摘要
綜述了Cu-Ni合金海水管系沖刷腐蝕的研究方法、腐蝕機理以及近年來沖刷腐蝕表征的新方法,主要分析了合金成分、微觀組織結構、溫度、pH值、含砂量、硫化物、流速和沖擊角等因素對沖刷腐蝕的影響規律,并對Cu-Ni合金海水沖刷腐蝕的研究趨勢進行展望。
關鍵詞: Cu-Ni合金 ; 沖刷腐蝕 ; 實驗研究 ; 數值模擬 ; 影響因素
1 前言
我國是一個人口眾多,資源相對緊缺的國家,但卻擁有豐富的海洋資源。開發海洋資源,發展沿海經濟,對我國經濟建設和社會發展都具有重大的戰略意義。而海洋資源的開發和利用離不開海上基礎設施的建設,目前海上基礎設施采用的絕大多數材料為金屬材料。早期的海水管道系統多用碳鋼、鑄鐵建造,雖然初始投入成本低,但因這些材料的耐海水腐蝕性能差,抗海生物污損能力低,不僅浪費大量的人力物力,縮短工程壽命,而且還常常釀成重大事故[1]。Cu-Ni合金因其耐流動海水腐蝕性能比較好,在船舶與海洋工程海水管路系統中的應用范圍逐漸擴大,如海水淡化處理管道、冷凝器管、海電廠的熱交換器等。據統計,Cu-Ni合金在商船和軍船的用量占船總重比例的2%~3%[2]。
但是Cu-Ni合金在海水環境服役過程中同樣會發生腐蝕問題,甚至造成嚴重的泄事故,如船舶海水管系,以往船舶海水管路選用TUP紫銅管,其腐蝕是常見問題;船用冷凝器管采用B30銅鎳合金,在東海海域含砂量很高的海水環境中使用存在嚴重腐蝕[3,4]。近些年海水管系多采用耐蝕性能更好的B10銅鎳合金,能夠較好地滿足船舶與海洋工程中高鹽、高壓、高速環境下的使用要求,但仍存在一定的沖刷腐蝕現象。海水管路的頻繁腐蝕穿孔,嚴重影響設備的正常使用,減少了船舶在航率,造成事故隱患[5]。由于材料在海水中的沖刷腐蝕涉及因素錯綜復雜,如流體的流速[6-9]、含沙量[6-8,10]、沙粒尺寸[7,8]、沖擊角[11-14]、pH值[14]、溫度[8,9,15]以及材料的組成[10,13]、微觀結構[16-18]、熱處理方法[19]等,Cu-Ni合金在海水中的腐蝕規律并不完全清楚[3,5],因此掌握Cu-Ni合金的沖刷腐蝕機理,找到有針對性的切實可行的防護措施和方法,對發展海上運輸、港口碼頭和海上石油鉆井平臺的建設有十分重要的意義。本文綜述了近年來國內外海洋腐蝕與防護工作人員在Cu-Ni合金海水沖刷腐蝕方面的研究工作和成果,并對其進行展望。
2 Cu-Ni合金海水沖刷腐蝕研究方法
2.1 實驗研究法
實驗研究法的共同點是通過將材料置于特定的試驗裝置中,利用相應的技術手段讓介質和試樣之間產生一種相對運動[20,21],通過失重和電化學測量等技術手段,研究Cu-Ni合金的沖刷腐蝕過程。目前,開展沖刷腐蝕較常用的試驗裝置有3類:旋轉試驗裝置、噴射沖刷試驗裝置和管流試驗裝置,不同的試驗裝置各有優缺點和適用范圍[22,23]。旋轉試驗裝置因為裝置結構簡單、價格低廉、所需溶液少、周期短等優點,國內外很多都采用旋轉試驗裝置;但其對電機平穩性和轉軸垂直度要求很高,旋轉引起的渦流影響大,實驗工況和管道實際工況差距較大[22,24]。噴射式試驗裝置適合于高流速下的沖刷腐蝕研究[25],但不能很好地模擬管道實際工況條件,實驗結果往往比實際情況更嚴重[26]。管流式試驗裝置能很好模擬實際管道工況條件,可精確控制流速,有良好的流體力學模型,實驗結果有很強的實用價值,但由于裝置建設費用和操作費用高[27]、占據空間較大等缺點,限制了其使用。
在沖刷腐蝕過程、結果的采集與記錄方面常采用失重法和電化學測量法。失重法操作簡單、直接、容易實現,在沖刷腐蝕研究中應用最廣,但其實驗周期較長[28]。電化學測試法包括極化曲線、電化學阻抗和電化學噪聲等測量方法。電化學方法不僅可用于定量測定沖刷腐蝕速率的大小,還可以用于深入研究沖刷腐蝕的機理,實驗周期短[22],但用于沖刷腐蝕的三電極體系難以構造且測量結果容易受到人為及環境因素的干擾。
沖刷腐蝕樣品的形貌、微觀組織結構、腐蝕產物的表征方法種類繁多,有表面光度儀、掃描電鏡 (SEM)、光學顯微鏡、透射電鏡 (TEM)、X射線光電子能譜 (XPS)、X射線衍射儀 (XRD)、Raman光譜等,不同的表征方法有不同的適用范圍。值得注意的是,近年來,聲發射技術被逐漸應用于材料的沖刷腐蝕過程的表征,如Burstein和Sasaki[29]通過測量電化學腐蝕電流的瞬變和聲發射信號的瞬變關系研究了流體沖擊角對304不銹鋼的沖刷腐蝕的影響;Frederic等[30]利用聲發射技術對碳鋼在濃硫酸中沖刷腐蝕的活化鈍化轉變過程進行了研究,結果表明流體流速超過臨界值后,鈍化膜破壞,聲信號也隨之急劇增大;Mohamed等[31]對碳鋼彎頭的沖刷腐蝕過程進行了聲發射技術監測,得到實驗條件下沖刷腐蝕的振幅范圍和頻率;Ukpai等[32,33]利用聲發射法研究了X65鋼的沖刷腐蝕,發現沖刷腐蝕速率與聲發射能量隨時間的變化規律比較同步,聲發射能量隨流速、含沙量的增大而增加。
2.2 數值模擬法
隨著計算機技術的快速發展,數值模擬方法在沖刷腐蝕的研究中被越發廣泛地應用。數值模擬研究是基于連續相流場計算,通過對流態進行數值仿真模擬計算,從而得出管道中流體速度場、壓力場、溫度場、固體顆粒和沖刷腐蝕區域的分布,達到預測沖刷腐蝕的方法[28]。與單純的理論計算相比,數值模擬在研究流體力學問題時可以得到數值解,更能適應研究復雜工程問題的需要。與實驗相比,數值模擬不會受到實驗條件的種種限制,能夠很好地指導實驗,更能大幅度節省實驗費用和時間,特別是對實驗難以完成的某些測量,則可以用計算機進行數值模擬。在管道的沖刷腐蝕研究方面,數值模擬的優點還在于能夠清晰地觀察到易腐蝕部位的流場情況,方便提取流動參數,如壓力、剪切應力和紊流度等,可結合流動情況和參數變化規律深入分析腐蝕原因,同時還能較為直觀地給出顆粒相的運動信息,如顆粒對過流部件壁面的碰撞作用等,進而對沖刷腐蝕速率進行計算和預測,這有利于進一步揭示多相流中沖刷腐蝕的規律及機理[28]。
目前,開展沖刷腐蝕數值模擬的主要方式有借助商用計算機流體動力學 (CFD) 軟件和自行開發模擬仿真軟件兩種。Ferng等[34]借助CFD方法計算獲得了管線內的流動參數,并將其與實測的局部壁面減薄數據對比,通過兩者之間的關系進行研究和拓展,為管壁檢測方案的設計提供指導。Davis等[35]利用CFD計算了O在流體中的擴散及向反應面轉移的特點,研究了收縮-擴張幾何模型內的沖刷腐蝕情況,獲得的沖刷腐蝕與實驗結果取得較好的一致性。Bozzini等[36]運用CFD軟件模擬了兩種互不相容液體、氣體、固體顆粒等四相流對管道彎頭的沖刷腐蝕,分別研究了氣相體積分數、流體流速、固相含量等因素對腐蝕的影響。Hu等[37]借助CFD模擬得到彎曲及焊接點部位的流動行為,從而輔助分析了管道失效的原因。北京化工大學團隊利用自行編制的程序分別開展了層流、紊流條件下,單相或兩相流中,碳鋼、不銹鋼等材料的流動腐蝕數值研究,探討了表面剪切力與腐蝕速率的關系,得到的結果與實測值有較好的一致性[38-41]。
在應用數值模擬法開展沖刷腐蝕研究中,也存在一定的問題,主要為邊界假設和模型依賴。
邊界假設:數值模擬計算模擬的邊界條件設定需要基于一定的假設,如顆粒的形狀是球形且直徑一致、忽略顆粒間的相互作用,因而要求介質中顆粒的含量要低。在顆粒含量較低時,固相對平板的沖擊不會影響到主流場;流體中各相是均勻混合的等[28]。而這些假設幾乎與實際情況不符,得到的結果也會有偏差。
模型依賴:數值模擬中腐蝕與沖刷的計算均要基于一定的計算模擬,如雙相流中腐蝕動力學模型,固體顆粒對金屬表面沖刷的模型等。而隨著研究體系與研究條件的不同,模型外推能力和適用性有限,因此目前還沒有一套通用的模型用于計算。此外,由于協同機制的認識有限且因材料而異,因此目前尚未提出一個考慮了沖刷和腐蝕協同作用的計算模型,也就無法開展協同作用的數值模擬計算[42,43]。
3 Cu-Ni合金海水沖刷腐蝕機理
在沖刷腐蝕過程中,材料的流失有腐蝕和沖刷兩種方式,腐蝕是材料以離子形式離開材料表面,而沖刷則是材料表面的腐蝕產物以固體顆粒形式脫離材料表面。沖刷腐蝕是材料受沖刷和腐蝕協同作用的結果,而不是沖刷作用和腐蝕作用兩者分別發生時的簡單疊加,在大多數的沖刷腐蝕過程中,材料的總失重要大于純沖刷與純腐蝕引起的失重之和[44,45]。純沖刷和純腐蝕之間的協同作用包括兩方面:一是沖刷的發生促進腐蝕反應,二是腐蝕也促進沖刷過程,其作用機制概括為如下兩種模式。
(1) 沖刷對腐蝕的影響
沖刷加速了傳質過程,促進去極化劑到達材料表面,促進腐蝕產物從材料表面剝落,從而引起加速腐蝕。沖刷過程中,沖刷介質會對材料表面施加一定的切應力。在沖刷的力學作用下,材料表面的鈍化膜將減薄或破裂,使得材料基體表面暴露在腐蝕介質中,加速了新的鈍化膜的形成,隨后這層鈍化膜又被沖刷作用所破壞,如此這兩個過程交替進行。如果材料形成鈍化膜的速率小于沖刷作用導致其剝離的速率,則由于沖刷造成的失重將非常顯著。
沖刷會導致材料產生一定程度的塑形變形、位錯的聚集和局部能量升高,形成應變電池。特別是當腐蝕介質中含有固體相時,沖刷作用會造成材料表面形成凹凸不平的沖蝕坑,進而增加材料的比表面積,即使腐蝕速率保持不變,也會因暴露面積增加而加劇腐蝕。
(2) 腐蝕對沖刷的影響
腐蝕將粗化材料表面,使材料表面的腐蝕不均勻,尤其是在材料相界面或缺陷處,容易出現局部腐蝕,造成微湍流的形成,進而促進沖刷過程;對于含碳化物作為基體的界面,相界面處由于腐蝕作用而較容易被流動介質沖刷剝落。
腐蝕將弱化材料的晶界、相界,破壞材料的表面結構,使其耐磨的硬化相暴露,或者溶解材料表面的加工硬化層,凸出基體表面,降低材料的力學性能及基體疲勞強度,使其易折斷甚至脫落,減小了沖刷時所受的阻力,進而促進沖刷。另外,腐蝕所形成的氧化層附著在材料表面,較易被高流速的流體所沖去,從而使腐蝕速率增大。
目前,對液/固兩相流沖刷腐蝕的組成形成了比較一致的觀點[46-52]:金屬的沖刷腐蝕總失重由純腐蝕、純沖刷、腐蝕對沖刷的影響和沖刷對腐蝕的影響4部分組成,即:
式中,T為總失重速率,通過失重測量得到;C為總腐蝕速率,通過電化學阻抗譜或極化曲線計算得到;E為總沖刷速率;C0為純腐蝕速率,通過測定試片在不含固體顆粒的靜止溶液中的失重得到[49,53],也可通過測定試片在不含固體顆粒的流動溶液中的失重得到[54];E0為純沖刷速率,在試片施加陰極保護條件下,通過測定試片失重獲得;Ce為沖刷加速腐蝕的速率;Ec為腐蝕加速沖刷的速率。
Stack等[55,56]對沖刷腐蝕交互作用機理做了進一步研究,根據沖刷磨損與電化學腐蝕在整個沖刷腐蝕中的貢獻程度,將沖刷腐蝕機制分為以下4類:(1) C/E<0.1時為沖刷磨損控制;(2) 0.1≤C/E<1.0時為沖刷磨損-電化學混合控制;(3) 1.0≤C/E<10.0時為電化學-沖刷磨損混合控制;(4) C/E≥10.0時為電化學控制。
4 Cu-Ni合金海水沖刷腐蝕影響因素
沖刷腐蝕的協同作用使其過程變得異常復雜,影響因素眾多,主要因素有材料自身因素,如材料本身的化學成份、力學性能 (特別是硬度)、組織結構、耐蝕性能、表面粗糙度等;液相因素,如腐蝕介質的溫度、溶解氧、pH值、各種活性離子的濃度、粘度、密度、固相和氣相在液相中的含量、固相顆粒硬度和粒度等;流體力學因素,如管道彎頭部位、流體的流速和流態等均會在材料表面產生不同的力學效果,進而影響材料的沖刷腐蝕。
4.1 材料因素的影響
4.1.1 合金成分 Crousier等[57]研究了不同Ni含量的Cu-Ni合金在NaCl溶液中的電化學行為,發現純Cu和Cu-Ni合金的極化曲線在陽極極化部分均出現了電流平臺,且隨Ni含量的增加,電流平臺值降低;當Ni含量在10%時,合金的電流平臺較寬,表明合金鈍態性能穩定;當Ni含量為30%時,電流平臺值與純Ni的鈍化電流值相近,結果表明,Ni是導致Cu-Ni合金鈍化現象的主要原因。研究人員[58,59]對不同Fe含量的Cu-Ni合金的耐海水腐蝕性能進行測試,結果表明,添加0.5%~2%的Fe可以顯著改善Cu-Ni合金的耐流動海水沖刷腐蝕性能。Efird[60]對比研究了不同Ni和Fe含量的Cu-Ni合金在靜態和高流速海水的腐蝕實驗后發現,未添加Fe的合金形成的腐蝕產物中O含量高;添加一定量Fe的合金所形成的腐蝕產物Ni含量高。B30銅鎳合金中添加0.5%~2%Fe能夠明顯改善材料在流動海水中的耐蝕性,并且在靜態海水中也得到證實[24,58,59]。實際上,無論是B30銅鎳合金還是B10銅鎳合金均添加一定量Fe,添加少量的Fe有益于耐蝕性,其作用存在兩種觀點:一種觀點認為固溶態Fe的作用在于形成含水氧化鐵的腐蝕產物膜,這種化合物充當陽極抑制劑[58];另一種觀點認為Fe和Ni一樣,能夠摻雜到缺陷的Cu2O點陣中,增加腐蝕產物膜的陽極和陰極阻力[61]。研究[24]表明,Mn能顯著提高Cu-Ni合金抗沖擊腐蝕性能,并且當Fe含量比較低時,Mn能起到替代Fe的作用;Mn還能消除Cu-Ni合金中過剩C的影響。另外微合金化可以提高Cu-Ni合金的耐沖蝕性,如添加微量的B[62,63]。
4.1.2 微觀組織結構 從相圖上看,Cu-Ni合金為無限互溶的連續固溶體。但在322 ℃以下,該合金存在一個產生亞穩分解的成分-溫度區域。當添加某些合金元素如Fe、Mn等將改變亞穩分解的成分-溫度區域的大小和位置。Fe在Cu-Ni合金中的溶解度很小,通常B30銅鎳合金中Fe溶解量為0.5%~1.0%,B10銅鎳合金中Fe溶解量為1.0%~1.5%。當Fe完全固溶時,合金表現出良好的耐蝕性;若合金出現沉淀態的Fe,所形成的腐蝕產物無Ni的富集且顏色變暗[64]。Cu-Ni合金在一定條件下沉淀出極小的Ni-Fe富集相,該Ni-Fe富集相不僅明顯影響合金的強度,而且降低合金的耐蝕性[24]。在海水中長時間暴露結果表明:B10銅鎳合金為均勻固溶體時腐蝕電位在活化方向略有變化,Rp-1值低且穩定,隨Fe含量增加而增大;連續沉淀的合金腐蝕電位在活化方向出現一個電位躍遷,在某些情況下,電位躍遷之后觀察到強烈的電位波動,Rp-1在含Fe量為2.0%和2.5%時達到最大;在晶界上存在不連續沉淀物的合金腐蝕電位在活化方向出現一個電位躍遷,并且Rp-1值始終較高且與含Fe量無關[24]。在海水中長時間暴露結果還表明,不連續沉淀的B10銅鎳合金形成的黑色腐蝕產物膜厚且多孔疏松而易脫落,其下為桔黃色晶體[24]。Cu-Ni合金沉淀相析出的條件尚未清楚,目前還未找到有效地抑制Cu-Ni合金沉淀特別是不連續沉淀發生的途徑。
4.2 液相因素的影響
4.2.1 溫度 溫度對Cu-Ni合金的影響主要表現在腐蝕反應的動力學參數、氧的擴散系數及溶解量等方面。其中腐蝕反應的動力學參數和氧的擴散系數隨著溫度的上升而逐漸增高,但是溫度升高時,氧會逐漸析出,使氧的溶解量降低;而且Cu-Ni合金的表面膜特性及再鈍化能力也會隨著溫度的變化而發生轉變[26]。溫度對Cu-Ni合金腐蝕行為影響的研究結果各異,即溫度升高,Cu-Ni合金腐蝕速率減小、增加或保持不變。這些差異是由于實驗條件不同造成的,包括水流、pH值變化、溶解氧等。Gat等[65]將材料按其沖刷腐蝕性能隨著溫度升高的變化趨勢分為二類:第一類材料耐沖刷腐蝕性能隨溫度升高而降低;第二類材料耐沖刷腐蝕性能則隨溫度升高而增強。并認為沖刷腐蝕過程并不是由單一機制完成,而是幾種機制共同完成的,但會有其中一種機制在沖刷腐蝕過程中占主導作用:因此,隨著溫度的升高,材料的沖刷腐蝕速率是增大還是減小取決于占主導作用的機制,而且主導機制也會隨溫度變化而發生變化。
4.2.2 pH值 國內外開展了眾多pH值對Cu-Ni合金耐蝕性影響的研究,Pehkonen等[66]詳細研究了溶液的pH值對白銅耐腐蝕性能的影響;Efird[67]對90-10和70-30 Cu-Ni合金在海水中的電位-pH值進行了研究,顯示在特定的電位下,溶液pH值不同時合金的腐蝕規律可能不同;遲長云等[68]研究了pH值變化對B30銅鎳合金腐蝕規律的影響;陳海燕等[69]研究了pH值變化對BFe30-1-1合金在NaCl溶液中的腐蝕規律。羅宗強等[70]研究了pH值對Cu-17Ni-3Al-X耐磨鑄造銅合金腐蝕的影響,其研究結果表明在3.5%NaCl溶液中,隨著溶液pH 值的升高,合金腐蝕速率逐漸降低;在中性和堿性溶液中,合金具有優異的耐蝕性;當溶液為強酸性 (pH值為3) 時,合金表面不易形成致密的保護膜;當溶液pH值為6,8和10時,合金表面產生Al、富Ni的Cu2O和Cu2(OH)3Cl腐蝕產物膜;當溶液為強堿性 (pH值為12) 時,合金容易形成致密的Cu2O膜。在不同pH值溶液中合金的腐蝕速率差異,主要是因為銅合金表面腐蝕膜的不同及銅合金電化學反應過程中陰極反應引起的;銅合金在酸性溶液中,于第二相附近出現晶間腐蝕[2]。
4.2.3 含砂量 海水含砂量對Cu-Ni合金沖刷腐蝕的影響主要表現在對切應力的影響,砂粒的硬度、粒徑大小、鋒利性以及濃度的變化均能改變海水對Cu-Ni合金表面的剪切應力的大小[26]。一般認為,砂粒硬度越大,對Cu-Ni合金表面的切應力也越大,Cu-Ni合金的腐蝕速率也越大。多角粒子的鋒利度要比圓形粒子的大得多,因此,砂粒的菱角越多,海水對Cu-Ni合金表面的切應力也越大,Cu-Ni合金的腐蝕速率也越大。研究[71-73]表明,隨著砂粒濃度增大,砂粒與Cu-Ni合金表面接觸的頻率和次數也逐漸增大,使Cu-Ni合金腐蝕速率也增大;但砂粒濃度進一步增大,在高濃度條件下,因砂粒之間的相互影響作用而產生了屏蔽效應,使對材料表面的切應力降低,反而使材料腐蝕速率降低。同時,由于砂粒的存在,使Cu-Ni合金表面附近的擴散層加劇了攪動,促進了海水中的離子與Cu-Ni合金表面的接觸更加頻繁,從而促進了腐蝕反應,使Cu-Ni合金腐蝕速率加大。
然而在含砂量較高,砂粒度較大的冷卻水中,當流速較高時,由電化學腐蝕與砂的磨損引起材料流失的比例關系,仍存在爭議。通常認為含砂量增加或砂粒度增大,腐蝕速率隨之增大。
4.2.4 硫化物 硫化物進入海水中途徑較多,如腐爛的動植物、工業廢棄物、自然產生硫酸鹽細菌還原等。硫化物加速Cu-Ni合金腐蝕的現象在自然海水和人工海水中都得到證實[74]。硫化物在海水中存在形式的多樣性使硫化物對Cu-Ni合金腐蝕影響的研究復雜化。在無氧的情況下,海水中的硫化物使Cu-Ni合金腐蝕電位向活化方向遷移[75]。在活化電位時,陰極反應依賴于氫離子還原,因此,即使在無氧時,腐蝕反應仍能進行。Macdonald等[75]研究表明,在硫化物含量高達55 mg/L、流速為5 m/s的海水中合金的腐蝕速率并不很高。此結果無法解釋艦船中Cu-Ni合金的早期失效行為。因此,Cu-Ni合金腐蝕加速的原因可能是由于其與硫化物的氧化物接觸,而并不是簡單的由硫化物單獨作用產生的。硫化物及其氧化產物導致形成多孔的非保護性的Cu2S膜,它阻礙保護性的氧化膜的正常生長,從而使腐蝕加速[24]。
4.3 流體力學因素的影響
4.3.1 流速 Cu-Ni合金是一類耐沖刷腐蝕性能較為優良的海洋用工程材料,但一般認為其在海水中使用存在一個臨界流速值,超過臨界流速值,材料沖刷腐蝕率明顯增大而快速失效。Cu-Ni合金相對臨界流速值受諸多因素影響,難以精確測定[24,76]。
目前,學術界對沖刷腐蝕臨界流速問題產生的機制存在一定的分歧,Efird[77]認為流動的海水在合金表面產生剪切應力,隨流速的增加,剪切應力增加。剪切力超過一定值使得合金表面腐蝕產物膜機械分離。因此,腐蝕產物的力學性能決定了臨界流速值,即臨界流動速度對應的剪切應力略超過腐蝕產物膜與基體的結合力。Efird計算出了B10銅鎳合金的臨界剪切應力為43.1 Nm-2。Tuthill[78]測試了Cu-Ni合金在海水環境下不同管徑下的臨界剪切力值,發現管徑越大,銅合金允許海水的流速越高。Bianchi等[79]認為高速流動的海水傳質系數大,使得表面的pH值降低以及表面膜通過可溶性的Cu的化合物擴散使溶解度增加;在侵蝕腔內,局部腐蝕形成活化-鈍化電池,這種電池具有自催化效應。Perkins等[80]認為在流動海水中,如果其中氣泡的尺寸大于界面層的厚度,則氣泡對保護層產生機械破壞作用。所產生的力可能破壞水力學上的界面層。再加上局部液體的直接沖擊和保護層破壞等因素,使腐蝕不斷發展。Syrett和Wing[81]認為Cu-Ni合金在流動的海水中存在一個臨界的破裂電位Eb。即在極化曲線上陽極電流突然上升的電位。當開路電位Ec>Eb時發生局部腐蝕,腐蝕速率很高;反之,發生均勻腐蝕且腐蝕速率很低。此外,還測得了不同流速以及不同暴露時間下B10銅鎳合金的自腐蝕電位和破裂電位,并且加以比較,結果表明:流速越高、暴露時間越長就越易發生局部腐蝕[24]。
4.3.2 沖擊角 含沙流體中,流體沖刷作用對沖刷磨損影響較大[82]。流體沖刷角對沖刷腐蝕的影響主要表現為剪切應力和正應力。剪切應力通過削薄甚至移除鋼表面的氧化膜而增強沖刷腐蝕過程。正應力則是通過撞擊或損傷電極表面而產生孔洞。沖刷角小于45°時,剪切應力占主導地位;大于45°時,正應力占主導地位[83,84]。
Tang等[83]認為,沖刷角從30°增至45°時,腐蝕速率隨沖刷角增大而增大,45°增至90°的過程中,沖刷腐蝕速率先隨沖刷角增大而降低,然后隨其增大而增大。研究[84,85]表明,沖刷角較小 (50°) 時,易產生較粗糙的電極表面,與光滑的金屬表面相比,表面點蝕坑更深且直徑更小,因此粗糙表面更容易產生可以發展到正常生長階段的點蝕坑,從而降低點蝕電勢;沖刷角較大 (90°) 時,更容易發生點蝕。
尹承軍[26]研究了沖擊角度對B10合金沖刷腐蝕行為的影響,結果表明在潔凈海水沖刷腐蝕過程中,海水的流動性促進了腐蝕產物膜的形成與溶解過程;也增強了海水對材料表面的沖刷作用,使得表面腐蝕產物膜的形成與破壞為一動態過程。而在含砂條件下,砂粒的存在增強了海水對材料表面的沖刷作用,使材料表面產生沖擊坑。且隨著沖擊角度的增大,沖擊坑的形狀逐漸由馬蹄狀轉變為點狀,穩定致密的膜層只能對B10合金在潔凈海水沖刷過程中起保護作用。
5 展望
(1) 實際工況中,Cu-Ni合金管的沖刷腐蝕破壞容易發生在彎管處,且破壞形式更復雜,今后應更多致力于彎管等特殊管道部位的沖刷腐蝕的研究,深入研究沖刷腐蝕體系各參數的影響規律,定量研究金屬管道的沖刷腐蝕。
(2) 創新發展實驗研究方法,設計更符合現場管道實際工況的管流式試驗裝置,將聲發射技術及原位觀測技術等引入Cu-Ni合金實驗研究中,實現對沖刷腐蝕過程的在線測量和動態觀測,有助于揭示沖刷腐蝕機理。
(3) 目前在Cu-Ni合金的沖刷腐蝕研究中關于流速、攻角、固相顆粒、流體流態等因素研究較多,但如溫度、壓力、溶解氧等環境因素影響機理的研究開展較少,針對工業化發展的新要求,對于高速、高溫、高鹽、高壓等極端嚴酷條件下Cu-Ni合金沖刷腐蝕的研究顯得尤為匱乏。今后,對Cu-Ni合金沖刷腐蝕的研究將更加貼近實際工況,高速、高溫、高鹽、高壓等極端嚴酷環境條件下Cu-Ni合金的沖刷腐蝕將成為研究重點。
The authors have declared that no competing interests eixt
免責聲明:本網站所轉載的文字、圖片與視頻資料版權歸原創作者所有,如果涉及侵權,請第一時間聯系本網刪除。
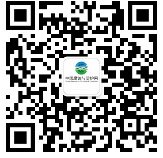
官方微信
《腐蝕與防護網電子期刊》征訂啟事
- 投稿聯系:編輯部
- 電話:010-62316606-806
- 郵箱:fsfhzy666@163.com
- 腐蝕與防護網官方QQ群:140808414