隨著世界工業生產的迅速發展,大量CO2排入大氣引發全球氣候變暖等一系列問題[1,2]。CO2捕集與儲存(carbon capture and storage,CCS)技術被認為是實現全球CO2減排的最有效方式[3~6],CO2的管道輸送是CCS技術鏈中十分重要的一環[7~9]。由于CO2流體的臨界參數較低(臨界壓力為7.38 MPa,臨界溫度為31.1℃)[10~12],輸送過程中溫度和壓力的變化易導致CO2流體相態的改變[13,14],故CO2管道輸送過程中常使CO2維持單一相態輸送。根據不同的輸送相態(純CO2相圖如圖1所示),CO2輸送可分為氣態、液態、密相態及超臨界態輸送4種方式[15]。當前世界上絕大多數CO2輸送管道建于美國,且輸送方式多采用超臨界態或密相態輸送[16]。超臨界態或密相態CO2輸送管道的運輸效率更高,但一旦發生泄漏等事故,易造成嚴重環境及安全災害,而氣態CO2輸送管道則具有較高的安全性[17,18]。作為CO2的主要排放國家之一,我國對CCS技術給予高度重視,且將CCS技術列入中長期發展規劃中。我國CO2輸送管道建設起步較晚,尚無成熟的大規模長距離CO2輸送管道投入運行,見報道的有齊魯石化至正理莊油田的75 km CO2輸送管道[19]、大慶油田建造的6.5 km CO2-EOR先導性試驗CO2輸送管道[20]和吉林油田建成的約50 km的CO2驅用管道,以上管道均為氣態CO2輸送管道[21]。
圖1 純CO2相圖
CO2管道在輸送過程中發生泄漏是十分嚴重的事故之一。美國管道安全處(OPS)的統計數據表明,45%的CO2輸送管道發生失效是由腐蝕造成的[22],由于CO2輸送管道內不可避免地含有水分及其他氣體雜質(如SOx、NOx、O2、H2S、N2等)[23,24],且在高壓環境下CO2與水的互溶度發生改變,在管內形成具有腐蝕性的溶液,極大地增加了管道發生腐蝕的風險。此外,相比于石油天然氣輸送管道,CO2輸送管道中CO2流體作為主相,與管內其他雜質的交互作用及理化性質隨環境發生的變化與油氣管道具有顯著差異,值得深入探究。目前國內外針對CO2輸送管線內腐蝕問題的研究主要集中在超臨界相態[25~34],對于含雜質氣態CO2輸送管道的內腐蝕研究較少。考慮到我國CCS技術的應用現狀和發展規劃,探明氣態CO2輸送管道的腐蝕行為及機理,并提出合理的腐蝕速率預測模型,對明確氣態CO2輸送管道腐蝕規律、規避管道發生腐蝕風險、減小管道運行經濟損失,具有十分重要的現實意義。本文針對目前含雜質氣態CO2輸送管道的內腐蝕研究進行了系統的綜述,總結了氣態CO2輸送管道腐蝕的影響因素,分析了氣態CO2輸送管道不發生腐蝕臨界含水量的確定,歸納了適用于氣態CO2輸送管道的腐蝕速率預測模型,并針對現有研究的不足提出了當前亟待解決的科學問題和研究展望。
1 氣態CO2輸送管道腐蝕的影響因素
氣態CO2輸送管道在低溫高壓條件下(20~50℃、2~5 MPa)運行,管道內不可避免地存在水分及其他雜質(如SOx、NOx、O2、H2S、N2等),雜質的存在及相互作用是引發管道發生腐蝕的潛在因素。表1[35~45]列出了近年來關于含雜質氣態CO2輸送管道腐蝕的研究結果,雜質的種類及含量、環境條件(溫度、壓力等)的變化都會對輸送管道的腐蝕行為產生重要影響,但雜質及環境條件對管道腐蝕的作用還需要進一步深入研究。
表1 近年來氣態CO2輸送管道腐蝕的研究結果[35~45]
1.1 雜質對氣態CO2輸送管道腐蝕的影響
1.1.1 雜質對互溶度的影響
水是腐蝕發生的根本條件,干燥的CO2不會導致腐蝕發生[46~48],腐蝕環境中水與CO2的互溶度決定了管道金屬表面水凝結析出的數量,并決定了金屬表面腐蝕溶液中腐蝕物質的濃度,故水與CO2的互溶度計算是腐蝕問題研究的基礎。高壓環境下,CO2輸送管道內存在的雜質對水與CO2的互溶度產生影響,雜質及溫度、壓力的變化可能導致水相析出,并改變水相的化學組成,引起管線發生腐蝕。Spycher等[49]首先使用簡化的H2O-CO2二元體系狀態方程初步計算了溫度范圍為12~100℃、壓力范圍為0.1~60 MPa條件下水與CO2的互溶度,但當溫度、壓力較高時計算結果精度不高且計算過程較為依賴現場數據。為了進一步細致研究互溶度隨溫度、壓力的變化,Choi和Ne?i?[37]提出了在不含雜質的情況下水與CO2的互溶度計算模型(如式(1)和(2)所示),其研究認為,當溫度范圍為15~85℃、壓力范圍為0.1~30 MPa時,隨著壓力的升高,水與CO2的互溶度均有所增大,但隨著溫度的升高,水在CO2中的溶解度有所增大,而CO2在水中的溶解度有所減小。此外,CO2在水中的溶解度遠大于水在CO2中溶解度。互溶度計算模型的建立為不同條件下水相析出量的確定提供了參考,并為描述腐蝕的嚴重程度提供了量化借鑒。
式中,為水在CO2相中的摩爾分數;為CO2在水相中的摩爾分數;P為壓力;T為溫度;P0為參比壓力(0.1 MPa);R為氣體常數;、分別為水、CO2的平均摩爾體積;KK分別為水、氣相CO2在參比壓力下的平衡常數;Φ、Φ分別為水、CO2的逸度系數。
在互溶度計算模型的基礎上,Sun等[36]探究了H2S對水與CO2互溶度的影響,指出H2S的加入降低了水在CO2相中的溶解度,并導致溶解于CO2相中的水部分析出,且析出量隨加入H2S含量的增大而增大,當溶解水從CO2相中析出成為游離水后,CO2與H2S溶于其中并生成腐蝕性物質(如CO2(aq)、H2CO3、HCO、CO、H2S(aq)、HS-等)導致金屬腐蝕加劇,故H2S雜質的存在將加劇管道鋼在CO2相中的腐蝕。除H2S外,N2也會影響水在CO2中的溶解度,Foltran等[50]研究認為,N2的存在顯著降低了水在CO2中的溶解度,尤其是在10.21 MPa且含10% N2的情況下,水在CO2中的溶解度從4450 × 10-6下降至3400 × 10-6 (下降約30%),這將導致大量游離水析出,極大地增加了管道鋼的腐蝕風險。當前針對管內雜質對水與CO2互溶度產生影響的系統研究仍然較少,除H2S、N2外,氣態CO2輸送管道內可能存在的其他雜質(如SOx、NOx、O2等)也會對水與CO2的互溶度產生影響。此外,雜質對有水相存在的管道發生腐蝕的影響不僅取決于雜質的種類及其在CO2相中的濃度,還取決于其在CO2相與水相間的分配行為,這種分配受到CO2相態、溫度、壓力及雜質間相互作用等因素的共同影響,故針對CO2-水-雜質體系中水與CO2間及不同物質間的互溶度的測定計算應給予足夠重視并進行詳盡研究。
1.1.2 雜質對腐蝕行為及腐蝕機理的影響
CO2輸送管道內存在的雜質首先會引起CO2流體的相特性發生變化[51] (含雜質CO2的相包線如圖2[51]所示),其次,雜質通過與水相反應形成腐蝕性溶液、參與陰陽極電化學反應、改變腐蝕機理、引發局部腐蝕等作用對管道鋼腐蝕行為產生影響,當前研究多關注H2S及O2對氣態CO2輸送管道腐蝕行為及腐蝕機理的影響。H2S通常來源于天然氣開采及預燃燒過程,可直接與管道鋼發生反應生成產物膜[52] (如式(3)所示),此外,H2S的存在能夠改變水分在管道表面的吸附性質,導致管道鋼表面生成一層薄水膜,H2S溶于其中并進行水解[33] (如式(4)和(5)所示),參與管道鋼腐蝕過程。Zhang等[35]研究表明,在氣態H2S/CO2環境中,碳鋼的腐蝕速率隨CO2分壓的升高而有所增大,CO2分壓的升高導致系統中腐蝕性物質(如H2CO3、HCO、H+)濃度增大從而導致腐蝕速率增大,但整體上碳鋼的腐蝕速率隨溫度、壓力及H2S分壓的變化較小,腐蝕速率介于0.6~0.7 mm/a之間,該研究并未對發生此現象的原因及相應的腐蝕機理進行詳細地討論,H2S在氣態H2S/CO2腐蝕體系中發揮的作用還需要進一步探究。Sun等[36]研究發現,在水飽和的氣態CO2環境(50℃、5 MPa)中,H2S的加入導致碳鋼的腐蝕速率增大近3倍,其分析認為H2S主要通過發生陰極反應來參與腐蝕過程并促進腐蝕進行(如式(6)所示),此外,H2S在碳鋼表面與基體金屬發生反應生成不同類型的硫化鐵腐蝕產物(如式(7)所示),如Fe1+xS、Fe1-xS等,腐蝕產物化學成分的不均勻性導致金屬表面產物膜保護性能產生差異,從而造成金屬表面發生嚴重的局部腐蝕[53]。除H2S外,SO2也會導致管道鋼發生局部腐蝕。Farelas等[54]研究指出,少量SO2即可引起管道發生嚴重的局部腐蝕,且SO2濃度的增大將加速局部腐蝕。Dugstad等[55]進一步探究了動態條件下SO2引發的局部腐蝕,結果表明即使系統中的含水量遠低于該條件下水在CO2中的溶解度,SO2的存在仍會導致管道鋼表面發生嚴重的局部腐蝕,但其并未對SO2引起管道鋼發生局部腐蝕的機理進行細致研究。Hua等[29]通過研究也得到了類似的結論,同時,其認為局部腐蝕坑在整個腐蝕過程中的開始、發展、終止等過程亟需進行詳盡研究。
圖2 含雜質CO2的相包線[51]
管道中O2對腐蝕的影響當前仍存在爭議。一方面,O2參與陰極電化學反應(如式(8)所示)且能夠抑制FeCO3保護膜的生成(如式(9)和(10)所示),對腐蝕起到促進作用[27];另一方面,O2能夠鈍化金屬并降低金屬的均勻腐蝕速率[25,56]。Lin等[41]運用原位電化學測量技術進行了研究,認為在高溫高壓氣態CO2環境中O2與金屬發生化學反應生成Fe(OH)3,破壞了金屬表面腐蝕產物膜的完整性,導致金屬表面發生局部腐蝕且腐蝕速率較大,該研究的實驗環境壓力雖然為1 MPa,與氣態CO2輸送管道的實際工作壓力有一定差距,但原位電化學測量技術的使用為氣態CO2輸送環境下管道鋼電化學腐蝕原理的研究提供了重要參考。
總體來說,雖然針對H2S及O2對氣態CO2輸送管道腐蝕行為及腐蝕機理影響的研究已經取得了一些成果,但二者共同存在時管道鋼的腐蝕行為特點及腐蝕機理尚不明確。在超臨界CO2輸送管道腐蝕研究領域,已有眾多研究[25,27,57~59]證明多種雜質共同存在時雜質間具有協同競爭效應(如H2S、O2、SO2、NO2等),不同雜質相互作用,通過影響水與CO2的溶解度,參與化學、電化學反應,改變腐蝕產物膜組成及結構等過程影響管道鋼的腐蝕行為。此外,SO2、NO2等其他雜質也會對管道鋼的腐蝕產生顯著影響[27,30,32]。因此,仍需要通過大量且系統的基礎實驗來探究不同雜質及其相互作用對氣態CO2輸送管道腐蝕行為及腐蝕機理的影響。
1.2 環境條件對氣態CO2輸送管道腐蝕的影響
1.2.1 壓力的影響
壓力能夠對管道鋼的腐蝕產生顯著影響。壓力的變化不僅能夠影響管道表面腐蝕產物膜的生成過程,還會通過影響CO2與水的互溶度導致體系中腐蝕性物質(如H2CO3)的含量發生變化[60],從而影響腐蝕過程。Choi和Ne?i?[61]認為在CO2分壓從4 MPa上升至8 MPa的過程中,雖然在7 MPa左右時CO2的相態從氣態轉變為超臨界態,但在50℃且反應時長為24 h的情況下,碳鋼的腐蝕速率并未明顯增大。相反,Seiersten等[62]認為當CO2壓力從1 MPa上升至5.6 MPa的過程中,在40℃并反應1~2周的情況下,碳鋼的腐蝕速率出現了明顯下降。二者研究中腐蝕速率數據的不一致可能與實驗溫度、測試時間、試樣表面積與水相體積比、流動條件等因素有關。為了進一步明確氣態CO2環境中壓力變化對碳鋼腐蝕速率的影響,Choi和Ne?i?[37]通過研究發現,腐蝕可以在高壓且無游離水生成的水飽和氣態CO2環境(50℃,4 MPa、6 MPa)中發生,當溫度、壓力發生微小變化時CO2中的溶解水便凝析至碳鋼表面并迅速被CO2飽和,導致碳鋼表面生成FeCO3保護膜,且保護性能隨壓力的增大而增強。該研究提出了有關管道鋼腐蝕的新見解,強調了壓力變化對管道鋼表面產物膜的作用,且該研究的環境條件與氣態CO2輸送管道運行工況相接近,為探究壓力波動對管道鋼內腐蝕的影響提供了參考。但該研究并未考慮雜質存在時壓力對管道鋼腐蝕行為的影響,研究結論有待進一步充實。
壓力的變化也會對水與CO2的互溶度產生影響,導致不同壓力下腐蝕性物質的濃度產生差異,從而影響管道鋼的腐蝕過程。Zhang等[38]發現,相同溫度(50℃)下X65碳鋼在超臨界CO2環境(9.5 MPa)中的腐蝕速率遠大于氣態CO2環境(1 MPa),其研究指出當壓力接近CO2的臨界點時,CO2在水中的溶解度迅速增大,導致超臨界環境的水溶液中腐蝕性物質(H2CO3、HCO、CO)濃度較大,相應的陰極反應速率加快,最終導致腐蝕速率明顯增大。類似地,Wei等[40]通過計算得知,50℃時氣態環境(1 MPa)中水在CO2中的溶解度約為超臨界環境(10 MPa)中的4倍,故氣態環境中溶解于CO2中的水分較多、凝結析出的水分較少,而超臨界環境中則有更多的水凝結聚集于試樣表面,此外,超臨界環境中碳鋼表面的腐蝕性物質(CO2、H2CO3、H+)濃度遠大于氣態環境,因此,超臨界CO2環境中的碳鋼腐蝕更加嚴重。兩者的研究均指出壓力會對水與CO2的互溶度產生顯著影響并最終導致管道鋼在不同壓力下的腐蝕速率產生明顯差異,但二者研究所取壓力較為局限,壓力變化對含雜質氣態CO2輸送條件下水與CO2及雜質間互溶度的影響還需進行系統研究。
1.2.2 溫度的影響
溫度對于管道鋼腐蝕的影響主要包括2個方面:一方面,隨著系統溫度的升高,反應分子獲得更多的能量,從而更多的分子越過活化能相互碰撞,導致腐蝕速率有所增大[63];另一方面,溫度影響FeCO3的生成過程,溫度的升高導致FeCO3成核速率加快,使得管道金屬表面的腐蝕防護膜更加完整、致密且具有保護性[64]。上述2種效應共同影響腐蝕速率,即在腐蝕產物膜生成前,高溫下金屬的腐蝕速率較大,然而當腐蝕產物膜生成后,高溫下金屬的腐蝕速率反而較小。Zhang等[38]研究指出,在氣態CO2環境中,隨著溫度的上升,X65碳鋼的腐蝕速率先增大后減小,而表面的腐蝕產物膜厚度逐漸減小,其分析認為溫度越高,FeCO3的過飽和度及沉積速率越大,導致高溫時腐蝕產物膜生成更加迅速且更加致密,保護性能更好,故高溫時碳鋼的腐蝕速率較低。此外,雖然低溫時腐蝕產物膜更厚,但其表面的孔狀缺陷更多,保護性能較差。該研究闡明了溫度通過影響管道鋼表面產物膜厚度及結構進而影響管道鋼的腐蝕速率,為探明溫度對氣態CO2輸送管道腐蝕行為的影響提供了研究思路。總體上,針對溫度對氣態CO2輸送管道腐蝕行為影響的研究還比較少,溫度變化對含雜質氣態CO2輸送系統中CO2與水的互溶度、管道鋼表面產物膜及腐蝕機理等因素的影響還需進行大量基礎實驗研究。
1.2.3 其他條件的影響
除壓力、溫度外,其他條件(如暴露角度、腐蝕反應時間、所處介質、流速等)對管道鋼的腐蝕行為也會產生不同程度的影響。在氣態CO2的輸送過程中,由于輸送溫度及壓力的波動,水分將凝結于管壁上,此過程可分為2種[65]:水分在側壁凝結并在重力的作用下滑落至管底;水分凝結并吸附于管頂,故暴露角度可對管道腐蝕產生明顯影響[66]。Wei等[40]研究表明,在氣態CO2環境中,液滴可以隨機地分布于水平放置的試樣表面,但難以附著于垂直的試樣表面,只能少量地聚集于垂直試樣的底部邊緣,故垂直放置的試樣腐蝕速率最小,水平放置的試樣腐蝕速率較大,該研究為氣態CO2輸送管道內部不同位置的腐蝕情況判斷提供了參考。
腐蝕反應時間的長短對管道鋼表面腐蝕產物膜的生成及結構變化產生顯著影響,腐蝕產物膜厚度、結構及致密程度等特征決定了管道鋼耐腐蝕的程度,即決定了管道鋼腐蝕速率的大小[67]。Liu等[42]研究認為,在含飽和水的氣態CO2環境中,低合金鋼的腐蝕速率隨腐蝕反應時間的延長先增大后減小,當反應時間為96 h時,金屬表面開始出現FeCO3晶體,且腐蝕速率達到最大值。總體上,腐蝕產物膜在金屬表面的覆蓋面積隨反應時間的延長由小變大,并最終形成一層完整的腐蝕產物膜。該研究為探究氣態CO2輸送管道內表面腐蝕產物膜隨服役時間延長的變化提供了研究思路,但該研究條件較為局限,含雜質條件下反應時間對氣態CO2輸送管道內表面腐蝕產物膜的影響及對管道鋼腐蝕速率的影響有待進一步研究。
管道鋼所處介質不同,則腐蝕反應類型及腐蝕機理也不同[68],管道內存在的離子將對管道鋼腐蝕電化學過程及腐蝕機理產生影響[69]。Almeida等[39]運用原位電化學測量技術研究指出,在24℃、3 MPa的氣態CO2環境中,X65碳鋼在CO2飽和鹽溶液中的腐蝕速率約為蒸餾水中的3倍,其分析認為鹽溶液中的pH值影響了CO2與Fe2+發生反應的類型及過程,從而影響了腐蝕反應的動力學平衡,導致腐蝕速率有所增大。該研究并未對腐蝕反應后金屬的表面形貌及腐蝕產物進行分析,但在氣態CO2管道內表面腐蝕反應類型及原理研究方面提出了新的見解。Liu等[70]研究了Cl-在管道鋼腐蝕過程中發揮的作用,結果表明在氣態CO2環境中,N80碳鋼的腐蝕速率隨Cl-含量的增加先增大后減小,在到達最大值之前,Cl-含量的增加導致腐蝕電流密度有所增大并加快了陽極反應速率,促進了腐蝕進行;然而,在到達最大值之后,Cl-含量的增加顯著降低了溶液中CO2的溶解度并降低了H+、H2O、H2CO3、HCO
等物質參與腐蝕反應的可能性,導致腐蝕速率有所降低。該研究闡釋了Cl-在管道鋼腐蝕過程中對腐蝕電化學反應及腐蝕反應物質參與腐蝕過程的影響,研究過程中電化學測量技術的使用為探究氣態CO2管道中雜質離子對管道鋼腐蝕行為及電化學腐蝕機理的作用提供了寶貴借鑒。
流動條件的改變將對管道鋼表面腐蝕產物膜產生直接影響。流速的變化將導致腐蝕產物膜的結構、致密程度、對金屬的保護性能等特性產生明顯差異,從而影響管道鋼的腐蝕行為[71]。劉丹[72]詳盡研究了氣態CO2輸送條件(60℃、5 MPa)下流速對N80碳鋼腐蝕行為及腐蝕機理的影響,指出流動加速了腐蝕反應的傳質過程,從而加速了陰極反應進程和腐蝕產物的脫落,導致管道鋼的腐蝕速率較靜態條件有所增大。此外,流動還能導致管道鋼發生局部腐蝕[73],Schmitt和Mueller[74]研究指出,如果流體臨界流動強度抑制了保護性腐蝕產物膜的再生,局部腐蝕就會在腐蝕產物膜局部破裂剝落的部位發生。在此基礎上,魏亮[75]詳盡研究了局部腐蝕過程中腐蝕產物膜在腐蝕坑內的演變過程,認為流動產生壁面剪切力的大小及局部腐蝕坑尺寸的大小決定了局部腐蝕坑內FeCO3保護膜能否再生,從而決定了局部腐蝕是否加劇。雖然當前已初步明確流動對CO2輸送管道鋼腐蝕產生了一些影響,但針對氣態CO2輸送環境中流動對管道鋼腐蝕造成影響的研究仍鮮有報道,故需要進行大量基礎實驗研究以明確流動條件下含雜質氣態CO2環境中管道鋼的腐蝕行為及腐蝕機理,從而為氣態CO2輸送管道的實際運行提供理論依據。
不同金屬材料的耐腐蝕性能也有明顯差異[76]。Hassani等[43]研究認為,在60℃、3 MPa的CO2飽和鹽溶液中金屬的耐腐蝕性由好到差依次為:13Cr鋼、5Cr鋼、碳鋼,腐蝕過程中雖然碳鋼及5Cr鋼表面生成的腐蝕產物膜較厚,但由于其多孔且附著性較差,導致碳鋼及5Cr鋼的腐蝕速率仍然較大,而13Cr鋼表面生成一層薄而緊實且附著性良好的鈍化膜,為13Cr鋼提供了良好的防護并顯著降低了13Cr鋼的腐蝕速率。該研究結合三電極原位電化學測量技術全面探究了氣態CO2環境下鹽溶液中金屬的耐腐蝕性能,為氣態CO2輸送管道鋼選擇提供了重要參考。
總體來說,當前有關氣態CO2輸送條件下管道鋼腐蝕的實驗及現場數據較少,不同環境條件下含雜質氣態CO2輸送管道的腐蝕行為及腐蝕機理需要進一步系統研究。
2 氣態CO2輸送管道臨界含水量研究
在CO2的實際管道輸送過程中,在輸送前需對所輸CO2流體進行脫水處理以避免管道內出現游離水導致管道發生腐蝕。美國現存CO2輸送管道對于含水量的要求十分嚴格,要求含水量低于50 × 10-6,即通常被認為是全脫水輸送[18]。李玉星等[77]歸納了富CO2輸送管道不發生腐蝕的最大含水量與壓力、溫度的關系(圖3[77]),并認為設定最高操作壓力下的露點要求并不安全。一般地,對于操作溫度高于4℃的純CO2輸送管道,避免發生腐蝕的含水量為(300~500) × 10-6 [78~80]。此外,Visser等[78]基于DYNAMIS規范認為CO2輸送管道的含水量上限在(20~630) × 10-6,顯然,將CO2輸送管道中的含水量降低至很低的數值是不必要且不經濟的,故需要根據管道運行的溫度、壓力及所含雜質來確定一個合理、經濟的臨界含水量,但當前還不存在針對CO2輸送管道最大含水量的國際共識。McGrail等[79]首先探究了22℃、6.25 MPa的氣態CO2環境中不同含水率下X70碳鋼的腐蝕行為,結果表明,經過72 h的腐蝕反應,在含水率為90%RH (相對濕度)的環境中碳鋼表面形成了腐蝕防護膜,然而,在含水率為55%RH的環境中,碳鋼經過42 d的反應也并未發生腐蝕,故其認為此條件下的臨界含水率介于55%RH與90%RH之間。在此基礎上,針對氣態CO2輸送管道,Jiang等[44]研究表明在游離水相出現前,X65碳鋼的均勻腐蝕速率不隨相對濕度的增加而變化,但當游離水出現后,均勻腐蝕速率明顯增大,如在溫度、壓力分別為35℃、4 MPa且存在游離水的情況下,X65碳鋼發生了嚴重的均勻腐蝕并出現了局部腐蝕,研究認為氣態CO2輸送管道不發生腐蝕的臨界含水率為80%RH。上述研究為氣態CO2輸送管道臨界含水量的確定提供了參考,但管道內可能存在的其他雜質(如SOx、NOx、O2、H2S、N2等)也會導致管道發生腐蝕,雜質種類及含量的變化將改變水與CO2的互溶度,從而影響水的凝結析出及管內腐蝕物質的濃度。此外,溫度、壓力的波動也將影響溶于CO2相中水分的析出。總體上,溫度、壓力及雜質將對氣態CO2輸送管道臨界含水量的確定產生重要影響,然而當前針對含雜質氣態CO2輸送管道臨界含水量的研究仍然較少,故需要對不同條件下含雜質氣態CO2輸送管道的臨界含水量進行大量的系統實驗研究,以確定合理的臨界含水量,從而保證氣態CO2輸送管道的經濟、安全運行。
圖3 富CO2輸送管道最大含水量與壓力、溫度的關系圖[77]
3 氣態CO2輸送管道腐蝕預測模型
基于物理化學過程的腐蝕預測模型的開發是腐蝕科學技術領域的研究熱點之一,模型可以幫助工程師判別腐蝕問題,從而做出與腐蝕防護相關的決策[81]。由于腐蝕問題與油氣井、管道及其他設備的安全運行密切相關,故腐蝕預測對于油氣工業生產尤為重要。CO2腐蝕是油氣工業中最常見的腐蝕類型,最早的CO2腐蝕模型由DeWaard與Milliams[48]于1975年提出,隨著CO2腐蝕受到越來越多的關注,更多的CO2腐蝕預測模型被提出且被研究者進行了很好的總結歸納[82]。盡管目前有多種CO2腐蝕預測模型[83~85],但其絕大多數僅能應用于CO2分壓范圍為0~2 MPa的油氣生產環境,當模型應用于更高分壓的CO2環境時,腐蝕速率預測值大多比實驗值高一個數量級[86,87],預測結果并不準確,而產生上述差異的根本原因是高分壓CO2環境中水化學及腐蝕機理特性與低分壓CO2環境有所不同。隨著CCS技術的不斷發展,高壓CO2輸送管道腐蝕預測也得到了廣泛關注,當前高壓CO2腐蝕預測模型研究已取得一些成果[88,89],其中,可應用于氣態CO2輸送管道的腐蝕速率預測模型如表2[90~96]所示。
表2 適用于氣態CO2輸送管道的腐蝕速率預測模型[90~96]
在低壓CO2管道腐蝕速率預測模型的基礎上,Choi等[97]對模型進行改進并提出了高壓CO2環境(0~14 MPa、0~80℃)中低碳鋼腐蝕速率預測模型,模型使用Spycher模型[49]及Duan模型[98,99]計算CO2的溶解度,運用H2CO3的Langmuir吸附等溫式[100]改進了電化學模型描述,模型計算得到的腐蝕速率與實驗數據吻合較好,且為高壓氣態CO2輸送管道腐蝕速率預測提供了模型改進參考。井筒系統(wellbore systems)用于隔離地下流體[101~103],需要在高溫、高壓、高含鹽、高含CO2的CO2封存環境中保持自身的完整性。Han等[104]結合Pitzer基礎水化學模型[105]與經典電化學模型[106]提出了應用于井筒系統的低碳鋼腐蝕速率預測模型,模型適用的溫度范圍為0~100℃、CO2分壓范圍為0.1~100 MPa,該模型計算范圍廣泛,為氣態CO2輸送管道腐蝕速率預測提供了借鑒,然而,此模型未考慮金屬表面生成的腐蝕產物膜對腐蝕速率的影響。腐蝕產物膜對腐蝕速率及產生局部腐蝕傾向的影響有待于進一步研究。針對CCS過程中的其他環節,也提出了一些腐蝕速率預測模型。Li等[107]建立了CO2封存條件下碳鋼的腐蝕速率預測模型,該模型綜合了多種子模型以量化相關腐蝕過程對腐蝕速率的作用,模型應用范圍廣泛,可實現氣態CO2輸送條件下管道的腐蝕速率預測,但其可靠性與可應用性在很大程度上依賴于現有的研究數據,故需要更廣泛的現場及實驗數據來驗證模型的準確性。總體來說,雖然目前存在的一些腐蝕速率預測模型可應用于氣態CO2輸送管道,但預測結果的精確程度并不能保證。當前針對氣態CO2輸送管道腐蝕速率預測模型的研究鮮有報道,氣態CO2輸送管道內可能存在的多種雜質間的相互作用決定了腐蝕機理的復雜性,導致腐蝕速率預測變得困難,而腐蝕速率預測對于管道的安全運行及完整性管理尤為重要,因此,氣態CO2輸送管道腐蝕速率預測模型的建立成為一項亟待解決的科學問題。
4 研究展望
目前針對含雜質氣態CO2輸送管道腐蝕的研究仍然較少,在雜質對腐蝕機理的影響、臨界含水量的確定、腐蝕模型的發展等方面仍存在一定的局限性。氣態CO2輸送環境下管道腐蝕研究亟待解決的科學問題和研究展望如下:
(1) 當前針對含雜質(H2O、N2、O2、NOx、SOx、H2S等)氣態CO2環境中水與CO2互溶度的計算研究較少,需進一步探究不同種類雜質對水與CO2互溶度的影響。
(2) 氣態CO2輸送環境下雜質間的協同競爭作用以及雜質對腐蝕產物膜特征及腐蝕機理的影響需要深入研究。
(3) 動態條件下含雜質氣態CO2環境中管道鋼的局部腐蝕行為及局部腐蝕機理需要系統研究。
(4) 目前在高壓且含微量水的環境中開展原位電化學測試十分困難,亟需確定含雜質氣態CO2環境中電化學測試規范以準確解釋氣態CO2輸送管道的腐蝕電化學機理。
(5) 建立含雜質氣態CO2輸送管道腐蝕產物膜的評價規范并量化腐蝕產物膜的生成、發展過程及對管道鋼的保護作用。
(6) 確定保證含雜質氣態CO2輸送管道不發生腐蝕的臨界含水量,為CO2管道輸送前的脫水環節提供經濟可行的參考。
(7) 當前存在的氣態CO2管道腐蝕模型仍然不夠精確,需要建立針對含雜質氣態CO2輸送條件下的管道內腐蝕預測模型,以指導管道安全運行,推動我國CCS技術的發展與應用。
參考文獻
1 Hekkert M P, Joosten L A J, Worrell E, et al. Reduction of CO2 emissions by improved management of material and product use: The case of primary packaging [J]. Resour. Conserv. Recy., 2000, 29: 33
2 Wang C L, Li Y X, Teng L, et al. Experimental study on dispersion behavior during the leakage of high pressure CO2 pipelines [J]. Exp. Therm. Fluid Sci., 2019, 105: 77
3 IPCC. Carbon Dioxide Capture and Storage [M]. New York: Cambridge University Press, 2005: 1
4 Czernichowski-Lauriol I, Berenblyum R, Bigi S, et al. CO2 GeoNet actions in Europe for advancing CCUS through global cooperation [J]. Energy Procedia, 2018, 154: 73
5 Bhave A, Taylor R H S, Fennell P, et al. Screening and techno-economic assessment of biomass-based power generation with CCS technologies to meet 2050 CO2 targets [J]. Appl. Energy, 2017, 190: 481
6 Reiner D M. Learning through a portfolio of carbon capture and storage demonstration projects [J]. Nat. Energy, 2016, 1: 15011
7 Gibbins J, Chalmers H. Carbon capture and storage [J]. Energy Policy, 2008, 36: 4317
8 Lilliestam J, Bielicki J M, Patt A G. Comparing carbon capture and storage (CCS) with concentrating solar power (CSP): Potentials, costs, risks, and barriers [J]. Energy Policy, 2012, 47: 447
9 Gale J, Davison J. Transmission of CO2-safety and economic considerations [J]. Energy, 2004, 29: 1319
10 Boot-Handford M E, Abanades J C, Anthony E J, et al. Carbon capture and storage update [J]. Energy Environ. Sci., 2014, 7: 130
11 Kruse H, Tekiela M. Calculating the consequences of a CO2-pipeline rupture [J]. Energy Convers. Manage, 1996, 37: 1013
12 Liu Z G, Gao X H, Li J P, et al. Corrosion behaviour of low-alloy martensite steel exposed to vapour-saturated CO2 and CO2-saturated brine conditions [J]. Electrochim. Acta, 2016, 213: 842
13 Wang C L, Gu S W, Li Y X, et al. Experimental study on foaming characteristics of CO2-crude oil mixture [J]. CIESC J., 2019, 70: 251
13 王財林, 顧帥威, 李玉星等. CO2-原油體系發泡特性實驗研究 [J]. 化工學報, 2019, 70: 251
14 Lovseth S W, Skaugen G, Stang H G J, et al. CO2 mix project: Experimental determination of thermo physical properties of CO2-rich mixtures [J]. Energy Procedia, 2013, 37: 2888
15 Vandeginste V, Piessens K. Pipeline design for a least-cost router application for CO2 transport in the CO2 sequestration cycle [J]. Int. J. Greenhouse Gas Control, 2008, 2: 571
16 Barker R, Hua Y, Neville A. Internal corrosion of carbon steel pipelines for dense-phase CO2 transport in carbon capture and storage (CCS)—A review [J]. Int. Mater. Rev., 2017, 62: 1
17 Lone S, Cockerill T, Macchietto S. The techno-economics of a phased approach to developing a UK carbon dioxide pipeline network [J]. J. Pipeline Eng., 2010, 9: 225
18 Sandana D, Hadden M, Race J, et al. Transport of gaseous and dense carbon dioxide in pipelines: is there an internal corrosion risk? [J]. J. Pipeline Eng., 2012, 11: 229
19 Qi G L. Research on CO2 pipeline and liquid separation project of Qilu Petrochemical to Zhenglizhuang oilfield [D]. Qingdao: China University of Petroleum (East China), 2014
19 亓冠玲. 齊魯二化廠至正理莊油田高89地區CO2輸送管道及液化分離工程方案研究 [D]. 青島: 中國石油大學(華東), 2014
20 Xie S X, Han P H, Qian Y. A pilot test and research on oil displacement by injecting CO2 in eastern Sanan of Daqing oilfield [J]. Oil Gas Recov. Technol., 1997, 4(3): 13
20 謝尚賢, 韓培慧, 錢 昱. 大慶油田薩南東部過渡帶注CO2驅油先導性礦場試驗研究 [J]. 油氣采收率技術, 1997, 4(3): 13
21 Division of Social Development Science and Technology, Ministry of Science and Technology Development, Department of International Cooperation, Ministry of Science and Technology, China Agenda 21 Management Center. Carbon capture, utilization and storage technology development in China [R]. Beijing, 2011
21 科學技術部社會發展科技司, 科學技術部國際合作司, 中國21世紀議程管理中心. 中國碳捕集、利用與封存(CCUS)技術進展報告 [R]. 北京, 2011
22 Johnson K, Holt H, Helle K, et al. Mapping of potential HSE issues related to large-scale capture, transport and storage of CO2 [R]. Horvik: Det Norsk Veritas, 2008
23 Choi Y S, Nesic S, Young D. Effect of impurities on the corrosion behavior of CO2 transmission pipeline steel in supercritical CO2-water environments [J]. Environ. Sci. Technol., 2010, 44: 9233
24 Sim S, Cole I S, Bocher F, et al. Investigating the effect of salt and acid impurities in supercritical CO2 as relevant to the corrosion of carbon capture and storage pipelines [J]. Int. J. Greenhouse Gas Control, 2013, 17: 534
25 Sun C, Sun J B, Wang Y, et al. Synergistic effect of O2, H2S and SO2 impurities on the corrosion behavior of X65 steel in water-saturated supercritical CO2 system [J]. Corros. Sci., 2016, 107: 193
26 Hua Y, Barker R, Neville A. The effect of O2 content on the corrosion behaviour of X65 and 5Cr in water-containing supercritical CO2 environments [J]. Appl. Surf. Sci., 2015, 356: 499
27 Sun J B, Sun C, Wang Y. Effects of O2 and SO2 on water chemistry characteristics and corrosion behavior of X70 pipeline steel in supercritical CO2 transport system [J]. Ind. Eng. Chem. Res., 2018, 57: 2365
28 Xiang Y, Wang Z, Xu C, et al. Impact of SO2 concentration on the corrosion rate of X70 steel and iron in water-saturated supercritical CO2 mixed with SO2 [J]. J. Supercrit. Fluids, 2011, 58: 286
29 Hua Y, Barker R, Neville A. The influence of SO2 on the tolerable water content to avoid pipeline corrosion during the transportation of supercritical CO2 [J]. Int. J. Greenhouse Gas Control, 2015, 37: 412
30 Sun C, Sun J B, Wang Y, et al. Effect of impurity interaction on the corrosion film characteristics and corrosion morphology evolution of X65 steel in water-saturated supercritical CO2 system [J]. Int. J. Greenhouse Gas Control, 2017, 65: 117
31 Hua Y, Jonnalagadda R, Zhang L, et al. Assessment of general and localized corrosion behavior of X65 and 13Cr steels in water-saturated supercritical CO2 environments with SO2/O2 [J]. Int. J. Greenhouse Gas Control, 2017, 64: 126
32 Hua Y, Neville A, Barker R. Corrosion behaviour of X65 steels in water-containing supercritical CO2 environments with NO2/O2 [A]. NACE Corrosion 2018 Conference and Expo. 2018 [C]. Phoenix: National Association of Corrosion Engineers, 2018: 11085
33 Wei L, Pang X L, Gao K W. Effect of small amount of H2S on the corrosion behavior of carbon steel in the dynamic supercritical CO2 environments [J]. Corros. Sci., 2016, 103: 132
34 Yu C, Wang H W, Gao X H. Corrosion behavior of carbon steel with pearlite-ferrite microstructure in water-saturated supercritical H2S/CO2 environment [J]. Int. J. Electrochem. Sci., 2018, 13: 6059
35 Zhang G A, Zeng Y, Guo X P, et al. Electrochemical corrosion behavior of carbon steel under dynamic high pressure H2S/CO2 environment [J]. Corros. Sci., 2012, 65: 37
36 Sun C, Sun J B, Luo J L. Unlocking the impurity-induced pipeline corrosion based on phase behavior of impure CO2 streams [J]. Corros. Sci., 2020, 165: 108367
37 Choi Y S, Ne?i? S. Determining the corrosive potential of CO2 transport pipeline in high pCO2-water environments [J]. Int. J. Greenhouse Gas Control, 2011, 5: 788
38 Zhang Y C, Pang X L, Qu S P, et al. Discussion of the CO2 corrosion mechanism between low partial pressure and supercritical condition [J]. Corros. Sci., 2012, 59: 186
39 Almeida T D C, Bandeira M C E, Moreira R M, et al. New insights on the role of CO2 in the mechanism of carbon steel corrosion [J]. Corros. Sci., 2017, 120: 239
40 Wei L, Pang X L, Zhou M, et al. Effect of exposure angle on the corrosion behavior of X70 steel under supercritical CO2 and gaseous CO2 environments [J]. Corros. Sci., 2017, 121: 57
41 Lin X Q, Liu W, Wu F, et al. Effect of O2 on corrosion of 3Cr steel in high temperature and high pressure CO2-O2 environment [J]. Appl. Surf. Sci., 2015, 329: 104
42 Liu Z G, Gao X H, Du L X, et al. Corrosion behavior of low-alloy steel with martensite/ferrite microstructure at vapor-saturated CO2 and CO2-saturated brine conditions [J]. Appl. Surf. Sci., 2015, 351: 610
43 Hassani S, Vu T N, Rosli N R, et al. Wellbore integrity and corrosion of low alloy and stainless steels in high pressure CO2 geologic storage environments: An experimental study [J]. Int. J. Greenhouse Gas Control, 2014, 23: 30
44 Jiang X, Qu D R, Song X L, et al. Critical water content for corrosion of X65 mild steel in gaseous, liquid and supercritical CO2 stream [J]. Int. J. Greenhouse Gas Control, 2019, 85: 11
45 Jiang X, Qu D R, Song X L, et al. Impact of water content on corrosion behavior of CO2 transportation pipeline [A]. NACE Corrosion 2015 Conference and Expo. 2015 [C]. Dallas: NACE International, 2015: 5844
46 Russick E M, Poulter G A, Adkins C L J, et al. Corrosive effects of supercritical carbon dioxide and cosolvents on metals [J]. J. Supercrit. Fluids, 1996, 9: 43
47 Zhang Y C, Gao K W, Schmitt G. Effect of water on steel corrosion under supercritical CO2 conditions [J]. Mater. Performance, 2011, 50: 62
48 DeWaard C, Milliams D E. Prediction of carbonic acid corrosion in natural gas pipelines [A]. First International Conference on the Internal and External Protection of Pipes [C]. UK: University of Durham, 1975: 28
49 Spycher K, Pruess K, Ennis-King J. CO2-H2O mixtures in the geological sequestration of CO2. I. Assessment and calculation of mutual solubilities from 12 to 1000oC and up to 600 bar [J]. Geochim. Cosmochim. Acta, 2003, 67: 3015
50 Foltran S, Vosper M E, Suleiman N B, et al. Understanding the solubility of water in carbon capture and storage mixtures: An FTIR spectroscopic study of H2O+CO2 +N2 ternary mixtures [J]. Int. J. Greenhouse Gas Control, 2015, 35: 131
51 Gu S W, Teng L, Li Y X, et al. Propagation characteristic of decompression wave for gaseous CO2 in pipeline containing impurities [J]. Petrochem. Technol., 2018, 47: 689
51 顧帥威, 滕 霖, 李玉星等. 含雜質氣態CO2管道減壓波傳播特性 [J]. 石油化工, 2018, 47: 689
52 Zeng Y M, Arafin M, Shi C, et al. Influence of impurity hydrogen sulfide on the corrosion performance of pipeline steels in supercritical carbon dioxide stream [A]. NACE Corrosion 2016 Conference and Expo. 2016 [C]. Vancouver: NACE International, 2016: 7223
53 Wei L, Pang X L, Gao K W. Corrosion of low alloy steel and stainless steel in supercritical CO2/H2O/H2S systems [J]. Corros. Sci., 2016, 111: 637
54 Farelas F, Choi Y S, Nesic S. Corrosion behavior of API 5L X65 carbon steel under supercritical and liquid CO2 phases in the presence of H2O and SO2 [J]. Corrosion, 2013, 69: 243
55 Dugstad A, Halseid M, Morland B. Effect of SO2 and NO2 on corrosion and solid formation in dense phase CO2 pipelines [J]. Energy Procedia, 2013, 37: 2877
56 Tang Y, Guo X P, Zhang G A. Corrosion behaviour of X65 carbon steel in supercritical-CO2 containing H2O and O2 in carbon capture and storage (CCS) technology [J]. Corros. Sci., 2017, 118: 118
57 Sun J B, Sun C, Zhang G A, et al. Effect of O2 and H2S impurities on the corrosion behavior of X65 steel in water-saturated supercritical CO2 system [J]. Corros. Sci., 2016, 107: 31
58 Sun C, Sun J B, Liu S B, et al. Effect of water content on the corrosion behavior of X65 pipeline steel in supercritical CO2-H2O-O2-H2S-SO2 environment as relevant to CCS application [J]. Corros. Sci., 2018, 137: 151
59 Hua Y, Barker R, Neville A. Understanding the influence of SO2 and O2 on the corrosion of carbon steel in water-saturated supercritical CO2 [J]. Corrosion, 2015, 71: 667
60 Xiang Y, Xu M H, Choi Y S. State-of-the-art overview of pipeline steel corrosion in impure dense CO2 for CCS transportation: Mechanisms and models [J]. Corros. Eng. Sci. Technol., 2017, 52: 485
61 Choi Y S, Ne?i? S. Corrosion behavior of carbon steel in supercritical CO2-water environments [A]. NACE Corrosion 2009 Conference and Expo. 2009 [C]. Atlanta: NACE International, 2009: 09256
62 Seiersten M. Materials selection for separation, transportation and disposal of CO2 [A]. NACE Corrosion 2001 Conference and Expo. 2001 [C]. Houston: NACE International, 2001: 01042
63 Tan J, Chan K S. Understanding Advanced Physical Inorganic Chemistry: The Learner's Approach [M]. Singapore: World Scientific Publishing Company, 2010: 1
64 Dugstad A. Fundamental aspects of CO2 metal loss corrosion, part I: mechanism [A]. NACE Corrosion 2006 Conference and Expo. 2006 [C]. San Diego: NACE International, 2006: 6111
65 Zhang Z, Hinkson D, Singer M, et al. A mechanistic model of top-of-the-line corrosion [J]. Corrosion, 2007, 63: 1051
66 Qu S P, Li X, Gao K W, et al. The effect of exposure angle on the corrosion behavior of low-carbon microalloyed steel under CO2 conditions [J]. Corrosion, 2015, 71: 343
67 Zhang J, Wang Z L, Wang Z M, et al. Chemical analysis of the initial corrosion layer on pipeline steels in simulated CO2-enhanced oil recovery brines [J]. Corros. Sci., 2012, 65: 397
68 Tran T, Brown B, Nesic S. Corrosion of mild steel in an aqueous CO2 environment—Basic electrochemical mechanisms revisited [A]. NACE Corrosion 2015 Conference and Expo. 2015 [C]. Dallas: NACE International, 2015: 5671
69 Ma H Y, Yang C, Li G Y, et al. Influence of nitrate and chloride ions on the corrosion of iron [J]. Corrosion., 2003, 59: 1112
70 Liu Q Y, Mao L J, Zhou S W. Effects of chloride content on CO2 corrosion of carbon steel in simulated oil and gas well environments [J]. Corros. Sci., 2014, 84: 165
71 Gao K W, Yu F, Pang X L, et al. Mechanical properties of CO2 corrosion product scales and their relationship to corrosion rates [J]. Corros. Sci., 2008, 50: 2796
72 Liu D. Corrosion behavior of carbon steel under dynamic supercritical CO2 environment [D]. Wuhan: Huazhong University of Science and Technology, 2015
72 劉 丹. 動態條件下碳鋼在超臨界CO2環境中腐蝕機理研究 [D]. 武漢: 華中科技大學, 2015
73 Nesic S, Wang S H, Cai J Y, et al. Integrated CO2 corrosion-multiphase flow model [A]. SPE International Symposium on Oilfield Corrosion [C]. Aberdeen: Society of Petroleum Engineers, 2004: 87555
74 Schmitt G A, Mueller M. Critical wall shear stresses in CO2 corrosion of carbon steel [A]. NACE Corrosion 1999 Conference [C]. San Antonio: NACE International, 1999: 44
75 Wei L. Study of corrosion mechanism of steels in supercritical CO2 environments [D]. Beijing: University of Science and Technology Beijing, 2016
75 魏 亮. 鋼在超臨界CO2環境中腐蝕機制的研究 [D]. 北京: 北京科技大學, 2016
76 Pfennig A, Kranzmann A. Effect of CO2 and pressure on the stability of steels with different amounts of chromium in saline water [J]. Corros. Sci., 2012, 65: 441
77 Li Y X, Liu M S, Zhang J. Impacts of gas impurities on the security of CO2 pipelines [J]. Nat. Gas Ind., 2014, 34: 108
77 李玉星, 劉夢詩, 張 建. 氣體雜質對CO2管道輸送系統安全的影響 [J]. 天然氣工業, 2014, 34: 108
78 De Visser E, Hendriks C, Barrio M, et al. DYNAMIS CO2 quality recommendations [J]. Int. J. Greenhouse Gas Control, 2008, 2: 478
79 McGrail B P, Schaef H T, Glezakou V A, et al. Water reactivity in the liquid and supercritical CO2 phase: Has half the story been neglected? [J]. Energy Procedia, 2009, 1: 3415
80 Mohitpour M, Golshan H, Murray A. Pipeline Design & Construction: A Practical Approach [M]. 2nd Ed., New York: American Society of Mechanical Engineers, 2003
81 Ne?i? S. Key issues related to modelling of internal corrosion of oil and gas pipelines—A review [J]. Corros. Sci., 2007, 49: 4308
82 Nyborg R. Overview of CO2 corrosion models for wells and pipelines [A]. NACE Corrosion 2002 Conference and Expo. 2002 [C]. Denver: NACE International, 2002: 2233
83 Nordsveen M, Ne?i? S, Nyborg R, et al. A mechanistic model for carbon dioxide corrosion of mild steel in the presence of protective iron carbonate films—Part 1: Theory and verification [J]. Corrosion, 2003, 59: 443
84 Ne?i? S, Nordsveen M, Nyborg R, et al. A mechanistic model for carbon dioxide corrosion of mild steel in the presence of protective iron carbonate films—Part 2: A numerical experiment [J]. Corrosion, 2003, 59: 489
85 Ne?i? S, Lee K L J. A mechanistic model for carbon dioxide corrosion of mild steel in the presence of protective iron carbonate films—Part 3: Film growth model [J]. Corrosion, 2003, 59: 616
86 Zhang Y, Gao K, Schmitt G, et al. Modeling steel corrosion under supercritical CO2 conditions [J]. Mater. Corros., 2013, 64: 478
87 Kongshaug K O, Seiersten M. Baseline experiments for the modeling of corrosion at high CO2 pressure [A]. NACE Corrosion 2004 Conference and Expo. 2004 [C]. New Orleans: NACE International, 2004: 4630
88 Thomas D C. Carbon Dioxide Capture for Storage in Deep Geologic Formations [M]. 2nd Ed., Amsterdam: Elsevier Science Ltd, 2005: 937
89 Xiang Y, Wang Z, Xu M H, et al. A mechanistic model for pipeline steel corrosion in supercritical CO2-SO2-O2-H2O environments [J]. J. Supercrit. Fluids, 2013, 82: 1
90 Gunaltun Y M. Combining research and field data for beorrosion rate prediction [A]. NACE Corrosion 1996 Conference [C]. Denver: NACE International, 1996: 96027
91 Nesic S, Nordsveen M, Nyborg R, et al. A mechanistic model for CO2 corrosion with protective iron carbonate films [A]. NACE Corrosion 2001 Conference and Expo. 2001 [C]. Houston: NACE International, 2001: 01040
92 Srinivasan S, Kane R D. Prediction of corrosivity of CO2/H2S production environments [A]. NACE Corrosion 1996 Conference [C]. Denver: NACE International, 1996: 11
93 Srinivasan S, Tebbal S. Critical factors in predicting CO2/H2S corrosion in multiphase systems [A]. NACE Corrosion 1998 Conference [C]. San Diego: NACE International, 1998: 38
94 John R C, Jordan K G, Kapusta S D, et al. SweetCor: an information system for the analysis of corrosion of steels by water and carbon dioxide [A]. NACE Corrosion 1998 Conference [C]. San Diego: NACE International, 1998: 20
95 Anderko A M, Young R D. Simulation of CO2/H2S corrosion using thermodynamic and electrochemical models [A]. NACE Corrosion 1999 Conference [C]. San Antonio: NACE International, 1999: 31
96 Anderko A M. Simulation of FeCO3/FeS scale formation using thermodynamic and electrochemical models [A]. NACE Corrosion 2002 Conference [C]. Orlando: NACE International, 2002: 102
97 Choi Y S, Hassani S, Vu T N, et al. Development of a prediction model for high pCO2 corrosion of mild steel [A]. NACE Corrosion 2019 Conference and Expo. 2019 [C]. Nashville: NACE International, 2019: 13157
98 Duan Z H, Sun R. An improved model calculating CO2 solubility in pure water and aqueous NaCl solutions from 273 to 533 K and from 0 to 2000 bar [J]. Chem. Geol., 2003, 193: 257
99 Duan Z H, Sun R, Zhu C, et al. An improved model for the calculation of CO2 solubility in aqueous solutions containing Na+, K+, Ca2+, Mg2+, Cl-, and SO42- [J]. Mar. Chem., 2006, 98: 131
100 Langmuir I. The adsorption of gases on plane surfaces of glass, mica and platinum [J]. J. Am. Chem. Soc., 1918, 40: 1361
101 Carey J W, Wigand M, Chipera S J, et al. Analysis and performance of oil well cement with 30 years of CO2 exposure from the SACROC Unit, West Texas, USA [J]. Int. J. Greenhouse Gas Control, 2007, 1: 75
102 Carey J W, Svec R, Grigg R, et al. Experimental investigation of wellbore integrity and CO2-brine flow along the casing-cement microannulus [J]. Int. J. Greenhouse Gas Control, 2010, 4: 272
103 Crow W, Williams D B, Carey J W, et al. Wellbore integrity analysis of a natural CO2 producer [J]. Energy Procedia, 2009, 1: 3561
104 Han J B, Carey J W, Zhang J S. A coupled electrochemical-geochemical model of corrosion for mild steel in high-pressure CO2-saline environments [J]. Int. J. Greenhouse Gas Control, 2011, 5: 777
105 Pitzer K S. Activity Coefficients in Electrolyte Solutions [M]. 2nd Ed., Boston: CRC Press, 1991: 75
106 Nesic S, Postlethwaite J, Olsen S. An electrochemical model for prediction of corrosion of mild steel in aqueous carbon dioxide solutions [J]. Corrosion, 1996, 52: 280
107 Li Q, Cheng Y F. Modeling of corrosion of steel tubing in CO2 storage [J]. Greenhouse Gas.: Sci. Technol., 2016, 6: 797
免責聲明:本網站所轉載的文字、圖片與視頻資料版權歸原創作者所有,如果涉及侵權,請第一時間聯系本網刪除。
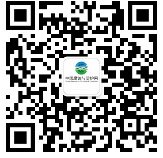
官方微信
《腐蝕與防護網電子期刊》征訂啟事
- 投稿聯系:編輯部
- 電話:010-62316606-806
- 郵箱:fsfhzy666@163.com
- 腐蝕與防護網官方QQ群:140808414