摘要
采用電化學方法(電化學阻抗和動電位極化)并配合浸泡失重法以及一系列表征,研究了常溫下碳鋼基體與CO2-Cl-的界面反應,以及加入HCO3-介質后CO2-Cl--HCO3-體系中HCO3-介質對碳鋼表面的成膜。結果表明,CO2介質的加入使碳鋼基體的溶解速率顯著提高但是對Cl-濃度的影響較小;添加高濃度的Cl-反而抑制CO2的溶解而使基體的腐蝕速率略微降低;在CO2+Cl-+HCO3-體系中加入微量的HCO3-后碳鋼表面成膜不明顯,疏松的腐蝕產物不能抑制碳鋼基體的進一步溶解;濃度過高的HCO3-使FeCO3的過飽和度提高從而加速細小晶體的析出,抑制腐蝕的進行。
關鍵詞: 金屬材料 ; 多介質協同作用 ; 電化學技術 ; 腐蝕機理
本文引用格式
張少華, 李彥睿, 衛英慧, 劉寶勝, 侯利鋒, 杜華云, 劉笑達. 多介質在碳鋼腐蝕過程中的協同作用. 材料研究學報[J], 2021, 35(10): 721-731 DOI:10.11901/1005.3093.2021.004
ZHANG Shaohua, LI Yanrui, WEI Yinghui, LIU Baosheng, HOU Lifeng, DU Huayun, LIU Xiaoda. Synergistic Effect of Multi-media on Carbon Steel Corrosion. Earth Science[J], 2021, 35(10): 721-731 DOI:10.11901/1005.3093.2021.004
輸送石油和天然氣的管線,是石油工業的“命脈”[1, 2]。集輸管線的腐蝕使其發生泄露式開裂而引起爆炸,可能造成重大安全事故和環境污染[3]。在油氣生產和運輸的管線中,存在著油氣田中的CO2氣體和地層水[4, 5]。CO2溶解在地層水中生成的H2CO3,對碳鋼管線的腐蝕性極強 [6, 7]。在管線流的不同區域,地層水中分布著不同濃度的Cl-離子[8]。文獻[9]研究了CO2與Cl-對油氣管線腐蝕的交互作用并解釋其機理,但是在工程條件下管線的腐蝕體系更為復雜。例如,NaHCO3作為一種pH值穩定劑常注入管線流中以限制其均勻腐蝕速率。HCO3-即能促進氧化膜的形成以增強碳鋼表面的鈍化[10, 11],還能發生兩步氧化反應加速管線內部減薄。因此,HCO3-的臨界濃度是控制腐蝕的關鍵[12]。
對于單一CO2、Cl-以及HCO3-介質的腐蝕機理,已進行了較多的研究。Linter、Burstein和Remita等[13, 14]研究了H2CO3的電化學活性、構建數學模型預測CO2環境中的陰極反應,但是并未發現H2CO3在鋼表面的直接還原;關于CO2相關物質能否直接作用于碳鋼陽極的溶解,學術界有不同的看法。Almedia等[15]認為,CO2沒有直接作用在碳鋼的自由表面,感抗弧的出現源于Fe-H2O相關物質的釋放;而Kahyarian等[16]根據陽極極化曲線的Tafel斜率從28 mV/dec降至22 mV/dec認為,CO2相關物質能直接作用于碳鋼陽極影響其溶解,關鍵是實驗采用暫態技術還是穩態Tafel技術。關于Cl-是否催化陽極溶解,前者提出Cl-能形成中間配合物使鐵基體溶解加速[17, 18];但是Barcia認為,在Fe*(Ⅰ)ads和Fe(Ⅱ)ads結構中Cl-與OH-相互競爭,當體系的pH值不小于3時Cl-對鐵基體陽極溶解的影響較小[19]。關于HCO3-的研究,主要集中在陰極析氫反應和陽極鈍化成膜反應:Mao等[20]發現,在HCO3-的濃度為0.5 mol/L和1.0 mol/L極化曲線出現典型的陽極電流峰時,碳鋼表面發生鈍化;而Zhang和Wright等[21, 22]則認為,過高濃度的HCO3-將使陰極反應加速。這些研究,加深了對碳鋼在單一CO2、Cl-及HCO3-介質體系中腐蝕機理的解釋。本文采用電化學技術(電化學阻抗與動電位極化)并配合浸泡失重法和一系列表征,研究油氣管線內多介質(CO2、Cl-、HCO3-)之間的協同作用對管線腐蝕的影響。
1 實驗方法
1.1 樣品制備
實驗用優質20碳素結構鋼管線的化學成分,如表1所示。用于浸泡實驗的試樣其尺寸為50 mm×10 mm×4 mm,用于電化學實驗的試樣其尺寸為15 mm×15 mm×4 mm。實驗前用丙酮將試樣除油,然后用SiC砂紙將其逐級打磨至2000#,用去離子水、無水乙醇依次清洗后用冷風吹干,放在干燥皿中備用。將部分試樣拋光后用脫脂棉蘸取5%的硝酸酒精擦拭試樣表面1 min,用于觀察顯微組織(圖1所示),可見主要由鐵素體(區域A)和珠光體(區域B)組成。實驗用腐蝕介質可分為三個體系:(1)在N2脫氧條件下,只包含0.2/1.0 mol/L Cl-介質的溶液體系;(2) 0.2/1.0 mol/L Cl-+飽和CO2溶液體系;(3) 0.1 mol/L Cl-+0/0.05/0.1/0.5 mol/L HCO3-+飽和CO2溶液體系。
表1 實驗用20碳鋼的化學成分
圖1 20碳鋼的顯微組織和區域A/B的EDS結果
1.2 浸泡測試
在容積為1 L的高溫高壓反應釜中進行浸泡實驗,其裝置如圖2所示。實驗前,有精度為0.0001 g的分析天平將實驗用試樣稱重,然后用游標卡尺測定尺寸以計算其表面積。每次實驗使用6個試樣,將其掛在反應釜的特定位置后向反應釜內加入相應體系的腐蝕介質(0.6 L),使試樣在溶液中的高度相同。溶液相對試樣的流速為60轉/min。將反應釜密封,對應不同腐蝕體系通入相應的氣體介質。腐蝕浸泡實驗達到預設的周期后迅速取出試樣,依次用去離子水和無水乙醇充分清洗后用冷風烘干,放入干燥皿中待測。其中的3個試樣用于計算腐蝕速率,將其放入酸洗液(酸洗液的配制:500 mL ρ=1.19 g/mL鹽酸+3.5 g六次甲基四胺,加蒸餾水配制成1000 mL溶液,GB/T 16545-1996,China,idt ISO 8407,1991)中用超聲振動3 min以去除其表面腐蝕產物[19],然后用去離子水和無水乙醇依次清洗后用冷風吹干,用天平稱量并記錄數據。腐蝕速率為
圖2 浸泡實驗系統
其中Δm為樣品腐蝕后的質量損失(g);ρ為材料的密度(g/cm3);S為試樣暴露在溶液中的面積(cm2);t為浸泡腐蝕時間(h)。其余的試樣用于表面形貌分析和成分檢測。
1.3 電化學阻抗測試和動電位極化測試
電化學阻抗測試系統由Bio-logic SP-150電化學工作站、電化學反應釜、標準的三電極體系以及配套設備組成。工作電極為20碳鋼試樣,參比電極為飽和甘汞電極,輔助電極為鉑電極。
試樣暴露在腐蝕介質中的面積為1.0 cm2。在工作電極背面焊接導線,將工作面積外的部分用環氧樹脂封裝。實驗前用SiC砂紙將試樣表面打磨,用無水乙醇將電極表面清洗后干燥。為了減小溶液的電阻,將工作電極與參比電極之間用魯金毛細管連接。每次開始測試電化學阻抗前,都需經過大約2 h的開路電位測試以使體系達到相對穩定狀態。測試頻率范圍為100 kHz~10 mHz,線性正弦擾動為10 mV。測試結束后用ZSimDemo軟件擬合阻抗曲線的數據以得到所需參數。每組電化學實驗都至少進行5次,以確保實驗的重復性。
動電位極化測試使用與電化學阻抗測試相同的裝置。開路電位穩定后進行動電位極化測試,掃描速率為0.5 mV/s。測試結束后將數據擬合以得到腐蝕電位Ecorr和電流密度Icorr等參數。
1.4 表面形貌的表征
用掃描電子顯微鏡(SEM)觀察腐蝕產物的表面和截面形貌,結合X射線衍射儀(XRD)和能譜分析儀(EDS)分析腐蝕產物的化學成分以確定腐蝕產物的組成。
2 結果和討論
2.1 動電位極化曲線和電化學阻抗(CO2+Cl-體系)
圖3給出了25℃下碳鋼在0.2/1.0 mol/L Cl-和0.2/1.0 mol/L Cl-+CO2(1 bar)溶液體系中的動電位極化曲線和電化學阻抗譜。擬合具有代表性的動電位極化曲線,如圖4a、b所示。結合電流密度值(圖4c)可以發現,在只有Cl-介質的溶液體系中,Cl-濃度的提高使陽極極化曲線的腐蝕電流輕微減小,而陰極極化曲線保持不變。其原因是,氯離子濃度過高使溶液的粘度提高,進而使溶液內的傳質環節受到限制;加入CO2介質,使極化曲線整體向高電流密度方向顯著遷移。對于陰極部分,生成的H2CO3通過“buffering”效應在金屬-電解質界面逐步解離產生H+,使陰極析氫反應顯著增強;而陽極部分,CO2介質的加入促進Fe-H2O相關物質的釋放,進而使碳鋼基體的溶解加速[15]。
圖3 碳鋼在25℃的0.2/1.0 mol/L Cl-和0.2/1.0 mol/L Cl-+CO2(1 bar)溶液體系中的動電位極化曲線、Nyquist圖和相應的等效電路
圖4 碳鋼在Cl-和Cl-+CO2 (1 bar) 溶液體系中的動電位極化曲線擬合結果以及相應的腐蝕電流密度和腐蝕速率
如圖3b所示,電化學阻抗譜圖具有與極化曲線相似的特征。分別用等效電路R(QR)和R(Q(R(RL)))擬合碳鋼在0.2/1.0 mol/L Cl-和0.2/1.0 mol/L Cl-+CO2(1 bar)溶液體系中的阻抗數據,如圖3c、d所示。等效電路中的元件由溶液電阻Rs、金屬基體/電解質之間的雙層容抗CPEdl、相位角常數ndl、電荷轉移電阻Rct以及感應電阻RL和感抗L。所得的參數值列于表2。結合擬合結果發現,在有不同濃度Cl-的飽和CO2溶液體系中,碳鋼的阻抗譜圖有兩個半圓,一個是與雙電容相關的高頻容抗弧,另一個是與Fe-H2O物質釋放相關的低頻感抗弧。這表明,在飽和CO2溶液體系中,Cl-濃度的提高并沒有使碳鋼的界面反應產生機理性轉變。Cl-濃度的提高使阻抗弧半徑稍有增大,因為過量的Cl-使溶解的CO2減少。但是,在只有Cl-介質的溶液體系中,碳鋼的阻抗譜圖只有容抗弧。同時,與有CO2-Cl-介質的溶液體系比較,碳鋼在只有Cl-介質的溶液體系中的阻抗半徑顯著增加。這表明,CO2介質的加入使碳鋼的腐蝕機制發生了變化。
表2 碳鋼在0.2/1.0 mol/L Cl-和0.2/1.0 mol/L Cl-+CO2(1 bar)溶液體系中電化學阻抗譜的擬合參數
2.2 浸泡后的表面形貌(CO2+Cl-體系)
圖5給出了在25℃下碳鋼在0.2/1.0 mol/L Cl-和0.2/1.0 mol/L Cl-+CO2(1 bar)溶液體系中浸泡24 h后的表面形貌。腐蝕速率與腐蝕電流密度的變化趨勢一致,如圖4c所示。在只有Cl-介質的溶液體系中碳鋼表面保持平整,只觀察到樣品制備過程中的劃痕;CO2介質加入溶液體系后,碳鋼表面出現均勻腐蝕的形貌,生成了較薄的腐蝕層(EDS與XRD結果指出其主要成分為Fe3C,如圖5(e)/5(f)/5(g)所示)。考慮到碳鋼的微觀組織由鐵素體-珠光體組成,Fe3C比鐵素體的腐蝕電位更正。因此,在鐵素體與Fe3C之間會形成一個電偶效應,鐵基體的選擇性溶解導致大量的Fe3C殘余[23, 24]。較高的陰極位點進一步加速了碳鋼的腐蝕,使其腐蝕速率較高。
圖5 碳鋼在25℃的0.2/1.0 mol/L Cl-和0.2/1.0 mol/L Cl-+CO2(1 bar)溶液體系中浸泡24 h后的表面形貌以及EDS/XRD結果
2.3 動電位極化曲線和電化學阻抗(CO2+Cl-+HCO3-體系)
針對HCO3-介質的加入,探討CO2-Cl--HCO3-體系中三種介質的協同作用。于HCO3-介質的加入使碳鋼表面膜化效應比較明顯,且溫度的提高有利于腐蝕產物的析出。因此,在60℃進行實驗以突出HCO3-介質對碳鋼表面腐蝕產物膜層的作用。
圖6a給出了在60℃碳鋼在CO2(1 bar)+0.1 mol/L Cl-+0/0.05/0.1/0.5 mol/L HCO3-溶液體系中的動電位極化曲線。首先,碳鋼在CO2(1 bar)+0.1 mol/L Cl-溶液體系中表現出活性溶解行為。添加0.05 mol/L HCO3-介質后碳鋼的陽極極化曲線基本與前者重合,表明添加此濃度的HCO3-介質并不能使碳鋼的腐蝕過程發生明顯的轉變。而HCO3-濃度達到0.1/0.5 mol/L時,極化曲線發生顯著的變化。即隨著腐蝕電位的提高碳鋼在初始階段表現為活性溶解行為,然后發生“偽鈍化”。其原因是,鈍化電流密度還處于較高的電流密度區間,表明致密氧化膜層的形成,對碳鋼基體有較強的保護。其間,可觀察到一個明顯的活化-偽鈍化轉變區間(電流密度隨著電位的增加而急劇減小)。HCO3-的濃度達到0.5 mol/L時在-0.2 V vs. SCE以上的動電位區間幾乎完全呈現出“偽鈍化”現象。擬合極化曲線得到相應的參數值,如表3所示,即腐蝕電位(Ecorr)、“偽鈍化”電位(Epass)、腐蝕電流密度(Icorr)和陰/陽極極化曲線斜率(βa/βc)。可以看出,隨著HCO3-濃度的提高Ecorr值增加且Icorr值減小,腐蝕程度減弱。同時,Epass值的降低(0.1~0.5 mol/L)表明其鈍化趨勢顯著增強。
圖6 碳鋼在60℃的CO2 (1 bar)+0.1 mol/L Cl-+0/0.05/0.1/0.5 mol/L HCO3-溶液體系中的動電位極化曲線和阻抗圖
表3 碳鋼在CO2 (1 bar)+0.1 mol/L Cl-+0/0.05/0.1/0.5 mol/L HCO3-溶液體系中所得動電位極化曲線的擬合參數值
為了闡明碳鋼與CO2/HCO3-/Cl-介質之間的界面反應,測試了電化學阻抗,如圖6b和6c所示。可以看出,Nyquist曲線由一個容抗組成,主要與碳鋼表面的電荷轉移電阻相關[25, 26]。用等效電路(R(QR))對EIS結果進行了擬合,結果如表4所示。對應0、0.05、0.1和0.5 mol/L HCO3-濃度下的chi-squared值分別為4.717×10-4、3.011×10-4、1.048×10-4和4.103×10-4,等效電路與實驗數據的吻合程度較高。隨著HCO3-濃度的提高容抗弧的半徑略有增加,對應的電荷轉移電阻Rct逐漸增大,可歸因于CO2(1 bar)+0.1 mol/L Cl-溶液體系中碳鋼表面的快速腐蝕;HCO3-釋放到溶液中,碳鋼表面吸附大量的HCO3-相關物質使界面反應受到抑制。同時,相位角和低頻阻抗幅值|Z|(圖6c)的逐漸增大也證明,在CO2(1 bar)+0.1 mol/L Cl-+HCO3-溶液體系中碳鋼表面的耐蝕性提高。
表4 碳鋼在CO2(1 bar)+0.1 mol/L Cl-+0/0.05/0.1/0.5 mol/L HCO3-溶液體系中的電化學阻抗譜擬合參數
為了進一步驗證HCO3-介質釋放到溶液體系中碳鋼表面的成膜效應,對CO2(1 bar)+0.1 mol/L Cl-+0/0.05/0.1/0.5 mol/L HCO3-溶液體系中的碳鋼進行循環伏安測試,如圖7所示。在CO2(1 bar)+0.1 mol/L Cl-溶液中碳鋼的正向與反向極化曲線完全重合,表明碳鋼表面基體維持裸露狀態;0.05 mol/L HCO3-的加入使極化曲線的陽極部分出現較大的暫態電流,反映了碳鋼的表面狀態發生了不均勻的變化; 0.1/0.5 mol/L HCO3-介質的加入,使其反向極化曲線向電流密度減小的方向移動且腐蝕電位提高(尤其加入0.5 mol/L HCO3-介質),表明在碳鋼表面形成了均勻致密的膜層。同時,分析碳鋼在CO2 (1 bar)+0.1 mol/L Cl-+0/0.05/0.1/0.5 mol/L HCO3-溶液體系中一次極化后的表面SEM形貌,如圖8所示。對于CO2(1 bar)+0.1 mol/LCl-溶液,碳鋼電極呈現Fe+Fe3C的腐蝕形貌,其原因是鐵素體的選擇性溶解。HCO3-介質的濃度為0.05 mol/L時在碳鋼表面出現少量的腐蝕產物,隨HCO3-濃度提高到0.1/0.5 mol/L腐蝕產物均勻致密,覆蓋了整個碳鋼表面。這個結果,與圖7中的循環伏安曲線相符。結合圖8b中的面掃描圖和文獻[12, 27, 28],腐蝕產物的成分為γ-Fe2O3。其原因是,在電極極化條件下FeCO3的穩定性較差,隨著電位的提高腐蝕產物以γ-Fe2O3的形式存在。
圖7 碳鋼在60℃的CO2(1 bar)+0.1 mol/L Cl-+0、0.05、0.1和0.5 mol/L HCO3-溶液體系中的循環伏安曲線
圖8 碳鋼在60℃的CO2 (1 bar)+0.1 mol/L Cl-+0、0.05、0.1和0.5 mol/L HCO3-溶液體系中極化到1.25 V vs. SCE的SEM形貌
2.4 浸泡后表面和橫截面的形貌(CO2+Cl-+ HCO3-體系)
圖9和圖10分別給出了碳鋼在60℃的CCO2(1 bar)+0.1 mol/L Cl-+0/0.05/0.1/0.5 mol/L HCO3-溶液體系中浸泡24 h后的表面和橫截面SEM形貌。圖11給出了碳鋼在CO2+Cl-+0.05/0.5 mol/L HCO3-體系浸泡24 h后表面腐蝕產物的XRD譜。與電化學結果對應,在CO2 (1 bar)+0.1 mol/L Cl-溶液中(圖9a和圖10a)并沒有觀察到腐蝕產物,在碳鋼的界面處生成了一層殘余的Fe3C;HCO3-濃度達到0.05 mol/L時在碳鋼表面生成了疏松且尺寸較大的FeCO3腐蝕產物,晶粒尺寸大約為8 μm(圖9b)。截面形貌表明,疏松的腐蝕產物不能抑制腐蝕的進一步發生,因此腐蝕產物層的厚度達到了48.39 μm (圖10b)。疏松的腐蝕產物可能使碳鋼基體局部暴露在溶液中而加速碳鋼的局部腐蝕,使碳鋼局部失效的可能性提高。HCO3-濃度達到0.1/0.5 mol/L時FeCO3晶體尺寸變得更加細小,約3 μm (0.1 mol/L HCO3-)和1 μm(0.5 mol/L HCO3-),如圖9(c/d)所示。腐蝕產物的橫截面也呈現出非常致密的特征,厚度分別減小至20.97 μm(圖10c)和18.84 μm(圖10d)。且在XRD圖譜中,隨著HCO3-濃度的提高對應于Fe的峰強度降低,而對應于FeCO3的峰強度顯著增強; HCO3-的濃度為0.5 mol/L時FeCO3的峰強度明顯高于Fe基體,表明碳鋼表面的FeCO3晶體的析出動力學加速,幾乎覆蓋了整個表面。致密的腐蝕產物在碳鋼基體與腐蝕介質之間形成一個屏障,能有效地抑制腐蝕的進一步進行。另一方面,HCO3-的加入提高了溶液的pH值,顯著降低了FeCO3晶體析出所需的Fe2+濃度,其相對過飽和度明顯提高。同時,晶體的形核率隨著相對過飽和度呈指數相關,而晶體長大速率隨著相過相對飽和度呈線性相關。因此,隨著HCO3-濃度的提高FeCO3晶體的形核主導了整個過程,在碳鋼表面呈現出更加細小的FeCO3晶體形貌。為了進一步驗證腐蝕產物的保護性,對覆蓋有腐蝕產物的碳鋼表面在CO2(1 bar)+0.1 mol/L Cl-溶液中進行EIS測試,如圖12所示。同時,用電化學等效電路擬合EIS結果,加入膜層容抗CPEf、相位角常數nf和膜層電阻Rf。加入0.05 mol/L的HCO3-介質后其Nyquist圖呈現出單一的容抗,在此條件下碳鋼表面形成的腐蝕產物保護性較弱,以電荷轉移電阻為主要控制環節;隨著HCO3-濃度的提高(0.1~0.5 mol/L)出現兩個容抗且半徑變大,Rct和Rf值明顯增加,表明腐蝕產物的耐腐蝕能力增強。這表明,碳鋼表面的膜層已較為致密,界面反應控制環節主要由電荷轉移電阻和膜層電阻組成。
圖9 碳鋼在60℃的CO2 (1 bar)+0.1 mol/L Cl-+0、0.05、0.1和0.5 mol/L HCO3-溶液體系中浸泡24 h后的表面SEM照片
圖10 碳鋼在60℃的CO2 (1 bar)+0.1 mol/L Cl-+0、0.05、0.1和0.5 mol/L HCO3-溶液體系中浸泡24 h后的橫截面SEM照片
圖11 碳鋼在60℃的CO2 (1 bar)+0.1 mol/L Cl-+0.05/0.5 mol/L HCO3-溶液體系中浸泡24 h后腐蝕產物的XRD譜
圖12 碳鋼在60℃的CO2 (1 bar)+0.1 mol/L Cl-+0/0.05/0.1/0.5 mol/L HCO3-溶液體系中浸泡24 h后的Nyquist曲線
3 結論
(1) 加入CO2介質使碳鋼基體的腐蝕溶解速率顯著提高而對Cl-濃度的影響較小,添加高濃度的Cl-能抑制CO2的溶解而使基體的腐蝕速率略微降低。
(2) 在CO2+Cl-+HCO3-體系中加入微量的HCO3-后碳鋼表面成膜不明顯,疏松的腐蝕產物不能抑制碳鋼基體的進一步溶解;而濃度過高的HCO3-使FeCO3的過飽和度提高、加速細小晶體的析出和抑制腐蝕。
參考文獻
1 Zhao J H, Wang X Q, Kang J, et al. Crack propagation behavior during DWTT for X80 pipeline steel processed via ultra-fast cooling technique [J]. Chin. J. Mater. Res., 2017, 31(10): 728
1 趙金華, 王學強, 康 健等. 超快冷工藝下X80管線鋼的DWTT裂紋擴展行為 [J]. 材料研究學報, 2017, 31(10): 728
2 Han X, Yu S, Li H, et al. Preparation and Properties of CuO Superhydrophobic Coating on X90 Pipeline Steel [J]. Chin. J. Mater. Res., 2017, 31(9): 672
2 韓祥祥, 于思榮, 李好等. X90管線鋼表面CuO超疏水涂層的制備和性能 [J]. 材料研究學報, 2017, 31(9): 672
3 Sun J, Zhang G, Liu W, et al. The formation mechanism of corrosion scale and electrochemical characteristic of low alloy steel in carbon dioxide-saturated solution [J]. Corros. Sci., 2012, 57: 131
4 Zhang G A, Lu M X, Wu Y S. Morphology and microstructure of CO2 corrosion scales [J]. Chin. J. Mater. Res., 2005, 19(5): 537
4 張國安, 路民旭, 吳蔭順. CO2腐蝕產物膜的微觀形貌和結構特征 [J]. 材料研究學報, 2005, 19(5): 537
5 Ne?i? S. Key issues related to modelling of internal corrosion of oil and gas pipelines-A review [J]. Corros. Sci., 2007, 49(12): 4308
6 Nesic S, Postlethwaite J, Olsen S. An electrochemical model for prediction of corrosion of mild steel in aqueous carbon dioxide solutions [J]. Corrosion, 1996, 52(4): 280
7 Zhu J Y, Tan C T, Bao F H, et al. CO2 corrosion behaviour of a novel Al-containing low Cr steel in a simulated oilfield formation water [J]. Chin. J. Mater. Res., 2020, 34(6): 443
7 朱金陽, 譚成通, 暴飛虎等. 一種新型含Al低Cr合金鋼在模擬油田采出液環境下的CO2腐蝕行為 [J]. 材料研究學報, 2020, 34(6): 443
8 Han J, Ne?i? S, Yang Y. Spontaneous passivation observations during scale formation on mild steel in CO2 brines [J]. Electrochim. Acta, 2011, 56(15): 5396
9 Zhang S, Hou L, Du H, et al. A study on the interaction between chloride ions and CO2 towards carbonsteel corrosion [J]. Corros. Sci., 2020, 167: 108531
10 Xu L, Xiao H, Shang W, et al. Passivation of X65 (UNS K03014) carbon steel in NaHCO3 solution in a CO2 environment [J]. Corros. Sci., 2016, 109: 246
11 Liu Z, Gao X, Li J, et al. Corrosion behaviour of low-alloy martensite steel exposed to vapour-saturated CO2 and CO2-saturated brine conditions [J]. Electrochim. Acta, 2016, 213: 842
12 Barker R, Burkle D, Charpentier T, et al. A review of iron carbonate (FeCO3) formation in the oil and gas industry [J]. Corros. Sci., 2018, 142: 312
13 Linter B R, Burstein G T. Reactions of pipeline steels in carbon dioxide solutions [J]. Corros. Sci., 1999, 41(1): 117
14 Remita E, Tribollet B, Sutter E, et al. Hydrogen evolution in aqueous solutions containing dissolved CO2: quantitative contribution of the buffering effect [J]. Corros. Sci., 2008, 50(5): 1433
15 Almeida T D C, Bandeira M C E, Moreira R M. New insights on the role of CO2 in the mechanism of carbon steel corrosion [J]. Corros. Sci., 2017, 120: 239
16 Kahyarian A, Brown B, Nesic S. Electrochemistry of CO2 corrosion of mild steel: Effect of CO2 on iron dissolution reaction [J]. Corros. Sci., 2017, 129: 146
17 Ashley G W, Burstein G T. Initial stages of the anodic oxidation of iron in chloride solutions [J]. Corrosion, 1991, 47(12): 908
18 Darwish N A, Hilbert F, Lorenz W J, et al. The influence of chloride ions on the kinetics of iron dissolution [J]. Electrochim. Acta, 1973, 18(6): 421
19 Barcia O E, Mattos O R. The role of chloride and sulphate anions in the iron dissolution mechanism studied by impedance measurements [J]. Electrochim. Acta, 1990, 35(6): 1003
20 Mao X, Liu X, Revie R W. Pitting corrosion of pipeline steel in dilute bicarbonate solution with chloride ions [J]. Corrosion, 1994, 50(9): 651
21 Zhang G, Lu M, Chai C, et al. Effect of HCO3- concentration on CO2 corrosion in oil and gas fields [J]. Int. J. Min. Met. Mater., 2006, 13(1): 44
22 Wright R F, Brand E R, Ziomek-Moroz M, et al. Effect of HCO3- on electrochemical kinetics of carbon steel corrosion in CO2-saturated brines [J]. Electrochim. Acta, 2018, 290: 626
23 Onyejia L, Mohammed S, Kale G. Electrochemical response of micro-alloyed steel under potentiostatic polarization in CO2 saturated brine [J]. Corros. Sci., 2018, 138: 146
24 Popoola L T, Grema A S, Latinwo G K, et al. Corrosion problems during oil and gas production and its mitigation [J]. Int. J. Ind. Chem., 2013, 4(1): 35
25 Heuer J K, Stubbins J F. An XPS characteristic of FeCO3 films from CO2 corrosion [J]. Corros. Sci., 1999, 41(7): 1231
26 Zhang D L, Wei E Z, Jing H, et al. Construction of super-hydrophobic structure on surface of super ferritic stainless steel B44660 and its corrosion resistance [J]. Chin. J. Mater. Res., 2021, 35(1): 7
26 張大磊, 魏恩澤, 荊赫等. 超級鐵素體不銹鋼表面超疏水結構的制備及其耐腐蝕性能 [J]. 材料研究學報, 2021, 35(1): 7
27 Davies D H, Burstein G T. The effect of bicarbonate on the corrosion and passivation of iron [J]. Corrosion, 1980, 36(8): 416
28 Kermani M B, Morshed A. Carbon dioxide corrosion in oil and gas production-A compendium [J]. Corrosion, 2003, 59(8): 659
免責聲明:本網站所轉載的文字、圖片與視頻資料版權歸原創作者所有,如果涉及侵權,請第一時間聯系本網刪除。
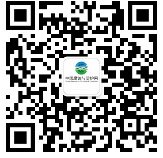
官方微信
《腐蝕與防護網電子期刊》征訂啟事
- 投稿聯系:編輯部
- 電話:010-62316606
- 郵箱:fsfhzy666@163.com
- 腐蝕與防護網官方QQ群:140808414