摘 要:某公司減速機輸入軸發生斷裂,對該斷軸進行了宏觀分析、室溫力學性能試驗、硬度試驗、金相組織分析、掃描電鏡(SEM)和 EDS 能譜分析等一系列檢測分析。結果表明:斷軸的原因是軸表面沒有進行有效滲碳處理,軸在交變旋轉彎曲應力的反復作用下,在應力集中的軸變徑處發生斷裂,并對失效機理進行了分析。
關鍵詞:減速機;斷軸;失效分析
2018 年 7 月某公司型號為 H2SV10A 的減速機輸入軸發生斷裂,圖1 為減速機輸入軸的結構。圖2 為斷裂失效輸入軸的宏觀照片。從圖 1和圖 2 可見,減速機輸入軸斷裂發生在準85 mm 外圓和100 mm 外圓的過渡階段,斷裂位置靠近85 軸徑側,即圖 1 中圓圈內標記區域。軸的材質為18CrNiMo7-6[1],屬于德國牌號。本文通過輸入軸失效分析,探尋其失效原因。
圖1 減速機輸入軸結構圖(mm)
圖2 斷裂失效輸入軸的宏觀照片
1 試驗方法及結果
1.1 宏觀分析
圖3 減速機輸入軸斷口的宏觀形貌照片
圖3 為減速機輸入軸斷口的宏觀形貌照片。斷口表面有較明顯的貝殼狀花樣, 屬于典型的疲勞斷裂。斷口由疲勞裂源區、裂紋擴展區和瞬間斷裂區組成。其中疲勞源有 3處,分別標示為 1、2、3 區域。仔細觀察斷口疲勞源區,1 和2 區域兩處表面較平坦,3 區域的疲勞源有剪切唇。疲勞源在距表面 2mm 范圍內,3 個疲勞源所處的區域之間有臺階和褶皺。裂紋擴展區貝紋線比較扁平,部分區域存在褶皺。斷口形貌為纖維狀,斷面有臺階和褶皺,表明減速機軸承受到了反復交變的旋轉彎曲應力。斷口瞬斷區域較小,約占整個斷口面積的 1/10,說明軸整體受力較小,屬于典型的低應力多疲勞源型高周疲勞斷裂。
1.2 軸的室溫拉伸試驗及沖擊性能檢測
對斷軸的力學性能進行檢測,依據國標 GB/T2975-1998 《鋼及鋼產品力學性能試驗取樣位置及試驗制備》[2]選取被檢試樣位置,根據國標GB/T228.1-2010《金屬材料拉伸試驗第 1 部分:室溫試驗方法》[3],在軸的縱向采用線切割進行拉伸試樣加工,制作標準試樣進行室溫拉伸試驗。根據 GB/T229-2007 《金屬材料 夏比擺錘沖擊試驗方法》[4],在軸縱向取沖擊試樣,試樣尺寸為 10mm×10mm×55mm,V 型缺口,試驗溫度為 20℃。每種試樣分別制作 3 個, 試樣選材為85 mm和100 mm兩側的母材。表 1 為斷軸的室溫拉伸試驗結果,表 2 為斷軸的沖擊性能檢測結果。
表1 斷軸的室溫拉伸試驗結果
由表 1 看到,斷軸室溫拉伸性能符合技術要求。
表2 斷軸沖擊性能檢測結果(J)
由表 2 看到,斷軸沖擊性能檢測結果符合技術要求。
1.3 軸、截面及斷口區域顯微硬度檢測
依據國標 GB/T 4340.1-2009 《金屬維氏硬度試驗第 1 部分:試驗方法》[5],對 1 和 2 區域沿徑向截取兩個條形金相試樣進行顯微硬度檢測,完成軸、截面及斷口區域顯微硬度檢測,顯微硬度載荷為 200g,作用時間 12s。斷軸不同區域的顯微硬度檢測結果見表 3。根據顯微硬度檢測結果,輸入軸 1 區域的所有截面硬度及斷口區域的硬度值基本相同,為355~403HV0.2。輸入軸 2 區域的所有截面硬度及斷口區域的硬度值基本相同,為 322~375 HV0.2。由此可見,1區域整體硬度比 2 區域的高,驗證了輸入軸未進行有效的表面滲碳處理。
表3 斷軸不同區域的顯微硬度檢測結果(HV0.2)
1.4 軸及截面的宏觀洛氏硬度檢測
依據國標 GB/T230.1-2018 《金屬洛氏硬度試驗第 1 部分:試驗方法》[6]加工試樣,根據 EN 10084-2008《滲碳鋼-交貨技術條件》標準要求,選取對應的部位進行洛氏硬度檢測。表 4 為斷軸宏觀洛氏硬度檢測結果。由表 4 可見,兩側軸徑距淬火端 1.5~7.0 mm 處的宏觀洛氏硬度不符合標準要求,除了100mm 側 1.5mm 處洛氏硬度較高外,軸的其余外表面和截面硬度值大致相等,整個截面的硬度也基本一致,為 38~35HRC。根據標準要求,該材質表面要進行滲碳處理,說明斷軸未進行有效的表面處理。
表4 斷軸宏觀洛氏硬度檢測結果(HRC)
1.5 軸及斷口區域金相組織分析
本次試驗研究分別在圖3 中標注的 1 和 2 區域沿徑向截取兩個條形試樣,在拋光機上進行磨制后,用4%硝酸酒精溶液侵蝕,在 GX71 型研究級金相顯微鏡下進行微觀組織分析,依據 DL/T 884-2004《火電廠金相檢驗與評定技術導則》[7]。圖4 為 1 區域外表面低倍形貌及外表面、斷口和心部的金相組織。其中,圖4(a)和(b)分別為 1 區域外表面低倍形貌和金相組織照片,外表面可見 1 條長約 0.077mm 的裂紋,表面未見滲碳層,其表面金相組織為回火索氏體。圖4(c)和(d)分別為 1 區域斷口和心部的金相組織照片,其組織為回火索氏體。
圖4 1區域外表面低倍形貌與外表面、斷口和心部的金相組織
圖5 2區域外表面低倍形貌及外表面、斷口表面、心部金相組織
圖5 為 2 區域外表面低倍形貌及外表面、斷口和心部的金相組織。其中,圖 5(a)為 2 區域外表面低倍形貌,表面未見滲碳層;圖5(b)為 2 區域斷口的金相組織照片,其組織為回火索氏體;圖 5(c)為 2 區域心部的金相組織,其組織為回火索氏體。從金相組織分析看,軸的表面未進行滲碳處理,組織未見異常。
1.6 掃描電鏡(SEM)分析
采用掃描電子顯微鏡對減速機斷軸斷面進行分析, 分別選取 1 區域疲勞源和瞬時斷裂區兩個部位進行掃描電鏡分析。圖 6 為 1 區域的疲勞源形貌。疲勞源為表面缺口,圖中的摩擦痕跡表明,此處可見由于受到反復的交變應力導致的滑移痕跡,進一步驗證此處就是疲勞源。圖7 為疲勞擴展區的疲勞條紋形貌。圖 8瞬時斷裂區低倍、解理及最后拉斷區韌窩形貌。圖 8(a)為瞬時斷裂區的斷口低倍形貌,圖 8(b)為瞬時斷裂區的解理斷口形貌。從掃描電鏡圖可看出, 瞬時斷裂區的大部分區域斷裂微觀形貌為解理斷裂,斷口微觀形貌呈河流花樣。瞬時斷口區域只有最后斷裂的部位呈現韌窩形態(圖 8(c))。由掃描電鏡的分析結果看, 斷口呈現典型的疲勞斷裂的微觀形貌特征。
圖8 瞬時斷裂區低倍、解理及最后拉斷區韌窩形貌
1.7 能譜(EDS)分析
采用 EADX 能譜儀對減速機輸入軸斷面區域表面進行微區半定量能譜分析。圖 9 為斷軸的疲勞源區域能譜分析。具體檢驗結果見表 5。由表 5 可見,疲勞源表面主要元素為 Fe、C和 Cr,說明疲勞源區域未見明顯氧化及外部介質的腐蝕。圖 10為斷軸瞬時斷裂區域能譜分析。具體檢驗結果見表 6。由表5 看到疲勞源表面主要元素為 Fe、C 和 Cr,說明瞬時斷裂區域未見明顯氧化及外部介質的腐蝕。疲勞源和瞬時斷裂區的微區能譜分析結果相近, 說明軸的斷面區域未受到外來腐蝕介質影響,軸斷裂與外部介質無關。
圖9 斷軸疲勞源區域能譜分析
圖10 斷軸瞬時斷裂區域能譜分析
表5 斷軸疲勞源區域能譜分析結果
表6 斷軸瞬時斷裂區域能譜分析結果
2 分析與討論
對減速機輸入軸斷口的宏觀分析表明,軸的斷裂呈現低應力多疲勞源型高周疲勞斷裂,斷裂區域位于變徑處偏85mm 側,該處是應力集中區域。軸的室溫拉伸試驗及沖擊性能檢測結果顯示,軸的強度和沖擊韌性試驗結果均符合技術要求。軸、截面及斷口區域顯微硬度和宏觀洛氏硬度檢測結果表明,軸的外表面未進行有效滲碳處理。軸及斷口區域金相組織分析結果表明該軸是在調質熱處理狀態下未經表面處理直接投入使用。斷口的掃描電鏡分析結果看,斷口的疲勞源及疲勞擴展區得到證實,斷口呈現典型的疲勞斷裂的微觀形貌特征。能譜分析結果顯示,軸的斷面區域未受到外來腐蝕介質影響,軸斷裂與外部介質無關。
軸的工作狀態要求其表面硬度較高、耐磨,心部硬度相對較低,韌性較好。通常情況,軸表面一般經高頻或中頻滲碳處理后才使用,而失效軸的調質使用狀態與理論要求的高頻或中頻表面處理使用狀態不相符,由于工藝上的不合理,造成軸的疲勞抗力降低。另外,軸在承受旋轉彎曲應力的作用下,由于軸的表面硬度較低,加上變徑處應力集中,該處本身就是軸運行中的薄弱區域,在變徑處過早的產生疲勞源。在軸的高速旋轉過程中,最先開裂的區域在交變的彎曲應力作用下對臨近區域進行摩擦,又在臨近區域產生新的疲勞源,進而產生 3 個疲勞源,隨著循環載荷的作用,疲勞裂紋不斷向基體內擴展,致使軸的有效承載尺寸減少,最后導致軸的斷裂。
3 結論
某公司H2SV10A 減速機輸入斷裂機理是低應力多疲勞源的高周疲勞斷裂。斷裂的內因是斷裂側的軸表面沒有進行有效滲碳處理,斷裂的外因是軸在交變旋轉彎曲應力的反復作用下,在應力集中的軸的變徑處發生斷裂。
參考文獻:
[1] 滲碳鋼-交貨技術條件(中文版)
[2] 鋼及鋼產品力學性能試驗取樣位置及試驗制備
[3] 金屬材料拉伸試驗第 1 部分:室溫試驗方法
[4] 金屬材料夏比擺錘沖擊試驗方法
[5] 金屬洛氏硬度試驗第 1 部分:試驗方法
[6] 金屬維氏硬度試驗第 1 部分:試驗方法
[7] 火電廠金相檢驗與評定技術導則
免責聲明:本網站所轉載的文字、圖片與視頻資料版權歸原創作者所有,如果涉及侵權,請第一時間聯系本網刪除。
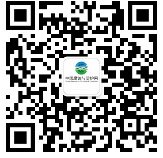
官方微信
《腐蝕與防護網電子期刊》征訂啟事
- 投稿聯系:編輯部
- 電話:010-62316606-806
- 郵箱:fsfhzy666@163.com
- 腐蝕與防護網官方QQ群:140808414