1、HCl-H2O(氯化氫)腐蝕
腐蝕部位:常壓塔頂五層塔盤,塔體,部分揮發線及常壓塔頂冷凝冷卻系統;減壓塔部分揮發線和冷凝冷卻系統。
腐蝕形態:碳鋼部件的全面腐蝕、均勻減薄;Cr13鋼的點蝕以及1Cr18Ni9Ti 不銹鋼為氯化物應力腐蝕開裂。
腐蝕原因:原油中含有的氯鹽加熱到120℃以上時,開始水解生成HCl,在塔頂低溫部位遇水滴形成鹽酸,成為腐蝕性極強的稀鹽酸腐蝕環境。與設備本體發生化學腐蝕。有硫化氫存在時進一步加劇腐蝕。
防護措施:以工藝防護為主,材料防腐為輔。
工藝防護即“一脫四注”:原油深度脫鹽,脫鹽后原油注堿、塔頂餾出線注氨(或胺)、注緩蝕劑、注水。該項防腐措施的原理是除去原油中的雜質,中和已生成的酸性腐蝕介質,改變腐蝕環境和在設備表面形成防護屏障。
材料防腐即在工藝防護基礎上,提高材料等級,選用如20R+0Cr13復合板制造常壓塔頂5層塔盤部位殼體。
2、S-H2S-RSH(硫醇)腐蝕
高溫硫腐蝕部位:焦化分餾塔底系統最嚴重,蒸餾減壓塔底系統次之,催化分餾塔底系統又次之。
腐蝕形態:化學腐蝕,均勻減薄。
腐蝕原因:硫化氫、硫醇和單質硫在350~400℃都能與金屬直接發生化學反應,而且硫化氫在340~400℃分解出來的元素硫有更強的活性,使腐蝕更為激烈。
防護措施:主要是選用耐蝕鋼材。如20R+0Cr13復合板。
3、RNH2-CO2-H2S-H2O(濕硫化氫)腐蝕
腐蝕部位:脫硫裝置再生塔底部,再生塔重沸器及富液系統管線,溫度90~120,壓力0.2MPa。
腐蝕形態:在堿性介質下(PH8~10.5)由碳酸鹽及胺引起的應力腐蝕開裂和均勻減薄。
腐蝕原因:乙醇胺與二氧化碳由不可逆反應生成的聚胺型物質是促進設備腐蝕的最普通的降解物質,在120度時降解析出二氧化碳。游離的或者化合的CO2 均能引起腐蝕,嚴重的腐蝕發生于有水的高溫部位(90℃)以上,濃度為20~30%時,腐蝕尤為嚴重,硫化氫與二氧化趟混合物的腐蝕比相應濃度的二氧化碳的腐蝕要輕,并隨硫化氫濃度的增加而降低。即硫化氫有抑制二氧化碳腐蝕的作用。
4、Fe+2CO2+2H2O、Fe(HCO3)2+H2Fe(HCO3)、(加熱)FeCO3+CO2+H2、Fe+H2CO3、FeCO3+H2腐蝕
防護措施:操作溫度高于90度的設備及管線焊后進行消除應力熱處理,控制焊縫及熱影響區的硬度小于HB200,換熱設備管束選用18-8鋼,改進操作條件,控制操作溫度,在單乙醇胺系統注入緩蝕劑等。
5、RCOOH(環烷酸)腐蝕
腐蝕部位:減壓爐出口轉油線、減壓塔進料段以下部位為重。常壓爐出口轉油線及常壓爐進料段次之。焦化分餾塔集油箱部位又次之。
腐蝕形態:遭受腐蝕的鋼材表面光滑無垢,位于介質流速低的部位腐蝕僅留下尖銳的孔洞;高流速部位的腐蝕則出現帶有銳邊的坑蝕或蝕槽。
腐蝕原因:環烷酸在低溫時腐蝕不強烈。一旦沸騰,特別是在高溫無水環境中,腐蝕最為激烈:2RCOOH+Fe--Fe(RCOO)2+H2當酸值大于0.5mgKOH/g原油,溫度在270~280℃和350~400℃時,環烷酸腐蝕最嚴重。
防護措施:主要是選用耐蝕鋼材,如316L等;設備管道以及爐管彎頭內壁焊縫應磨平,保持內壁光滑,防止預生渦流而加劇腐蝕;適當加大爐出口轉油線管徑,降低流速。
6、氫氟酸的腐蝕
腐蝕部位:主要是烷基化裝置內與介質接觸的設備及管道,以洗化廠烷基苯裝置為主。
腐蝕形態:為均勻腐蝕;氫鼓泡和氫脆;應力腐蝕和縫隙腐蝕4種。
腐蝕原因:氫氟酸對金屬材料的腐蝕是電化學腐蝕,其腐蝕是按電化學過程進行,即陽極產生金屬溶解(均勻腐蝕)陰極析出氫,導致氫鼓泡、氫脆及應力腐蝕開裂。
防護措施:材料選用:碳鋼在65℃以下,濃度大于75%的氫氟酸介質中油較好的抗腐蝕性能,但應選用鎮靜鋼板。在溫度大于71℃且低于136℃時,任意濃度的氫氟酸介質中均可適用于蒙乃爾合金,但當介質帶有氧或鐵鹽等有害雜質時期耐蝕性能就有所降低。
制造的特殊要求:凡是和氫氟酸介質接觸的碳鋼、蒙乃爾設備焊接后應經消除應力熱處理。
焊縫硬度不應大于HB235。
免責聲明:本網站所轉載的文字、圖片與視頻資料版權歸原創作者所有,如果涉及侵權,請第一時間聯系本網刪除。
相關文章
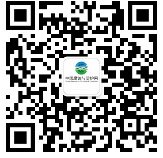
官方微信
《腐蝕與防護網電子期刊》征訂啟事
- 投稿聯系:編輯部
- 電話:010-62316606-806
- 郵箱:fsfhzy666@163.com
- 腐蝕與防護網官方QQ群:140808414
點擊排行
PPT新聞
“海洋金屬”——鈦合金在艦船的
點擊數:8223
腐蝕與“海上絲綢之路”
點擊數:6544