微生物的生命活動或其代謝產物直接或間接影響腐蝕的現象被稱為微生物腐蝕(MIC),研究發現油氣田系統中存在一種最主要的腐蝕性厭氧微生物——硫酸鹽還原菌(SRB)。近年來,SRB在天然氣生產中的影響逐漸明顯,嚴重的SRB腐蝕會使管線發生穿孔泄漏,影響天然氣生產,最終導致經濟損失和環境污染。
從2017年7月起,四川某天然氣區塊井下油管、平臺生產工藝管線、采氣管線均出現了較嚴重的腐蝕穿孔,共影響產量7336萬平方米,圖1為現場腐蝕管道的宏觀形貌。
圖1 X區塊天然氣集輸管道SRB腐蝕坑形貌
由圖1可見,該管道上腐蝕坑邊緣呈階梯狀,具有明顯的攀爬現象,管道內表面坑蝕嚴重,坑點附近管材內表面呈黑色。X射線衍射測試發現,腐蝕產物中含有FeS,而管道輸送介質中沒有含硫成分。SRB生長代謝會產生含硫物質,因此初步判斷造成X區塊天然氣集輸管線腐蝕的主要原因是SRB腐蝕。
為深入研究天然氣集輸管線在含SRB的采出水中的腐蝕情況,新疆油田儲氣庫有限公司和西南石油大學的研究人員通過浸泡腐蝕試驗,針對X區塊天然氣氣田的某管道建立腐蝕速率預測模型,以期為有效控制天然氣氣田集輸管線的腐蝕提供一定的理論依據。
SRB腐蝕試驗
01 試驗材料與溶液
試驗材料為天然氣氣田集輸管線常用的N80S、N80、BG90SS、L245N、L360NS鋼。試樣尺寸為50 mm×25 mm×2 mm,試樣依次經過200~1000號砂紙打磨、去離子水清洗、丙酮除油后,再將其放入酒精中浸泡,取出吹干,最后用濾紙包好,并保存于干燥器內,試驗開始前需對試樣進行30分鐘的紫外線滅菌。
試驗溶液為根據采出水配制的模擬溶液,其中含0.04125 g/L MgSO4、2.2977 g/L CaCl2、32.0346 g/L NaCl、0.436548 g/L NaHCO3,溶液pH為6.5。在模擬溶液中加入SRB,SRB加量分別為0、1×106、2×106、3×106、4×106、5×106、6×106 個/mL。
02 試驗方法
分別在常壓和高壓條件下,對5種試驗鋼材料進行SRB腐蝕試驗。
常壓條件下,設定每組1個錐形瓶,每個錐形瓶放入2個試片,并分別向錐形瓶內倒入650 mL含不同量SRB的模擬溶液。對錐形瓶進行1小時的通氮氣除氧,接著用封口膜密封瓶口,置于45 ℃恒溫箱中,腐蝕時間為7天。
高壓條件下,取800 mL含不同量SRB的模擬溶液置于高壓釜中,向釜體內泵入氮氣,使釜內壓力提高至5.5 MPa,啟動加熱程序,加熱至45 ℃,腐蝕時間為7天,每組試驗各做3個平行樣,達到預定時間后,切斷電源,迅速取出腐蝕掛片。
試驗結束后,按照GB/T 16545-2015《金屬和合金的腐蝕 腐蝕試樣上腐蝕產物的清除》標準對試片表面腐蝕產物和生物膜進行清洗處理,然后采用失重法計算不同條件下各試驗鋼的平均腐蝕速率及腐蝕速率增率,如下式所示:
式中:ri為試驗鋼在含SRB模擬溶液中的腐蝕速率增率,%;vi為試驗鋼在含SRB模擬溶液中的平均腐蝕速率,mm/a;v0為試驗鋼在不含SRB模擬溶液中的平均腐蝕速率,mm/a。
03 常壓條件下的SRB腐蝕結果
(a) 腐蝕速率 (b) 腐蝕速率增率
圖2 常壓條件下各試驗鋼在含不同量SRB模擬溶液中的腐蝕速率及其增率
由圖2a可見:常壓條件下,所有試驗鋼的腐蝕速率均隨模擬溶液中SRB含量的增加而增大;在未添加SRB的模擬溶液中,N80S鋼的腐蝕速率最大,為0.187 mm/a,L245N鋼的腐蝕速率最小,為0.148 mm/a;在模擬溶液中添加SRB后,N80S鋼的腐蝕速率仍比其他4種試驗鋼大,而腐蝕速率最小的是N80鋼。
以上結果說明,SRB會加速腐蝕各試驗鋼;在添加了不同量SRB的模擬溶液中,N80S鋼最易腐蝕;在未添加SRB的模擬溶液中,L245N鋼最耐腐蝕,而在模擬溶液中加入SRB后,N80鋼最不易腐蝕。
由圖2b可見:常壓條件下在模擬溶液中加入SRB后,L245N鋼的腐蝕速率增率最大,說明其受SRB的影響大,而N80鋼的腐蝕速率增率最小,說明其受SRB的影響最小;5種試驗鋼受SRB影響的大小順序為:L245N鋼>L360NS鋼>N80S鋼>BG90SS鋼>N80鋼。
04 高壓條件下的SRB腐蝕結果
(a) 腐蝕速率 (b) 腐蝕速率增率
圖3 高壓條件下各試驗鋼在含不同量SRB模擬溶液中的腐蝕速率及其增率
由圖3a可見,高壓條件下,所有試驗鋼的腐蝕速率均隨模擬溶液中SRB含量的增加而增大;在未添加SRB的模擬溶液中,N80S鋼的腐蝕速率最大,為0.203 mm/a,L360NS鋼的腐蝕速率最小,為0.149 mm/a;在模擬溶液中添加SRB后,N80S鋼的腐蝕速率仍是5種試驗鋼中最大的,而腐蝕速率最小的是N80鋼。
以上結果說明,高壓條件下無論模擬溶液中是否添加SRB,N80S鋼均最易腐蝕;在未添加SRB的模擬溶液中,L360NS鋼最耐腐蝕,而在模擬溶液中加入SRB后,N80鋼最不易腐蝕。
由圖3b可見:高壓條件下在添加了SRB的模擬溶液中,L360NS鋼的腐蝕速率增率最大,其最大值達80%以上,說明其受SRB的影響大,而N80鋼的腐蝕速率增率最小,說明其受SRB的影響最小,表現出良好的抗細菌腐蝕性;5種試驗鋼受SRB影響的大小順序為:L360NS鋼>L245N鋼>N80S鋼>BG90SS鋼>N80鋼。
微生物腐蝕速率預測模型
X區塊某條天然氣集輸管道的材料為L360鋼,起點壓力為5.5 MPa,起點溫度為45 ℃,采出水pH為6.5,與試驗條件相同。因此,基于半經驗型腐蝕速率預測模型中的DW91模型,并結合該管道微生物腐蝕機理,以管道中SRB含量為變量,溫度、壓力、pH為定量,采用origin軟件將試驗所得數據代入DW91模型進行擬合,結果如圖4所示。
圖4 DW91模型擬合結果
根據DW91模型擬合得到微生物腐蝕速率與SRB數量之間的關系式:
式中:v為腐蝕速率,mm/a;t為管道運行溫度,℃;p為管道運行壓力,105 Pa;c(H+)為采出水中H+的濃度;n為SRB含量,個/mL。
運用PIPESIM軟件模擬X區塊天然氣集輸管道沿線的壓力和溫度參數,結果如圖5和圖6所示,并將參數代入式(2)中以驗證腐蝕速率預測模型的適用性。管道腐蝕速率的模型預測結果與管道實際內檢測數據對比如表1所示。
圖5 X區塊天然氣集輸管道沿線壓力的模擬值
圖6 X區塊天然氣集輸管道沿線溫度的模擬值
表1 管道腐蝕速率的模型預測結果與內檢測結果
由表1可見,使用式(2)所示預測模型計算的腐蝕速率與測量值存在0.06~0.07 mm/a的差距。這是因為在實際測量時壓力和溫度不是定量,而是沿管線變化的。
分別以壓力和溫度作為變量,使用origin軟件對原預測模型進行修正,得到修正的預測模型,如下式所示:
用修正后模型對管道的腐蝕速率進行預測,結果也列于表1中。由表1可見,修正后管道SRB腐蝕速率預測模型的預測值與測量值的相對誤差均小于10%,該預測值更接近X區塊天然氣集輸管道的實際SRB腐蝕速率,這說明綜合考慮管道沿線溫度和壓力兩大關鍵要素對原預測模型進行修正后的SRB腐蝕速率預測模型具有較好的可靠性。
結論
(1) SRB對腐蝕影響較大,即便是在試驗中表現出良好抗細菌腐蝕性的N80鋼,在加入SRB后,其腐蝕速率也增長了10%以上,并隨著SRB含量增加而增大,而在常壓下抗細菌腐蝕性弱的L245N鋼,加入SRB后其腐蝕速率更是增加了20%~60%;在高壓環境中加入SRB后,L360NS鋼的腐蝕速率最高增長達80%。此外,相比于常壓環境,高壓條件下各鋼材的腐蝕速率都有所增加。
(2) 結合X區塊天然氣集輸管道基礎情況和試驗數據,擬合得到微生物腐蝕預測模型,計算得出的腐蝕速率與實測數據存在0.06~0.07 mm/a的差距;結合PIPESIM模擬得出檢測點的壓力和溫度,對原模型進行修正,得到適用性更佳的微生物腐蝕預測模型。
免責聲明:本網站所轉載的文字、圖片與視頻資料版權歸原創作者所有,如果涉及侵權,請第一時間聯系本網刪除。
相關文章
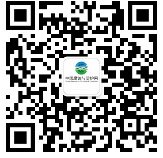
官方微信
《腐蝕與防護網電子期刊》征訂啟事
- 投稿聯系:編輯部
- 電話:010-62316606-806
- 郵箱:fsfhzy666@163.com
- 腐蝕與防護網官方QQ群:140808414
點擊排行
PPT新聞
“海洋金屬”——鈦合金在艦船的
點擊數:8178
腐蝕與“海上絲綢之路”
點擊數:6496