金屬材料的點蝕、縫隙腐蝕、晶間腐蝕、電偶腐蝕及應力腐蝕開裂等局部腐蝕過程屬于熱力學自發過程[1],是金屬材料常見的失效損傷形式。局部腐蝕不僅是制約其服役壽命和相關設備安全運行的關鍵因素,還帶來了巨大的經濟損失。2014年我國金屬腐蝕帶來的經濟損失約為2127.8億元,占當年國內生產總值的3.34%[2]。如果能理清影響局部腐蝕發展過程的關鍵環境因子和材料學因素,不僅能為金屬構件的服役壽命評估/預測提供一定的理論依據,還能指導耐蝕新材料研發。因此,對金屬材料的局部腐蝕損傷過程開展深入研究具有十分重要的理論意義和工程價值。
隨著局部腐蝕電化學理論、數值計算以及相應模擬軟件的發展,金屬局部腐蝕的研究取得了很大進步[3~7]。例如,采用pencil電極(也稱為artificial pit電極)方法可以原位研究點蝕發展過程,闡明點蝕發展的速率決定步驟以及鹽膜在點蝕發展過程中的作用[8~14]。采用冷凍聚焦離子束(FIB)切割技術配合透射電子顯微電鏡(TEM)技術、X射線光電子能譜(XPS)等技術可以研究蝕孔內部鹽膜的微觀結構和成分[15,16]。這些研究加深了人們對局部腐蝕損傷過程的理解,進而可以建立模型對局部腐蝕過程開展仿真模擬,克服實驗復雜度高、周期較長及經費高的缺點,實現對金屬構件腐蝕損傷的壽命評估與預測。目前用于模擬局部腐蝕損傷的模型主要有:有限元模型(finite element method,FEM)[17~26]、有限體積模型(finite volume method,FVM)[27]、任意Lagrangian-Eulerian (ALE)法[28,29]、水平集模型(level-set method,LSM)[30,31]、相場(phase-field,PF)模型[32~43]、元胞自動機(cellular automata,CA)模型[44~47]等。這些模型都允許損傷沿任意方向擴展,但要求損傷在相鄰單元的界面上保持連續,這會增加三維問題網格劃分的復雜性[48]。
近場動力學(peridynamics,PD)理論的出現為局部腐蝕的模擬帶來了新的生機。PD理論由Silling[49]在2000年首次提出,并將其應用于固體力學,成功解決了經典連續力學(classical continuum mechanics,CCM)在求解不連續問題時面臨的奇異性。經過20多年的發展,PD方法已被成功用于模擬材料裂紋擴展[50~53]和傳熱[54~57]等領域,同時用于研究多尺度[58]、多物理場[59]耦合問題。隨著研究人員對PD理論的深入研究,2015年PD首次被用于模擬局部腐蝕[60],并獲得了較為滿意的結果,這為PD在腐蝕中的應用奠定了基礎,PD腐蝕損傷模型較其他模型(FEM、FVM、ALE、PF及CA)存在以下優點[60,61]:(1) 采用非局部擴散控制方程;(2) 通過鍵的斷裂來表征由腐蝕產生的損傷;(3) 引入相變機制表征固/液界面的自由移動;(4) 采用單點Gaussian積分進行無網格離散化處理;(5) 非局部Dirichlet 邊界條件和非局部Neumann 邊界條件。但PD也存在一些缺點,如表面效應(surface effects)和復雜的三維數值計算的過程需要結合并行計算完成[62]。
本文主要介紹了基于近場動力學的局部腐蝕模型及其數值實現,重點綜述了近場動力學方法在局部腐蝕(點蝕、縫隙腐蝕、晶間腐蝕、電偶腐蝕及應力腐蝕開裂)中的研究進展,指出目前研究難點及未來研究方向。
1 基于近場動力學的局部腐蝕損傷模型及其數值實現
1.1 近場動力學基本理論
CCM理論基于連續性假設,如圖1a[62]所示,物質點(微小體積)只能與其直接接觸的物質點相互作用,以偏微分方程為控制方程,其空間導數難免會面臨不連續的情況,因此CCM理論解決不連續問題(如裂縫、腐蝕等)時數值解會出現奇異性。為解決這一非連續奇異性問題,Silling[49]引入一種新的連續介質動力學公式,即PD理論。該理論采用空間積分描述物質點的運動,突破了CCM理論在不連續問題上的瓶頸。
圖1 經典連續力學中的相互作用[62]與近場動力學(PD)中的相互作用[48]
PD是一種非局部理論,可以看作宏觀意義上的分子動力學,其將材料離散為空間域內的一系列物質點,如圖1b[48]所示,這些物質點能夠攜帶位移、損傷等信息[49,62~64],物質點 x 不僅與其直接接觸的物質點通過鍵相互作用,還與一定范圍內的其他物質點 x'相互作用[65]。這一半徑為δ的相互作用范圍稱為物質點 x 的近場域(horizon- x,Hx ),物質點 x'稱為物質點 x 在近場域內的“族”(family members),物質點 x 僅與其近場域內的物質點相互作用。
基于Newton第二定律的思想可以推導出PD基本控制方程為[49]:
式中, 為物質點 x 的密度; 質點 x 在時間t處的二階導數; u 和 u'分別為點 x 和 x'的位移; 為點 x'在物質點 x 近場域內的體積,可通過空間離散化求得,具體算法見1.3節; b 為物質點 x 處的體力密度; f 為物質點 x 與 x'間的本構力函數。
材料損傷和結構破壞后,由于物質點會發生相應的變化,因此可以引入水平參數β(ξij, t) (其中,ξij 為近場范圍內相互作用的兩物質點 x 與 x'間的相對距離,下角標i和j分別為物質點 x 和 x')反映鍵的狀態,β(ξij, t)定義如下[49]:
從而材料損傷就可以通過耦合PD控制方程與水平參數所得的損傷系數d( x, t)來反映[49]:
1.2 基于近場動力學的局部腐蝕模型
傳質模型在PD局部腐蝕模型的建立中起著重要的作用,傳質模型遵循Nernst-Planck方程,描述的是擴散、對流和電遷移對傳質的貢獻,其數學表達式為[66]:
式中,J為傳質通量,mol/(m2?s);K為擴散系數,m2/s;C為離子濃度,mol/m3; C為濃度梯度;n為離子的電荷數;F為Faraday常數,96494 C/mol;R為氣體常數,8.314 J/(mol·K);T為熱力學溫度,K;為電位梯度,mV/m;v為離子對流速率,m/s;-K?C代表擴散項;
代表電遷移項;Cv代表對流項。
對流和電遷移的貢獻在某些情況下可以忽略。比如在電化學體系中加入大量支持電解質可以降低或消除電遷移的影響,傳質過程就可以簡化為擴散和對流2個步驟,但因液相的擴散系數很大,在傳質過程中起主導地位,因此對流傳質可以忽略不計,最后將離子的擴散等效為離子的等效擴散,因此Nernst-Planck方程式可簡化為[60]:
式中,K(η)為固體節點中的等效擴散系數,固體節點中的等效擴散相當于由于金屬溶解而導致的界面移動;η為過電位;KL為液體節點中的等效擴散系數。
PD局部腐蝕模型將腐蝕過程的陽極反應看作金屬固體-電解質雙相系統中的非局部擴散的模型,如圖2[60]所示,這種擴散不僅發生在電解質中(溶液中金屬離子的擴散,J1),同時也發生在金屬固體中(金屬原子失電子的溶解,J2)。
圖2 基于擴散的一維PD腐蝕模型[60]
固體節點的 與η存在相應的關系[60]
式中,K0為零過電位下固體節點的等效擴散系數,K0實際上是根據電極過程動力學相關理論,忽略陽極過程逆反應部分的Butler-Volmer方程,將交換電流密度看作零過電位下的等效擴散系數;α為傳遞系數,其值域為[0, 1];z為電子轉移數;ba為陽極Tafel斜率。
以點蝕為例,推導PD腐蝕損傷模型的一維控制方程。受活化控制的點蝕發展過程,其固/液界面的移動依靠固體中的等效擴散系數,并且移動速度與過電位呈指數關系,靠近固/液界面處的液體節點的濃度存在一個臨界值(即飽和溶解度,Csat),在腐蝕過程中,固/液界面是自由移動的,因此可引入一種相變機制反映界面的移動情況,當固體節點的濃度低于溶液中的Csat時,固體節點發生溶解,轉變為液體節點,其數學模型為[60]:
式中,C(x)為物質點x處的濃度。
固體節點的最大濃度Csolid (未腐蝕節點的濃度)可由Scheiner和Hellmich[67]的研究來計算:
式中, 為平均摩爾質量。
傳質過程受擴散控制的金屬-溶液兩相材料(bi-material)的傳統腐蝕模型(一維模型)可表述為[60]:
式中,C(x,t)為物質點x在時間t處的濃度。
這一傳統數學模型的求解對固/液界面處濃度的連續性要求很高,但固/液界面往往是在不斷變化著的,界面處的濃度也在不斷變化,因此需要改進傳統模型,類比Bobaru和Duangpanya[55]對二維傳熱的研究,可將濃度與時間的微分轉換為對空間域上擴散通量的求積[60]:
式中,核函數J(x?, x, t)為微通量,類比Oterkus等[68]、Chen和Bobaru[69]對近場動力學熱傳導問題的研究,這一核函數可以通過具體方程式求解[60]:
式中,k(x, x')為微擴散系數,其可由等效擴散系數Kη,L求得;C(x', t)為物質點x'在t時間步處的濃度;Kη,L為固體或液體節點的等效擴散系數;kη,L為固體或液體的微擴散系數,即當Kη,L等于K(η)時,kη,L為kη,當Kη,L等于KL時,kη,L為kL,下角標η和L分別為過電位和液體節點;l為擴散鍵長;|x - x'|為物質點x'和x之間的相對距離;C(x')為物質點x'的濃度;l1為固體節點與固/液界面的距離;l2為液體節點與固/液界面的距離。
由 式(12)的空間離散化處理可得到離散后的PD方程[60]:
式中,Cn + 1為物質點x在tn + 1時間步的濃度,這里利用前向Euler法進行計算;Cn 為物質點x在tn 時間步的濃度;Δt為Cn + 1和Cn 之間的時間間隔。
腐蝕會引起材料的損傷,在擴散鍵(通過該鍵,固/液節點發生相互作用)上耦合力學鍵(與擴散鍵類似,用于監測由腐蝕引起的損傷),擴散鍵與力學鍵的耦合實際上是表示各節點處由濃度變化而發生的腐蝕損傷,如圖3[60]所示,擴散鍵受相變機制(phase change)的影響,但其不會發生斷裂,力學鍵則會隨節點濃度的降低而發生斷裂,因此可以引入一個與濃度相關的腐蝕損傷準則,反映材料的腐蝕損傷[60]:
圖3 相變機制和濃度致損模型[60]
合并式(12)~(20)即可得到應用于模擬點蝕損傷的一維PD控制方程,其二維和三維下的PD控制方程與一維類似,但需要對核函數J(x?, x, t)做相應的修改。PD腐蝕損傷控制方程較靈活,模擬不同類型的局部腐蝕,只需要在原有控制方程上添加其他方程(如應力腐蝕開裂中,需要添加應力方程),能夠解決局部腐蝕模擬中對應的次表面層(subsurface)的腐蝕損傷、花邊蓋(lacy covers)的形成以及鈍化膜破裂等關鍵問題,所以PD局部腐蝕控制方程能夠運用到點蝕、縫隙腐蝕、晶間腐蝕、電偶腐蝕及應力腐蝕開裂等多種局部腐蝕形式。Jafarzadeh等[70,71]建立了縫隙腐蝕對應的PD控制方程,該控制方程的關鍵點為將陽極溶解動力學簡化為金屬離子濃度與電流密度的關系。Jafarzadeh等[72]還建立了晶間腐蝕對應的PD控制方程,該控制方程的關鍵點為將晶界與晶粒視為兩相,晶粒為母相,晶界為第二相,且兩相分別對應不同的微擴散系數。Zhao等[73]建立了電偶腐蝕對應的PD控制方程,該控制方程的關鍵點為計算腐蝕金屬/電解質溶液界面處的電勢分布。Jafarzadeh等[74]建立了應力腐蝕開裂對應的PD控制方程,該控制方程的關鍵點為金屬表面的電化學反應與應力之間的耦合。
PD模型中所涉及的參數需要根據具體的局部腐蝕來確定,模擬包括點蝕、晶間腐蝕、電偶腐蝕、應力腐蝕開裂以及縫隙腐蝕所需要的主要參數有:η,i0 (交換電流密度),Csolid,Csat,n,T,K0,K(η),KL,k(x, x'),m,ba,d(x, t),σ (拉應力), μ (拉應力下產生的位移)等。
1.3 數值實現
非局部近場動力學方程是一個時間微分-空間積分方程,不具備解析解,通常采用無網格方法對其進行數值求解,該計算方法在處理損傷演化和裂紋擴展問題時具有優勢。美國Sandia國家實驗室科研人員研發了基于無網格法的PD開源計算程序PERIDIGM,可以實現近場動力學力學問題的數值求解[75,76]。目前研究人員使用C、FORTRAN、Python及MATLAB等編程語言編寫應用PD方法模擬材料腐蝕損傷的程序。采用單點Gaussian積分無網格法求解PD方程(式(1))時,首先離散處理PD控制方程[76]:
式中:為物質點 xi 在時間tn 處的二階導數,上角標n為時間tn,下角標i為物質點 xi;N為與物質點 x 相互作用的物質點的數目; 和 分別為物質點 xi 和 xj 在tn 時間處的位移;Vij 為物質點 xj 被 xi 的近場范圍所覆蓋的體積,下角標i和j分別為物質點 xi 和 xj; bi 為物質點 xi 處的體力密度。
式(21)將求積轉化為對物質點 xi 的近場范圍內所有點 xj 的求和,圖4a[48]使用均勻離散化且δ = 3Δx (其中,Δx為均勻網格離散化的網格尺寸),此時近場域內一共有28個物質點與中心點 k 發生相互作用,這是一種無網格離散化。圖4b[77]說明并不是近場范圍內的所有點的Vij 都可以被精確計算,這就需要對Vij 進行修正,在現有的研究中,解決這一問題的算法有多種[75,78~80]:FA、PA-PDLAMMPS、PA-HHB、PA-AC、IPA-HHB及IPA-AC等,但數值模擬是為了在節省研發開支的基礎上得到高保真的結果,為實驗提供有意義的參考,因此綜合已有的研究,可使用PA-HHB算法[77]對面積進行修正,該算法兼顧高精確度和高計算效率,具體算法如圖5所示。
圖4 二維近場范圍的均勻離散化[48]與面積修正[77]
圖5 用于面積修正的PA-HHB算法流程圖
對面積或體積進行修正后, 式(21)就可寫為:
對于特定的腐蝕問題,需要定義PD模型的初始條件和邊界條件。PD模型是一種非局部的空間積分,其求解過程需要相應的初始條件、非局部Dirichlet邊界條件[60,70,72,74]、非局部Neumann邊界條件[60,70,72,74]及非局部Robin邊界條件[73],不同的局部腐蝕類型相應的初始條件和邊界條件如圖6[60,70,72~74]所示。
圖6 點蝕、縫隙腐蝕、晶間腐蝕、電偶腐蝕以及應力腐蝕開裂對應的PD二維初始條件和邊界條件[60,70,72~74]
2 近場動力學在局部腐蝕損傷模擬中的應用
2.1 點蝕
實際上,金屬的點蝕不僅發生在固/液界面處,靠近固/液界面處一定厚度的金屬上(次表面層,subsurface)也發生了腐蝕。Chen和Bobaru[60]將點蝕過程中的陽極反應轉化為PD中的等效擴散,并以304不銹鋼為例模擬其次表面層的點蝕損傷,提出與濃度相關的損傷模型(concentration-dependent damage,CDD)和與損傷相關的腐蝕模型(damage-dependent corrosion,DDC)。CDD模型中,當固體節點濃度因腐蝕而降低時,其局部發生機械損傷,損傷系數與濃度呈正比。DDC模型中,當損傷系數達到臨界值時,一定范圍內的固體節點會轉化為液體節點,等效擴散系數發生相應變化。上述模型通過引入一種相變機制(phase-change)實現固/液界面的自由移動。如圖7a[60]所示,PD模型預測得到的極化曲線與實驗結果吻合。通過在PD數值模型中引入m (m = δ / Δx,為“域因子”,horizon factor),m能影響反應控制的腐蝕演化計算結果,如圖7b~d[60]所示,次表面層的損傷深度(h1)和點蝕深度(h2)隨著m的增大而增加。該模型是PD理論在腐蝕損傷中的首次探索,雖然獲得的結果與實驗結果較好吻合,但該模型存在以下不足:(1) 蝕孔內存在多個電極反應,模型只考慮金屬的陽極反應而忽略去極化劑的陰極反應;(2) 該模型僅考慮活化極化控制的陽極溶解過程,即假設腐蝕前沿界面處的電位是一常數,與實際腐蝕情況不符,需要改進該模型方能模擬其他類別的局部腐蝕損傷;(3) 該模型缺乏對點蝕萌生的預測,模型的預測結果基于在初始條件中假設存在一個起始點蝕,并未考慮鈍化膜破裂的機理,不能全面地預測點蝕的演化(即鈍化膜破裂-金屬溶解-點蝕萌生-點蝕擴展等一系列的演化)。
圖7 PD腐蝕模型預測結果和實驗測得極化曲線的對比結果及“域因子”(m)收斂性研究[60]
式(8)反映了過電位的大小對局部腐蝕存在影響,相關研究[81]表明在304不銹鋼的點蝕模擬中,點蝕坑的深度與過電位大小呈正相關。此外,Chen和Bobaru[60]提出異質材料的腐蝕模型,將耐蝕性較好的一相作為母相,耐蝕性較差的一相作為第二相,如圖8[60]所示,在豎直方向上發生的點蝕損傷較大。這種模型對模擬晶間腐蝕或夾雜物附近的腐蝕有重要作用。
圖8 用于研究異質材料點蝕損傷的2個示例以及例A和例B腐蝕20 s后的損傷演化圖[60]
在PD腐蝕模型中引入文獻[82,83]提出的濃度準則,可以研究再鈍化與重結晶對點蝕的影響,但需要考慮鹽膜覆蓋下的電極表面的電化學反應。如圖9[71,84]所示,PD模擬再鈍化與重結晶對304不銹鋼在0.1 mol/L NaCl溶液中發生點蝕的影響,沒有充分考慮鹽膜覆蓋下的電極表面的電化學反應,得到的三維下的點蝕坑和花邊蓋比實驗結果小。
圖9 三維模擬的初始和邊界條件[71],304不銹鋼點蝕生長的模擬結果[84]與實驗結果對比圖,以及模擬腐蝕83 s后的花邊蓋[71]
以蝕坑底部金屬/溶液界面處金屬的溶解舉例, 式(9)所采用的溶解判據存在一定的問題。根據經典點蝕理論[85],蝕坑底部金屬是否發生溶解(即固相到液相的轉變),并不是通過比較Csolid與溶液中的Csat大小決定,而是通過比較蝕坑底部固/液界面處金屬陽離子濃度(Csurf)與金屬再鈍化對應的金屬陽離子臨界濃度(Ccrit)進行判斷。只有當Csurf大于或等于Ccrit時,蝕坑內金屬才能持續溶解,進而點蝕才穩定生長。此外,當Csurf達到Csat時,蝕坑底部將沉積金屬鹽膜,點蝕生長轉化為擴散控制。因此,Chen和Bobaru[60]提出的模型還無法準確處理鹽膜覆蓋下點蝕生長的相關問題,Jafarzadeh等[86]利用經典點蝕理論[85]對該模型進行改進,如圖10a[86]所示,模擬了鹽膜覆蓋下的點蝕生長,與Chen和Bobaru[60]的模型進行比較,如圖10b[86]所示,該模型的結果更接近實際情況。
圖10 鹽膜的形成、原PD模型和改進的PD模型得到的腐蝕損傷的時間演化[86]
2.2 縫隙腐蝕
縫隙腐蝕是縫隙內部形成濃差電池而誘發的一種局部腐蝕,在近場動力學中,將縫隙腐蝕的自催化陽極溶解動力學簡化為金屬離子濃度與電流密度之間的關系,如圖11[70]所示,這一簡化對定義固/液界面處的局部溶解微通量提供了可能。
圖11 PD縫隙腐蝕模型中的自催化效應[70]
2.3 晶間腐蝕
晶間腐蝕是沿著材料晶界發生的一種局部腐蝕,由于晶界的陽極反應速率大于晶粒的陽極反應速率,晶界總是比晶粒優先腐蝕,依據Chen和Bobaru[60]的異質材料腐蝕模型,研究晶間腐蝕時可將晶粒視為母相,晶界視為第二相[72]。該模型還可以模擬由單個晶間腐蝕發展到整個晶粒溶解的過程,即模擬多晶材料的腐蝕。晶界上的金屬間化合物的微小顆?;虺恋硐喽加锌赡苁堑诙?晶粒和晶界都發生溶解,且晶體取向能影響多晶材料的腐蝕。如圖12[72]所示,其模擬結果與實驗結果存在一定的差異。
圖12 PD模擬2024-T3鋁合金浸泡在NaCl溶液中發生晶間腐蝕的深度與時間的曲線,及與實驗結果之間的比較[72]
2.4 電偶腐蝕
電偶腐蝕是指金屬構件在電解質溶液中構成腐蝕電池,產生電偶電流,加快了腐蝕電位較低的金屬的溶解,減慢了腐蝕電位較高的金屬的溶解,從而發生的一種電化學腐蝕,有時也稱接觸腐蝕。耦合PD腐蝕斷裂模型(PD corrosion-fracture,PD-CF)[73],可以通過求解相應的靜電問題來確定腐蝕速率。圖13a[73]為AE44鎂合金(Mg-4Al-4La-0.4Mn)/低碳鋼和AE44鎂合金/6063鋁合金電偶腐蝕的PD模擬結果,其電流密度雖與COMSOL Multiphysics?多物理場仿真軟件的模擬結果吻合較好,但陰極電流模擬結果(約為-120 A/m2)比實驗結果(約為-50 A/m2)[87]要大得多。圖13b[73]所示為AE44/6063偶對的電偶腐蝕PD模擬結果,雖然其與COMSOL模擬結果相吻合,但與實驗結果存在明顯的差異,實驗結果[87]顯示實際的電偶腐蝕并不完全沿著2種材料的相界面發生,腐蝕電位較高的6063鋁合金也出現了腐蝕,這說明在腐蝕環境中,存在其他形式的局部腐蝕,該PD-CF模型卻沒有考慮這一點。
圖13 AE44鎂合金/低碳鋼偶對的電極表面的初始電流密度和AE44鎂合金/6063鋁合金偶對腐蝕深度的定量分析[73]
2.5 應力腐蝕開裂
應力腐蝕開裂 (stress corrosion cracking,SCC)是指金屬材料在腐蝕環境和拉應力的作用下,其裂紋尖端的陽極區連續溶解,促進裂紋萌生和擴展的一種腐蝕損傷。近場動力學首次被用來研究氫致應力腐蝕開裂(hydrogen induced stress-corrosion cracking)[88],建立了近場動力學微觀力學模型(peridynamics micro-mechanical model)和近場動力學氫晶界擴散模型(peridynamics hydrogen grain boundary-diffusion model),為進一步研究具有復雜形狀、載荷條件、多個裂縫以及三維的SCC奠定了基礎。點蝕處的裂紋萌生和擴展可以誘發SCC,這種裂紋可以沿晶/穿晶擴展,相關研究[89]表明,點蝕坑的微觀結構對模擬裂紋的形核與擴展有顯著影響。在SCC中產生的裂紋容易發生擴展,研究[90]表明,起始于金屬材料表面損傷層的裂紋,經過腐蝕產物層擴展后會引起不可預測的脆性斷裂。在力學-化學耦合近場動力學模型(mechano-chemical coupled peridynamics)中施加一些斷裂條件也可以模擬SCC[74]。Shi等[91]利用近場動力學研究了表面附有點蝕坑的碳鋼管在壓應力和彎曲應力2種不同載荷條件下蝕坑處的裂紋擴展。如圖14[91]所示,模擬結果顯示碳鋼管在壓應力作用下,裂紋在縱向形核并沿該方向擴展;在彎曲應力作用下,裂紋在圓周方向形核并沿該方向擴展。
圖14 壓應力和彎曲應力下時間步長為1500的點蝕坑的裂紋擴展[91]
在隨后的研究中,Chen等[92]對Jafarzadeh等[74]提出的模型加以改進,可以模擬任何由力-化耦合和機械應變產生的腐蝕損傷。以三點彎曲條件下金屬梁的二維應力腐蝕開裂為例,獲得了由點蝕到裂紋形核的轉變時間、斷裂瞬間點蝕坑的尺寸和形狀以及點蝕坑中的裂紋的形核與擴展,并通過與海工鋼應力腐蝕開裂實驗結果進行對比驗證了模型。
3 結語與展望
本文綜述了PD理論在點蝕、晶間腐蝕、電偶腐蝕等不同局部腐蝕損傷模擬的研究進展,主要結論如下:
(1) PD模型通過表面擴散、離子傳輸、金屬/溶液界面處的電化學反應及固/液界面的自由移動可成功模擬局部腐蝕過程。
(2) PD局部腐蝕損傷模型可以模擬點蝕中次表面層的損傷和花邊蓋的形成、鹽膜覆蓋下點蝕的生長、簡化縫隙腐蝕中的自催化效應、晶間腐蝕、腐蝕金屬/電解質溶液界面處的電勢分布以及壓應力和彎曲應力下點蝕坑處的裂紋擴展。
(3) PD局部腐蝕損傷模型通過其他數值模擬結果和實驗結果進行校準,但其仍處于發展的階段,目前還不能指導耐蝕性材料的研發。
PD作為一種非局部理論,在材料斷裂和傳熱等方面有著較為成熟的應用,且能成功模擬金屬材料局部腐蝕損傷演化,但金屬材料的腐蝕往往受多個影響因素(腐蝕產物、晶體結構、夾雜物等)和多物理場多相(如服役環境存在固、液、氣多相耦合作用)的影響,加之PD模型對局部腐蝕損傷演化的研究仍處于發展階段,因此PD模型未來的發展可朝著以下方向進行:
(1) 局部腐蝕新機理與PD模型的融合:腐蝕模擬現階段所面臨的重大挑戰是金屬材料在實際服役條件下的腐蝕演化高保真建模和準確預測其剩余服役壽命等[93]。目前所建立的PD局部腐蝕損傷模型所采用的腐蝕發生(如前文提及的金屬溶解導致的固/液轉變)的判定標準缺乏理論支撐,與現行腐蝕理論存在偏差。因此,建立基于腐蝕機理的用于腐蝕損傷模擬及壽命預測的腐蝕模型是PD理論未來發展的重要方向。Frankel團隊[8~14]近年在局部腐蝕理論方面的理論工作,對進一步完善模型提供了新的可能。
(2) PD模型的改進與優化:已有的PD腐蝕模型考慮的電化學參數較少,這對模擬結果存在一定影響,可以利用電化學測試和現代表征等技術獲取相關參數,改進和校準PD腐蝕模型,比如較為復雜的晶間腐蝕,需要在原有模型上增加多個參數,如晶界的厚度、晶粒尺寸等;金屬材料在磁場環境下的電化學腐蝕則需引入電磁場這個關鍵參數。并且PD模型不應只局限于模擬發生在完好金屬上的局部腐蝕損傷,對腐蝕產物覆蓋下的局部腐蝕損傷模擬也是很重要的。通過對模型的改進與優化,使得PD模型能指導耐蝕性材料的研發。
(3) PD模擬多場多相耦合作用下金屬的腐蝕損傷:以水上飛機、船舶及海上光伏支架等海上裝備用鋁合金材料為例,其服役環境主要是海水/大氣界面,是典型的多場多相耦合環境[94~96]。這些結構材料在海水/大氣交替和浪花拍打等作用下,受溫度、pH值、溶解氧的影響發生的腐蝕是影響海洋工程與武器裝備能否長期穩定使用的關鍵因素,然而實海實驗復雜、耗時長、成本大,因此利用PD模型模擬多場多相耦合下金屬材料的局部腐蝕損傷顯得尤為重要。
(4) PD模型與機器學習:實際上金屬材料的局部腐蝕情況是十分復雜的,其受多因素的影響,若同時考慮所有因素的影響,會增加PD模型的計算量,通過機器學習可以尋找影響局部腐蝕的重要因素,結合相關的局部腐蝕理論,利用PD模型研究這些因素的影響,這樣能在計算量和可靠性之間找到最佳的平衡。
參考文獻
1 Xia D H, Deng C M, MacDonald D, et al. Electrochemical measurements used for assessment of corrosion and protection of metallic materials in the field: A critical review [J]. J. Mater. Sci. Technol., 2022, 112: 151
doi: 10.1016/j.jmst.2021.11.004
2 Hou B R, Li X G, Ma X M, et al. The cost of corrosion in China [J]. npj Mater. Degrad., 2017, 4: 1
doi: 10.1038/s41529-019-0105-2
3 Xia D H, Mao Y C, Zhu Y, et al. A novel approach used to study the corrosion susceptibility of metallic materials at a dynamic seawater/air interface [J]. Corros. Commun., 2022, 6: 62
doi: 10.1016/j.corcom.2022.03.001
4 Xia D H, Qin Z B, Song S Z, et al. Combating marine corrosion on engineered oxide surface by repelling, blocking and capturing Cl-: A mini review [J]. Corros. Commun., 2021, 2: 1
doi: 10.1016/j.corcom.2021.09.001
5 Alkire R. Editors' choice-perspective-mathematical modeling of electrochemical systems at multiple scales [J]. J. Electrochem. Soc., 2020, 167: 013517
6 Ji Y Y, Xu Y Z, Zhang B B, et al. Review of micro-scale and atomic-scale corrosion mechanisms of second phases in aluminum alloys [J]. Trans. Nonferrous Met. Soc. China, 2021, 31: 3205
doi: 10.1016/S1003-6326(21)65727-8
7 Weidner J W, Balbuena P B, Weber A Z, et al. Mathematical modeling of electrochemical systems at multiple scales in honor of Professor John Newman [J]. J. Electrochem. Soc., 2017, 164: Y13
doi: 10.1149/2.0731711jes
8 Li T S, Wu J, Frankel G S. Localized corrosion: Passive film breakdown vs. pit growth stability, Part VI: Pit dissolution kinetics of different alloys and a model for pitting and repassivation potentials [J]. Corros. Sci., 2021, 182: 109277
doi: 10.1016/j.corsci.2021.109277
9 Li T S, Frankel G S. Repassivation underneath salt film on stainless steel pits [J]. Corros. Sci., 2022, 203: 110353
doi: 10.1016/j.corsci.2022.110353
10 Frankel G S, Li T S, Scully J R. Perspective-localized corrosion: Passive film breakdown vs pit growth stability [J]. J. Electrochem. Soc., 2017, 164: C180
doi: 10.1149/2.1381704jes
11 Li T S, Scully J R, Frankel G S. Localized corrosion: Passive film breakdown vs pit growth stability: Part II. A model for critical pitting temperature [J]. J. Electrochem. Soc., 2018, 165: C484
doi: 10.1149/2.0591809jes
12 Li T S, Scully J R, Frankel G S. Localized corrosion: Passive film breakdown vs. pit growth stability: Part III. A unifying set of principal parameters and criteria for pit stabilization and salt film formation [J]. J. Electrochem. Soc., 2018, 165: C762
doi: 10.1149/2.0251811jes
13 Li T S, Scully J R, Frankel G S. Localized corrosion: passive film breakdown vs pit growth stability: Part V. Validation of a new framework for pit growth stability using one-dimensional artificial pit electrodes [J]. J. Electrochem. Soc., 2019, 166: C3341
doi: 10.1149/2.0431911jes
14 Li T S, Scully J R, Frankel G S. Localized corrosion: Passive film breakdown vs. pit growth stability: Part IV. The role of salt film in pit growth: A mathematical framework [J]. J. Electrochem. Soc., 2019, 166: C115
doi: 10.1149/2.0211906jes
15 Li T S, Perea D E, Schreiber D K, et al. Cryo-based structural characterization and growth model of salt film on metal [J]. Corros. Sci., 2020, 174: 108812
doi: 10.1016/j.corsci.2020.108812
16 Wang Y C, Song S Z, Wang J Q, et al. Correlation between passivity breakdown and composition of passive film formed on alloy 690 studied by sputtering XPS and FIB-HRTEM [J]. J. Electrochem. Soc., 2019, 166: C332
doi: 10.1149/2.1291912jes
17 Turnbull A, Wright L, Crocker L. New insight into the pit-to-crack transition from finite element analysis of the stress and strain distribution around a corrosion pit [J]. Corros. Sci., 2010, 52: 1492
doi: 10.1016/j.corsci.2009.12.004
18 Wenman M R, Trethewey K R, Jarman S E, et al. A finite-element computational model of chloride-induced transgranular stress-corrosion cracking of austenitic stainless steel [J]. Acta. Mater., 2008, 56: 4125
doi: 10.1016/j.actamat.2008.04.068
19 Vankeerberghen M. Will finite-element analysis find its way to the design against stress corrosion cracking? [J]. Environ.-Induced Crack. Mater., 2008, 1: 115
20 Paraskevoulakos C, Tanner D W J, Scott T B. Finite element modelling approach to investigate the degradation of intermediate level waste drums induced from interior metallic corrosion [J]. Eng. Struct., 2017, 147: 385
doi: 10.1016/j.engstruct.2017.06.012
21 Fallahnezhad K, Oskouei R H, Taylor M. Development of a fretting corrosion model for metallic interfaces using adaptive finite element analysis [J]. Finite. Elem. Anal. Des., 2018, 148: 38
doi: 10.1016/j.finel.2018.05.004
22 Qin G J, Cheng Y F, Zhang P. Finite element modeling of corrosion defect growth and failure pressure prediction of pipelines [J]. Int. J. Press. Vessels Pip., 2021, 194: 104509
doi: 10.1016/j.ijpvp.2021.104509
23 Fatoba O O, Leiva-Garcia R, Lishchuk S V, et al. Simulation of stress-assisted localised corrosion using a cellular automaton finite element approach [J]. Corros. Sci., 2018, 137: 83
doi: 10.1016/j.corsci.2018.03.029
24 Roy K, Lau H H, Fang Z Y, et al. Effects of corrosion on the strength of self-drilling screw connections in cold-formed steel structures-experiments and finite element modeling [J]. Structures, 2022, 36: 1080
doi: 10.1016/j.istruc.2021.12.052
25 Bailly-Salins L, Borrel L, Jiang W, et al. Modeling of high-temperature corrosion of zirconium alloys using the eXtended finite element method (X-FEM) [J]. Corros. Sci., 2021, 189: 109603
doi: 10.1016/j.corsci.2021.109603
26 Jasra Y, Singhal S, Upman R, et al. Finite element simulation of stress corrosion cracking in austenitic stainless steel using modified Lemaitre damage model [J]. Mater. Today: Proc., 2020, 26: 2314
27 Onishi Y, Takiyasu J, Amaya K, et al. Numerical method for time-dependent localized corrosion analysis with moving boundaries by combining the finite volume method and voxel method [J]. Corros. Sci., 2012, 63: 210
doi: 10.1016/j.corsci.2012.06.001
28 Sun W, Liu G C, Wang L D, et al. An arbitrary Lagrangian-Eulerian model for studying the influences of corrosion product deposition on bimetallic corrosion [J]. J. Solid State Electrochem., 2013, 17: 829
doi: 10.1007/s10008-012-1935-9
29 Sun W, Wang L D, Wu T T, et al. An arbitrary Lagrangian-Eulerian model for modelling the time-dependent evolution of crevice corrosion [J]. Corros. Sci., 2014, 78: 233
doi: 10.1016/j.corsci.2013.10.003
30 Duddu R. Numerical modeling of corrosion pit propagation using the combined extended finite element and level set method [J]. Comput. Mech., 2014, 54: 613
doi: 10.1007/s00466-014-1010-8
31 Duddu R, Kota N, Qidwai S M. An extended finite element method based approach for modeling crevice and pitting corrosion [J]. J. Appl. Mech., 2016, 83: 081003
32 Ansari T Q, Xiao Z H, Hu S Y, et al. Phase-field model of pitting corrosion kinetics in metallic materials [J]. npj Comput. Mater., 2018, 4: 38
doi: 10.1038/s41524-018-0089-4
33 Ansari T Q, Huang H T, Shi S Q. Phase field modeling for the morphological and microstructural evolution of metallic materials under environmental attack [J]. npj Comput. Mater., 2021, 7: 143
doi: 10.1038/s41524-021-00612-7
34 Lin C, Ruan H H, Shi S Q. Phase field study of mechanico-electrochemical corrosion [J]. Electrochim. Acta, 2019, 310: 240
doi: 10.1016/j.electacta.2019.04.076
35 Nguyen T T, Bolivar J, Réthoré J, et al. A phase field method for modeling stress corrosion crack propagation in a nickel base alloy [J]. Int. J. Solids Struct., 2017, 112: 65
doi: 10.1016/j.ijsolstr.2017.02.019
36 St?hle P, Hansen E. Phase field modelling of stress corrosion [J]. Eng. Fail. Anal., 2015, 47: 241
doi: 10.1016/j.engfailanal.2014.07.025
37 Mai W J, Soghrati S, Buchheit R G. A phase field model for simulating the pitting corrosion [J]. Corros. Sci., 2016, 110: 157
doi: 10.1016/j.corsci.2016.04.001
38 Mai W J, Soghrati S. A phase field model for simulating the stress corrosion cracking initiated from pits [J]. Corros. Sci., 2017, 125: 87
doi: 10.1016/j.corsci.2017.06.006
39 Nguyen T T, Bolivar J, Shi Y, et al. A phase field method for modeling anodic dissolution induced stress corrosion crack propagation [J]. Corros. Sci., 2018, 132: 146
doi: 10.1016/j.corsci.2017.12.027
40 Xiao Z H, Hu S Y, Luo J L, et al. A quantitative phase-field model for crevice corrosion [J]. Comput. Mater. Sci., 2018, 149: 37
doi: 10.1016/j.commatsci.2018.03.011
41 Mai W J, Soghrati S. New phase field model for simulating galvanic and pitting corrosion processes [J]. Electrochim. Acta, 2018, 260: 290
doi: 10.1016/j.electacta.2017.12.086
42 Chadwick A F, Stewart J A, Enrique R A, et al. Numerical modeling of localized corrosion using phase-field and smoothed boundary methods [J]. J. Electrochem. Soc., 2018, 165: C633
doi: 10.1149/2.0701810jes
43 Tsuyuki C, Yamanaka A, Ogimoto Y. Phase-field modeling for pH-dependent general and pitting corrosion of iron [J]. Sci. Rep., 2018, 8: 12777
doi: 10.1038/s41598-018-31145-7 pmid: 30143681
44 Lishchuk S V, Akid R, Worden K, et al. A cellular automaton model for predicting intergranular corrosion [J]. Corros. Sci., 2011, 53: 2518
doi: 10.1016/j.corsci.2011.04.027
45 Di Caprio D, Vautrin-Ul C, Stafiej J, et al. Morphology of corroded surfaces: Contribution of cellular automaton modelling [J]. Corros. Sci., 2011, 53: 418
doi: 10.1016/j.corsci.2010.09.052
46 Córdoba-Torres P, Nogueira R P, De Miranda L, et al. Cellular automaton simulation of a simple corrosion mechanism: Mesoscopic heterogeneity versus macroscopic homogeneity [J]. Electrochim. Acta, 2001, 46: 2975
doi: 10.1016/S0013-4686(01)00524-2
47 Cui C J, Ma R J, Chen A R, et al. Experimental study and 3D cellular automata simulation of corrosion pits on Q345 steel surface under salt-spray environment [J]. Corros. Sci., 2019, 154: 80
doi: 10.1016/j.corsci.2019.03.011
48 Oterkus E, Oterkus S, Madenci E. Peridynamic Modeling, Numerical Techniques, and Applications [M]. Amsterdam: Elsevier, 2021: 186
49 Silling S A. Reformulation of elasticity theory for discontinuities and long-range forces [J]. J. Mech. Phys. Sol., 2000, 48: 175
doi: 10.1016/S0022-5096(99)00029-0
50 Rabczuk T, Ren H L. A peridynamics formulation for quasi-static fracture and contact in rock [J]. Eng. Geol., 2017, 225: 42
doi: 10.1016/j.enggeo.2017.05.001
51 Sanchez G, Aperador W, Cerón A. Corrosion grade classification: A machine learning approach [J]. Indian Chem. Eng., 2020, 62: 277
52 Hu W K, Ha Y D, Bobaru F. Peridynamic model for dynamic fracture in unidirectional fiber-reinforced composites [J]. Comput. Methods Appl. Mech. Eng., 2012, 217-220: 247
doi: 10.1016/j.cma.2012.01.016
53 Karpenko O, Oterkus S, Oterkus E. Peridynamic analysis to investigate the influence of microstructure and porosity on fatigue crack propagation in additively manufactured Ti6Al4V [J]. Eng. Fract. Mech., 2022, 261: 108212
doi: 10.1016/j.engfracmech.2021.108212
54 Bobaru F, Duangpanya M. The peridynamic formulation for transient heat conduction [J]. Int. J. Heat Mass Transf., 2010, 53: 4047
doi: 10.1016/j.ijheatmasstransfer.2010.05.024
55 Bobaru F, Duangpanya M. A peridynamic formulation for transient heat conduction in bodies with evolving discontinuities [J]. J. Comput. Phys., 2012, 231: 2764
doi: 10.1016/j.jcp.2011.12.017
56 Wang L J, Xu J F, Wang J X. A peridynamic framework and simulation of non-Fourier and nonlocal heat conduction [J]. Int. J. Heat Mass Transf., 2018, 118: 1284
doi: 10.1016/j.ijheatmasstransfer.2017.11.074
57 Nikolaev P, Sedighi M, Jivkov A P, et al. Analysis of heat transfer and water flow with phase change in saturated porous media by bond-based peridynamics [J]. Int. J. Heat Mass Transf., 2022, 185: 122327
doi: 10.1016/j.ijheatmasstransfer.2021.122327
58 Askari E, Bobaru F, LEhoucq R B, et al. Peridynamics for multiscale materials modeling [J]. J. Phys.: Conf. Ser., 2008, 125: 012078
59 Gerstle W, Silling S, Read D, et al. Peridynamic simulation of electromigration [J]. Comput. Mater. Contin., 2008, 8: 75
60 Chen Z G, Bobaru F. Peridynamic modeling of pitting corrosion damage [J]. J. Mech. Phys. Sol., 2015, 78: 352
doi: 10.1016/j.jmps.2015.02.015
61 Jafarzadeh S, Chen Z G, Bobaru F. Computational modeling of pitting corrosion [J]. Corros. Rev., 2019, 37: 419
doi: 10.1515/corrrev-2019-0049
62 Madenci E, Oterkus E. Peridynamic Theory and Its Applications [M]. New York: Springer, 2014: 19
63 Silling S A, Epton M, Weckner O, et al. Peridynamic states and constitutive modeling [J]. J. Elasticity, 2007, 88: 151
doi: 10.1007/s10659-007-9125-1
64 Macek R W, Silling S A. Peridynamics via finite element analysis [J]. Finite Elem. Anal. Des., 2007, 43: 1169
doi: 10.1016/j.finel.2007.08.012
65 Chen Z G. Advances in corrosion damage modeling [J]. Chin. J. Sol. Mech., 2019, 40: 99
65 陳子光. 腐蝕損傷模型研究進展 [J]. 固體力學學報, 2019, 40: 99
66 Cao C N. Principles of Electrochemistry of Corrosion [M]. 3rd Ed., Beijing: Chemical Industry Press, 2008: 60
66 曹楚南. 腐蝕電化學原理 [M]. 第 3版, 北京: 化學工業出版社, 2008: 60
67 Scheiner S, Hellmich C. Stable pitting corrosion of stainless steel as diffusion-controlled dissolution process with a sharp moving electrode boundary [J]. Corros. Sci., 2007, 49: 319
doi: 10.1016/j.corsci.2006.03.019
68 Oterkus S, Madenci E, Agwai A. Peridynamic thermal diffusion [J]. J. Comput. Phys., 2014, 265: 71
doi: 10.1016/j.jcp.2014.01.027
69 Chen Z G, Bobaru F. Selecting the kernel in a peridynamic formulation: A study for transient heat diffusion [J]. Comput. Phys. Commun., 2015, 197: 51
doi: 10.1016/j.cpc.2015.08.006
70 Jafarzadeh S, Zhao J M, Shakouri M, et al. A peridynamic model for crevice corrosion damage [J]. Electrochim. Acta, 2022, 401: 139512
doi: 10.1016/j.electacta.2021.139512
71 Jafarzadeh S, Chen Z G, Zhao J M, et al. Pitting, lacy covers, and pit merger in stainless steel: 3D peridynamic models [J]. Corros. Sci., 2019, 150: 17
doi: 10.1016/j.corsci.2019.01.006
72 Jafarzadeh S, Chen Z G, Bobaru F. Peridynamic modeling of intergranular corrosion damage [J]. J. Electrochem. Soc., 2018, 165: C362
doi: 10.1149/2.0821807jes
73 Zhao J M, Jafarzadeh S, Rahmani M, et al. A peridynamic model for galvanic corrosion and fracture [J]. Electrochim. Acta, 2021, 391: 138968
doi: 10.1016/j.electacta.2021.138968
74 Jafarzadeh S, Chen Z G, Li S M, et al. A peridynamic mechano-chemical damage model for stress-assisted corrosion [J]. Electrochim. Acta, 2019, 323: 134795
doi: 10.1016/j.electacta.2019.134795
75 Lehoucq R B, Silling S A, Seleson P, et al. Peridynamics with LAMMPS: A user guide [R]. Albuquerque: Sandia National Laboratories, 2011
76 Silling S A, Askari E. A meshfree method based on the peridynamic model of solid mechanics [J]. Comput. Struct., 2005, 83: 1526
doi: 10.1016/j.compstruc.2004.11.026
77 Seleson P. Improved one-point quadrature algorithms for two-dimensional peridynamic models based on analytical calculations [J]. Comput. Methods Appl. Mech. Eng., 2014, 282: 184
doi: 10.1016/j.cma.2014.06.016
78 Liu J J, Lin Y Z, Li X Y. Numerical simulation for carbon steel flow-induced corrosion in high-velocity flow seawater [J]. Anti-Corros. Methods Mater., 2008, 55: 66
doi: 10.1108/00035590810859430
79 Bobaru F, Yang M J, Alves L F, et al. Convergence, adaptive refinement, and scaling in 1D peridynamics [J]. Int. J. Numer. Methods Eng., 2009, 77: 852
doi: 10.1002/nme.2439
80 Silling S A. Linearized theory of peridynamic states [J]. J. Elasticity, 2010, 99: 85
doi: 10.1007/s10659-009-9234-0
81 Bai X M, Tang J Q, Gong J M. Numerical modeling of 1D corrosion pit propagation under different overpotentials using peridynamic method [J]. J. Nanjing Tech Univ. (Nat. Sci. Ed.) 2017, 39(6): 91
81 白小敏, 唐建群, 鞏建鳴. 不同過電位下一維點蝕的近場動力學數值模擬 [J]. 南京工業大學學報(自然科學版), 2017, 39(6): 91
82 Laycock N J, White S P, Noh J S, et al. Perforated covers for propagating pits [J]. J. Electrochem. Soc., 1998, 145: 1101
doi: 10.1149/1.1838423
83 Laycock N J, White S P. Computer simulation of single pit propagation in stainless steel under potentiostatic control [J]. J. Electrochem. Soc., 2001, 148: B264
doi: 10.1149/1.1376119
84 Almuaili F A. Characterisation off 3D pitting corrosion kinetics of stainless steel in chloride containing environments [D]. Manchester: University of Manchester, 2017
85 Gaudet G T, Mo W T, Hatton T A, et al. Mass transfer and electrochemical kinetic interactions in localized pitting corrosion [J]. AIChE J., 1986, 32: 949
doi: 10.1002/aic.690320605
86 Jafarzadeh S, Chen Z G, Bobaru F. Peridynamic modeling of repassivation in pitting corrosion of stainless steel [J]. Corrosion, 2018, 74: 393
doi: 10.5006/2615
87 Deshpande K B. Experimental investigation of galvanic corrosion: comparison between SVET and immersion techniques [J]. Corros. Sci., 2010, 52: 2819
doi: 10.1016/j.corsci.2010.04.023
88 De Meo D, Diyaroglu C, Zhu N, et al. Modelling of stress-corrosion cracking by using peridynamics [J]. Int. J. Hydrog. Energy, 2016, 41: 6593
doi: 10.1016/j.ijhydene.2016.02.154
89 De Meo D, Russo L, Oterkus E, et al. Peridynamics for predicting pit-to-crack transition [A]. 58th AIAA/ASCE/AHS/ASC Structures, Structural Dynamics, and Materials Conference [C]. Grapevine: American Institute of Aeronautics and Astronautics, 2017: 0568
90 Li S M, Chen Z G, Wang F, et al. Analysis of corrosion-induced diffusion layer in ZK60A magnesium alloy [J]. J. Electrochem. Soc., 2016, 163: C784
doi: 10.1149/2.1001613jes
91 Shi C X, Gong Y, Yang Z G, et al. Peridynamic investigation of stress corrosion cracking in carbon steel pipes [J]. Eng. Fract. Mech., 2019, 219: 106604
doi: 10.1016/j.engfracmech.2019.106604
92 Chen Z G, Jafarzadeh S, Zhao J M, et al. A coupled mechano-chemical peridynamic model for pit-to-crack transition in stress-corrosion cracking [J]. J. Mech. Phys. Sol., 2021, 146: 104203
doi: 10.1016/j.jmps.2020.104203
93 Council N R. Research Opportunities in Corrosion Science and Engineering [M]. Washington: The National Academies Press, 2011: 120
94 Xia D H, Ji Y Y, Mao Y C, et al. Localized corrosion mechanism of 2024 aluminum alloy in a simulated dynamic seawater/air interface [J]. Acta Metall. Sin., 2022, DOI: 10.11900/0412.1961.2022.00196
94 夏大海, 計元元, 毛英暢 等. 2024鋁合金在模擬動態海水/大氣界面環境中的局部腐蝕機制 [J]. 金屬學報, 2022, DOI: 10.11900/0412.1961.2022.00196
95 Mao Y C, Zhu Y, Sun S K, et al. Localized corrosion of 5083 Al-alloy in simulated marine splash zone [J]. J. Chin. Soc. Corr. Prot., 2022, DOI: 10.11902/1005.4537.2022.162
95 毛英暢, 祝 鈺, 孫圣凱 等. 5083鋁合金在模擬海洋浪花飛濺區的局部腐蝕行為 [J]. 中國腐蝕與防護學報, 2022, DOI: 10.11902/1005.4537.2022.162
96 Liu W, Wang J. Environmental impact of material corrosion research progress in marine splash zone [J]. J. Chin. Soc. Corr. Prot., 2010, 30: 504
96 劉 薇, 王 佳. 海洋浪濺區環境對材料腐蝕行為影響的研究進展 [J]. 中國腐蝕與防護學報, 2010, 30: 504
免責聲明:本網站所轉載的文字、圖片與視頻資料版權歸原創作者所有,如果涉及侵權,請第一時間聯系本網刪除。
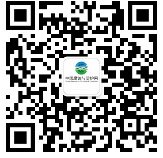
官方微信
《腐蝕與防護網電子期刊》征訂啟事
- 投稿聯系:編輯部
- 電話:010-62316606-806
- 郵箱:fsfhzy666@163.com
- 腐蝕與防護網官方QQ群:140808414