輕金屬通常是指相對(duì)密度在4.5以下的金屬,主要包括鋁、鎂、鈦等金屬。 伴隨著國民經(jīng)濟(jì)和國防現(xiàn)代化的發(fā)展 ,輕金屬材料的應(yīng)用越來越廣泛 。鎂合金被譽(yù)為“21世紀(jì)的綠色工程材料”,是目前最輕的金屬結(jié)構(gòu)材料,具有密度小、比強(qiáng)度和比剛度高、阻尼減振性好、導(dǎo)熱及電磁屏蔽效果佳、機(jī)加工性能優(yōu)良、零件尺寸穩(wěn)定 、易回收等優(yōu)點(diǎn)。廣泛應(yīng)用于航空航天、國防、汽車工業(yè)、電子通信、醫(yī)療及一般民用產(chǎn)品等行業(yè)。
我國是鎂資源大國,在鎂及鎂合金工業(yè)應(yīng)用方面擁有得天獨(dú)厚的優(yōu)勢(shì)。然而在國內(nèi),鎂合金的應(yīng)用現(xiàn)狀和預(yù)期仍然存在巨大的差距,這是因?yàn)殒V及鎂合金還存在一些固有缺點(diǎn),如鎂合金化學(xué)和電化學(xué)活性很高,耐腐蝕、耐磨性較差等,很大程度上制約了鎂合金的開發(fā)和應(yīng)用。因而,在目前全球環(huán)境惡化和資源短缺問題日益嚴(yán)峻的壓力下,加強(qiáng)對(duì)鎂合金耐蝕耐磨性能的研究,積極探索提高鎂合金耐蝕性能的方法途徑,對(duì)拓寬鎂合金的應(yīng)用范圍并充分發(fā)揮其性能優(yōu)勢(shì)有著十分重要的現(xiàn)實(shí)意義。
通常而言,控制鎂合金的成分,合理控制材料制備工藝,可以改善鎂合金的綜合性能,但會(huì)使生產(chǎn)成本大幅增加。由于金屬材料的腐蝕、磨損和疲勞斷裂等材料的失穩(wěn)多始于表面,因此通過對(duì)材料表面處理可進(jìn)一步提高鎂及鎂合金的使用特性,具有顯著的經(jīng)濟(jì)和社會(huì)效益。鎂合金常用的表面處理工藝主要有電鍍、化學(xué)轉(zhuǎn)化、陽極氧化、氣相沉積、微弧氧化、激光表面處理等。
鎂合金:向金屬鎂中加入少量的其他金屬 ,如鋁、鋅、錳、鋯等元素時(shí),形成以鎂為基的合金,即鎂合金,可以大大提高鎂合金的強(qiáng)度,因此用于結(jié)構(gòu)材料的一般為鎂合金。密度≈鋁的2/3,鋼的1/4,是目前最輕的金屬結(jié)構(gòu)材料;鎂合金還具有比強(qiáng)度高、導(dǎo)熱導(dǎo)電性能好、阻尼減振、電磁屏蔽、易于機(jī)械加工和容易回收等優(yōu)點(diǎn),
由于鎂化學(xué)性質(zhì)和電化學(xué)活性高,在大氣中特別是在潮濕和沿海地區(qū)很容易受到腐蝕這限制了鎂合金的廣泛應(yīng)用。控制鎂合金的成分和形成均勻的組織可以提高鎂合金的抗蝕 ,但鎂合金的最終腐蝕防護(hù)常需要進(jìn)行表面處理,以便改善鎂合金的性能,擴(kuò)大鎂合金的應(yīng)用領(lǐng)域,提高鎂合金材料的使用壽命。
金屬鎂的應(yīng)用主要集中在鎂合金生產(chǎn) 、鋁合金生產(chǎn) 、煉鋼脫硫、稀土合金、金屬還原、腐蝕保護(hù)及其他領(lǐng)域。如很多鋼廠都采用鎂脫硫,使用鎂粒的脫硫效果 比碳化鈣好。使用鎂犧牲陽極進(jìn)行陰極保護(hù),是一種有效防止金屬腐蝕的方法 ,鎂犧牲陽極廣泛用于石油管道、天然氣、煤氣管道和儲(chǔ)罐、冶煉廠、加油站的腐蝕防護(hù)以及熱水器、換熱器、蒸發(fā)器、鍋爐等設(shè)備。目前鎂合金已成為新型材料的發(fā)展方向之一。“十三五”規(guī)劃指出鎂合金材料重點(diǎn)發(fā)展方向?yàn)椋汉娇蘸教煊酶邚?qiáng)鎂合金大尺寸復(fù)雜鑄造件 ,高強(qiáng)耐熱鎂合金大規(guī)格擠壓型材/鍛件,3C產(chǎn)品用鎂合金精密壓鑄件,大卷重、低成本、高成形性鎂合金板帶材,汽車輕量化結(jié)構(gòu)件用鎂合金精密壓鑄件等。同時(shí),“十三五” 規(guī)劃預(yù)測鎂金屬年增速7.1%,高于十種有色金屬平均增速 4.1%。這是因?yàn)殒V合金具有良好的輕量性、切削性、耐蝕性、減振性 、尺寸穩(wěn)定性和耐沖擊性,遠(yuǎn)遠(yuǎn)優(yōu)于其他材料。這些特性使得鎂合金廣泛應(yīng)用于航空航天、汽車、電子通信、 醫(yī)療、軍事等領(lǐng)域。
針對(duì)鎂合金腐蝕的特點(diǎn),國內(nèi)外的研究者提出了提高鎂合金耐腐蝕性的主要方法:
①開發(fā)新的合金或提高鎂合金的純度 ;
②采用快速凝固技術(shù);
③采用表面強(qiáng)化技術(shù)。
前兩種方法主要是提高整體部件的耐蝕性,而后一種方法是在整體提高的基礎(chǔ)上,通過不同方法在表面形成一種很薄的功能層來提高鎂合金的耐蝕性。
鎂合金的腐蝕形態(tài)包括全面腐蝕和局部腐蝕。通常而言,全面腐蝕將會(huì)造成局部腐蝕的產(chǎn)生,而局部腐蝕則更容易受到弱電解質(zhì)和小陽極/陰極相對(duì)面積比的影響。局部腐蝕又分為電偶腐蝕 、點(diǎn)蝕 、絲狀腐蝕 、應(yīng)力腐蝕開裂與腐蝕疲勞等。
針對(duì)鎂合金腐蝕的特點(diǎn),表面強(qiáng)化技術(shù)是目前鎂合金防腐蝕最常用的技術(shù)。而用于鎂合金防護(hù)表面強(qiáng)化技術(shù)大致有陽極 氧化處理 、化學(xué)轉(zhuǎn)化處理 、微弧氧化處理 、表面滲層 、電鍍和化學(xué)鍍處理 、熱噴涂 、有機(jī)涂層 、氣相沉積 、激光處理等 ,這些方法各有其優(yōu)缺點(diǎn)。
鎂及鎂合金基體表面狀態(tài)和清潔程度是保證鎂合金強(qiáng)化處理后膜層質(zhì)量的先決條件。如果基體表面粗糙、銹蝕或有油污存在,將不會(huì)得到光亮、平滑、結(jié)合力良好和耐蝕性高的膜層。實(shí)踐證明,當(dāng)膜層出現(xiàn)鼓泡、脫落、花斑和耐蝕性差等現(xiàn)象時(shí),大多是因前處理不當(dāng)造成的。因此,要想得到高質(zhì)量的膜層,必須加強(qiáng)前處理的管理,按工藝要求嚴(yán)格執(zhí)行。同其他金屬前處理工藝相似,鎂及鎂合金基體前處理工藝一般主要有以下幾個(gè)方面。 (1)粗糙表面的整平 包括磨光、拋光(機(jī)械拋光 、化學(xué)拋光和電化學(xué)拋光)、滾光和噴砂等。 (2)脫脂包括有機(jī)溶劑脫脂 、化學(xué)脫脂和電化學(xué)脫脂等。 (3)浸蝕包括強(qiáng)浸蝕、電化學(xué)浸蝕和弱浸蝕。 鎂合金表面強(qiáng)化前處理工藝流程一般為: 由于鎂合金表面狀態(tài)不相同,其強(qiáng)化處理技術(shù)不同,對(duì)膜層質(zhì)量的要求也不 一樣,所以要根據(jù)鎂合金基體的特性、表面狀態(tài)及對(duì)膜層的質(zhì)量要求,有針對(duì)性地選擇適宜的鍍前處理工藝。
在鎂合金件成形過程中,工件表面或多或少附著有氧化 膜、脫模劑、離型劑 等雜質(zhì),這些雜質(zhì)會(huì)在后續(xù)處理如微弧氧化、電鍍等處理過程中脫落并進(jìn)人電解液 ,影響電解液的壽命。此外,鎂合金表面的自然氧化物疏松多孔和化學(xué)成分不均勻等特性也通常會(huì)導(dǎo)致后續(xù)表面處理結(jié)合力不佳。因而對(duì)鎂合金表面進(jìn)行適當(dāng)?shù)恼剑绱蚰ァ娚暗阮A(yù)處理 ,則能很好地改善膜層的結(jié)合力和耐蝕性能等。對(duì)于鎂合金的表面整平 ,目前應(yīng)用較多的有噴砂、磨光等。
*由于鎂合金硬度不高 ,在機(jī)械磨光工序中稍不注意就會(huì)破壞鎂合金壓鑄零件表面的致密層,使鑄件表層的微細(xì)裂紋、氣孔外露,造成涂裝表面出現(xiàn)起泡 、縮孔等缺陷,因此在對(duì)鎂合金進(jìn)行表面整平時(shí) ,一定要嚴(yán)格控制整平工藝,確保不降低其耐蝕性能。此外,由于鎂合金粉末燃點(diǎn)低 ,與氧的親和力高 ,在噴丸、機(jī)械磨光過程中容易發(fā)生燃燒 ,甚至引起爆炸,因此操作時(shí)還應(yīng)注意安全。
鎂及鎂合金部件在加工及存放等過程中,不可避免地會(huì)黏附各種油污,如礦物油、植物油和動(dòng)物油等。而這些油污的存在通常會(huì)影響后續(xù)表面處理的質(zhì)量。因此在對(duì)鎂合金件進(jìn)行表面強(qiáng)化處理前通常需要進(jìn)行脫脂處理。
鎂及鎂合金化學(xué)性質(zhì)活潑,只有在 pH>12的堿溶液中生成 Mg(OH):才趨于穩(wěn)定,在其他水溶液中都不穩(wěn)定。在純凈的自來水中浸泡也會(huì)發(fā)生腐蝕 ;在酸中,鎂與 H+發(fā)生激烈的氧化還原反應(yīng),析出大量氫氣與熱量 ,會(huì)引起零件的過蝕 ,甚至發(fā)生自燃 、爆炸事故 。因而,目前生產(chǎn)上鎂合金化學(xué)脫脂一般使用堿性脫脂法。這種方法的實(shí)質(zhì)是依靠皂化和乳化作用 ,前者可以除去動(dòng)植物油 ,后者可以除去礦物油。堿性脫脂溶液通常含有氫氧化鈉 、碳酸鈉、磷酸三鈉、焦磷酸鈉、硅酸鈉以及其他表面活性劑等。
表1 鎂合金堿性脫脂液組成及工藝
表2 乳化液脫脂工藝
將金屬工件浸入酸、酸性鹽和緩蝕劑等溶液中,以除去金屬表面的氧化膜、氧化皮和銹蝕產(chǎn)物的過程稱為浸蝕或酸洗。
鎂化學(xué)性質(zhì)活潑,鎂合金在各種環(huán)境介質(zhì)中的耐腐蝕性能都比較差 。為了提高鎂合金材料的耐腐蝕性能,通常要對(duì)鎂合金材料的表面進(jìn)行強(qiáng)化處理,在其表 形成具有一定防腐蝕能力的覆蓋層。鎂合金常用的表面強(qiáng)化處理方法有化學(xué)轉(zhuǎn)化處理、陽極氧化處理、電鍍、化學(xué)鍍 、有機(jī)涂層等。在進(jìn)行這些處理之前 ,必須對(duì)鎂合金材料進(jìn)行浸蝕 (酸洗)除銹 ,以除去其表面的氧化物、腐蝕產(chǎn)物以及其他污染物 ,同時(shí)浸蝕還可以為后續(xù)表面處理提供更多的結(jié)合位點(diǎn),增強(qiáng)鍍層的結(jié)合力,提高其表面質(zhì)量 。
表3 鎂合金浸蝕液組成及工藝
鎂合金自然氧化膜不致密,不能有效保護(hù)金屬基體。此外,金屬鎂電負(fù)性很強(qiáng),當(dāng)與其他金屬接觸時(shí),易發(fā)生電偶腐蝕,引起鎂的加速溶解。這些都限制了鎂合金的應(yīng)用。因此,鎂合金件出廠時(shí)都要經(jīng)過表面處理以提高其抗腐蝕性能。通常最常用、操作簡單的方法是化學(xué)處理(化學(xué)轉(zhuǎn)化處理)或電化學(xué)處理 (即陽極氧化)。
表4 鎂合金磷酸鹽化學(xué)轉(zhuǎn)化工藝
磷酸鹽化學(xué)轉(zhuǎn)化處理各成分的作用及影響
表5 鎂合金磷酸鹽一高錳酸鹽化學(xué)轉(zhuǎn)化工藝
磷酸鹽-高錳酸鹽化學(xué)轉(zhuǎn)化處理影響因素
溶液組成和工藝參數(shù)的影響
工藝流程
為了進(jìn)一步改善膜層質(zhì)量,促進(jìn)膜層生長,通常需要向微弧氧化電解液中加 入各種添加劑。目前研究的添加劑大多為可溶性鹽或有機(jī)物,按照作用主要分為以下幾類:
① 抑制試樣表面尖端放電,提高電解液穩(wěn)定性 。
主要有 KF、甘油、C3H8O3, Na2EDTA等。
② 有助于放電,提高溶液的電導(dǎo)率。
主要有 NaOH、KOH、NaF和 NaAl02 等 ;但添加劑的含量過高會(huì)抑制放電或引起嚴(yán)重的邊緣放電。
③ 減少膜層的孔洞和裂紋,相應(yīng)地提高陶瓷層的致密性 、耐蝕性能。
如 Na2W04、氫氧化鉀、EDTA、蒙脫石、稀土鹽、有機(jī)酸鹽、二氧化硅、硅酸鋁等。
④ 調(diào)整陶瓷層色彩的成分 ,如 Cu2+呈藍(lán)色,Ni2+呈紫綠色,Cr3+呈綠色 。
表 常見鎂合金的酸洗液及工藝 表 鎂合金活化液的組成及操作工藝 表 不同主鹽體系化學(xué)鍍鎳液配方及工藝條件 圖 不同主鹽體系的鍍層厚度隨時(shí)間變化的曲線 圖 不同主鹽鍍鎳體系所得的鍍層的微觀形貌 表 不同穩(wěn)定劑對(duì)化學(xué)鍍鎳液穩(wěn)定性和沉積速度的影響 圖 溫度對(duì)化學(xué)鍍鎳沉積速度和鍍層孔隙率的影響
免責(zé)聲明:本網(wǎng)站所轉(zhuǎn)載的文字、圖片與視頻資料版權(quán)歸原創(chuàng)作者所有,如果涉及侵權(quán),請(qǐng)第一時(shí)間聯(lián)系本網(wǎng)刪除。
-
標(biāo)簽: 鎂合金, 表面強(qiáng)化, 腐蝕
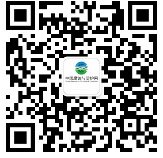
官方微信
《腐蝕與防護(hù)網(wǎng)電子期刊》征訂啟事
- 投稿聯(lián)系:編輯部
- 電話:010-62316606
- 郵箱:fsfhzy666@163.com
- 腐蝕與防護(hù)網(wǎng)官方QQ群:140808414