影響金屬腐蝕的各種因素缺少分析,且每次需要長時間才能完成。現在主要利用不斷發展的新型數學分析與計算工具來實現大數據的處理,如最基本的數據統計分析與加工。當前應用于腐蝕中的數據挖掘技術有貝葉斯網絡、灰色關聯分析、隨機森林、灰色預測、多元線性回歸、人工神經網絡 (ANN)、支持向量機 (SVM)、支持向量回歸 (SVR)、馬爾科夫鏈等。不同的數據處理方法其功能各不相同,需要根據不同的腐蝕數據類型或預測目標選擇不同的數據挖掘方法。目前大部分腐蝕預測的模擬仿真研究主要是預測材料腐蝕速率和材料腐蝕壽命。當前應用于腐蝕中的數據挖掘手段如表1所示,它們使用的腐蝕數據范圍如圖1所示。
表1 應用于腐蝕研究的數據挖掘方法介紹
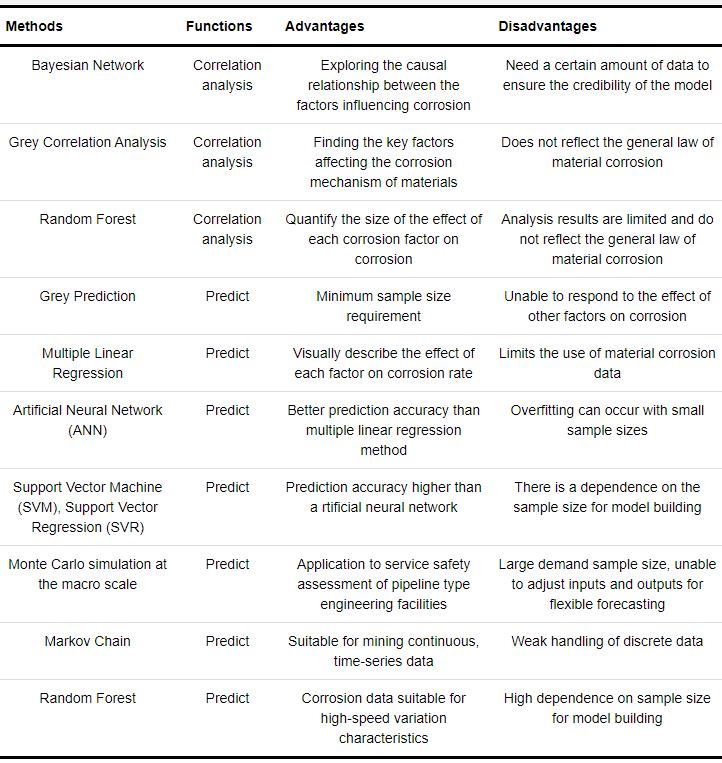
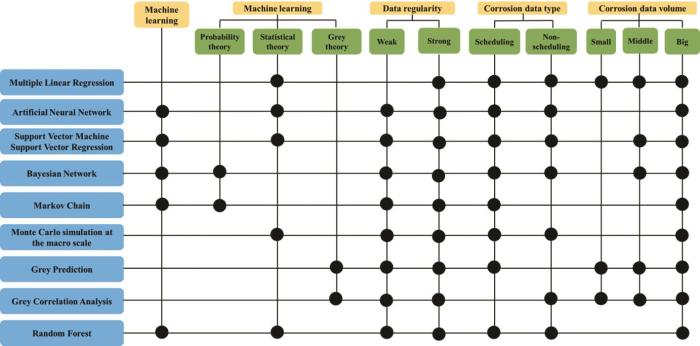
圖1 主要數據挖掘方法在腐蝕數據中的應用范圍
21世紀初,已有研究者將人工神經網絡 (ANN) 用于研究材料的大氣腐蝕,例如,研究碳鋼的腐蝕速率與Cl-、相對濕度、溫度、硫酸鹽沉積速率之間的相關性[73-76],并預測裂紋的擴展速率[77,78]和金屬的腐蝕起始時間[79]。Wei等[80]利用數據降維處理和人工神經網絡模型建立了低合金鋼腐蝕電位與其影響因素的關系模型,通過Pearson相關分析篩選出關鍵合金元素對低合金鋼腐蝕電位的影響以及評估低合金鋼腐蝕速率的計算公式 (6):

使用K-means對材料進行腐蝕等級劃分后,使用支持向量機 (SVM) 對兩極腐蝕電位之間的界面進行提取和可視化處理,界面方程計算公式如 (7),式 (7) 中每個i、f分別代表x、y軸,n、Wi、fi、b和γ是SVM的參數。ANN在樣本量較大時得到的數據結果較準確,但當數據樣本小時,采用預測結果較好的支持向量回歸 (SVR) 來預測材料的腐蝕[81]。還有研究者采用SVR與GA (遺傳算法) 混合模型來預測鋼或鋅的大氣腐蝕情況時,得出結論混合模型提供了更好的預測能力[82,83]。
隨機森林 (RF) 模型結構比一般的機器學習模型結構層次深,對高變化性的數據具有較好的處理能力[84,85]。在用RF模型預測不同材料在不同的環境下長時間的腐蝕速率時,發現環境因素中雨水pH值對腐蝕速率影響最大[86];對監測結果進行訓練后并與ANN和SVR模型相比,RF模型的預測能力明顯最強[70]。基于RF模型與分類和回歸樹 (CART) 模型,Zhi等[87]提出了DCCF-WKNNs的深層結構模型,其模型結構如圖2所示,對該模型的精度進行驗證后,DCCF-WKNNs模型具有最佳的泛化性能。DCCF-WKNNs模型作為一種有力的工具為低合金鋼大氣腐蝕的建模和知識挖掘提供了的幫助。
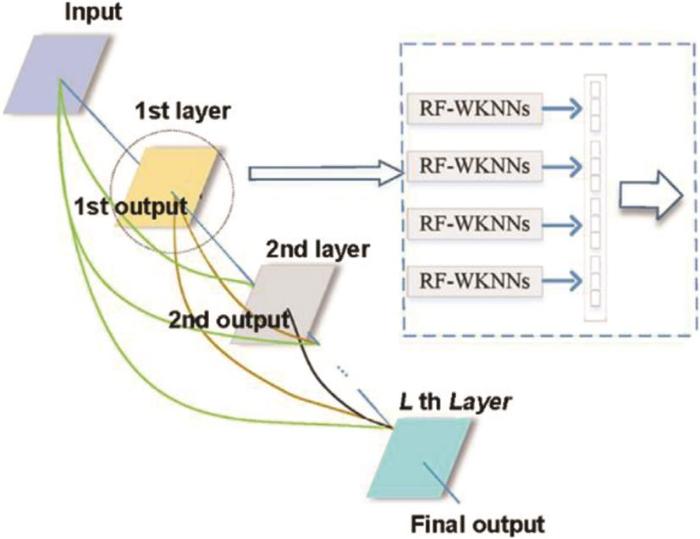
圖2 CCF-WKNNs模型結構[88]
大數據處理方法還可用來研究高分子材料的老化機理和預測高分子材料的壽命。Gao等[88]利用路徑分析、k-means聚類和多元線性回歸方法描述了丙烯酸聚氨酯涂料表面老化與環境因素之間的關系,并預測了涂料在未測試區域的表觀老化行為。在ANN基礎上發展的BP-ANN (back propagation artificial neural networks) 模型,通過皮爾遜相關法、因子分析和灰色關聯法確定了影響聚碳酸酯PC老化的關鍵環境參數[89,90]。將該模型進行反復訓練并優化,在公式 (8) 和公式 (9) 的基礎上繪制了基于黃色指數的PC老化高分辨率預測圖。并得到具有高預測精度和泛化能力 (generalization performance) 的模型。該模型將有助于大氣環境中基于PC的組件的快速設計、選擇和評估。
在判斷材料的大氣腐蝕等級時,根據ISO 9223標準,利用潤濕時間、SO2濃度、Cl-濃度3個關鍵參數來判斷材料的腐蝕等級,采用關聯規則理論,以置信度的形式建立3種參數與碳鋼腐蝕等級之間的關聯規則。最后通過分段式劑量響應函數加權求得材料的腐蝕速率,進而確定材料的腐蝕等級[91]。但當3種關鍵數據出現缺失時,則利用貝葉斯網絡和聯合樹推理理論作為數學處理建模方法來判斷材料的大氣腐蝕等級[92]。計算機根據年平均溫度、年降雨量、日照時間、風速和是否沿海等五個環境因素自動判別金屬材料大氣腐蝕等級。
傳統的研發高品質耐蝕鋼的方法需要大量的長周期室外暴露腐蝕試驗數據做支撐,研發周期長、費用高、環境因素耦合性差,數據獲得困難,數據量稀缺對耐蝕鋼品質的提升影響巨大。傳統的評價耐蝕鋼性能的方法不能準確地反映合金元素的微量變化及組織結構的微小差異對耐蝕性的影響,更無法反映耐蝕性的演化規律,甚至導致很多相反的結論,直接影響耐蝕鋼性能的提升。李曉剛團隊[93]現已將大數據監測技術用于高品質耐蝕鋼的研發上,基于大數據技術快速評價耐蝕新鋼種的耐蝕性,建立了耐蝕新鋼種成分、組織、結構以及環境因素耦合關聯的耐蝕鋼高分辨評估系統,能大大地縮短研發周期,同時還用于已服役耐蝕鋼結構的腐蝕狀態監測及腐蝕剩余壽命的評估。
4 總結與展望
近年來,材料大氣腐蝕試驗方法研究正在發生從宏觀表征向納米尺度表征、從定性到比較精確定量、從長期試驗到快速試驗方向、從碎片化數據向大數據方向發展。大數據處理方法也已經多樣化,但每種方法都有自己的優缺點,將每種方法相互補充,可以從多個角度獲得對金屬大氣腐蝕機理與規律的新的認識。
材料腐蝕大數據監測和處理技術是在已有的大氣腐蝕加速試驗方法基礎上,發展更真實地模擬大氣環境以及重現性好的大氣加速腐蝕試驗方法,應用于多種材料的腐蝕 (老化) 機理及規律探究,使從短期的加速試驗結果精確預測長期的腐蝕行為和壽命成為可能。電化學方法作為一種研究大氣腐蝕強有力的手段,采用大數據技術采集數據后,仍需與各種物理手段相結合,以得到材料的宏觀與微觀組織結構信息,才能更準確的探究材料在大氣環境下的腐蝕狀態。各種腐蝕檢測和監測技術優勢互補才是腐蝕大數據監測發展的方向。在探針檢測基礎上建立腐蝕實時在線監測網,將腐蝕監測獲得的數據利用數據庫技術和現代化數據處理手段,用先進的數學方法進行分析、判斷,可以獲得以前片段化數據無法確定材料 (設備) 的腐蝕行為特征與類型,可以成為高品質耐蝕新材料開發和設備腐蝕壽命精確評定的基礎。
參考文獻
1 Biezma M V, Cristóbal J R S. Methodology to study cost of corrosion [J]. Corros. Eng. Sci. Technol., 2005, 40: 344
2 Chen Y C, An Z J. Corrosion analysis and protection design of organic coatings about transmission tower [J]. Mod. Paint Finish., 2010, 13(10): 23
2 陳耀財, 安貞基. 輸電鐵塔腐蝕分析與有機涂料防護設計 [J]. 現代涂料與涂裝, 2010, 13(10): 23
3 The atmospheric corrosion of steels as influenced by changes in chemical composition [A]. Proc. 1stInt. Cong. Met. Corros [C]. Butterworth, London, UK, 1962, 276
4 Chandler K A, Kilculen M B.A review with particular reference to atmospheric condition in the United Kingdom [J]. Br. Corros. J.,1974, 5: 24
5 Wallinder I O, Leygraf C. Seasonal variations in corrosion rate and runoff rate of copper roofs in an urban and a rural atmospheric environment [J]. Corros. Sci., 2001, 43: 2379
6 Odnevall I. Atmospheric corrosion of field exposed zinc-A multianalytical characterization of corrosion products from initial films to fully developed layers [D]. Sweden: Royal Institute of Technology, 1994
7 Wang S M, Xiao Y D, Zhang S P. SO2/salt-spray synergistic accelerated test simulating atmospheric exposure corrosion behavior of zinc [J]. Corros. Prot., 2005, 26: 13
7 王紹明, 蕭以德, 張三平. SO2/鹽霧復合循環加速腐蝕試驗模擬鋅在戶外大氣暴露腐蝕行為 [J]. 腐蝕與防護, 2005, 26: 13
8 Xu N X, Zhang C D, Ding C H. A new approach to accelerate atmospheric corrosion test [J]. J. Chin. Soc. Corros. Prot., 1990, 10: 228
8 徐乃欣, 張承典, 丁翠紅. 加速大氣腐蝕試驗的一個新方案 [J]. 中國腐蝕與防護學報, 1990, 10: 228
9 Wang X, Cao X L, Xu M. Study and test of electrolytic corrosion for HVDC support insulator [J]. High Voltage Eng., 2006, 32(3): 31
9 王烜, 曹曉瓏, 徐曼. 高壓直流支柱絕緣子電化學腐蝕試驗研究 [J]. 高電壓技術, 2006, 32(3): 31
10 Rahman S, Divi S, Chandra D, et al. Effect of different salts on the corrosion properties of friction type A607 steel rock bolt in simulated concentrated water [J]. Tunn. Undergr. Space Technol., 2008, 23: 665
11 Zhu F, Persson D, Thierry D, et al. Formation of corrosion products on open and confined metal surfaces exposed to periodic wet/dry conditions—A comparison between zinc and electrogalvanized steel [J]. Corrosion, 2001, 57: 582
12 Wang Y, Mu X, Dong J H, et al. Insight into atmospheric corrosion evolution of mild steel in a simulated coastal atmosphere [J]. J. Mater. Sci. Technol., 2021, 76: 41
13 Chen W J, Fang L, Pan G. Corrosion evolution characteristics of Q235B steel in O3/SO2 composite atmosphere [J]. J. Chin. Soc. Corros. Prot., 2021, 41: 450
13 陳文娟, 方蓮, 潘剛. O3/SO2復合大氣環境中Q235B鋼的腐蝕演化特性 [J]. 中國腐蝕與防護學報, 2021, 41: 450
14 Li J, Li M, Sun Z. Development of an artificial climatic complex accelerated corrosion tester and investigation of complex accelerated corrosion test methods [J]. Corrosion, 1999, 55: 498
15 Kelvin L. V. Contact electricity of metals [J]. Lond., Edinb., Dub. Philos. Mag. J. Sci., 1898, 46: 82
16 Zisman W A. A new method of measuring contact potential differences in metals [J]. Rev. Sci. Instrum., 1932, 3: 367
17 Stratmann M. The investigation of the corrosion properties of metals, covered with adsorbed electrolyte layers—A new experimental technique [J]. Corros. Sci., 1987, 27: 869
18 Sun Z H, Li J Z, Liu M H, et al. Application of Kelvin probe vibrating capacitor technique in study of atmospheric corrosion [J]. Corros. Sci. Prot. Technol., 2001, 13: 451
18 孫志華, 李家柱, 劉明輝等. Kelvin探頭振動電容法技術在大氣腐蝕中的應用 [J]. 腐蝕科學與防護技術, 2001, 13: 451
19 Stratmann M, Leng A, Fürbeth W, et al. The scanning Kelvin probe; a new technique for the in situ analysis of the delamination of organic coatings [J]. Prog. Org. Coat., 1996, 27: 261
20 Wang J, Tsuru T. Electrochemical measurements under thin electrolyte layer using Kelvin probe reference electrode [J]. J. Chin. Soc. Corros. Prot., 1995, 15: 173
21 Wang J, Tsuru T. An investigation on oxygen reduction under thin electrolyte layer using Kelvin probe reference electrode [J]. J. Chin. Soc. Corros. Prot., 1995, 15: 174
22 Schmutz P, Frankel G S. Characterization of AA2024‐T3 by scanning Kelvin probe force microscopy [J]. J. Electrochem. Soc., 1998, 145: 2285
23 Schmutz P, Frankel G S. Corrosion study of AA2024‐T3 by scanning Kelvin probe force microscopy and in situ atomic force microscopy scratching [J]. J. Electrochem. Soc., 1998, 145: 2295
24 Guo L Q, Li M, Shi X L, et al. Effect of annealing temperature on the corrosion behavior of duplex stainless steel studied by in situ techniques [J]. Corros. Sci., 2011, 53: 3733
25 Sathirachinda N, Pettersson R, Pan J S. Depletion effects at phase boundaries in 2205 duplex stainless steel characterized with SKPFM and TEM/EDS [J]. Corros. Sci., 2009, 51: 1850
26 Sathirachinda N, Pettersson R, Wessman S, et al. Scanning Kelvin probe force microscopy study of chromium nitrides in 2507 super duplex stainless steel—Implications and limitations [J]. Electrochim. Acta, 2011, 56: 1792
27 Mallinson C F, Harvey A, Watts J F. The nobility of second phase particles in S-65 beryllium studied by scanning Kelvin probe force microscopy [J]. Corros. Sci., 2016, 112: 669
28 Bettini E, Kivis?kk U, Leygraf C, et al. Study of corrosion behavior of a 22%Cr duplex stainless steel: influence of nano-sized chromium nitrides and exposure temperature [J]. Electrochim. Acta, 2013, 113: 280
29 Buzolin R H, Mohedano M, Mendis C L, et al. As cast microstructures on the mechanical and corrosion behaviour of ZK40 modified with Gd and Nd additions [J]. Mater. Sci. Eng., 2017, 682A: 238
30 Taylor S R. Incentives for using local electrochemical impedance methods in the investigation of organic coatings [J]. Prog. Org. Coat., 2001, 43: 141
31 Annergren I, Thierry D, Zou F. Localized electrochemical impedance spectroscopy for studying pitting corrosion on stainless steels [J]. J. Electrochem. Soc., 1997, 144: 1208
32 Li M C, Cheng Y F. Corrosion of the stressed pipe steel in carbonate-bicarbonate solution studied by scanning localized electrochemical impedance spectroscopy [J]. Electrochim. Acta, 2008, 53: 2831
33 Zhong C, Tang X, Cheng Y F. Corrosion of steel under the defected coating studied by localized electrochemical impedance spectroscopy [J]. Electrochim. Acta, 2008, 53: 4740
34 Isaacs H S,Kissel G.Surface preparation and pit propagation in stainless steels [J]. J. Electrochem. Soc., 1972, 119(12): 1628
35 Sim?es A, Battocchi D, Tallman D, et al. Assessment of the corrosion protection of aluminium substrates by a Mg-rich primer: EIS, SVET and SECM study [J]. Prog. Org. Coat., 2008, 63: 260
36 Bai Y L, Shen G L, Qin Q Y, et al. Effect of thiourea imidazoline quaternary ammonium salt corrosion inhibitor on corrosion of X80 pipeline steel [J]. J. Chin. Soc. Corros. Prot., 2021, 41: 60
36 白云龍, 沈國良, 覃清鈺等. 硫脲基咪唑啉季銨鹽緩蝕劑對X80管線鋼腐蝕的影響 [J]. 中國腐蝕與防護學報, 2021, 41: 60
37 Bard A J, Fan F R F, Kwak J, et al. Scanning electrochemical microscopy. Introduction and principles [J]. Anal. Chem., 1989, 61: 132
38 Casillas N, Charlebois S J, Smyrl W H, et al. Scanning electrochemical microscopy of precursor sites for pitting corrosion on titanium [J]. J. Electrochem. Soc., 1993, 140: L142
39 Zhu Y Y, Williams D E. Scanning electrochemical microscopic observation of a precursor state to pitting corrosion of stainless steel [J]. J. Electrochem. Soc., 1997, 144: L43
40 Williams D E, Mohiuddin T F, Zhu Y Y. Elucidation of a trigger mechanism for pitting corrosion of stainless steels using submicron resolution scanning electrochemical and photoelectrochemical microscopy [J]. J. Electrochem. Soc., 1998, 145: 2664
41 Katemann B B, Inchauspe C G, Castro P A, et al. Precursor sites for localised corrosion on lacquered tinplates visualised by means of alternating current scanning electrochemical microscopy [J]. Electrochim. Acta, 2003, 48: 1115
42 Skerry B S, Johnson J B, Wood G C. Corrosion in smoke, hydrocarbon and SO2 polluted atmospheres—Ⅰ. General behaviour of iron [J]. Corros. Sci., 1988, 28: 657
43 Stratmann M, Streckel H, Kim K T, et al. On the atmospheric corrosion of metals which are covered with thin electrolyte layers-iii. the measurement of polarisation curves on metal surfaces which are covered by thin electrolyte layers [J]. Corros. Sci., 1990, 30: 715
44 Zakipour S, Leygraf C. Quartz crystal microbalance applied to studies of atmospheric corrosion of metals [J]. Br. Corros. J., 1992, 27: 295
45 Neufeld A K, Cole I S, Bond A M, et al. The initiation mechanism of corrosion of zinc by sodium chloride particle deposition [J]. Corros. Sci., 2002, 44: 555
46 Zhang J B, Wang Y H, Jiang Y L, et al. Micro-droplets phenomenon and atmospheric corrosion—Ⅰ. Formation and spreading of micro-droplets [J]. J. Chin. Soc. Corros. Prot., 2006, 26: 207
46 張際標, 王燕華, 姜應律等. 微液滴現象與大氣腐蝕—Ⅰ. 微液滴的形成與擴展 [J]. 中國腐蝕與防護學報, 2006, 26: 207
47 Zhang J B, Wang J, Wang Y H, Phenomenon of micro-droplets formation on metals during the deliquescence of salt particles in atmosphere [J]. Acta Phys. -Chim. Sin., 2005, 21: 993
48 Zhang J B, Wang Y H, Jiang Y L, et al. Micro-droplets phenomenon and atmospheric corrosion—Ⅱ. Electrochemical characteristics of the micro-droplets phenomenon [J]. J. Chin. Soc. Corros. Prot., 2006, 26: 282
48 張際標, 王燕華, 姜應律等. 微液滴現象與大氣腐蝕—Ⅱ. 微液滴現象的電化學表征 [J]. 中國腐蝕與防護學報, 2006, 26: 282
49 Tsuru T, Tamiya K I, Nishikata A. Formation and growth of micro-droplets during the initial stage of atmospheric corrosion [J]. Electrochim. Acta, 2004, 49: 2709
50 Zhang J B, Wang J, Wang Y H, et al. Micro-droplets phenomenon and atmospheric corrosionⅢ. Spreading behaviors of micro-droplets under cyclic wet-dry conditions [J]. J. Chin. Soc. Corros. Prot., 2006, 28: 151
50 張際標, 王佳, 王燕華等. 微液滴現象與大氣腐蝕Ⅲ. 干濕交替下微液滴的擴展行為 [J]. 中國腐蝕與防護學報, 2006, 28: 151
51 Sauerbrey G Z. Use of quartz vibrator for weighing thin films on a microbalance [J]. J. Physik., 1959, 155: 206
52 Encarna??o J M, Rosa L, Rodrigues R, et al. Piezoelectric biosensors for biorecognition analysis: application to the kinetic study of HIV-1 Vif protein binding to recombinant antibodies [J]. J. Biotechnol., 2007, 132: 142
53 Legault R A, Pearson V P. The kinetics of the atmospheric corrosion of aluminized steel [J]. Corrosion, 1978, 34: 344
54 Legault R A, Preban A G. Kinetics of the atmospheric corrosion of low-alloy steels in an industrial environment [J]. Corrosion, 1975, 31: 117
55 Zhang X Y, Han E-H, Persson D, et al. In-situ infrared reflection absorption spectroscopy studies of confined zinc surfaces exposed under periodic wet-dry conditions [J]. J. Chin. Soc. Corros. Prot., 2002, 22: 32
55 張學元, 韓恩厚, Persson D等. 利用IRAS研究鋅表面在濕干交替條件下的腐蝕行為 [J]. 中國腐蝕與防護學報, 2002, 22: 32
56 Aastrup T, Wadsak M, Schreiner M, et al. Experimental in situ studies of copper exposed to humidified air [J]. Corros. Sci., 2000, 42: 957
57 Wadsak M, Schreiner M, Aastrup T, et al. Combined in-situ investigations of atmospheric corrosion of copper with SFM and IRAS coupled with QCM [J]. Surf. Sci., 2000, 454-456: 246
58 Itoh J, Sasaki T, Seo M, et al. In situ simultaneous measurement with IR-RAS and QCM for investigation of corrosion of copper in a gaseous environment [J]. Corros. Sci., 1997, 39: 193
59 Dravnieks A, Cataldi H A. Industrial applications of a method for measuring small amounts of corrosion without removal of corrosion products [J]. Corrosion, 1954, 10: 224
60 Freedman A J, Troscinski E S, Dravnieks A. An electrical resistance method of corrosion monitoring in refinery equipment [J]. Corrosion, 1958, 14: 29
61 Legat A. Monitoring of steel corrosion in concrete by electrode arrays and electrical resistance probes [J]. Electrochim. Acta, 2007, 52: 7590
62 He Z, Wang X P, Liu Z H, et al. Passivation and pitting of 316L and HR-2 stainless steel in hydrochloric acid liquid membrane environment [J]. J. Chin. Soc. Corros. Prot., 2020, 40: 17
62 何壯, 王興平, 劉子涵等. 316L和HR-2不銹鋼在鹽酸液膜環境中的鈍化與點蝕 [J]. 中國腐蝕與防護學報, 2020, 40: 17
63 Marja-Aho M, Rajala P, Huttunen-Saarivirta E, et al. Copper corrosion monitoring by electrical resistance probes in anoxic groundwater environment in the presence and absence of sulfate reducing bacteria [J]. Sens. Actuators, 2018, 274A: 252
64 Li Z L, Fu D M, Li Y, et al. Application of an electrical resistance sensor-based automated corrosion monitor in the study of atmospheric corrosion [J]. Materials, 2019, 12: 1065
65 Hren M, Kosec T, Legat A. Characterization of stainless steel corrosion processes in mortar using various monitoring techniques [J]. Const. Build. Mater., 2019, 221: 604
66 Birbilis N, Nairn K M, Forsyth M. Transient response analysis of steel in concrete [J]. Corros. Sci., 2003, 45: 1895
67 Mansfeld F, Kenkel J V. Electrochemical monitoring of atmospheric corrosion phenomena [J]. Corros. Sci., 1976, 16: 111
68 Xiao Y D, Zhou X J, Zhang S P. An electrochemical study for atmospheric corrosion of low-alloy steel [J]. Corros. Sci. Prot. Technol., 1995, 7: 200
68 蕭以德, 周學杰, 張三平. 低合金鋼大氣腐蝕的電化學研究 [J]. 腐蝕科學與防護技術, 1995, 7: 200
69 Pei Z B, Zhang D W, Zhi Y J, et al. Towards understanding and prediction of atmospheric corrosion of an Fe/Cu corrosion sensor via machine learning [J]. Corros. Sci., 2020, 170: 108697
70 Li X G, Li Q, Pei Z B, et al. Latest developments on atmospheric corrosion monitoring technologies for steels [J]. Angang Technol., 2020, (6): 1
70 李曉剛, 李清, 裴梓博等. 鋼鐵大氣腐蝕監測技術研究進展 [J]. 鞍鋼技術, 2020, (6): 1
71 Li C L, Ma Y T, Li Y, et al. EIS monitoring study of atmospheric corrosion under variable relative humidity [J]. Corros. Sci., 2010, 52: 3677
72 Yang F, Zhou Y F, Hu K F, et al. Progress of corrosion and protection monitoring/inspection technologies [J]. Total Corros. Control, 2009, 23(11): 46
72 楊飛, 周永峰, 胡科峰等. 腐蝕防護監測檢測技術研究的進展 [J]. 全面腐蝕控制, 2009, 23(11): 46
73 Smets H M G, Bogaerts W F L. SCC analysis of austenitic stainless steels in chloride-bearing water by neural network techniques [J]. Corrosion, 1992, 48: 618
74 Rosen E M, Silverman D C. Corrosion prediction from polarization scans using an artificial neural network integrated with an expert system [J]. Corrosion, 1992, 48: 734
75 Trasatti S P, Mazza F. Crevice corrosion: a neural network approach [J]. Br. Corros. J., 1996, 31: 105
76 Cai J P, Cottis R A, Lyon S B. Phenomenological modelling of atmospheric corrosion using an artificial neural network [J]. Corros. Sci., 1999, 41: 2001
77 Shi J B, Wang J H, Macdonald D D. Prediction of primary water stress corrosion crack growth rates in Alloy 600 using artificial neural networks [J]. Corros. Sci., 2015, 92: 217
78 Shi J B, Wang J H, Macdonald D D. Prediction of crack growth rate in Type 304 stainless steel using artificial neural networks and the coupled environment fracture model [J]. Corros. Sci., 2014, 89: 69
79 Cavanaugh M K, Buchheit R G, Birbilis N. Modeling the environmental dependence of pit growth using neural network approaches [J]. Corros. Sci., 2010, 52: 3070
80 Wei X, Fu D M, Chen M D, et al. Data mining to effect of key alloying elements on corrosion resistance of low alloy steels in Sanya seawater environment Alloying Elements [J]. J. Mater. Sci. Technol., 2021, 64: 222
81 Ren J C. ANN vs. SVM: which one performs better in classification of MCCs in mammogram imaging [J]. Knowl. Based. Syst., 2012, 26: 144
82 Fang S F, Wang M P, Qi W H, et al. Hybrid genetic algorithms and support vector regression in forecasting atmospheric corrosion of metallic materials [J]. Comput. Mater. Sci., 2008, 44: 647
83 Wen Y F, Cai C Z, Liu X H, et al. Corrosion rate prediction of 3C steel under different seawater environment by using support vector regression [J]. Corros. Sci., 2009, 51: 349
84 Bengio Y. Learning deep architectures for AI [J]. Found. Trends? Mach. Learn., 2009, 2: 1
85 Breiman L. Random forests [J]. Mach. Learn., 2001, 45: 5
86 Zhi Y J, Fu D M, Zhang D W, et al. Prediction and knowledge mining of outdoor atmospheric corrosion rates of low alloy steels based on the random forests approach [J]. Metals, 2019, 9: 383
87 Zhi Y J, Yang T, Fu D M. An improved deep forest model for forecast the outdoor atmospheric corrosion rate of low-alloy steels [J]. J. Mater. Sci. Technol., 2020, 49: 202
88 Gao J, Li C, Lv Z, et al. Correlation between the surface aging of acrylic polyurethane coatings and environmental factors [J]. Prog. Org. Coat., 2019, 132: 362
89 Wu D Q, Zhang D W, Liu S P, et al. Prediction of polycarbonate degradation in natural atmospheric environment of China based on BP-ANN model with screened environmental factors [J]. Chem. Eng. J., 2020, 399: 125878
90 Paturi U M R, Cheruku S, Geereddy S R. Process modeling and parameter optimization of surface coatings using artificial neural networks (ANNs): State-of-the-art review [J]. Mater. Today, 2021, 38: 2764
91 Zhao X F, Fu D M, Pei Z B, et al. Optimization of sectional dose-response function and determination method of corrosion category for carbon steel [J]. Corros. Prot., 2018, 39: 805
91 趙興鋒, 付冬梅, 裴梓博等. 分段式劑量響應函數優化及碳鋼腐蝕等級判別方法 [J]. 腐蝕與防護, 2018, 39: 805
92 Xu Q. Study on corrosion grade discrimination and material selection method based on Bayes and influence diagram [D]. Beijing: University of Science and Technology Beijing, 2013
92 徐慶. 基于Bayes和影響圖的腐蝕等級判別及選材的方法研究 [D]. 北京: 北京科技大學, 2013
93 Yang X J, Yang Y, Sun M H, et al.A new understanding of the effect of Cr on the corrosion resistance evolution of weathering steel based on big data technology [J]. J. Mater. Sci. Tech., 2022, 104: 67
免責聲明:本網站所轉載的文字、圖片與視頻資料版權歸原創作者所有,如果涉及侵權,請第一時間聯系本網刪除。
相關文章
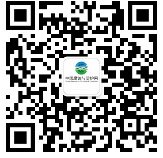
官方微信
《腐蝕與防護網電子期刊》征訂啟事
- 投稿聯系:編輯部
- 電話:010-62316606-806
- 郵箱:fsfhzy666@163.com
- 腐蝕與防護網官方QQ群:140808414
點擊排行
PPT新聞
“海洋金屬”——鈦合金在艦船的
點擊數:8168
腐蝕與“海上絲綢之路”
點擊數:6492