“十三五”期間,我國深水油氣裝備實現國產化,相關技術躍居世界先進水平。中心管匯是深水生產系統中最復雜、最典型的核心設備之一,用于分配、控制、管理石油和天然氣的流動。雙相不銹鋼材料具有出色的耐蝕性和力學性能,在中心管匯上有廣泛的應用。
良好的防腐蝕是確保該設備在壽命期內正常服役的關鍵,管道外涂層在這方面發揮著重要作用,但目前相關研究和關注較少。工程中也存在因雙相不銹鋼具有優異耐蝕性而忽視其防腐蝕涂裝的認識誤區。
為此,海洋石油工程股份有限公司的技術人員結合工程應用,通過介紹雙相不銹鋼表面涂層的重要性,從表面處理、涂裝系統、涂層修復等方面提供了實現良好防腐蝕涂裝的技術參考。
生產設施及材料介紹
01
水下中心管匯
深水生產系統已成為深水及邊際油氣田開發的重要模式。中心管匯(Central Manifold)被喻為水下“油氣樞紐站”,是設計和制造難度極高的設備,如圖1所示。
圖1 中心管匯
中心管匯主要分布在海底的井口群之間,承擔著將深海油氣匯集并輸送的重要作用,在南海500級流花、1500級陵水等深水及超深水油氣田的開發中,隨著關鍵技術自主創新和核心設備自主研制,中心管匯已實現國產化并成功應用,是目前國產化水平最高的水下關鍵設備。
02
雙相不銹鋼
雙相不銹鋼中鐵素體與奧氏體各約占50%,較少相含量最少達到30%。雙相不銹鋼兼具奧氏體不銹鋼和鐵素體不銹鋼的優點:與鐵素體不銹鋼相比,雙相不銹鋼塑性、韌性更高,室溫脆性、耐晶間腐蝕性能和焊接性能明顯提高;與奧氏體不銹鋼相比,雙相不銹鋼強度高且耐晶間腐蝕、耐氯化物應力腐蝕性能提高。
水下生產設施需具有較長的服役壽命和極高的可靠性,因為它一旦失效可能造成嚴重的后果且維護費用高昂。雙相不銹鋼在耐點蝕、耐縫隙腐蝕、耐應力腐蝕方面性能優異,廣泛應用于中心管匯主工藝管線、小口徑儀表管、閥門等。
流花某氣田中心管匯的主工藝管線、管件使用材料為S31803雙相不銹鋼,管線三維圖如圖2所示,該中心管匯經過了防腐蝕涂裝。
圖2 中心管匯的管線三維圖
雙相不銹鋼管線涂層的作用
處于深水的雙相不銹鋼管線,長期面臨海水浸泡、高壓、低溫、沖擊等,腐蝕環境復雜而嚴苛。雙相不銹鋼管線處于陰極保護之下,外防腐蝕涂層起到減小陽極消耗,降低氫致應力開裂風險,提高抗腐蝕性的重要作用。
減小陽極消耗
隨著水深的增加,海水溫度變低、壓力增大、pH降低,海水中的碳酸鈣低于飽和度,不易形成保護性石灰質沉積垢層。壓力增大會增加涂層的吸水率,加速涂層的失效,涂層電阻在較短時間內明顯降低。相比于常壓海水環境,涂層在深海高壓環境中更容易失效。研究表明,在高壓(6 MPa)海水中浸泡30天后,常規涂層的阻抗降低1000倍。因此,在深水環境中服役的水下設施需要更大的陰極保護電流,這導致陽極消耗量增加。我國南海某深水氣田在開發之初就遇到了管線陽極消耗過快的問題。由于空間和質量的限制,在水下設施中不可能無限增加陽極的數量和質量。
對于雙相不銹鋼管線來說,采用防腐蝕涂層和陰極保護相互補充方式是較為經濟、安全可靠的防腐蝕手段。涂層的致密性和低電導率將大大減小管線對于陰極保護電流的需求,水下設施可被快速極化到最佳保護電位從而得到有效保護,陽極的使用壽命也得到延長。同時涂層有助于實現陰極保護電流的均勻分布,這對于深水中心管匯實現設計壽命有著非常重要的意義。
降低氫致應力開裂風險
應力腐蝕開裂(SCC)是材料在應力和特定介質協同作用下產生的脆性斷裂現象。在拉應力作用下,原子氫滲入并擴散到合金晶體結構內部導致合金脆性斷裂的失效形式稱為氫致應力開裂(HISC)。HISC是一種非延性失效模式,由應力、氫含量和易受影響的鋼的微觀結構共同作用引起。雙相不銹鋼對HISC敏感,從環境中吸收一定量的氫和高應力部件微觀結構的共同作用可以誘導雙相不銹鋼發生氫致應力開裂。氫致應力開裂主要可從三個方面控制:材料微觀結構、介質中氫的來源、負載評估。
圖3為荔灣某深水氣田水下雙相不銹鋼管線服役后發生氫致應力開裂的情況。檢測結果表明,回收管道的母材含有較多的氫(質量分數約為0.0172%),焊縫含氫量相對較少(質量分數約0.0084%)。這是因為出現裂紋后氫迅速擴散出金屬。
圖3 氫致應力開裂
分析發現,雖然焊口組織中鐵素體的平均含量符合工程規范要求,但裂紋區域局部鐵素體含量非常高。由于氫原子的直徑比金屬原子小很多,在鐵素體中具有很好的滲透擴散性,大量氫原子擴散進入鐵素體后產生氫氣發生體積膨脹,導致該區域產生開裂。
在海洋環境中,陰極保護電位須嚴格控制在適當范圍。雙相不銹鋼在海水中暴露于高應力以及保護電位負于-800 mV(相對于Ag/AgCl參比電極)時,容易受到氫致應力開裂的影響。當管線材料中存在結構缺陷、兩相組織存在不均勻,服役環境中有豐富的氫源時,雙相不銹鋼有較高的開裂風險。表面的涂層可以顯著降低雙相不銹鋼對于保護電流的需求從而降低鋼材表面氫原子的富集,同時起到屏蔽氫的作用,達到抑制氫致應力開裂的目的。但涂層不是100%的屏障,細小的裂紋或缺陷都可能導致局部產生和吸收氫,因此涂層的質量至關重要。
提高耐腐蝕性能
自然條件下雙相不銹鋼優良的耐腐蝕性能主要依靠其表面的鈍化膜,在海水環境中,雙相不銹鋼的耐腐蝕性能會減弱。這主要是因為氯離子半徑比較小,易于擴散和穿透,吸附在金屬表面,與鈍化膜發生反應,使鈍化膜破壞直到出現微觀缺口;缺口處的雙相不銹鋼失去鈍化膜的保護變成陽極區,而鈍化膜未被破壞部分雙相不銹鋼則是陰極區,如此形成了大陰極小陽極模型,使陽極區快速腐蝕形成點蝕坑。水下設施接觸的海泥中往往含有細菌等微生物,微生物沉積在雙相不銹鋼表面形成膜,使不銹鋼點蝕敏感性增大。管線外部的保護涂層可以起到隔離氯離子、微生物、污染物等的作用,從而提高管線的耐腐蝕性能。
雙相不銹鋼管線的防腐蝕涂裝
由于材料和服役環境的特殊性與碳鋼管線相比,雙相不銹鋼管線的涂裝在涂層選用、檢驗儀器、施工設備、涂裝工藝等方面有更高要求。
01
表面處理
表面處理是涂層優良附著的基礎,表面一致有助于涂層的均勻分散。雙相不銹鋼管線宜采用噴砂處理(除銹等級為Sa2.5級),噴砂處理時必須采用不含氯化物的尖銳的石榴石、氧化鋁等非金屬磨料以形成鋸齒狀的輪廓。
經表面處理后,雙相不銹鋼表面粗糙度的推薦值為50~85 μm。表面粗糙度過大會使波峰處涂料不能完全覆蓋金屬基材,涂層厚度偏薄,防護性能下降。表面粗糙度過小會使涂層附著力下降,導致涂層提早損壞。
金屬基材上的可溶性鹽會增加水分子的滲透壓導致涂層起泡,表面可溶性鹽分控制在20 mg/m2以下(可溶性鹽電導率宜控制在170 μS/cm以下)。噴砂處理后雙相不銹鋼表面附著的灰塵雜質會產生涂層起泡問題,可接受最低除銹等級為Sa2級。
02
涂層系統
涂料性能是長效防腐蝕的關鍵,陰極保護對涂層有剝離作用,因此在選擇防腐蝕涂層時,應考慮涂層的電性能、力學性能、化學性能等。受制造、空間等限制,熱固性交聯融結環氧等屏蔽性能較佳的涂層在管線上不便實施,因此水下中心匯管常采用液態環氧涂料。
雙相不銹鋼是一種特殊的合金材料,液態涂料在其表面的浸潤性相對較差,必須選擇附著力優良的涂層體系。NORSOK M-501標準推薦的涂裝系統中,油漆類型為雙組分環氧/環氧酚醛,最小干膜厚度為350 μm,最小涂裝遍數為2遍,顏色為黃(RAL1004)。
深水防腐蝕涂層系統與深水陰極保護系統必須很好地兼容,這就要求涂層具有良好的耐陰極剝離及耐海水浸泡性能。通過最少4200小時的常溫海水浸泡和陰極剝離兩項測試,評估涂層的附著力、耐滲透性、致密性、腐蝕蔓延性以及耐電流的剝離性等。如果管線操作溫度超過50 ℃,還應在不低于最高服役溫度下對涂層再進行陰極剝離測試。
常溫管線涂層可采用雙組分厚漿型環氧,溫度較高時采用環氧酚醛。環氧酚醛有很高的交聯密度,自由體積小,溫度較高時其高交聯的網絡使水分子、離子等難以通過,因此耐溫性通常優于環氧。
為確保涂層的防腐蝕性能,推薦對深水涂層進行額外的高壓浸泡測試,利用電化學、光譜、表面分析等方法檢驗涂層在高壓、低溫下的性能及其變化。涂層厚度不應低于350 μm,適當增加厚度可增強涂層對腐蝕介質的屏蔽能力,阻止滲透。圖4為水下機器人(ROV)在水下對管線進行操作,深水能見度極低,為便于觀察,管線面漆顏色宜采用辨識度較高的黃色RAL1004。
圖4 ROV水下操作
03涂層厚度測量
雙相不銹鋼中的鐵素體會產生不均勻的鐵磁性,其電磁特性對膜厚測量儀傳感器的磁場分布產生影響,從而影響常用磁性或者電渦流探頭的靈敏度。在工程中用鐵基、非鐵基或自動識別底材類型的探頭測量膜厚均可能產生偏離。厚度是涂層質量控制的重點,涂層過厚會導致應力集中,涂層過薄會使其屏蔽性能不足。雙相不銹鋼涂層厚度宜采用超聲波厚測量儀器進行檢測。超聲波脈沖可以準確測量各涂層的厚度,使用前應按涂層厚度范圍設置量程以獲得準確值。
04游離鐵污染控制
陰極保護電流對不銹鋼鈍化膜的影響較為復雜,極化電位不同可能會導致表面鈍化膜變化。鈍化膜在雙相不銹鋼管線整體防腐蝕體系中仍然發揮著重要的防護作用,特別是對于欠保護或電流屏蔽處管線。游離鐵會導致雙相不銹鋼表面污染從而影響鈍化膜的形成,如圖5所示。雙相不銹鋼管線的表面處理和噴涂應在獨立的車間或專用場地進行,噴砂和作業環境均需與碳鋼作隔離處理。
圖5 雙相不銹鋼表面的鐵污染
藍點檢測法可用于檢驗鐵污染。檢測溶液為1 g K3[Fe(CN)6]加3 mL質量分數為65%~85%的硝酸和100 mL去離子水。濾紙浸漬溶液后貼附于待測雙相不銹鋼表面或直接將溶液滴涂于雙相不銹鋼表面,15秒內出現藍點表明存在游離鐵。
05焊縫節點涂層的修復
水下中心管匯雙相不銹鋼管線常規建造工藝是預涂管線、管件,焊接后再對焊縫進行修補涂裝,受空間限制此時往往不再具備噴砂作業條件。用常規鋼絲刷或針槍等工具對修復位置打磨只能產生光滑表面,不能形成明顯波峰、波谷的鋸齒狀外形。低表面粗糙度和波浪外形會造成涂層附著力差,影響其抗陰極剝離性能,形成薄弱點。在2012版NORSOK M-501標準中,對于浸沒區不銹鋼表面粗糙度的要求為50~85 μm,而對于非海洋大氣區和2004版浸沒區表面粗糙度的要求為25~45 μm。
管線的焊縫是氫致應力開裂最為敏感的部位,焊縫處涂層質量較為重要,提高涂層的附著力可以提高其抗陰極剝離性能。推薦使用立式鋼絲刷等工具持續沖刷打磨該區域鋼材表面,使該區域鋼材表面產生與噴砂類似的清潔度和表面粗糙度,以提高涂層的附著力從而提高其防腐蝕性能和屏蔽作用。在打磨處理前,焊縫表面應處理平整,控制余高3 mm以下,防止應力集中。涂層完全固化后,用濕海綿漏涂點檢測儀進行100%針孔檢測。
水下油氣生產系統是深水油氣田開發的重要模式,我國相關裝備的研制起步較晚,目前仍存在技術不足等問題,因此向海洋工程制造業深水高端裝備進軍,開展相關探索和實踐具有重要意義。水下中心管匯是深海油氣田開發的核心裝備之一,管線是該設備正常運行的關鍵。陰極保護下雙相不銹鋼管線涂層能起到減小陽極消耗,降低氫致應力開裂風險,提高耐腐蝕性的重要作用。工程設計和制造中應結合雙相不銹鋼管線的服役特點制定針對性的防腐蝕涂裝方案,采用專業儀器設備檢測,確保防腐蝕涂層的質量和可靠性。
免責聲明:本網站所轉載的文字、圖片與視頻資料版權歸原創作者所有,如果涉及侵權,請第一時間聯系本網刪除。
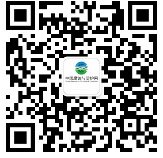
官方微信
《腐蝕與防護網電子期刊》征訂啟事
- 投稿聯系:編輯部
- 電話:010-62316606
- 郵箱:fsfhzy666@163.com
- 腐蝕與防護網官方QQ群:140808414