鋁合金具有高比強度/比模量、高耐蝕等優點,是兩棲飛機和車輛、艦載飛機、跨海大橋等高技術海洋工程裝備與構筑物十分重要的結構材料[1~3]。水上飛機和艦船用鋁合金常選用耐蝕性好的2×××系、5×××系及6×××系[4,5]。海上鋁合金裝備長期受海水和鹽霧的侵蝕,同時受海風和海浪沖擊,工況條件復雜嚴酷,具有腐蝕類型多和速率高、腐蝕部位隱蔽多發、腐蝕損傷程度大等特點[6]。鋁合金材料的腐蝕問題不僅造成巨大的維修成本,而且已成為決定海洋裝備壽命、保證技戰術水平的關鍵因素。
大型艦船、兩棲飛機和車輛等鋁合金海洋裝備的服役環境除了海水和海洋大氣外,還涉及海水/海洋大氣的交界區域,即海水/大氣界面區[7,8]。海水/大氣界面區主要分為3種環境工況:水線區、潮差區和飛濺區。對于船舶等浮式結構物,“海水/大氣界面區”通常稱為“水線區”,是指船舶重載水線和輕載水線之間的船體區域,該區域由于經常交替受到海水浸泡和大氣曝曬,表面涂層易受到海水以及漂浮物的沖刷和撞擊而損壞,所以是腐蝕比較嚴重的區域。對于跨海大橋鋼樁等固定式海洋結構物,“海水/大氣界面區”即為“潮差區”,是指平均低潮位和平均高潮位之間的區域。飛濺區是指潮差區之上受到浪花飛濺作用的區域,除了表面有干濕交替外,浪花的沖擊作用是很重要的因素。水線區、潮差區和飛濺區有相似之處(即干濕交替),但3者環境工況有明顯差別。本工作主要研究的是第一種情況,值得注意的是此種情況下的海水/大氣界面區是動態水線作用下的界面區(下文簡稱為水氣界面區)。
水氣界面處于干濕交替、供氧充足、鹽分濃縮的環境中,腐蝕環境涉及大氣、海水、海鹽等多相耦合作用[9,10]。我國積累了鋁合金在實海海水潮汐區[11]、全浸區[12]和飛濺區[13]長達16 a的腐蝕數據,總結了平均腐蝕速率和點蝕深度的變化規律。國外學者[14]也做了碳鋼的實海暴露實驗,發現浪花飛濺區和水線下方的腐蝕速率遠遠大于水線處和大氣區。由于供氧差異等因素導致水氣界面區的腐蝕電位與海水中的腐蝕電位不同,形成宏觀腐蝕電池,導致材料表面局部陽極區域腐蝕加速[15]。低碳鋼在靜水條件下,由于水線上下區域的氧濃度差異和水線下方鄰近區域因氧還原形成的pH梯度,水線腐蝕由氧濃差和pH共同控制[16];在流動環境中,由于水線附近的OH-容易擴散,并不會形成pH梯度,水線腐蝕此時完全由氧濃差控制[16]。目前國內外關于金屬材料在水氣界面區的腐蝕研究已取得了重要的進展,建立了模擬潮差[15]和浪花飛濺[17]等模擬測試裝置,但缺少動態水氣界面區模擬裝置及配套的原位實時腐蝕測試技術。
本工作搭建由電動推桿、時間繼電器及腐蝕電化學傳感器組成的模擬動態水氣界面腐蝕測試平臺,采用腐蝕電位監測、電化學阻抗譜(EIS)和電化學噪聲(EN)技術研究2024鋁合金在水氣界面區的腐蝕電化學行為及局部腐蝕機制,并分析水氣界面區與全浸區腐蝕行為的差異性,探討不同區域腐蝕電位不同對宏觀腐蝕電池的影響機制,為深入理解海水/大氣界面的局部腐蝕損傷機制奠定理論基礎。
1.1 實驗材料
實驗所用金屬材料為2024鋁合金,冷軋后經固溶和時效處理,其化學成分(質量分數,%)為:Cu 4.7,Mg 1.4,Mn 0.86,Fe 0.55,Si 0.51,Zn 0.30,Ti 0.15,Ni 0.1,Al余量。試片尺寸為250 mm × 105 mm × 2 mm。
1.2 模擬動態水氣界面綜合腐蝕測試平臺的搭建
搭建的模擬動態水氣界面腐蝕測試平臺如圖1a所示,主要由水氣界面模擬控制系統和電化學測試系統組成。水氣界面模擬控制系統由電動推桿、時間繼電器、水箱及試樣架組成(圖1a)。塑料試樣架上可同時放置4片鋁合金試樣,在電動推桿及時間繼電器的控制下試樣架及其鋁合金試樣上下往復運動,推進步長為10 cm,每次上下移動時間間隔為30 s,即水氣界面區處于交替的“浸入-移出”海水環境中,實驗共進行54 d。鋁合金試樣處于大氣區、水氣界面區和全浸區的高度分別為10、10和5 cm (圖1b)。水箱中盛有體積為40 L的3.5%NaCl (質量分數)溶液。電化學測試系統主要由4個電化學傳感器和PARSTAT 2273電化學工作站組成。水氣界面區和全浸區分別放置1個EIS測試傳感器和1個EN傳感器。值得注意的是,為了滿足電化學測試穩定性的要求以及消除溶液Ohm電位降的影響,水氣界面區的電化學測試是當試樣移至水下時進行的。
1.3 EIS測試
EIS測試傳感器由對電極和參比電極組成(圖1c),主要用于測量水氣界面區與全浸區的開路電位(OCP)及EIS。對電極為鍍Pt鈮棒,參比電極為Ag/AgCl電極(在3.5%NaCl溶液中相對于飽和甘汞電極的電位為1~3 mV)。EIS測試采用控制電位的方法,待腐蝕電位穩定后開始測試,施加電位正弦波的幅值為10 mV,測試頻率范圍為105∼10-2 Hz,共測40個數據點。EIS數據采用Orazem課題組近期編制的Measurement Model Installer (Version 1.4)軟件進行擬合[18,19]。
1.4 電化學噪聲測試
EN測試采用零阻電流(ZRA)檢測模式,可同時測得電位噪聲和電流噪聲。EN檢測傳感器如圖1d所示,傳感器主要包括面積為1.48 cm2的圓盤形鋁合金電極(記為WE2)和Ag/AgCl參比電極(圖1d)。圓形電極與待測2024鋁合金試片(記為WE1)為同種材質,因此,電流噪聲實際上測的是WE1和WE2之間的電偶電流,電位噪聲測的是WE1和WE2耦接后的電位隨時間的波動規律。由于WE1和WE2的面積不同,實際上EN檢測的電極系統屬于非對稱電極系統(asymmetrical electrode system)。采用非對稱電極系統的目的是為了將來便于現場檢測。由于非對稱電極系統計算得到的噪聲電阻與腐蝕速率之間的關系較為復雜,而且噪聲電阻主要反映了腐蝕體系均勻腐蝕的速率,因此本工作并沒有計算噪聲電阻[20]。本工作主要采用EN數據的頻域分析評估局部腐蝕敏感性,將EN數據先采用五次多項式擬合剔除直流分量[21],再進行快速Fourier變換(FFT)后,利用FFT頻譜圖中高頻線性區斜率和白噪聲水平判斷局部腐蝕強度。高頻線性區的斜率越陡,低頻白噪聲水平越大,局部腐蝕傾向越明顯[22,23]。
1.5 表面和截面形貌觀察及成分分析
采用VHX-2000C光學顯微鏡(OM)觀察試樣表面宏觀形貌,采用SU1510鎢燈絲掃描電鏡(SEM)觀察2024鋁合金在水氣界面區和全浸區的表面和截面微觀形貌,并利用能譜儀(EDS)對鋁合金不同位置的腐蝕產物進行元素成分分析。采用濃HNO3去除鋁合金表面的腐蝕產物后,計算平均腐蝕深度(5~8個點取平均值)和蝕孔密度。
2.1 腐蝕電位檢測
圖2為水氣界面區2024鋁合金的腐蝕電位隨“浸入-移出”水面的周期性變化趨勢。2024鋁合金腐蝕電位(移出水面時)總體變化趨勢為先變正后變負,4、15和34 d的腐蝕電位分別為-0.798、-0.787和-0.794 V (vs Ag/AgCl)。實驗至4 d時,界面區鋁合金浸入溶液以后,腐蝕電位迅速負移約10 mV,移出水面后,迅速正移約10 mV。腐蝕電位主要由陰陽極反應進行的難易程度來控制,假定界面區和全浸區的陽極反應動力學基本一致,那么腐蝕電位主要由陰極反應進行的速率來決定。由于界面區的O含量相對全浸區較高,因此腐蝕電位較正。實驗至15 d,腐蝕電位隨“浸入-移出”水面的周期性變化幅度減小(約4 mV),而且隨著浸入溶液,腐蝕電位緩慢負移,移出水面以后,腐蝕電位緩慢正移,這主要是因為表面覆蓋一層腐蝕產物所致。由于腐蝕產物膜有一定厚度,因此溶液完全滲透需要一定的時間,腐蝕電位變化遲緩。實驗進行至34 d,腐蝕電位周期性波動的幅值又增加至10 mV,這主要是因為鋁合金表面不斷生成的腐蝕產物使得原來的腐蝕產物部分脫落,露出鋁合金基體。因此,浸入溶液后,鋁合金的腐蝕電位負移的速率比15 d的快,但比4 d的慢。電位負移速率的快慢也與局部腐蝕敏感性有一定關系,相比表面覆蓋鈍化膜的金屬來說,裸金屬的電位負移速率要快。因此,電位負移速率的變化體現了局部腐蝕敏感性先降低后增加的趨勢。
2.2 電化學阻抗譜特征
采用EIS技術對2024鋁合金在水氣界面和全浸區54 d的腐蝕過程進行了檢測,結果分別如圖3a和b所示。從圖3a可以看出,水氣界面區的容抗弧半徑出現先增大后減小的趨勢,33 d對應的容抗弧半徑最大。1 d對應的容抗弧半徑約15 kΩ·cm2,由于容抗弧半徑近似等于腐蝕體系的極化電阻,說明此時鈍化膜雖然有一定的耐蝕性,但易發生破裂,局部腐蝕萌生。隨著腐蝕進行,鋁合金表面生成一層較為均勻致密的腐蝕產物層,容抗弧半徑不斷增大,33 d達到最大值。此后由于腐蝕的不斷進行,靠近鋁合金基體的腐蝕產物的生成會導致外層的腐蝕產物膜部分脫落,容抗弧半徑有所減小,與10 d的容抗弧半徑相當。前5 d的EIS呈現“單”容抗弧特征,之后由于腐蝕產物膜的覆蓋,呈現“雙”容抗弧特征,表明腐蝕體系最開始的電極反應速率由鈍化膜的完整性控制,逐漸變為由腐蝕產物膜層控制。
全浸區的EIS測試結果如圖3b所示。容抗弧半徑呈現逐漸增大的趨勢,54 d的容抗弧半徑最大。表明溶液區的腐蝕產物對基體的保護性與水氣界面區有所不同。全浸區前5 d的EIS呈現“單”容抗弧特征,而后出現“雙”容抗弧特征。
圖4為鈍性金屬電極在電解質溶液中的電化學等效電路模型[24],Re為溶液電阻。腐蝕電位下總的阻抗主要包含2個獨立的部分:陽極部分和陰極部分,分別對應陽極反應過程和陰極反應過程。陽極分支中,Cdl為雙電層電容,Rox,i為帶電物種(陽離子空位)在鈍化膜中移動的阻力,屬于離子運動的電阻;由于鈍化膜/溶液界面和鋁合金基體/鈍化膜界面的電化學反應對應的阻抗相比于Rox,i很小,因此都可以忽略。ZF3O2為鈍化膜/溶液界面O2還原的Faraday電阻,Rox,e為電子在鈍化膜中移動的阻力。Cdl位于陽極部分,這主要是因為在鈍化膜/溶液界面,鈍化膜中的空位和離子與雙電層中的離子達到了動態平衡,形成了穩定的雙電層。
圖4給出的電化學等效電路是一種理想情況,即僅針對鋁合金表面覆蓋一層完整的均質鈍化膜。實際的腐蝕體系的鈍化膜局部可能已經發生孔蝕,而且局部有腐蝕產物覆蓋,因此很難準確判斷實際腐蝕體系存在幾個時間常數,因為不同區域的電容和電阻值是不同的。本工作所測的EIS數據存在時間常數的彌散現象,這可能是由于材料表面不同區域的傳質過程不同,或是由于電極幾何因素引起的電流和電位分布不均勻,或是由于腐蝕產物膜的多孔結構及其分布不均勻造成的。為了解決此問題,Orazem課題組[18,19]近期提出了一種普適性模型Measurement Model,該模型可以較為準確地提取溶液電阻、極化電阻和無限頻率下的有效電容。當腐蝕體系存在k個電阻-電容(RC),電路的復阻抗Z表達式為[18]:
式中,k稱為Voigt元件個數,其值由軟件自動確定,當確定原則是增加k值,回歸參數的擬合誤差限制在95.4% (± 2) (為總體標準差)的置信區間;Ri和Ci為對應第i個元件的極化電阻和電容,1 ik;ω為測試頻率。從 式(1)可以看出,當ω無限大時,可以通過 式(2)計算腐蝕金屬電極的有效電容Ceff[18]:
式中,。當測試頻率趨近于0時,可以得到體系的極化電阻Rp[18]:
圖5為擬合得到的Rp和Ceff。可以看出,界面區的Rp先增大后減小,全浸區的Rp基本呈現增大-減小-再增大的趨勢。界面區和全浸區的Ceff差別不大,且呈現先減小再增加的趨勢。腐蝕前期由于界面區腐蝕產物的生成,導致表面膜的介電常數發生改變,因此Ceff減小。后期由于腐蝕產物膜的脫落,Ceff有所增大,但界面區和全浸區的Ceff差別不大。
2.3 電化學噪聲特征
圖6a和b給出了水氣界面區的電化學電流噪聲和電位噪聲測試結果,測試時水氣界面移至水下,以消除溶液Ohm電阻對測試結果的影響。3 d時的電位噪聲出現典型的局部腐蝕的特征,即有很多暫態峰,幅值達到4 mV (圖6b);電流噪聲的波動幅值為20 nA (圖6a),而且此時電位和電流噪聲的波動頻率較快,表明鈍化膜破裂修復事件發生的頻率較高。10 d時,電位噪聲波動幅值有所減小,約為1 mV;電流噪聲波動幅值也有減小,約為10 nA,表明由于腐蝕產物的覆蓋作用,局部腐蝕發展速率有所減緩。實驗進行至49 d時,電位噪聲和電流噪聲波動周期逐漸變長,表明隨著腐蝕產物的增加,物質傳遞速率減慢,使得電位與電流波動周期變長[23,25]。
圖7給出了全浸區的電流噪聲和電位噪聲測試結果。3 d時的電位噪聲和電流噪聲波動幅值和波動周期與水氣界面區類似。隨著時間延長至10 d,電位和電流噪聲的波動幅值減小,表明腐蝕產物的生成一定程度上抑制了局部腐蝕的強度。49 d時,電位噪聲和電流噪聲波動周期漸變長,其原因與水氣界面區相同。
圖8給出了2024鋁合金在水氣界面區(圖8a和c)和全浸區(圖8b和d)的電化學噪聲數據通過快速Fourier變換得到的功率譜密度(PSD),通過計算電位和電流PSD高頻線性區的斜率可以看出,其值均小于或接近-20 dB/dec,表明其腐蝕形態主要是局部腐蝕。對比低頻白噪聲水平,可以發現,水氣界面區電流噪聲的低頻白噪聲水平先下降再上升(圖8c)。全浸區的低頻白噪聲水平基本呈現一直下降的趨勢(圖8d),表明局部腐蝕強度隨時間延長有所下降。水氣界面區和全浸區的測試結果與EIS結果基本一致。
2.4 表面和截面腐蝕形貌分析
圖9為2024鋁合金大氣區、水氣界面區和全浸區宏觀腐蝕形貌隨時間的變化。圖中4個虛線圓圈標出的區域為EIS和EN檢測的區域。試樣表面主要分為3個區域:上面是大氣區,中間是水氣界面區,下面是全浸區。實驗3 d后,可以看到水氣界面區和大氣區交界處開始有鹽層沉積。水氣界面區有一層白色腐蝕產物,且腐蝕產物分布較為連續。由于界面區的鋁合金處于“浸入-移出”海水的動態環境中,腐蝕坑內的腐蝕產物如Al3+隨著試樣移出水面,會隨著水流方向流出蝕孔,遇到O2后會反應生成Al的氫氧化物和氧化物,因此導致水氣界面區被一層白色腐蝕產物覆蓋。全浸區也出現了白色腐蝕產物,但分布較為分散。當實驗至第15 d,水氣界面區和大氣區交界處的鹽沉積量明顯增多,水氣界面區的宏觀腐蝕形貌變化不大,全浸區的點蝕數目增多。實驗至第52 d,水氣界面區和大氣區交界處的NaCl鹽沉積量增多,其他區域的宏觀腐蝕形貌并無明顯變化。
圖10a和b為腐蝕54 d后2024鋁合金試片不同區域的平均點蝕深度和點蝕密度統計結果。由圖10a的結果可以看出,全浸區和水氣界面區的點蝕深度為2~5 μm,且水氣界面區的點蝕深度比溶液區的小。水氣界面區的點蝕深度由下至上逐漸減小。低水線位置的點蝕深度沒有顯著突變,說明宏觀電偶作用不明顯。高水線位置上方由于鹽沉積,點蝕深度增至約60 μm,高水線附近的宏觀腐蝕電池作用明顯,水線上方為陽極,下方為陰極。圖10b的結果表明,全浸區的點蝕密度隨著高度增加而增加,從234 mm-2增至612 mm-2。界面區的點蝕密度為119~250 mm-2,且隨著高度增加有遞減趨勢。總體來看,全浸區的點蝕數量比界面區多,表明點蝕更容易萌生和發展。大氣區由于腐蝕較為嚴重,點蝕密度無法進行統計。
圖11給出了2024鋁合金大氣區、水氣界面區和全浸區腐蝕54 d后的微觀形貌。大氣區主要觀察的是鹽層沉積物下的局部腐蝕情況,如圖11a所示,其局部腐蝕較為嚴重。此區域由于鹽度高,濕度大,因此腐蝕環境十分苛刻,鋁合金的腐蝕電位較低,陰極反應不僅有O2還原,可能還有析氫反應(取決于蝕孔內部的電位是否低于析氫反應的過電位),蝕孔內部由于局部酸化,pH值降低,可導致析氫反應速率加快。圖11b為水氣界面區的微觀腐蝕形貌,可以看出整個表面都有一層腐蝕產物,局部腐蝕產物發生了脫落。此外,圖11b標出了界面區鋁合金試樣的上下移動方向,可以看出腐蝕產物在蝕孔下方有明顯的“流動”痕跡(虛線圈出的區域),這主要是因為試樣在向上移出水面的過程中,蝕孔內部腐蝕產生的Al3+流出蝕孔外部,并與O2反應生成Al的氧化物或氫氧化物。圖11c和d為全浸區的微觀腐蝕形貌,全浸區有部分區域沒有明顯的腐蝕產物,可以看出夾雜物在早期腐蝕過程中的作用。2024鋁合金中的夾雜物主要有Al7Cu2Fe和AlCuFeMnSi相[26],Al元素在腐蝕過程中優先溶解,在夾雜物表面形成腐蝕產物;其他元素在腐蝕過程中因失去Al元素而發生重排,重新沉積在夾雜物表面,此時由于夾雜物表面電勢高于周圍基體,它們作為陰極相與基體之間發生微電偶腐蝕[27]。值得注意的是,夾雜物中Al的優先溶解是由原子級的脫合金化驅動的,而夾雜物周圍基體的溶解則是由夾雜物與基體之間的微電偶效應驅動的。隨著周圍基體的溶解,在夾雜物與基體之間形成溝槽[28] (圖11d)。隨著腐蝕的進行,溝槽底部形成類似于點蝕的自催化環境,當腐蝕進行到一定程度時,夾雜物可以脫落[26]。
表1列出了圖11中9個點的EDS分析結果。白色區域所在的位置O含量更高,說明白色區域主要是Al的氧化物和氫氧化物;深色區域O含量低,主要是表面腐蝕產物剝落之后的致密腐蝕層[29]。部分區域還存在少量的Si和Fe,主要來源于夾雜物。
2.5 水氣界面與全浸區腐蝕行為的差異性
通過表面形貌觀察和EIS、EN測試可以發現,水氣界面區和全浸區腐蝕過程的主要差別在于O含量不同。水氣界面區處于“浸入-移出”海水的動態環境中,移出水面后,其暴露于大氣環境中,O含量較高;而且移出水面30 s的時間間隔內,其表面并未完全干燥,表面覆蓋一層薄液膜,其腐蝕環境是高濕和高O含量的環境。在此環境下,鋁合金腐蝕產物萌生較快,3 d后表面生成一層相對致密的腐蝕產物層,對腐蝕起了一定的抑制作用。由于鋁合金表面不斷生成新的腐蝕產物,在應力作用下會使上層的腐蝕產物部分脫落,耐蝕性有一定降低。但由于起始階段生成的腐蝕產物膜層較為致密,對氧的傳輸擴散有一定阻礙作用,因此之后腐蝕產物膜層的生成速率減緩,第33 d阻抗模值達到最大值,而后阻抗模值有所減小。水氣界面區蝕孔數量少且蝕孔小,說明在這一區域鈍化膜即使易破裂,但點蝕萌生后發展比較緩慢。點蝕發展的必要條件是蝕孔內維持酸化條件,研究結果表明蝕孔內部的pH值可低至1~3[30]。蝕孔內的陽極反應和陰極反應如反應式(4)~(7)所示[31],陽極反應生成的Al3+會快速發生水解反應生成Al(OH)2Cl和H+[31],導致孔內產生酸性環境。蝕孔內的陰極反應除了H+還原以外(式(6)),還有O2的還原反應(式(7))[32]。由于界面區O濃度高,很容易通過擴散到達蝕孔內部,消耗H+,因此難以維持蝕孔內的酸化條件。
陽極反應:
陰極反應:
全浸區由于O含量較少,腐蝕產物生成速率較慢,蝕孔分布較為分散。另一方面,孔蝕一旦萌生,由于溶液中的O含量有限,不容易消耗H+,相比水氣界面區較容易維持局部酸化的環境。因此,全浸區的蝕孔數量少,蝕孔作為陽極區,蝕孔周圍的鋁合金作為陰極區。
2.6 不同區域之間的宏觀腐蝕電池效應
通過腐蝕電位測試可以看到,水氣界面區的腐蝕電位和全浸區的腐蝕電位相差10 mV左右,因此低水線位置處存在宏觀腐蝕電池效應。水線下方為陽極,水線上方為陰極。但由于電位相差的數值不大,耦合后的電偶電流數值較小。此外,宏觀腐蝕電池效應只存在于低水線位置附近,因為水氣界面區溶液電阻較大。因此,低水線位置對應的宏觀腐蝕電池為氧濃差電池。邢佩等[33]研究了E690鋼在不同O含量的NaCl溶液中的氧濃差腐蝕行為,結果表明陰陽極面積比和陰極區O含量都會影響氧濃差腐蝕過程,當陰陽極面積比c / a ≥ 4時,陰極區O含量是影響腐蝕過程的主要因素。關于水氣界面區與全浸區的鋁合金面積比是否對腐蝕有影響課題組正在進行研究。高水線位置附近也存在宏觀腐蝕電池效應:高水線下方的電位較正;水線上方鹽度大,幾乎處于鹽飽和的狀態,而且濕度大,偶爾存在浪花飛濺,所以水線上方的腐蝕電位較負,通過SEM結果也可以看出此處發生了嚴重的局部腐蝕。因此,高水線上方為陽極,高水線下方為陰極,但高水線位置的宏觀腐蝕電池主要為氯離子濃度引起的濃差電池,而不是氧濃差電池。
(1) 水氣界面區隨著鋁合金浸入和移出水面,腐蝕電位呈現“下降-上升”的周期性波動,波動幅值為5~10 mV,腐蝕電位快速下降和上升的速率體現了局部腐蝕敏感性較大,緩慢下降和上升體現了由于腐蝕產物膜的覆蓋作用導致局部腐蝕敏感性降低。
(2) EIS測試結果表明,水氣界面區和全浸區的極化電阻均呈現先增大后減小趨勢,表明界面區的腐蝕產物膜比全浸區的腐蝕產物膜耐蝕性好。界面區和全浸區的有效電容值差別不大,且均呈現先減小再增加的趨勢。腐蝕前期由于界面區腐蝕產物的生成,導致表面膜的介電常數發生改變,因此有效電容值減小。后期由于腐蝕產物膜的脫落,有效電容值有所增大。
(3) EN測試結果表明,電流噪聲的波動幅值及其PSD低頻白噪聲水平先減小后增大,表明局部腐蝕敏感性先減小后增大,電位噪聲的PSD高頻線性區斜率均小于-20 dB/dec,表明其腐蝕類型均為局部腐蝕。
(4) 動態水氣界面區腐蝕產物呈連續分布特征,全浸區腐蝕產物分布較為分散,這主要是由于動態水氣界面區O含量豐富以及腐蝕產生的Al3+流出蝕孔所致。
(5) 全浸區和水氣界面區的點蝕深度為2~5 μm,高水線上方由于鹽沉積,點蝕深度增至約60 μm。全浸區的點蝕密度隨著高度增加而增加,從234 mm-2增至612 mm-2。界面區的點蝕密度為119~250 mm-2,且隨著高度增加有遞減趨勢。與全浸區相比,界面區蝕孔數量少且尺寸小,說明在這一區域點蝕萌生后發展比較緩慢,主要是由于界面區O濃度高所致。
免責聲明:本網站所轉載的文字、圖片與視頻資料版權歸原創作者所有,如果涉及侵權,請第一時間聯系本網刪除。
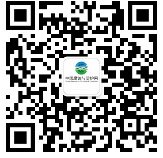
官方微信
《腐蝕與防護網電子期刊》征訂啟事
- 投稿聯系:編輯部
- 電話:010-62316606-806
- 郵箱:fsfhzy666@163.com
- 腐蝕與防護網官方QQ群:140808414