油氣管道是開采和輸送油氣的重要通道,是保證油氣田正常生產開發的重要產品,其質量要保證能夠維持一定的油氣開采年限。隨著能源需求量的增加和國家保障能源安全戰略要求的實施,油氣勘探力度不斷加大,管體斷裂事故不斷增加,給油田帶來巨大損失。
某采氣廠發生油氣管道管體開裂事故,嚴重影響了工作進度。來自吐哈石油勘探開發有限公司等的李銳峰等研究人員采用一系列理化檢驗方法對該管道的開裂原因進行分析。
-01-
理化檢驗
1.1 宏觀觀察
開裂管道規格為76mm×5mm(外徑×壁厚),送檢的管段長度為930mm,開裂處位于管段中部,沿縱向開裂,開裂口縱向長度為80mm,最大張開寬度為7mm,開裂處存在輕微鼓脹變形(見圖1),并可見壁厚減薄,且呈45°剪切特征(見圖2)。裂口周圍的防腐層破損脫落,其余部位的防腐層呈龜裂形貌。因裂口兩側管體發生塑性變形,故兩側斷口無法完全對接(見圖3)。將開裂部位的管體縱向剖開,發現管體內表面呈紅褐色,有均勻的腐蝕形貌(見圖4)。
1.2 壁厚及外徑測量
使用超聲波測厚儀對開裂管道的壁厚進行測量。管道開裂區域的壁厚測量點如圖5所示,由A~B端取5個剖面進行壁厚測量,每個剖面沿周向取8個測量點,測量結果如表1所示。由表1可知:遠離開裂部位的管道平均壁厚為5.52~5.67mm,最小壁厚為5.36 mm。開裂所在的鼓脹區平均壁厚為5.00~5.15mm,最小壁厚為4.62mm。分別測量管體鼓脹區及遠離開裂部位管道的外徑,結果如表2所示。管道壁厚及管徑測量結果表明,裂口位置發生了明顯的塑性變形及壁厚減薄。
1.3 外防腐層性能檢測
依據SY/T 0315—2013 《鋼質管道熔結環氧粉末外涂層技術規范》,選取遠離開裂部位外防腐層進行檢測,結果如表3所示。由表3可知:管道外防腐層性能檢測結果符合SY/T 0315—2013的要求。
1.4 化學成分分析
依據ASTM A751-14a《鋼制品化學分析標準試驗方法、試驗操作和術語》,采用直讀光譜儀及TC600型氧氮分析儀對遠離開裂部位的管道進行化學成分分析,結果如表4所示。由表4可知,管道的化學成分均符合GB/T 9711—2017《石油天然氣工業 管線輸送系統用鋼管》要求。
1.5 拉伸試驗
從遠離開裂部位的管道上截取試樣,在材料試驗機上進行拉伸試驗,結果如表5所示。試樣的拉伸試驗結果符合GB/T 9711—2017標準要求。
1.6 維氏硬度測試
從遠離開裂部位的管道處截取試樣,使用維氏硬度計測試管道的維氏硬度,在試樣外表面、中間、內表面3個部分分別測試3個點(見圖6),測試結果如表6所示。硬度測試結果表明:材料硬度符合GB/T 9711—2017標準要求。
1.7 金相檢驗
從遠離開裂部位的管道上截取試樣,依據ASTM E3-11(2017) 《金相試樣制備標準指南》,ASTM E45-18a 《鋼中夾雜物含量的測定———標準檢驗法》,ASTM E112-13 《平均晶粒度測定的標準試驗方法》,用光學顯微鏡觀察試樣,結果如表7(表中F為鐵素體,P為珠光體)及圖7所示。
1.8 斷口分析
管體開裂部位經超聲波清洗后觀察兩側斷口,其宏觀形貌如圖8所示。由圖8可知,原始斷口處厚度有明顯減薄,斷面為紅褐色,表面覆蓋了一層較厚的腐蝕產物。對剪切唇一側斷口用乙醇清洗并觀察斷面,發現其為典型的45°剪切斷口,斷口表面呈纖維狀;斷口內未發現特征花樣及裂紋源區。
清理45°斷口表面腐蝕產物,采用掃描電鏡(SEM)觀察。斷口近內、外表面SEM形貌如圖9所示。高倍下觀察斷口形貌,斷口表面覆蓋腐蝕產物,可見金屬基體部位均呈韌窩形貌。微觀斷口形貌存在大量韌窩,表明該管段為典型的韌性斷裂。結合宏觀斷口特征可知:斷口處管體有明顯鼓包塑性變形;由斷口的宏觀形貌及微觀形貌特征可知,該管段斷裂模式為塑性斷裂。
從斷口處截取試樣(見圖10),依據ASTM E3-11(2017)進行金相檢驗,結果表明試樣斷口處顯微組織沿周向拉伸變形,組織均為F+P(見圖11)。
對開裂斷口處的腐蝕產物進行能譜分析,其主要成分有Fe、C、O、Ca、Mn元素等(見圖12)。
-02-
氫致開裂試驗
從遠離開裂部位的管道上截取縱向試樣,尺寸(長×寬×厚)為100mm×20mm×5mm,依據GB/T 8650—2015 《管線鋼和壓力容器鋼抗氫致開裂評定方法》進行抗氫致開裂(HIC)試驗,試驗條件如表8所示,試驗結果如表9所示(表中CSR為裂紋敏感率,CLR為裂紋長度率,CTR為裂紋厚度率),96hHIC試驗前后試樣表面的宏觀形貌如圖13所示。試驗結果符合GB/T 9711—2017標準要求。
-03-
硫化物應力開裂試驗
從遠離開裂部位的管道上截取縱向試樣,依據GB/T 4157—2017 《金屬在硫化氫環境中抗硫化物應力開裂和應力腐蝕開裂的實驗室試驗方法》方法A,進行抗硫化物應力開裂(SSC)試驗,試驗結果如表10所示,720hSSC試驗后,試樣表面的宏觀形貌如圖14所示。試驗結果符合GB/T 9711—2017標準要求。
-04-
有限元分析
用有限元分析軟件對現場實際工況進行模擬,有助于直觀地對開裂原因及過程進行說明。管內介質設置為天然氣和水,與實際情況一致。開井作業后,管體內流體分布及開裂部位附近形變和應力分布如圖15~16所示。由圖15~16可知:在管道起伏部位,開井作業幾分鐘后,管道內發生湍流,造成局部水壓增大。靠近環焊縫兩端管體外弧側,在介質流動的作用下,易形成湍流漩渦,所受沖擊載荷較大,會造成管壁減薄,韌性降低;在開井作業情況下,閥門開啟后,環焊縫兩側應力分布較大,易產生水擊效應,造成壁厚不均,嚴重時會造成管道脹裂。
-05-
綜合分析
對開裂管段正常部位進行管段外防腐層檢測、壁厚及直徑測量、化學成分分析、拉伸試驗、維氏硬度測試、HIC試驗、SCC試驗,其結果均符合SY/T 0315—2013和GB/T 9711—2017標準要求。
由宏觀觀察結果可知,開裂部位的管道存在輕微鼓包變形,爆裂起源于鼓脹變形量最大、壁厚減薄最大處,鼓脹區最大直徑為90.76mm,減薄處最小壁厚為4.62mm,減薄明顯。斷口呈典型的45°剪切斷口,為典型的塑性斷口。斷口處壁厚明顯減薄,該部位組織沿周向拉伸變形,未見明顯脫碳特征,管道內、外表面未見明顯腐蝕坑或裂紋等;斷口呈現韌窩形貌。該管段在開裂之前發生屈服塑性變形。同時進一步對斷口處產物進行能譜分析,其主要成分為Fe、C、O、Ca、Mn等元素,主要是鐵的氧化物,未發生應力腐蝕。
綜上所述,該管段開裂的主要原因是該段管道特殊的地理位置,且開井作業后引起管道壓力突然增加,造成管體局部發生鼓脹,進一步導致管道爆裂。
-06-
結論與建議
(1) 開裂管道正常部位的外防腐層檢測、幾何尺寸測量、化學成分分析、拉伸試驗、維氏硬度測試、抗氫致開裂試驗、抗硫化物應力腐蝕試驗結果均符合SY/T 0315—2013和GB/T 9711—2017標準要求。
(2) 管段的開裂模式為塑性斷裂。
(3) 為減小水擊效應的影響,建議適當增加該段管道的壁厚和強度,并優化該段管道的布置;在開井作業時,在條件允許的情況下,建議適當延長閥門的動作時間。
免責聲明:本網站所轉載的文字、圖片與視頻資料版權歸原創作者所有,如果涉及侵權,請第一時間聯系本網刪除。
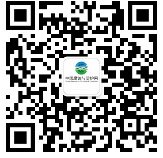
官方微信
《腐蝕與防護網電子期刊》征訂啟事
- 投稿聯系:編輯部
- 電話:010-62316606-806
- 郵箱:fsfhzy666@163.com
- 腐蝕與防護網官方QQ群:140808414