自20世紀末中國石化開始加工進口高硫原油以來,催化裂化裝置原料所含硫、環烷酸等腐蝕性雜質的含量不斷增加,腐蝕已成為影響裝置安全穩定運行的重要因素。通過對裝置的腐蝕狀況進行分析,對腐蝕部位、腐蝕形態、腐蝕影響因素進行研究,提出相應的應對措施,對于保障裝置的安全穩定運行非常必要。
催化裂化裝置是我國煉油工業最重要的二次加工裝置,生產了我國80%的汽油和35%的柴油。催化裂化裝置原料適應性強,產品價值高,同時也是重油加工的重要手段,大比例摻煉渣油進一步提高了裝置的經濟效益。中國石化系統催化裂化裝置實際加工量占原油一次加工量的37.4%,居煉油二次加工裝置首位。
裝置基本情況
某石化公司重油催化裂化裝置于1995年建成投產,加工能力為100×104t/a,加工原料有減壓蠟油、減壓渣油和溶劑脫瀝青油,裝置減壓渣油加工量超過40%。裝置再生部分采用兩級再生,第二再生器布置在第一再生器上部,第一再生器采用貧氧再生,控制再生溫度在700℃以下,燒去所有氫和80%碳,第二再生器采用富氧再生,燒去所有碳,使再生催化劑碳含量小于0.1%。反應油氣經分餾得到汽油、柴油、液化氣、干氣等產品。
裝置設計原料硫含量為0.5%(質量分數),從表1可以看出,裝置生產中原料硫含量已超過設計值,最高達到1.1%。原料硫含量增加,引起裝置低溫部位和高溫部位物料腐蝕性雜質含量增加,使腐蝕加重。
反應再生部分的腐蝕和損傷
反應再生部分的腐蝕和損傷類型主要有催化劑的沖刷磨蝕、金屬超溫變形和損傷開裂、高溫煙氣腐蝕等。
1、反應再生部分的沖蝕和磨蝕
催化劑的沖刷磨蝕在再生器主風分布管、翼閥閥板、滑閥、三級旋風分離器單管、原料油噴頭等部位較為嚴重。圖1為第二再生器主風分布管出風口磨蝕形貌,可以看到主風分布短管基本沖蝕沒有了;圖2為再生滑閥導軌的磨損,導軌的一部分已沖蝕掉了;圖3 是三級旋風分離器的單管的磨蝕,已經穿孔。
催化劑的沖刷磨蝕主要通過在構件表面設置耐磨襯里,控制襯里材料、襯里的施工質量來防止過快沖蝕,對于無法進行耐磨襯里的構件(如滑閥導軌等),需要通過耐蝕合金堆焊、表面滲硼等表面處理方法,提高抗沖蝕能力;還可考慮優化局部結構,減緩流速和局部渦流以便減緩沖蝕。
2、金屬的超溫變形和損傷
金屬的超溫變形損傷包括反應器和再生器器壁和內構件的損傷。反應器和再生器采用碳鋼制造,設計溫度300℃,內壁采用隔熱耐磨襯里來保證壁溫低于設計溫度,但在反應器和再生器結構不連續部位(如大開孔部位、變徑部位),由于襯里質量難以保證,催化劑在局部的高流速和渦紊流造成局部襯里損壞,使器壁金屬超溫,造成器壁金屬的超溫鼓包,內部金相組織裂化損傷,裝置第一再生器外取熱催化劑返回口部位、第二再生器外旋風分離器催化劑返回口部位都發生過超溫損傷;內構件損傷主要是由于結構設計時對結構變形協調考慮不夠周到,升降溫速度過快形成較大的熱應力,造成較大變形甚至焊縫開裂。
為了防止局部器壁超溫變形鼓包,在局部結構不連續部位襯里施工和維修時,應適當多布置保溫釘,嚴格控制保溫釘焊接質量,使焊縫焊角尺寸達到設計要求,并做好襯里施工質量控制,運行中定期使用紅外熱像儀或測溫筆檢測壁溫,發現異常時及時分析并采取措施。
通過合理選擇反應器和再生器內構件材質,保證材料的耐溫性能滿足使用要求,優化結構改善升溫后的變形協調性,減緩局部應力集中,防止內件的異常變形和焊縫開裂,保證結構的運行安全性。
3、高溫煙氣的腐蝕
高溫煙氣的腐蝕發生在再生器和三旋煙道等再生煙氣經過的部位,再生溫度高達700℃以上,煙氣中二氧化碳、水蒸氣、二氧化硫、氮氧化物等對金屬有腐蝕作用,再生器和煙道采用非金屬襯里防止腐蝕的發生,無法采用非金屬襯里的部分采用奧氏體不銹鋼腐蝕防腐。主要問題是非金屬襯里在運行中會產生裂紋,煙氣滲透到金屬器壁和襯里之間,當器壁溫度低于煙氣露點時,形成高濃度酸性溶液,為NOx-SOx-H2O腐蝕環境,對碳鋼造成硝酸鹽應力腐蝕開裂,對煙氣膨脹節造成點蝕穿孔和應力腐蝕開裂。
催化裂化裝置運行經驗表明,再生器硝酸鹽應力腐蝕開裂與再生工藝、壁溫、材料的敏感性、結構應力水平等有關,煙氣中SOx主要是SO2,隨著再生過剩氧含量提高,SO3含量增加,導致露點提高,而且采用一氧化碳助燃劑增大強化燒焦能使煙氣中NO2增加,增加開裂敏感性。16MnR材料在焊接時Mn容易發生偏析,形成富Mn帶造成局部淬硬組織出現,敏感性較高,20R敏感性較低,焊后消除應力熱處理有助于防止開裂的發生。本裝置第一再生器和第二再生器器壁材質均為16MnR,具有一定的開裂敏感性。第一再生器采用貧氧再生,過剩氧含量低,實測煙氣露點51℃,壁溫在100~120℃,因此硝酸鹽應力腐蝕開裂敏感性較低。第二再生器為完全再生,過剩氧含量6%,實測煙氣露點141℃,未保溫時壁溫在100~120℃,硝酸鹽應力腐蝕開裂較高,為了防止應力腐蝕開裂的發生,裝置對再生器器壁采用了外保溫措施提高壁溫,從運行經驗來看,有明顯效果,但應注意在實際生產中由于開車、停車和生產、操作的正常波動,有時仍會造成設備壁溫低于煙氣露點,不能完全防止應力腐蝕開裂的發生,需要在工藝操作中采取相應措施。
對于再生系統煙氣膨脹節,材料有0Cr18Ni9、0Cr17Ni12Mo2、B315、FN2等幾種選擇,在煙氣冷凝時處在SOx-Cl--H2O腐蝕環境中,發生點蝕穿孔和應力腐蝕開裂,可采取措施進行保溫或伴熱提高壁溫,防止煙氣冷凝而發生腐蝕。FN2、B315是我國開發的兩種用于膨脹節的材料,具有優良的抗晶間腐蝕、點蝕、氯離子腐蝕和硫腐蝕能力,力學性能優良,在煉油行業得到了成功應用。膨脹節更換應優先考慮這兩種材料,在特別苛刻環境下,應考慮采用625制造膨脹節。
分餾部分的腐蝕
1、分餾部分高溫部位的腐蝕
分餾部分高溫部位主要是分餾塔下部柴油段以下的換熱設備和管線,腐蝕類型為S-H2S-RSH高溫腐蝕,分餾塔下部塔盤、人字擋板已經采用不銹鋼,未發現明顯的腐蝕,分餾塔塔體腐蝕較輕。原料油換熱溫度到200℃進入反應器,高溫部位換熱器未發現嚴重的腐蝕狀況,油漿管道已采用1Cr5Mo鋼,其他管道為碳鋼,油漿管道和其他高溫管道腐蝕較輕。考慮到以后裝置加工原料硫等腐蝕性雜質含量的提高帶來的腐蝕可能加重的趨勢,在裝置運行中應加強對回煉油管線等高溫管線的測厚檢查,根據實際腐蝕狀況進行局部材質升級。
2、分餾部分低溫部位的腐蝕
分餾部分低溫部位主要是分餾塔(T201)頂部和塔頂冷凝冷卻系統的設備和管線,腐蝕為H2S-Cl--NH3-H2O型。油氣出分餾塔的初次換熱器與除鹽水換熱,6臺并聯,油氣走殼程,結垢嚴重,六臺換熱器管束分別采用了碳鋼、Ni-P鍍和不銹鋼。從實際腐蝕情況看,碳鋼管束表面有密集的蝕坑;Ni-P鍍管束蝕坑較少,但蝕坑比碳鋼管束深,有的接近穿孔;不銹鋼管束外壁光滑,腐蝕較輕。
油氣的初凝部位可能在分餾塔頂初次換熱器(E201A~F)內部,形成高濃度的酸性溶液,對管束造成嚴重腐蝕。根據中國石化《煉油生產裝置工藝防腐蝕管理規定》,此部位應根據塔頂冷凝水pH值情況,在塔頂注氨水,并可考慮注緩蝕劑,在工藝防腐措施達到要求的工藝指標的情況下可采用碳鋼管束,換熱器結構上可以加大入口管直徑,采用外導流結構,以降低流速,減緩沖蝕。Ni-P鍍能夠提高抗蝕能力,但Ni-P鍍為陰極性涂層,一旦存在局部缺陷,將會加速局部腐蝕,Ni-P鍍管束必須在質量得到嚴格控制的情況下才適合選用。相關文獻指出,18-8不銹鋼在pH>6及氯離子小于200pom的環境可以使用,在催化分餾塔頂部位,氯含量較少,可以采用奧氏體不銹鋼管束,但成本較高。
3、吸收穩定部分的腐蝕
吸收穩定部分的腐蝕主要表現在貧富吸收油換熱器(E315AB)、解吸塔底重沸器(E304)和穩定塔底重沸器(E306),其中解吸塔底重沸器(E304)和穩定塔底重沸器(E306)的腐蝕尤為嚴重。貧富吸收油換熱器(E315AB)殼程介質為吸收后的重石腦油,管程介質為吸收前的重石腦油,管束腐蝕主要是濕硫化氫引起的腐蝕,可以考慮把管束升級為08Cr2AlMo,這種鋼是我國開發的抗濕硫化氫腐蝕的鋼種,抗濕硫化氫腐蝕能力是碳鋼的4 倍以上。解吸塔底重沸器(E304)和穩定塔底重沸器(E306)管束的腐蝕不僅有硫化氫等腐蝕介質的腐蝕,還有介質在管束表面汽化引起的沖蝕,需要把管束材質由碳鋼升級為00Gr19Ni10,其中解吸塔底重沸器(E304)的殼體應由一般結構換熱器殼體更新為帶蒸發空間的殼體,兩臺設備在運行中殼體內應保持一定的液位高度,使管束完全浸沒在液體中,防止管束頂部換熱管處于干濕交替狀態,造成局部液滴的突沸產生較大的沖擊力,加快管束的腐蝕。
循環冷卻水的腐蝕
循環冷卻水的腐蝕屬于電化學腐蝕,與水質的控制和管理、水冷器的材質和結構形式、工藝運行參數有關。裝置水冷器噴涂了防腐涂料,對管板的腐蝕起到了防護作用,多數水冷器管箱安裝了吸收陽極塊,有效減緩了管箱殼體和管板的腐蝕。有部分管板上的涂料已經破損,在破損部位有明顯的腐蝕。涂料耐溫有一定限制,在裝置開停工蒸汽吹掃時,需要采取相應的保護措施保護涂層防止超溫破壞。
裝置中的產品油漿水冷器 E209A~D,循環水走殼程,換熱管表面結垢,引起較為嚴重的垢下腐蝕。原因是油漿入口溫度較高(達160℃),使管壁溫度偏高,易于結垢,同時循環水走殼程也易使循環水流速偏低,提高了結垢傾向,需要適當降低油漿入口溫度,適當提高殼程循環水流速,并定期排污,以減緩油漿水冷器的腐蝕。
總結
本套催化裂化裝置設備腐蝕較為嚴重的主要是反應器、再生器襯里破損部位和內件、再生煙氣膨脹節,分餾塔頂冷卻部分的第一組換熱器,以及吸收穩定部分解吸氣重沸器和穩定塔底重沸器。
(1)為了防止反應器和再生器襯里在裝置運行中發生損壞引起器壁材料的磨蝕和超溫損傷,需要嚴格控制襯里材料的質量,嚴格控制襯里施工質量。在開停工和操作運行中,要防止溫度的過快升降,并加強重點部位壁溫的檢查。
(2)在膨脹節導流筒和波紋管間不填充保溫材料,對膨脹節進行外保溫,以提高煙氣膨脹節的壁溫,防止煙氣冷凝造成腐蝕破壞。在故障停工時,要采取伴熱措施,以防止煙氣冷凝。
(3)對分餾塔頂換熱器的腐蝕,需要重點做好"三注"工藝防腐措施,換熱器結構上可加大接管直徑、采用外導流措施降低流速來減緩腐蝕。需保證并聯的各換熱器流量基本一致,防止出現偏流。
(4)解吸塔底重沸器殼體建議更換為帶蒸發空間的殼體,以減緩液體在管束表面沸騰引起的沖蝕。解吸塔底重沸器和穩定塔底重沸器管束建議升級為00Cr19Ni10,運行中殼程應保持一定液位高度,使管束完全浸沒在液體中,以防止液體快速蒸發對管束造成巨大的沖擊力,加快腐蝕。
(5)對塔頂低溫系統管道及分餾部分的高溫系統管線,要進行定期測厚檢查,測厚頻率結合使用時間、實際壁厚、操作條件等確定,運行中加強對重點部位的檢查,以保證裝置的安全穩定運行。
免責聲明:本網站所轉載的文字、圖片與視頻資料版權歸原創作者所有,如果涉及侵權,請第一時間聯系本網刪除。
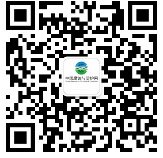
官方微信
《腐蝕與防護網電子期刊》征訂啟事
- 投稿聯系:編輯部
- 電話:010-62316606
- 郵箱:fsfhzy666@163.com
- 腐蝕與防護網官方QQ群:140808414